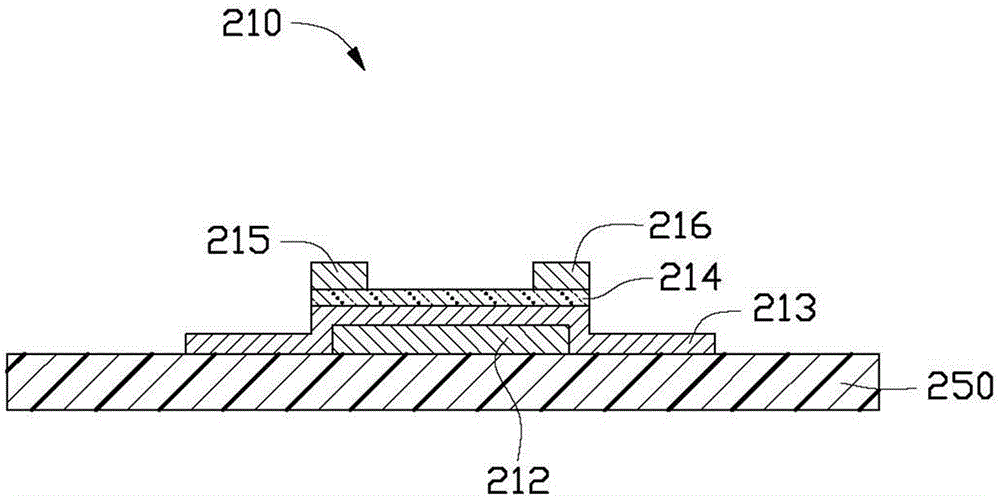
本发明涉及一种薄膜晶体管及其制备方法、薄膜晶体管面板以及显示装置。
背景技术:
:随着信息技术的飞速发展,平板显示技术正向着更高分辨率、更快响应速度、更低能耗、全透明器件以及柔性显示等目标发展,这也对有源驱动显示(如AMLCD,ActiveMatrixLiquidCrystalDisplay)中TFT(thinfilmtransistor)器件的性能提出更高要求。传统的非晶硅TFT由于其迁移率较低(~0.5cm2V-1s-1)的特性不能满足高分辨率、大尺寸LCD的显示要求,更限制其在AMOLED(ActiveMatrixOrganicLightEmittingDiode)显示中的应用。而低温多晶硅TFT虽然迁移率较高,但是其生产成本过高,大面积均匀性较难保证,不适合应用于大面积、高分辨显示器。相较于非晶硅TFT和低温多晶硅TFT,基于非晶氧化物半导体InGaZnO4的薄膜晶体管(IGZO-TFT)以其透过率高、制备温度低、工艺兼容性好等诸多优点,能够替代非晶硅TFT,并且有望用于透明显示以及OLED显示。然而,IGZO-TFT器件迁移率在非晶硅TFT和低温多晶硅TFT之间,若能进一步提高IGZO-TFT的器件迁移率,其优势将更明显。研究发现,二元氧化物氧化铟锌(IZO)的迁移率远大于三元氧化物IGZO,但由于其载流子浓度过高,且在使用中易受光照及栅压等影响导致性能参数发生变化,即稳定性差,因此不适合制备TFT器件。技术实现要素:有鉴于此,确有必要提供一具有迁移率较高且稳定性较好的氧化物半导体膜的薄膜晶体管及其制备方法、薄膜晶体管面板以及显示装置。一种薄膜晶体管,包括半导体层、源极、漏极、栅极及绝缘层,该源极与漏极间隔设置,该半导体层与该源极和漏极电连接,该栅极通过该绝缘层与该半导体层、源极及漏极绝缘设置,该半导体层为一氧化物半导体膜,该氧化物半导体膜含有铟元素(In)、铈元素(Ce)、锌元素(Zn)及氧元素(O),该In:Ce:Zn的摩尔比为2:(0.5~2):1,氧化物半导体膜为n型半导体,载流子浓度为1012cm-3~1020cm-3,载流子迁移率为5.0cm2V-1s-1~45.0cm2V-1s-1。一种薄膜晶体管的制备方法,包括在绝缘基底上制备半导体层、源极、漏极、栅极及绝缘层的步骤,该制备半导体层的步骤包括使用一溅射靶,通过溅射法在基底上溅射形成氧化物膜的步骤,该溅射靶含有化合物In2CexZnO4+2x,其中x=0.5~2。一种薄膜晶体管面板,包括一绝缘基板;多个源极线,该多个源极线位于绝缘基板表面并按行相互平行设置;多个栅极线,该多个栅极线位于绝缘基板表面并按列相互平行设置,该多个栅极线与该多个源极线交叉并绝缘设置,从而将该绝缘基板表面划分成多个网格区域;多个像素电极,每一像素电极设置于每一网格区域中;以及多个上述薄膜晶体管,每一薄膜晶体管设置于每一网格区域中,该薄膜晶体管包括一源极、一与该源极间隔设置的漏极、一半导体层、以及一栅极,该源极与一源极线电连接,该漏极与一像素电极电连接,该半导体层与该源极和漏极电连接,该栅极通过一绝缘层与该半导体层、源极及漏极绝缘设置并与一栅极线电连接。一种显示装置,包括上述薄膜晶体管面板。与现有技术相比,三元氧化物ICZO中铈(Ce)元素的加入不仅能降低载流子浓度,同时还能保证高迁移率,从而具有较好的半导体性能,适合用于制备薄膜晶体管,用于薄膜晶体管面板及平板显示装置中。