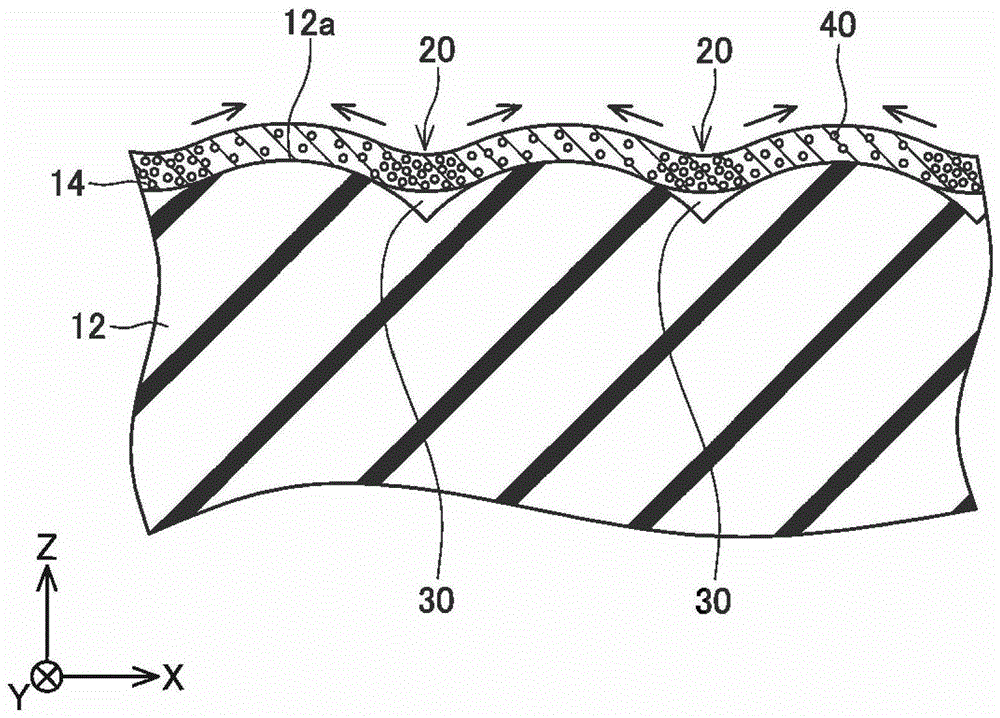
本发明涉及压电元件。
背景技术:压电元件具有陶瓷基板和形成在该陶瓷基板的表面上的电极。若在压电元件的陶瓷基板上施加外力,则陶瓷基板形变,在电极上产生电压(压电效应)。另外,若在压电元件的电极上施加电压,则电场施加在陶瓷基板上,陶瓷基板形变(逆压电效应)。再者,在日本特开2005-72325号公报中公开了具有多个内部电极的压电元件。在想要得到上述压电效应或逆压电效应时,因形成在陶瓷基板的表面上的电极的刚性而阻碍了陶瓷基板的形变。由此,出现陶瓷基板的形变量减少,且压电元件难以形变的问题。例如,在想要得到压电效应时,如果压电元件难以形变,则相对于施加在压电元件上的力,产生的电压变小。另外,在想要得到逆压电效应时,如果压电元件难以形变,则相对于施加在压电元件上的电压,产生的形变量变小。
技术实现要素:因而,在本说明书中,提供一种具有难以阻碍陶瓷基板的形变的电极的压电元件。本说明书所公开的压电元件具有陶瓷基板和电极,所述陶瓷基板在表面上形成有槽,所述电极形成在所述陶瓷基板的所述表面上且跨越所述槽延伸。在所述槽的底面与跨越该槽的部分的所述电极之间,形成有至少一个间隙。在该压电元件中,在槽的底面和电极之间形成有间隙。即,电极在槽的底面不与陶瓷基板接触。该不与陶瓷基板接触的部分的电极比与陶瓷基板接触的部分的电极能够更柔软地变形。因此,很难因电极阻碍陶瓷基板的形变。因而,该压电元件容易形变。另外,本说明书提供新的压电元件的制造方法。该制造方法包括:在形成有槽的陶瓷基板的表面上形成跨越所述槽而延伸的电极的工序;以及通过加热陶瓷基板,使电极从槽的底面剥离的工序。根据该制造方法,能够制造具有跨越槽的部分不与陶瓷基板接触的电极的压电元件。附图说明图1是实施例的压电元件10的纵剖视图。图2是电极14和陶瓷基板12的边界部分的放大剖视图。图3是与图2相对应的剖面的电子显微镜照片。图4是陶瓷基板12的上表面12a的电子显微镜照片。图5是表示压电元件10的制造方法的流程图。图6是比较例的压电元件的电极14和陶瓷基板12的边界部分的放大剖视图。图7是与图6相对应的剖面的电子显微镜照片。图8是表示各压电元件的评价结果的表。图9是变形例的压电元件的电极14和陶瓷基板12的边界部分的剖面的电子显微镜照片。具体实施方式也可以在电极的内部形成比槽的底部的至少一个间隙还小的微细孔。根据该结构,电极整体能够更柔软地变形。因此,能够得到更易形变的压电元件。也可以使跨越槽的部分的电极内的微细孔的体积比率高于没有跨越槽的部分的电极内的微细孔的体积比率。根据该结构,跨越槽的部分的电极能够更柔软地变形。因此,能够得到更易形变的压电元件。电极的厚度也可以是50nm以上且500nm以下。根据该结构,由于电极的厚度足够薄,因此电极能够更柔软地变形。因此,能够得到更易形变的压电元件。形成间隙的槽也可以是在烧成陶瓷基板时形成在烧成面上的槽。该槽在烧成陶瓷基板时自然地形成在陶瓷基板的烧成面上。如果使用该槽,则能够很容易地形成间隙。槽也可以沿着出现在所述陶瓷基板的上表面上的晶粒的边界形成。间隙也可以在陶瓷基板的表面上形成多个。