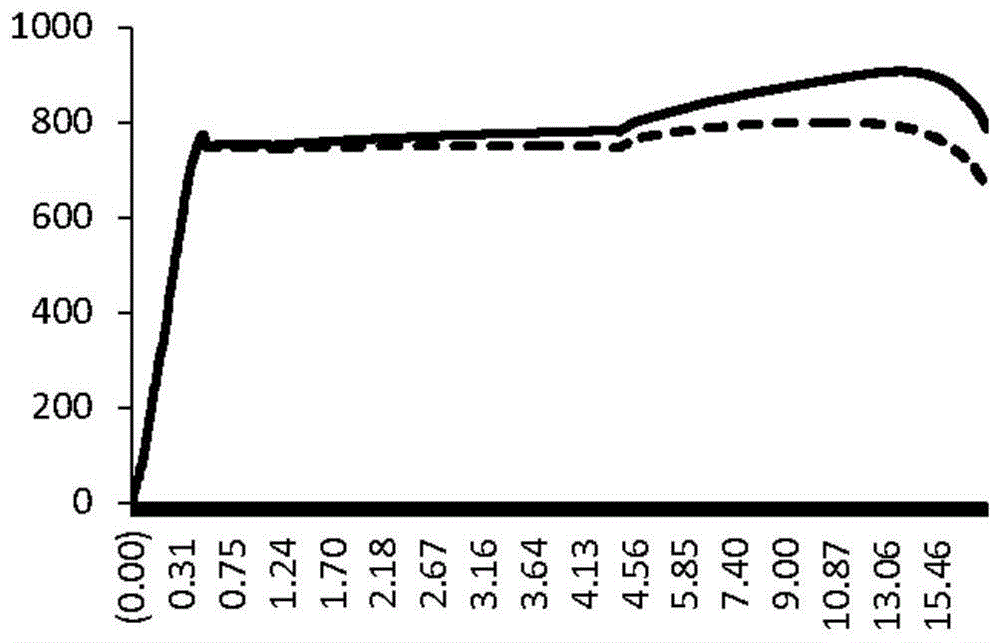
本发明涉及金属加工工艺领域,尤其涉及一种基于有限元仿真的金属板料冲孔工艺参数优化方法。
背景技术:
:金属材料的冲孔加工主要采用模具冲孔的方式,能够在金属板材上快速加工出孔洞特征,冲孔加工工艺参数的选择直接关系到产品的质量和成材率。目前一般采用试验法优化冲孔工艺参数,具体地说,通过反复的调整模具尺寸、冲孔参数最终找到合适的冲孔工艺,此方法需要制作大量的试样,试验过程费时费力。另外,生产厂家也可以参考冲孔国标来指导冲孔模具间隙,但国标只能满足基本的冲孔要求,对于高要求(尺寸精度要求、孔面表面粗糙度、撕裂带宽度等)的孔洞仍需要采用试验法进行冲孔工艺参数的摸索制定。技术实现要素:为了解决以上问题,本发明的目的是提供一种基于有限元仿真的金属板料冲孔工艺参数优化方法,能够高效率、高精度的优化金属板料冲孔工艺参数。为实现上述目的,本发明所设计的基于有限元仿真的金属板料冲孔工艺参数优化方法,包括步骤:(1)建立冲孔几何模型:根据国标要求建立金属板料冲孔过程的冲孔几何模型,在冲孔几何模型中设定冲孔几何参数;(2)建立材料弹塑性本构模型:获取金属板料的工程应力应变曲线,并根据工程应力应变曲线获得真应力-塑性应变曲线,根据真应力-塑性应变曲线建立材料弹塑性本构模型;(3)建立材料断裂失效模型:根据典型的力学性能试验建立材料断裂失效模型;(4)建立冲孔有限元模型:将冲孔几何模型转化为冲孔有限元模型,冲孔有限元模型中设置有冲孔几何参数,然后向冲孔有限元模型的金属板料属性中输入材料弹塑性本构模型和材料断裂失效模型,并设置冲孔工艺参数,最后设置冲孔的输出结果;(5)优化各项参数:在冲孔有限元模型中输入不同的冲孔几何参数和冲孔工艺参数,反复迭代计算,直至输出的冲孔质量满足要求,从而确定最优冲孔几何参数和冲孔工艺参数。作为优选方案,所述步骤(2)中,根据工程应力应变曲线获得真应力-塑性应变曲线后,对真应力-塑性应变曲线拟合外推至应变为1,得到完整真应力-塑性应变曲线,然后再根据完整真应力-塑性应变曲线建立完整的材料弹塑性本构模型。作为优选方案,它还包括材料弹塑性本构模型的标定过程,具体过程为,在完整的材料弹塑性本构模型中设置参数范围输出模拟的力-变形曲线,然后进行单向拉伸试验,监控试验力及拉伸应变形变情况,得到试验的力-变形曲线,对比模拟的力-变形曲线与试验的力-变形曲线,不断修正完整的材料弹塑性本构模型中的参数,以确定最优拟合参数,得到最接近实际的完整的材料弹塑性本构模型。作为优选方案,所述步骤(3)中材料断裂失效模型的具体建立过程为,首先采用全应力状态的方式对金属材料分别进行剪切拉伸、平面应变、缺口拉伸、中心孔拉伸、等轴双拉的典型力学性能试验,读取材料断裂时的断裂应变;然后基于五种典型力学性能试验建立相对应的五种仿真模型,分别提取仿真模型中的失效单元的相关参数信息,结合试验时读取的断裂时的断裂应变,通过基于现象的韧性断裂公式进行拟合,构建得到材料断裂失效模型。作为优选方案,还包括分别采用剪切拉伸、平面应变、缺口拉伸、中心孔拉伸、等轴双拉等试验对得到的材料断裂失效模型进行验证与修正,具体过程为:首先获取每种典型力学性能试验的力-变形曲线,然后再次将材料断裂失效模型和材料弹塑性本构模型添加到仿真模型中,加载与试验相同的边界条件与载荷进行仿真计算,分别提取仿真计算结果中的力-变形曲线,反复比对仿真力-变形曲线和对应的试验力-变形曲线的变化趋势,不断修正材料断裂失效模型的参数,从而获得最接近实际的材料断裂失效模型。