另外,由于In、Ce及Zn均可在室温进行溅射,该溅射形成半导体膜的过程可以在室温进行,从而简化了生产工艺。附图说明图1为本发明实施例薄膜晶体管的结构示意图。图2为本发明另一实施例薄膜晶体管的结构示意图。图3为本发明实施例薄膜晶体管的制备方法的流程图。图4为本发明实施例薄膜晶体管面板的俯视结构示意图。图5为本发明实施例薄膜晶体管面板的剖视结构示意图。图6为本发明另一实施例薄膜晶体管面板的俯视结构示意图。图7为本发明另一实施例薄膜晶体管面板的剖视结构示意图。图8为本发明实施例显示装置的结构示意图。图9为本发明实施例2-1氧化物半导体薄膜的XRD图谱。图10为本发明实施例2-1氧化物半导体薄膜的电学性能随溅射氧气流量的变化数据图。图11为本发明实施例2-1氧化物半导体薄膜的扫描电镜照片。图12为本发明实施例2-2氧化物半导体薄膜的电学性能随溅射氧气流量的变化数据图。图13为本发明实施例2-2氧化物半导体薄膜的扫描电镜照片。图14为本发明实施例2-3氧化物半导体薄膜的电学性能随溅射氧气流量的变化数据图。图15为本发明实施例2-3氧化物半导体薄膜的扫描电镜照片。主要元件符号说明薄膜晶体管面板100,200薄膜晶体管110,210栅极112,212绝缘层113,213半导体层114,214源极115,215漏极116,216通孔118,218像素电极120,220源极线130,230栅极线140,240绝缘基底150,250钝化层160,260网格区域170,270液晶显示装置300偏光层310第一配向层320液晶层330第二配向层340第二偏光层350如下具体实施方式将结合上述附图进一步说明本发明。具体实施方式下面将结合附图及具体实施例对本发明提供的薄膜晶体管及其制备方法、薄膜晶体管面板以及显示装置作进一步的详细说明。请参阅图1,本发明实施例提供一种薄膜晶体管110,该薄膜晶体管110设置在绝缘基底150表面,包括半导体层114、源极115、漏极116、栅极112及绝缘层113。该源极115与漏极116间隔设置,该半导体层114与该源极115和漏极116电连接,该栅极112通过该绝缘层113与该半导体层114、源极115及漏极116绝缘设置。该半导体层114为一氧化物半导体膜,包括体铟元素(In)、铈元素(Ce)、锌元素(Zn)及氧元素(O),该In:Ce:Zn的摩尔比为2:(0.5~2):1,氧化物半导体膜为n型半导体,载流子浓度为1012cm-3~1020cm-3,载流子迁移率为5.0cm2V-1s-1~45.0cm2V-1s-1。该氧化物半导体膜优选为非晶质氧化物。在另一实施例中,该氧化物半导体膜中也可含有晶态In2CexZnO4+2x。在一实施例中,该氧化物半导体膜除该In、Ce、Zn及O元素外,仅含有微量杂质,该杂质的含量优选为小于10ppm。该氧化物半导体膜的禁带宽度优选为3.0eV~3.5eV。该氧化物半导体膜的可见光透过率优选为60%~90%。该氧化物半导体膜的厚度优选为50nm~1000nm。该氧化物半导体膜的载流子浓度优选为1013cm-3~1015cm-3。该氧化物半导体膜的载流子迁移率优选为12.3cm2V-1s-1~45.0cm2V-1s-1。该氧化物半导体膜可以通过使用上述溅射靶,通过溅射法获得。