压电元件也可以用作利用了d31方向的形变的驱动器。也可以在相对于陶瓷基板的所述表面成为相反侧的表面的背面上形成槽。进而还可以具有形成在背面上,且跨越背面的槽延伸的电极。也可以在背面的槽的底面和跨越该槽的部分的电极之间形成至少一个间隙。根据该结构,陶瓷基板由一对电极夹住。由于一对电极的双方能够柔软地变形,因此能够得到更易形变的压电元件。也可以在陶瓷基板的背面形成多个间隙。一对电极面对的方向也可以是陶瓷基板的厚度方向。即,一对电极也可以是产生施加在陶瓷基板上的电场之中最高的电场的电极。例如,利用d33方向的形变的压电元件有时具备多个内部电极。在这种压电元件的端面上形成有用于相互连接内部电极的电极(配线)。上述一对电极与形成在利用d33方向的形变的压电元件的端面上的电极不同。槽的底面与电极之间的间隙也可以沿着槽延伸。实施例如图1所示,实施例的压电元件10具备陶瓷基板12、电极14和电极16。电极14形成在陶瓷基板12的上表面12a上。电极16形成在陶瓷基板12的下表面12b上。陶瓷基板12由压电体构成。再者,以下,有时将陶瓷基板12的厚度方向称为Z方向,将与Z方向正交的一个方向(沿着陶瓷基板12的上表面的方向)称为X方向,将相对于X方向及Z方向这双方正交的方向称为Y方向。再者,对于压电元件10,由从电极14朝向电极16的方向的电场实施了极化处理。若在电极14和电极16之间施加电极14成为高电位的电压,则相对于陶瓷基板12沿着Z方向施加电场。于是,陶瓷基板12如箭头100所示那样向Z方向膨胀,同时如箭头102所示那样向X方向及Y方向收缩。压电元件10被用作利用了X方向的形变的驱动器。即,压电元件10是利用了施加在陶瓷基板12上的电场的方向(即,Z方向)与驱动器的驱动所采用的形变的方向(即,X方向)大致正交的d31方向的形变的压电元件。图2是压电元件10的纵剖视图,放大表示陶瓷基板12和电极14的边界面。另外,图3表示与图2相对应的区域的压电元件10的电子显微镜照片。如图2、3所示,在陶瓷基板12的上表面12a上形成有多个槽20。图4表示陶瓷基板12的上表面12a的电子显微镜照片。在陶瓷基板12中存在多个晶粒22,如图4所示,晶粒22出现在陶瓷基板12的上表面12a上。槽20沿着出现在陶瓷基板12的上表面12a上的晶粒22的边界(晶界)形成。槽20在烧成陶瓷基板12的过程中形成在其烧成面上。在此所说的“烧成面”只要是在上述烧成工序中烧成的陶瓷基板12的面,则没有特别地限定,在仅指陶瓷基板12的上表面12a的情况和指陶瓷基板12的上表面12a及下表面12b这双方的情况下,都能够使用。如图2、3所示,电极14沿着陶瓷基板12的上表面12a的凹凸形成。只是,电极14不与槽20的底面接触。再者,在此所说的槽20的底面指的是槽20的最深部的表面。在电极14和槽20的底面之间形成有间隙30。间隙30沿着槽20延伸。各间隙30的宽度(平行于陶瓷基板12的上表面12a的方向的宽度(在图2中是X方向的尺寸))是260nm~500nm左右,其平均值约为330nm。另外,各间隙30的深度(Z方向的尺寸)约为54nm~110nm左右,其平均值约为80nm。另外,电极14的厚度是100nm~370nm左右。