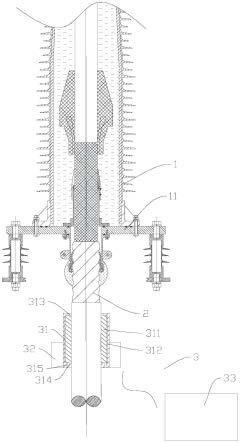
1.本发明涉及漏油检测技术领域,特别是涉及一种高压电缆充油终端的漏油监测装置及方法。
背景技术:2.电缆终端广泛应用于电力、石油化工、冶金、铁路港口和建筑等各个领域,其作用是装配到电缆线路的首末端,用以完成与其他电气设备连接的装置。其中,高压电缆终端用于把地下的电缆和高压输电塔上的高压输导线可靠联接。
3.现有高压电缆终端产品包括全预制干式硅橡胶户外终端和充油式终端,广泛使用的为充油式终端,而充油式终端故障大部分是由于终端内部注油流失,造成的终端耐压故障。这种漏油过程一般是个长期缓慢的过程,当充油式终端的油位下降到一定程度,就会引发终端耐压故障。而现有对高压电缆终端的检查周期为每1至3年停电检查一次,检查手段主要通过油位指示器去检测充油式终端内部的油位高度,由于高压电缆终端的高压特性,这种检测只能用于停电检查,而无法实现实时监测,若在检查周期内,充油式终端的油位快速下降,则可能引起高压电缆及电缆终端的故障。因此,需要设计一种高压电缆充油终端的实时漏油监测装置。
技术实现要素:4.本发明要解决的技术问题在于克服现有技术中的缺陷,从而提供一种高压电缆充油终端的漏油监测装置及方法。
5.为实现上述目的,本发明采用了如下技术方案:
6.一种高压电缆充油终端的漏油监测装置,包括:
7.电容传感器,包覆在充油终端与电缆交界处的电缆上,用于吸收所述充油终端的漏油;
8.电容检测模块,与所述电容传感器电连接,用于定期检测所述电容传感器的电容值;
9.数据处理模块,与所述电容检测模块信号连接,用于将当前检测到的电容值与初始电容值相比计算所述电容值的变化量,并通过查询数据库将所述电容值的变化量换算成漏油的重量,在漏油的重量超过设定阈值后发出警报;
10.电源模块,与所述电容检测模块电连接供电。
11.优选地,所述电容传感器具有供漏油进入的上开口,且所述电容传感器包括吸油层和感应层,所述上开口的位置与所述吸油层的位置对应;
12.所述吸油层贴合所述电缆设置,并与所述感应层接触,所述吸油层用于吸收所述充油终端的漏油;所述感应层包覆在所述吸油层和所述电缆的外侧,与所述电容检测模块电连接。
13.优选地,所述电容传感器包括两个分部,所述分部周向设置在所述电缆的表面;
14.所述分部均包括绝缘外壳、感应层和吸油层,所述感应层为方形pcb材质或方形金属板材,固定在所述绝缘外壳的内部,所述吸油层相对所述感应层靠近所述电缆;
15.两个所述绝缘外壳的相对面彼此贴合,所述吸油层的相对端彼此贴合,在所述电容传感器安装在所述电缆上之后,两个所述感应层之间的距离固定;
16.所述电容检测模块固定在所述绝缘外壳的外壁上,所述感应层通过穿出所述绝缘外壳的导线与所述电容检测模块电连接,且对导线穿出处作密封处理。
17.优选地,所述绝缘外壳为中空方形结构,所述上开口设置在所述绝缘外壳的上表面,且所述绝缘外壳还包括下端部,所述下端部包括电缆贯穿孔,所述电缆贯穿孔的孔径与所述电缆的直径相适配,所述上开口的内径大于所述电缆贯穿孔的孔径。
18.优选地,所述上开口的内径与所述电缆贯穿孔的孔径之差大于等于两个感应层的厚度之和。
19.优选地,所述吸油层的材料为疏水吸油型聚丙烯;
20.所述下端部具有漏水孔,所述漏水孔的孔径小于1mm。
21.优选地,两个所述分部可拆卸连接;
22.还包括紧固件,所述紧固件套设或缠绕在两个所述分部的外侧,以将两个所述分部相对贴合并固定在所述电缆上。
23.优选地,所述电容传感器与充油终端与电缆交界处的距离为10cm-20cm。