该溅射靶由氧化铟(In2O3)、氧化铈(CeO2)及氧化锌(ZnO)混合后烧结形成,该溅射靶中含有化合物In2CexZnO4+2x,其中x=0.5~2。优选地,该化合物In2CexZnO4+2x为晶态。该溅射靶中可以含有非晶态的In、Ce及Zn的氧化物,优选地,晶态In2CexZnO4+2x在该溅射靶中的含量为80%以上。在一实施例中,该溅射靶仅含有由In2O3、CeO2及ZnO氧化物混合后烧结形成的物质及微量杂质,该杂质的含量优选为小于10ppm。在另一实施例中,该溅射靶仅含有晶态In2CexZnO4+2x及微量杂质,该杂质的含量优选为小于10ppm。在一实施例中,该溅射靶由In2O3、CeO2及ZnO混合后烧结形成的烧结物经过机械加工成型得到。该溅射靶的相对密度优选大于或等于90%,该相对密度=溅射靶实际密度:In2CexZnO4+2x理论密度×100%。该溅射靶的体电阻优选为10-2Ωcm~10Ωcm。该溅射靶表面的粗糙度优选小于或等于2微米,更优选为小于或等于0.5微米。该溅射靶的平均抗弯强度优选为大于或等于50MPa,更优选为大于或等于55MPa。该薄膜晶体管110可以为顶栅型或背栅式,当为顶栅型时,上述半导体层114设置于上述绝缘基底150表面。上述源极115及漏极116间隔设置于上述半导体层114表面。上述绝缘层113设置于上述半导体层114表面。上述栅极112设置于上述绝缘层113表面,并通过该绝缘层113与该半导体层114及源极115和漏极116绝缘设置。所述半导体层114位于所述源极115和漏极116之间的区域形成一沟道。上述源极115及漏极116的设置位置不限。只要确保上述源极115及漏极116间隔设置,并与上述半导体层114电接触即可。具体地,所述源极115及漏极116可以间隔设置于所述半导体层114的上表面,位于所述绝缘层113与半导体层114之间,此时,源极115、漏极116与栅极112设置于半导体层114的同一侧,形成一共面型薄膜晶体管110。或者,所述源极115及漏极116可以间隔设置于所述半导体层114的下表面,此时,源极115、漏极116与栅极112设置于半导体层114的不同侧,位于所述绝缘基底110与半导体层114之间,形成一交错型薄膜晶体管110。请参阅图2,在另一实施例中,该薄膜晶体管210为背栅式结构,包括一栅极212、一绝缘层213、一半导体层214、一源极215及一漏极216。上述栅极212设置于所述绝缘基底250表面;上述绝缘层213设置于该栅极212表面;上述半导体层214设置于该绝缘层213表面,通过绝缘层213与栅极212绝缘设置;上述源极215及漏极216间隔设置并与上述半导体层214电接触,该源极215、漏极216及半导体层214通过绝缘层213与上述栅极212电绝缘。所述半导体层214位于所述源极215和漏极216之间的区域形成一沟道。所述源极215及漏极216可以间隔设置于该半导体层214的上表面,此时,源极215、漏极216与栅极212设置于半导体层214的不同面,形成一逆交错型薄膜晶体管210。或者,所述源极215及漏极216可以间隔设置于该半导体层214的下表面,位于绝缘层213与半导体层214之间,此时,源极215、漏极216与栅极212设置于半导体层214的同侧,形成一逆共面型薄膜晶体管210。请参阅图3,本发明实施例提供一种薄膜晶体管的制备方法,包括在绝缘基底上制备半导体层、源极、漏极、栅极及绝缘层的步骤。