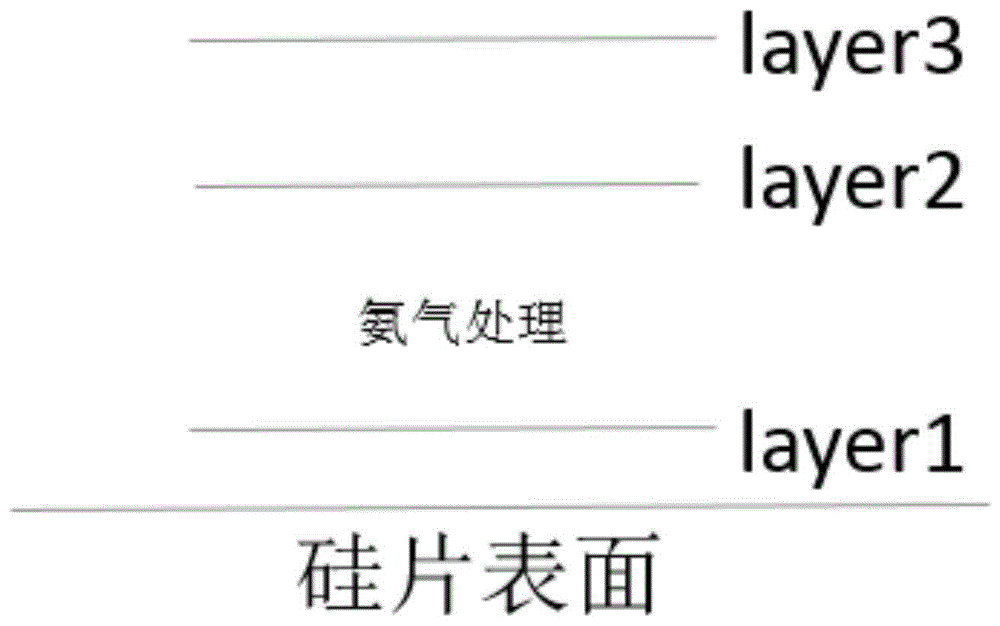
本发明属于太阳能电池
技术领域:
,尤其涉及一种太阳能电池片的表面钝化处理方法。
背景技术:
:近年来,光伏行业发展迅速,随着光伏产能的加大,行业内的竞争压力也日趋严峻,降本提效成了现在不容忽视的一个重要的课题。为了能达到提效的目的,量产中通常会在太阳电池的表面镀一层sinx膜,同时满足表面钝化和减反射的需求。值得注意的是,在实际生产过程中,为了能使电池片达到较好的表面钝化和体钝化效果,通常在沉积sinx膜前会先用nh3进行处理,来清洗硅片表面的杂质及有机物,并使氢原子深入硅片中以加强钝化效果。但是采用nh3直接轰击硅片表面,会致使表面损伤严重,形成更多的表面缺陷,使表面复合速率提高,降低钝化效果,且nh3处理后,硅片表面微观不平整,会导致沉积sinx膜变薄,影响电池片的钝化效果。技术实现要素:有鉴于此,本发明要解决的技术问题在于提供一种太阳能电池片的表面钝化处理方法,该处理方法可提高电池片氢含量及钝化效果。本发明提供了一种太阳能电池片的表面钝化处理方法,包括:s1)在太阳能电池片的表面沉积第一sinx薄膜,得到沉积第一sinx薄膜的太阳能电池片;s2)将所述沉积第一sinx薄膜的太阳能电池用nh3等离子体进行表面处理,得到处理后的太阳能电池片;s3)在所述处理后的太阳能电池片表面依次沉积第二sinx薄膜与第三sinx薄膜。优选的,所述第一sinx薄膜的厚度为5~10nm;所述第一sinx薄膜的折射率为2.1~2.4。优选的,所述第一sinx薄膜的厚度为8~10nm;所述第一sinx薄膜的折射率为2.35~2.39。优选的,所述步骤s2)中表面处理处理时,nh3的流量为2000~6000sccm;表面处理的时间为30~120s;表面处理的射频功率为6000~8000w;表面处理的占空比为1:(10~15)。优选的,所述步骤s2)中表面处理时,nh3的流量为4000~6000sccm;表面处理的时间为30~120s;表面处理的射频功率为7000~8000w;表面处理的占空比为1:(10~15)。优选的,所述第二sinx薄膜的厚度为20~25nm;所述第二sinx薄膜的折射率为2.05~2.1。优选的,所述第三sinx薄膜的厚度为45~55nm;所述第三sinx薄膜的折射率为1.95~2.03。本发明提供了一种太阳能电池片的表面钝化处理方法,包括:s1)在太阳能电池片的表面沉积第一sinx薄膜,得到沉积第一sinx薄膜的太阳能电池片;s2)将所述沉积第一sinx薄膜的太阳能电池用nh3等离子体进行表面处理,得到处理后的太阳能电池片;s3)在所述处理后的太阳能电池片表面依次沉积第二sinx薄膜与第三sinx薄膜。与现有技术相比,本发明在太阳能电池片表面沉积一层致密的sinx薄膜,然后再用nh3等离子体进行表面处理,既避免了电池片表面的损伤,减少了体缺陷,同时还可增加第一sinx薄膜中的氢含量,使氢离子渗入到硅片体内,减少了硅片体内的晶界及晶粒内部的缺陷,使钝化效果加强,也极大地扩展了该薄膜的硅氮比窗口,提高了电池片的开路电压与效率。