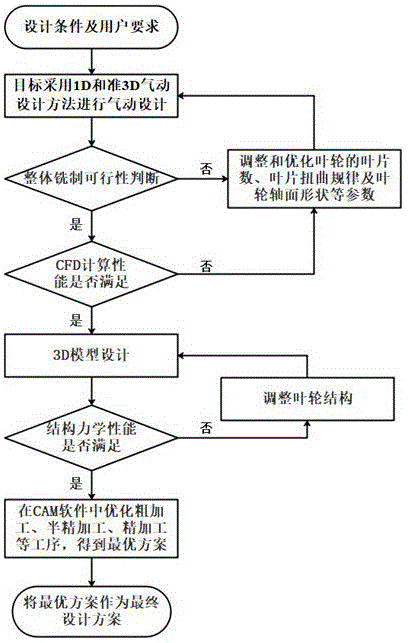
本发明涉及一种用于整体铣制离心压缩机叶轮加工的辅助设计方法,尤其涉及一种整体铣制离心压缩机闭式叶轮的设计方法。
背景技术:
:叶轮机械也称透平机械、涡轮机械广泛地应用于石化、煤化工、天然气、核电、化肥、冶金、环保和其他等行业,在国民经济尤其是整个重工业体系中占有十分重要的地位。越来越多的人认为,叶轮机械的设计制造水平已成为衡量一个国家工业整体实力的最重要标志之一。叶轮作为叶轮机械装置中的“心脏”设备,其性能直接影响到机组整体性能的优劣和可靠性。目前,由于三元闭式叶轮具有效率高、可靠性高的优点,压缩机中大量采用三元闭式叶轮。但是三元闭式叶轮叶片型面复杂,扭曲程度大,通道狭窄,轴盘和盖盘回转面曲率较大,不可避免地在铣削叶间流道的过程容易产生刀具干涉、过切而不能实现流道的整体加工,使叶轮整体铣制困难,因此,传统的闭式叶轮一般采用铣制+焊接的加工方式。该加工方式容易存在局部区域焊接困难或出现焊接缺陷,造成叶轮强度低,加工制造和探伤的难度较大,需要的毛坯材料较多,造成资源浪费,同时还存在加工周期不确定性的风险。随着核电、天然气和石油化工等相关行业对离心压缩机叶轮性能提出越来越高的要求,需要在加工前通过新的设计方法使叶轮气动性能优良、结构可靠稳定、加工制造质量和周期等可控,同时也需考虑尽量降低制造成本和加工周期。技术实现要素:本发明的目的在于提供一种整体铣制离心压缩机闭式叶轮的设计方法,能设计闭式叶轮的多种加工方法,加工时可根据需要选择最优的加工方案,使得通过该方案加工得到的叶轮能同时具有良好的气动性能、强度刚度和加工质量,同时降低加工成本和周期,解决了传统闭式叶轮加工中存在的焊接缺陷、探伤困难以及叶轮性能和加工周期不能保证等问题。本发明是这样实现的:一种整体铣制离心压缩机闭式叶轮的设计方法,包括以下步骤:步骤1:确定闭式叶轮的设计条件和用户要求,通过气动设计得到闭式叶轮的气动几何结构;步骤2:将步骤1中计算得到的闭式叶轮的气动几何结构导入3dcad软件中,并判断闭式叶轮整体铣制的可行性,若可行,则执行步骤3,若不可行,则执行步骤4;步骤3:分析闭式叶轮的气动性能参数,并与用户要求的性能参数进行对比,若气动性能参数符合用户要求,则执行步骤5,若气动性能参数不符合用户要求,则执行步骤4;步骤4:返回步骤1,调整和优化叶轮的气动几何结构;步骤5:将气动性能参数符合用户要求的闭式叶轮的气动几何结构导入3dcad软件中,建立闭式叶轮的3d几何模型;步骤6:对闭式叶轮的3d几何模型进行性能分析,并将3d几何模型的性能参数与用户要求的性能参数进行对比,若3d几何模型的性能参数符合用户要求,则执行步骤7,若3d几何模型的性能参数不符合用户要求,则调整闭式叶轮的气动几何结构,并返回步骤5;步骤7:将通过步骤6校核的3d几何模型导入cam程序中,进行闭式叶轮初加工、半精加工和精加工的工序编制和模拟,并统计每种加工工序的总工时,选择结构可加工性能和气动性能兼顾的加工方案。所述的设计条件和用户要求包括叶片数量、叶片长短、叶片扭曲度、叶片轴面形状、压缩机性能的流量、压比、功率和效率。