具体地,该制备半导体层的步骤包括使用上述溅射靶,通过溅射法在基底上溅射形成氧化物半导体膜的步骤。具体地,该溅射靶的制备方法包括:将In2O3粉末、CeO2粉末及ZnO粉末均匀混合形成一混合体,该混合体中In:Ce:Zn的摩尔比为2:(0.5~2):1;以及将该混合体在1250°C~1650°C进行烧结。在该混合体中,该In2O3粉末、CeO2粉末及ZnO粉末的粒径优选为小于或等于10微米,更优选为0.5微米~2微米。该In2O3粉末、CeO2粉末及ZnO粉末的纯度优选为3N(质量百分比99.9%)~5N(质量百分比99.999%)。该In2O3粉末、CeO2粉末及ZnO粉末摩尔比例为In2O3:CeO2:ZnO=2:(1~4):2。该In2O3粉末、CeO2粉末及ZnO粉末可以在空气或保护气体(如Ar气或N2气)中进行混合,该混合步骤可进一步包括:将该In2O3粉末、CeO2粉末及ZnO粉末在液态介质中进行球磨;及将球磨后的混合物烘干去除该液态介质。该液态介质为不与原料In2O3粉末、CeO2粉末及ZnO粉末发生反应,且通过之后的烘干步骤可以去除,不向混合物中引入其它杂质。该液态介质例如可以是水、乙醇及丙酮中的至少一种。该球磨是在球磨机中进行,该液态介质与该原料In2O3粉末、CeO2粉末及ZnO粉末置入该球磨机中。该球磨机的转速优选为100rpm~600rpm。在球磨的过程中,一方面可以将该In2O3粉末、CeO2粉末及ZnO粉末充分混合均匀,另一方面可以将粉末的粒径细化,得到所需粒径的原料粉末。该球磨时间以混合均匀并且原料粒度达到要求为准。该烘干的温度优选为30°C~60°C,该烘干步骤可以在空气或保护气体(如Ar气或N2气)中进行,优选为在高纯(3N~5N)保护气体中进行烘干。该烧结的步骤可以是将该混合体进行热压烧结(非等静压)、常压烧结或热等静压烧结。该热压烧结的压力可以为30MPa~100MPa,烧结时间可以为1小时~24小时。该热等静压烧结的压力可以为100MPa~300MPa,烧结时间可以为1小时~40小时。该常压烧结的烧结时间可以为1小时~40小时。该烧结过程在保护气体中进行,该保护气体可以为Ar气或N2气,优选为纯度为3N~5N的Ar气或N2气。当烧结过程中同时施加压力时,该混合体可以在烧结过程中成型,以形成预定形状的溅射靶,适于后续溅射使用。具体可以是将该烧结体放入具有预定形状的模具中进行热压烧结或等静压烧结。当该烧结为常压烧结时,该混合体可以在烧结前先进行成型,以形成预定形状的溅射靶,适于后续溅射使用。具体可以是将该烧结体放入具有预定形状的模具中进行压制。该压制所用的压力可以为30MPa~300MPa。另外,当采用任何烧结方式进行烧结前,均可对混合体进行预成型步骤,例如可以采用模具、浇铸或注射等方式使混合体预成型,在预成型过程中可以在混合体中加入粘结剂和/或溶剂。该粘结剂和/或溶剂在后续的烧结步骤中可以被完全去除。在烧结后得到具有预定形状的烧结体后可以直接作为该溅射靶使用,也可以进一步进行加工成型、打磨等步骤。在烧结过程中,原料In2O3粉末、CeO2粉末及ZnO粉末反应生成晶态In2CexZnO4+2x。在该制备半导体层的步骤中,该溅射法可以为磁控溅射法,例如直流溅射法或交流溅射法(如中频磁控溅射法或射频磁控溅射法),优选为中频磁控溅射法或射频磁控溅射法。该溅射的电流优选为0.1A~2.0A。该溅射的时间优选为1分钟~120分钟。