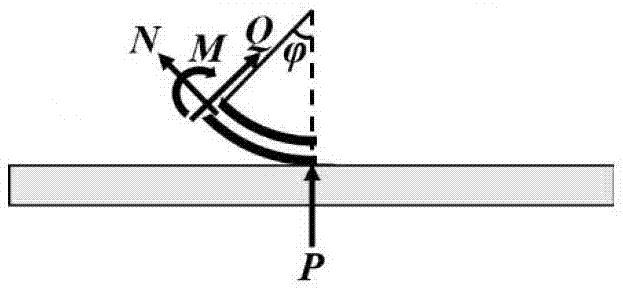
本发明涉及涂层力学性能测试领域,特别是指一种管材涂层弯曲强度测试方法。
背景技术:
管材是常用的工程材料构件形式,例如:锅炉管道、航空航天发动机尾喷管、环形燃烧室、管形火焰筒、枪炮管等。为实现管材构件在服役环境下长时间的安全可靠服役,通常需要在管材表面涂覆保护涂层(耐磨涂层、耐腐蚀涂层、耐高温涂层、隔热涂层等)。弯曲强度作为脆性材料的主要强度指标,其反映了材料对于弯曲载荷的抗力;且强度问题是工程材料实际应用中最根本的问题,是工程构件设计的依据,准确测试管材表面涂层的弯曲强度对于管材涂层复合构件最大承载力设计至关重要。管材表面涂层的弯曲强度是管材复合构件经济安全设计的必需参数,对于确保管材涂层复合构件的服役安全性与可靠性、及其残余寿命预测具有重要意义。目前针对涂层强度的测试方法主要有以下三种:①涂层界面结合强度测试,利用国际标准“iso13124:2011fineceramics(advancedceramics,advancedtechnicalceramics)—testmethodforinterfacialbondstrengthofceramicmaterials”可测得梁试样表面涂层的界面拉伸粘结强度与剪切强度,但是无法适用于管材表面涂层弯曲强度的测试;②剥离后涂层的弯曲强度,即将涂层从基体表面剥离,然后可将涂层视为均质材料,利用三/四点弯曲法即可测得其弯曲强度。该方法仅适用于条/梁状涂层的弯曲强度测试,而无法测得管/环状异形涂层的弯曲强度;且对于厚度较小(几十~几百μm)的涂层,由于弯曲强度的厚度效应会导致测得的弯曲强度值偏大。③块体材料表面涂层弯曲强度测试,利用国际标准“iso19603:2016fineceramics(advancedceramics,advancedtechnicalceramics)—testmethodfordeterminingelasticmodulusandstrengthofthickceramiccoating”仅能测得矩形截面梁试样表面涂层的弯曲强度,而无法应用于管材表面涂层弯曲强度的测试。因此,以上测试方法均不适用于管材涂层弯曲强度的测量。中国专利文献cn106289978a公开了一种测量管材涂层弹性模量的方法,该方法实现了管材表面涂层弹性模量的测试评价,但无法测得管材涂层的弯曲强度。迄今为止尚未提出一种可用于测量管材涂层弯曲强度的方法。技术实现要素:本发明提供一种管材涂层弯曲强度测试方法,本发明能够简单、快捷地测试管材涂层的弯曲强度。为解决上述技术问题,本发明提供技术方案如下:一种管材涂层弯曲强度测试方法,包括以下步骤:利用缺口环压缩试验测得管材外侧涂层与管材基体的弹性模量之比α;对管材外侧涂层-基体缺口环复合试样进行径向压缩试验,直至管材外侧涂层发生开裂破坏,记录管材外侧涂层开裂的临界载荷值pc;通过如下公式计算管材外侧涂层的弯曲强度σc:其中,r0为管材外侧涂层-基体缺口环复合试样横截面的几何轴线曲率半径,h为管材基体厚度,h=r-r,r为管材基体的外半径,r为管材基体的内半径;h为管材外侧涂层的厚度,h=rc-r,rc为管材外侧涂层的外半径;yz为管材外侧涂层-基体缺口环复合试样横截面的中性轴至管材基体内表面的距离,e为管材外侧涂层-基体缺口环复合试样横截面的几何轴线至中性轴间的距离,a为管材外侧涂层-基体缺口环复合试样横截面的面积,a=bh+αbh;b为管材外侧涂层-基体缺口环复合试样的轴向长度。进一步的,所述管材外侧涂层-基体缺口环复合试样通过如下方法制得:对管材外侧涂层表面进行研磨处理;从管材上切取环状试样,所述环状试样的轴向长度与管材厚度之比为1~5,所述环状试样的轴向长度与管材外半径之比为0.2~1.0;对所述环状试样的圆边进行倒角处理;在所述环状试样上制备一个缺口,缺口宽度小于管材的外半径,得到管材外侧涂层-基体缺口环复合试样。进一步的,利用力学试验机对管材外侧涂层-基体缺口环复合试样进行径向压缩试验,加载速率使得管材外侧涂层开裂的时间为3~30s;通过管材外侧涂层-基体缺口环复合试样的载荷-横梁位移曲线或声发射测试装置测得管材外侧涂层开裂破坏的临界载荷值pc;所述管材外侧涂层厚度大于等于20μm。