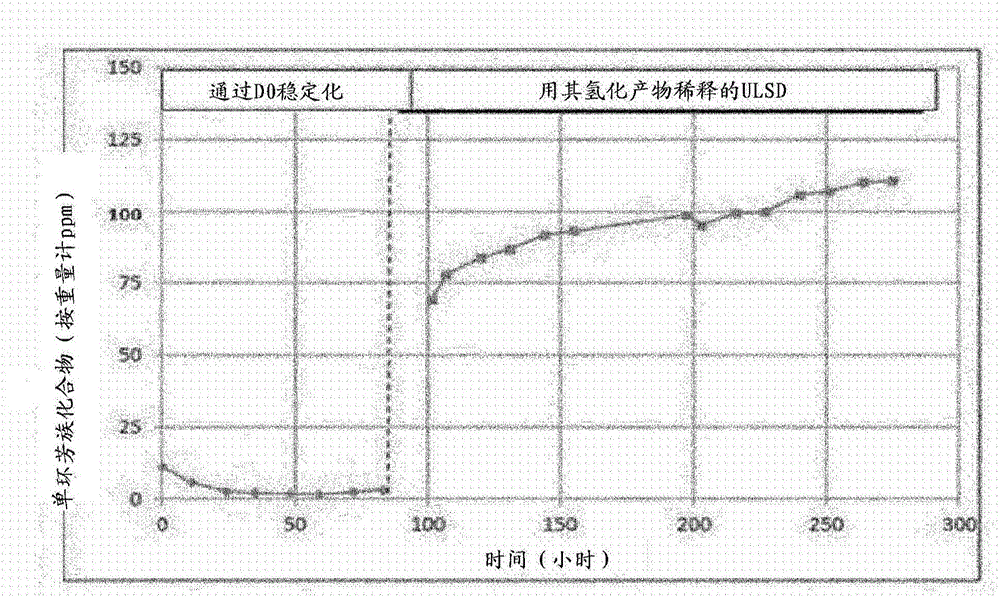
本发明涉及用于使石油馏分脱芳构化以产生硫含量非常低且芳族化合物含量非常低的脱芳构化的含烃流体的方法。特别地,本发明涉及用于使石油馏分深度脱芳构化的方法,所述方法包括利用石油馏分和一种或更多种惰性轻质稀释剂的混合物进行的至少一个脱芳构化循环,所述稀释剂的馏程不超过80℃。本发明还涉及源自所述方法的脱芳构化的含烃流体及其用途。本发明同样地涉及用于实施所述方法的装置。
背景技术:
:含烃流体广泛用作溶剂,例如用于粘合剂、清洗液、爆炸物,用于装饰涂料、漆和印刷墨的溶剂。轻质含烃流体用于例如金属提取、金属加工或脱模、工业润滑剂和钻井液的应用中。含烃流体也可以用作粘合剂和密封剂体系如硅酮填补剂中的稀释油,在基于增塑聚氯乙烯的制剂中用作降粘剂,在用作絮凝剂(例如,在水处理中、在采矿作业期间或在造纸中)的聚合物制剂中用作溶剂,以及还用作印染浆的增稠剂。此外,含烃流体还可以在多种其他应用如化学反应中用作溶剂。含烃流体的化学性质和组成根据该流体的目标用途而显著不同。含烃流体的重要特性是馏程(通常根据标准ASTMD-86来测定或者通过用于较重质物质的减压蒸馏技术根据ASTMD-1160来测定)、闪点、密度、苯胺点(根据标准ASTMD-611测定)、芳族化合物含量、硫含量、粘度、颜色和折射率。这些流体可以分类为链烷烃的、异链烷烃的、脱芳构化的、环烷烃的、非脱芳构化的和/或芳族的。如通过根据标准ASTMD-86测定的初沸点(InitialBoilingPoint,IBP)和终沸点(FinalBoilingPoint,FBP)之间的窄范围所表明的,这些流体倾向于具有窄的沸程。初沸点和终沸点将根据流体的目标用途进行选择。然而,窄馏分的使用提供了精确的闪点的益处,这出于安全原因是重要的。窄馏分也为流体带来重要的特性,例如更明确的苯胺点或溶解能力,以及粘度和限定的蒸发条件(对于干燥很重要的体系),最后是更精确的表面张力。该馏程优选地小于80℃。为了生产这些含烃流体,在加氢脱芳构化单元中通过催化氢化过程处理用作原料的石油馏分,所述催化氢化过程由例如在高压下运行的数个串联反应器构成。这些反应器具有一个或更多个催化床。这些单元由主处理段构成,所述主处理段通常为:原料储存单元、具有数个反应器的氢化段、和蒸馏塔。为此,参见图4。通常为氢化段安装的配置是一系列的数个串联反应器。通过氢化进行加氢脱芳构化的单元的效率取决于这些反应器中的催化剂的稳定性和性能。氢化流出物然后被蒸馏成成品。氢化段中通常使用的催化剂是基于镍或贵金属的。氢化反应是高度放热的,第一氢化反应器的温度通过用非反应性稀释剂稀释原料(称为“新鲜”原料)来控制。作为稀释剂,已知的是使用氢化原料(即,氢化流出物)的一部分,其因此返回到第一反应器的入口并通过再循环与待处理原料在进入之前混合(通常为50重量%/50重量%的新鲜原料/氢化原料)。因此,这种再循环使得可以控制氢化反应的放热。为了生产特定的含烃流体,优选的原料是特定的瓦斯油馏分,例如具有低硫含量的原料。典型的原料可以例如对应于氢化裂解的真空瓦斯油(hydrocrackedvacuumgasoil,HCVGO)。被认为常规的某些原料可导致催化剂的立即逐渐失活。例如,难起反应的、重质且难以处理的原料。难起反应的重质原料可能是这样的原料:其硫含量大于5ppm,聚芳族分子含量大于1重量%,终馏点大于330℃并且具有高含量的环烷烃-芳族化合物。