该溅射的温度可以为常温或高温,优选小于或等于400°C。当采用高温时,该制备方法可进一步包括在溅射前将该基底在真空中预热的步骤,该预热温度例如可以为50°C~400°C。该溅射法中使用的载气可以为稀有气体、稀有气体与氧气的混合气或稀有气体与氢气的混合气,该稀有气体优选为Ar气。该载气优选为Ar气与氧气的混合气。该氧气的流量优选小于3sccm。载气中各气体的纯度优选为3N~5N。该溅射时溅射室内的压力优选为0.1Pa~2.0Pa。该基板的材料为绝缘材料且能够耐受该氧化物半导体膜制备过程中的加热温度。当该氧化物半导体膜制备过程所用温度较低,如采用常温溅射,该基板的材料选择范围较宽。该基板的材料可以列举为玻璃、硅或聚合物(如PI、PE、PET等)。在进行溅射前,该制备方法可进一步包括对基底进行清洁的步骤,以去除基底表面的杂质。在进行溅射前,该基底材料可以安装在夹具上进行固定,该基底与该溅射靶可以相互平行,也可以呈一夹角,该夹角可以为20º~85º之间。该基底与该溅射靶之间的距离优选小于或等于8cm。在进行溅射在该基底上形成氧化物膜后,该氧化物膜可直接作为氧化物半导体膜。在另一实施例中,该制备方法还可进一步包括将该氧化物膜退火的步骤。具体地,是在真空、氮气或保护气体(如Ar气)中进行退火。该退火过程的本底真空优选为10-3Pa~10Pa。该退火温度优选为100°C~400°C,升温速率优选为1°C/min~20°C/min,退火时间优选为1小时~10小时。该退火过程可在一定程度上提高该氧化物膜的结晶度,从而对氧化物半导体膜产品的性能进行调整。本发明实施例提供的薄膜晶体管及其制备方法中,采用原位掺杂Ce的氧化铟锌得到In2CexZnO4+2x溅射靶,其中x=0.5~2。利用该溅射靶溅射得到n型氧化物半导体膜,In:Ce:Zn的摩尔比例为2:(0.5~2):1。该n型氧化物半导体膜的载流子霍尔迁移率在5.0cm2V-1s-1~45.0cm2V-1s-1,载流子浓度在1012cm-3~1020cm-3,可以用于制备n型薄膜晶体管,用于平板显示器或其它电子设备中。该Ce元素在该氧化物半导体膜中的含量不能太小或太大,当x<0.5,半导体氧化物膜的性质偏向IZO,容易导致膜的稳定性降低,应用到半导体元件在使用中易受光照及栅压等影响使该半导体氧化物膜的参数发生变化;当x>2时,该半导体氧化物膜的迁移率下降,影响半导体元件性能。当该薄膜晶体管110为顶栅型时,该薄膜晶体管110的制备方法可进一步包括:在该绝缘基底150表面形成该半导体层114;在该半导体层114上间隔形成该源极115及该漏极116,使该源极115及漏极116与该半导体层114电连接;在该源极115、漏极116及半导体层114上覆盖该绝缘层113;在该绝缘层113上形成栅极112。此时得到的薄膜晶体管110为共面型薄膜晶体管110。在另一实施例中,该薄膜晶体管110的制备方法可进一步包括:在该绝缘基底150表面间隔形成该源极115及该漏极116;在该源极115及漏极116上形成该半导体层114,使该源极115及漏极116与该半导体层114电连接;在该源极115、漏极116及半导体层114上覆盖该绝缘层113;在该绝缘层113上形成栅极112。此时得到的薄膜晶体管110为交错型薄膜晶体管110。