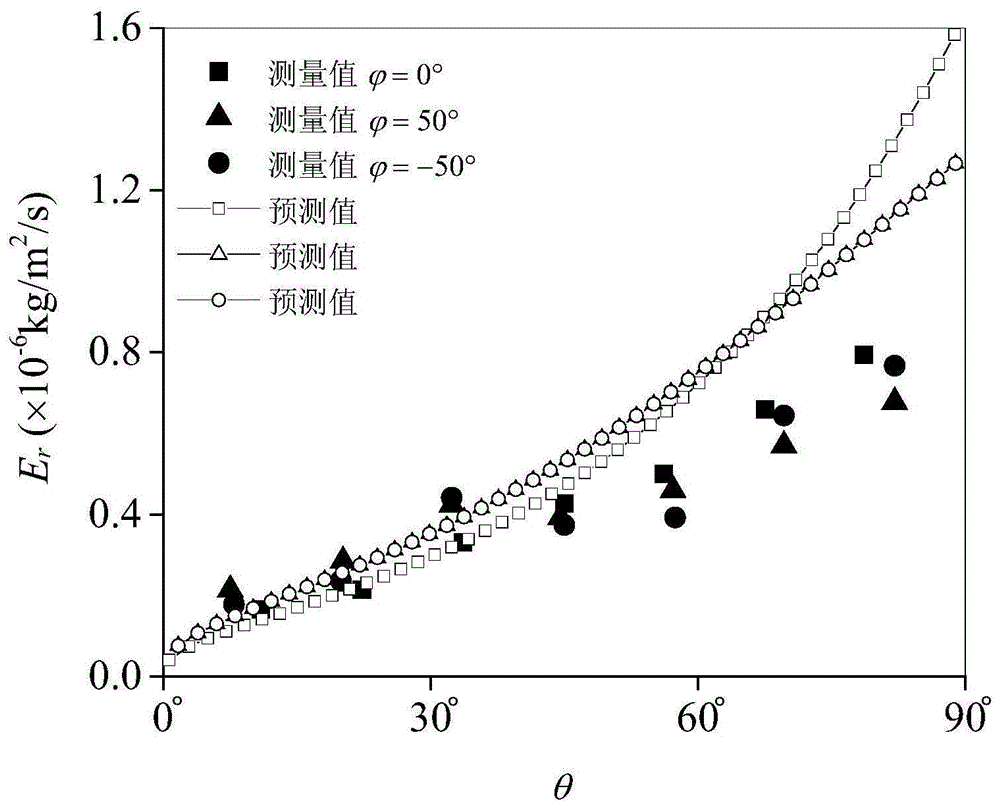
本发明属于固体颗粒冲蚀的显式算法领域,特别涉及该领域中的一种液相弯头中固体颗粒冲蚀的显式算法。
背景技术:
:管道中的固体颗粒冲蚀问题广泛存在于各种工业设备中,如油气输送管线、疏浚吹填设备、旋转除尘器、航空发动机等。管线中的固体颗粒随流体一起高速运动,在流向突然改变处会以较高动量撞击管道内壁,进而造成严重的材料损伤。弯头作为一种常见的改变流体流动方向的部件,最容易出现固体颗粒冲蚀。管道在固体颗粒冲蚀的作用下发生变薄、破裂、流体泄露,会造成严重的生产事故,危害人员安全与周边生态环境。因此,采取一种简单有效的方法分析弯头处的固体颗粒冲蚀,对于指导许多工业领域的装备设计、保养维护具有重要意义。现有的分析弯头处固体颗粒冲蚀的方法主要有两种。第一种方法为基于大量实验数据拟合出来的经验或半经验算法。这种方法一般是颗粒冲蚀理论的延伸,通过实验数据拟合出输送速度指数、角度函数、以及部件形状系数;一些更为精细的模型会基于部件内流场形态,给出颗粒群平均碰撞速度与平均碰撞角度。但此方法并不跟踪弯头中颗粒的运动轨迹,无法反映弯头中颗粒冲蚀的完整机理,故需要使用大量的经验系数,影响了该方法的适用范围与计算精度。第二种方法基于计算流体力学的方法模拟管道内流场,在流场中释放大量离散颗粒并使用拉格朗日方法跟踪颗粒群,最后将受冲蚀面上的颗粒碰撞速度与碰撞角度代入颗粒冲蚀理论计算弯头冲蚀。由于详细分析了弯头颗粒冲蚀过程中的每一个细节,该方法操作较为复杂,一般需要划分网格、迭代运算,在计算过程中需要耗费较大的计算资源,因此并不适用于工程运用。技术实现要素:本发明所要解决的技术问题就是提供一种液相弯头中固体颗粒冲蚀的显式算法。本发明采用如下技术方案:一种液相弯头中固体颗粒冲蚀的显式算法,其改进之处在于,包括如下步骤:(1)求解管道内流场的基本特征:紊流管道的雷诺数re为:式中vm为管流平均速度,d为管道直径,ρf为流体密度,μf为流体粘性;管道的摩阻系数f为:管流的摩阻流速v*为:(2)求解弯头内流场:设弯头内轴向速度分布vif为:其中,vf为弯头上游长直管道中流体的轴向速度,l为弯头中流体微团在平行于弯头对称面的平面上的径向坐标;r为弯头的中心半径;(3)计算颗粒的落点:颗粒在运动平面上的初始径向坐标为l0,入口处的极坐标为以上坐标满足以下关系:则颗粒的碰撞点坐标lhit为:其中θhit为颗粒运动平面上的碰撞点角坐标,dp为颗粒粒径,ρp为颗粒密度;(4)计算颗粒的碰撞速度:颗粒撞击弯头时的轴向与径向速度分别为:轴向径向则颗粒的撞击速度为:其中为弯头的轴向方向,为弯头的径向方向;(5)求解颗粒的碰撞角度:颗粒落点处弯头曲面的法向量为:为管道截面上流体微团的角坐标,θ为颗粒运动平面上的角坐标;则颗粒的碰撞角度φ为:(6)求解颗粒碰撞点处的材料损失比:将颗粒的碰撞速度与碰撞角度代入以下方程:erd=c2(vhitsinφ-vtsh)2er=fs(erc+erd)式中,vhit为颗粒的碰撞速度