这些化合物是最难进行加氢脱芳构化处理的,因此,这些原料呈现出催化剂失活增加的更大风险。因此,炼油厂中产生的所有常规原料不能用于加氢脱芳构化方法。如果炼油厂中产生的原料包含更大量的芳族化合物或更难进行加氢脱芳构化处理的分子,则脱芳构化步骤将难以进行,反应器的催化床失活将大大加速,并且将不能满足最终产品的技术规格。因此,难以使用炼油厂中产生的常规瓦斯油,即使这些原料与特定的瓦斯油相比是广泛可得的。专利申请US7291257描述了一种用于氢化处理石油原料的方法,所述方法包括使用溶剂/稀释剂,所述溶剂/稀释剂可以是氢化原料的一部分或者也可以是柴油,并且其唯一作用是增加溶液中氢的百分比。类似地,专利申请WO2012133138也涉及使用稀释剂,使得可以降低通过催化重整获得的重质石油馏分的多环芳族化合物的氢化反应的放热性,然后再次重整以获得包含单环芳族烃的馏分。在该专利申请中,稀释剂对应于重质馏分的氢化反应产物的一部分。迄今为止文献中存在的稀释步骤仅使得可以通过用其氢化流出物稀释待处理原料来限制氢化反应的放热性。关于在使用常规炼油厂原料以获得源自反应的期望产品期间的催化床的失活增加并没有提供解决方案。事实上,很大程度上引起催化剂失活的芳族化合物能够通过与待处理原料混合的氢化流出物被再次引入。因此,使用存在于现有技术水平下的与稀释剂混合的常规炼油厂原料不能使催化失活减少并且不能获得所产生的含烃流体所需的特性。本发明的主要目的之一在于提供用于制备含烃流体的方法,所述方法具有增加的供应原料的灵活性。本发明的另一个目的在于提供用于生产含烃流体的优化方法,所述方法使得可以使常规炼油厂原料深度脱芳构化。本发明的一个目的还在于在常规炼油厂原料的脱芳构化期间获得增加的芳族化合物转化率。另外,本发明的另一个目的在于在常规炼油厂原料的处理期间控制和限制氢化反应器的催化剂失活。本发明的一个目的还在于增加氢化催化剂在常规炼油厂原料的处理期间的使用寿命。技术实现要素:这些目的使用新型的脱芳构化方法来实现。本发明涉及一种用于使石油馏分脱芳构化以产生硫含量小于或等于5ppm且芳族化合物含量小于或等于300ppm的脱芳构化的含烃流体的方法,所述含烃流体根据标准ASTMD-86的沸点为100℃至400℃,并且由根据标准ASTMD-86测定的初沸点(IBP)与终沸点(FBP)之差所定义的馏程不超过80℃,所述方法包括利用石油馏分和馏程不超过80℃的一种或更多种惰性轻质稀释剂的混合物进行的至少一个脱芳构化循环。有利地,所述方法包括至少一个稀释步骤,其中稀释剂由单一的惰性轻质稀释剂构成,所述惰性轻质稀释剂选自单独或混合物形式的饱和的含烃化合物,优选链烷烃。优选地,根据本发明的方法的脱芳构化循环是在80℃至300℃的温度和20巴至200巴的压力下进行的催化氢化。根据一个实施方案,根据本发明的石油馏分与惰性轻质稀释剂之间的质量比为10/90,优选30/70,并且更优选50/50。优选地,通过蒸馏使根据本发明的惰性轻质稀释剂与脱芳构化循环之后获得的氢化产物分离,然后使所述惰性轻质稀释剂再循环。优选地,根据本发明的惰性轻质稀释剂根据标准ASTMD-86的馏程为100℃至250℃,优选140℃至200℃,并且其初沸点与其终沸点之差小于或等于80℃。根据本发明,惰性轻质稀释剂的终沸点优选地比待处理石油馏分的初沸点低至少10℃,并且更优选地低20℃。优选地,根据本发明的惰性轻质稀释剂是饱和的并且更优选是链烷烃的。