当该薄膜晶体管210为背栅型时,该薄膜晶体管210的制备方法可进一步包括:在该绝缘基底250表面形成该栅极212;在该栅极212上覆盖该绝缘层213;在该绝缘层213上间隔形成该源极215及该漏极216;在该源极215、漏极216上形成该半导体层214,使该源极215及漏极216与该半导体层214电连接。此时得到的薄膜晶体管210为逆共面型薄膜晶体管110。在另一实施例中,该薄膜晶体管210的制备方法可进一步包括:在该绝缘基底250表面形成该栅极212;在该栅极212上覆盖该绝缘层213;在该绝缘层213上间隔形成该半导体层214;在该半导体层214上间隔形成该源极215及该漏极216,使该源极215及漏极216与该半导体层214电连接。此时得到的薄膜晶体管210为逆交错型薄膜晶体管110。请一并参阅图4及图5,本技术方案实施例还提供一薄膜晶体管面板100。该薄膜晶体管面板100包括多个薄膜晶体管110、多个像素电极120、多个源极线130、多个栅极线140及一绝缘基底150。上述多个薄膜晶体管110、多个像素电极120、多个源极线130及多个栅极线140均设置在绝缘基底150的同一表面上。上述多个源极线130按行相互平行设置,上述多个栅极线140按列相互平行设置,并与源极线130交叉并绝缘设置,从而将绝缘基底150划分成多个网格区域170。上述多个像素电极120及多个薄膜晶体管110分别设置于上述网格区域170中,上述多个像素电极120之间以及上述多个薄膜晶体管110之间间隔设置。每一网格区域170设置一个薄膜晶体管110及一个像素电极120,该像素电极120与该薄膜晶体管110可以间隔设置或重叠设置。本实施例中,该像素电极120覆盖该薄膜晶体管110。所述像素电极120与薄膜晶体管110的漏极116接触从而电连接。具体地,上述薄膜晶体管110上可进一步设置一钝化层160。该钝化层160覆盖上述薄膜晶体管110,并具有一暴露上述漏极116的通孔118。上述像素电极120覆盖整个网格区域170及其上的薄膜晶体管110,并通过通孔118与漏极116电连接。所述钝化层160的材料为绝缘材料。该钝化层160可以保证上述像素电极120只与薄膜晶体管110的漏极116电连接,而与薄膜晶体管110的其他部分绝缘设置。所述薄膜晶体管110的源极与一源极线130电连接。具体地,上述网格区域170以矩阵方式按行及按列排列。上述每行网格区域170中的薄膜晶体管110的源极115均与其所在行的源极线130电连接。上述薄膜晶体管110的栅极112与一栅极线140电连接。具体地,上述每列网格区域170中的薄膜晶体管110的栅极112均与其所在列的栅极线140电连接。所述像素电极120为一导电薄膜,该导电薄膜的材料为一导电材料,当用于液晶显示器中时,该像素电极120可选择为铟锡氧化物(ITO)层、锑锡氧化物(ATO)层、铟锌氧化物(IZO)层或金属性碳纳米管薄膜等透明导电层。请参阅图6及图7,本技术方案另一实施例还提供一种薄膜晶体管面板200。该薄膜晶体管面板200包括多个薄膜晶体管210、多个像素电极220、多个源极线230、多个栅极线240及一绝缘基板250。本实施例的薄膜晶体管面板200与前一实施例的薄膜晶体管面板100基本相同,区别在于该薄膜晶体管210为背栅式结构。所述像素电极220与薄膜晶体管210的漏极216接触从而电连接。具体地,上述薄膜晶体管210上可进一步设置一钝化层260。该钝化层260覆盖上述薄膜晶体管210,并具有一暴露上述漏极216的通孔218。