一种管材涂层弯曲强度测试方法,包括以下步骤:利用缺口环压缩试验测得管材内侧涂层与管材基体的弹性模量之比α;对管材内侧涂层-基体闭口环复合试样进行径向压缩试验,直至管材内侧涂层发生开裂破坏,记录管材内侧涂层开裂的临界载荷值pc;通过如下公式计算管材内侧涂层的弯曲强度σc:其中,r0为管材内侧涂层-基体闭口环复合试样横截面的几何轴线曲率半径,h为管材基体厚度,h=r-r,r为管材基体的外半径,r为管材基体的内半径;h为管材内侧涂层的厚度,h=r-rc,rc为管材内侧涂层的内半径;e为管材内侧涂层-基体闭口环复合试样横截面的几何轴线至中性轴间的距离,ρz为管材内侧涂层-基体闭口环复合试样横截面中性轴的曲率半径,a为管材内侧涂层-基体闭口环复合试样横截面的面积,a=bh+αbh;b为管材内侧涂层-基体闭口环复合试样的轴向长度。进一步的,所述管材内侧涂层-基体闭口环复合试样通过如下方法制得:对管材内侧涂层表面进行研磨处理;从管材上切取环状试样,所述环状试样的轴向长度与管材厚度之比为1~5,所述环状试样的轴向长度与管材外半径之比为0.2~1.0;对所述环状试样的圆边进行倒角处理,得到管材内侧涂层-基体闭口环复合试样。进一步的,利用力学试验机对管材内侧涂层-基体闭口环复合试样进行径向压缩试验,加载速率使得管材内侧涂层开裂的时间为3~30s;通过管材内侧涂层-基体闭口环复合试样的载荷-横梁位移曲线或声发射测试装置测得管材内侧涂层开裂破坏的临界载荷值pc;所述管材内侧涂层厚度大于等于20μm。一种管材涂层弯曲强度测试方法,包括以下步骤:利用缺口环压缩试验测得管材两侧涂层与管材基体的弹性模量之比α;对管材两侧涂层-基体缺口环复合试样进行径向压缩试验,直至管材外侧涂层发生开裂破坏,记录管材外侧涂层开裂的临界载荷值pc;通过如下公式计算管材两侧涂层的弯曲强度σc:其中,r0为管材两侧涂层-基体缺口环复合试样横截面的几何轴线曲率半径,h为管材基体厚度,h=r-r,r为管材基体的外半径,r为管材基体的内半径;h1为管材外侧涂层的厚度,h1=rc-r,rc为管材外侧涂层的外半径;h2为管材内侧涂层的厚度,h2=r-rc,rc为管材内侧涂层的内半径;yz为管材两侧涂层-基体缺口环复合试样横截面的中性轴至管材内侧涂层内表面的距离,e为管材两侧涂层-基体缺口环复合试样横截面的几何轴线至中性轴间的距离,a为管材两侧涂层-基体缺口环复合试样横截面的面积,a=bh+αb(h1+h2);b为管材两侧涂层-基体缺口环复合试样的轴向长度。进一步的,所述管材两侧涂层-基体缺口环复合试样通过如下方法制得:对管材两侧涂层表面进行研磨处理;从管材上切取环状试样,所述环状试样的轴向长度与管材厚度之比为1~5,所述环状试样的轴向长度与管材外半径之比为0.2~1.0;对所述环状试样的圆边进行倒角处理;在所述环状试样上制备一个缺口,缺口宽度小于管材的外半径,得到管材两侧涂层-基体缺口环复合试样。一种管材涂层弯曲强度测试方法,包括以下步骤:利用缺口环压缩试验测得管材两侧涂层与管材基体的弹性模量之比α;对管材两侧涂层-基体闭口环复合试样进行径向压缩试验,直至管材内侧涂层发生开裂破坏,记录管材内侧涂层开裂的临界载荷值pc;通过如下公式计算管材两侧涂层的弯曲强度σc:其中,r0为管材两侧涂层-基体闭口环复合试样横截面的几何轴线曲率半径,h为管材基体厚度,h=r-r,r为管材基体的外半径,r为管材基体的内半径;h1为管材外侧涂层的厚度,h1=rc-r,rc为管材外侧涂层的外半径;h2为管材内侧涂层的厚度,h2=r-rc,rc为管材内侧涂层的内半径;e为管材两侧涂层-基体闭口环复合试样横截面的几何轴线至中性轴间的距离,ρz为管材两侧涂层-基体闭口环复合试样横截面中性轴的曲率半径,a为管材两侧涂层-基体闭口环复合试样横截面的面积,a=bh+αb(h1+h2);b为管材两侧涂层-基体闭口环复合试样的轴向长度。进一步的,所述管材两侧涂层-基体闭口环复合试样通过如下方法制得:对管材两侧涂层表面进行研磨处理;从管材上切取环状试样,所述环状试样的轴向长度与管材厚度之比为1~5,所述环状试样的轴向长度与管材外半径之比为0.2~1.0;对所述环状试样的圆边进行倒角处理,得到管材两侧涂层-基体闭口环复合试样。