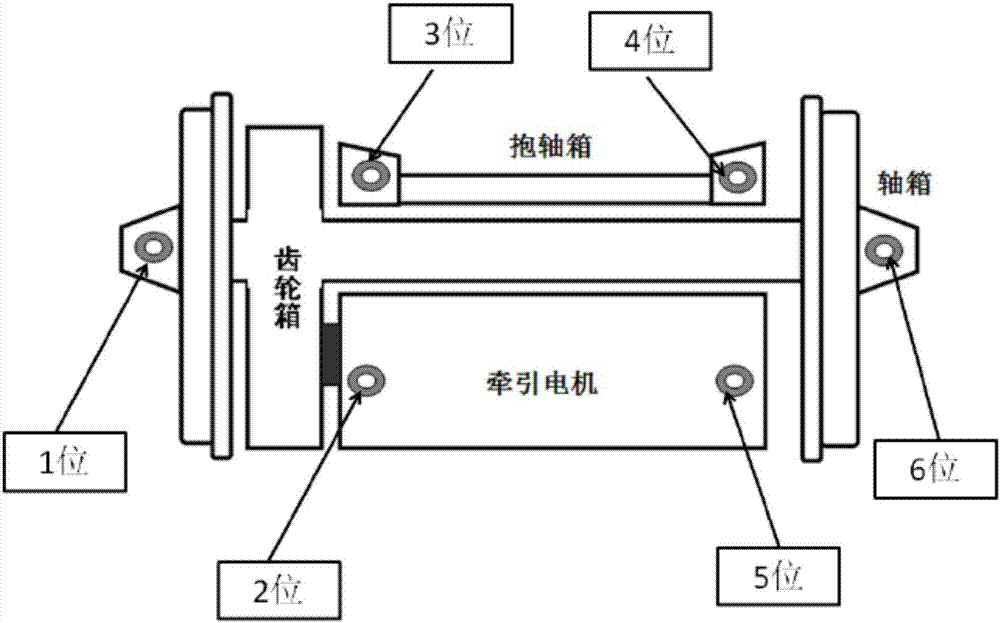
本发明涉及一种轴承监测方法,更具体地,涉及一种铁路机车和动车组转向架轴承在线监测方法。
背景技术:
:机车和动车组转向架轴承监测系统是专门针对转向架轴承(包括电机轴承、抱轴箱轴承、轴箱轴承等)、通过采集各部位轴承的温度和冲击振动信息,对轴承状态进行实时监测的车载系统。如图1所示(以六轴机车为例),机车转向架轴承在线监测系统由中央处理平台、主机监测板卡、数据前置处理器、温度振动复合传感器或(和)温度传感器及连接线组成。其中,主机监测板卡是机车走行部故障监测系统的主要部件,能够实时采集被监测对象的状态数据,进行在线监测诊断,并完成集中显示、报警和数据记录等功能;数据前置处理器安装于机车转向架上,介于系统主机模块与传感器之间,完成信息的预处理及总线传输;温度振动复合传感器或/和温度传感器安装于各部位轴承座上,实现故障冲击、温度两个物理量的复合监测。如何对相关数据进行分析判断,通过技术手段和相关规则提取出能够反应轴承状态的特征值,进而对机车和动车组走行部安全状况作出综合判断,达到故障报警的目的,并避免机车带故障运行,保证运行安全,是转向架轴承监测系统的核心技术。目前机车和动车组转向架轴承监测系统温度报警方式主要有两种:1、绝对值报警方式:指某轴承位置的传感器采集到的温度大于90℃时,监测系统发出报警。2、温升报警方式:指某轴承位置的传感器采集到的温度值比参考温度值高55k时,监测系统发出报警。目前机车和动车组转向架轴承监测系统振动报警方式为评定故障量值(db)法。现有解决铁路机车和动车组转向架轴承在线监测问题的技术方案还存在以下技术问题:1、在绝对值报警方式中,受到环境温度、车型等因素的影响,故障轴承测点温度没有达到绝对值报警的条件,进而导致轴承故障的漏报;2、在温升报警方式中,比较方式是轴承测点温度与位置不同的环境温度相比,由于车速、电机通风状况等外在因素的影响,导致了轴承故障的漏报;3、目前的在线判断方式均为利用一个统一的标准评价所有车辆,而没有根据每辆车的运用工况不同以及车辆自身状态进行比较判断;4、目前的诊断系统只是单纯的设定温度、冲击振动数据的阈值,而未将其结果进行融合形成一个更加科学的结论。技术实现要素:本发明根据铁路机车和动车组的应用特点和故障轴承温度、冲击振动数据的特点,提出多种判断方法,并根据各种判据的判断结果形成了一个综合判断结论,最后根据机车的车速、部件的危害程度提出司机操作方案。本发明提出的铁路机车和动车组转向架轴承在线监测方法,该方法包括:a步骤:采集多个测点位中的一个对应的轴承的温度数据和振动数据;b步骤:利用多种温度判断法得到温度判断结果:其中,x1表示绝对温度法的判断结果,x2表示温升速率法的判断结果,x3表示温度异轴同位法的判断结果,x4表示温度历史比较法的判断结果,x≥1,其中,绝对温度法指根据分别比较多个测点位中的一个对应的轴承在连续多个温度采集周期中的温度与绝对温度阀值的差值来判断轴承的状况;温升速率法是指根据计算多个测点位中的一个对应的轴承在一个温度采集周期中的温度与在上一个温度采集周期中的温度的差值、并且计算连续多个差值中的一个与温升速率阀值的差值来判断轴承的状况;温度异轴同位法是指根据确定多个位号相同的测位点中的每一个对应的轴承中温升速率最小的测点位对应的轴承、并且分别计算其它位号相同的测点位中的一个对应的轴承的温升速率与温升速率最小的轴承的温升速率的差值来判断轴承的状况;和温度历史比较法是指根据计算多个测点位中的一个对应的轴承在连续多个温度采集周期中的温度与特定环境中的历史温度阀值来判断轴承的状况;c步骤:利用多种振动判断法得到振动判断结果:其中,x5表示故障量值法的判断结果,x6表示振动异轴同位法的判断结果,x7表示振动历史比较法的判断结果,x≥1,其中,故障量值法是指根据监测到的多个测点位中的一个对应的轴承的故障量值来判断轴承的状况;振动异轴同位法是指根据确定多个位号相同测点位中的每一个对应的轴承中故障量值最小的轴承、并且分别比较其它位号相同的测点位中的一个对应的轴承的故障量值与故障量值最小的轴承的故障量值来判断轴承的状况;和振动历史比较法是指根据计算特定环境中多个测点位中的一个对应的轴承在连续多个振动采集周期中的故障量值与特定环境中多个测点位中的所述一个对应的轴承的历史故障量值阀值的差值来判断轴承的状况;d步骤:结合温度判断结果和振动判断结果,计算轴承正常、预警/报警的决策函数:e步骤:获得车速诊断函数:其中,y≥1,y≥60;f步骤:获得部件损伤后的危害程度的诊断函数:其中,z≥1;和g步骤:根据上述多个诊断函数获得最终的司机执行方案的决策函数:在本发明的一个实施例中,对多个测点位中的一个对应的轴承的温度数据进行温度循环采集,优选地,温度循环采集的周期为2秒。在本发明的一个实施例中,在b步骤中绝对温度法为:当多个测点位中的一个对应的轴承在连续h个温度循环采集周期内采集到的温度不大于第一绝对温度阀值或者温升不大于第一绝对温升阀值,则轴承正常;当多个测点位中的一个对应的轴承在连续h个温度循环采集周期内采集到的温度在第一绝对温度阀值与第二绝对温度阀值之间或者温升在第一绝对温升阀值与第二绝对温升阀值之间,则发出温度预警;当多个测点位中的一个对应的轴承在连续h个温度循环采集周期内采集到的温度在第二绝对温度阀值与第三绝对温度阀值之间或者温升在第二绝对温升阀值与第三绝对温升阀值之间,则发出i级温度报警;和当多个测点位中的一个对应的轴承在连续h个温度循环采集周期内采集到的温度大于第三绝对温度阀值或者温升大于第三绝对温升阀值,则发出ii级温度报警,优选地,h≥5。