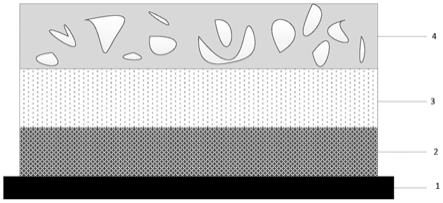
[0001]
本发明涉及锂电池领域,尤其涉及一种硫化物极片材料、其制备方法及锂电池。
背景技术:[0002]
锂离子电池主要由正极材料、负极材料、电解液、隔膜及正负极集流体等组成,是一种高能量密度、高效率的电能储存装置,已经被广泛用于可移动电子设备。锂离子电池的性能与材料的性质密切相关。
[0003]
过渡金属硫化物具有较高理论容量,如cos2具有870mah/g的比容量,nis2具有590mah/g比容量、mos2具有670mah/g比容量以及vs2具有466mah/g的比容量,因此其在锂电池领域的研究尤为活跃。
[0004]
但是过渡金属硫化物作为电极材料具有的缺陷也是显而易见的,如过渡金属硫化物电导率较低,导致较大的容量损失;此外过渡金属硫化物在锂脱嵌过程中,容易导致硫离子的穿梭效应,导致材料结构不稳定,容易脱落;同时会导致自放电,容量衰减严重等问题。
[0005]
为此,越来越多的科研工作者尝试对过渡金属硫化物材料进行改性,以制备电化学性能良好的极片材料及电极。
技术实现要素:[0006]
本发明要解决的技术问题是:提供一种硫化物极片材料、其制备方法及锂电池,所述硫化物极片材料用于锂电池时,锂离子扩散系数大,可抑制硫离子穿梭,结构稳定,导电率高,循环稳定性高。
[0007]
本发明提供了一种硫化物极片材料的制备方法,包括以下步骤:
[0008]
步骤(s1):在集流体的表面形成聚多巴胺层;
[0009]
步骤(s2):在所述聚多巴胺层上形成过渡金属硫化物层;
[0010]
步骤(s3):将形成有聚多巴胺层和过渡金属硫化物层的集流体置于含有盐酸多巴胺和氧化石墨烯的混合溶液中,进行水热反应,然后在惰性气体中进行退火处理,得到硫化物极片材料。
[0011]
优选地,所述步骤(s1)具体为:
[0012]
将集流体置于盐酸多巴胺-三羟甲基氨基甲烷溶液中,10~35℃条件下混合搅拌12~48h,在集流体的表面形成聚多巴胺层。
[0013]
优选地,所述盐酸多巴胺溶液浓度为1~5mg/ml,三羟甲基氨基甲烷溶液的浓度为1~2mg/ml。
[0014]
优选地,所述步骤(s2)具体为:
[0015]
将形成有聚多巴胺层的集流体置于过渡金属硫化物的前驱体溶液中,混合反应,在所述聚多巴胺层上形成过渡金属硫化物层。
[0016]
优选地,所述混合反应的温度为100~180℃,时间为12~24h。
[0017]
优选地,所述过渡金属硫化物层为mos2层、vs2层、cos2层、或者nis2层。
[0018]
优选地,所述步骤(s3)中,所述氧化石墨烯的浓度为2~10mg/ml,盐酸多巴胺的浓度为1~5mg/ml,所述盐酸多巴胺与氧化石墨烯质量比为1:2~5。
[0019]
优选地,所述步骤(s3)中,所述水热反应的温度为80~180℃,所述水热时间为12~24h;所述退火处理的温度为600~1000℃,所述退火处理的时间为1~5h。
[0020]
本发明提供了一种硫化物极片材料,依次包括:
[0021]
集流体基底;
[0022]
设置于所述集流体基底上的结晶碳层;
[0023]
设置于所述结晶碳上的过渡金属硫化物层;以及
[0024]
包覆在所述过渡金属硫化层上的氮掺杂的多孔石墨烯层。
[0025]
本发明还提供了一种锂电池,包括极片,所述极片由上述技术方案所述方法制备的硫化物极片材料或者上述技术方案所述的硫化物极片材料经过制备形成。
[0026]
与现有技术相比,本发明利用多巴胺与氧化石墨烯两种碳材料,首先是利用多巴胺在集流体形成一聚多巴胺层,聚多巴胺层能够为过渡金属硫化物的沉积提供良好的附着位点,使过渡金属硫化物沉积较为均匀;其次通过在石墨烯溶液中加入盐酸多巴胺,对氧化石墨烯进行改性,使其生成多巴胺交联的含有氮元素的氧化石墨烯。退火后,形成了氮掺杂的多孔石墨烯包覆过渡金属硫化物极片材料,进一步增加了过渡金属硫化物活性物质的电导率。