上述像素电极220覆盖整个网格区域270及其上的薄膜晶体管210,并通过通孔218与漏极216电连接。所述钝化层260的材料为绝缘材料。本发明实施例提供一种显示装置,该显示装置包括上述薄膜晶体管面板100或薄膜晶体管面板200。请参阅图8,该显示装置为一液晶显示装置300,从上至下依次包括盖板310、第一偏光层320、公共电极层330、第一配向层340、液晶层350、第二配向层360、薄膜晶体管面板100或200及第二偏光层370。该盖板310设置于该液晶显示装置300的上侧,该第一偏光层320设置在该盖板310的下表面,该第一偏光层320用于控制通过液晶层350的偏振光的出射。该公共电极层330设置在该第一偏光层320的下表面,用于与该薄膜晶体管面板100或200共同形成偏转电场。该第一配向层340设置于所述公共电极层330的下表面,靠近液晶层350设置。该第一配向层340的下表面可包括多个平行的第一沟槽,用于使液晶层350的液晶分子定向排列。所述液晶层350包括多个长棒状的液晶分子。该第二配向层360设置在该薄膜晶体管面板100或200的上表面,靠近液晶层350设置。第二配向层360的上表面可包括多个平行的第二沟槽,所述第一配向层340的第一沟槽的排列方向与第二配向层360的第二沟槽的排列方向垂直。该第二偏光层370设置在该薄膜晶体管面板100或200的下表面。该第二偏光层370的作用为将导光板发出的光进行起偏,从而得到沿单一方向偏振的光线。所述第二偏光层370的偏振方向与第一偏光层320的偏振方向垂直。该液晶显示装置300可进一步包括设置在该第二偏光层370下侧的背光模组。该背光模组包括光源及导光板。实施例1:溅射靶及其制备方法实施例1-1称量纯度为4N的209gIn2O3粉末、260gCeO2粉末和61gZnO粉末(三种氧化物摩尔比例为In2O3:CeO2:ZnO=1:2:1),将三种粉末放入球磨罐中混合。球磨介质选为无水乙醇,球磨转速200rpm,球磨时间10h。球磨结束后在压力为1atm、纯度为5N的Ar气保护下烘干1h。烘干后将粉末放入热压烧结炉中,在高纯Ar气氛围中进行热压烧结,烧结压力为50MPa,烧结温度为1350℃,升温速率为15ºC/min,烧结时间为5h。烧结结束后随炉冷却至室温取样。靶材相对密度>87%,体电阻0.75Ωcm。将靶材用于中频交流磁控溅射,起弧容易,溅射稳定。实施例1-2称量纯度为4N的249gIn2O3粉末、231gCeO2粉末和73gZnO粉末(三种氧化物摩尔比例为In2O3:CeO2:ZnO=2:3:2),将三种粉末放入球磨罐中混合。球磨介质选为无水乙醇,球磨转速为400rpm,球磨时间为20h。球磨结束后在压力为1atm、纯度为5N的Ar气保护下烘干1h。采用常压烧结制备靶材,将粉末放入普通压机中,压力为75MPa,保压时间为60min。脱模后放入烧结炉,在高纯N2气氛围中进行烧结,烧结温度为1450℃,升温速率为10ºC/min,烧结时间为8h。烧结结束后随炉冷却至室温取样。靶材相对密度>85%,体电阻0.12Ωcm。将靶材用于中频交流磁控溅射,起弧容易,溅射稳定。实施例1-3称量纯度为4N的209gIn2O3粉末、260gCeO2粉末和61gZnO粉末(三种氧化物摩尔比例为In2O3:CeO2:ZnO=1:2:1),放入球磨罐中混合。球磨介质选为无水乙醇,球磨转速500rpm,球磨时间为10h。