在本发明的一个实施例中,在b步骤中温升速率法为:以温度循环采集p次为一个判断周期,判断多个测点位中的一个对应的轴承在连续q个判断周期内的温升速率:如果连续q个判断周期内温升速率均不超过第一温升速率阀值,则轴承正常;如果连续q个判断周期内温升速率均在第一温升速率阀值与第二温升速率阀值之间,则发出温度预警;如果连续q个判断周期内温升速率均在第二温升速率阀值与第三温升速率阀值之间,则发出温度i级报警;和如果连续q个判断周期内温升速率均超过第三温升速率阀值,则发出温度ii级报警,优选地,p≥5,q≥3。在本发明的一个实施例中,在b步骤中温度异轴同位法为:确定多个位号相同的测点位中的每一个对应的轴承中温升速率最小的一个;和分别计算其它位号相同的测点位中的一个对应的轴承的温升速率与温升速率最小的一个的温升速率的差值δvi,根据δvi判断相应轴承的状况:如果在连续m个温度循环采集周期内δvi均没有超过第一异轴同位温升速率阀值,则轴承正常;如果在连续m个温度循环采集周期内δvi在第一异轴同位温升速率阀值与第二异轴同位温升速率阀值之间,则发出温度预警;如果在连续m个温度循环采集周期内δvi在第二异轴同位温升速率阀值与第三异轴同位温升速率阀值之间,则发出i级温度报警;以及如果在连续m个温度循环采集周期内δvi超过第三异轴同位温升速率阀值,则发出ii级温度报警,优选地,m≥3。在本发明的一个实施例中,温度历史比较法中的特定环境包括特定车速v车和特定环境温度t环,在b步骤中温度历史比较法为:建立用于存储特定车速v车和特定环境温度t环下多个测点位中的每一个对应的轴承历史温度数据和历史温度均值的历史温度数据库;周期地更新历史温度数据库,当在一个温度更新周期内多个测点位中的每一个对应的轴承均无故障时,获取所述一个温度更新周期内的环境温度t环、车速v车以及多个测点位中的每一个对应的轴承的温度t更新,使用温度t更新更新所述一个温度更新周期内的环境温度t环和车速v车对应的特定环境温度t环和特定车速v车下的多个测点位中的每一个对应的轴承的历史温度数据和历史温度均值,优选地,温度更新周期为1天;和在一个温度循环采集周期中,比较多个测点位中的一个对应的轴承的温度ti与历史温度数据库中存储的与被比较的测点位对应的历史温度均值,并根据比较的结果判断被比较测点位对应的轴承的状况。在本发明的一个实施例中,历史温度数据库包括多个特定环境温度t环中的每一个与多个特定车速v车组成的多个组合,其中建立历史温度数据库的步骤包括:获取多个测点位中的每一个对应的轴承运行正常的一个温度更新周期内的环境温度t环、车速v车和多个测点位中的每一个对应的轴承的温度t建表;分别比较采集到环境温度t环与多个特定环境温度t环、车速v车与多个特定车速v车,以确定最接近且大于采集到环境温度t环的特定环境温度t环以及最接近且大于采集到的车速v车的特定车速v车;将采集到的温度t建表存储到通过上述比较确定的特定环境温度t环和特定车速v车对应的温度组合;计算对应的温度组合中多个测点位中的每一个的历史温度均值;和记录更新对应的温度组合的温度数据的次数s。在本发明的一个实施例中,历史温度数据库的更新包括以下步骤:在多个测点位中的每一个对应的轴承运行正常的一个温度更新周期内,获取环境温度t环、车速v车以及多个测点位中的每一个对应的轴承的温度t更新;获取与环境温度t环和车速v车对应的多个组合中的一个,称为温度匹配组合;和使用温度t更新更新温度匹配组合中的历史温度均值,公式如下:在本发明的一个实施例中,在多个组合中的每一个中:存储r个温度更新周期中采集的多个测点位中的每一个对应的轴承的温度数据,并且当s=r+i时,用第s次记录的温度数据覆盖温度历史数据库中的第i个数据,优选地,r在[90,100]之间。在本发明的一个实施例中,判断轴承的运行状况的步骤包括:获取环境温度t环、车速v车以及多个测点位中的一个对应的轴承的温度t测;确定与环境温度t环和车速v车对应的多个组合中的一个,称为温度监测匹配组合;和比较温度t测与温度监测匹配组合中与多个测点位中的所述一个对应的轴承对应的历史温度均值z,根据t测-z的值判断:如果在连续w个温度循环采集周期内t测-z的值均小于第一历史温度阀值,则判定轴承正常;如果在连续w个温度循环采集周期内t测-z的值在第一历史温度阀值与第二历史温度阀值之间,则发出温度预警;如果在连续w个温度循环采集周期内t测-z的值在第二历史温度阀值与第三历史温度阀值之间,则发出i级温度报警;以及如果在连续w个温度循环采集周期内t测-z的值均超过第三历史温度阀值,则发出ii级温度报警,优选地,w≥3。在本发明的一个实施例中,对多个测点位中的每一个对应的轴承的故障量值数据进行振动循环采集,优选地,振动循环采集以机车车轮转10圈为一个周期。在本发明的一个实施例中,c步骤中的故障量值法包括以下步骤:获取机车的冲击值sv、多个测点位中的每一个对应的轴承的转速n(r/min)以及多个测点位中的每一个对应的轴承的轴径d(mm),利用以下公式计算故障量值adb:依据故障量值adb大小判断轴承运行状况。在本发明的一个实施例中,c步骤中的振动异轴同位法为:计算多个位号相同的测点位中的每一个对应的轴承中故障量值最小的一个;和分别计算其它位号相同的测点位中的每一个对应的轴承的故障量值与故障量值最小的一个的故障量值的差值δai,根据δai判断:如果在连续m’个振动循环采集的周期内δai均没有超过第一异轴同位振动阀值,则轴承正常;如果在连续m’个振动循环采集的周期内δai在第一异轴同位振动阀值与第二异轴同位振动阀值之间,则发出振动预警;如果在连续m’个振动循环采集的周期δai在第二异轴同位振动阀值与第三异轴同位振动阀值之间,则发出i级振动报警;以及如果在连续m’个振动循环采集的周期内δai超过第三异轴同位振动阀值,则发出ii级振动报警,优选地,m’≥3。