优选地,根据本发明的惰性轻质稀释剂包含大量的异链烷烃和少量的正链烷烃。优选地,根据本发明的惰性轻质稀释剂包含大于90重量%的异链烷烃,并且更优选大于99重量%的异链烷烃。优选地,根据本发明的惰性轻质稀释剂通过UV光谱法测量的芳族化合物含量小于50ppm,优选小于20ppm。优选地,根据本发明的惰性轻质稀释剂根据标准ASTMD-6229的苯化合物含量按重量计小于10ppm,优选小于1ppm。优选地,根据本发明的惰性轻质稀释剂根据标准ASTMD-5453的硫含量小于2ppm,优选小于1ppm。优选地,根据本发明的惰性轻质稀释剂根据标准ENISO3104的在20℃下的运动粘度为0.75mm2/s至204mm2/s,优选1mm2/s至1.5mm2/s,并且更优选1.1mm2/s至1.4mm2/s。优选地,根据本发明的惰性轻质稀释剂是通过原油的常压蒸馏、减压蒸馏、催化裂化、低聚和/或氢化获得的含烃馏分。优选地,根据本发明的惰性轻质稀释剂是通过丙烯馏分或丁烯馏分的低聚和氢化获得的含烃馏分。优选地,根据本发明的惰性轻质稀释剂是源自丙烯馏分或丁烯馏分的低聚和氢化的汽油馏分或煤油馏分。优选地,根据本发明的石油馏分根据标准ENISO20846的硫含量小于15ppm,优选小于10ppm或甚至小于5ppm。根据一个实施方案,通过根据本发明的方法获得的脱芳构化的含烃流体优选地具有:-小于或等于5ppm,优选小于3ppm或甚至小于0.5ppm的硫含量,-小于或等于300ppm,优选小于100ppm或甚至小于50ppm的芳族化合物含量,-小于60重量%,优选小于50重量%或甚至小于40重量%的环烷烃含量,和/或-小于30重量%,优选小于25重量%或甚至小于20重量%的多环烷烃含量,和/或-大于40重量%,优选大于60重量%或甚至大于70重量%的链烷烃含量,和/或-大于20重量%,特别地大于30重量%或甚至大于40重量%的异链烷烃含量。本发明的另一个主题是通过根据本发明的方法获得的脱芳构化的含烃流体的以下用途:作为钻井液、作为工业溶剂、作为切削液、作为轧制油、作为放电加工液、作为工业润滑剂中的防锈剂、作为稀释油、作为基于增塑聚氯乙烯的制剂中的降粘剂、作为作物保护液。本发明的一个主题还在于通过根据本发明的方法获得的脱芳构化的含烃流体的以下用途:用于涂覆液、用于金属提取、用于采矿工业、用于爆炸物、用于混凝土脱模制剂、用于粘合剂、用于印刷墨、用于金属加工液、用于基于硅酮的聚合物制剂或密封产品、用于树脂、用于药物产品、用于化妆品制剂、用于漆组合物、用于在水处理中使用的聚合物、用于造纸、或者用于印染浆或清洗溶剂。本发明的一个主题同样在于惰性轻质稀释剂与石油馏分混合用于脱芳构化方法中以提高氢化产率和减少催化剂失活的用途。本发明还涉及一种用于实施根据本发明的方法的装置,其包括至少两个串联连接的氢化反应器、在反应器出口处的至少一个蒸馏塔、和位于反应器与蒸馏塔之间的用于从脱芳构化的含烃流体中提取惰性轻质稀释剂的塔(在图3中也称为分离塔),所述氢化反应器各自具有至少一个催化床。附图说明附图1至3是根据本发明的方法的深度脱芳构化单元和所获得的结果的图示。图4是常规脱芳构化方法的一般布局。具体实施方式根据本发明的方法涉及脱芳构化单元的氢化反应器的运行条件的改进,从而允许生产脱芳构化的含烃流体。特别地,根据本发明的方法涉及惰性轻质溶剂作为待处理原料的稀释剂的用途:用以限制氢化反应器的催化床失活,用以提高转化率和氢化产率并因此使得源自石油馏分的常规炼油厂原料能够加氢脱芳构化以生产所述脱芳构化的含烃流体。