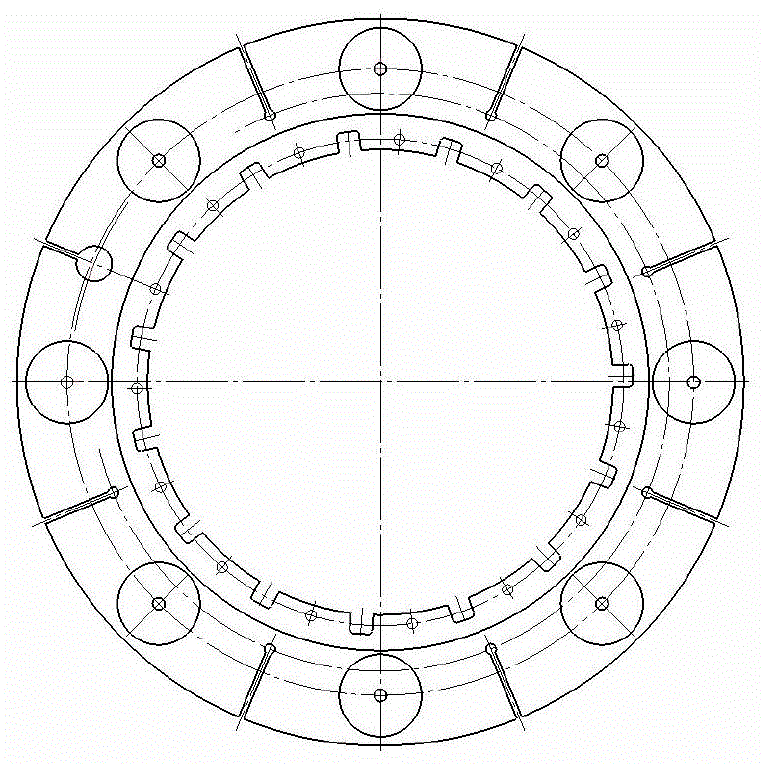
本发明涉及一种航空机轮汽缸座组件的隔热板,属于航空机械
技术领域:
,可用于航空机轮汽缸座组件的隔热或热防护。
背景技术:
:航空机轮在飞机进行着陆刹车、地面滑行时根据需求需进行制动或频繁点刹,当航空机轮刹车能量在大量累积时,刹车盘温度升高,长时间下航空机轮的汽缸座组件会在热量辐射或传导下,导致汽缸座油液温度上升,最终造成汽缸座油液炭化或密封圈失效。因此,需要对汽缸座进行热防护。目前,现有技术中有相关技术方案来解决航空机轮刹车装置汽缸座的热防护问题,但是隔热板结构形式、安装方式和安装部位均与本发明的安装方式和安装部位不同。现有技术中,航空机轮刹车装置或汽缸座组件的隔热措施有两项,在公告号为CN105179385B的专利中公开了一种用于航空刹车机轮的隔热装置,该装置采用不锈钢骨架、不锈钢垫块、不锈钢加强环和铆钉组合而成的隔热板组件,并且隔热板组件安装在刹车盘和刹车装置活塞组件之间。但该隔热装置存在隔热效果差、重量大和结构复杂的缺陷,并且该装置安装在刹车装置活塞组件和刹车盘之间时,占用了航空机轮11刹车盘总厚度的尺寸空间。降低了航空机轮刹车装置的吸热能力,导致航空机轮和汽缸座组件设计温度的升高,降低了刹车盘的可磨损量,缩短了刹车盘的使用寿命。在公开号为CN104895970A的发明创造中公开了一种用于飞机刹车装置的隔热板组件。该隔热板组件采用夹层结构的隔热板组件,使用不锈钢作为骨架,在骨架之间使用隔热材料,且骨架两面使用不锈钢薄板与骨架材料焊接而成。该种结构刹车装置隔热板是安装在汽缸座组件和刹车壳体配合面之间,使用连接汽缸座组件和刹车壳体的螺栓进行固定。由于该热板组件与汽缸座组件直接接触,导致部分热量通过热传导使该汽缸座组件温度上升,从而使汽缸座内的油液温度升高,降低了该隔热板的隔热效果。同时该隔热板组件还存在结构和制造复杂、重量大、安装不方便的缺陷。技术实现要素:为克服现有技术中存在的隔热效果差、结构复杂、重量大、安装不方便的不足,本发明提出了一种隔热板组件。本发明包括隔热板和两个指示杆架。所述两个指示杆架对称的分布在隔热板平面端端面的边缘处,并使该指示杆架中的水平板的下表面与该隔热板的表面贴合,通过该指示杆架中的竖直板与刹车装置中的汽缸座组件固连;所述隔热板的另一个端表面有轴向凸出的加强板,该隔热板的外缘至内缘之间形成的斜面与汽缸座组件安装型面一致。当所述水平板与隔热板平面端的端表面固连后,该水平板的边缘与该隔热板外圆的边平齐。隔热板和汽缸座组件之间的间隙为5~6mm。所述指示杆架由相互垂直的水平板和竖直板组成。在该水平板上分布的连接孔与隔热板是的条形孔的位置相适应;在该水平板上有刹车盘磨损指示杆过孔。所述指示杆架的总高度为22.5mm。在隔热板盘面的外缘处对称的分布有两组条形通孔,并且两组条形通孔中各通孔宽度方向的中心线相互平行并空间垂直于该隔热板轴线所在的垂直面;所述各所述条形通孔的长度为7mm,宽度为5.2mm。本发明安装在航空机轮刹车装置的汽缸座组件上,用于防止航空机轮吹风降温时,由于汽缸座在大量的刹车装置热量的直接热交换或热辐射,导致刹车装置汽缸座内油液温度快速上升,超出标准规定,最终导致汽缸座油液炭化或刹车装置汽缸座密封圈失效。隔热板包含与汽缸座活塞数量相同的孔,保证活塞组件与隔热板组件之间不干涉。通过对称分布在隔热板外边缘两侧的条形孔调整隔热板与指示杆架之间的位置,以弥补指示杆架上的螺纹孔与隔热板上条形孔沿汽缸座平面的尺寸累积安装误差。与现有技术相比,本发明的隔热板组件结构简单,重量不足0.4kg。