;er为单位质量颗粒造成的弯头材料质量损失;fs为颗粒形状系数,对于尖锐颗粒fs=1.0,对于圆形颗粒fs=0.2,介于两者之间时fs=0.5;式中其他参数取值见下表:材料碳钢1018碳钢4130无缝钢316无缝钢2205铬钢13镍钢625铝合金6061c15.90×10-84.94×10-84.58×10-83.92×10-84.11×10-84.58×10-83.96×10-8c24.25×10-83.02×10-85.56×10-82.30×10-83.09×10-84.22×10-83.38×10-8κ0.50.40.40.40.50.40.4vtsh5.53.05.82.35.15.57.3(7)求解颗粒撞击处的有效输沙率:若弯头上游管道沿垂直方向,则单位时间单位面积的输沙率cp为:若弯头上游管道沿水平方向,则在重力作用下管道截面上颗粒分布并不均匀,单位时间单位面积的输沙率cp为:式中,g为重力加速度;h为颗粒在弯头入口处沿重力方向的相对坐标,取值在—1与1之间;wp为单位时间管道横截面上的输沙质量;i1为修正的1阶贝塞尔函数;(8)求解入口冲蚀扩散系数:冲蚀扩散系数η即为入口处颗粒的有效活动区域与冲蚀覆盖区域之间的面积比:式中xhit为弯头空间颗粒撞击处的笛卡尔坐标,其与极坐标之间有如下转换关系:xhit=lhitcosθhitzhit=lhitsinθhit其中为颗粒在弯头入口处的极坐标;(9)计算弯头上固体颗粒冲蚀:弯头曲面上任意位置处单位时间单位面积上的材料质量损失er为:er=cpηer。本发明的有益效果是:本发明旨在提供一种计算液相弯头中固体颗粒运动轨迹及造成冲蚀的显式算法,基于相关理论构建了弯头内的近似流场,通过将颗粒运动方程进行简化得到运动轨迹的显式解,追踪颗粒碰撞管壁造成的材料损失。以上过程可将弯头内颗粒冲蚀的微观机理与宏观表现紧密联系起来,由于忽略了对颗粒冲蚀弯头过程影响不大的流场要素,可以有效地节省计算资源。附图说明图1a是使用本发明实施例1所公开显式算法所得的预测结果与实验数据的对比图a;图1b是使用本发明实施例1所公开显式算法所得的预测结果与实验数据的对比图b。具体实施方式为了使本发明的目的、技术方案及优点更加清楚明白,以下结合附图和实施例,对本发明进行进一步详细说明。应当理解,此处所描述的具体实施例仅仅用以解释本发明,并不用于限定本发明。本发明的目的是提供一种计算液相弯头中固体颗粒冲蚀的显式算法,基于简化的弯头内流场,推导出液相弯头中显式的颗粒轨迹,将颗粒碰撞管壁的角度、速度、落点代入颗粒冲蚀理论,即可得到液相弯头中固体颗粒冲蚀的显式解。该算法致力于在一定程度上反映液相弯头中固体颗粒冲蚀的完整机理,并尽量简化分析与计算流程,使其适用于工程应用。为达到以上发明目的,先进行如下的理论分析:(1)近似呈现弯头内的流场,突出影响颗粒轨迹的流场特点。弯头内的流场特性直接影响流场中颗粒的运动特性、分布规律。尽可能精确地模拟出弯头内流场,是准确分析弯头内颗粒冲蚀的基础。