在本发明的一个实施例中,振动历史比较法中的特定环境包括特定车速v车’和特定环境温度t环’,在c步骤中振动历史比较法为:建立用于存储特定车速v车’和特定环境温度t环’下多个测点位中的每一个对应的轴承的历史振动数据和历史振动均值的历史振动数据库;周期地更新历史振动数据库,当在一个振动更新周期内多个测点位中的每一个对应的轴承均无故障时,获取所述一个振动更新周期内的环境温度t环’、车速t车’以及多个轴承中的每一个的多个测点位中的每一个的故障量值a,使用故障量值a更新所述一个振动更新周期内的环境温度和车速对应的特定环境温度和特定车速下的多个测点位中的每一个对应的轴承的历史振动均值,优选地,振动更新周期为1天;和在每一个振动循环采集周期中,比较多个测点位中的一个对应的轴承的故障量值a与历史振动数据库中存储的与该轴承的历史振动均值,并根据比较结果判断多个测点位中的所述一个对应的轴承的运行状况。在本发明的一个实施例中,振动数据库包括:多个振动循环采集周期中采集的多个测点位中的每一个对应的轴承的故障量值a;和多个特定环境温度t环’中的每一个与特定车速v车’的多个组合,其中建立历史振动数据库的步骤包括:获取多个测点位中的每一个对应的轴承运行正常的一个振动更新周期内的环境温度t环’、车速v车’和多个测点位中的每一个对应的轴承的故障量值a建表;分别比较采集到环境温度t环’与多个特定环境温度t环’、车速v车’与多个特定车速v车’,以确定最接近且大于采集到环境温度t环’的特定环境温度t环’以及最接近且大于采集到的车速v车’的特定车速v车’;将采集到的温度a建表存储到通过上述比较确定的特定环境温度t环’和特定车速v车’对应的振动组合;计算对应的振动组合中多个测点位中的每一个对应的轴承的历史振动均值;以及记录更新所述对应的振动组合的振动数据的次数s’在本发明的一个实施例中,振动数据库的更新包括以下步骤:在多个测点位中的每一个对应的轴承运行正常的一个振动更新周期内,获取环境温度t环’、车速v车’以及故障量值a更新;比较环境温度t环’、车速v车’与多个组合中的每一个对应的特定环境温度和特定车速,以确定与环境温度t环’、车速v车’最接近的组合,称为振动匹配组合;使用故障量值a更新更新振动匹配组合中的历史振动均值,公式如下:在本发明的一个实施例中,在多个组合中的每一个中:存储r’个振动更新周期中采集的多个测点位中的每一个对应的轴承的振动数据,并且当s’=r’+i时,用第s’次记录的振动数据覆盖历史振动数据库中的第i个数据,优选地,r’在90到110之间。在本发明的一个实施例中,判断轴承的运行状况包括以下步骤:获取环境温度t环’、车速v车’以及多个测点位中的一个对应的轴承的故障量值ai’;比较环境温度t环’和车速v车’与多个组合中的每一个对应的特定环境温度t环’和特定车速v车’,以确定与环境温度t环’和车速v车’最接近的组合,称为振动监测匹配组合;比较故障量值ai’与振动监测匹配组合中与多个测点位中的每一个对应的轴承的历史振动均值a’,根据ai’-a’的值判断:如果在连续w’个循环周期内ai’-a’的值均小于第一历史故障量值阀值,则判定轴承正常;如果在连续w’个循环周期内ai’-a’的值在第一历史故障量值阀值与第二历史故障量值阀值之间,则发出振动预警;如果在w’个循环周期内ai’-a’的值在第二历史故障量值阀值与第三历史故障量值阀值之间,则发出i级振动报警;如果在w’个循环周期内ai’-a’值均超过第三历史故障量值阀值,则发出ii级振动报警,优选地,w’≥3,优选地,第一历史故障量值阀值为6db,第二历史故障量值阀值为10db,第三历史故障量值阀值为15db。在本发明的一个实施例中,当出现温度预警、i级温度报警、ii级温度报警、振动预警、i级振动报警或者ii级振动报警时,分别存储温度数据和振动数据。本发明提出的铁路机车和动车组转向架轴承在线监测方法综合温度数据、振动数据等监测数据判断轴承的运行状况,可以获得更加准确科学的诊断结果;同时结合机车的车速、不同位置的轴承损坏时对机车的行驶的危害程度等给出科学的司机操作方案。另外,本发明针对机车转向架的特点,并且结合机车轴承的累积温度和振动数据,提出了温度历史比较法、振动历史比较法、温度异轴同位比较法和振动异轴同位比较法,使得轴承状况诊断更加准确。附图说明图1为根据本发明一个示例性实施例的铁路机车和动车组转向架轴承在线监测方法所使用的机车转向架轴承在线监测系统的组成示意图;和图2为图1中所示的机车转向架轴承在线监测系统中传感器的安装位置示意图。具体实施方式下文将以铁路机车为例说明本发明公开的铁路机车转向架轴承在线监测方法。详细说明本发明提出的铁路机车和动车组转向架轴承在线监测方法之前需要指出的是,在本发明的一个示例性实施例中采用《机车车载安全防护系统(6a系统)机车走行部故障监测子系统一技术条件》中规定的轴位号以及传感器的安装位置的编号方式。如图2所示,轴位号用两位数字表示传感器在机车测点安装位置上的位置坐标,第一位(十位)表示轴号;第二位(个位)表示位号,0位固定为表示温度传感器;轴号从司机室i开始计算;位号从靠近齿轮箱端轴箱开始计算,以半悬挂单齿轮结构为例,每轴6个测点位,从齿轮箱所在端开始,依次为:1位:齿端轴箱轴承座;2位:齿端电机轴承座;3位:齿端抱轴轴承座;4位:非齿端抱轴轴承座;5位:非齿端电机轴承座;6位:非齿端轴箱轴承座。本发明公开的铁路机车和动车组转向架轴承在线监测方法综合轴承数据的诊断结果、车速以及不同轴承损伤后的危害程度提出司机操作方案,具体地,参照图1和2,本发明提出的方法包括以下步骤。a步骤:采集多个测点位中的每一个对应的轴承的温度数据和振动数据。即,如图1所示,由安装在多个测点位中的每一个上的温度振动复合传感器或/和温度传感器采集温度数据和振动数据,通过数据线将温度数据和振动数据传送到相应的数据前置处理器,然后由主机监测板卡定期从各数据前置处理器采集温度数据和振动数据。b步骤:利用多种温度判断法得到温度判断结果:当i=1时,x1表示绝对温度法的判断结果,其中绝对温度法指根据分别比较多个测点位中的每一个对应的轴承在连续多个温度采集周期中的温度与绝对温度阀值的差值来判断轴承的状况,其中绝对温度阀值是为轴承的不同温度预警/报警级别设定的临界值。