[0027]
本发明制备的硫化物极片材料由于氮掺杂的多孔石墨烯包覆过渡金属硫化物表面,能够起到稳定极片材料的作用,避免活性物质在脱嵌锂过程中出现材料结构的坍塌,抑制硫离子穿梭效应,从而有利于锂离子电池的长效循环。
附图说明
[0028]
图1表示本发明实施例制备的硫化物极片材料的结构示意图。
具体实施方式
[0029]
为了进一步理解本发明,下面结合实施例对本发明优选实施方案进行描述,但是应当理解,这些描述只是为进一步说明本发明的特征和优点,而不是对本发明的限制。
[0030]
本发明的实施例公开了一种硫化物极片材料的制备方法,包括以下步骤:
[0031]
步骤(s1):在集流体的表面形成聚多巴胺层;
[0032]
步骤(s2):在所述聚多巴胺层上形成过渡金属硫化物层;
[0033]
步骤(s3):将形成有聚多巴胺层和过渡金属硫化物层的集流体置于含有盐酸多巴胺和氧化石墨烯的混合溶液中,进行水热反应,然后在惰性气体中退火处理,得到硫化物极片材料。
[0034]
按照本发明,以下具体说明硫化物极片材料的制备方法:
[0035]
步骤(s1):在集流体的表面形成聚多巴胺层。
[0036]
本发明选择的集流体可以为铜箔、多孔铜、或者泡沫铜,所述材料的集流体能够提供良好的附着位点,同时结构稳定,导电性良好,同时有利于多巴胺的自聚。
[0037]
聚多巴胺层能够为过渡金属硫化物的沉积提供良好的附着位点,使过渡金属硫化物沉积较为均匀,有利于充分利用活性物质。
[0038]
优选地,所述步骤(s1)具体为:
[0039]
将集流体置于盐酸多巴胺-三羟甲基氨基甲烷溶液中,10~35℃条件下混合搅拌12~48h,在集流体的表面形成聚多巴胺层。
[0040]
所述盐酸多巴胺溶液浓度优选为1~5mg/ml,三羟甲基氨基甲烷溶液的浓度优选为1~2mg/ml,更优选为1.2mg/ml。
[0041]
所述聚多巴胺层的厚度优选为0.5~10μm。
[0042]
步骤(s2):在所述聚多巴胺层上形成过渡金属硫化物层。
[0043]
所述过渡金属硫化物层为极片材料的活性物质层。
[0044]
优选地,所述步骤(s2)具体为:
[0045]
将形成有聚多巴胺层的集流体置于过渡金属硫化物的前驱体溶液中,混合反应,在所述聚多巴胺层上形成过渡金属硫化物层。
[0046]
所述过渡金属硫化物的前驱体溶液包括过渡金属盐、含硫化合物和溶剂。
[0047]
所述混合反应为水热反应。
[0048]
所述混合反应的温度优选为100~180℃,时间优选为12~24h。
[0049]
所述过渡金属硫化物层可以选用mos2层、vs2层、cos2层、或者nis2层。
[0050]
步骤(s3):将形成有聚多巴胺层和过渡金属硫化物层的集流体置于含有盐酸多巴胺和氧化石墨烯的混合溶液中,进行水热反应,然后在惰性气体中进行退火处理,得到硫化物极片材料。
[0051]
经过水热反应,完成盐酸多巴胺对于氧化石墨烯改性,生成多巴胺交联的含有氮元素的氧化石墨烯。
[0052]
所述氧化石墨烯的浓度优选为2~10mg/ml,盐酸多巴胺的浓度优选为1~5mg/ml,所述盐酸多巴胺与氧化石墨烯质量比优选为1:2~5。
[0053]
所述水热反应的温度优选为80~180℃,所述水热时间优选为12~24h。
[0054]
经过所述水热反应后,在惰性气体中进行退火处理,
[0055]
所述退火处理的温度优选为600~1000℃,所述退火处理的时间优选为1~5h。
[0056]
经过退火处理,聚多巴胺层转化为结晶碳,多巴胺交联的含有氮元素的氧化石墨烯在过渡金属硫化物层表面形成氮掺杂的多孔石墨烯。
[0057]
本发明的实施例公开了一种硫化物极片材料,如图1所示,依次包括:
[0058]
集流体基底(1);