24.优选地,所述电源模块包括电池,还包括互感取电单元和/或太阳能充电单元。
25.为实现上述目的,本发明还采用了如下技术方案:
26.一种高压电缆充油终端的漏油监测方法,采用如上述的漏油监测装置,包括如下步骤:
27.步骤一、将所述电容传感器安装在充油终端与电缆交界处的电缆上,使所述电容传感器覆盖所述电缆的周向表面;
28.步骤二、在安装完成后,进行初始测量,确定所述电容传感器的初始电容值;后续定期通过电容检测模块检测所述电容传感器的电容值;
29.步骤三、当充油终端出现漏油,漏油从充油终端与电缆交界处沿着电缆流入电容传感器,电容传感器吸收漏油,使电容传感器之间的相对介电常数发生变化,导致所述电容检测模块检测到的所述电容传感器的电容值发生变化;所述电容检测模块将检测到的电容值与与初始电容值相比,计算变化量;
30.步骤四、将变化量的数据传输至数据处理模块,通过查询数据库,将所述电容值的变化量换算成漏油的重量,数据库记录所述电容值的变化量与所述漏油的重量的对照关系;
31.步骤五、所述数据处理模块判断漏油的重量超过设定阈值后发出警报,并缩短所述电容检测模块的检测周期。
32.相比现有技术,本发明的有益效果在于:
33.上述技术方案中所提供的高压电缆充油终端的漏油监测装置,在充油终端和电缆交界处设置电容传感器,利用电容传感器吸收充油终端的漏油,相较于电容传感器初安装时的电容值,吸收了漏油后的电容传感器由于中间介质的相对介电常数发生变化,其电容值也发生变化,控制电容检测模块定期对电容传感器的电容值进行检测,由电容值的变化
量确定漏油的重量,由此判断充油终端的漏油严重程度,可实现实时检测,并及时发现充油终端的油位大幅下降,及时排出充油终端的故障险情。由于充油终端的绝缘油为无味、无毒、不易挥发的液体,因此被电容传感器吸收后可长期滞留于电容传感器中,而漏油监测装置检测当前的电容值相对初始电容值的变化量即可计算从充油终端开始漏油到当前检测时的所有漏油的重量,由此准确反馈充油终端的剩余油量和油位。本发明的漏油监测装置结构简单,安装方便,电容传感器只是包覆在充油终端与电缆交界处的电缆外周,并不会破坏充油终端的安装工艺,不需要停电,新旧高压电缆充油终端,都可以安装,实用价值高。
附图说明
34.为了更清楚地说明本发明具体实施方式或现有技术中的技术方案,下面将对具体实施方式或现有技术描述中所需要使用的附图作简单地介绍,显而易见地,下面描述中的附图是本发明的一些实施方式,对于本领域普通技术人员来讲,在不付出创造性劳动的前提下,还可以根据这些附图获得其他的附图。
35.图1为本发明实施例的漏油监测装置安装在电缆上的示意图。
36.图2为本发明实施例的电容传感器及电容检测模块的剖面示意图。
37.图3为本发明实施例的电容传感器及电容检测模块的示意图。
38.附图标记说明:
39.1、充油终端;11、底座;2、电缆;3、漏油监测装置;31、电容传感器;311、吸油层;312、感应层;313、上开口;314、下端部;315、漏水孔;316、第一分部;317、第二分部;318、电缆贯穿孔;319、绝缘外壳;32、电容检测模块;321、导线;33、数据处理模块;34、紧固件。
具体实施方式
40.下面将结合附图对本发明的技术方案进行清楚、完整地描述,显然,所描述的实施例是本发明一部分实施例,而不是全部的实施例。基于本发明中的实施例,本领域普通技术人员在没有做出创造性劳动前提下所获得的所有其他实施例,都属于本发明保护的范围。