稀释剂:本发明的方法包括用轻质惰性溶剂稀释原料的步骤。“轻质”意指可以通过蒸馏(优选常压蒸馏或温和的减压蒸馏)容易地与氢化段出口处的氢化流出物分离的溶剂。“氢化流出物”意指氢化原料的产物,即在蒸馏段之前的氢化段出口处获得的源自原料的产物。优选地,轻质惰性溶剂的终沸点比待处理石油馏分的初沸点低至少10℃,更优选地低至少20℃。“惰性”意指不与与其混合的待处理原料发生化学反应的溶剂,优选链烷烃。不受该理论的束缚,原料的惰性可由链烷烃(特别是异链烷烃)的性质和链烷烃的量引起。此外,应理解,根据本发明的惰性轻质稀释剂不对应于氢化原料的产物。惰性轻质稀释剂不是氢化流出物。有利地,惰性轻质稀释剂是这样的含烃馏分:所述含烃馏分根据标准ASTMD-86的馏程DR(以℃计)为100℃至250℃,优选140℃至200℃,并且其初沸点与终沸点之差小于或等于80℃。稀释剂可以包括馏程在该馏分的馏程内的一种或更多种馏分。根据一个特定实施方案,惰性轻质稀释剂是完全饱和的并且优选是链烷烃的。优选地,稀释剂由支化C7-C14烷烃,优选C9-12烷烃构成。有利地,惰性轻质稀释剂由大量的异链烷烃和少量的正链烷烃构成。优选地,通过GC-MS测定,稀释剂包含大于90重量%的异链烷烃,并且更优选大于99重量%的异链烷烃。惰性轻质稀释剂优选不含芳族化合物。“不含”意指通过UV光谱法测量,芳族化合物小于50ppm,并且更优选芳族化合物小于20ppm。惰性轻质稀释剂优选地不含苯化合物。“不含”意指根据标准ASTMD-6229,苯化合物小于10ppm,并且更优选苯化合物小于1ppm。优选地,惰性轻质稀释剂根据标准ASTMD-5453的典型硫含量小于2ppm并且优选小于1ppm。惰性轻质稀释剂根据标准ENISO3104的在20℃下的典型运动粘度通常为0.75mm2/s至2.04mm2/s,优选1mm2/s至1.5mm2/s,并且更优选1.1mm2/s至1.4mm2/s。优选惰性轻质稀释剂根据标准ASTMD-97的典型倾点为-40℃至-60℃,优选-50℃至-60℃。优选惰性轻质稀释剂根据标准ISO2977的苯胺点为50℃至80℃,优选55℃至70℃。此外,惰性轻质稀释剂的优点在于,在市场上容易获得并且在源自油蒸馏的产物链中是相对经济的。根据本发明的用作稀释剂的惰性轻质溶剂是含烃馏分。在本发明的含义中,“含烃馏分”意指源自原油蒸馏的馏分,优选源自原油的常压蒸馏和/或减压蒸馏的馏分,优选源自常压蒸馏随后进行减压蒸馏的馏分。根据本发明的含烃馏分优选为源自丙烯馏分或丁烯馏分的轻质馏分,更优选汽油或煤油馏分。根据本发明的含烃馏分还优选地在高压下经历催化裂化、低聚和/或氢化的步骤。含烃馏分可以是经历上述步骤的含烃馏分的混合物。待处理原料:根据本发明的“待处理原料”意指源自油精炼的待处理石油馏分。根据本发明,典型的炼油厂原料可以是任何类型,包括源自馏出物氢化裂解单元的原料,以及具有高芳族化合物含量的原料,例如常规超低硫柴油原料、重质柴油或旨在用于航空的燃料,或者这些原料的特定级分。常规超低硫柴油(ULSD)通常包含小于10ppm的硫(根据标准ENISO20846的方法测量的),其密度为0.820g/cm3至0.845g/cm3(根据标准ENISO12185的方法测量的),并且其通常满足EuroV柴油标准要求和欧洲指令2009/30/EC中限定的规格。