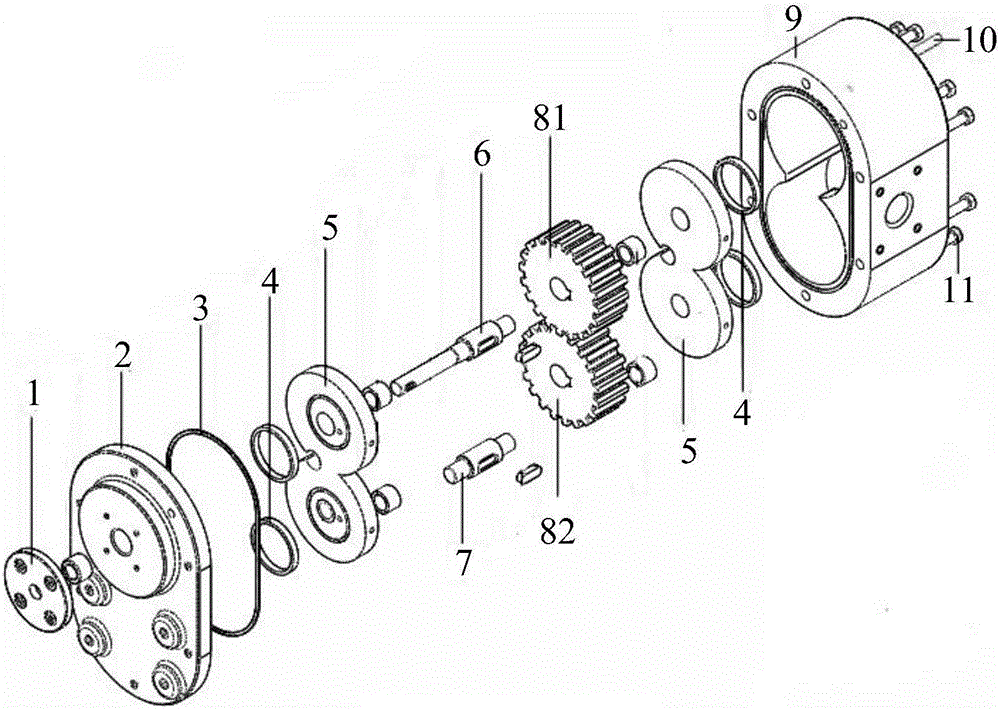
本实用新型涉及外啮合齿轮泵
技术领域:
,特别是涉及一种适用于低/超低粘度介质的外啮合齿轮泵。
背景技术:
:外啮合齿轮泵是一种泵送工作油液的动力工具,因具有价格、可靠性、寿命和自吸能力等方面优势,在常规油类介质应用中相当广泛。在空间狭窄、发射成本高和失重的航天环境下,外啮合齿轮泵因具有结构简单,体小量轻,高可靠性,长寿命,尤其具有良好的自吸性,污染敏感性小,维修方便等方面的特点,近来被认为是部分替代现有航天用泵的较好选择。目前,外啮合齿轮泵在国外航天器尤其国际空间站的水处理系统中得到了采用;同样,液氨外啮合齿轮泵在国外航天器,尤其国际空间站的热控系统中,也被广泛采用。水和液氨的共同特点在于介质的低粘度或超低粘度,当常规油介质类外啮合齿轮泵采用该类低粘度或超低粘度介质时,内泄漏将会大幅增加,从而引起泵容积效率的快速下降和出口压力上不去的问题。外啮合齿轮泵内主要存在四对摩擦副,其中,泵体内表面摩擦副(简称为径向摩擦副,其内的间隙简称为径向间隙,通过径向间隙的泄漏称为径向泄漏)和主、从动齿轮端面摩擦副(简称为轴向摩擦副,其内的间隙简称为轴向间隙,通过径向间隙的泄漏称为轴向泄漏),则主要决定该泵运转时的内部泄漏量,如何减少该类泄漏量是低粘度或超低粘度介质外啮合齿轮泵开发的关键,考虑到介质的低粘度或超低粘度,泵的出口压力一般为≤1MPa的低压,而不像常规油介质类外啮合齿轮泵的出口压力可分为高压(最高可达35MPa)、中压和低压。目前,在固定间隙的外啮合齿轮泵中,小排量泵轴向间隙一般在0.01~0.03mm;大排量泵轴向间隙一般在0.03~0.05mm。径向间隙一般情况下可在0.03~0.1mm之间选取。技术实现要素:本实用新型的目的在于提供一种工作介质从低压区侧向进入,从高压区轴向流出且径向和轴向的总泄漏量小的适用于低/超低粘度介质的流向垂直型外啮合齿轮泵。本实用新型的目的是通过以下技术方案实现的:一种适用于低/超低粘度介质的流向垂直型外啮合齿轮泵,包括泵壳、前盖和后盖,前盖和后盖分别安装在泵壳的两侧形成腔体;腔体内安装有主动齿轮和从动齿轮,主动齿轮和从动齿轮相互啮合构成齿轮副,齿轮副两侧均设有浮动轴套,低压区的泵壳侧壁上设有介质入口,高压区的浮动轴套上开有圆形缺口,后盖上设有与圆形缺口相对应的介质出口,介质出口位于高压区一侧且介质出口的中心与主动齿轮的中心连线距离等于介质出口的中心与从动齿轮的中心连线距离;工作介质通过介质入口进入泵壳内,在齿轮副的带动下从低压区进入高压区,最后通过介质出口流出。所述介质出口为直径为10mm的圆形出口,圆形出口的圆心偏离齿轮副中心连线9.16mm,出口直径ФD和位置H符合外啮合齿轮泵圆形卸荷槽的设计,介质出口即兼具出口侧卸荷槽的作用。所述低压区进口边缘夹角α1为120°,较大的进口边缘夹角可避免低粘度或超低粘度介质因自吸力不足而造成的气穴现象,即减少了过渡区夹角α0,降低了来自过渡区的轴向泄漏;高压区出口边缘夹角α2为26.1°,较小的出口边缘夹角可降低高压区的泄漏,从而使总泄漏量最小化。