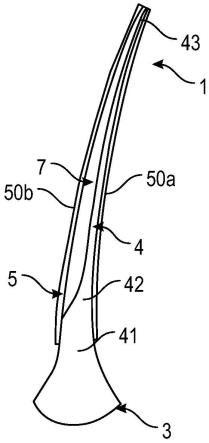
1.本发明涉及飞行器涡轮机的技术领域,飞行器涡轮机例如为涡轮喷气发动机或涡轮螺旋桨发动机。更具体地,本发明涉及一种用于涡轮机的螺旋桨风扇叶片及用于制造用于涡轮机的螺旋桨风扇叶片的方法。
背景技术:2.现有技术尤其包括文献us-a1-2013/039774和ep-a2-2500263。
3.以已知的方式,在护罩式架构的假设中,飞行器涡轮机在气流的方向上从上游到下游包括风扇、低压压缩机、高压压缩机、燃烧室、高压涡轮和低压涡轮。低压压缩机的转子由低压涡轮的转子驱动,高压压缩机的转子由高压涡轮的转子驱动。
4.涡轮机包括在外壳内旋转的转子叶片。这例如是涡轮机的被保持外壳围绕的风扇叶片的情况。这种叶片通常包括根部和桨叶,根部包括侧向面,侧向面连接到桨叶并用于在转子盘的安装壳体中形成支承面。
5.这种叶片被设计成具有良好的机械强度,并且降低了叶片在运行期间发出的噪音,以便优化涡轮机的空气动力学性能。
6.通常,为了改善例如风扇模块及其叶片的空气动力学性能,涡轮机的旁通比(by-pass ratio,bpr)增加。这导致叶片的外径和叶片的跨度的增加。这种大尺寸可以降低这些叶片的一些固有模式,特别是叶片弯曲时的固有频率。这些叶片的固有模式可以通过大大增加形成叶片的壁的厚度来增强。然而,这会显著增加叶片的重量以及涡轮机的总体尺寸。
7.以类似的方式,风扇的厚度的尺寸的这种论证在护罩式架构(风扇叶片)或未带护罩的架构(螺旋桨叶片)、带或不带机械减速器的架构、或“牵引式”(螺旋桨叶片位于涡轮机的前部)配置或“推进式”(螺旋桨叶片位于涡轮机的后部)配置的情况下仍然有效。
8.通常,高弦长叶片的桨叶的外表面(或称为蒙皮)比桨叶的中心部分更多地机械工作。因此,可以设想生产被称为“中空”的叶片,该叶片的桨叶的中心部分可以由更轻的材料(例如,泡沫)制成,从而优化叶片的总质量。然而,该中心部分不具有任何结构刚性,并且在极端运行条件下(例如,摄入固体颗粒),叶片的完整性可能会受到严重影响。
9.本发明针对该问题提出了一种简单、有效且经济的解决方案。
技术实现要素:10.本发明提出了一种用于飞行器涡轮机的风扇或螺旋桨叶片,所述叶片由复合材料制成并包括桨叶和根部,所述根部由翼梁的纵向端部形成,所述翼梁由纤维增强件形成,所述纤维增强件由三维编织的线形成,并且所述翼梁的一部分在所述桨叶的内部延伸,所述桨叶具有由蒙皮限定的空气动力学轮廓,所述蒙皮由编织线形成并且围绕翼梁的所述部分,所述翼梁和所述蒙皮嵌入聚合树脂中。翼梁的所述部分包括突出的纵向加强件,所述纵向加强件在所述纵向加强件之间界定用于容纳由多孔材料形成的纵向插入件的空间。
11.本发明的纵向加强件由类似于具有空气动力学轮廓的桨叶蒙皮的编织线制成,允
许确保在蒙皮和翼梁之间有效且均匀地传递力,而没有任何约束或变形的集中区域。因此,本发明的叶片(特别是具有大弦长的叶片)由于存在由多孔材料制成的纵向插入件而具有较轻的总质量,并且由于存在由复合材料制成的纵向加强件(由树脂致密的纤维增强件)而增强了机械强度。事实上,叶片的刚性增强,以抵抗震动或冲击,例如,抵抗鸟吸入的力。
12.根据本发明的叶片可以包括一个或多个单独或相互结合的以下特征:
[0013]-通过翼梁的线的解开来形成每个加强件;实际上,在每次解开之后,特别是翼梁的经线解开之后,纬线的编织厚度增加,以便在解开处形成过厚。每个解开和过厚允许形成3d编织加强件。
[0014]-所述翼梁的横向厚度从根部朝向翼梁的相对端部减小;
[0015]-所述蒙皮包括至少部分分离桨叶的拱腹壁和拱背壁的解开,特别是在蒙皮的后缘处;
[0016]-所述加强件布置在所述翼梁的部分的拱腹面或拱背面上;
[0017]-所述翼梁包括两个至十二个彼此间隔开的加强件;
[0018]-每个加强件具有可变厚度,特别是在2mm至5mm之间;
[0019]-形成根部的端部在蒙皮的外部延伸;