并且该隔热板组件通过两处指示杆架支撑,并分别使用螺钉进行固定,安装拆卸方便。由于隔热板组件组成零件少、安装和拆卸便捷,外场换装时,仅需拆除外场刹车装置的指示杆架,重新更换本发明的指示杆架,不影响外场的刹车装置布局,实现了原位安装。本发明以最小的重量代价和最简便的安装方式提出了航空机轮汽缸座热防护的解决方案。本发明将隔热板组件安装在汽缸座组件上,通过隔热板阻挡来自刹车装置的热量,避免刹车装置热量直接同汽缸座组件接触,阻隔热量的直接热传导和热辐射,降低汽缸座组件内油液温度。在航空领域中,为减轻航空器的起飞重量,提高经济性能,往往对航空器的各零部件有较为严格的重量控制。本发明所提出的用于航空机轮汽缸座组件的隔热板组件与现有技术的隔热板组件进行对比,本发明的隔热板采用更少的零件,同时使用铝制材料来减轻隔热板组件重量,实现了良好的热防护性能,间接降低某飞机的重量,实现了良好的经济性。具体重量对见表1表1现有技术与本发明重量对比表现有技术1现有技术2本发明1.1kg1.6kg0.4kg本发明所提出的用于航空机轮汽缸座组件的隔热板组件已经完成了不同工况的动力试验和温度测试工作,通过试验发现,航空机轮刹车装置在安装隔热板组件后,汽缸座组件油液温度较未安装隔热板组件时,降低了约25~35℃,热防护效果明显。公告号为CN105179385B的专利中提出的用于航空刹车机轮的隔热装置由于安装在汽缸座活塞组件和刹车盘之间,且安装方式不能限制隔热板沿轴向的位置,导致隔热装置在长期的振动、冲击以及加速度环境使用下,易造成隔热装置的变形或损坏。且隔热板在使用刹车冷却风扇进行刹车冷却降温时,不能阻隔刹车装置热量和汽缸座之间的热传导,降温效果不明显,仅降低约10~20℃。公开号为CN104895970A中提出的用于飞机刹车装置的隔热板组件在进行刹车冷却降温时,由于设计的隔热板在安装部位周围区域同汽缸座紧密贴合,在进行刹车冷却吹风降温时,当大量热量吹向隔热板时,造成隔热板与汽缸座贴合部位温度快速上升,最终造成降温约20至25℃。与所述航空刹车机轮的隔热板组件相比,本发明的热防护效果可使汽缸座降温25~35℃,且重量仅为所述航空机轮隔热板组件重量的25%。所述航空刹车机轮的隔热板组件由于沿圆周方向在隔热板内圆部位进行固定,且隔热板组件直径较大,隔热板外圆部位无固定,因此仅能承受飞机着陆过程中6g的冲击和振动载荷,在较大振动和冲击载荷下,容易造成隔热板组件的变形和断裂。本发明所提出的用于航空机轮汽缸座组件的隔热板组件安装在汽缸座组件上,避免了隔热板组件安装在刹车装置活塞组件和刹车盘之间时,占用航空机轮11刹车盘总厚度的尺寸空间。隔热板组件安装在汽缸座组件时,刹车装置可以使用隔热板组件安装在刹车装置活塞组件和刹车盘之间时的尺寸空间增加刹车盘总厚度,提高航空机轮刹车装置的吸热能力,降低航空机轮和汽缸座组件的温度,并能够提高刹车盘的可磨损量,延长刹车盘使用寿命。本发明的隔热板为满足20g的冲击、振动和加速度要求,同时满足汽缸座组件的热防护效果和0.5kg的重量要求,本发明的隔热板组件采用了铝合金材料,由于铝合金材料的刚度较差、热传导系数高,在刹车装置进行刹车风扇冷却降温时,铝合金隔热板温升较快,为满足热防护效果,本发明所述隔热板组件通过指示杆架高度的设计,使隔热板组件与汽缸座组件平面之间设计一定的间隙,通过空气的阻隔,并根据气流流动的方向、汽缸座的形状以及隔热板的耐冲击要求,进行了隔热板组件外形的优化,使热空气从刹车盘传递向汽缸座时,将热空气引导出刹车装置汽缸座之外,从而使汽缸座更少的接触热空气,达到汽缸座组件降温的效果。