本实用新型具有以下有益效果:(1)本实用新型的工作介质流向路径为垂直型,即工作介质从低压区侧向进入,从高压区轴向流出,避免了常规高压侧向出口对泵壳强度、刚度的破坏,从而可适当降低泵壳的厚度;(2)本实用新型在齿轮副的两侧均设有浮动轴套,可实现轴向摩擦副间隙的自动补偿,以控制轴向泄漏;(3)本实用新型的介质出口不仅用于介质的流出还兼具卸荷槽的作用;(4)本实用新型的低压区进口边缘夹角较大,高压区夹角较小,有效的降低了总泄漏量。附图说明图1为本实用新型的立体结构图。图2为本实用新型的爆炸图。图3为本实用新型的另一立体结构图。图4为本实用新型的介质进出口尺寸结构示意图。图5为进、出口边缘夹角对容积率的影响示意图。图中标记:1、压盘;2、前盖;3、泵壳密封件;4、浮动轴套外侧密封圈;5、浮动轴套;6主动轴;7、从动轴;81、主动齿轮;82、从动齿轮;9、泵壳;10、定位销;11、固定螺钉;12、后盖;13、介质入口;14、介质出口。具体实施方式如图1~图5所示,本实施例提供的适用于低/超低粘度介质的流向垂直型外啮合齿轮泵包括压盘1、前盖2、密封件3、浮动轴套外侧密封圈4、浮动轴套5、主动轴6、从动轴7、齿轮副、泵壳9、定位销10、固定螺钉11和后盖12,压盘1安装在前盖2上,前盖2和后盖12分别安装在泵壳9的两侧形成腔体,前盖2和后盖12与泵壳9的连接处设有泵壳密封件3,腔体内安装有由主动齿轮81和从动齿轮82相互啮合构成的齿轮副,齿轮副两侧均安装有浮动轴套5,浮动轴套5的外侧安装有浮动轴套外侧密封圈4,主动轴6依次穿过压盘1、前盖2、泵壳密封件3、浮动轴套外侧密封圈4和浮动轴套5与齿轮副的主动齿轮81连接,从动轴7与齿轮副的从动齿轮82连接,后盖12通过固定螺钉11固定在泵壳9上,后盖12上安装有定位销10。所述介质入口13设置在低压区泵壳9的侧壁上,介质通过介质入口13进入泵壳9内,在齿轮副的带动下从低压区进入高压区,高压区的泵壳9与齿轮副为全齿密封,高压区的浮动轴套5上开有圆形缺口,后盖12上设有与圆形缺口相对应的介质出口14,介质出口14位于高压区侧并且介质出口14的圆心与主动齿轮81的轴心连线距离等于介质出口14的圆心与从动齿轮82的轴心连线距离;介质最后通过介质出口14流出;介质入口13与介质出口14构成垂直型流向结构,避免了常规高压侧向出口对泵壳9强度、刚度的破坏,从而可以适当降低泵壳9的厚度,降低泵的重量。所述介质出口14为直径Ф10mm的圆形出口,圆形出口的圆心距离齿轮副中心连线的距离H为9.16mm,出口直径ФD和位置H符合外啮合齿轮泵圆形卸荷槽的设计,介质出口14兼具出口侧卸荷槽的作用。如图4所示,所述低压区进口边缘夹角α1为120°,较大的进口边缘夹角可避免低粘度或超低粘度介质因自吸力不足而造成的气穴现象,即减少了过渡区夹角α0,降低了来自过渡区的轴向泄漏;高压区出口边缘夹角α226.1°,较小的出口边缘夹角可降低高压区的泄漏,从而使总泄漏量最小化。