本发明具有以下有益效果:本发明提出的管材涂层弯曲强度测试方法实现了管材表面外侧、内侧和两侧涂层弯曲强度的准确、简便测量,通过对管材涂层-基体缺口/闭口环复合试样进行径向压缩试验,记录涂层开裂的临界载荷值pc,利用所推导的计算公式即可计算得管材涂层的弯曲强度。该方法操作简单,无需对管/环构件进行复杂加工处理,只需从管/环构件上切取一段圆环试样(缺口环试样还需制备一个缺口),对其进行简单的压缩加载(无需特殊复杂的夹具),即可测得管材外侧、内侧和两侧涂层的弯曲强度。附图说明图1为缺口环试样在压缩载荷作用下的受力分析:p为所施加的压缩载荷;n为切向力;q为径向力;m为弯矩;为径向力与垂线间的夹角;图2为管材外侧涂层-基体缺口环复合试样1/2高度处横截面的正应力径向分布图;图3为管材内侧涂层-基体闭口环复合试样内侧与外侧的正应力分布;图4为管材内侧涂层-基体闭口环复合试样顶端/底端横截面正应力的径向分布图;图5为管材两侧涂层-基体缺口环复合试样1/2高度处横截面正应力的径向分布图;图6为管材两侧涂层-基体闭口环复合试样内侧与外侧的正应力分布;图7为管材两侧涂层-基体闭口环复合试样顶端/底端横截面正应力的径向分布图;图8为内侧碳化硅涂层-石墨基体闭口环复合试样的载荷-横梁位移曲线。具体实施方式为使本发明要解决的技术问题、技术方案和优点更加清楚,下面将结合附图及具体实施例进行详细描述。本发明提供一种管材涂层弯曲强度测试方法,用于计算管材外侧涂层的弯曲强度,该方法包括以下步骤:利用缺口环压缩试验测得管材外侧涂层与管材基体的弹性模量之比α;本发明采用中国专利文献cn106289978a公开的测量管材涂层弹性模量的方法测得管材外侧涂层与管材基体的弹性模量之比α,具体测试方法不再在本发明中进行赘述。对管材外侧涂层-基体缺口环复合试样进行径向压缩试验,直至管材外侧涂层发生开裂破坏,记录管材外侧涂层开裂的临界载荷值pc;试验时,缺口位于试样高度的一半处。由于利用缺口环压缩试验测量管材涂层与管材基体的弹性模量之比α时(前一步骤)需要用到缺口环试样,本步骤的管材外侧涂层-基体缺口环复合试样可以使用前一步骤已经制作好的缺口环试样。通过如下公式计算管材外侧涂层的弯曲强度σc:其中,r0为管材外侧涂层-基体缺口环复合试样横截面的几何轴线曲率半径,h为管材基体厚度,h=r-r,r为管材基体的外半径,r为管材基体的内半径;h为管材外侧涂层的厚度,h=rc-r,rc为管材外侧涂层的外半径;yz为管材外侧涂层-基体缺口环复合试样横截面的中性轴至管材基体内表面的距离,e为管材外侧涂层-基体缺口环复合试样横截面的几何轴线至中性轴间的距离,a为管材外侧涂层-基体缺口环复合试样横截面的面积,a=bh+αbh;b为管材外侧涂层-基体缺口环复合试样的轴向长度。本发明提出的管材涂层弯曲强度测试方法实现了管材表面外侧涂层弯曲强度的准确、简便测量,通过对管材外侧涂层-基体缺口环复合试样进行径向压缩试验,记录管材外侧涂层开裂的临界载荷值pc,利用所推导的计算公式即可计算得管材外侧涂层的弯曲强度。该方法操作简单,无需对管/环构件进行复杂加工处理,只需从管/环构件上切取一段圆环试样并制备一个缺口(管材外侧涂层-基体缺口环复合试样),对其进行简单的压缩加载(无需特殊复杂的夹具),即可测得管材外侧涂层的弯曲强度。本发明中,由于利用缺口环压缩试验测量管材涂层与管材基体的弹性模量之比α时需要用到缺口环试样,因此在进行径向压缩试验时的管材外侧涂层-基体缺口环复合试样可以是测量α时的试样。本发明的管材外侧涂层-基体缺口环复合试样可以通过如下方法制得:利用车床和砂纸对管材外侧涂层表面进行研磨处理,砂纸模数由120目逐渐增加至800目。待涂层表面研磨完成后,从管材上切取环状试样,环状试样的轴向长度与管材厚度之比为1~5,环状试样的轴向长度与管材外半径之比为0.2~1.0。测试管材外侧涂层弯曲强度时,对环状试样的圆边进行倒角处理。在环状试样上制备一个缺口,缺口宽度小于管材的外半径,得到管材外侧涂层-基体缺口环复合试样。本发明利用力学试验机对管材外侧涂层-基体缺口环复合试样进行径向压缩试验,加载速率由试验机横梁位移控制,且加载速率使得管材外侧涂层开裂的时间为3~30s。