作为优选方案,所述步骤(1)中的冲孔几何参数包括冲头直径、凹模内孔直径、板料厚度;所述步骤(4)中,冲孔工艺参数包括接触摩擦系数、压边力大小和冲孔速度。作为优选方案,所述步骤(4)中冲孔的输出结果包括冲孔的直径大小和冲裁断面质量。本发明的优点在于:与现有试验法优化冲孔工艺参数的方法相比,本发明基于有限元仿真的金属板料冲孔工艺参数优化方法通过仿真计算可以快速的完成冲孔模拟计算,不用制作试样,能节省大量的时间、降低试验成本。附图说明图1为工程应力-应变曲线与真应力-塑性应变曲线示意图;图中实线为真应力-塑性应变曲线,虚线为工程应力-应变曲线;图2为完整真应力-塑性应变曲线示意图;图3为单向拉伸试验示意图;图4为修正材料弹塑性本构模型的流程框图;图5为仿真与实验的力-变形对比示意图;其中实线为实验的力-变形曲线,虚线为仿真的力-变形曲线;图6为材料断裂失效模型曲线示意图;图7为冲孔有限元模型输出的应力云图结果示意图,其中1表示冲孔,d表示冲孔的直径;图8为冲孔几何模型的结构示意图,1-冲头,2-压边圈,3-板料,4-凹模。具体实施方式为更好地理解本发明,以下将结合附图和具体实例对发明进行详细的说明。实施例以某6mm钢板冲孔为例,6mm厚700mpa级高强钢板冲压直径10mm孔;基于有限元仿真的金属板料冲孔工艺参数优化方法,包括步骤:(1)建立冲孔几何模型根据国标要求建立金属板料冲孔过程的冲孔几何模型,结合图8所示,冲孔几何模型包含冲头1、压边圈2、板料3及凹模4,在有限元求解软件中直接建模方式,并采用参数化建模,设定冲头直径、凹模内孔直径、板料厚度为参数变量。(2)构建材料弹塑性本构模型(2.1)首先通过单向拉伸试验,获取金属板料的工程应力应变曲线数据,获取的金属材料的工程应力应变曲线,不能真实反映该金属材料的塑性,需要变换为真应力-塑性应变曲线,利用下列公式(1)、公式(2)、公式(3)进行工程应力应变曲线向真应力-塑性应变曲线转变,工程应力应变曲线数据和真应力-塑性应变曲线结合图1所示。ε真=ln(1+ε工程)(1)σ真=σ工程(1+ε工程)(2)其中:ε—应变;σ—应力;e—弹性模量。获得真应力-塑性应变曲线后,剔除颈缩点之后的数据,可采用公式4所示的shs模型进行外延,对金属板料的真应力-塑性应变曲线进行拟合外推,外推至应变为1,得到如图2所示的完整真应力-塑性应变曲线,基于拟合外推得到的完整真应力-塑性应变曲线在有限元软件中建立初步的材料弹塑性本构模型。(2.2)标定材料弹塑性本构模型,在初步的材料弹塑性本构模型中设置参数范围输出模拟的力-变形曲线,然后如图3所示,进行单向拉伸试验,监控试验力及拉伸应变形变情况,得到试验的力-变形曲线,如图4所示的修正流程图,对比模拟的力-变形曲线与试验的力-变形曲线,不断修正材料弹塑性本构模型中的相关参数,以确定最优拟合参数,得到最接近实际的完整的材料弹塑性本构模型。(3)构建材料断裂失效模型:金属板料在冲孔过程中,首先会发生大的弹塑性变形,此阶段材料状态可用材料弹塑性本构模型表征,当变形超过极限时材料会发生断裂,因此需构建材料断裂失效模型以表征材料在断裂过程中的应力应变状态。(3.1)采用全应力状态的方式进行5种典型力学性能试验,包含剪切拉伸、平面应变、缺口拉伸、中心孔拉伸、等轴双拉,采用全应变场静态测量系统对试验过程进行实时监控,并读取材料断裂时的断裂应变。基于5种典型力学性能试验建立与五种试验对应的仿真模型,分别为剪切拉伸仿真模型、平面应变仿真模型、缺口拉伸仿真模型、中心孔拉伸仿真模型、等轴双拉仿真模型,分别提取上述五种仿真模型中的失效单元的相关参数信息,结合试验时读取的断裂时的断裂应变,通过基于现象的韧性断裂公式进行拟合,构建得到材料断裂失效模型。