弯头上游的紊流流场经充分发展,进入弯头后流场的速度、压力等基本属性发生剧烈变化,欲精确呈现弯头流场的所有细节势必会耗费较高的计算资源。由于弯头内的固体颗粒冲蚀仅与靠近弯头外侧的、能够撞击管壁的那部分颗粒运动规律有关,因此无需模拟出弯头中的所有流场细节,仅关注直接影响弯头内固体颗粒冲蚀的流场特性即可。弯头上游长直管道中流场的轴向速度分布为:式中,vm为管道内流体输送速度;v*为管道内摩阻流速;d为管道直径;r为流体的径向坐标。流体进入弯头后轴向速度剧烈变化,流层之间的切应力可以忽略。因此,流体微团进入弯头后做曲线运动,运动过程中应满足角动量守恒关系。由于在长直管道中流体微团几乎均为直线运动,可以假设这些流体微团运动过程中均拥有相同的虚拟半径r′,即:vifl=vfr′式中,vif为弯头中流体的轴向速度;l为弯头中流体微团在平行于弯头对称面的平面上的径向坐标。弯头中的流体仍然满足质量守恒关系,则:式中,为管道截面上流体微团的角坐标。(2)跟踪颗粒在弯头中的运动,简化运动方程后得到显式解。固体颗粒进入弯头后,一方面会在惯性下保持原有的运动状态,一方面会受到流体拖曳作用致使运动轨迹发生弯曲。由于靠近弯头外侧的固体颗粒几乎不会发生垂直于弯头对称面的运动,因此仅考虑固体颗粒在平行于弯头对称面的平面上的曲线运动即可。在该平面上,颗粒的运动方程为:式中,为弯头的轴向方向、径向方向;mp为固体颗粒质量;f为流体对颗粒的拖曳力;θ为颗粒运动平面上的角坐标。流体对颗粒的拖曳力为:式中,dp为颗粒粒径;ρf、ρp分别为流体与颗粒密度;cd为拖曳力系数;μf为流体粘性;vslip为流体与颗粒间速度差。由式(2.4)-(2.5c)可得颗粒运动方程的分解形式:颗粒进入弯头后,在周围流体作用下轴向速度会逐渐趋近于流体速度;此外,式(2.6b)中离心力项远大于速度变化率项。基于以上结论,可以对颗粒运动方程进行简化进而得到显式解:(3)求解颗粒撞击参数,结合颗粒冲蚀理论计算弯头冲蚀分布。基于颗粒运动轨迹,求解颗粒碰撞管壁时的碰撞角度、碰撞速度以及落点。将颗粒的碰撞速度与碰撞角度代入相关的颗粒冲蚀理论,计算相应颗粒落点处的材料质量损失比。之后基于颗粒初始位置处沙粒的有效活动区域与输沙率,计算颗粒落点处冲蚀的覆盖区域与质量损失。统计从弯头入口处任意点出发的颗粒造成的弯头质量损失,即可得到弯头外部的颗粒冲蚀分布。实施例1,本实施例公开了一种液相弯头中固体颗粒冲蚀的显式算法,包括如下步骤:(1)求解管道内流场的基本特征:紊流管道的雷诺数re为:式中vm为管流平均速度,d为管道直径,ρf为流体密度,μf为流体粘性;管道的摩阻系数f为:管流的摩阻流速v*为:(2)求解弯头内流场:由之前的理论分析可知,弯头内轴向速度分布vif为:其中,vf为弯头上游长直管道中流体的轴向速度,l为弯头中流体微团在平行于弯头对称面的平面上的径向坐标;r为弯头的中心半径;(3)计算颗粒的落点:颗粒在运动平面上的初始径向坐标为l0,入口处的极坐标为以上坐标满足以下关系:则颗粒的碰撞点坐标lhit为:其中θhit为颗粒运动平面上的碰撞点角坐标,