球磨结束后在压力为1atm、纯度为5N的N2气保护下烘干1h。将粉末进行包裹后,放入等静压机中,在高纯Ar气氛围中进行烧结。烧结压力为100MPa,烧结温度为1450℃,升温速率为10ºC/min,烧结时间为20h。烧结结束后随炉冷却至室温取样。靶材相对密度>86%,体电阻0.62Ωcm。将靶材用于中频交流磁控溅射,起弧容易,溅射稳定。实施例2:氧化物半导体膜实施例2-1选用市售普通钠钙玻璃作为基底,将基底洗净并用N2吹干后置入磁控溅射仪中。基底与靶材表面平行,距离8cm。靶材为实施例1-1掺铈氧化铟锌靶材In2CexZnO4+2x,三种氧化物摩尔比例为In2O3:CeO2:ZnO=1:2:1。采用40sccm的Ar和0~2sccm的O2作为工作气体,工作电流为1.0A,工作气压为0.7Pa,在室温进行磁控溅射,溅射时间为28min,制得250nm厚的ICZO薄膜,经过Hall测试测得该ICZO薄膜霍尔迁移率达14cm2V-1s-1~25.6cm2V-1s-1,载流子浓度在1013cm-3~1020cm-3。请参阅图9,从XRD谱图可以看到该ICZO薄膜为无定形结构。请参阅图10,ICZO薄膜载流子浓度及霍尔迁移率随溅射使用的O2流量的变化数据如图10所示。请参阅图11,ICZO薄膜扫描电镜表面形貌如图11所示。实施例2-2选用市售普通钠钙玻璃作为衬底,将基片洗净并用N2吹干后置入磁控溅射仪中。基底与靶材表面平行,距离8cm。靶材为实施例1-2掺铈氧化铟锌靶材In2CexZnO4+2x,制备该靶材所用的三种氧化物摩尔比例为In2O3:CeO2:ZnO=2:3:2,用40sccm的Ar和0~3sccm的O2作为工作气体,基底预热温度为250℃,工作电流为1.0A,工作气压为0.7Pa,溅射时间为28min,制得250nm厚的ICZO薄膜。经过Hall测试测得该ICZO薄膜霍尔迁移率达17.8cm2V-1s-1~45.0cm2V-1s-1,载流子浓度在1015cm-3~1020cm-3。请参阅图12,ICZO薄膜载流子浓度及霍尔迁移率随溅射使用的O2流量的变化数据如图12所示。请参阅图13,ICZO薄膜扫描电镜表面形貌如图13所示。实施例2-3选用市售普通钠钙玻璃作为基底,将基片洗净并用N2吹干后置入磁控溅射仪中。基底与靶材表面平行,距离8cm。靶材为实施例1-3掺铈氧化铟锌靶材In2CexZnO4+2x,制备该靶材所用的三种氧化物摩尔比例为In2O3:CeO2:ZnO=1:2:1。采用40sccm的纯Ar作为工作气体,工作电流为1.0A,工作气压为0.7Pa,在室温进行磁控溅射,溅射时间为28min,制得250nm厚的ICZO薄膜,经过Hall测试测得该ICZO薄膜霍尔迁移率达15.6cm2V-1s-1,载流子浓度为1020cm-3。将溅射态薄膜放入石英管式炉内退火,在1Pa真空下退火1h,退火温度为150ºC到350ºC,可得载流子浓度在1014cm-3~1020cm-3,霍尔迁移率在17.1cm2V-1s-1~20.6cm2V-1s-1之间的ICZO薄膜,适合制备TFT器件。请参阅图14,ICZO薄膜载流子浓度及霍尔迁移率随退火温度的变化数据如图14所示。请参阅图15,ICZO薄膜扫描电镜表面形貌如图15所示。另外,本领域技术人员还可在本发明精神内做其他变化,当然,这些依据本发明精神所做的变化,都应包含在本发明所要求保护的范围之内。当前第1页1 2 3