其通常通过对来自常压蒸馏的直馏瓦斯油馏分进行严格加氢脱硫来获得。常规的炼油厂原料还可以通过在催化剂的存在下在高压下添加氢进行氢化裂解以获得更短且更简单的分子。HydrocarbonProcessing(1996年11月,第124至128页),HydrocrackingScienceandTechnology(1996)以及专利US4347124、US4447315、WO-A-99/47626中提供了对氢化裂解方法的描述。初馏:在将待处理石油馏分作为原料引入氢化单元之前可以任选地进行所述石油馏分的初馏步骤。然后将任选地经初馏的石油馏分稀释并氢化。稀释:根据本发明的方法的稀释速率可以为10重量%/90重量%至50重量%/50重量%,并且优选30重量%/70重量%至50重量%/50重量%的待处理原料/稀释剂。优选地,作为待处理原料的石油馏分仅用单一的如上所述的轻质惰性稀释剂稀释,或者用由数种如上所述的稀释剂构成的混合物稀释。根据一个特定实施方案,不包括这些惰性轻质稀释剂与其他已知稀释剂(例如芳族稀释剂,如苯及其衍生物)的混合物。有利地,所述方法包括至少一个稀释步骤,其中稀释剂由单一的惰性轻质稀释剂构成,所述惰性轻质稀释剂选自单独或混合物形式的饱和的含烃化合物,优选链烷烃。稀释剂与原料的混合点在图3中示出。所述稀释剂可以是在A点引入的“新鲜”稀释剂或者在氢化段出口处通过蒸馏回收然后与流出物分离的稀释剂。在该第二种情况下,稀释剂在B点引入。氢化:在氢化单元中使用的氢通常是高纯度氢,其纯度例如超过99%,但是也可以使用其他水平的纯度。氢化在一个或更多个串联的反应器中进行。反应器可以包括一个或更多个催化床。催化床通常为固定催化床。本发明的氢化方法优选地包括两个或三个反应器,优选三个反应器,并且更优选地在三个串联反应器中进行。第一反应器允许基本上所有的不饱和化合物和多至约90%的芳族化合物氢化。在第二阶段中,即在第二反应器中,继续进行芳族化合物的氢化,并且因此多至99%的芳族化合物被氢化。第三反应器中的第三阶段是完成阶段,其使得可以获得小于300ppm,优选小于100ppm并且更优选小于50ppm的芳族化合物含量,即使在具有高沸点(例如,大于300℃)的产物的情况下也是如此。通常,具有高沸点的级分包含难以进行脱芳构化的重质芳族化合物。典型的氢化催化剂可以是本体或负载的,并且可以包括以下金属:镍、铂、钯、铼、铑、钨酸镍、镍钼、钼、钴钼。载体可以是二氧化硅、氧化铝或二氧化硅-氧化铝、或沸石。优选的催化剂是氧化铝载体上的基于镍的催化剂(其比表面积为100m2/g催化剂至200m2/g催化剂)、或基于镍的本体催化剂。典型的氢化条件如下:-压力:20巴至200巴,优选60巴至180巴,并且更优选100巴至160巴;-温度:80℃至300℃,优选120℃至250℃,并且更优选160℃至200℃;-液时空速(Liquidhourlyspacevelocity,LHSV):0.2小时-1至5小时-1,优选0.5小时-1至3小时-1,并且更优选0.8小时-1至2小时-1;-处理速率:50Nm3/吨原料至300Nm3/吨原料,优选80Nm3/吨原料至250Nm3/吨原料,并且更优选100Nm3/吨原料至200Nm3/吨原料。有利地,在上述条件下利用氢化直到获得具有非常低的芳族化合物含量,优选小于300ppm,优选小于100ppm并且更优选小于50ppm的脱芳构化的含烃流体。