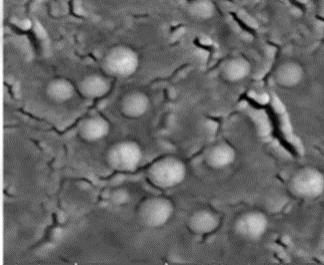
1.本发明属于金属表面处理技术领域,具体涉及一种铝合金表面微弧氧化处理工艺。
技术背景
2.铝及其合金因密度小、比强度高、导热导电性好、易加工成型和回收利用等优点已成为轻量化制造的主要材料,在航空航天、汽车、建筑、电子和包装等工程领域被广泛应用,是使用量仅次于钢铁的第二类金属材料。但由于铝及其合金表面强度低、耐腐蚀和耐磨性能往往不能满足设计要求,尤其是在酸性或者碱性氛围中极易发生腐蚀,制约了铝合金的应用。表面处理是提高铝及其合金的表面硬度、耐蚀耐磨性能和装饰性,延长其使用寿命和扩大应用范围的一个非常重要的手段。
3.铝合金表面着色处理技术不仅能提高铝合金表面的耐蚀耐磨等性能,还同时满足了装饰性需求,近年来受到广泛关注。用传统的着色技术制备的黑色陶瓷膜硬度较低,耐磨性能及耐光老化性能较差,氧化膜容易褪色。而采用微弧氧化技术制备的陶瓷膜具有硬度较高、附着力强、耐腐蚀性较好、色泽稳定、耐光老化性能好等优点,微弧氧化也因此成为一门很有发展潜力的表面着色技术。
4.微弧氧化(mao)又称阳极火花沉积(asd)、等离子体氧化(mpo)或火花放电阳极氧化(anof),还有人称为等离子增强电化学表面陶瓷化(pecc),是一种在有色金属(al、ti、ta、mg 等) 及其合金表面原位生长陶瓷层的技术。微弧氧化的基本原理就是将有色金属置于电解液中,在强电场作用下溶液中气体电离、金属表面氧化产生等离子体,使基体表面产生微区火花放电斑点,在热化学、等离子体化学、电化学、扩散反应和高温相变等一系列复杂反应的共同作用下生成具有高硬度、高结合强度、耐磨和耐蚀等特点的绝缘性氧化膜。
5.微弧氧化着色技术是利用含有着色盐的电解液,通过微弧氧化技术在有色金属表面原位制备各种颜色陶瓷膜的技术,利用该技术制备的陶瓷膜层色泽稳定、耐光性好、不易褪色且附着力和其它性能也较好。铝合金微弧氧化着色技术无论工艺还是性能方面,相比传统的铝合金着色技术都具有更大的优势,是铝合金着色处理的新方向。尽管国内外对微弧氧化工艺做了大量的研究,特别是对微弧氧化陶瓷膜结构、性能的影响因素的研究,但对微弧氧化着色技术的研究却不多,目前对铝合金微弧氧化着色的研究主要包括以下几个方面:
①
通过选择不同的着色盐或添加剂,改变电解液组分、浓度来制备出不同颜色的膜层;
②
研究电解液组分、浓度等对铝合金着色工艺和膜层性能的影响等;
③
研究电参数如电压、电流密度和氧化时间等对膜层颜色、膜层性能(如耐磨性、耐蚀性和耐光性等)的影响。
6.