[0020]-所述叶片包括位于桨叶的边缘中的一个边缘上的保护元件,例如,热塑性聚氨酯薄膜;
[0021]-所述纵向插入件的多孔材料选自型聚合物泡沫、铝泡沫、金属蜂窝和/或型聚合物。
[0022]
本发明还涉及一种用于制造根据本发明的一个实施例的叶片的方法,所述方法包括以下步骤:
[0023]
a)通过三维编织线来生产第一纤维预成型件,第一纤维预成型件称为“翼梁预成型件”;所述预成型件包括被配置为形成叶片根部的纵向端部和被配置为插入叶片桨叶内部的部分;
[0024]
b)通过三维编织或编结线来生产第二纤维预成型件,第二纤维预成型件称为“蒙皮预成型件”;所述蒙皮预成型件被配置为形成空气动力学轮廓;
[0025]
e)将翼梁预成型件布置在蒙皮预成型件内;
[0026]
f)将所述预成型件定位在模具中,然后注入热固性树脂,以获得叶片。
[0027]
根据本发明,在步骤e)和步骤f)之前,所述方法包括以下步骤:
[0028]
a2)在步骤a)中,在翼梁的所述部分上形成多个纵向加强件,并且在加强件之间界定空间,
[0029]
c)生产多孔材料的纵向插入件,
[0030]
d)将所述插入件插入所述翼梁预成型件的所述相应空间中。
[0031]
有利地,在步骤a2)中,通过经线的解开并在所述线解开处增加纬线,来形成所述加强件。
[0032]
优选地,在步骤f)之后,所述方法包括:步骤g),修整叶片,以形成叶片的最终轮廓;和/或步骤h),将加强件粘合到桨叶的边缘中的一个边缘,以形成叶片的后缘和/或前缘。
[0033]
特别地,所述方法的步骤b)包括:子步骤b2),产生经线的解开,例如,在蒙皮预成
型件的后缘侧处。
附图说明
[0034]
从以下通过非限制性示例并参考附图进行的描述中,将更好地理解本发明,并且本发明的其他细节、特征和优点将变得更加清楚,在附图中:
[0035]
[图1]图1是根据本发明的风扇叶片的示意性前视图;
[0036]
[图2]图2是沿着图1的叶片的竖直平面b的示意性截面图;
[0037]
[图3a]图3a是根据第一实施例的包括加强件的沿着图1的叶片的水平平面a的示意性轴向截面图;
[0038]
[图3b]图3b是根据第二实施例的包括加强件的沿着图1的叶片的平面a的示意性轴向截面图;
[0039]
[图4]图4示出了根据本发明的用于制造图1的叶片的方法的连续步骤;和
[0040]
[图5]图5是根据图4的制造步骤中的一个制造步骤的翼梁预成型件的示意性前视图;
[0041]
[图6a]图6a是沿着图5的水平平面d的翼梁预成型件的示意性轴向截面图,其中加强件折叠;
[0042]
[图6b]图6b是图6a的示意性轴向截面图,其中加强件展开;
[0043]
[图7]图7是沿着图5的翼梁预成型件的竖直平面c的示意性截面图。
[0044]
在本技术的附图中,术语“纵向”定义了在图1的轴线或平面b的方向上的延伸。术语“轴向”定义了在图1的轴线或平面a的方向上的延伸。术语“横向”定义了在垂直于图1中的轴线a和轴线b的方向上的延伸。
具体实施方式
[0045]
本发明通常适用于飞行器涡轮机中使用的不同类型的风扇或螺旋桨叶片,飞行器涡轮机例如为飞行器涡轮喷气发动机或涡轮螺旋桨发动机。本发明在大型叶片中具有有利的但非唯一的应用,这些大型叶片由于其尺寸而具有较大的质量,这对涡轮机的总质量具有显著的影响。
[0046]
以传统的方式,在护罩式架构的假设中,涡轮机从上游到下游(即在气流的流动方向上)包括风扇、一个或多个压缩机、燃烧室、一个或多个涡轮以及用于喷射离开一个或多个涡轮的燃烧气体的喷嘴。
[0047]
图1示出了用于安装在涡轮机上的风扇叶片1,该风扇叶片包括:桨叶2和根部3,该桨叶具有用于形成叶片的空气动力学部分的空气动力学轮廓的结构,该根部由较大厚度的部分形成,例如,具有球根状的横截面。空气动力学轮廓桨叶2具有沿轴线a在其前缘20a和后缘20b之间的可变厚度的弯曲轮廓。
[0048]