(3.2)验证与修正材料断裂失效模型,首先获取剪切拉伸试验的力-变形曲线;然后将材料断裂失效模型和材料弹塑性本构模型添加到剪切拉伸仿真模型中,加载与试验相同的边界条件与载荷进行仿真计算,分别提取仿真计算结果中的力-变形曲线,反复比对仿真力-变形曲线和剪切拉伸试验力-变形曲线的变化趋势(如图5所示,将仿真的力-变形曲线与试验的力-变形曲线比对),若趋势重合度高则表明剪切拉伸时材料断裂失效模型与实际相接近,若力-变形曲线变化趋势相差较大则需重新进行拟合,需修正材料失效模型参数,不断调整、比对、优化;采用平面应变、缺口拉伸、中心孔拉伸、等轴双拉等试验验证的步骤与上述的剪切拉伸试验相同,在此不再赘述,过程参数及材料模型参数如表1、表2,其中表1中a、b、c、d表示过程参数,最终获得如图6所示的最接近实际的材料断裂失效模型。表1五种试验过程中材料断裂参数表参数abcd剪切拉伸0.1420.9920.0390.093平面应变0.7920.4620.6150.588缺口拉伸0.8870.5860.5580.693中心孔拉伸0.9890.6020.4630.934等轴双拉0.8561.0350.6310.712表2材料失效模型参数值表(4)构建冲孔有限元模型:将步骤(1)的冲孔几何模型转化为冲孔有限元模型,并完成划分网格,板料冲孔部位的网格尺寸尽可能细;冲孔有限元模型具有冲头直径、凹模内孔直径、板料厚度的参数设置,然后设置材料属性,金属板料属性中输入材料弹塑性本构模型和材料断裂失效模型,其他部件均设置为刚性材料;选用合适单元类型;接触部位均设置接触,设置摩擦类型和摩擦系数;设置边界条件;设置分析步,采用显式动力算法;设置施加载荷参数,包括压边力和冲孔速度;设定输出等一系列有限元常规操作。(5)求解计算、评估结果、优化各项参数:在冲孔有限元模型中输入冲头直径、凹模内孔直径、板料厚度、冲孔速度、压边力大小、接触摩擦系数,在有冲孔有限元模型进行求解计算,完成计算后查看如图7所示的输出结果,输出结果可测量得到冲孔1的直径尺寸大小、可查看冲孔1的冲裁断面质量。在冲孔有限元模型中输入不同的冲头直径、凹模内孔直径、板料厚度、冲孔速度、压边力大小、接触摩擦系数,反复迭代计算,直至输出的孔尺寸大小和冲裁断面质量满足要求,从而确定最优冲孔参数:6mm厚700mpa级高强钢板冲压直径10mm孔最佳工艺参数:冲头直径10mm;凹模内孔直径11.32mm;冲孔速度4m/s;压边力大小:压边力确保接触压力>2.8mpa;接触摩擦系数<0.15。与现有试验法优化冲孔工艺参数的方法相比,本发明基于有限元仿真的金属板料冲孔工艺参数优化方法具有以下优点:(1)本发明通过仿真计算可以快速的完成冲孔模拟计算,不用制作试样,能节省大量的时间、降低试验成本。(2)本发明分别建立冲孔几何模型和材料模型(材料模型包括材料弹塑性本构模型和材料断裂失效模型),然后将材料模型添加到冲孔几何模型中进行求解计算,设计思路清晰明确,得到的输出结果科学可靠。(3)本发明在材料弹塑性本构模型和材料断裂失效模型的构建中,均采用模拟的力-变形曲线与试验的力-变形曲线的对比修正方法,使得到的材料弹塑性本构模型和材料断裂失效模型更加精确。以上所述实施例仅表达了本发明的几种实施方式,其描述较为具体和详细,但并不能因此而理解为对本发明专利范围的限制。应当指出的是,对于本领域的普通技术人员来说,在不脱离本发明构思的前提下,还可以做出若干变形和改进,这些都属于本发明的保护范围。因此,本发明专利的保护范围应以所附权利要求为准。当前第1页12