41.在本发明的描述中,需要说明的是,术语“中心”、“上”、“下”、“左”、“右”、“竖直”、“水平”、“内”、“外”等指示的方位或位置关系为基于附图所示的方位或位置关系,仅是为了便于描述本发明和简化描述,而不是指示或暗示所指的装置或元件必须具有特定的方位、以特定的方位构造和操作,因此不能理解为对本发明的限制。此外,术语“第一”、“第二”、“第三”仅用于描述目的,而不能理解为指示或暗示相对重要性。
42.在本发明的描述中,需要说明的是,除非另有明确的规定和限定,术语“安装”、“相连”、“连接”应做广义理解,例如,可以是固定连接,也可以是可拆卸连接,或一体地连接;可以是机械连接,也可以是电连接;可以是直接相连,也可以通过中间媒介间接相连,可以是两个元件内部的连通。对于本领域的普通技术人员而言,可以具体情况理解上述术语在本发明中的具体含义。
43.如附图1所示,本发明实施例提供了一种高压电缆充油终端的漏油监测装置,电容传感器31,包覆在充油终端1与电缆2交界处的电缆2上,用于吸收充油终端1的漏油;电容检测模块32,与电容传感器31电连接,用于定期检测电容传感器31的电容值,并与初始电容值相比计算电容值的变化量;数据处理模块33,与电容检测模块32信号连接,用于通过查询数
据库将电容值的变化量换算成漏油的重量,并在漏油的重量超过设定阈值后发出警报;电源模块(未画出),与电容检测模块32电连接供电。
44.如附图1至附图3所示,电容传感器31具有供漏油进入的上开口313,且电容传感器31包括吸油层311和感应层312,上开口313的位置与吸油层311的位置对应,使漏油沿电缆2流下时,由上开口313进入电容传感器31,直接被吸油层311吸收。
45.电容传感器31的原理相当于电容式液位传感器,包括绝缘主体和位于绝缘主体内侧的吸油层311和感应层312,吸油层311用于吸收充油终端1的漏油,感应层312包覆在吸油层311和电缆2的外侧,与电容检测模块32电连接。如附图1所示,电容传感器31位于充油终端1的下方,经过长时间的观察和实验,充油终端1内的油一般从充油终端1的底座11与电缆2的连接处或底座11与搪铅的连接处漏出,因此,漏油会沿着电缆2向下流,进入电容传感器31,被与电缆2贴合的吸油层311吸收,使得电容传感器31的相对介电常数发生变化。当电容传感器安装在电缆上之后,电容两极(感应层)的距离保持不变,对电容两极施加相同的电压,根据电容公式,u
a-ub为电容两极的电势差,εr为电容两极之间的相对介电常数,k为静电力常量,s为电容两极的正对面积,d为电容两极的距离,由于π、k、s以及d均保持不变,因此,当电容值发生变化时,即为电容两极之间的相对介电常数发生变化,而电容传感器中间的电缆材质也不会发生变化,由此可推导是吸油层吸收了漏油而导致电容两极之间的相对介电常数发生变化,漏油量与电容值的变化值有对应关系,该对应关系可通过若干实验获得,并建立漏油量与电容值的变化值的对应关系数据库。
46.电容检测模块32固定在筒状的绝缘主体外侧,且与感应层312电连接;电源模块也固定在筒状的绝缘主体外侧,且与电容检测模块32电连接,对电容检测模块32供电,使电容检测模块32能够对电容传感器31的感应层312的两极施加电压。
47.电容检测模块32对电容传感器31的感应层312施加的每次电压均相同,用于定期检测电容传感器31的电容值。在电容传感器31刚刚安装在电缆2上时,吸油层311中没有漏油,此时对电容传感器31的电容值进行检测,获得初始电容值。由于电容传感器31包覆在电缆2上,电缆2的尺寸材质不同也会使得电容传感器31的相对介电常数不同,因此,本发明实施例通过定期检测电容传感器31的电容值,并与初始电容值相比计算电容值的变化量,由变化量换算成漏油的重量,排除不同尺寸材质的电缆2对初始电容值的影响。
