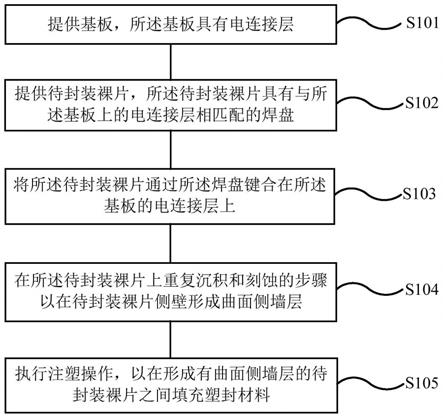
1.本技术涉及半导体制造领域,尤其涉及一种封装方法、封装结构及封装模块。
背景技术:2.芯片封装是先切割芯片然后封装,晶圆级封装是将封装工艺前移,在晶圆上对芯片封装完成再切割独立芯片。晶圆级封装能够集成晶圆制造,封装和测试,从而简化制造过程。晶圆级封装还可以减小封装尺寸,从而节省材料,而且缩短的制造周期时间提高了生产量并降低每单位制造成本。但是晶圆级封装将裸片键合在基板的过程中,会在芯片的边缘形成空隙,从而影响芯片的良率。
3.因此如何避免在芯片的周围产生空隙是需要解决的技术问题。
技术实现要素:4.本技术所要解决的技术问题是提供一种封装方法、封装结构、及封装模块,以避免在芯片的周围产生空隙。
5.为了解决上述问题,本技术提供了一种封装方法。所述封装方法包括:提供基板,所述基板具有电连接层;提供待封装裸片,所述待封装裸片具有与所述基板上的电连接层相匹配的焊盘;将所述待封装裸片通过所述焊盘键合在所述基板的电连接层上;在所述待封装裸片上重复沉积和刻蚀的步骤以在待封装裸片侧壁形成曲面侧墙层;执行注塑操作,以在形成有曲面侧墙层的待封装裸片之间填充塑封材料。
6.在一些实施例中,在所述待封装裸片上重复沉积和刻蚀的步骤以在待封装裸片侧壁形成曲面侧墙层之后,还包括:在所述待封装裸片顶部沉积保护层,所述保护层的厚度与所述待封装裸片厚度的比值范围为10
‑7~10
‑5。
7.在一些实施例中,所述基板具有第一介质层,所述电连接层形成于所述第一介质层中;所述待封装裸片具有第二介质层,所述焊盘形成于所述第二介质层中;所述将所述待封装裸片通过所述焊盘键合在所述基板的电连接层上,包括:将所述待封装裸片的所述第二介质层的表面贴合所述基板的所述第一介质层的表面,且所述焊盘覆盖所述电连接层;执行高温退火操作,以使所述焊盘与所述电连接层键合。
8.在一些实施例中,执行高温退火操作,以使所述焊盘与所述电连接层键合,包括:在第一温度下执行第一高温退火操作,以使所述第一介质层与所述第二介质层熔融键合;在第二温度下执行第二高温退火操作,以使所述焊盘与所述电连接层熔融键合;其中,所述第二温度大于所述第一温度。
9.在一些实施例中,所述执行注塑操作,以在形成有曲面侧墙层的待封装裸片之间填充塑封材料,包括:在所述待封装裸片上重复预设次数的注塑和刻蚀的步骤,以在形成有曲面侧墙层的待封装裸片之间填充塑封材料且所述塑封材料覆盖所述待封装裸片。
10.在一些实施例中,所述封装方法还包括:执行平坦化操作去除部分所述塑封材料,保留的所述塑封材料与所述待封装裸片顶部平齐。
11.在一些实施例中,所述封装方法还包括:切割所述塑封材料及所述基板,以形成多个封装模块,各所述封装模块包括一待封装裸片。
12.在一些实施例中,在所述待封装裸片上重复沉积和刻蚀的步骤以在待封装裸片侧壁形成曲面侧墙层,包括:在所述待封装裸片上沉积绝缘材料层,所述绝缘材料层覆盖所述待封装裸片的侧壁和顶面,以及所述待封装裸片之间基板的顶面;部分刻蚀所述沉积绝缘材料层,以去除所述待封装裸片和所述基板的顶面的绝缘材料层。
13.本技术还提供了一种封装结构。所述封装结构包括:基板,所述基板具有电连接层;多个待封装裸片,所述多个待封装裸片具有与所述基板上的电连接层相匹配的焊盘,所述多个待封装裸片通过所述焊盘键合在所述基板的电连接层上;曲面侧墙层,形成于所述待封装裸片的侧壁;封装层,填充于各所述待封装裸片之间。