[0059]
设置于所述集流体基底上的结晶碳层(2);
[0060]
设置于所述结晶碳上的过渡金属硫化物层(3);以及
[0061]
包覆在所述过渡金属硫化层上的氮掺杂的多孔石墨烯层(4)。
[0062]
进一步的,所述过渡金属硫化物的硫含量为10~40wt%,氮元素含量为0.01~5wt%,过渡金属元素含量为10~60wt%,其中过渡金属可以是mo、v、co、ni等,其余为氧元素含量。
[0063]
本发明的实施例还公开了一种锂电池,包括极片,所述极片由上述技术方案所述方法制备的硫化物极片材料或者上述技术方案所述的硫化物极片材料经过制备形成。
[0064]
为了进一步理解本发明,下面结合实施例对本发明提供的硫化物极片材料、其制备方法及锂电池进行详细说明,本发明的保护范围不受以下实施例的限制。
[0065]
实施例1
[0066]
(1)将铜箔置于1mg/ml盐酸多巴胺-tris混合溶液中,在10℃下自聚12h成膜形成聚多巴胺,负载在铜箔表面,所述聚多巴胺层的厚度为0.5~10μm;
[0067]
(2)将聚多巴胺层修饰后的铜箔置于0.076mg/ml钼酸铵与10mg/ml硫脲的混合溶液反应釜中,180℃反应24h,即可均匀得生长在聚多巴胺层上的mos2层;
[0068]
(3)将生长mos2层及聚多巴胺层的铜箔置于1mg/ml盐酸多巴胺与2mg/ml氧化石墨烯的混合溶液中,高温水热80℃,反应12h,反应完后进一步将其置于氩气环境中,600℃退火1h即可制备氮掺杂的多孔石墨烯包覆的过渡金属硫化钼极片材料。
[0069]
实施例2
[0070]
(1)将多孔铜置于5mg/ml盐酸多巴胺-tris混合溶液中,在35℃下自聚48h成膜形成聚多巴胺,负载在多孔铜表面,所述聚多巴胺层的厚度为0.5~10μm;
[0071]
(2)将聚多巴胺层修饰后的多孔铜置于0.076mg/ml钼酸铵与10mg/ml硫脲的混合溶液反应釜中,180℃反应24h,即可均匀得生长在聚多巴胺层上的mos2层;
[0072]
(3)将形成mos2层及聚多巴胺层的多孔铜置于5mg/ml盐酸多巴胺与10mg/ml氧化石墨烯的混合溶液中,高温水热80℃,反应12h,反应完后进一步将其置于氩气环境中,1000℃退火5h即可制备氮掺杂的多孔石墨烯包覆的过渡金属硫化钼极片材料。
[0073]
实施例3
[0074]
(1)将泡沫铜置于3mg/ml盐酸多巴胺-tris混合溶液中,在35℃下自聚48h成膜形成聚多巴胺,负载在泡沫铜表面,所述聚多巴胺层的厚度为0.5~10μm;
[0075]
(2)将聚多巴胺层修饰后的泡沫铜置于0.076mg/ml钼酸铵与10mg/ml硫脲的混合溶液反应釜中,180℃反应24h,即可均匀得生长在聚多巴胺层上的mos2层;
[0076]
(3)将生长mos2层及聚多巴胺层的泡沫铜置于2mg/ml盐酸多巴胺与10mg/ml氧化石墨烯的混合溶液中,高温水热180℃,反应12h,反应完后进一步将其置于氩气环境中,1000℃退火5h即可制备氮掺杂的多孔石墨烯包覆的过渡金属硫化钼极片材料。
[0077]
实施例4
[0078]
(1)将铜箔置于2mg/ml盐酸多巴胺-tris混合溶液中,在10℃下自聚24h成膜形成聚多巴胺,负载在铜箔表面,所述聚多巴胺层的厚度为0.5~10μm;
[0079]
(2)将聚多巴胺层修饰后的铜箔置于20mg/ml硫代乙酰胺与10mg/ml偏钒酸钠混合溶液反应釜中,180℃反应24h,即可均匀得生长在聚多巴胺层上的vs2层;
[0080]
(3)将生长vs2层及聚多巴胺层的铜箔置于2mg/ml盐酸多巴胺与5mg/ml氧化石墨烯的混合溶液中,高温水热180℃,反应24h,反应完后进一步将其置于氩气环境中,800℃退火2h即可制备氮掺杂的多孔的石墨烯包覆的过渡金属硫化钒极片材料。
[0081]
实施例5