在电极14的内部形成有多个微细孔40。微细孔40是直径约为20nm~80nm左右的间隙。微细孔40的体积比形成在槽20的底面上的间隙30的体积小得多。再者,微细孔40的尺寸根据位置而不同。跨越槽20的部分的电极14(即,间隙30的上部的电极14)的内部的微细孔40的直径是30~80nm左右,其平均值约为45nm。相对于此,没有跨越槽20的部分的电极(与陶瓷基板12接触的部分的电极14)的内部的微细孔40的直径是20~60nm左右,其平均值约为35nm。即,微细孔40的直径的平均值是跨越槽20的部分的电极14的一方大于没有跨越槽20的部分的电极14的一方。另外,电极14内的微细孔40的体积比率也是跨越槽20的部分的一方大于没有跨越槽20的部分。跨越槽20的部分的电极14的内部的微细孔40的体积比率约为8%。相对于此,没有跨越槽20的部分的电极14的内部的微细孔40的体积比率约为4%。陶瓷基板12的下表面12b侧的电极16形成为与上表面12a侧的电极14大致相同。即,在陶瓷基板12的下表面12b上也形成有多个槽20,电极16以跨越下表面12b的槽20的方式形成。在下表面12b的槽20的底面和电极16之间形成有间隙30。另外,在电极16的内部形成有微细孔40。电极16的内部的微细孔40比电极16和槽20的底面之间的间隙30小得多。微细孔40的尺寸及体积比率都是跨越槽20的部分的电极16一方大于没有跨越槽20的部分的电极16。接下来,说明压电元件10的制造方法。图5是表示压电元件10的制造方法的流程图。首先,在步骤S2中,以压电体为主要原料的生片成型为板状。在此,将生片的表面形成得大致平坦。在步骤S4中,将生片加热。由此,生片被脱溶剂及烧成,从而得到陶瓷基板12。在烧成中,陶瓷基板12多结晶化,并在陶瓷基板12中形成晶粒。由此,在陶瓷基板12的表面上形成槽20。这时的陶瓷基板12的表面粗糙度以Ra是0.01~0.1um。在步骤S6中,在陶瓷基板12的上表面12a及下表面12b上均匀地涂敷树脂酸金。在本实施例中,通过网板印刷或旋转涂敷法涂敷树脂酸金。通过之后的干燥,有机溶剂挥发,形成树脂酸金的干燥膜。再者,树脂酸金是由溶解在有机溶剂中的Au(金)的有机金属化合物构成的糊料。另外,在树脂酸金中添加有微量的玻璃成分,以使得后述的Au膜相对于陶瓷基板12很好地粘合。再者,在本实施例中,虽然说明了使用了树脂酸金的例子,但作为有机金属化合物也可以使用含有Pt(铂)或Cu(铜)的树脂盐酸。在步骤S8中,用带式烧成炉加热陶瓷基板12。带式烧成炉是以陶瓷基板12通过炉内的方式构成的烧成炉。当陶瓷基板12在炉内移动时,用预定的温度曲线加热陶瓷基板12。带式烧成炉内的最高温度设定为约600℃。陶瓷基板12一进入带式烧成炉就被升温,并在约600℃的温度时维持预定时间。在升温过程中,树脂酸金中的有机成分被脱溶剂。之后,当陶瓷基板12达到约600℃的最高温度时,由于玻璃熔融,Au烧结,从而在陶瓷基板12的上表面12a及下表面12b上形成Au膜。该Au膜就是电极14、16。通过使树脂酸金中的有机成分脱溶剂,能够形成厚度薄至100~370nm左右且在内部具有多个微细孔40的电极14、16。