14.在一些实施例中,所述封装结构还包括:保护层,所述保护层位于所述待封装裸片顶部,所述保护层的厚度与所述待封装裸片厚度的比值范围为10
‑7~10
‑5。
15.在一些实施例中,所述基板具有第一介质层,所述电连接层形成于所述第一介质层中;所述待封装裸片具有第二介质层,所述焊盘形成于所述第二介质层中。
16.在一些实施例中,从待封装裸片的顶部至底部方向,所述曲面侧墙层的厚度递增。
17.在一些实施例中,所述各所述待封装裸片之间的间距与所述待封装裸片厚度的比值范围为10
‑3~10
‑2。
18.在一些实施例中,所述保护层的材料为氮化硅、氧化硅、或氮氧化硅其中之一。
19.本技术还提供了一种封装模块。所述封装模块,包括:第一芯片,所述芯片具有电连接层;第二芯片,所述第二芯片具有与所述第一芯片上的电连接层相匹配的焊盘,所述第二芯片通过所述焊盘键合在所述第一芯片的电连接层上;所述第二芯片包括裸片和形成于所述裸片侧壁的曲面侧墙层及形成于所述裸片顶部的保护层;封装层,覆盖所述曲面侧墙层的侧壁。
20.在一些实施例中,所述封装模块还包括:堆叠体,堆叠在所述第二芯片上,且与所述第一芯片中的所述电连接层互连。
21.上述技术方案,通过在待封装裸片侧壁形成曲面侧墙层之后,有利于后续材料沉积在曲面侧墙层,使塑料能够更好的填充在待封装裸片的周围,避免在待封装裸片的周围产生空隙。
附图说明
22.图1是本技术中一实施例的封装方法的示意图;
23.图2是本技术一实施例的基板及待封装裸片的示意图;
24.图3是本技术另一实施例的基板及待封装裸片的示意图;
25.图4是本技术一实施例的第二高温退火操作的示意图;
26.图5是本技术一实施例的第二高温退火操作的示意图;
27.图6是本技术一实施例的沉积绝缘材料层的示意图;
28.图7是本技术一实施例的部分刻蚀绝缘材料层的示意图;
29.图8是本技术一实施例的沉积保护层的示意图;
30.图9是本技术一实施例的执行注塑操作的示意图;
31.图10是本技术一实施例的封装结构的示意图;
32.图11是本技术一实施例的封装模块的示意图。
具体实施方式
33.下面结合附图对本技术提供的封装方法、封装结构、及封装模块的具体实施方式做详细说明。
34.图1是本技术中一实施例的封装方法的示意图。所述封装方法包括:步骤s101,提供基板,所述基板具有电连接层;步骤s102,提供待封装裸片,所述待封装裸片具有与所述基板上的电连接层相匹配的焊盘;步骤s103,将所述待封装裸片通过所述焊盘键合在所述基板的电连接层上;步骤s104,在所述待封装裸片上重复沉积和刻蚀的步骤以在待封装裸片侧壁形成曲面侧墙层;步骤s105,执行注塑操作,以在形成有曲面侧墙层的待封装裸片之间填充塑封材料。
35.下面请继续参阅图1,步骤s101,提供基板,所述基板具有电连接层。步骤s102,提供待封装裸片,所述待封装裸片具有与所述基板上的电连接层相匹配的焊盘。所述焊盘的数量为一个以上。图2是本技术一实施例的基板及待封装裸片的示意图。下面请参阅图2,所述基板1具有电连接层2,所述待封装裸片3具有与所述基板1上的电连接层2相匹配的焊盘4。在本实施例中,所述焊盘为铜焊盘。