管材外侧涂层开裂破坏可通过管材外侧涂层-基体缺口环复合试样的载荷-横梁位移曲线判断,加载载荷开始下降跃迁时所对应的载荷值即为管材外侧涂层开裂的临界载荷;或者可由声发射测试装置捕捉到管材外侧涂层开裂时的声信号,继而根据管材外侧涂层-基体缺口环复合试样的载荷-时间曲线可获得管材外侧涂层开裂的临界载荷。管材外侧涂层厚度可由数码显微镜或扫描电镜测得;管材基体厚度、管/环试样的轴向长度可由工具显微镜或游标卡尺测得;管材外侧涂层-基体缺口环复合试样的外半径、内半径可利用游标卡尺或外径千分尺测得。管材外侧涂层厚度应大于等于20μm。本发明提供另一种管材涂层弯曲强度测试方法,用于计算管材内侧涂层的弯曲强度,该方法包括以下步骤:利用缺口环压缩试验测得管材内侧涂层与管材基体的弹性模量之比α;本发明采用中国专利文献cn106289978a公开的测量管材涂层弹性模量的方法测得管材内侧涂层与管材基体的弹性模量之比α,具体测试方法不再在本发明中进行赘述。对管材内侧涂层-基体闭口环复合试样进行径向压缩试验,直至管材内侧涂层发生开裂破坏,记录管材内侧涂层开裂的临界载荷值pc;通过如下公式计算管材内侧涂层的弯曲强度σc:其中,r0为管材内侧涂层-基体闭口环复合试样横截面的几何轴线曲率半径,h为管材基体厚度,h=r-r,r为管材基体的外半径,r为管材基体的内半径;h为管材内侧涂层的厚度,h=r-rc,rc为管材内侧涂层的内半径;e为管材内侧涂层-基体闭口环复合试样横截面的几何轴线至中性轴间的距离,ρz为管材内侧涂层-基体闭口环复合试样横截面中性轴的曲率半径,a为管材内侧涂层-基体闭口环复合试样横截面的面积,a=bh+αbh;b为管材内侧涂层-基体闭口环复合试样的轴向长度。本发明提出的管材涂层弯曲强度测试方法实现了管材表面内侧涂层弯曲强度的准确、简便测量,通过对管材内侧涂层-基体闭口环复合试样进行径向压缩试验,记录管材内侧涂层开裂的临界载荷值pc,利用所推导的计算公式即可计算得管材内侧涂层的弯曲强度。该方法操作简单,无需对管/环构件进行复杂加工处理,只需从管/环构件上切取一段圆环试样(简单处理后得到管材内侧涂层-基体闭口环复合试样),对其进行简单的压缩加载(无需特殊复杂的夹具),即可测得管材内侧涂层的弯曲强度。本发明的管材内侧涂层-基体闭口环复合试样通过如下方法制得:利用车床和砂纸对管材内侧涂层表面进行研磨处理,砂纸模数由120目逐渐增加至800目。待管材内侧涂层表面研磨完成后,从管材上切取环状试样,环状试样的轴向长度与管材厚度之比为1~5,环状试样的轴向长度与管材外半径之比为0.2~1.0。测试管材内侧涂层弯曲强度时,对环状试样的圆边进行倒角处理,得到管材内侧涂层-基体闭口环复合试样。本发明利用力学试验机对管材内侧涂层-基体闭口环复合试样进行径向压缩试验,加载速率由试验机横梁位移控制,且加载速率使得管材内侧涂层开裂的时间为3~30s。管材内侧涂层开裂破坏可通过管材内侧涂层-基体闭口环复合试样的载荷-横梁位移曲线判断,加载载荷开始下降跃迁时所对应的载荷值即为涂层开裂的临界载荷;或者可由声发射测试装置捕捉到管材内侧涂层开裂时的声信号,继而根据管材内侧涂层-基体闭口环复合试样的载荷-时间曲线可获得管材内侧涂层开裂的临界载荷。管材内侧涂层厚度可由数码显微镜或扫描电镜测得;管材基体厚度、管/环试样的轴向长度可由工具显微镜或游标卡尺测得;管材内侧涂层-基体闭口环复合试样的外半径、内半径可利用游标卡尺或外径千分尺测得。管材内侧涂层厚度应大于等于20μm。本发明还提供另一种管材涂层弯曲强度测试方法,用于计算管材内外两侧涂层的弯曲强度,该方法包括以下步骤:利用缺口环压缩试验测得管材两侧涂层与管材基体的弹性模量之比α;本发明采用中国专利文献cn106289978a公开的测量管材涂层弹性模量的方法测得管材两侧涂层与管材基体的弹性模量之比α,具体测试方法不再在本发明中进行赘述。对管材两侧涂层-基体缺口环复合试样进行径向压缩试验,直至管材外侧涂层发生开裂破坏,记录管材外侧涂层开裂的临界载荷值pc;试验时,缺口位于试样高度的一半处。