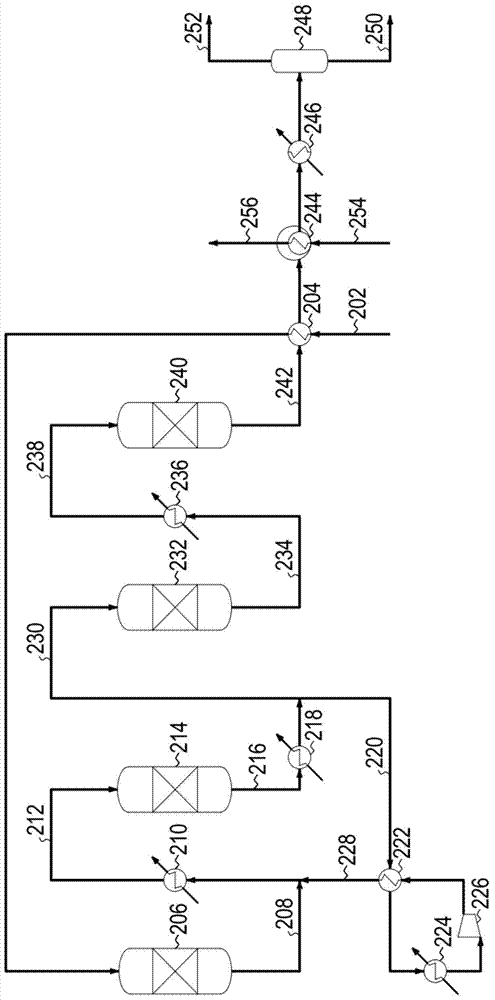
本公开涉及甲烷化方法和甲烷化系统。
背景技术:由煤经气化反应或由焦炉煤气以及随后在一个或多个反应器中将制得的合成气甲烷化以获得最终产品中足够高的CH4含量,可以大规模制造代用天然气(SNG)。甲烷化步骤通常在一系列绝热的固定床反应器中进行,其中发生的主要反应是:CO+H2O=CO2+H2(1)CO+3H2=CH4+H2O(2)在始于CO2和H2的甲烷化的情况下,据信反应的机理首先经由逆水煤气变换(即反应(1)的逆反应)进行,接着是CO甲烷化以形成CH4,因此总反应是:CO2+4H2=CH4+2H2O(3)合成气的甲烷化是高度放热的,这导致这些反应器中温度大幅上升。同时,入口温度必须足够高以引发该过程。因此,用于甲烷化的原料合成气传统上在脱硫之前使用来自下游反应器的热废气通过气体/气体热交换来预热。由于甲烷化方法是高度放热的,产生大量废热,一部分处于无法将该废热用于制造高压蒸汽的温度下。因此,使用低等级热用于在气体/气体热交换器中预热原料合成气是能量有效的,如US4,130,575中所示。由于穿过系统的压力损失,气体/气体原料合成气预热器的泄露(例如管破裂)可能导致原料合成气进入热的废气并由此绕过硫化单元。此类绕行可能导致下游反应器的硫中毒,并导致工艺阶段中甲烷化之间不合意的平衡,进而导致较低的原料合成气总转化率。为了避免这种低效运行的风险,已经确定,通过诸如水蒸汽或油的流体传热介质进行的实际上低效的传热是有益的,尽管存在附加投资和附加的运行费用。次级间接热交换在下文中用于热交换过程,其中借助具有热交换介质流的热交换回路传递热量,以使得热交换器用于将热量由热的工艺流传递(收集)至热交换介质流,然后在另外的热交换器中使用热交换介质将热量传递(提供)至冷的工艺流。其中描述了两个用于热交换的装置在次级热交换回路中通过流体传热介质热连接,同时与所述甲烷化阶段中反应的与生成的气体流为流体分离,这意味着流体传热介质不在甲烷化阶段中在反应中立即发生,但是不能排除例如将蒸汽输送至蒸汽涡轮机或进料至汽化器或甲烷化段上游的化学过程,以使得水或水分子的原子成为进入甲烷化段的进料流的一部分。术语“热交换介质”和“流体传热介质”对用于提供不同元件之间的热接触而不提供流体接触的料流而言可互换使用。术语“集热热交换器”用于这样的热交换器:其中热交换介质接收来自具有比热交换介质更高温度的工艺气体的热能。术语“供热热交换器”用于这样的热交换器:其中热交换介质向具有比热交换介质更低温度的工艺气体提供热能。术语“通过流体传热介质输出热量”应当用于通过流体传热介质将能量由甲烷化阶段传递至合成天然气工厂的另一段或例如在蒸汽涡轮机中传递能量。
技术实现要素:在广义上,本公开涉及甲烷化系统,其包含保持一定量的甲烷化催化剂的至少一个甲烷化反应器,所述反应器具有用于富含氢气和碳氧化物如一氧化碳和/或二氧化碳的进料气体流的入口,所述反应器被进一步配置为引导所述进料气体与所述甲烷化催化剂接触,并且其中所述甲烷化反应器还包括具有比所述进料气体更高的温度的富甲烷气体流的出口,其中所述甲烷化系统还包含:热交换回路,其在所述甲烷化系统中与进料气体流和富甲烷气体流为流体分离,所述热交换回路还包括集热装置,其被配置为在所述甲烷化反应器下游冷却所述富甲烷气体并加热流体传热介质,和供热装置,其被配置为在所述甲烷化反应器上游通过冷却流体传热介质来加热所述进料气体,通过在单独的热交换回路中使用流体传热介质所获得的相关益处在于避免了该过程中由进料气体向富甲烷气泄露的风险。在其它实施方案中,所述流体传热介质包含至少90%的选自水蒸气、熔盐和油的一种材料,水蒸气的相关益处在于是一种容易获得的具有高热容量的流体传热介质。