36.下面请继续参阅图1,步骤s103,将所述待封装裸片通过所述焊盘键合在所述基板的电连接层上。图3是本技术另一实施例的基板及待封装裸片的示意图。下面请参阅图3,在本实施例中,所述基板1具有第一介质层5,所述电连接层2形成于所述第一介质层5中;所述待封装裸片3具有第二介质层6,所述焊盘4形成于所述第二介质层6中。所述将所述待封装裸片3通过所述焊盘4键合在所述基板1的电连接层2上,包括:将所述待封装裸片3的所述第二介质层6的表面贴合所述基板1的所述第一介质层2的表面,且所述焊盘4覆盖所述电连接层2;执行高温退火操作,以使所述焊盘4与所述电连接层2键合。
37.在本实施例中,执行高温退火操作,以使所述焊盘与所述电连接层键合,包括:在第一温度下执行第一高温退火操作,以使所述第一介质层与所述第二介质层熔融键合;在第二温度下执行第二高温退火操作,以使所述焊盘与所述电连接层熔融键合;其中,所述第二温度大于所述第一温度。图4是本技术一实施例的第一高温退火操作的示意图。下面请参阅图4,在第一温度下执行第一高温退火操作,以使所述基底1上的所述第一介质层5与所述待封装裸片3上的所述第二介质层6熔融键合。图5是本技术一实施例的第二高温退火操作的示意图。下面请参阅图5,在第二温度下执行第二高温退火操作,以使所述待封装裸片3上的焊盘4与所述基底1上的所述电连接层2熔融键合。在一些实施例中,采用苯并环丁烯作为粘合剂将所述待封装裸片通过所述焊盘键合在所述基板的电连接层上。
38.下面请继续参阅图1,步骤s104,在所述待封装裸片上重复沉积和刻蚀的步骤以在待封装裸片侧壁形成曲面侧墙层。在一些实施例中,在所述待封装裸片上重复沉积和刻蚀的步骤以在待封装裸片侧壁形成曲面侧墙层,包括:在所述待封装裸片上沉积绝缘材料层,所述绝缘材料层覆盖所述待封装裸片的侧壁和顶面,以及所述待封装裸片之间基板的顶面;部分刻蚀所述沉积绝缘材料层,以去除所述待封装裸片和所述基板的顶面的绝缘材料层。图6是本技术一实施例的沉积绝缘材料层的示意图。下面请参阅图6,在本实施例中在所
述待封装裸片3上沉积绝缘材料层7,所述绝缘材料层7覆盖所述待封装裸片3的侧壁和顶面,以及所述待封装裸片3之间基板1上的所述第一介质层5的顶面。图7是本技术一实施例的部分刻蚀绝缘材料层的示意图。下面请参阅图7,部分刻蚀所述沉积绝缘材料层,以去除所述待封装裸片3和所述基板1上所述第一介质层5的顶面的绝缘材料层,在待封装裸片3侧壁形成曲面侧墙层8。
39.图8是本技术一实施例的沉积保护层的示意图。下面请参阅图8,在本实施例中,所述在所述待封装裸片上重复沉积和刻蚀的步骤以在待封装裸片侧壁形成曲面侧墙层8之后,还包括:在所述待封装裸片顶部沉积保护层9,所述保护层9的厚度与所述待封装裸片厚度的比值范围为10
‑7~10
‑5。所述待封装裸片3形成有器件层的正面对着基板1正面,在所述待封装裸片3背面沉积保护层9。在一些实施例中,所述保护层的材料为氮化硅、氧化硅、或氮氧化硅其中之一。在本实施例中,所述保护层的材料为氧化硅,所述待封装裸片的厚度为100毫米~300毫米,所述保护层的厚度为100埃米~2000埃米,以抵挡制程过程中的反复刻蚀。
