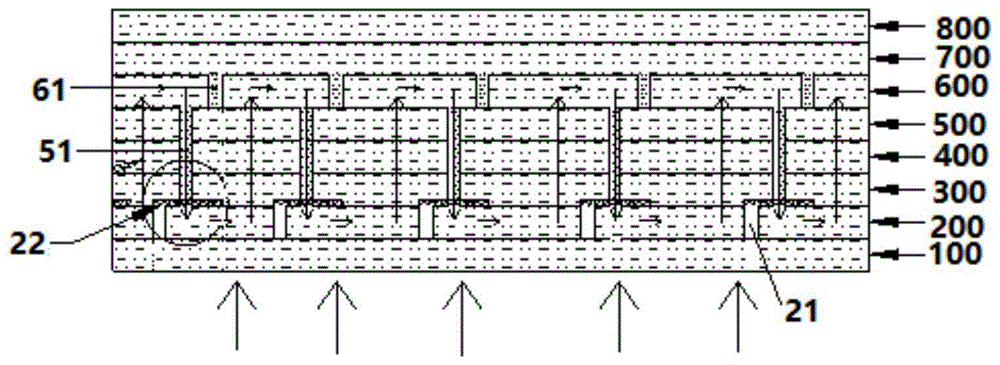
本发明涉及太阳能电池
技术领域:
,特别涉及一种钙钛矿电池。
背景技术:
:目前钙钛矿电池处于实验室研发阶段,在小面积单体电池的效率方面取得迅速发展,短短几年的时间效率已经达到23.3%。现阶段正在努力解决钙钛矿电池的稳定性以及电池的大面积化制备。国内也有些企业开始着手于商业化大面积钙钛矿电池的制备,如协鑫在45cm*65cm尺寸上的效率达15.7%,纤纳在19.3cm2面积上的效率达17.9%。现阶段在钙钛矿电池组件封装方面的研究投入较少。目前的封装方式都是延续非晶薄膜电池的封装方式,即在电池及组件的制作过程中采用3道激光划线工序。其中,激光划线p1是划穿透明导电氧化物层,激光划线p2是划穿空穴传输层、钙钛矿吸收层、电子传输层,激光划线p3是划穿金属电极层,通过三次激光划线实现钙钛矿电池的切割和串联。对于组件尺寸为1100*1400mm的电池,行业通常采用的划线电池宽度为8.9mm,整个面积划分成120个小电池串联而成,形成组件。每个小电池都包含三道激光划线,三道激光划线会造成钙钛矿电池的局部死区,在划线区域入射光转换电能不能有效传出,全部转换成热量,造成此部分电池的浪费,对于整个钙钛矿组件来说综合损失达2.7%。且死区部分电池会出现局部高温,诱导钙钛矿电池组件降解,加速组件的降解及衰减,降低电池使用寿命。同时,电池焊接引出时一侧的单个小电池电流因无法有效导出,会进一步降低电池的总效率。因此,现有钙钛矿电池封装方式有待进一步改进。技术实现要素:有鉴于此,本发明旨在提出一种钙钛矿电池,以解决现有采用激光切割的钙钛矿电池出现死区,造成能量浪费且出现局部高温的问题。为达到上述目的,本发明的技术方案是这样实现的:一种钙钛矿电池,包括:钢化玻璃;透明导电氧化物层,所述透明导电氧化物层具有多个等间距布置的第一激光切割通道,在所述透明导电氧化物层上方具有反光膜,所述透明导电氧化物层与所述钢化玻璃相连,所述第一激光切割通道的一端与所述钢化玻璃相连,所述第一激光切割通道的另一端与所述反光膜相连;电子传输层,所述电子传输层与所述透明导电氧化物层或所述反光膜相连;钙钛矿光吸收层,所述钙钛矿光吸收层与所述电子传输层相连;空穴传输层,所述空穴传输层与所述钙钛矿光吸收层相连,且在所述电子传输层、所述钙钛矿光吸收层和所述空穴传输层中,具有多个贯穿所述电子传输层、所述钙钛矿光吸收层和所述空穴传输层的等间距布置的第二激光切割通道,所述第二激光切割通道的一端与所述透明导电氧化物层相连;金属电极层,所述金属电极层具有多个等间距布置的第三激光切割通道,且所述金属电极层与所述空穴传输层相连,所述第三激光切割通道的一端与所述空穴传输层相连;封装材料层,所述封装材料层与所述金属电极层相连,所述第三激光切割通道的另一端与所述封装材料层相连;盖板玻璃,所述盖板玻璃与所述封装材料层相连。进一步地,所述反光膜的宽度不小于所述第一激光切割通道的宽度。进一步地,所述反光膜的宽度不小于所述第一激光切割通道与所述第二激光切割通道在水平方向的宽度。进一步地,所述反光膜的宽度等于所述第一激光切割通道与所述第三激光切割通道在水平方向的宽度。进一步地,所述反光膜的结构为金字塔结构或棱镜型结构。进一步地,所述反光膜的材质为银或氧化铝。进一步地,通过蒸镀或磁控溅射或粘贴的方式在所述透明导电氧化物层上方形成所述反光膜。进一步地,所述第一激光切割通道与所述第二激光切割通道在水平方向的距离不小于120um。