如图2所示,桨叶2包括拱腹壁50a和拱背壁50b,这两个壁50a、50b形成叶片的外部蒙皮5。这种桨叶蒙皮5可以由浸渍有热固性树脂的编织细丝形成。可以在桨叶的前缘20a和/或后缘20b的区域中添加保护元件90。保护元件90可以是热塑性聚氨酯薄膜。
[0049]
此外,这些壁50a、50b通过翼梁4彼此间隔开。翼梁4包括在蒙皮5的外部延伸并形成叶片根部3的纵向端部41以及布置在桨叶蒙皮5的内部的部分42。翼梁4的厚度可以从根
部的端部41朝向翼梁的相对端部43(即,在叶片的跨度方向上)减小。在相对于叶片的纵向轴线b的横向方向上(当加强件未展开时)测量该厚度(图1)。该端部43布置在叶片桨叶2的顶部。可以通过由三维(3d)编织线制成的纤维预成型件来获得这种翼梁。类似地,可以通过三维编织线来获得蒙皮5。
[0050]
本发明的一个特征在于,翼梁的部分42包括基本上纵向突出的加强件6,加强件在加强件之间界定了用于容纳纵向插入件7的空间8。
[0051]
图3a和3b示出了组装在形成在翼梁的加强件6之间的容纳空间8中的插入件6的两个非限制性示例。用于容纳叶片的空间8可以具有不同的几何形状,这取决于加强件6在桨叶内部的布置。图3a中的加强件6基本上平行于轴线b延伸。图3b中的加强件是倾斜的,从而形成轴向横截面为三角形和梯形的空间8。
[0052]
在示例中,加强件6布置在翼梁4的拱腹面40a上。替代地,根据期望的应用,加强件6也可以布置在翼梁4的拱背面40b上或两个面40a、40b上。
[0053]
每个翼梁4可以具有两个到十二个加强件6。加强件6例如以规则的(图3a)或随机的(图3b)方式彼此间隔开。
[0054]
每个加强件6对于每个翼梁4具有可变的厚度。例如,加强件6的厚度可以在2至5mm之间,优选在3至4.5mm之间。在平行于轴线a、垂直于叶片的轴线b的方向上测量该厚度(图1)。
[0055]
桨叶的蒙皮5的厚度可以在2至5mm之间,优选在3至4.5mm之间。
[0056]
例如,在图4中总结叶片1的制造方法的连续步骤。
[0057]
在步骤a)中,通过3d编织获得纤维翼梁预成型件400。
[0058]
图5至图7非常示意性地示出了旨在形成叶片1的翼梁4的纤维预成型件400。
[0059]
在步骤a1)中,生产3d连续纤维带织物,以形成翼梁预成型件的部分42。该部分42可以具有恒定或可变的厚度。
[0060]
通过提花织机获得翼梁预成型件400的3d编织,在该提花织机上,一束经线或股线已经被布置成多个重叠层,每个层有几百根线(图中未示出),经线被纬线401绑定(图6a和图6b)。一般来说,经线垂直于纬线布置。
[0061]
在所示的示例中,3d编织是“互锁”编织模式。“互锁”织造是指如下的一种编织图案:在该编织图案中,每层纬线绑定几层经线,其中单个纬线列中的所有线在该图案的平面内具有相同的运动。
[0062]
可以使用其他已知类型的3d编织,例如,特别是在申请人的文献wo-a2-2006/136755中描述的那些。该文献特别描述了通过将用于部件的纤维增强结构编织成单件来实现,例如,具有第一类型芯图案和第二类型蒙皮图案的叶片,这允许同时赋予这种类型部件所期望的机械和空气动力学性能。
[0063]
根据本发明的预成型件400可以由碳纤维线编织而成。
[0064]
由于预成型件400是以不同的厚度和宽度编织的,所以没有编织许多经线,从而允许限定预成型件400的轮廓和所需的连续变化的厚度。在申请人的文献ep-a1-1 526 285中描述了一种演进的3d编织的示例,该示例尤其允许在旨在形成前缘的第一边缘和旨在形成后缘的较小厚度的第二边缘之间改变预成型件的厚度。
[0065]
更具体地,在编织的步骤a2)中,在预成型件400内在连续的经线层之间产生解开
403。解开是指纬线没有穿过的区域,纬线将连续的经线层绑在一起。除了在解开处,经线层通过一根或多根纬线的纬线绑在一起。
[0066]
经线的解开403一方面允许形成翼梁的加强件6,另一方面允许在这些加强件6之间产生空间8。这些空间8被配置为接收叶片桨叶内部的插入件7。