在所述的步骤1中,闭式叶轮的气动几何结构的计算方法是:闭式叶轮的叶片曲面为m*n贝塞尔曲面,设为贝塞尔曲面的(m+1)*(n+1)个空间点,则闭式叶轮的叶片的m*n贝塞尔曲面定义为:,其中,为n次bernstein基函数;连接点列中相邻两点组成特征网格。在所述的步骤2中,判断闭式叶轮整体铣制可行性的标准是:铣制交接区域的接刀光顺程度,若铣制交接区域的接刀光顺,则符合整体铣制可行性,若铣制交接区域的接刀不光顺,则不符合整体铣制可行性。所述的铣制交接区域的长度大于20mm时,铣制交接区域的接刀光顺,符合整体铣制可行性。在所述的步骤7中,进行半精加工工序的编制和模拟时,半精加工工序后穿插进行固溶热处理。本发明与现有技术相比,具有如下有益效果:1、本发明可以更有效和快速地设计出符合要求的较优闭式叶轮加工方案,并兼顾叶轮的性能和加工周期。2、本发明经设计后确定的最佳加工方案,在气动性能不低的条件下,在加工时仅使用一个叶轮锻件毛坯即可,节省了锻件材料和焊材等材料费用。3、本发明能根据要求选择加工方案,使闭式叶轮能整体铣制,避免了因焊接及其后续热处理等工序造成的质量缺陷,大大提高了闭式叶轮的加工质量。4、本发明能满足闭式叶轮整体铣制的要求,整体铣制得到的叶轮强度和刚度都有保证,并具有更好的耐腐蚀性。5、本发明结合热处理工艺,可以提高刀具寿命和成本,进一步降低叶轮的加工工时和费用。综上所述,本发明在气动设计阶段,在保证满足气动设计流量、压升和效率等设计目标的前提下,通过调整和优化叶轮的叶片数、叶片扭曲规律及叶轮轴面形状等参数,得到了初始的叶轮气动几何结构,然后对其进行cfd分析验证其气动性能是否达到设计要求;通过气动性能考核后,对该气动结构进行3d模型设计,再进行强度和频率等结构力学性能考核;通过考核后将闭式叶轮几何模型导入三维铣制加工软件,进行整体铣制的可加工性能分析,如可行再进行粗加工、半精加工、精加工等详细加工工序参数的分析和优化,为减少加工工时,期间还可能穿插热处理工艺。如此经过几轮循环优化,得到几个能满足气动性能和结构力学性能的要求为约束条件的可行方案,以最少的加工工时为目标函数得到最优的叶轮设计方案。附图说明图1是本发明整体铣制离心压缩机闭式叶轮的设计方法的流程图;图2是贝塞尔曲面图;图3是闭式叶轮从内外两侧进刀加工时的整体铣制可行性判断图。图中,1刀,2闭式叶轮。具体实施方式下面结合附图和具体实施例对本发明作进一步说明。请参见附图1,一种整体铣制离心压缩机闭式叶轮的设计方法,包括以下步骤:步骤1:确定闭式叶轮的设计条件和用户要求,所述的设计条件和用户要求包括叶片数量、叶片长短、叶片扭曲度、叶片轴面形状、压缩机性能的流量、压比、功率和效率等;通过现有技术中1d和准3d气动设计方法,计算得到闭式叶轮的气动几何结构,计算步骤如下:请参见附图2,在步骤1中,闭式叶轮的叶片曲面为m*n贝塞尔曲面,设为贝塞尔曲面(m+1)*(n+1)个空间点,则闭式叶轮的叶片的m*n贝塞尔曲面定义为:,其中,为n次bernstein基函数;连接点列中相邻两点组成特征网格。为了简化叶片曲面,工程上常采用由轮盘(hub)侧和轮盖(shroud)侧组成的曲面来表达叶片曲面。