若用带式烧成炉加热电极14、16,则认为电极14、16以如下的方式变形。即,若加热电极14、16,则如上所述,电极14、16中的有机成分被脱溶剂,在电极14、16内形成多个比较大的间隙40。之后,若电极14、16被加热到约600℃,则由于Au原子在电极14、16的内部烧结,因此电极14、16收缩。随着电极14、16收缩,间隙40变小,同时间隙40的个数减少。另外,随着电极14、16的收缩进行,电极14、16的厚度变薄。这时,由于电极14、16的烧结向由陶瓷基板12的槽20包围的高的部分进行,因此如图2的箭头所示,收缩还向远离槽20的方向发生。其结果,槽20内的电极14、16从槽20的底面剥离,形成间隙30。另外,由于电极14、16如此收缩,因此在跨越槽20的部分的电极14、16内,暂且变小的微细孔40扩大。因此跨越槽20的部分的电极14、16内的微细孔40的体积比率变高。另外,若持续提高步骤S8的最高温度,则微细孔40彼此相连的比例以及微细孔40贯通电极14、16而与间隙30及电极14、16的外部连通的比例增加。其结果,陶瓷基板12的外表面经由微细孔40露出于电极14、16的外部的比例增加。在步骤S10中,切割陶瓷基板12,从而分割成多个压电元件10。这样就制造出了上述压电元件10。接下来,与比较例1、2的压电元件比较而说明实施例的压电元件的特性。在图6、7中,表示了比较例1、2的压电元件的纵剖面(在比较例1和比较例2中,压电元件的剖面结构大致相同)。比较例1、2的压电元件是对于与实施例的压电元件相同的陶瓷基板12通过溅射来形成电极14、16的部件。再者,电极14、16由形成在陶瓷基板12上的Ni-Cr膜(镍和铬的合金的膜)和形成在Ni-Cr膜上的Au膜构成。另外,比较例1的压电元件是在大致常温下进行溅射而形成电极14、16,比较例2的压电元件是在将陶瓷基板12加热到约230℃的同时进行溅射而形成了电极14、16。如图6、7所示,通过溅射,形成密合在包括槽20内的陶瓷基板12的表面整体上的电极14、16。即,在比较例1、2的压电元件10中,在槽20内没有形成间隙30。另外,通过溅射形成致密的电极14、16。即,在比较例1、2的压电元件10的电极14、16内没有形成微细孔40。图8表示对于实施例的压电元件和比较例1、2的压电元件评价c轴晶畴取向率和形变量的结果。在此,评价了在制造后进行250℃的高温老化试验且之后实施了极化处理的样品、和在制造后没有进行高温老化试验但实施了极化处理的样品。再者,图8的c轴晶畴取向率是通过对各压电元件的陶瓷基板12进行X射线衍射而分别测定晶体的c轴的衍射强度Ic和晶体的a轴的衍射强度Ia,并由Ic/(Ia+Ic)的公式算出的值。c轴晶畴取向率高表示在陶瓷基板12中存在很多c轴沿着电场的施加方向的晶体。因而,c轴晶畴取向率高意味着陶瓷基板12中的晶体的晶畴旋转难以发生,并且在施加电场时陶瓷基板12要形变的量较小。已知如果陶瓷元件中所产生的压缩应力大,则c轴晶畴取向率变大。再者,c轴晶畴取向率只表示陶瓷基板12的特性。各压电元件的实际的形变难易度不只是根据陶瓷基板12,还根据电极14、16的结构而变化。