附图说明图1为本发明实施例1表面钝化处理后的太阳能电池片的结构示意图;图2为本发明比较例1表面钝化处理后的太阳能电池片的结构示意图;图3为本发明实施例1及比较例1表面钝化处理后太阳能电池片在不同波长下的反射率曲线图。具体实施方式下面将结合本发明实施例,对本发明实施例中的技术方案进行清楚、完整地描述,显然,所描述的实施例仅仅是本发明一部分实施例,而不是全部的实施例。基于本发明中的实施例,本领域普通技术人员在没有做出创造性劳动前提下所获得的所有其他实施例,都属于本发明保护的范围。本发明提供了一种太阳能电池片的表面钝化处理方法,包括:s1)在太阳能电池片的表面沉积第一sinx薄膜,得到沉积第一sinx薄膜的太阳能电池片;s2)将所述沉积第一sinx薄膜的太阳能电池用nh3等离子体进行表面处理,得到处理后的太阳能电池片;s3)在所述处理后的太阳能电池片表面依次沉积第二sinx薄膜与第三sinx薄膜。其中,所述太阳能电池片为本领域技术人员熟知的待处理的太阳能电池即可,并无特殊的限制,本发明中优选含有pn结的硅片。在太阳能电池片的表面沉积第一sinx薄膜,得到沉积第一sinx薄膜的太阳能电池连;所述沉积优选采用等离子增强化学气相沉积方法(pecvd)进行;所述第一sinx薄膜的厚度优选为5~10nm,更优选为8~10nm;所述sinx薄膜的折射率优选为2.1~2.4,更优选为2.2~2.4,再优选为2.2~2.3,最优选为2.25~2.3。将所述沉积第一sinx薄膜的太阳能电池用nh3等离子体进行表面处理,得到处理后的太阳能电池片;所述表面处理时nh3的流量优选为2000~6000sccm,更优选为4000~6000sccm,再优选为5000~6000sccm;所述表面处理的时间优选为30~120s,更优选为50~100s,再优选为80~90s;所述表面处理的射频功率优选为6000~8000w;所述表面处理的占空比优选为1:(10~15),更优选为1:(12~15)。先在太阳能电池表面沉积一层薄的sinx薄膜进行保护,再用nh3等离子体进行表面处理,不会硅片表面造成损伤,而且还可使氢原子渗入至硅片中去,减少晶体内部缺陷,加强硅片表面甚至体内的钝化效果。在处理后的太阳能电池片表面依次沉积第二sinx薄膜与第三sinx薄膜;所述沉积优选采用等离子增强化学气相沉积方法(pecvd)进行;所述第二sinx薄膜的厚度优选为20~25nm,更优选为22~25nm,再优选为24~25nm;所述第二sinx薄膜的折射率优选为2.05~2.1;所述第三sinx薄膜的厚度优选为45~55nm,更优选为48~52nm,再优选为50nm;所述第三sinx薄膜的折射率优选为1.95~2.03,更优选为2.0。本发明在太阳能电池片表面沉积一层致密的sinx薄膜,然后再用nh3等离子体进行表面处理,既避免了电池片表面的损伤,减少了体缺陷,同时还可增加第一sinx薄膜中的氢含量,使氢离子渗入到硅片体内,减少了硅片体内的晶界及晶粒内部的缺陷,使钝化效果加强,也极大地扩展了该薄膜的硅氮比窗口,提高了电池片的开路电压与效率。为了进一步说明本发明,以下结合实施例对本发明提供的一种太阳能电池片的表面钝化处理方法进行详细描述。