由于利用缺口环压缩试验测量管材涂层与管材基体的弹性模量之比α时(前一步骤)需要用到缺口环试样,本步骤的管材两侧涂层-基体缺口环复合试样可以使用前一步骤已经制作好的缺口环试样。通过如下公式计算管材两侧涂层的弯曲强度σc:其中,r0为管材两侧涂层-基体缺口环复合试样横截面的几何轴线曲率半径,h为管材基体厚度,h=r-r,r为管材基体的外半径,r为管材基体的内半径;h1为管材外侧涂层的厚度,h1=rc-r,rc为管材外侧涂层的外半径;h2为管材内侧涂层的厚度,h2=r-rc,rc为管材内侧涂层的内半径;yz为管材两侧涂层-基体缺口环复合试样横截面的中性轴至管材内侧涂层内表面的距离,e为管材两侧涂层-基体缺口环复合试样横截面的几何轴线至中性轴间的距离,a为管材两侧涂层-基体缺口环复合试样横截面的面积,a=bh+αb(h1+h2);b为管材两侧涂层-基体缺口环复合试样的轴向长度。本发明提出的管材涂层弯曲强度测试方法实现了管材表面内外两侧涂层弯曲强度的准确、简便测量,通过对管材两侧涂层-基体缺口环复合试样进行径向压缩试验,记录管材外侧涂层开裂的临界载荷值pc,利用所推导的计算公式即可计算得管材两侧涂层的弯曲强度。该方法操作简单,无需对管/环构件进行复杂加工处理,只需从管/环构件上切取一段圆环试样并制备一个缺口(管材两侧涂层-基体缺口环复合试样),对其进行简单的压缩加载(无需特殊复杂的夹具),即可测得管材两侧涂层的弯曲强度。本发明中,由于利用缺口环压缩试验测量管材涂层与管材基体的弹性模量之比α时需要用到缺口环试样,因此在进行径向压缩试验时的管材两侧涂层-基体缺口环复合试样可以是测量α时的试样。本发明的管材两侧涂层-基体缺口环复合试样可以通过如下方法制得:利用车床和砂纸对管材两侧涂层表面进行研磨处理,砂纸模数由120目逐渐增加至800目。待管材两侧涂层表面研磨完成后,从管材上切取环状试样,环状试样的轴向长度与管材厚度之比为1~5,环状试样的轴向长度与管材外半径之比为0.2~1.0。测试管材两侧管材涂层弯曲强度时,对环状试样的圆边进行倒角处理。在环状试样上制备一个缺口,缺口宽度小于管材的外半径,得到管材两侧涂层-基体缺口环复合试样。本发明利用力学试验机对管材两侧涂层-基体缺口环复合试样进行径向压缩试验,加载速率由试验机横梁位移控制,且加载速率使得管材涂层开裂的时间为3~30s。管材涂层开裂破坏可通过管材两侧涂层-基体缺口环复合试样的载荷-横梁位移曲线判断,加载载荷开始下降跃迁时所对应的载荷值即为管材涂层开裂的临界载荷;或者可由声发射测试装置捕捉到管材涂层开裂时的声信号,继而根据管材两侧涂层-基体缺口环复合试样的载荷-时间曲线可获得管材涂层开裂的临界载荷。管材涂层厚度可由数码显微镜或扫描电镜测得;管材基体厚度、管/环试样的轴向长度可由工具显微镜或游标卡尺测得;管材两侧涂层-基体缺口环复合试样的外半径、内半径可利用游标卡尺或外径千分尺测得。管材涂层厚度应大于等于20μm。本发明还提供另一种管材涂层弯曲强度测试方法,用于计算管材内外两侧涂层的弯曲强度,该方法包括以下步骤:利用缺口环压缩试验测得管材两侧涂层与管材基体的弹性模量之比α;本发明采用中国专利文献cn106289978a公开的测量管材涂层弹性模量的方法测得管材涂层与管材基体的弹性模量之比α,具体测试方法不再在本发明中进行赘述。对管材两侧涂层-基体闭口环复合试样进行径向压缩试验,直至管材内侧涂层发生开裂破坏,记录管材内侧涂层开裂的临界载荷值pc。通过如下公式计算管材两侧涂层的弯曲强度σc:其中,r0为管材两侧涂层-基体闭口环复合试样横截面的几何轴线曲率半径,h为管材基体厚度,h=r-r,r为管材基体的外半径,r为管材基体的内半径;h1为管材外侧涂层的厚度,h1=rc-r,rc为管材外侧涂层的外半径;h2为管材内侧涂层的厚度,h2=r-rc,rc为管材内侧涂层的内半径;e为管材两侧涂层-基体闭口环复合试样横截面的几何轴线至中性轴间的距离,ρz为管材两侧涂层-基体闭口环复合试样横截面中性轴的曲率半径,a为管材两侧涂层-基体闭口环复合试样横截面的面积,a=bh+αb(h1+h2);b为管材两侧涂层-基体闭口环复合试样的轴向长度。本发明提出的管材涂层弯曲强度测试方法实现了管材表面内外两侧涂层弯曲强度的准确、简便测量,通过对管材两侧涂层-基体闭口环复合试样进行径向压缩试验,记录管材内侧涂层开裂的临界载荷值pc,利用所推导的计算公式即可计算得管材两侧涂层的弯曲强度。