技术实现要素:7.基于上述微弧氧化电解着色的内容,本发明提供了一种高性能铝合金表面处理工
艺,通过预先在氧化膜孔道内沉积v2o5纳米球颗粒,然后进行微弧氧化着色处理,获得的微弧氧化膜的呈现黑绿色氧化膜,氧化膜颜色均匀,色差小,获得的铝合金微弧氧化膜硬度、耐腐蚀性等物化性质优良,具体如下:一种高性能铝合金表面处理工艺,包括如下处理步骤:(1)制备纳米圆球状钒氧化物悬浮液水溶液:(a)将3-5g钒酸钠加入到双氧水溶液中,40-45℃下磁力搅拌10-20min获得0.1-0.3m的钒酸钠溶液,降至室温;(b)使用硝酸溶液调节钒酸钠溶液的ph为2.9-3.2,然后加入0.7-0.9g的聚乙烯吡咯烷酮,继续搅拌30-40min,获得前驱体溶液;(c)将获得的前驱体溶液放置于水热反应釜中,然后以5℃/min升温至150-160℃,恒温保存24-26h后,自然冷却;在升温前,预先使用高纯氧气排空所述水热反应釜,(d)使用去离子水过滤洗涤,获得褐色的3-5g/l的钒氧化物悬浮液水溶液;(2)阳极氧化处理:对铝材进行表面预处理,将经过表面预处理的作为阳极,以0.3m的草酸溶液为电解液,温度20℃,电压20v下阳极氧化处理15min,获得阳极氧化膜,将阳极氧化处理后的铝材进行氮气烘干处理;(3)浸泡处理:将获得的阳极氧化铝材置于钒氧化物悬浮液水溶液,进行超声搅拌和静置间歇处理,将浸泡处理后的铝材进行氮气烘干处理;(4)微弧氧化处理:电解液包括有硅酸钠8-9g/l,铝酸钠4-5g/l,氢氧化钠5-6g/l,氟化钾8-10g/l,钒酸铵0.3-0.4 g/l;(5)后处理。
8.进一步的,纳米圆球状钒氧化物的尺寸为5-15nm。
9.进一步的,阳极氧化的膜厚度为1-2μm,孔径40-50nm。
10.进一步的,所述超声搅拌和静置间歇处理中的超声搅拌频率为40khz,超声搅拌时间为2min,静置时间为15min,浸泡总时间24-48h,浸泡温度25
±
2℃。
11.进一步的,微弧氧化电解电源为双向脉冲电源,微弧氧化时间:40-60 min,正向电压:350-400v,负向电压:40-60v,正向脉冲占空比为40-50%,负向脉冲占空比为10%-20%,脉冲频率:300-400hz,微弧氧化温度为10-15℃。
12.进一步的,后处理为冲洗烘干、水热封孔或疏水修饰中的一种。
13.本发明首先采用水热法制备球形的钒氧化物,所述氧化物颜色为褐色,主要成分为v2o5,包括但不限于vo2或v2o3,通过水热处理获得的钒氧化物的尺寸均匀,颗粒尺寸集中于5-15nm,所述颗粒尺寸小于后续阳极氧化膜孔径的大小,方便后续的钒氧化物沉积在阳极氧化膜的孔道内,如附图1所示。
14.对于铝合金阳极氧化膜的处理过程,本发明预先对铝合金进行表面处理,表面处理包括有机械抛光,脱脂脱油和活化处理,主要目的在于获得无油无脂无氧化膜的洁净氧化铝结构。
15.对于一次阳极氧化,可以获得均匀的纳米孔道,所述孔道的纳米孔径为孔径40-50nm,所述孔径明显小于前序水热法制备的钒氧化物的颗粒尺寸,为了获得的上述孔径范围,需要对阳极氧化中的参数进行合理的规划,首先电解液,选用草酸,相比于传统的硫酸,草酸在相同条件下获得的孔径更大,如硫酸在温度20℃,电压20v下阳极氧化处理获得的孔
径为14-17nm左右,所述孔径并不利于后续的钒氧化物的沉积,草酸的浓度选择为0.3m,草酸液浓度较高时,氧化铝膜的孔径较大,孔的排列较为规则;草酸液浓度较低时,氧化铝膜的孔径则较小,孔洞排列的有序性也较差。因为随着硫酸浓度的升高,对孔壁的溶解能力增强,在高的氧化电压条件下,氧化铝膜的孔径较大,孔洞排列紧密且比较规则;在低的氧化电压条件下,氧化铝膜的孔径则较小,孔分布的规律性也变差。基于上述认知,本发明采用的阳极氧化膜制备参数为:以0.3m的草酸溶液为电解液,温度20℃,电压20v下阳极氧化处理15min,获得阳极氧化膜,所述阳极氧化膜中的孔道孔径较大,孔壁较薄,阳极氧化膜的厚度适中,如果为了减少阳极氧化膜的电阻对后续微弧氧化膜的影响,可以适当的打磨除去部分阳极氧化膜,用以减少膜层电阻。