进一步地,所述第二激光切割通道与所述第三激光切割通道在水平方向的距离不小于120um。进一步地,所述第一激光切割通道与所述第三激光切割通道在水平方向的距离不小于240um。相对于现有技术,本发明所述钙钛矿电池,具有以下优势:通过在透明导电氧化物层上方形成反光膜,且反光膜与第一激光切割通道的一端相连,当光线射入经过第一激光切割通道和/或第二激光切割通道、第三激光切割通道时,在反光膜的作用下,可将原本无法利用的光经反光膜反射到邻近钙钛矿光吸收层,进而得到再利用。如此,可将原本造成电池局部过热的光吸收转化为电能,降低第一激光切割通道和/或第二激光切割通道、第三激光切割通道附近的温度,减小钙钛矿电池的损失,延缓电池的降解速度。同时,可通过光的再利用降低因为正负极全背面引出导致的单侧电池失效对整个电池损失的影响,提升电池的封装效率。附图说明构成本发明的一部分的附图用来提供对本发明的进一步理解,本发明的示意性实施例及其说明用于解释本发明,并不构成对本发明的不当限定。在附图中:图1为根据本发明一个实施例钙钛矿电池的结构示意图;图2为本发明实施例1中电池经反射膜反射的光的线路图。具体实施方式需要说明的是,在不冲突的情况下,本发明中的实施例及实施例中的特征可以相互组合。下面将参考附图并结合实施例来详细说明本发明。在本发明的一个方面,本发明提出了一种钙钛矿电池,根据本发明的实施例,参考图1,该电池包括:钢化玻璃100、透明导电氧化物层200、电子传输层300、钙钛矿光吸收层400、空穴传输层500、金属电极层600、封装材料层700和盖板玻璃800。根据本发明的实施例,钢化玻璃100的宽度、长度、高度及具体材质并不受特别限制,本领域技术人员可以根据实际需要进行选择。例如,宽度、长度和高度可以为适用于大面积钙钛矿电池的尺寸。根据本发明的实施例,透明导电氧化物层200具有多个等间距布置的第一激光切割通道21,在透明导电氧化物层200上方具有反光膜22,透明导电氧化物层200与钢化玻璃100相连,第一激光切割通道21的一端与钢化玻璃100相连,第一激光切割通道21的另一端与反光膜22相连。具体的,太阳光从玻璃照射进来,到达透明导电氧化物层,透明导电氧化物层为电池的负极。透明导电氧化物层可以为掺杂氟的氧化锡(fto)透明导电层钢化玻璃或氧化铟锡(ito)导电层。且可以通过化学气相沉积法或磁控溅射法在钢化玻璃上形成透明导电氧化物层。需要说明的是,透明导电氧化物层的尺寸及反光膜的材质并不受特别限制,本领域技术人员可以根据实际需要进行选择。例如反光膜的材质可以为银或氧化铝。发明人发现,第一激光切割通道切断了电池的负极,将大电池分割成多个小电池单元。当光线射入经过第一激光切割通道和/或第二激光切割通道、第三激光切割通道时,在反光膜的作用下,可将原本无法利用的光经反光膜反射到邻近钙钛矿光吸收层,进而得到再利用。如此,可将原本造成电池局部过热的光吸收转化为电能,降低第一激光切割通道和/或第二激光切割通道、第三激光切割通道附近的温度,减小钙钛矿电池的损失,延缓电池的降解速度。同时,可通过光的再利用降低因为正负极全背面引出导致的单侧电池失效对整个电池损失的影响,提升电池的封装效率。根据本发明的一个实施例,反光膜的宽度不小于第一激光切割通道的宽度。由此,至少可以让射入第一激光切割通道中的光得到反射,实现钙钛矿吸收层对至少由第一激光切割通道上方的反光膜反射出来的光的吸收再利用,进而提高整个电池对光能的利用率,提高组件效率,同时降低因局部温度升高造成的失效风险。