另外,图8的形变量通过在各压电元件的电极14、16之间施加预定的电压,并检测X方向的形变量(尺寸的变化量)而测定。图8的形变量是表示压电元件的形变难易度的值。首先,说明未实施高温老化试验的各压电元件的特性。如图8所示,未实施高温老化试验的样品的c轴晶畴取向率虽然是实施例的压电元件一方远高于比较例1的压电元件,可是未实施高温老化试验的样品的形变量还是实施例的压电元件一方高于比较例1的压电元件。即,在未实施高温老化试验的样品中,虽然陶瓷基板12是实施例的压电元件一方要形变的量小于比较例1的压电元件,可是实际的形变量还是实施例的压电元件一方高于比较例1的压电元件。认为这是由电极结构的不同引起的。即,在比较例1的压电元件中,电极14、16密合在陶瓷基板12上,同时电极14、16是致密的。因此,陶瓷基板12的形变被电极14、16阻碍。相对于此,在实施例的压电元件中,由于在电极14、16中形成有间隙30及微细孔40,因此电极14、16容易配合陶瓷基板12的形变而伸缩。因而,在实施例的压电元件中,形变量变大。再者,已实施高温老化试验的比较例2的压电元件,虽然c轴晶畴取向率稍微高于实施例的压电元件,可是形变量比实施例的压电元件小得多。认为这也是由电极结构的不同引起的(即,比较例2的压电元件的电极14、16是致密的)。另外,未实施高温老化试验的样品的c轴晶畴取向率是在实施例的压电元件和比较例2的压电元件中高。认为这是由于在实施例和比较例2的压电元件的制造工序中,在形成电极14、16时,加热了陶瓷基板12。即,在制造工序中,在形成电极14、16时,若对陶瓷基板12加热,则陶瓷基板热膨胀。电极14、16相对于热膨胀的状态的陶瓷基板12粘合,并且陶瓷基板12和电极14、16一体化。之后,当冷却到常温时,电极14、16和陶瓷基板12共同收缩。由于作为金属材料的电极14、16热膨胀率比陶瓷基板12大,因此电极14、16的收缩量也大于陶瓷基板12的收缩量。因而,若将压电元件从电极14、16和陶瓷基板12粘合的温度冷却到常温,则在陶瓷基板12上产生压缩应力。因此,认为实施例和比较例2的压电元件在极化处理前的c轴晶畴取向率大。再者,在制造工序中,实施例的压电元件的电极14、16被暴露的温度约为600℃。相对于此,比较例2的压电元件的电极14、16被暴露的温度约为230℃,低于实施例。但是,c轴晶畴取向率是实施例的压电元件一方低于比较例2的压电元件。认为这是由于在实施例的压电元件的制造工序中,由于电极14、16从陶瓷基板12的槽20的底面剥离、以及在电极14、16中形成微细孔40,从而抑制了在陶瓷基板12上产生的压缩应力。另外,未实施高温老化试验的比较例1的压电元件的c轴晶畴取向率极低。认为这是由于比较例1的压电元件的电极14、16在制造工序中没有加热陶瓷基板12,因此没有产生由上述热膨胀差引起的对于陶瓷基板12的压缩应力。接下来,说明由高温老化试验引起的各压电元件的特性的变化。比较例1的压电元件的c轴晶畴取向率是已实施高温老化试验的样品一方比未实施高温老化试验的样品大得多。