16.然后通过后续的浸泡处理:将获得的阳极氧化铝材置于钒氧化物悬浮液水溶液,进行超声搅拌和静置间歇处理,所述超声搅拌和静置间歇处理中的超声搅拌频率为40khz,超声搅拌时间为2min,静置时间为15min,浸泡总时间24-48h,浸泡温度25
±
2℃,通过多次的搅拌和静置,使得水热法制备的钒氧化物能够充分的滞留在阳极氧化膜的孔道内,如附图2所示,该步骤对于后续一步微弧氧化着色的颜色色差有直接的影响,至关重要。
17.然后是微弧氧化着色处理,处理方法为一步微弧氧化处理,处理过程中采用的硅酸钠8-9g/l,铝酸钠4-5g/l,氢氧化钠5-6g/l,氟化钾8-10g/l,钒酸铵0.3-0.4 g/l,微弧氧化电解电源为双向脉冲电源,微弧氧化时间:40-60 min,正向电压:350-400v,负向电压:40-60v,正向脉冲占空比为40-50%,负向脉冲占空比为10%-20%,脉冲频率:300-400hz,微弧氧化温度为10-15℃。一般认为钒酸盐的显色机理是:钒酸盐在微弧氧化放电过程中反应生成 vox,如v2o3等金属氧化物沉积在膜层中。由于钒的氧化物含量的不同,导致膜层的色度变化;且认为随钒酸盐质量浓度的增加,氧化物的沉积量增加,膜层颜色变深,在微弧氧化过程中,钒氧化物来源分别为前期阳极氧化膜孔道中沉积的钒氧化物,以及后续微弧氧化电解液中的钒酸铵,由于微弧氧化过程较为激烈,使得0.3-0.4 g/l钒酸铵氧化形成的v2o5的沉积量较上,且分布不均匀,这就导致出现明显的色差,如色度不均匀,试样边缘颜色较深,中间部分颜色较浅或着色不完全等情况出现,如果直接在微弧氧化液中添加大量的钒酸铵不但会导致无法获得所需的墨绿或者黑绿色的氧化膜,如获得黄绿色的氧化膜,而且电解液中的钒酸铵的浓度过高,会引起局部击穿电压过高,产生破坏性电弧,使得膜层表面质量差,容易出现疏松、孔洞,而且会直接降低微弧氧化膜的硬度和耐腐蚀性,虽然颜色喜好因人而异,但是微弧氧化膜的物化性能下降确实不愿意获得的结果,而预先在孔道内增加适量的钒氧化物,v2o5被还原时,制得一系列低氧化态氧化物,如深蓝色的二氧化钒,黑色的v2o3和vo等,钒的氧化物或化合物与陶瓷膜相结合或附着在表面以及微孔中,使表面呈现一定的颜色,获得本发明所需的黑绿色或者墨绿色。
18.此外,本发明采用双向脉冲微弧氧化,采用双向脉冲获得的膜层光滑,双极脉冲会使膜层表面放电孔洞尺寸变小及孔洞周围的堆积物变少,膜层表面熔融物颗粒变小,膜层的粗糙度降低,膜层表面光滑均匀,如附图3所示,膜层的色差减小,进而获得色度高、色泽均匀、综合性能好的黑色膜。
19.有益技术效果(1)本发明通过预先在一次氧化膜的孔道内加入水热法制备的纳米钒氧化物颗粒,有效的增加了微弧氧化膜中的钒氧化物的含量,可以获得高质量、无色差的微弧氧化
膜。
20.(2)获得的微弧氧化膜的颜色为黑绿色或者墨绿色,色泽度高,硬度好,耐腐蚀性能强。
21.附图说明
22.附图1实施例2中水热法制备获得的球形钒氧化物的tem图。
23.附图2实施例2中将钒氧化物填充到阳极氧化膜孔道内的sem图。
24.附图3实施例2中获得的微弧氧化膜的sem图。
具体实施方式
25.实施例1一种高性能铝合金表面处理工艺,包括如下处理步骤:(1)制备纳米圆球状钒氧化物悬浮液水溶液。
26.(a)将3g钒酸钠加入到双氧水溶液中,40℃下磁力搅拌10-20min获得0.1m的钒酸钠溶液,降至室温。
27.(b)使用硝酸溶液调节钒酸钠溶液的ph为2.9,然后加入0.7g的聚乙烯吡咯烷酮,继续搅拌30min,获得前驱体溶液。
28.(c)将获得的前驱体溶液放置于水热反应釜中,然后以5℃/min升温至150℃,恒温保存24h后,自然冷却;在升温前,预先使用高纯氧气排空所述水热反应釜。
29.(d)使用去离子水过滤洗涤,获得褐色的3g/l的钒氧化物悬浮液水溶液,所述纳米圆球状钒氧化物的尺寸为5-15nm。