根据本发明的再一个实施例,反光膜的宽度不小于第一激光切割通道与第二激光切割通道之间的宽度,即反光膜的宽度至少可以让第一激光切割通道与第二激光切割通道的光得到反射,实现钙钛矿吸收层对至少由第一激光切割通道和第二激光切割通道上方的反光膜反射出来的光的吸收再利用,进一步提高整个电池对光能的利用率,提高组件效率,同时降低因局部温度升高造成的失效风险。根据本发明的又一个实施例,反光膜的宽度等于第一激光切割通道与第三激光切割通道之间的宽度。即反光膜的宽度刚好可以让第一激光切割通道与第二激光切割通道、第三激光切割通道的光得到反射,实现钙钛矿吸收层对由第一激光切割通道和第二激光切割通道、第三激光切割通道上方的反光膜反射出来的光的吸收再利用,进一步提高整个电池对光能的利用率,同时减少电池因过热造成的损失。且当反光膜的宽度等于第一激光切割通道与第三激光切割通道之间的宽度时,可以在实现钙钛矿吸收层对射入第一激光切割通道、第二激光切割通道和第三激光切割通道的光的再吸收利用的同时,降低透明导电氧化物层上方反光膜的成本。根据本发明的又一个实施例,反光膜的具体结构并不受特别限制,本领域技术人员可以根据实际需要进行选择,只要能实现将射入第一激光切割通道、第二激光切割通道和第三激光切割通道中的至少之一的光反射出去被邻近的钙钛矿吸收层吸收便可。优选可以让射入第一激光切割通道、第二激光切割通道和第三激光切割通道的光尽可能多的进行一次反射即到达邻近钙钛矿吸收层的反光膜结构。例如,可以为金字塔结构或棱镜型结构。根据本发明的又一个实施例,在透明导电氧化物层上方形成反光膜的方式并不受特别限制,本领域技术人员可以根据实际需要进行选择,例如可以通过蒸镀或磁控溅射或粘贴的方式。需要说明的是,反光膜的材质、成分、厚度并不受特别限制,只要能实现反光的功能即可。根据本发明的实施例,电子传输层300与透明导电氧化物层200或反光膜22相连。电子传输层可以为二氧化钛致密层,覆盖在具有反光膜的透明导电氧化物层的表面。电子传输层可将电子从钙钛矿吸收层传输到透明导电氧化物层,同时可以阻止空穴从钙钛矿吸收层传输到透明导电氧化物层。需要说明的是,在具有反光膜的透明导电氧化物层上形成电子传输层的具体方式并不受特别限制,本领域技术人员可以根据实际需要进行选择。根据本发明的实施例,钙钛矿光吸收层400与电子传输层300相连。具体的,钙钛矿光吸收层可以吸收太阳光并产生电子空穴对。需要说明的是,钙钛矿光吸收层的具体形成方式并不受特别限制,本领域技术人员可以根据实际需要进行选择。根据本发明的实施例,空穴传输层500与钙钛矿光吸收层400相连,且在电子传输层300、钙钛矿光吸收层400和空穴传输层500中,具有多个贯穿电子传输层300、钙钛矿光吸收层400和空穴传输层500的等间距布置的第二激光切割通道51,第二激光切割通道51的一端与透明导电氧化物层200相连。具体的,空穴传输层可以为spiro-ometad、pcbm、rcp、cuscn或niox。空穴传输层可将空穴从钙钛矿吸收层传输到金属电极层。需要说明的是,空穴传输层的具体形成方式并不受特别限制,本领域技术人员可以根据实际需要进行选择。第二激光切割通道的一端可直接与透明导电氧化物层相连,也可穿透反光膜与透明导电氧化物层相连。发明人发现,第二激光切割通道切断电池的电子传输层、钙钛矿光吸收层和空穴传输层,且第二激光切割通道的另一端与金属电极层相连,由此可形成电流通道,完成电池的串联。根据本发明的一个实施例,第一激光切割通道与第二激光切割通道在水平方向的距离不小于120um。