以下实施例中所用的试剂均为市售。实施例1s1)于含有pn结的硅片表面先沉积一层折射率较高的sinx薄膜,厚度8nm,折射率为2.25,得到沉积第一sinx薄膜的太阳能电池片。s2)将所述沉积第一sinx薄膜的太阳能电池用nh3等离子体进行表面处理,得到处理后的太阳能电池片,通入6000sccmnh3,处理时间为90s,射频功率8000w,占空比1:15。s3)在处理后的太阳能电池片表面分别沉积其他两层sinx膜(第二层sinx,厚度24nm,折射率为2.10;第三层sinx,厚度50nm,折射率为2.0)。参见图1,图1为本发明实施例1表面钝化处理后的太阳能电池片的结构示意图。比较例1s1)将含有pn结的硅片用nh3等离子体进行表面处理,通入5000sccmnh3,处理时间为90s,射频功率6000w,占空比1:15。s2)在处理后的太阳能电池表面依次沉积三层sinx膜(第一层sinx,厚度5nm,折射率为2.25;第二层sinx,厚度23nm,折射率为2.10;第三层sinx,厚度50nm,折射率为2.0)。参见图2,图2为本发明比较例1表面钝化处理后的太阳能电池片的结构示意图。比较例2s1)于含有pn结的硅片表面先沉积一层折射率较高的sinx薄膜,厚度8nm,折射率为2.25,得到沉积第一sinx薄膜的太阳能电池片。s2)在第一sinx薄膜表面沉积第二sinx薄膜,厚度24nm,折射率为2.1,得到沉积两层sinx薄膜的太阳能电池片。s3)将所述沉积两层sinx薄膜的太阳能电池用nh3等离子体进行表面处理,得到处理后的太阳能电池片,通入6000sccmnh3,处理时间为90s,射频功率8000w,占空比1:15。s4)在处理后的太阳能电池表面分别沉积第三sinx膜,厚度50nm,折射率为2.0。对实施例1、比较例1与比较例2中表面钝化处理后的太阳能电池片进行检测(测试采用halm公司专业的电池检测设备,标片为fraunhofer太阳能研究所检测的一级标片),得到结果见表1;得到不同波长下表面钝化处理后太阳能电池片的反射率曲线图如图3所示;由图3可知比较例1先进行表面氨气处理,膜厚较薄,低波长的反射率没有优势,对光的吸收降低,影响电池效率。表1性能检测结果膜厚(nm)voc(v)isc(a)ffeta(%)未处理的硅片820.6701339.86284783.0001222.47856比较例1780.6725619.86007182.6857222.49024实施例1820.67389.86386782.8477422.52924比较例2820.6717259.86275682.1705422.4874由表1可知,未处理的硅片无氨气处理,由于电池表面没有氢钝化,电池开压较低;比较例1直接表面氨气处理后,由于硅片表面产生损伤,表面高低出现缺陷,膜厚降低,钝化效果优势小;比较例2在第二层膜后再用氨气处理,由于膜厚已有30nm左右,氢原子进入硅片表面较少,钝化效果不明显;实施例1在第一层膜(8nm左右)后用氨气处理,由于原子层较薄,氢原子比较容易进入硅片表面,且对硅片表面的损伤不大,钝化效果较好,开压较高,有提效的优势。当前第1页12