步骤2:将步骤1中计算得到的闭式叶轮的气动几何结构导入现有技术的3dcad软件中,根据拟采用加工的五轴机床行程、主轴头等几何参数从叶轮进口和叶轮出口进行模拟铣制,并根据模拟铣制的交接区域的接刀光顺程度的判断闭式叶轮整体铣制的可行性,若可行,则执行步骤3,若不可行,则执行步骤4。在所述的步骤2中,模拟铣制的交接区域长度大于20mm时,认为该交接区域的接刀光顺程度符合要求,即整体铣制时没有接刀痕。步骤3:运用现有技术的cfd(computationalfluiddynamics,即计算流体动力学)软件分析设计的闭式叶轮的内部流场结构,得到设计的闭式叶轮的气动性能参数,并与用户要求的性能参数进行对比,若设计的闭式叶轮的气动性能参数符合用户要求,则执行步骤5,若设计的闭式叶轮的气动性能参数不符合用户要求,则执行步骤4。步骤4:返回步骤1,调整和优化叶轮的气动几何结构。步骤5:将气动性能参数符合用户要求的闭式叶轮的气动几何结构导入现有技术的3dcad软件中,考虑到闭式叶轮的前后盘结构、与主轴的连接形式、口圈密封等因素,建立闭式叶轮的3d几何模型。步骤6:采用现有技术的有限元方法对闭式叶轮的3d几何模型进行强度刚度和频率性能等分析,并将闭式叶轮的3d几何模型的性能参数与用户要求的性能参数进行对比,若闭式叶轮的3d几何模型的性能参数符合用户要求,即其叶片数量相对较少,叶轮进口附近位置扭曲度较小,进出口开敞性较好,且轴面形状较为平直,则执行步骤7;若闭式叶轮的3d几何模型的性能参数不符合用户要求,则返回步骤5,调整闭式叶轮的气动几何结构并重新建立3d几何模型。请参见附图3,步骤7:将通过步骤6中有限元方法校核的3d几何模型导入现有技术的cam(computeraidedmanufacturing,计算机辅助制造)程序中,进行详细的闭式叶轮初加工、半精加工和精加工等加工工序的编制和模拟,如图3模拟的从内外两侧进刀1的闭式叶轮2的整体铣制可行性判断图,并统计每种加工方法需要的总工时,选择结构可加工性能和气动性能兼顾的加工方案。在进行半精加工工序的编制和模拟时,半精加工工序后穿插进行固溶热处理。由于加工工艺可优化的参数较多,如铣制过程中刀具的进刀量、转速等参数不同对加工工时影响很大,因此,需取不同参数组合,得到多个加工方案并分别计算其加工所需工时,应至少对比4种不同的铣制方案,如表1所示,相对于方案1,方案2至方案4分别改变了叶片数量,且方案4缩短了叶片的前缘位置,相比方案1-3,叶片进口高度扩大了105mm,轴向距离缩短了71mm。表14种不同铣制方案方案1方案2方案3方案4叶片数量1791811在对4种不同铣制方案进行设计时,其气动性能参数如表2所示:表24种方案的叶轮气动性能参数方案1方案2方案3方案4叶片结构17长叶片9长叶片9长叶片+9短叶片11长叶片压差大小大小效率高低高低流道窄宽窄,但进口比方案1开敞宽整体铣制可行性可铣制易铣制可铣制,且比方案1易铣制进口叶片扭曲严重,加工性一般如表2所示,在可加工性方面:方案2最好,方案3次之,方案4较差,方案1最差;在气动性能方面:方案1和方案3比较好,方案2和方案4较差。综上,选取最优方案3。当前第1页12