dp为颗粒粒径,ρp为颗粒密度;(4)计算颗粒的碰撞速度:颗粒撞击弯头时的轴向与径向速度分别为:轴向径向则颗粒的撞击速度为:其中为弯头的轴向方向,为弯头的径向方向;(5)求解颗粒的碰撞角度:颗粒落点处弯头曲面的法向量为:为管道截面上流体微团的角坐标,θ为颗粒运动平面上的角坐标;则颗粒的碰撞角度φ为:(6)求解颗粒碰撞点处的材料损失比:将颗粒的碰撞速度与碰撞角度代入以下方程:erd=c2(vhitsinφ-vtsh)2er=fs(erc+erd)式中,vhit为颗粒的碰撞速度;er为单位质量颗粒造成的弯头材料质量损失;fs为颗粒形状系数,对于尖锐颗粒fs=1.0,对于圆形颗粒fs=0.2,介于两者之间时fs=0.5;式中其他参数取值见下表:材料碳钢1018碳钢4130无缝钢316无缝钢2205铬钢13镍钢625铝合金6061c15.90×10-84.94×10-84.58×10-83.92×10-84.11×10-84.58×10-83.96×10-8c24.25×10-83.02×10-85.56×10-82.30×10-83.09×10-84.22×10-83.38×10-8κ0.50.40.40.40.50.40.4vtsh5.53.05.82.35.15.57.3(7)求解颗粒撞击处的有效输沙率:若弯头上游管道沿垂直方向,则单位时间单位面积的输沙率cp为:若弯头上游管道沿水平方向,则在重力作用下管道截面上颗粒分布并不均匀,单位时间单位面积的输沙率cp为:式中,g为重力加速度;h为颗粒在弯头入口处沿重力方向的相对坐标,取值在—1与1之间;wp为单位时间管道横截面上的输沙质量;i1为修正的1阶贝塞尔函数;(8)求解入口冲蚀扩散系数:冲蚀扩散系数η即为入口处颗粒的有效活动区域与冲蚀覆盖区域之间的面积比:式中xhit为弯头空间颗粒撞击处的笛卡尔坐标,其与极坐标之间有如下转换关系:xhit=lhitcosθhitzhit=lhitsinθhit其中为颗粒在弯头入口处的极坐标;(9)计算弯头上固体颗粒冲蚀:弯头曲面上任意位置处单位时间单位面积上的材料质量损失er为:er=cpηer。选择以下两组实验数据与本实施例所公开显式算法所得的预测结果进行验证对比,(1)p.frawley,j.corish,a.niven,m.geron,combinationofcfdanddoetoanalysesolidparticleerosioninelbows,int.j.comput.fluiddynamics23(2009)411-426.(2)l.zeng,g.a.zhang,x.p.guo,erosion-corrosionatdifferentlocationsofx65carbonsteelelbow,corros.sci.85(2014)318-330.这两组实验选取了不同的测量方法,参数的取值跨度也较大,所呈现的实验数据具有较高的可信性。对比图如图1a,1b所示,可见本实施例所公开显式算法所得的预测结果具有较高的计算精度。当前第1页12