[0067]
更具体地,翼梁预成型件是平织的,其中,在每根经线解开之后,纬线的编织厚度增加,以在解开处形成过厚。增加是指纬线没有穿过的局部区域,纬线将连续的经线层绑在一起。因此,每个解开和过厚允许形成3d编织加强件。
[0068]
在3d编织结束时,在步骤a3)中,在编织质量的极限处切割经线和纬线,以提取图5和图6a所示的翼梁预成型件,因为这是从3d编织中发出的。例如,用高压水射流切割加强件的多余长度和/或翼梁预成型件的轮廓(例如,前缘/后缘)。
[0069]
在步骤a4)中,线解开允许展开过厚,从而露出图6b和图7所示的翼梁预成型件上的加强件。
[0070]
应当注意,每个翼梁的一组加强件可以通过不同的3d编织模式形成,特别是根据经线和纬线交织的选择、加强件的数量和位置,以便相对于叶片的期望尺寸通过翼梁的部分加强该加强件的机械强度。
[0071]
应当注意,存在几种可能性来相对于纬线编织股线的路径,以产生翼梁预成型件的部分42和加强件6。在3d编织的可能性中,纬线相对于股线的编织路径可以通过加强件进入,以穿过翼梁预成型件的部分并离开,或者通过翼梁预成型件的部分进入,然后通过加强件离开,或者在穿过翼梁预成型件的部分之后通过加强件进入,并通过另一加强件离开。这允许根据叶片的期望尺寸和刚度提出具有可变加强件的叶片。
[0072]
例如,如果所有纬线都通过翼梁部分进入,特别是在翼梁预成型件的前缘侧上进入,然后通过加强件离开,则纬线的比例朝着预成型件的后缘减小。相反,如果所有纬线都通过加强件进入并穿过翼梁预成型件的部分,则纬线的比例朝着预成型件的后缘增加。
[0073]
在图6a和6b中非常示意性地示出了预成型件400的非排他性3d互锁图案编织模式。具体地,图6a和6b示出了通过解开403a、403b、403c、403a’翼梁预成型件400中的经线而形成的四种类型的加强件6a、6b、6c、6a’。图6a示出了编织的展开的加强件,而图6b示出了展开的加强件。在所示的示例中,不同的纬线绑定经线,以形成翼梁的部分42,该部分在弦的方向上具有恒定的厚度,然后在部分42的四个区域处解开403a、403b、403c、403a’经线。在每个解开处,通过纬线401a、401b、401c绑定翼梁部分42的与解开403a、403b、403c、403a’相邻的部分42a、42b、42c、42a’中的经线层的经线,来实现厚度的增加。特别地,两个加强件6a、6a’由第一纬线401a编织而成,第一纬线通过加强件6a进入,以穿过部分42,并通过加强件6a’离开(反之亦然)。为此,在解开403a、403a’中的一个处添加经线,使得纬线401a可以将这些经线与翼梁的部分42a、42a’的经线层的经线绑定,并且产生3d编织增加。然后,加强件6b由第二纬线401b编织,第二纬线通过加强件6b进入,以穿过部分42,并通过翼梁预成型件的后缘40b离开。为此,也在解开403b处添加经线,使得纬线401b可以将这些经线与翼梁的部分42b的经线层的经线绑定。根据所示的示例,加强件6c由第三纬线401c编织而成,该第三纬线通过翼梁预成型件的前缘40a进入,以穿过部分42,并通过加强件6c离开。为此,纬线401c绑定翼梁的部分42c的经线层的经线,以在解开403c处产生编织增加。
[0074]
图7示出了从端部41穿过部分42朝着翼梁的相对端部43径向延伸的翼梁预成型件
400的正视图。此外,预成型件400包括添加到翼梁预成型件的端部41的叶片根部3以及装配到翼梁预成型件的相对端部43的叶片头部9。
[0075]
制造方法的步骤b)允许生产纤维蒙皮预成型件(图中未单独示出),该纤维蒙皮预成型件用于形成叶片桨叶的空气动力学轮廓。
[0076]
以与上述翼梁预成型件400相同的方式,可以通过借助于提花型织机进行的3d编织来获得蒙皮预成型件,在该提花型织机上,一束经线已经被布置成多层,每层几百根线,经线被纬线绑定。
[0077]