[0082]
(1)将多孔铜置于3mg/ml盐酸多巴胺-tris混合溶液中,在25℃下自聚24h成膜形成聚多巴胺,负载在铜箔表面,所述聚多巴胺层的厚度为0.5~10μm;
[0083]
(2)将聚多巴胺层修饰后的多孔铜置于20mg/ml硫代乙酰胺与10mg/ml偏钒酸钠混合溶液反应釜中,180℃反应24h,即可均匀得到生长在聚多巴胺层修饰的多孔铜上的vs2层;
[0084]
(3)将生长vs2层及聚多巴胺层的多孔铜置于3mg/ml盐酸多巴胺与6mg/ml氧化石
墨烯的混合溶液中,高温水热180℃,反应24h,反应完后进一步将其置于氩气环境中,800℃退火2h即可制备氮掺杂的多孔石墨烯包覆的过渡金属硫化钒极片材料。
[0085]
实施例6
[0086]
(1)将泡沫铜置于3mg/ml盐酸多巴胺-tris混合溶液中,在25℃下自聚24h成膜形成聚多巴胺,负载在泡沫铜表面,所述聚多巴胺层的厚度为0.5~10μm;
[0087]
(2)自聚多巴胺膜后的泡沫铜置于20mg/ml硫代乙酰胺与10mg/ml偏钒酸钠混合溶液反应釜中,180℃反应24h,即可均匀得到生长在聚多巴胺层上的vs2层;
[0088]
(3)将生长vs2层及聚多巴胺层的铜箔置于2mg/ml盐酸多巴胺与10mg/ml氧化石墨烯的混合溶液中,高温水热180℃,反应24h,反应完后进一步将其置于氩气环境中,1000℃退火2h即可制备氮掺杂的多孔石墨烯包覆的过渡金属硫化钒极片材料
[0089]
实施例7
[0090]
(1)将铜箔置于2mg/ml盐酸多巴胺-tris混合溶液中,在25℃下自聚24h成膜形成聚多巴胺,负载在铜箔表面,所述聚多巴胺层的厚度为0.5~10μm;
[0091]
(2)将聚多巴胺层修饰的铜箔置于5.8mg/ml六水合硝酸钴与10mg/ml五水合硫代硫酸钠混合溶液反应釜中,180℃反应10h,即可均匀得到生长在聚多巴胺层上的cos2层;
[0092]
(3)将生长cos2层及聚多巴胺层的铜箔置于3mg/ml盐酸多巴胺与8mg/ml氧化石墨烯的混合溶液中,高温水热180℃,反应24h,反应完后进一步将其置于氩气环境中,800℃退火2h即可制备氮掺杂的多孔石墨烯包覆的过渡金属硫化钴极片材料。
[0093]
实施例8
[0094]
(1)将多孔铜置于3mg/ml盐酸多巴胺-tris混合溶液中,在35℃下自聚48h成膜形成聚多巴胺,负载在多孔铜表面,所述聚多巴胺层的厚度为0.5~10μm;
[0095]
(2)将聚多巴胺层修饰的多孔铜置于5.8mg/ml六水合硝酸钴与10mg/ml五水合硫代硫酸钠混合溶液反应釜中,180℃反应10h,即可均匀得到生长在聚多巴胺膜层上的cos2层;
[0096]
(3)将生长cos2层及聚多巴胺层的多孔铜置于2mg/ml盐酸多巴胺与7mg/ml氧化石墨烯的混合溶液中,高温水热100℃,反应12h,反应完后进一步将其置于氩气环境中,800℃退火2h即可制备氮掺杂的多孔石墨烯包覆的过渡金属硫化钴极片材料。
[0097]
实施例9
[0098]
(1)将泡沫铜置于5mg/ml盐酸多巴胺-tris混合溶液中,在35℃下自聚48h成膜形成聚多巴胺,负载在泡沫铜表面,所述聚多巴胺层的厚度为0.5~10μm;
[0099]
(2)将聚多巴胺层修饰的泡沫铜置于5.8mg/ml六水合硝酸钴与10mg/ml五水合硫代硫酸钠混合溶液反应釜中,180℃反应10h,即可均匀得到生长在聚多巴胺层上的cos2层;
[0100]
(3)将生长cos2及聚多巴胺层的泡沫铜置于2mg/ml盐酸多巴胺与5mg/ml氧化石墨烯的混合溶液中,高温水热180℃,反应24h,反应完后进一步将其置于氩气环境中,600℃退火3h即可制备氮掺杂的多孔石墨烯包覆的过渡金属硫化钴极片材料。
[0101]
实施例10
[0102]