根据绝对温度法获得轴承状况并作出轴承正常、温度预警或不同级别的温度报警的判断。当i=2时,x2表示温升速率法的判断结果,其中温升速率法是指根据计算多个测点位中的一个对应的轴承在一个温度采集周期中的温度与在上一个温度采集周期中的温度的差值、并且计算连续多个差值中的一个与温升速率阀值的差值来判断轴承的状况,其中温升速率阀值是为轴承的不同温度预警/报警级别设定的在特定时间周期内温升速率的临界值。根据温升速率法获得的比较结果作出轴承正常、温度预警或者不同级别的温度报警的判断。当i=3时,x3表示温度异轴同位法的判断结果,其中温度异轴同位法是指根据确定多个测点位中多个位号相同的轴承中温升速率最小的测点位对应的轴承、并且分别计算其它位号相同的轴承中的一个对应的轴承的温升速率与温升速率最小的轴承的温升速率的差值来判断轴承的状况。例如,特定测点位为1位,安装在1位的轴承中温升速率最小的轴承是4轴1位,则分别计算其它安装在1位的轴承的温升速率与4轴1位的温升速率的差值。根据温度异轴同位法获得的比较结果分别作出轴承正常、温度预警或者不同级别的温度报警的判断。当i=4时,x4表示温度历史比较法的判断结果,其中温度历史比较法是指根据计算多个测点位中的一个对应的轴承在连续多个温度采集周期中的温度与特定环境中的历史温度阀值的差值来判断轴承的状况,其中历史温度阀值是在多次采集多个测点位中的每一个对应的轴承的温度数据的基础上计算得到的相应轴承的温度数据,可以表征历史上多个轴承中的每一个运行正常的情况下的各轴承的温度临界值。根据温度历史比较法的比较结果作出轴承正常、温度预警或者不同级别的温度报警的判断。在本发明的一个实施例中,特定环境包括特定车速和特定环境温度。其中,x≥1,即,轴承正常、温度预警、i级温度报警以及ii级温度报警所对应的xi的取值具有倍数关系。c步骤:利用多种振动判断法得到振动判断结果:当i=5时,x5表示故障量值法的判断结果,其中故障量值法是指根据监测到的多个测点位中的一个对应的轴承的故障量值来判断轴承的状况。根据故障量值法的结果作出轴承正常、振动预警或者不同级别的振动报警的判断。当i=6时,x6表示振动异轴同位法的判断结果,其中振动异轴同位法是指根据确定多个测点位中多个位号相同的测点位中的每一个对应的轴承中故障量值最小的轴承、并且分别计算其它位号相同的测点位中的一个对应的轴承的故障量值与故障量值最小的轴承的故障量的差值来判断轴承的状况。例如以1位为特定测点位,故障量值最小的是4轴1位对应的轴承,则分别计算其它1位中的每一个对应的轴承的故障量值与4轴1位对应的轴承的故障量值的差值。根据振动异轴同位法中比较得到的结果作出轴承正常、振动预警或者不同级别的振动报警的判断。当i=7时,x7表示振动历史比较法的判断结果,其中振动历史比较法是指根据计算特定环境中多个测点位中的一个对应的轴承在连续多个振动采集周期中的故障量值与特定环境中多个测点位中的所述一个对应的轴承的历史故障量值阀值的差值来判断轴承的状况,其中特定轴承的历史故障量值阀值是在多次采集多该轴承的振动数据的基础上计算得到的振动数据,可以表征历史上多个轴承中的每一个运行正常的情况下的振动故障量值的临界值。根据振动历史比较法的比较结果作出轴承正常、振动预警或者不同级别的振动报警的判断。其中,x≥1,即,轴承正常、振动预警、i级振动报警以及ii级振动报警所对应的xi的取值具有倍数关系。d步骤:结合温度判断结果和振动判断结果,计算轴承正常、预警/报警的决策函数:对于故障轴承来说,早期冲击振动信号反应较为明显,而在中后期冲击振动信号、温度信号均有明显体现。因此,在上述决策函数f(x)1中,仅根据振动数据判断达到报警级别时无需对报警级别进行升级;当根据振动数据和温度数据的判断均达到报警级别或者多项温度判据均达到报警级别时,应对报警级别进行升级。e步骤:获得车速诊断函数:其中,y≥1,即,车速在临界值ykm/h的不同侧时,f(x)2的取值具有倍数关系。ykm/h为车速的临界值,且y≥60,即,当车速≤60km/h时,车速对司机执行方案中的影响较小;当车速>60km/h时,车速对司机执行方案的影响较大。在本发明的一个实施例中,y=60。f步骤:获得部件损伤后的危害程度的诊断函数:其中,z≥1,即,在电机轴承损伤、轴箱轴承损伤以及抱轴箱轴承损伤的情况下f(x)3的取值呈倍数关系。并且由f(x)3的取值可知,电机轴承损伤对机车的危害程度小于轴箱轴承和抱轴箱轴承损伤对机车的危害程度。g步骤:根据上述多个诊断函数获得最终的司机执行方案的决策函数:对于机车转向架的异轴同位轴承,其受载与结构基本相同,因此对于状况良好的轴承,多个异轴同位的温升速率及故障量值相差不大。同时,当机车被分配到某个路局后,其运营路线及环境条件基本不会有较大变化,同一轴承的温度及振动数据也相差不大。基于机车及其转向架轴承的上述特点,本发明提出的根据温度历史比较法、温升速率法、振动历史比较法、温度异轴同位法、振动历史比较法以及振动异轴同位法计算得到的温度预警/报警结果和振动预警/报警结果具有可靠性。进一步地,综合采用温度数据和振动数据的上述判断方法,形成了更加准确科学的轴承状况诊断结果,最终根据车速、不同轴承损伤后的危害程度提出了司机操作方案,使得该方法具有更高的可靠性。在本发明的一个实施例中,当出现温度预警、i级温度报警、ii级温度报警、振动预警、i级振动报警或者ii级振动报警时,分别存储相应的温度数据和相应的振动数据,即冻结报警时的故障数据,这样既保存了报警前的各种故障数据,又不会在正常工况下产生大量的无用数据。下面将以实施例的方式说明采用上述绝对温度法、温升速率法、温度异轴同位法、温度历史比较法、故障量值法、振动异轴同位法和振动历史比较法判断轴承状况的方法。本领域技术人员应当理解的是本发明的实施方式并不限于以下具体实施例。1.