该方法操作简单,无需对管/环构件进行复杂加工处理,只需从管/环构件上切取一段圆环试样(经简单处理后得到管材两侧涂层-基体闭口环复合试样),对其进行简单的压缩加载(无需特殊复杂的夹具),即可测得管材两侧涂层的弯曲强度。本发明的管材两侧涂层-基体闭口环复合试样通过如下方法制得:利用车床和砂纸对管材两侧涂层表面进行研磨处理,砂纸模数由120目逐渐增加至800目。待管材两侧涂层表面研磨完成后,从管材上切取环状试样,环状试样的轴向长度与管材厚度之比为1~5,环状试样的轴向长度与管材外半径之比为0.2~1.0。测试管材两侧管材涂层弯曲强度时,对环状试样的圆边进行倒角处理,得到管材两侧涂层-基体闭口环复合试样。本发明利用力学试验机对管材两侧涂层-基体闭口环复合试样进行径向压缩试验,加载速率由试验机横梁位移控制,且加载速率使得管材涂层开裂的时间为3~30s。管材涂层开裂破坏可通过管材两侧涂层-基体闭口环复合试样的载荷-横梁位移曲线判断,加载载荷开始下降跃迁时所对应的载荷值即为管材涂层开裂的临界载荷;或者可由声发射测试装置捕捉到管材涂层开裂时的声信号,继而根据管材两侧涂层-基体闭口环复合试样的载荷-时间曲线可获得管材涂层开裂的临界载荷。管材涂层厚度可由数码显微镜或扫描电镜测得;管材基体厚度、管/环试样的轴向长度可由工具显微镜或游标卡尺测得;管材两侧涂层-基体闭口环复合试样的外半径、内半径可利用游标卡尺或外径千分尺测得。管材涂层厚度应大于等于20μm。目前关于管材涂层弯曲强度的测试评价研究,国内外仍处于研究空白阶段,为突破管材涂层弯曲强度的测试技术瓶颈,本发明通过对管材缺/闭口环试样进行径向压缩加载试验,即可测得管材外侧涂层、内侧涂层与两侧涂层的弯曲强度,其理论推导过程如下:对外侧涂层复合缺口环试样进行径向压缩试验直至涂层发生开裂破坏,其受力分析如图1所示,复合试样横截面所受正应力可由下式进行计算:涂层基体式中,y为与复合环试样横截面中性层间的距离;ρ为距中性层y处的曲率半径;为横截面径向力与垂直方向间的夹角。由式(5)可知,最大正应力应位于即缺口环试样的1/2高度处。由式(5)、式(6)及材料力学分析计算可得外侧涂层复合缺口环试样1/2高度处横截面正应力沿径向的分布情况如图2所示(假设α=5,正值为拉应力,负值为压应力)。由图2可知,管材外侧涂层复合试样在压缩至开裂的过程中,在1/2高度处,其基体内侧受压,而基体外侧与涂层处受拉,在中性层处应力发生突变,且其外侧涂层表面所受拉应力最大,因此涂层的弯曲强度可由下式进行计算:对于管材内侧涂层复合缺口环试样,其在缺口环压缩试验过程中,管材复合试样1/2高度处外侧所受拉应力最大,即开裂破坏是始于外侧基体,因此通过缺口环试验是无法测得内侧涂层的弯曲强度。而闭口环试样在压缩过程中,其所受拉应力最大值位于管材内侧,因此可利用闭口环试验测试管材内侧涂层的弯曲强度。对内侧涂层闭口环复合试样进行压缩加载,直至试样发生开裂破坏,由材料力学可得复合试样横截面上的正应力:基体涂层式中,为横截面径向力与水平线间的夹角。由于圆环试样的对称性,可选取的1/4圆环为研究对象,则内侧涂层闭口环复合试样内侧与外侧位置所受的正应力如图3所示(正值为拉应力,负值为压应力)。由图3可以看出,内侧涂层复合闭口环试样在的内侧位置处所受拉应最大。(即闭口环顶端/底端)位置处复合试样横截面的正应力分布(以α=5为例)如图4所示,则管材内侧处所受拉应力最大,即复合试样的开裂是始于内侧涂层,通过载荷-位移曲线或声发射装置测得内侧涂层开裂的临界载荷pc,利用下式即可求算出涂层的弯曲强度:对于两侧涂层管材试样而言,可利用缺口环法或闭口环法测试涂层的弯曲强度。对两侧涂层复合缺口环试样进行压缩试验时,1/2高度处缺口环试样横截面上的正应力沿径向的分布情况(假设α=5)如图5所示。两侧涂层复合缺口环试样内侧涂层处受最大压应力,而外侧涂层处受最大拉应力,即外侧涂层首先发生开裂,裂纹逐渐向内侧扩展。