在步骤b1)中,进行3d连续纤维带编织,以形成蒙皮预成型件。
[0078]
在步骤b2)中,可以例如在蒙皮预成型件的后缘侧处产生经线的解开,以便部分地分离蒙皮预成型件的拱腹壁50a和拱背壁50b。特别地,这种解开允许便于将翼梁预成型件400的部分42引入该蒙皮预成型件内部。
[0079]
在3d编织结束时,在步骤b3)中,例如,利用加压水射流,在编织质量的极限处切割经线和纬线,以提取期望的蒙皮预成型件。
[0080]
在叶片成形之前,在步骤c)中生产纵向插入件7。这些插入件7被配置为组装到用于容纳翼梁预成型件400的空间8中。
[0081]
在步骤c1)中,插入件7可被加工成具有与预成型件400的空间8的形状相匹配的形状。这些插入件7可以直接通过具有壳体的空间8的形状的模具生产,或者通过传统形式的模具生产,然后这些插入件被切割成与壳体的空间8相对应的形状。插入件可以由蜂窝材料制成,从而不会显著增加叶片的总重量。这种蜂窝材料可以是非结构化的(例如,聚合物泡沫、铝泡沫等)或结构化的(例如,金属蜂窝或类似的聚合物)。选择插入件的形状和厚度,以便于将其放置在翼梁预成型件中,而不损坏翼梁预成型件并且不改变叶片桨叶的最终空气动力学表面。
[0082]
在步骤d)中,插入件7布置在用于容纳翼梁预成型件400的空间8中。优选地,由操作者手动执行该步骤d)。示踪剂可用于引导和控制插入件在翼梁预成型件的容纳空间中的正确定位,而不改变叶片蒙皮的空气动力学表面。
[0083]
在步骤e)中,整合纵向插入件7的翼梁预成型件400被组装在蒙皮预成型件内部,例如,在通过解开蒙皮预成型件的线而形成的空腔中。
[0084]
一旦翼梁预成型件400的部分42已经布置在蒙皮预成型件中,如此形成的纤维预成型件在步骤f)中聚合(或致密化)。优选地,在聚合之前,重新缝合通过解开而分离的蒙皮预成型件的后缘20b。
[0085]
纤维预成型件的聚合可以在单个操作中进行,即,一旦组装,通过同时聚合翼梁和蒙皮预成型件。在这种情况下,这些预成型件用相同的聚合树脂(或基质)致密化。
[0086]
根据本发明的一个变型实施例,翼梁预成型件可以单独与第一树脂聚合,然后如上所述被引入到蒙皮预成型件中,蒙皮预成型件然后与不同于第一树脂的第二树脂聚合。
[0087]
此外,翼梁和蒙皮预成型件可以由具有相同或不同性质的纤维制成的线制成。
[0088]
纤维预成型件的聚合包括由构成树脂的材料填充预成型件的全部或部分体积的孔隙。
[0089]
可以通过树脂传递模塑(resin transfert moulding,rtm)技术获得构成桨叶的复合材料的树脂。根据rtm技术,如上所述,带有布置在蒙皮预成型件内部的插入件的翼梁
预成型件被放置在模具中,其中桨叶的外形具有空气动力学轮廓。包括组装好的预成型件的模具被放置在烘箱中。然后将热固性树脂注入模具中。适用于rtm技术的树脂是公知的,例如,环氧树脂。这些树脂优选地具有低粘度,以便于注入到纤维中。根据叶片必须经受的热机械约束来确定烘箱的温度和/或树脂的化学性质的选择。一旦树脂被注入到预成型件的整个纤维增强件中,树脂就根据rtm技术通过热处理聚合。注入和聚合后,叶片脱模。
[0090]
在步骤g)中,修整叶片,以去除多余的树脂并形成叶片的最终轮廓。
[0091]
最后,在步骤h)中,前缘和/或后缘增强件可以粘合到叶片的相应边缘。保护元件90可以胶合到叶片上,例如,热塑性聚氨酯薄膜。
[0092]
上述不同的步骤允许获得如图1和图2所示的风扇叶片1。因此,该叶片1包括具有由复合材料(由基质致密化的纤维增强件)制成的空气动力学轮廓的桨叶2、具有也由复合材料(由基质致密化的纤维增强件)制成的加强件的翼梁4以及由蜂窝材料制成的插入件。
[0093]
然而,本发明不限于涡轮机的风扇叶片,而是可以应用于涡轮机的其它护罩式(风扇)或未带护罩(螺旋桨)的叶片以及活动(转子)或固定(定子)的叶片。本发明的叶片也可以应用于风力或水力涡轮机领域以及可再生能源领域。