40.下面请继续参阅图1,步骤s105,执行注塑操作,以在形成有曲面侧墙层的待封装裸片之间填充塑封材料。图9是本技术一实施例的执行注塑操作的示意图。下面请参阅图9,所述执行注塑操作,以在形成有曲面侧墙层的待封装裸片之间填充塑封材料,包括:在所述待封装裸片3上重复预设次数的注塑和刻蚀的步骤,以在形成有曲面侧墙层的待封装裸片3之间填充塑封材料且所述塑封材料覆盖所述待封装裸片3。在另一些实施例中,所述封装方法还包括:执行平坦化操作去除部分所述塑封材料,保留的所述塑封材料与所述待封装裸片顶部平齐,形成封装层10。在一些实施例中,所述封装方法还包括:切割所述塑封材料及所述基板,以形成多个封装模块,各所述封装模块包括一待封装裸片。下面请继续参阅图9,在一些实施例中,所述基板1具有第一介质层5,所述电连接层2形成于所述第一介质层5中;所述待封装裸片3具有第二介质层6,所述焊盘4形成于所述第二介质层6中。在一些实施例中,从待封装裸片的顶部至底部方向,所述曲面侧墙层8的厚度递增。在一些实施例中,所述各所述待封装裸片之间的间距与所述待封装裸片厚度的比值范围为10
‑3~10
‑2。
41.上述技术方案,通过在待封装裸片3侧壁形成曲面侧墙层8之后,有利于后续执行注塑操作中塑料10沉积在曲面侧墙层8,使塑料10能够更好的填充在待封装裸片3的周围,避免了在待封装裸片的周围产生空隙。在所述待封装裸片上重复沉积和刻蚀的步骤以在待封装裸片侧壁形成曲面侧墙层之后,在所述待封装裸片顶部沉积保护层9,以抵挡制程过程中的反复刻蚀。再切割所述塑封材料及所述基板,以获得多个封装模块。减少了裸片键合在基板的过程中,在芯片的边缘形成空隙,从而提高了芯片的良率。
42.本技术还提供了一种封装结构。图10是本技术一实施例的封装结构的示意图。所述封装结构包括:基板1,所述基板1具有电连接层2;多个待封装裸片3,所述多个待封装裸片3具有与所述基板上的电连接层相匹配的焊盘4,所述多个待封装裸片3通过所述焊盘4键合在所述基板的电连接层2上;曲面侧墙层,形成于所述待封装裸片的侧壁;封装层10,填充于各所述待封装裸片3之间。
43.图1是本技术中一实施例的封装方法的示意图。上述封装结构通过所述封装方法获得。所述封装方法包括:步骤s101,提供基板,所述基板具有电连接层;步骤s102,提供待封装裸片,所述待封装裸片具有与所述基板上的电连接层相匹配的焊盘;步骤s103,将所述
待封装裸片通过所述焊盘键合在所述基板的电连接层上;步骤s104,在所述待封装裸片上重复沉积和刻蚀的步骤以在待封装裸片侧壁形成曲面侧墙层;步骤s105,执行注塑操作,以在形成有曲面侧墙层的待封装裸片之间填充塑封材料。
44.下面请继续参阅图1,步骤s101,提供基板,所述基板具有电连接层。步骤s102,提供待封装裸片,所述待封装裸片具有与所述基板上的电连接层相匹配的焊盘。所述焊盘的数量为一个以上。图2是本技术一实施例的基板及待封装裸片的示意图。下面请参阅图2,所述基板1具有电连接层2,所述待封装裸片3具有与所述基板1上的电连接层2相匹配的焊盘4。在本实施例中,所述焊盘为铜焊盘。
45.下面请继续参阅图1,步骤s103,将所述待封装裸片通过所述焊盘键合在所述基板的电连接层上。图3是本技术另一实施例的基板及待封装裸片的示意图。下面请参阅图3,在本实施例中,所述基板1具有第一介质层5,所述电连接层2形成于所述第一介质层5中;所述待封装裸片3具有第二介质层6,所述焊盘4形成于所述第二介质层6中。所述将所述待封装裸片3通过所述焊盘4键合在所述基板1的电连接层2上,包括:将所述待封装裸片3的所述第二介质层6的表面贴合所述基板1的所述第一介质层2的表面,且所述焊盘4覆盖所述电连接层2;执行高温退火操作,以使所述焊盘4与所述电连接层2键合。