绝对温度法主机监测板卡周期性对各前置处理器准备好的温度数据进行循环采集,例如以2s为周期进行循环采集,并将采集到的各测点位温度数据存于表1。例如,n1指第2s时采集的多个测点位中的每一个对应的轴承的温度数据。温度数据按照表1进行循环存储。在本实施例中,存储连续36个循环采集周期中采集的温度数据,即,在第36个的循环采集周期中采集的数据存储到n36后,第37个循环采集周期中采集的温度数据覆盖n1。这样,自动累积并更新温度数据可以充分考虑机车及服役工况的动态门槛值数据,避免一刀切的单一判据,提高报警的准确性和科学性。判断周期温度数据温度数据温度数据温度数据温度数据温度数据温升速率1n1n2n3n4n5n6v12n7n8n9n10n11n12v23n13n14n15n16n17n18v34n19n20n21n22n23n24v45n25n26n27n28n29n30v56n31n32n33n34n35n36v6表1:温度数据存储表当多个测点位中的每一个对应的轴承在连续h个(例如,6个)温度循环采集周期中采集到的温度不大于第一绝对温度阀值或者温升不大于第一绝对温升阀值,则轴承正常。当多个测点位中的每一个对应的轴承在连续6个温度循环采集周期中采集到的温度在第一绝对温度阀值与第二绝对温度阀值之间或者温升在第一绝对温升阀值与第二绝对温升阀值之间,则发出温度预警。当多个测点位中的每一个对应的轴承在连续6个温度循环采集周期内采集到的温度在第二绝对温度阀值与第三绝对温度阀值之间或者温升在第二绝对温升阀值与第三绝对温升阀值之间,则发出i级温度报警。当多个测点位中的每一个对应的轴承在连续6个温度循环采集周期内采集到的温度大于第三绝对温度阀值或者温升大于第三绝对温升阀值,则发出ii级温度报警。同时,当出现温度预警、i级温度报警或者ii级温度报警时,存储报警时的温度数据。其中h≥5。需要说明的,对于运行在不同工况的机车上述第一绝对温度阀值、第一绝对温升阀值、第二绝对温度阀值、第二绝对温升阀值、第三绝对温度阀值以及第三绝对温升阀值的取值不同,可以参考机车运行的具体地理位置的环境温度或者海拔高度等因素确定上述阀值。例如,对于运行在中国东北地区的机车,可以选择第一绝对温度阀值为70℃、第一绝对温升阀值为30k、第二绝对温度阀值为75℃、第二绝对温升阀值35k、第三绝对温度阀值80℃以及第三绝对温升阀值为40k;对于运行在中国南部地区的机车,可以选择第一绝对温度阀值为80℃、第一绝对温升阀值为40k、第二绝对温度阀值为85℃、第二绝对温升阀值45k、第三绝对温度阀值90℃以及第三绝对温升阀值为50k。2.温升速率法以与绝对温度法相同的方式建立表1。以p次(例如,6次)温度循环采集为一个判断周期(即,在n6、n12、n18、n24、n30、n36做温升速率判断,如表1所示),判断多个测点位中的每一个对应的轴承在连续q个(例如,3个)判断周期内的温升速率情况。如表1所示,以v2为例,v2中记录了在第2个判断周期内多个测点位中的每一个的温升速率,并且对于多个测点位中的一个对应的轴承的温升速率的计算公式为使用n12中存储的该轴承的温度值减去n6中存储的该轴承的温度值。如果连续3个判断周期内温升速率均不超过第一温升速率阀值,则轴承正常。如果连续3个判断周期内温升速率均在第一温升速率阀值与第二温升速率阀值之间,则发出温度预警。如果连续3个判断周期内温升速率均在第二温升速率阀值与第三温升速率阀值之间,则发出温度i级报警。如果连续3个判断周期内温升速率均超过第三温升速率阀值,则发出温度ii级报警。在本发明的一个实施例中,p≥5,q≥3,以保证判断结果的准确性。同时,当出现温度预警、i级温度报警或者ii级温度报警时,存储报警时的温度数据。与绝对温度法相同,对于运行在不同工况的机车上述第一温升速率阀值、第二温升速率阀值以及第三温升速率阀值的取值不同,可以参考机车运行的具体地理位置的环境温度或者海拔高度等因素确定上述阀值。例如,对于运行在中国东北地区的机车,可以选择第一温升速率阀值为3k、第二温升速率阀值为4k以及第三温升速率阀值为5k;而对于运行在中国南部地区的机车,可以选择第一温升速率阀值为4k、第二温升速率阀值为5k以及第三温升速率阀值为6k。3.温度异轴同位法以与绝对温度法相同的方式建立表1。计算多多个位号相同的测点位中的每一个对应的轴承中在特定测点位温升速率最小的轴承,例如将多个测点位中的1位作为特定测点位,并且其中温升速率最小的是4轴1位。分别计算其它1位中的每一个对应的轴承的温升速率与4轴1位对应的轴承的温升速率的差值δvi,根据δvi判断相应的轴承的状况。如果在连续m个(例如,3个)温度循环采集的周期内δvi均没有超过第一异轴同位温升速率阀值,则轴承正常。如果在连续3个温度循环采集周期内δvi在第一异轴同位温升速率阀值与第二异轴同位温升速率阀值之间,则发出温度预警。如果在连续3个温度循环采集的周期内δvi在第二异轴同位温升速率阀值与第三异轴同位温升速率阀值之间,则发出i级温度报警。如果在连续3个温度循环采集的周期内δvi超过第三异轴同位温升速率阀值,则发出ii级温度报警。其中,m≥3。同时,当出现温度预警、i级温度报警或者ii级温度报警时,存储预警或报警时的温度数据。与温升速率法相同,对于运行在不同工况的机车,上述第一异轴同位温升速率阀值、第二异轴同位温升速率阀值以及第三异轴同位温升速率阀值的取值不同,可以参考机车运行的具体地理位置的环境温度或者海拔高度等因素确定上述阀值。例如,对于运行在中国东北地区的机车,可以选择第一异轴同位温升速率阀值为1k、第二异轴同位温升速率阀值为2k以及第三异轴同位温升速率阀值为3k;而对于运行在中国南部地区的机车,可以选择第一异轴同位温升速率阀值为2k、第二异轴同位温升速率阀值为3k以及第三异轴同位温升速率阀值为4k。4.温度历史比较法温度历史比较法通过建立适当容量的历史温度数据库,找出不同工况正常运行状态下的温度极限值,实现轴承故障的在线诊断。