根据复合试样的载荷-位移曲线或利用声发射装置确定外侧涂层开裂的临界载荷值pc,由下式即可求算出涂层的弯曲强度:对两侧涂层闭口环复合试样进行压缩加载时,由于圆环试样的对称性,可选取的1/4圆环为研究对象,则两侧涂层闭口环复合试样内侧与外侧位置所受的正应力如图6所示(正值为拉应力,负值为压应力)。由图6可以看出,复合试样在的内侧位置处所受拉应最大。(即闭口环顶端/底端)位置处两侧涂层复合试样横截面的正应力分布(以α=5为例)如图7所示,管材外侧涂层处受压应力作用,而管材内侧处所受拉应力最大,即复合试样的开裂是始于内侧涂层,通过载荷-位移曲线或声发射装置测得内侧涂层开裂的临界载荷pc,利用下式即可求算出涂层的弯曲强度:下面结合具体测试示例进一步说明本发明提出的管材涂层弯曲强度测试方法。该测试方法只为具体说明本发明的技术方案,不作为本发明其他实施方式的限制。以下示例均选用在环状石墨基体(外半径20mm,内半径17mm,轴向长度8mm)表面上化学气相沉积碳化硅涂层复合环试样。利用缺口环压缩试验测试石墨基体环试样的弹性模量,加载速率由横梁位移控制,选用0.2mm/min,载荷上限为8n。缺口环压缩试验测得石墨基体的弹性模量为es=11.06±0.56gpa。示例1:外侧涂层弯曲强度的测量首先利用缺口环压缩试验测得碳化硅涂层的弹性模量,具体测试方法参照中国专利cn106289978a。缺口环压缩试验测试管材外侧涂层弹性模量时加载速率选用0.2mm/min,载荷上限为6n。涂层的弹性模量为ec=367.39±12.89gpa,则α=33.21±1.16。然后利用缺口环压缩试验测试管材外侧涂层弯曲强度,加载速率选用0.5mm/min,加载至涂层发生开裂破坏。对于石墨基体-碳化硅涂层复合缺口环试样,其破坏形式为:加载至最大载荷值后,载荷出现急剧降低,且涂层与基体整体发生断裂破坏,则此时的载荷最大值即为涂层开裂的临界载荷值pc。利用游标卡尺测得管材外侧涂层复合试样的外半径rc与内半径r;利用数码显微镜测得涂层厚度h;则石墨基体的外半径r=rc-h,基体厚度为h=r-r。将测得的α、pc及复合缺口环试样的几何尺寸代入式(1)即可计算得外侧管材涂层的弯曲强度,测试结果如表1所示,测得外侧碳化硅涂层的弯曲强度为σc=259.38±31.32mpa。表1石墨环基体外侧碳化硅涂层弯曲强度的测试结果no.es/gpapc/nrc/mmr/mmr/mmασc/mpa111.0627.6520.0419.9316.9133.21293.95211.0628.5619.9819.8316.9433.21256.80311.0626.9820.0419.8816.8633.21218.59411.0621.9320.1120.0117.1433.21268.19示例2:内侧涂层弯曲强度的测量首先利用缺口环压缩测试管材内侧涂层弹性模量,具体测试方法参照中国专利cn106289978a,加载速率由横梁位移控制,选用0.2mm/min,载荷上限为6n。缺口环压缩试验测得内侧碳化硅涂层的弹性模量为ec=349.51±28.40gpa,则α=31.60±2.57;然后利用闭口环压缩试验测试管材内侧涂层弯曲强度,以0.5mm/min的横梁位移速率对内侧碳化硅涂层-石墨基体复合闭口环试样进行径向压缩加载,加载至涂层发生开裂,试样的载荷-横梁位移曲线如图8所示,其加载载荷开始下降跃迁时对应的载荷值即为内侧碳化硅涂层发生开裂的临界载荷pc。利用游标卡尺测得管材内侧涂层复合试样的外半径r与内半径rc;利用数码显微镜测得涂层厚度h;则石墨基体的内半径r=rc+h,基体厚度h=r-r。将测得的α、pc及复合闭口环试样的几何尺寸代入式(2)即可计算得内侧管材涂层的弯曲强度,测试结果如表2所示,测得内侧碳化硅涂层的弯曲强度为σc=282.01±18.30mpa。表2石墨环基体内侧碳化硅涂层弯曲强度的测试结果no.es/gpar/mmr/mmrc/mmpc/nασc/mpa111.0620.0616.9816.9450.1231.60300.81211.0620.0316.9716.9152.9031.60259.54311.0620.0816.9616.9153.7031.60292.18411.0619.9917.0517.0233.7931.60275.50示例3:两侧涂层弯曲强度的测量首先利用缺口环压缩试验测试两侧涂层弹性模量,具体测试方法参照中国专利cn106289978a,加载速率选用0.2mm/min,载荷上限为10n。