30.(2)阳极氧化处理:对铝材进行表面预处理,将经过表面预处理的作为阳极,以0.3m的草酸溶液为电解液,温度20℃,电压20v下阳极氧化处理15min,将阳极氧化处理后的铝材进行氮气烘干处理。
31.(3)浸泡处理:将获得的阳极氧化铝材置于钒氧化物悬浮液水溶液,进行超声搅拌和静置间歇处理,超声频率为40khz,超声时间为2min,静置时间为15min,浸泡总时间24h,浸泡温度25
±
2℃,将浸泡处理后的铝材进行氮气烘干处理。
32.(4)微弧氧化处理:电解液包括有硅酸钠8g/l,铝酸钠4g/l,氢氧化钠5g/l,氟化钾8g/l,钒酸铵0.3 g/l;电解电源为双向脉冲电源,微弧氧化时间:40 min,正向电压:350v,负向电压:40 v;正向脉冲占空比为40%、负向脉冲占空比为10%,脉冲频率:300hz,微弧氧化温度为10℃。
33.(5)后处理:所述后处理为冲洗烘干。
34.实施例2一种高性能铝合金表面处理工艺,包括如下处理步骤:(1)制备纳米圆球状钒氧化物悬浮液水溶液。
35.(a)将4g钒酸钠加入到双氧水溶液中,42.5℃下磁力搅拌15min获得0.2m的钒酸钠溶液,降至室温。
36.(b)使用硝酸溶液调节钒酸钠溶液的ph为3.0,然后加入0.8g的聚乙烯吡咯烷酮,
继续搅拌35min,获得前驱体溶液。
37.(c)将获得的前驱体溶液放置于水热反应釜中,然后以5℃/min升温至155℃,恒温保存25h后,自然冷却;在升温前,预先使用高纯氧气排空所述水热反应釜。
38.(d)使用去离子水过滤洗涤,获得褐色的4g/l的钒氧化物悬浮液水溶液。
39.(2)阳极氧化处理:对铝材进行表面预处理,将经过表面预处理的作为阳极,以0.3m的草酸溶液为电解液,温度20℃,电压20v下阳极氧化处理15min,将阳极氧化处理后的铝材进行氮气烘干处理。
40.(3)浸泡处理:将获得的阳极氧化铝材置于钒氧化物悬浮液水溶液,进行超声搅拌和静置间歇处理,超声频率为40khz,超声时间为2min,静置时间为15min,浸泡总时间24-48h,浸泡温度25
±
2℃,将浸泡处理后的铝材进行氮气烘干处理。
41.(4)微弧氧化处理:电解液包括有硅酸钠8.5g/l,铝酸钠4.5g/l,氢氧化钠5.5g/l,氟化钾9g/l,钒酸铵0.35 g/l;电解电源为双向脉冲电源,微弧氧化时间:50 min,正向电压:375v,负向电压:50 v;正向脉冲占空比为45%、负向脉冲占空比为15%,脉冲频率:350hz,微弧氧化温度为10℃。
42.(5)后处理:所述后处理为冲洗烘干。
43.实施例3一种高性能铝合金表面处理工艺,包括如下处理步骤:(1)制备纳米圆球状钒氧化物悬浮液水溶液。
44.(a)将5g钒酸钠加入到双氧水溶液中, 45℃下磁力搅拌20min获得0.3m的钒酸钠溶液,降至室温。
45.(b)使用硝酸溶液调节钒酸钠溶液的ph为3.2,然后加入0.9g的聚乙烯吡咯烷酮,继续搅拌40min,获得前驱体溶液。
46.(c)将获得的前驱体溶液放置于水热反应釜中,然后以5℃/min升温至160℃,恒温保存26h后,自然冷却;在升温前,预先使用高纯氧气排空所述水热反应釜。
47.(d)使用去离子水过滤洗涤,获得褐色的5g/l的钒氧化物悬浮液水溶液。
48.(2)阳极氧化处理:对铝材进行表面预处理,将经过表面预处理的作为阳极,以0.3m的草酸溶液为电解液,温度20℃,电压20v下阳极氧化处理15min,将阳极氧化处理后的铝材进行氮气烘干处理。
49.(3)浸泡处理:将获得的阳极氧化铝材置于钒氧化物悬浮液水溶液,进行超声搅拌和静置间歇处理,超声频率为40khz,超声时间为2min,静置时间为15min,浸泡总时间48h,浸泡温度25
±
2℃,将浸泡处理后的铝材进行氮气烘干处理。