使用温度历史比较法判断轴承状况包括以下步骤。以与绝对温度法相同的方式建立表1。建立用于存储特定车速和特定环境温度下多个测点位中的每一个对应的轴承的历史温度数据和历史温度均值的历史温度数据库,并且周期地更新历史温度数据库。当在一个温度更新周期内多个测点位中的每一个对应的轴承均无故障时,获取所述一个温度更新周期内的环境温度、车速以及多个测点位中的每一个对应的轴承的温度数据,使用该工况下的温度数据更新所述一个温度更新周期内的环境温度和车速对应的特定环境温度和特定车速下的多个测点位中的每一个对应的轴承的历史温度均值。优选地,温度更新周期为1天。在每一个温度循环采集周期中,比较多个测点位中的一个对应的轴承的温度与历史温度数据库中存储的与该测点位对应的轴承的历史温度均值,并根据比较结果判断被比较的测点位所安装的轴承的状况。在本发明的一个实施例中,历史温度数据库包括多个特定环境温度t环中的每一个与多个特定车速v车组成的多个组合。建立历史温度数据库包括以下步骤。获取一个温度更新周期内的环境温度t环、车速v车和多个测点位中的每一个对应的轴承的温度t建表。分别比较采集到环境温度t环与多个特定环境温度t环、特定车速v车与多个特定车速v车,以确定最接近且大于采集到环境温度t环的特定环境温度t环以及最接近且大于采集到的车速v车的特定车速v车。在本发明的一个实施例中,当采集到的环境温度t环小于或等于特定环境温度t环±1℃时,可以认为t环≤t环;当采集到的车速v车小于或等于特定车速v车±1km/h时,可以认为v车≤v车。将采集到的温度t建表存储到与通过上述比较确定的特定环境温度t环和特定车速v车对应的温度组合。记录更新该对应的温度组合中的温度数据的次数s。以下为根据本发明一个示例性实施例的建立历史温度数据库的方法。建立历史温度数据库并以表格显示特定环境温度中的每一个与特定车速的多个组合,如表2所示,其中针对每个特定环境温度和特定车速的组合存储连续100个温度更新周期内采集的温度数据,其中未显示每个组合中多个测点位中的每一个对应的轴承的温度数据。表2:历史温度数据表表2中每格信息存储特定速度、特定环境温度下多个测点位中的每一个对应的轴承的历史温度均值,以及在计算该历史温度均值之前的温度数据更新次数s。例如z11=[z111、z112…zabc…z165、z166、n11],其中,a表示该历史温度均值在历史温度数据表中的行数,b表示该历史温度均值所表示的测点位所在的轴号,c表示该历史温度均值所表示的测点位的位号。因此,z111表征车速为20km/h、环境温度为-50℃的工况下1轴1位轴承的历史温度均值,z112表征该工况下1轴2位轴承的历史温度均值,z165表征该工况下6轴5位轴承的历史温度均值,n11表征该工况下对z11的更新次数s。历史温度数据库的更新包括以下步骤。在一个温度更新周期内,获取环境温度t环、车速v车以及多个测点位中的每一个对应的轴承的温度t更新。获取与环境温度t环和车速v车对应的多个组合中的一个,称为温度匹配组合。使用温度t更新更新温度匹配组合中的历史温度均值,更新公式为:以下为根据本发明一个示例性实施例的更新历史温度数据库的方法。在第i个温度更新周期内,1轴1位满足车速在19至21km/h、环境温度在-49至-51℃的条件下的最高温度为t111,对z11进行更新,求解公式如下:其中,z111+代表更新后的1轴1位轴承的历史温度均值;z111代表更新前的1轴1位轴承的历史温度均值;n11代表更新前速度为20km/h,环温在-50℃的数据更新次数;t111-i代表在第i个温度更新周期内采集的1轴1位的最高温度。更新之后n11自动加1,完成对z11的更新。进一步地,在多个组合中的每一个中:存储r个温度更新周期中采集的多个测点位中的每一个对应的轴承的温度数据,并且当s=r+i时,用第s次采集的温度数据覆盖历史温度数据库中的第i个数据,优选地,r’在[90,110]之间。即,在温度历史比较法中自动积累并更新典型工况下正常运行的轴承的历史温度数据,提高振动报警的准确性和科学性。下面以1轴1位轴承在特定车速为20km/h,特定环境温度为-50℃的情况为例,当采集次数达到第101次时,1轴1位的轴承的历史温度均值z111的求解公式如下:式中,z111+代表更新后的1轴1位轴承的历史温度均值;z111代表更新前的1轴1位轴承的历史温度均值;t111-101代表第101次温度更新周期内上述工况下的1轴1位轴承的最高温度。当第102次出现上述工况时,则覆盖第2次数据,利用第3次到第102次的温度均值,作为历史判据实现温度的在线诊断。根据本发明的一个示例性实施例,根据历史温度数据判断轴承运行状况的方法包括以下步骤。在一个温度循环采集周期内,获取环境温度t环、车速v车以及多个测点位中的一个对应的轴承的温度t测。获取与环境温度t环和车速v车对应的特定环境温度和特定车速的多个组合中的一个,称为温度监测匹配组合。比较温度t测与温度监测匹配组合中与多个测点位中的所述一个对应的轴承的历史温度均值z,根据t测-z的值判断:如果在连续w个循环周期内t测-z的值均小于第一历史温度阀值,则判定轴承正常;如果在连续w个循环周期内t测-z的值在第一历史温度阀值与第二历史温度阀值之间,则发出温度预警;如果在连续w个循环周期内t测-z的值在第二历史温度阀值与第三历史温度阀值之间,则发出i级温度报警;如果在连续w个循环周期内t测-z的值均超过第三历史温度阀值,则发出ii级温度报警。在本发明的一个实施例中,连续采集的循环周期个数w≥3,以保证判断的准确性。在本发明的一个实施例中,第一历史温度阀值、第二历史温度阀值和第三历史温度阀值的取值可以参考机车运行的具体地理位置的环境温度或者海拔高度等因素确定上述阀值。例如,对于运行在中国东北地区的机车,可以选择第一历史温度阀值为8℃、第二历史温度阀值为10℃以及第三历史温度阀值15℃;对于运行在中国南部地区的机车,可以选择第一历史温度阀值为10℃、第二历史温度阀值为12℃以及第三历史温度阀值17℃。