在其它实施方案中,集热装置和供热装置被配置为所述流体传热介质的压力比进料气体或富甲烷气体的压力低至少50%,相关益处在于提供有效的传热回路,并且由于流体热传介质的相变(如水/水蒸气)有可能甚至获得有效热交换的益处。在其它实施方案中,进料气体的压力高于20巴、30巴或50巴,热交换介质的压力低于10巴或5巴,相关益处在于有效甲烷化方法的提高的进料气体压力,并且相关益处在于简单热交换回路的中等热交换介质压力。在其它实施方案中,热交换后的进料气体的温度为120-350℃,相关益处在于进料气体具有适于激活化学反应的温度。在其它实施方案中,富甲烷气体在热交换前的温度为450-750℃,相关益处在于该温度对应于高反应程度,而低于对催化活性材料有害的温度。在其它实施方案中,本公开涉及一种工艺装置,其包含上述甲烷化系统,还包含用于气化包括煤、石油焦(petcoke)、废弃物或可再生燃料在内的碳质材料的反应器,相关益处在于提供了由此类通过其它方法难以转化的材料生产合成天然气的装置,该方法操作安全、能够有效地进行热交换并具有低投资成本。在其它实施方案中,所述进料气体包括焦炉煤气。本公开的再一方面涉及一种甲烷化方法,包括以下步骤:通过与热交换介质的热交换来预热富含氢气和碳氧化物的进料气体,所述碳氧化物如一氧化碳和/或二氧化碳,在甲烷化反应方面为催化活性的材料的存在下使所述进料气体反应以形成具有高于所述进料气体的温度的富甲烷气体,和将热量从所述富甲烷气体传递至所述热交换介质,其相关益处在于避免了在热交换器中将富甲烷气体传递至所述进料气体的风险。本公开的再一方面涉及一种生产含有至少90%的甲烷的代用天然气的方法,包括上述甲烷化方法,以及一个或多个使所述富甲烷气体与其它在甲烷化方面具有催化活性的材料接触的附加步骤,其相关益处在于提供了一种以安全且有效的方式将反应性进料气体转化为有吸引力的燃料的方法。本公开的再一方面涉及一种用于制造合成天然气的系统,其包含上述甲烷化系统或者上述工艺装置。在大规模化学方法中,方法中各种元件的有效热集成是重要的。因此,通常做法是使用热交换器,以便将放热过程中释放的热量转移作为进料气体的能量输入,以提供高到足以激活进料气体的温度。此类配置通常被称为进料/流出物热交换配置,其需要使用相当巨大和昂贵的气体/气体热交换器,但是在许多方法中此类配置因其热效率而是一种优选的有效配置。在合成天然气生产(这是一个高度放热的过程)中,这已经被视为最佳做法,并已经开发了收集出口水蒸气(steamforexport)流中的能量的配置。通常出口水蒸气是在例如锅炉中产生的高压(并因此是高温的)水蒸气。但是,根据本公开,提出了使用与常用的气体/气体热交换器相比不那么有效的进料与流出物之间的热交换装置,即所谓的次级间接热交换,其中主要工艺回路与次级热交换回路为热连通,所述次级热交换回路被配置成经由流体传热介质如水蒸气、油或盐提供传热手段。这种设计的背景并不建立在运行成本发明,而是建立在工艺风险管理方面,根据该工艺风险管理可以确定,进料气体泄露至下游工艺流中的潜在风险可能会导致超出规格的产品。此外,如果进料气体泄露到中间位置的话,进一步的风险在于:进料气体可能在下游反应器中经历放热甲烷化反应,并可能使反应器过热,导致对催化剂的破坏。使用热交换介质的单独回路的其它益处在于这种热交换介质回路可以被配置为独立加热该热交换介质,这在工艺启动过程中和具有波动条件的其它情况下提供益处。附图说明图1描述了本公开的甲烷化方法,其中采用3个绝热甲烷化反应器和用水蒸气作为热交换介质的热交换器,以及图2描述了现有技术的甲烷化方法,其中采用3个绝热甲烷化反应器和进料-流出物热交换器。具体实施方式在本公开中,术语“富含氢气和碳氧化物的进料气体”应当被理解为具有形成高含量甲烷的潜力的气体,例如,其可以包含总量为至少40%的氢气和碳氧化物。