(1)将铜箔置于2mg/ml盐酸多巴胺-tris混合溶液中,在25℃下自聚24h成膜形成聚多巴胺,负载在铜箔表面,所述聚多巴胺层的厚度为0.5~10μm;
[0103]
(2)将聚多巴胺层修饰的铜箔置于2mg/ml六合和氯化镍与10mg/ml硫脲混合溶液
反应釜中,180℃反应24h,即可均匀得到生长在聚多巴胺层上的nis2层;
[0104]
(3)将生长nis2及聚多巴胺层的铜箔置于2mg/ml盐酸多巴胺与5mg/ml氧化石墨烯的混合溶液中,高温水热100℃,反应12h,反应完后进一步将其置于氩气环境中,800℃退火2h即可制备氮掺杂的多孔石墨烯包覆的过渡金属硫化镍极片材料。
[0105]
实施例11
[0106]
(1)将多孔铜置于2mg/ml盐酸多巴胺-tris混合溶液中,在25℃下自聚48h成膜形成聚多巴胺,负载在多孔铜表面,所述聚多巴胺层的厚度为0.5~10μm;
[0107]
(2)将聚多巴胺层修饰后的多孔铜置于2mg/ml六合和氯化镍与10mg/ml硫脲混合溶液反应釜中,180℃反应24h,即可均匀得到生长在聚多巴胺层上的nis2层;
[0108]
(3)将生长nis2层及聚多巴胺层的多孔铜置于2mg/ml盐酸多巴胺与6mg/ml氧化石墨烯的混合溶液中,高温水热180℃,反应24h,反应完后进一步将其置于氩气环境中,1000℃退火2h即可制备多孔氮掺杂石墨烯包覆过渡金属硫化镍极片材料。
[0109]
实施例12
[0110]
(1)将泡沫铜置于5mg/ml盐酸多巴胺-tris混合溶液中,在25℃下自聚48h成膜形成聚多巴胺,负载在泡沫铜表面,所述聚多巴胺层的厚度为0.5~10μm;
[0111]
(2)将聚多巴胺层修饰的泡沫铜置于2mg/ml六合和氯化镍与10mg/ml硫脲混合溶液反应釜中,180℃反应24h,即可均匀得到生长在聚多巴胺层上的nis2层;
[0112]
(3)将生长nis2层及聚多巴胺层的泡沫铜置于5mg/ml盐酸多巴胺与10mg/ml氧化石墨烯的混合溶液中,高温水热180℃,反应12h,反应完后进一步将其置于氩气环境中,1000℃退火5h即可制备氮掺杂的多孔石墨烯包覆的过渡金属硫化镍极片材料。
[0113]
将实施例1~12制备的极片材料制成极片,与金属锂片,碳酸酯溶液组装成纽扣电池测试其性能。
[0114]
将实施例1~12制得的锂电池进行测试,测试其在25℃、0.2c/0.2c、下的循环性能测试、循环500圈后的电池放电容量,测试结果如表1所示。
[0115]
表1
[0116][0117]
从表1可知,采用本发明方法制备得到的硫化物极片材料具有良好的循环稳定性及倍率稳定性。在充放电500次后,材料依然能够保持较高的可逆容量,说明氮掺杂的多孔石墨烯包覆能够有效稳定过渡金属硫化物,不至于过渡金属硫化物在充放电过程中造成硫离子穿梭效应。同时集流体上的过渡金属硫化物的均匀沉积,使活性物质得到充分利用。而且,氮掺杂的多孔石墨烯能够提高过渡金属硫化物的电导率,从而增加其倍率性能,与此同时,多孔结构缩短了锂离子传输通道,降低了脱嵌时间,同时增大了极片材料的比表面积,能够良好的导通锂离子及传输电子,稳定了材料结构,从而有利于降低极化,提高极片及锂电池的循环寿命。
[0118]
以上实施例的说明只是用于帮助理解本发明的方法及其核心思想。应当指出,对于本技术领域的普通技术人员来说,在不脱离本发明原理的前提下,还可以对本发明进行若干改进和修饰,这些改进和修饰也落入本发明权利要求的保护范围内。
[0119]
对所公开的实施例的上述说明,使本领域专业技术人员能够实现或使用本发明。对这些实施例的多种修改对本领域的专业技术人员来说将是显而易见的,本文中所定义的一般原理可以在不脱离本发明的精神或范围的情况下,在其它实施例中实现。因此,本发明将不会被限制于本文所示的这些实施例,而是要符合与本文所公开的原理和新颖特点相一致的最宽的范围。