以下为使用表2所示的历史温度数据库判断轴承状况的方法的示例性实施例。在一个温度循环采集周期内,车速为v车km/h、环境温度为t环℃(环境温度取该温度循环采集周期内的两个温度测点的均值),轴承温度为ti时,根据历史温度表找出区间v车∈[v1,v2]、t环∈[t1,t2],如表3所示。根据就近原则,例如v车更加靠近v1,t环更加靠近t1,则将ti与t1进行比较。若在连续w个(例如,3个)温度循环采集周期内对于某一测点位的轴承的温度ti均有ti-t1<t第一历史温度阀值,则判定轴承正常,同时存储该温度循环采集周期内的多个轴承的温度数据;如在连续3个循环采集周期内对某一测点位的轴承的温度ti均有t第一历史温度阀值<ti-t<t第二历史温度阀值,则发出温度预警;若在连续3个温度循环采集周期内对某一测点位的轴承的温度ti均有t第二历史温度阀值<ti-t1<t第三历史温度阀值,则发出i级温度报警;若连续3个温度循环采集周期内对某一测点位的轴承的温度ti均有ti-t1>t第三历史温度阀值,则发出ii级温度报警。表3:车速环境温度表由上述说明可以知道,本发明提出的使用历史温度比较法判断机车轴承的运行状况的方法为不同工况下的机车建立可靠的历史温度数据库,并且自动更新典型工况下正常运行的温度数据,给当前轴承的运行状况的判断提供可靠的判断标准,提高了报警的准确性和科学性。5.故障量值法主机监测板卡周期性对各前置处理器准备好的振动数据进行循环采集,例如以车轮转动10圈周期进行循环采集,并将采集到的各测点位振动数据存于表4。例如,a1指第10圈时采集的多个测点位中的每一个对应的轴承的振动数据。振动数据按照表4进行循环存储,在本实施例中循环存储连续36个振动循环采集周期内采集的多个测点位中的每一个对应的轴承的振动数据,即,在第36个循环采集周期中采集的数据存储到a36后,第37个循环采集周期中采集的振动数据覆盖a1。这样,自动累积并更新振动数据可以充分考虑机车及服役工况的动态门槛值数据,避免一刀切的单一判据,提高报警的准确性和科学性。表4:故障量值存储表故障量值法是指根据监测到的多个测点位中的一个对应的轴承的故障量值判断轴承的运行状况。故障量值(db)的计算公式如下:式中:adb——故障量值;sv——冲击值,表征冲击值大小的物理量,参见《tgjw225-2010机车走行部车载监测装置检修规范》;n——轴承、齿轮、踏面所在轴的转速(r/min);d——轴承、齿轮、踏面所在轴的轴径(mm)。当故障量值达到表5中的值时,发出相应的报警。表5:故障量值判断表6.振动异轴同位法振动异轴同位法是指根据确定多个位号相同测点位中的每一个对应的轴承中故障量值最小的轴承、并且计算其它位号相同的测点位中的一个对应的轴承的故障量值与故障量值最小的轴承的故障量值来判断轴承的状况。以与故障量值法相同的方式建立表4。计算多个位号相同的测点位中的每一个对应的轴承中故障量值最小的轴承,例如将多个测点位中的1位作为特定测点位,其中故障量值最小的是4轴1位。分别计算其它安装在1位的轴承的故障量值与安装在4轴1位的轴承的故障量值的差值δai,根据δai判断相应轴承状况。如果在连续m’个(例如,3个)振动循环采集的周期内δai均没有超过第一异轴同位故障量值阀值,则轴承正常。如果在连续3个振动循环采集的周期内δai在第一异轴同位故障量值阀值与第二异轴同位故障量值阀值之间,则发出振动预警。如果在连续3个振动循环采集的周期内δai在第二异轴同位故障量值阀值与第三异轴同位故障量值阀值之间,则发出i级振动报警。如果在连续3个振动循环采集的周期内δai超过第三异轴同位故障量值阀值,则发出ii级振动报警。其中,m’≥3,以保证判断的准确性。同时,当出现振动预警、i级振动报警或者ii级振动报警时,存储报警时的振动数据。在本发明的一个示例性实施例中,第一异轴同位故障量值阀值为6db、第二异轴同位故障量值阀值为10db、第三异轴同位故障量值阀值为15db。但是本领域技术人员可以理解的是,第一异轴同位故障量值阀值、第二异轴同位故障量值阀值以及第三异轴同位故障量值阀值的取值可以根据机车的具体工况进行确定。7.振动历史比较法振动历史比较法通过建立适当容量的历史振动数据库,找出不同工况正常运行状态下的振动极限值,实现轴承故障的在线诊断。使用振动历史比较法判断轴承状况包括以下步骤。以与绝故障量值法相同的方式建立表4。建立用于存储特定车速和特定环境温度下多个测点位中的每一个对应的轴承的历史故障量值数据和历史振动均值的历史振动数据库。周期地更新历史振动数据库,当在一个振动更新周期内多个测点位中的每一个对应的轴承均无故障时,获取所述一个振动更新周期内的环境温度、车速以及多个测点位中的每一个对应的轴承的故障量值,使用获取的多个测点位中的每一个对应的轴承的故障量值更新所述一个振动更新周期内的环境温度和车速对应的特定环境温度和特定车速下的多个测点位中的每一个对应的轴承的历史故障量值和历史故障量值均值。优选地,振动更新周期为1天。在每一个振动循环采集周期中,比较多个测点位中的一个对应的轴承的故障量值与历史振动数据库中存储的与该测点位对应的轴承的历史振动均值,并根据比较结果判断被比较的测点位安装的轴承的状况。在本发明的一个实施例中,历史振动数据库包括多个特定环境温度t环’中的每一个与多个特定车速v车’组成的多个组合。建立历史振动数据库包括以下步骤。获取一个振动更新周期内的环境温度t环’、特定车速v车’和多个测点位中的每一个对应轴承的故障量值a。分别比较采集到环境温度t环’与多个特定环境温度t环’、特定车速v车’与多个特定车速v车’,以确定最接近且大于采集到环境温度t环’的特定环境温度t环’以及最接近且大于采集到的车速v车’的特定车速v车’。