在本公开中,“碳氧化物”是指一氧化碳和/或二氧化碳。在本公开中,术语“富甲烷气体”应当被理解为这样的产物气体:其中甲烷的浓度高于进料气体中甲烷的浓度。通常,富甲烷气体中甲烷的浓度为至少20%。在图1中,描述了采用水蒸气作为热交换介质的甲烷化方法。将合成气102通过水蒸气流104加热,并引导至与硫保护器(sulfurguard)106中的催化活性材料接触。将再循环的富甲烷气体128添加到脱硫合成气108中,以获得第一甲烷化反应器进料气体112。将甲烷化反应器进料气体112加热110,并引导至第一甲烷化反应器114,由此取出第一富甲烷气体116,并将其在热交换器118中冷却,产生高压出口水蒸气。将第一富甲烷气体的再循环部分120在到达再循环压缩机126之前通过热交换器122冷却并通过冷却器124进一步冷却。将该气体通过热交换器122加热,提供再循环的富甲烷气体128。使第一富甲烷气体的未再循环部分130进一步在第二132和第三140甲烷化反应器中反应,并中间冷却136(通常产生高压出口水蒸气)第二阶段富甲烷气体134。将第三阶段富甲烷气体142冷却(通常伴随工艺水在锅炉144中的冷凝)并进一步通过冷却器146冷却,随后在冷凝器148中分离水150,制得合成天然气152。该实施方案中锅炉144的冷却介质154是水,水以水蒸气156、158的形式离开锅炉,通过将水蒸气冷凝为水160,由此向与合成气102的热交换104提供加热介质158,并提供低压出口水蒸气156。在本公开的其它实施方案中,水蒸气可以由替代的热交换介质如熔盐或油代替。在本公开的其它实施方案中,在其它热交换器中抽取的能量也可以被传递用于预热进料气体,例如,通过在热交换器(优选136,但也可能是118)中加热流体传热介质并在加热器110中使用该流体传热介质用于预热脱硫的甲烷化反应器进料气体。在图2中,描述了使用进料-流出物热交换器的甲烷化方法。将合成气202加热204并引导与硫保护器206中的催化活性材料接触。将再循环的富甲烷气体228添加到脱硫的合成气208中以获得第一甲烷化反应器进料气体212。将甲烷化反应器进料气体212加热210并引导至第一甲烷化反应器214,由该反应器中取出第一富甲烷气体216,并将其在热交换器218中冷却,产生高压出口水蒸气。将第一富甲烷气体的再循环部分220在到达再循环压缩机226之前通过热交换222冷却,并通过冷却器224进一步冷却。将该气体通过热交换222加热,提供再循环的富甲烷气体228。使第一富甲烷气体的未再循环部分230进一步在第二232和第三240甲烷化反应器中反应,并中间冷却236(通常产生高压出口水蒸气)第二阶段富甲烷气体234。将第三阶段富甲烷气体242首先在热交换器204中冷却(附加地通常伴随水在锅炉244中的冷凝)并通过冷却器246进一步冷却,随后在冷凝器248中分离水250,并制得合成天然气252。锅炉244的冷却介质254是水,其以低压水蒸气256的形式离开锅炉。实施例表1和2显示了进料气体的组成、流量和温度。对于本公开的方法(表1对应于图1,其使用基于水蒸气的热交换回路)和现有技术的方法(表2对应于图2,其如图2所示使用进料/流出物热交换器)显示了中间产物气体和最终的合成天然气。其中料流穿过热交换器,THX入和THX出表示热交换器之前和之后的温度。表1和表2的比较表明,两种方法的运行条件相同,但是根据表2,当采用用水蒸气的次级间接热交换时,水蒸气的输出156和254/256由7665Nm3减少至6629Nm3,此外,获得8725m3的低价值的温热冷凝物料流。但是,这种降低的效率被认为针对提高的工艺操作安全性起到了良好的平衡,这种安全性例如通过用外部水蒸气源预热进料流的可能性或通过避免气体/气体热交换器中的泄露来获得。此外,在波动式操作过程中获得的灵活性被认为足以弥补降低的效率。