所述齿轮副是由一对具有相同齿形参数的齿轮构成,其参数为:模数3,齿数20,齿顶高系数0.6,压力角15°,变位系数0.0375;齿轮副与过渡区泵壳9采用无减少径向力措施的全齿密封,确保0.05mm径向间隙下的足够密封长度;且具有与轴分开加工,利于更换齿轮和齿轮轴,轴径Ф10mm、齿顶圆直径Ф31.91mm和齿根圆直径Ф27.56mm,确保0.03mm轴向间隙下的足够密封长度。根据现有经实验验证的相关研究理论,得径向摩擦副内的径向泄漏量qa为轴向摩擦副内的轴向泄漏量qz为式中,z为齿数;z0为过渡区齿数;α0为过渡区夹角;Δp为齿轮高低压腔压差,即为出口压力减去进口压力;b为齿宽;μ为流体粘度;ha为径向间隙;hz为轴向间隙;n为工作转速;ra为齿顶圆半径;r为分度圆半径;rs为齿轮轴半径;sa为齿顶圆厚度。如果在泵指定的额定流量qe前提下,只考虑径向泄漏qa和轴向泄漏qz两种流量损失,则泵的容积率λV和泄漏率分项分别为如以模数m,齿数z,齿顶高系数h*,压力角α,变位系数x为设计变量,以λV≥给定容积效率为目标,以及若干约束函数建立优化模型,其中,m∈[2,6],z∈[8,20],x∈[-0.5,0.5],h*∈[0.6,1.25],α∈[15°,35°]。在给定的设计条件Δp=0.4MPa;qe=48L/min;n=3000rpm;ha=0.05mm;hz=0.03mm;液氨粘度μ=0.18mPa·s;顶隙系数0.25;rs=10mm;α1=80°和α2=50°;下的优化结果如表1所示。表1优化结果m/mmZα/°xh(*)b/mmqa/L/minqa/L/minλv/%320150.03750.624.410.822.8492.37α1和α2对容积率λV的影响,如表2和图5中的λV(α1)、λV(α2)所示。由图5可见,α1↑时λV(α1)先上升后下降,最大值发生在130°左右,但总体变化幅度不大,因此,较大的α1虽然对泵的容积率影响甚微,却避免了因自吸力不足而造成泵的气穴现象,取α1=120°。但α2↑时λV(α2)↓,且幅度较大,故只能采用较小的进口直径。表2进、出口边缘夹角对应容积率α1,α2/°λV(α1)λV(α2)5092.1292.377092.2691.649092.3790.8511092.4389.9813092.4489.0115092.1887.8817091.8586.5219091.2884.7821090.3479.5323088.7672.62采用与上同样的设计要求,如果按照常规油泵的要求进行优化设计,即不考虑泄漏的问题,仅仅考虑体积最小。则模数为2.5;齿数为11;变位系数0.2329;齿顶高系数为1.2;齿宽为27.58;另取20°的压力角。经计算qa=33.276L/min;qz=10.1516L/min;λV=9.53%,完全不符合容积效率的设计要求。以上所述仅是本实用新型优选的实施方式,但本实用新型的保护范围并不局限于此,任何基于本实用新型所提供的技术方案和发明构思进行的改造和替换都应涵盖在本实用新型的保护范围内。当前第1页1 2 3