在本发明的一个实施例中,当采集到的环境温度t环’小于特定环境温度t环’±1℃时,可以认为t环’≤t环’;当采集到的车速v车’小于特定车速v车’±1km/h时,可以认为v车’≤v车’。将采集到的故障量值a存储到与通过上述比较确定的特定环境温度t环’和特定车速v车’对应的振动组合。记录更新该对应的振动组合中的振动数据的次数s’。以下为根据本发明一个示例性实施例的建立振动历史数据库的方法。建立历史振动数据库,以表格显示特定环境温度和特定车速的多个组合,如表6所示,其中针对每个特定环境温度和特定车速的组合存储连续100次循环采集的振动数据,并且其中未显示每个组合中多个测点位中的每一个对应的轴承的故障量值。表6:历史振动数据参考表表6中每格信息存储特定车速v车’、特定环境温度t环’下各个传感器的监测的相应轴承的历史故障量值均值,以及每个历史故障量值均值之前的振动数据采集次数,它表征该台机车历史上正常运行时的平均故障量值的均值。例如a11=[a111、a112…a165、a166、n11],其中,a111表征速度20km/h、环温为-50℃工况下1轴1位轴承的历史故障量值均值,a112表征该工况下1轴2位轴承的历史故障量值均值,a165表征该工况下6轴5位轴承的历史故障量值均值,a166表征6轴6位轴承的历史故障量值均值,n11表征该工况下a11的采集数据的次数。历史振动数据库的更新包括以下步骤。在一个振动更新周期内,获取环境温度t环’、车速v车’以及多个测点位中的每一个对应的轴承的振动故障量值a。获取与环境温度t环’和车速v车’对应的多个组合中的一个,称为振动匹配组合。使用故障量值a更新振动匹配组合中的历史振动均值,更新公式为:其中,为1轴1位安装的轴承的更新后的历史振动均值,a111为1轴1位安装的轴承的更新前的历史振动均值,n11为更新前1轴1为安装的轴承的更新次数,a111-i为在该振动更新周期内1轴1位安装的轴承的最大故障量值。进一步地,在多个组合中的每一个中:存储r’个振动更新周期中采集的多个测点位中的每一个对应的轴承的振动数据,并且当s’=r’+i时,用第s’次采集的振动数据覆盖历史振动数据库中的第i个数据,优选地,r’在[90,110]之间。即,在振动历史比较法中自动积累并更新典型工况下正常运行的轴承的历史故障量值,提高振动报警的准确性和科学性。下面以1轴1位轴承在特定车速为20km/h、特定环境温度为-50℃、r’=100的情况为例,当采集次数达到第101次时,1轴1位的轴承的历史故障量值均值a111的求解公式如下:式中,代表更新后的1轴1位轴承的历史故障量值均值;a111代表更新前的1轴1位轴承的历史故障量值均值;a111-101代表第101次振动更新周期内上述工况下的1轴1位轴承的最高故障量值。当第102次出现上述工况时,则覆盖第2次数据,利用第3次到第102次的故障量值均值作为历史判据实现振动的在线诊断。根据本发明的一个示例性实施例,根据历史振动数据判断轴承运行状况的方法包括以下步骤。在一个振动循环采集周期内,获取环境温度t环’、车速v车’以及多个测点位中的一个对应的轴承的故障量值a。获取与环境温度t环’和车速v车’对应的特定环境温度t环’和特定车速v车’的多个组合中的一个,称为振动监测匹配组合。比较故障量值a’与振动监测匹配组合中与多个测点位中的所述一个对应的轴承的历史故障量值均值a’,根据a′-a′的值判断:如果在连续w’个振动循环采集周期内a′-a′的值均小于第一历史故障量值阀值,则判定轴承正常;如果在连续w’个振动循环采集周期内a′-a′的值在第一历史故障量值阀值与第二历史故障量值阀值之间,则发出振动预警;如果在连续w’个振动循环采集周期内a′-a′的值在第二历史故障量值阀值与第三历史故障量值阀值之间,则发出i级振动报警;如果在连续w’个振动循环采集周期内a′-a′的值均超过第三历史故障量值阀值,则发出ii级振动报警。在本发明的一个实施例中,连续采集的循环采集周期个数w’≥3,以保证判断的准确性。在本发明的一个实施例中,第一历史故障量值阀值为6db、第二历史故障量值阀值为10db和第三历史故障量值阀值为15db,但是本领域技术人员应当理解的是,在不同工况第一历史故障量值阀值、第二历史故障量值阀值和第三历史故障量值阀值的取值可以做相应变化。以下为使用表6所示的历史振动数据库判断轴承状况的方法的示例性实施例。在一个振动循环采集周期内,车速为v’km/h、环境温度为t环’℃(环境温度取该振动循环采集周期内的两个振动测点的均值),轴承故障量值为a′时,根据历史振动数据表找出区间v′∈[v1′,v2′]、t环′∈[t1′,t2′],如表7所示。根据就近原则,例如v′更加靠近v1′,t环′更加靠近t1′,则将故障量值a′与a1′比较。若在连续w’个(例如,3个)振动循环采集周期内某一测点位的轴承的故障量值ai′,均有ai′-a1′<a第一历史故障量值阀值时,则判定轴承正常,同时存储该振动循环采集周期内的多个轴承的振动数据;如在连续3个循环采集周期内某一测点位对应的轴承的故障量值ai′均有a第一历史故障量值阀值<ai′-a1′<a第二历史故障量值阀值,则发出振动预警;若在连续3个振动循环采集周期内某一测点位的轴承的故障量值ai′均有a第二历史故障量值阀值<ai′-a1′<a第三历史故障量值阀值,则发出i级振动报警;若连续3个振动循环采集周期内某一测点位位轴承的故障量值ai′,均有ai′-a1′>a第三历史故障量值阀值,则发出ii级振动报警。表7:车速环境振动表由上述说明可以知道,本发明提出的使用历史振动比较法判断机车轴承的运行状况的方法为不同工况下的机车建立可靠的历史振动数据库,并且自动更新典型工况下正常运行的历史振动数据,给当前轴承的运行状况的判断提供可靠的判断标准,提高了报警的准确性和科学性。尽管对本发明的典型实施例进行了说明,但是显然本领域技术人员可以理解,在不背离本发明的精神和原理的情况下可以进行改变,其范围在权利要求书以及其等同物中进行了限定。当前第1页12