有利地,在上述条件下利用氢化直到获得95%至100%,优选98%至99.99%的芳族化合物的转化率。在这些条件下,最终产物的芳族化合物含量将保持非常低,通常小于300ppm,即使其沸点较高(通常大于300℃或甚至大于320℃)也是如此,并且其硫含量也将非常低,通常小于5ppm。可以使用包括两个或三个催化床或更多个催化床的反应器。催化剂可以以可变的或基本上相同的量存在于每个反应器中,例如,对于三个反应器,根据重量,量可以是0.05-0.5/0.10-0.70/0.25-0.85,优选0.07-0.25/0.15-0.35/0.4-0.78,并且更优选0.10-0.20/0.20-0.32/0.48-0.70。根据本发明的方法用轻质惰性稀释剂稀释原料使得可以限制氢化段反应器的催化床的失活,从而相对于用常规方法的氢化流出物的稀释延长了催化剂的使用寿命。推测这是由于在轻质惰性稀释剂中不存在芳族化合物所致。有利地,根据本发明的方法使得可以获得95%至100%,优选98%至99.99%的芳族化合物的转化率。根据本发明的方法有利地使得可以将催化床的失活限制为小于0.05ppm单环芳族化合物/小时,优选小于0.01ppm单环芳族化合物/小时。再循环:在氢化段的出口处,通过蒸馏,优选常压蒸馏或温和的减压蒸馏,使惰性轻质稀释剂与氢化产物分离,然后再循环到串联的第一反应器的入口,从而使得可以通过与待处理原料混合来重复使用该稀释剂。可能需要在再循环系统中或者在反应器之间插入骤冷箱以使反应器或催化床之间的流出物冷却,从而控制各反应器的温度。在一个实施方案中,使至少部分的惰性轻质稀释剂和/或分离的气体在用于供给氢化阶段的系统中再循环。该稀释有助于将反应的放热性保持在可控的限度内,特别是在第一阶段中。再循环还允许反应之前的热交换以及更好的温度控制。来自氢化单元的流出物主要包含氢化产物和氢。使用闪蒸分离器将流出物分离成气相(主要是剩余的氢)和液相(主要是氢化的烃)。该过程可以使用三个闪蒸分离器来进行,一个在高压下,一个在中压下并且一个在低压(非常接近大气压)下。在闪蒸分离器的顶部收集的气态氢可以再循环到供给氢化单元的系统中或者反应器之间的氢化单元中的不同水平处。闪蒸分离器使得能够利用液体/蒸气平衡阶段实现分离。其有利地用于本发明,原因是其能够分离沸点相差非常大的化合物的混合物。单个阶段就能够实现良好的分离。蒸馏和分馏:根据一个实施方案,在大气压下分离最终产物。然后直接将其供给至真空分馏单元。优选地,分馏将在10毫巴至50毫巴并且更优选约30毫巴的压力下进行。分馏可以以这样的方式进行:可以同时将多种含烃流体从分馏塔中移除,并且其沸点可以预先确定。蒸馏塔通过数个液体/蒸气平衡阶段(至少3个阶段)实现了混合物的分离。对于给定的混合物,化合物的沸点越接近,分离阶段的数目就越多。因此,氢化反应器、分离器和分馏单元可以直接连接,而不需要使用中间罐。氢化和分馏的这种整合使得能够实现优化的热整合以及减少的设备数和能量节约。通过所述方法获得的脱芳构化的含烃流体:根据所述方法的一个实施方案产生的脱芳构化的含烃流体的沸点为100℃至400℃,并且芳族化合物含量非常低,通常小于300ppm,优选小于100ppm并且更优选小于50ppm。所产生的脱芳构化的含烃流体还具有极低的硫含量,小于5ppm,优选小于3ppm并且更优选小于0.5ppm,其水平太低以致于不能通过能够测量极低硫含量的常规分析仪检测到。