具体的,第一激光切割通道与第二激光切割通道在水平方向上的距离是指第一激光切割通道的中心线与第二激光切割通道的中心线在水平方向的距离。发明人发现,由于设备的控制精度有限,若宽度小于120um,第一激光切割通道即有可能和第二激光切割通道重合,出现电池短路现象,增加产品的不良率。根据本发明的实施例,金属电极层600具有多个等间距布置的第三激光切割通道61,且金属电极层600与空穴传输层500相连,第三激光切割通道61的一端与空穴传输层500相连。具体的,金属电极层为电池的正极,金属电极层可以为au、ag、al、cu等。需要说明的是,金属电极层的具体形成方式并不受特别限制,本领域技术人员可以根据实际需要进行选择。发明人发现,第三激光切割通道切断电池的金属电极,即正极,如此将大面积电池切割成了多个小面积电池。根据本发明的一个实施例,第二激光切割通道与第三激光切割通道在水平方向的距离不小于120um。具体的,第二激光切割通道与第三激光切割通道在水平方向上的距离是指第二激光切割通道的中心线与第三激光切割通道的中心线在水平方向的距离。发明人发现,由于设备的控制精度有限,若第二激光切割通道与第三激光切割通道的宽度小于120um,则第二激光切割通道有可能和第三激光切割通道重合,出现电池短路的现象,增加产品的不良率。根据本发明的再一个实施例,第一激光切割通道与第三激光切割通道在水平方向的距离不小于240um。具体的,第一激光切割通道与第三激光切割通道在水平方向上的距离是指第一激光切割通道的中心线与第三激光切割通道的中心线在水平方向的距离。发明人发现,若第一激光切割通道与第三激光切割通道的间距太小,则在生产过程中可能会出现第一激光切割通道与第二激光切割通道重合,或第三激光切割通道与第二激光切割通道重合的现象,造成电池出现短路情况,增加产品的不良率。根据本发明的实施例,封装材料层700与金属电极层600相连,第三激光切割通道61的另一端与封装材料层700相连。具体的,封装材料层可以为poe、eva、surlyn、uv固化胶等。发明人发现,封装材料层可将电池与盖板玻璃密封连接,给电池以足够的支撑,阻隔外部水汽、空气的进入,防止电池被氧化和水解,增加产品的运行可靠性及机械性能。根据本发明的实施例,盖板玻璃800与封装材料层700相连。发明人发现,盖板玻璃可给电池提供机械支撑。具体的,光从透明导电氧化物层照入,钙钛矿光吸收层中的钙钛矿吸收高于禁带宽度的光子能量后,产生电子空穴对,即处于价带的电子由基态跃迁到激发态,被激发到了导带。价带中的空穴通过空穴传输层,被传输到金属电极层中。而导带中被激发的电子注入到能级较低的电子传输层的导带中,并将电子传输到透明导电氧化物层。之后电子再从透明导电氧化物层经外电路传输到金属电极层,并与金属电极层中的空穴复合。整个电池由多个小电池单元组成,每个小电池单元的尺寸大小本领域的技术人员可以根据实际需要进行选择。每个小电池单元都包含第一激光切割通道、第二激光切割通道和第三激光切割通道。在第一激光切割通道、第二激光切割通道和第三激光切割通道的作用下,有利于电子和空穴的传输,实现各个小电池单元之间的串联,增加电池的总电流强度,提高电池对光能的利用率。下面参考具体实施例,对本发明进行描述,需要说明的是,这些实施例仅仅是描述性的,而不以任何方式限制本发明。实施例1参考图1,一长度为1400mm、宽度为1100mm的钙钛矿电池,包括:厚度为3.2mm的钢化玻璃;厚度为150nm的氧化铟锡(ito)导电层,氧化铟锡(ito)导电层具有多个等间距布置的第一激光切割通道,在氧化铟锡(ito)导电层上方具有金字塔形、材质为银、厚度为80nm的反光膜,该反光膜可使得射入的光线经一次反射到达邻近钙钛矿光吸收层的光占比50%,即经多次反射到达邻近钙钛矿光吸收层的光的占比也为50%。