认为这是由于比较例1的压电元件的电极14、16在制造工序中没有被暴露到高温,因此在高温老化试验中,以电极14、16中的Au原子成为细密状态的方式产生大的原子的再配列,并且电极14、16收缩。即,在高温老化试验中,由于电极14、16收缩,因此在陶瓷基板12中产生压缩应力,c轴晶畴取向率上升。再者,在比较例1的压电元件中,由于电极14、16的整体相对于陶瓷基板12密合,因此如图6的箭头所示,电极14、16的整体向其中心收缩。另外,由于在电极14、16中没有形成微细孔,因此由电极14、16的收缩产生的力直接传递给陶瓷基板12。因此,在陶瓷基板12上施加极高的压缩应力。其结果,通过高温老化试验,比较例1的压电元件的c轴晶畴取向率上升得很多。比较例2的压电元件的c轴晶畴取向率虽然不像比较例1那样,但已实施高温老化试验的样品一方也大于未实施高温老化试验的样品。认为在制造工序中,接受了230℃的热处理的比较例2的电极14、16在高温老化试验中,也以Au原子成为细密状态的方式产生原子的再配列,并进行一定程度的收缩。相对于此,在实施例的压电元件中,在未实施高温老化试验的样品和已实施高温老化试验的样品之间,c轴晶畴取向率大致相等。认为这是由实施例的电极14、16中的间隙30及微细孔40的作用引起的。即,在实施例的压电元件中,由于形成有间隙30,因此在槽20的底部,电极14、16不与陶瓷基板12接触。因此,如图2的箭头所示,在由槽20包围的区域内,电极14、16收缩,并很难产生跨越槽20的收缩。另外,由于在电极14、16中形成有微细孔40,因此电极14、16在一定程度上容易变形。进而,由于跨越槽20的部分的电极14、1不与陶瓷基板12接触,并且微细孔40的体积比率高,因此能够更柔软地变形。因此认为,即便电极14、16由于Au原子的再配列而收缩,压缩应力也很难作用于陶瓷基板12。进而,实施例的电极14、16在制造工序中被暴露在600℃的温度。因此,认为在高温老化试验中,由Au原子的再配列引起的电极14、16的收缩量小于比较例1、2。由此,认为压缩应力很难作用于陶瓷基板12。正如以上说明,在实施例的压电元件中,在高温老化试验中,c轴晶畴取向率几乎没有变化。因此,在已实施高温老化试验的样品中,实施例的压电元件的c轴晶畴取向率最低。如上所述,在比较例1、2的压电元件中,由于通过高温老化试验,c轴晶畴取向率上升,因此通过高温老化试验,形变量降低。相对于此,在实施例的压电元件中,由于通过高温老化试验,c轴晶畴取向率几乎没有变化,因此通过高温老化试验,形变量几乎没有变化。如此,实施例的压电元件在制造后即便被暴露在高温,特性几乎没有变化。实施例的压电元件相对于温度极其稳定。因此,在已实施高温老化试验的样品中,实施例的压电元件的形变量比比较例1、2的压电元件的形变量明显高。如以上说明,实施例的压电元件由于在槽20的底部和电极14、16之间形成有间隙30,因此间隙30的上部的电极14、16能够柔软地变形。另外,由于在电极14、16内形成有多个微细孔40,因此电极14、16整体能够柔软地变形。另外,由于在跨越槽20的部分的电极14、16中微细孔40的体积比率高,因此该部分的电极14、16尤其能够柔软地变形。因而,电极14、16很难阻碍陶瓷基板12的形变。因此该压电元件形变量高。