脱芳构化的含烃流体产物还有利地具有:-小于60重量%,特别地小于50重量%或甚至小于40重量%的环烷烃含量,和/或-小于30重量%,特别地小于25重量%或甚至小于20重量%的多环烷烃含量,和/或-大于40重量%,特别地大于60重量%或甚至大于70重量%的链烷烃含量,和/或-大于20重量%,特别地大于30重量%或甚至大于40重量%的异链烷烃含量。此外,在苯胺点或溶解能力、分子量、蒸气压、粘度、限定的蒸发条件(对于干燥很重要的体系)以及限定的表面张力方面,所产生的脱芳构化的含烃流体具有卓越的特性。根据所述方法的一个实施方案产生的脱芳构化的含烃流体可以单独地或以混合物形式用作:钻井液、工业溶剂、切削液、轧制油、放电加工液、工业润滑剂中的防锈剂、稀释油、基于增塑聚氯乙烯的制剂中的降粘剂、作物保护液。根据所述方法的一个实施方案产生的脱芳构化的含烃流体还可以单独地或以混合物形式用于涂覆液、用于金属提取、用于采矿工业、用于爆炸物、用于混凝土脱模制剂、用于粘合剂、用于印刷墨、用于金属加工液、用于基于硅酮的聚合物制剂或密封产品、用于树脂、用于药物产品、用于化妆品制剂、用于漆组合物、用于在水处理中使用的聚合物、用于造纸、或者用于印染浆或清洗溶剂。实施例在本说明书的剩余部分中,通过对本发明进行举例说明而给出了实施例,但所述实施例决不旨在限制范围。待处理原料、稀释剂和混合物的特性:在新鲜原料(“新鲜原料”意指如上所述的待处理的典型的炼油厂原料)与轻质惰性稀释剂混合进行的处理与如在现有技术水平下所述的新鲜原料与其氢化流出物混合进行的处理之间进行比较测试,如上所述,所述轻质惰性稀释剂根据标准ASTMD-86的馏程DR(以℃计)为100℃至250℃,并且初沸点与终沸点之差小于或等于80℃。·ULSD原料:起始新鲜原料是ULSD柴油,商业常规炼油厂原料。·IP140:采用如上所述的稀释剂作为参照:主要由C10-C12异链烷烃构成的Isane-140(也称为IP140),所述稀释剂由TotalFluids公司销售并且符合以上限定的轻质惰性稀释剂。·氢化ULSD:在常规氢化方法中从氢化的起始新鲜原料中获得的氢化流出物。表1示出了新鲜ULSD原料和相应的新鲜氢化原料的物化特性。表1表2示出了所使用的稀释剂的主要物化特性。表2表3示出了所测试的不同混合原料中存在的芳族化合物的量及其密度。混合物由35重量%的新鲜ULSD原料和65重量%的稀释剂构成。表3所测试的不同原料之间的芳族化合物的量差异是极小的并且不影响所得结果的分析比较。为了能够以恒定的质量流量工作,已根据本领域技术人员公知的方法使液时空速(LHSV)适应于所测试原料的密度差异。运行条件:中试单元由装载有来自Johnson-Matthey的112mlHTC-700型催化剂的2个串联反应器构成。催化剂等量地分布在2个反应器中,并且与碳化硅SiC0.1mm以50体积%/50体积%的比例混合。根据Johnson-Matthey建议的工序进行催化活化:·在150℃下在氮气N2(80Nl/小时)中干燥1小时(加热速率:60℃/小时)·冷却至低于40℃的温度,然后在50巴的压力下根据以下温度梯段在氢气H2(20Nl/小时至25Nl/小时)中还原:-以60℃/小时的速率:使温度升高至120℃并稳定1小时;-以60℃/小时的速率:使温度升高至230℃并稳定3小时;-在进入稳定化阶段之前冷却至150℃。使用常规炼油厂瓦斯油(例如,来自ZR炼油厂(Zeeland炼油厂)的D0瓦斯油)进行稳定化阶段,并在表4所述的运行条件下保持数天。