50.(4)微弧氧化处理:电解液包括有硅酸钠9g/l,铝酸钠5g/l,氢氧化钠6g/l,氟化钾10g/l,钒酸铵0.4 g/l;电解电源为双向脉冲电源,微弧氧化时间: 60 min,正向电压: 400v,负向电压: 60 v;正向脉冲占空比为50%、负向脉冲占空比为20%,脉冲频率:400hz,微弧氧化温度为15℃。
51.(5)后处理:所述后处理为冲洗烘干。
52.对比例1一种高性能铝合金表面处理工艺,包括如下处理步骤:(1)制备纳米圆球状钒氧化物悬浮液水溶液。
53.(a)将4g钒酸钠加入到双氧水溶液中,42.5℃下磁力搅拌15min获得0.2m的钒酸钠溶液,降至室温。
54.(b)使用硝酸溶液调节钒酸钠溶液的ph为3.0,然后加入0.8g的聚乙烯吡咯烷酮,继续搅拌35min,获得前驱体溶液。
55.(c)将获得的前驱体溶液放置于水热反应釜中,然后以5℃/min升温至155℃,恒温保存25h后,自然冷却;在升温前,预先使用高纯氧气排空所述水热反应釜。
56.(d)使用去离子水过滤洗涤,获得褐色的4g/l的钒氧化物悬浮液水溶液。
57.(2)浸泡处理:将获得铝材置于钒氧化物悬浮液水溶液,进行超声搅拌和静置间歇处理,超声频率为40khz,超声时间为2min,静置时间为15min,浸泡总时间24-48h,浸泡温度25
±
2℃,将浸泡处理后的铝材进行氮气烘干处理。
58.(3)微弧氧化处理:电解液包括有硅酸钠8.5g/l,铝酸钠4.5g/l,氢氧化钠5.5g/l,氟化钾9g/l,钒酸铵0.35 g/l;电解电源为双向脉冲电源,微弧氧化时间:50 min,正向电压:375v,负向电压:50 v;正向脉冲占空比为45%、负向脉冲占空比为15%,脉冲频率:350hz,微弧氧化温度为10℃。
59.(4)后处理:所述后处理为冲洗烘干。
60.对比例2一种高性能铝合金表面处理工艺,包括如下处理步骤:(1)阳极氧化处理:对铝材进行表面预处理,将经过表面预处理的作为阳极,以0.3m的草酸溶液为电解液,温度20℃,电压20v下阳极氧化处理15min,将阳极氧化处理后的铝材进行氮气烘干处理。
61.(2)微弧氧化处理:电解液包括有硅酸钠8.5g/l,铝酸钠4.5g/l,氢氧化钠5.5g/l,氟化钾9g/l,钒酸铵0.35 g/l;电解电源为双向脉冲电源,微弧氧化时间:50 min,正向电压:375v,负向电压:50 v;正向脉冲占空比为45%、负向脉冲占空比为15%,脉冲频率:350hz,微弧氧化温度为10℃。
62.(3)后处理:所述后处理为冲洗烘干。
63.如上表,对于单铝合金而言,腐蚀电压为-1.146v,腐蚀电流密度为3.66*10-6
a/cm2,相比于实施例2,对比例1中不设置阳极氧化步骤,这就会导致钒氧化物无法有效的维持到铝材表面,相反会在铝材表面通过范德华力发生简单的吸附,从而导致钒氧化物在表面的团聚,这就导致对比例1中显色的钒氧化物在微弧氧化膜中非均匀分布,色差值为0.79,电解着色效果较差,此外,由于钒氧化物在表面的团聚,导致微弧氧化过程中的电流明显区别,这就导致表面粗糙度较高为1.16μm,耐腐蚀性为3.35*10-7
a/cm2,关于lab值,lab色彩模型是由照度(l)和有关色彩的a, b三个要素组成。l表示照度,相当于亮度,a表示从红色至绿色的范围,b表示从蓝色至黄色的范围,实施例2获得的微弧氧化膜为墨绿色,对比例1获得的微弧氧化膜为偏黄色,对比例2获得的微弧氧化膜为褐色,而对比例2中不设置钒
氧化物的吸附,仅仅是简单的阳极氧化后续进行微弧氧化,获得的色差为正常微弧氧化色差值,为0.38,粗糙度0.97μm和腐蚀电流密度2.58*10-7
均优于对比例1,本发明着色微弧氧化膜的色差为0.12,粗糙度为0.8μm,且耐腐蚀性优良。
64.以上显示和描述了本发明的基本原理和主要特征以及本发明的优点。本行业的技术人员应该了解,本发明不受上述实施例的限制,上述实施例和说明书中描述的只是说明本发明的原理,在不脱离本发明精神和范围的前提下,本发明还会有各种变化和改进,这些变化和改进都落入要求保护的本发明范围内。本发明要求保护范围由所附的权利要求书及其等效物界定。