48.在电容检测模块32定期检测电容传感器31的电容值,并通过有线或无线的方式,将检测数据传送至数据处理模块33,数据处理模块33包括控制电路(未画出)和运算芯片(未画出),用于接收电容检测模块32发送的数据,并将当前检测到的电容值与初始电容值相比计算电容值的变化量,并通过查询数据库将电容值的变化量换算成漏油的重量。运算芯片存储着初始电容值和变化量与漏油重量的对照数据库,数据库中的数据可由若干次实验获得。
49.考虑到数据处理模块33中的运算芯片的运算会消耗大量电能,数据处理模块33可设置在靠近充油终端1和电缆2的地面上,并连接有线电源或大容量电池模组。优选地,数据处理模块33还包括第一通讯单元(未画出),电容检测模块32包括第二通讯单元(未画出),第一通讯单元和第二通讯单元无线通讯连接。电容检测模块32定时启动检测,以节省电源,
同时,电源模块除了微型电池外,还包括互感取电单元,利用电缆2的电场取电,或,还包括太阳能充电单元,利用太阳能对微型电池进行充电,从而延长电容检测模块32的工作时间,实现长时间的无人监测。
50.优选地,为方便电容传感器31的安装,如附图2和附图3所示,电容传感器31包括两个分部,第一分部316和第二分部317周向设置在电缆2的表面,第一分部316和第二分部317均包括绝缘外壳319、感应层311和吸油层312,感应层311为方形pcb材质或方形金属板材,固定在绝缘外壳319的内部,具体可为粘接,或者,也可为在绝缘外壳319的内壁上采用真空喷镀法镀上坚固、且导电良好的镀层,作为感应层311。吸油层312相对感应层311靠近电缆2;吸油层312由柔性材料制成,可始终贴合电缆2的外表面。两个绝缘外壳319的相对面彼此贴合,吸油层312的相对端彼此贴合,以避免漏油从缝隙中流走。值得注意的是,在电容传感器31安装在电缆上之后,两个感应层312之间的距离固定,即电容传感器的两极距离固定。
51.优选地,绝缘外壳319为中空方形结构,上开口313设置在绝缘外壳319的上表面,且绝缘外壳319还包括下端部314,下端部314包括电缆贯穿孔318,电缆贯穿孔318的孔径与电缆2的直径相适配,保证绝缘外壳319的下端部314与电缆2的外表面贴合,上开口313的内径大于电缆贯穿孔318的孔径,方便漏油进入电容传感器。
52.优选地,上开口313的内径与电缆贯穿孔318的孔径之差大于等于两个感应层312的厚度之和,避免感应层312暴露在上开口,影响感应层312的使用寿命。
53.电容检测模块32固定在绝缘外壳319的外壁上,感应层312通过穿出绝缘外壳319的导线321与电容检测模块32电连接,且对导线穿出处(未画出)作密封处理,避免漏油从导线穿出处流出。
54.两个分部之间的连接方式为可拆卸连接或固定连接,固定连接的方式为,在所有分部周向设置在电缆2的外周之后,将分部的外周的焊接固定或粘接固定;可拆卸连接的方式为:采用紧固件34,比如卡箍,卡箍套设在若干分部的外侧,以将若干分部固定在电缆2上,卡箍可调整松紧,从而使得吸油层311与电缆2的外周表面贴合,但不会过分挤压吸油层311,影响吸油层311的吸油效果;或者,紧固件34也可为封装胶带,在电容传感器31及电容检测模块32安装在电缆2上后,利用封装胶带缠绕在整个模块的外周面,且注意避让电容传感器31的上开口313,避免影响漏油进入电容传感器31,也可保护电容传感器31外部的电容检测模块32,使整个模块可以固定在电缆2上。