进而,由于电极14、16能够柔软地变形,因此即便由于热而在电极14、16上产生收缩,也很难在陶瓷基板12上产生压缩应力。因而,实施例的压电元件即便被暴露到高温,形变量也很难降低。进而,由于实施例的压电元件的电极14、16在制造工序中被暴露到高温,因此之后即便被暴露到高温,也很难收缩。由此,实施例的压电元件在暴露到高温时形变量很难降低。另外,在实施例的制造方法中,若将电极14、16暴露到高温,则电极14、16收缩,电极14、16从槽20的底面剥离。因而,在制造工序中,虽然将电极14、16暴露到高温(即,虽然电极14、16收缩),也没有在陶瓷基板12上产生高的压缩应力。因而,根据该制造方法,能够制造形变量高,且即便暴露到高温特性也很难变化的压电元件。再者,间隙30及微细孔40不一定必须形成在电极14、16的整体上。即便在电极14、16的一部分上形成间隙30及微细孔40,也能够在该部分上得到上述效果。另外,在只在电极14、16的任一方上形成间隙30及微细孔40的情况下,也能够得到上述效果。另外,在图5的步骤2中,也可以通过在进行了表面粗糙化处理的载带上进行生片成型,将载带表面状态复印在生片上。之后,通过与实施例1同样地实施各制造工序,如图9所示,能够制造具有表面进行了粗糙化的陶瓷基板12的压电元件。再者,图9的陶瓷基板12的表面粗糙度以Ra为0.1~1.0um左右。在图9的结构中,也沿着晶界的槽20形成有间隙30。另外,在上述实施例的制造方法中,在烧成面的槽20(即,沿着晶界延伸的槽20)内形成了间隙30。但是,也可以通过加工来形成用于形成间隙30的槽。例如,也可以在图5的步骤4之后,通过机械加工(研磨或切削等)在陶瓷基板12的表面上形成微小的槽。之后,如果与实施例同样地实施步骤S6、S8,则在通过机械加工形成的槽内形成间隙30。另外,也可以在图5的步骤2中,在生片的表面上按压成型模来形成槽。通过烧成形成了槽的生片,得到在表面上具有槽的陶瓷基板12。之后,如果与实施例同样地实施步骤S6、S8,则在由成型模形成的槽内形成间隙30。另外,在上述实施例中,说明了电极14、16的厚度为100nm~370nm的情况。只要电极14、16是这种程度的厚度,就能够有效地抑制陶瓷基板12内的压缩应力。再者,如果电极14、16的厚度为50nm~500nm,能够抑制对陶瓷基板12产生压缩应力的情况。另外,在上述实施例的步骤S8中,用约600℃的温度热处理陶瓷基板。但是,也可以用其他的温度进行热处理。只是,如果热处理温度超过750℃,则由于电极的收缩,跨越槽的部分的电极有可能断裂。另外,如果热处理温度低于550℃,则电极和陶瓷基板的连接强度有可能变弱。因而,优选的是热处理温度在550℃以上且750℃以下。以上,详细地说明了本发明的具体例,但这些只不过是例示,并不限定权利要求书。在权利要求书所记载的技术中,包括将以上例示的具体例进行各种变形、变更的方案。本说明书和附图所说明的技术要素是单独或以各种组合来发挥技术上的有效性的要素,并不限定于申请时权利要求所记载的组合。另外,本说明书和附图所例示的技术是同时达到多个目的的技术,达到其中一个目的自身就具有技术上的有效性。