表4压力(巴)100LHSV(小时-1)1.5H2/HC(Nl/l*)100温度(℃)150*标准升/升表5包括与ULSD原料/氢化ULSD相比的D0原料的物化特性。表5当来自中试单元的流出物中的单环芳族化合物的量(每天测量两次)达到按重量计约11ppm的稳定值时,停止稳定化阶段。然后将不同的原料引入中试单元中,并将温度逐渐升高(5℃/小时)至150℃。表6示出了在处理所测试原料的不同混合物期间应用的运行条件。表6结果:图1和图2示出了在处理USLD原料/氢化ULSD的混合物和ULSD原料/IP140的混合物期间,来自中试单元的流出物中单环芳族化合物的量随时间的变化。在评估在HTC700催化剂上的ULSD原料期间,来自中试单元的流出物的单环芳族化合物逐渐增加,表明催化剂快速地逐渐失活。失活速率可以评估为0.2ppm单环芳族化合物/小时(图1)。相反地,使用Isane-140作为稀释剂,芳族化合物的量随着时间保持稳定并且非常低。失活速率可以评估为小于0.01ppm单环芳族化合物/小时(图2)。当ULSD原料/氢化ULSD通过时,确认失活(图2)。来自中试单元的流出物中的芳族化合物的量是用IP140稀释原料时的几乎4倍高。ULSD原料/氢化ULSD处理期间的失活速率可以评估为0.3ppm单环芳族化合物/小时,这接近图1中示出的失活速率。这些结果还表明,对于新催化剂或者已经暴露于原料的催化剂,催化失活机理是相同的。实际上,对于图1和图2中的ULSD原料/氢化ULSD获得的曲线的外观是相同的。不受理论的束缚,认为作为焦炭前体的某些单环芳族化合物是催化床的失活增加的部分原因。IP140与氢化ULSD之间的主要差异是在后者中存在残留的单环芳族化合物(按重量计约560ppm)。这些化合物被认为是难处理的,因为其在单元中不发生氢化。因此,怀疑失活具体是由待处理原料中包含的单环芳族化合物或环烷-芳族化合物的量引起。这些单环芳族化合物被认为具有成为焦炭前体的强烈倾向。已知焦炭本身能够导致催化床的失活增加。考虑到密度变化对计算结果的影响可忽略不计以及在所有假设的情况下35重量%的ULSD原料贡献约16%的芳族化合物,可以近似地计算出芳族化合物的转化率。用IP140制备的原料的转化率(输出芳族化合物的量在这种情况下为按重量计约25ppm并且通过流出物的单环芳族化合物的UV测量来评估)为:用氢化ULSD制备的原料的转化率(输出芳族化合物的量在这种情况下为按重量计约120ppm并且通过流出物的单环芳族化合物的UV测量来评估)为:因此,使用轻质惰性稀释剂如稀释剂IP140使得不仅可以提高催化剂的稳定性,还可以获得更高的芳族化合物转化率。因此,使用根据本发明的方法大大改善了脱芳构化单元的性能。事实上,难处理的芳族化合物不被再循环到催化段中。事实上,轻质惰性稀释剂不包含芳族化合物。不使用再循环的氢化流出物来稀释新鲜原料,而是使用所描述的惰性轻质溶剂来稀释该新鲜原料。该稀释剂可以容易地通过蒸馏(优选常压或温和的减压蒸馏)与获得的氢化产物分离。因此,考虑到了最终产物中所需的单环芳族化合物的要求而不引起氢化段的催化剂失活增加。在与产物分离之后,使稀释剂再循环到工艺入口。因此,所述方法使得可以处理最初不适合并且不适于生产所寻求的含烃流体的常规炼油厂原料。仅需要对氢化过程进行微小的改变。需要将能够分离惰性轻质稀释剂与最终产物的单件设备添加到氢化段和分馏段的出口。图3是根据一个特定实施方案的方法的图示。当前第1页1 2 3