缺口环压缩试验测得两侧碳化硅涂层的弹性模量为ec=362.51±20.53gpa,则α=32.77±1.86。然后利用缺口环压缩试验测试两侧涂层的弯曲强度,加载速率选用0.5mm/min,加载至涂层发生开裂破坏。对于石墨基体-两侧碳化硅涂层复合缺口环试样,其破坏形式为:加载至最大载荷值后,载荷出现急剧降低,且涂层与基体整体发生断裂破坏,则此时的载荷最大值即为涂层开裂的临界载荷值pc。利用游标卡尺测得管材两侧涂层复合试样的外半径rc与内半径rc;利用数码显微镜测得外侧涂层厚度h1,内侧涂层厚度h2;则石墨基体的内半径r=rc+h2,石墨基体的外半径r=rc-h1,石墨基体厚度h=r-r。将测得的α、pc及复合缺口环试样的几何尺寸代入式(3)即可计算得两侧管材涂层的弯曲强度,测试结果如表3所示,测得两侧碳化硅涂层的弯曲强度为σc=283.17±21.98mpa。表3缺口环压缩试验测得的石墨环基体两侧碳化硅涂层的弯曲强度no.es/gparc/mmr/mmr/mmrc/mmpc/nασc/mpa111.0620.0819.9416.9816.9145.0332.77283.06211.0620.1119.9816.9216.8450.3732.77310.51311.0620.1220.0116.9116.8238.1532.77256.69411.0620.0919.9716.9216.8542.2832.77282.42或者利用闭口环压缩试验测试两侧涂层的弯曲强度,加载速率选用0.5mm/min,加载至能发生开裂破坏。加载过程中,利用声发射测试装置捕捉涂层开裂的声信号,进而可确定涂层开裂对应的时间;进而由试样的载荷-时间曲线确定涂层开裂的临界载荷pc。利用游标卡尺测得管材两侧涂层复合试样的外半径rc与内半径rc;利用数码显微镜测得外侧涂层厚度h1,内侧涂层厚度h2;则石墨基体的内半径r=rc+h2,石墨基体的外半径r=rc-h1,石墨基体厚度h=r-r。将测得的α、pc及复合闭口环试样的几何尺寸代入式(4)即可计算得内侧管材涂层的弯曲强度,测试结果如表4所示,测得内侧碳化硅涂层的弯曲强度为276.08±18.05mpa。表4闭口环压缩试验测得的石墨环基体两侧碳化硅涂层的弯曲强度no.es/gparc/mmr/mmr/mmrc/mmpc/nασc/mpa111.0620.1119.9616.9716.87103.5232.77260.05211.0620.1420.0017.0116.92114.2032.77295.63311.0620.1019.9716.9716.87109.8332.77272.55为验证管材涂层弯曲强度测试方法的正确性与可靠性,试验选用单面涂层梁试样的测试结果作为参比,测试方法参照国际标准iso19603:2016。测试方法如下:首先将制备石墨基体试样与单面涂层复合试样,切割加工成2mm×4mm×36mm;三点弯曲试验测试弹性模量时,跨距选用30mm,加载速率由横梁位移控制,选用0.2mm/min,加载上限为10n;三点弯曲试验测试弯曲强度时,跨距选用30mm,加载速率由横梁位移控制,选用0.5mm/min,加载直至涂层发生开裂或试样断裂。三点弯曲法测得石墨基体的弹性模量为es=10.99±0.36gpa,碳化硅涂层的弹性模量为ec=354.24±20.10gpa,则α=32.23±1.83。参照iso19603:2016,可由涂层开裂的临界载荷值及单面涂层梁试样的几何尺寸测得碳化硅涂层弯曲强度为σc=262.72±22.56mpa。上述碳化硅管材外侧、内侧、两侧涂层的弯曲强度值(259.38~283.17mpa)与三点弯曲法测得的碳化硅涂层弯曲强度值(262.72mpa)基本一致,由此证明了本发明所提出的管材涂层弯曲强度测试方法在理论和实验操作方面都是准确可靠的。以上所述是本发明的优选实施方式,应当指出,对于本
技术领域:
的普通技术人员来说,在不脱离本发明所述原理的前提下,还可以做出若干改进和润饰,这些改进和润饰也应视为本发明的保护范围。当前第1页12