通过仿真计算和试验验证,本发明所述的隔热板较未安装隔热板时,能够降低汽缸座的25~35℃。本发明所述的隔热板组件中的指示杆架重新进行了优化设计,将指示杆架长度增加,增加了隔热板和指示杆架的贴合面积,并在两侧分别通过4个螺钉进行固定,增加了隔热板的安装可靠性。隔热板由于采用铝合金材料,铝合金刚度较差且隔热板直径较大,厚度仅为2mm,为避免承受飞机起飞和着陆过程中20g的冲击、振动和加速度等载荷,将隔热板内侧通过冲压,使隔热板沿圆周方向在外缘水平方向和内缘形成一定角度的斜面,在倾斜部位形成一圈强化带,增强隔热板自身的刚度,并可以导引来自刹车装置的热空气。经过仿真优化计算和试验验证,本发明的隔热板组件能够承受飞机起飞和着陆过程中的20g的冲击、振动和加速度。附图说明图1是现有技术中一种隔热板的结构示意图;图2是现有技术中另一种隔热板的结构示意图;图3是图2的侧视图;图4是本发明的结构示意图;图5是图4的左视图;图6是隔热板组件的结构示意图;图7是图6的A-A向视图;图8是隔热板的结构示意图;图9是图8的侧视图;图10是指示杆架轴测示意图。图中:1.隔热板;2.指示杆架;3.安装螺钉;4.汽缸座组件;5.刹车盘磨损指示杆;6.刹车盘;7.加强板;8.条形通孔;9.刹车盘磨损指示杆过孔。具体实施方式本实施例是安装于某型飞机航空机轮汽缸座组件的隔热板组件,包括隔热板1和两个指示杆架2。所述两个指示杆架对称的分布在隔热板一个平面端端面的边缘处,并使该指示杆架中的水平板的下表面与该隔热板的表面贴合,通过该指示杆架中的竖直板与刹车装置中的汽缸座组件固连;所述隔热板的另一个端表面有轴向凸出的加强板,该隔热板的外缘至内缘之间形成了的斜面与汽缸座组件安装型面一致。当所述水平板与隔热板平面端的端表面固连后,该水平板的边缘与该隔热板外圆的边平齐。隔热板和汽缸座组件之间的间隙为5~6mm。所述隔热板1为环状,采用铝合金材料冲压而成。该隔热板的最大外圆的形状与所配合的汽缸座组件4的外形相同。所述隔热板的一个端表面为平面;所述隔热板的另一个端表面有轴向凸出的加强板7,该隔热板的外缘至内缘之间形成了20°的斜面;该斜面与汽缸座组件安装型面一致。在所述隔热板的端表面上均布有与所述汽缸座组件连接的连接孔,并使各所述连接孔位于隔热板1的最大外圆上。在隔热板盘面上对称的分布有两组条形通孔8,并且两组条形通孔中各通孔宽度方向的中心线相互平行并空间垂直于该隔热板轴线所在的垂直面;每组条形通孔的数量为4个;各所述条形通孔的长度为7mm,宽度为5.2mm;各条形通孔的两端均为半圆形。所述条形通孔均用于指示杆架2的连接固定,并通过调整隔热板与指示杆架之间的位置,以弥补指示杆架2上的螺纹孔与隔热板上条形孔沿汽缸座平面的尺寸累积安装误差。在所述条形孔处的隔热板内表面对称的分布有两个径向的凹槽,用于避让安装在汽缸座组件4上的热电偶。本实施例的指示杆架2采用不锈钢加工而成,由相互垂直的水平板和竖直板组成。所述的水平板与隔热板固连,在该水平板上分布有与隔热板的条形孔相配合的4个M5的螺纹连接孔和一个φ6的刹车盘磨损指示杆过孔9;所述刹车盘磨损指示杆过孔用于通过刹车盘磨损指示杆。所述指示杆架中的竖直板用于与刹车装置6中的汽缸座组件4固连;指示杆架中的水平板与隔热板平面端的端表面固连;当所述水平板与隔热板平面端的端表面固连后,该水平板的边缘与该隔热板外圆的边平齐。本实施例的指示杆架中,水平板的长度为60mm,总高度为22.5mm。当指示杆架高度为22.5mm时,隔热板和汽缸座组件之间设计间隙为5~6mm,以保证热空气在刹车冷却风扇的推动下,使汽缸座组件接受的热辐射和热传导降至理想的设计区域。当前第1页1 2 3