46.在本实施例中,执行高温退火操作,以使所述焊盘与所述电连接层键合,包括:在第一温度下执行第一高温退火操作,以使所述第一介质层与所述第二介质层熔融键合;在第二温度下执行第二高温退火操作,以使所述焊盘与所述电连接层熔融键合;其中,所述第二温度大于所述第一温度。图4是本技术一实施例的第一高温退火操作的示意图。下面请参阅图4,在第一温度下执行第一高温退火操作,以使所述基底1上的所述第一介质层5与所述待封装裸片3上的所述第二介质层6熔融键合。图5是本技术一实施例的第二高温退火操作的示意图。下面请参阅图5,在第二温度下执行第二高温退火操作,以使所述待封装裸片3上的焊盘4与所述基底1上的所述电连接层2熔融键合。在一些实施例中,采用苯并环丁烯作为粘合剂将所述待封装裸片通过所述焊盘键合在所述基板的电连接层上。
47.下面请继续参阅图1,步骤s104,在所述待封装裸片上重复沉积和刻蚀的步骤以在待封装裸片侧壁形成曲面侧墙层。在一些实施例中,在所述待封装裸片上重复沉积和刻蚀的步骤以在待封装裸片侧壁形成曲面侧墙层,包括:在所述待封装裸片上沉积绝缘材料层,所述绝缘材料层覆盖所述待封装裸片的侧壁和顶面,以及所述待封装裸片之间基板的顶面;部分刻蚀所述沉积绝缘材料层,以去除所述待封装裸片和所述基板的顶面的绝缘材料层。图6是本技术一实施例的沉积绝缘材料层的示意图。下面请参阅图6,在本实施例中在所述待封装裸片3上沉积绝缘材料层7,所述绝缘材料层7覆盖所述待封装裸片3的侧壁和顶面,以及所述待封装裸片3之间基板1上的所述第一介质层5的顶面。图7是本技术一实施例的部分刻蚀绝缘材料层的示意图。下面请参阅图7,部分刻蚀所述沉积绝缘材料层,以去除所述待封装裸片3和所述基板1上所述第一介质层5的顶面的绝缘材料层,在待封装裸片3侧壁形成曲面侧墙层8。
48.图8是本技术一实施例的沉积保护层的示意图。下面请参阅图8,在本实施例中,所述在所述待封装裸片上重复沉积和刻蚀的步骤以在待封装裸片侧壁形成曲面侧墙层8之后,还包括:在所述待封装裸片顶部沉积保护层9,所述保护层9的厚度与所述待封装裸片厚度的比值范围为10
‑7~10
‑5。所述待封装裸片3形成有器件层的正面对着基板1正面,在所述
待封装裸片3背面沉积保护层9。在一些实施例中,所述保护层的材料为氮化硅、氧化硅、或氮氧化硅其中之一。在本实施例中,所述保护层的材料为氧化硅,所述待封装裸片的厚度为100毫米~300毫米,所述保护层的厚度为100埃米~2000埃米,以抵挡制程过程中的反复刻蚀。
49.下面请继续参阅图1,步骤s105,执行注塑操作,以在形成有曲面侧墙层的待封装裸片之间填充塑封材料。图9是本技术一实施例的执行注塑操作的示意图。下面请参阅图9,所述执行注塑操作,以在形成有曲面侧墙层的待封装裸片之间填充塑封材料,包括:在所述待封装裸片3上重复预设次数的注塑和刻蚀的步骤,以在形成有曲面侧墙层的待封装裸片3之间填充塑封材料且所述塑封材料覆盖所述待封装裸片3。在另一些实施例中,所述封装方法还包括:执行平坦化操作去除部分所述塑封材料,保留的所述塑封材料与所述待封装裸片顶部平齐,形成封装层10。在一些实施例中,所述封装方法还包括:切割所述塑封材料及所述基板,以形成多个封装模块,各所述封装模块包括一待封装裸片。下面请继续参阅图9,在一些实施例中,所述基板1具有第一介质层5,所述电连接层2形成于所述第一介质层5中;所述待封装裸片3具有第二介质层6,所述焊盘4形成于所述第二介质层6中。在一些实施例中,从待封装裸片的顶部至底部方向,所述曲面侧墙层8的厚度递增。在一些实施例中,所述各所述待封装裸片之间的间距与所述待封装裸片厚度的比值范围为10