氧化铟锡(ito)导电层与钢化玻璃相连,第一激光切割通道的一端与钢化玻璃相连,第一激光切割通道的另一端与反光膜相连;厚度为60nm的电子传输层,电子传输层与透明导电氧化物层或反光膜相连;厚度为400nm的钙钛矿光吸收层,钙钛矿光吸收层与电子传输层相连;厚度为70nm的空穴传输层,空穴传输层与钙钛矿光吸收层相连,且在电子传输层、钙钛矿光吸收层和空穴传输层中,具有多个贯穿电子传输层、钙钛矿光吸收层和空穴传输层的等间距布置的第二激光切割通道,第二激光切割通道的一端穿透反光膜与透明导电氧化物层相连,第二激光切割通道与第一激光切割通道的距离为120um;厚度为100nm的金属电极层,金属电极层具有多个等间距布置的第三激光切割通道,且金属电极层与空穴传输层相连,第三激光切割通道的一端与空穴传输层相连,第三激光切割通道与第一激光切割通道的距离为240um;厚度为0.5mm的封装材料层,封装材料层与金属电极层相连,第三激光切割通道的另一端与封装材料层相连;厚度为3.2mm的盖板玻璃,盖板玻璃与封装材料层相连。其中,反光膜的宽度与第一激光切割通道和第三激光切割通道之间的距离相等,即入射到第一激光切割通道、第二激光切割通道和第三激光切割通道的光都能被反射膜反射出去,进一步被钙钛矿光吸收层吸收。上述电池各介质的折射率、消光系数、吸收系数如表1所示。表1各介质的折射率、消光系数、吸收系数介质类型折射率消光系数吸收系数厚度(nm)ag反光膜0.1653.2070.06880ito导电层1.870.030.0005150钢化玻璃1.5048空气1参考图2,激光切割通道为i区,钙钛矿光吸收区标为ii区。根据光学界面反射及介质中传输损失原理,光的界面反射率r=(n2-n1)2/(n2+n1)2,光在介质中的透过率t=e-ɑ*l,其中,n1、n2分别为两种不同介质的折射率;l为光的传输距离;ɑ为介质的吸收系数。参考图2,对于a点,光线射入后经一次反射到达邻近的b点,经测量,lab=69nm,则:ra=(1.87-0.165)2/(1.87+0.165)2=70.2%,ta=e-0.0005*69=96.61%,最终到达钙钛矿光吸收层的光占入射光的70.2%*96.61%=67.82%;对于c点,光线射入后经c点反射到d点再依次到达e和f点,经测量lcd+lde+lef=435.44nm,则:rc=rd=(1.87-0.165)2/(1.87+0.165)2=70.2%,re=(1.87-1.5048)2/(1.87+1.5048)2+(1.5048-1)2/(1.5048+1)2=4.06%=1.17%+4.06%=5.23%,tc=e-0.0005*435.44=80.44%最终到达钙钛矿光吸收层的光占入射光的70.2%*70.2%*5.23%*80.44=2.07%;因经一次反射和多次反射到达邻近钙钛矿吸收层的光占比为1:1,所以,最终在反光膜的作用下到达邻近钙钛矿吸收层的光占入射光的百分比为67.82%/2+2.07%/2=34.95%,即在上述反光膜的作用下,可使得34.95%的射入激光切割通道的光得到再利用,整个电池的效率相对提升0.98%,效果显著。以上所述仅为本发明的较佳实施例而已,并不用以限制本发明,凡在本发明的精神和原则之内,所作的任何修改、等同替换、改进等,均应包含在本发明的保护范围之内。当前第1页12