55.由于高压电缆2充油终端1一般设置在户外,风吹雨淋,因此,可能也会有部分雨水从上开口313进入电容传感器31,影响检测结果,因此,本发明实施例的吸油层311优选为疏水吸油型聚丙烯,对聚丙烯进行疏水处理,避免其吸收雨水,且可在电容传感器31的底部增加下端部314,下端部314的内壁与电缆2的表面贴合,吸油层311位于下端部314上方,避免吸油层311脱落,下端部314具有漏水孔315,漏水孔315的孔径小于1mm,便于雨水排出电容传感器31,而吸油层311为亲油材质,油不会从漏水孔315处流出。
56.优选地,充油终端1的底座11一般较为宽大,可起到一定的遮挡效果,因此,控制电容传感器31与充油终端1与电缆2交界处的距离,使得充油终端1的底座11可遮挡部分雨水,且可使漏油尽快进入电容传感器31中,电容传感器31与充油终端1与电缆2交界处的距离为10cm-20cm,避免距离过大,充油终端1的底座11无法起到良好的遮雨效果,也避免距离过小,影响充油终端1的安装工艺和正常工作。
57.基于上述实施例的漏油监测装置,本发明实施例还公开一种高压电缆充油终端的漏油监测方法,包括如下步骤:
58.步骤一、将电容传感器31安装在充油终端1与电缆2交界处的电缆2上,使电容传感器31覆盖电缆2的周向表面;
59.步骤二、在安装完成后,进行初始测量,确定电容传感器31的初始电容值;后续定期通过电容检测模块32检测电容传感器31的电容值;
60.步骤三、当充油终端1出现漏油,漏油从充油终端1与电缆2交界处沿着电缆2流入电容传感器31,电容传感器31吸收漏油,使电容传感器31之间的相对介电常数发生变化,导致电容检测模块32检测到的电容传感器31的电容值发生变化;电容检测模块32将检测到的电容值与与初始电容值相比,计算变化量;
61.步骤四、将变化量的数据传输至数据处理模块33,通过查询数据库,将电容值的变化量换算成漏油的重量,数据库记录电容值的变化量与漏油的重量的对照关系;
62.步骤五、数据处理模块33判断漏油的重量超过设定阈值后发出警报;并缩短电容检测模块32的检测周期,电容检测模块的检测周期可由工作人员事先设定,并由计时器控制,具体控制方法为现有技术,在此不再赘述。
63.以630电缆为例,作为感应层的两块电极板长宽厚=150mm*120mm*0.3mm,包裹电缆的面积=180平方厘米,同时获取等同面积的吸油层,且吸油层的厚度大于感应层的厚度,比如559mm,依附感应层,且吸油层的材质选择聚丙烯,吸附量为7gal./case(26.5l/case);重量:6.2lbs.(2.8kg)。绝缘外壳的材料为高强度塑料,依次将电极板和吸油层放入绝缘外壳内部并固定,在绝缘外壳的外壁固定电容检测模块,并与电极板电连接,而后将两个分部安装在电缆的适合位置,并合拢固定,安装完成后,启动电容检测模块,并与地面的数据处理模块建立通讯连接,开始实时检测。该实施例中,初始电容值为28nf,经实验检测获得,电容值的变化量与漏油重量的对照关系表为:
[0064][0065]
漏油重量的设定阈值为8kg,当漏油重量超过8kg,则控制数据处理模块对上位服务器发出警报,通知工作人员过来检修;当漏油重量在12kg-16kg之间,则将电容检测模块的检测周期从1天缩短为半小时,以加强漏油监测装置对充油终端的监测,及早发现充油终端的严重漏油现象,并督促工作人员尽快检修,排查故障。
[0066]
上述实施方式仅为本发明的优选实施方式,不能以此来限定本发明保护的范围,
本领域的技术人员在本发明的基础上所做的任何非实质性的变化及替换均属于本发明所要求保护的范围。