‑3~10
‑2。
50.上述技术方案,通过在待封装裸片3侧壁形成曲面侧墙层8之后,有利于后续执行注塑操作中塑料10沉积在曲面侧墙层8,使塑料10能够更好的填充在待封装裸片3的周围,避免在待封装裸片的周围产生空隙。在所述待封装裸片上重复沉积和刻蚀的步骤以在待封装裸片侧壁形成曲面侧墙层之后,在所述待封装裸片顶部沉积保护层9,以抵挡制程过程中的反复刻蚀。再切割所述塑封材料及所述基板,以获得多个封装模块。减少了裸片键合在基板的过程中,在芯片的边缘形成空隙,从而提高了芯片的良率。
51.本技术还提供了一种封装模块。图11是本技术一实施例的封装模块的示意图。所述封装模块,包括:第一芯片11,所述芯片具有电连接层2;第二芯片12,所述第二芯片12具有与所述第一芯片11上的电连接层2相匹配的焊盘4,所述第二芯片12通过所述焊盘4键合在所述第一芯片11的电连接层2上;所述第二芯片12包括裸片3和形成于所述裸片侧壁的曲面侧墙层8及形成于所述裸片顶部的保护层9;封装层10,覆盖所述曲面侧墙层的侧壁。在一些实施例中,所述封装模块还包括:堆叠体(未示出),堆叠在所述第二芯片上,且与所述第一芯片中的所述电连接层2互连。
52.在一些实施例中,所述保护层的厚度与所述待封装裸片厚度的比值范围为10
‑7~10
‑5。所述待封装裸片形成有器件层的正面对着基板正面,在所述待封装裸片背面沉积保护层。在一些实施例中,所述保护层的材料为氮化硅、氧化硅、或氮氧化硅其中之一。在本实施例中,所述保护层的材料为氧化硅,所述待封装裸片的厚度为100毫米~300毫米,所述保护层的厚度为100埃米~2000埃米,以抵挡制程过程中的反复刻蚀。
53.在一些实施例中,形成于所述裸片侧壁的曲面侧墙层的步骤包括:在所述待封装裸片上沉积绝缘材料层,所述绝缘材料层覆盖所述待封装裸片的侧壁和顶面,以及所述待封装裸片之间基板的顶面;部分刻蚀所述沉积绝缘材料层,以去除所述待封装裸片和所述基板的顶面的绝缘材料层。图6是本技术一实施例的沉积绝缘材料层的示意图。下面请参阅图6,在本实施例中在所述待封装裸片3上沉积绝缘材料层7,所述绝缘材料层7覆盖所述待
封装裸片3的侧壁和顶面,以及所述待封装裸片3之间基板1上的所述第一介质层5的顶面。图7是本技术一实施例的部分刻蚀绝缘材料层的示意图。下面请参阅图7,部分刻蚀所述沉积绝缘材料层,以去除所述待封装裸片3和所述基板1上所述第一介质层5的顶面的绝缘材料层,在待封装裸片3侧壁形成曲面侧墙层8。
54.上述技术方案,通过在待封装裸片3侧壁形成曲面侧墙层8之后,有利于后续材料沉积在曲面侧墙层8,曲面侧墙层避免了在待封装裸片的周围产生空隙。在所述待封装裸片上重复沉积和刻蚀的步骤以在待封装裸片侧壁形成曲面侧墙层之后,在所述待封装裸片顶部沉积保护层9,以抵挡制程过程中的反复刻蚀。再切割所述塑封材料及所述基板,以获得多个封装模块。减少了裸片键合在基板的过程中,在芯片的边缘形成空隙,从而提高了芯片的良率。
55.以上所述仅是本技术的优选实施方式,应当指出,对于本技术领域的普通技术人员,在不脱离本发明原理的前提下,还可以做出若干改进和润饰,这些改进和润饰也应视为本发明的保护范围。