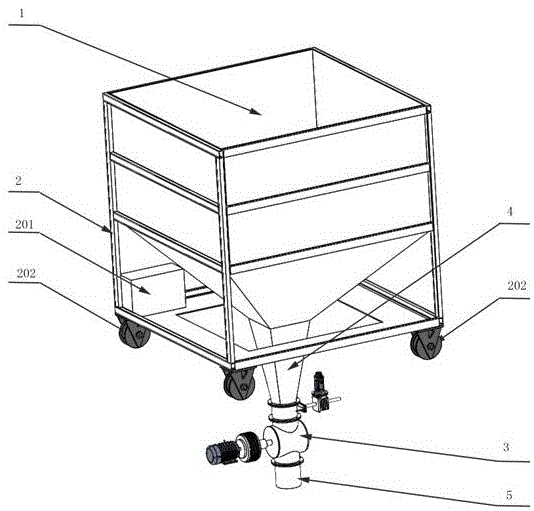
本实用新型涉及土木工程装备
技术领域:
,具体涉及一种钢壳混凝土的定速调节下料装置。
背景技术:
:深中通道是连接珠江两岸的战略性跨江通道,是集超宽海底隧道、超大跨桥梁、深水人工岛、水下互通"四位"一体的集群工程,规模空前、建设条件异常复杂、综合技术难度再上新高,是继港珠澳大桥之后,我国又一项世界级重大跨海交通工程。深中通道将采用“三明治”结构钢壳混凝土沉管(以下简称钢壳混凝土沉管),其总长5035m、拟划分为33个节段(26×165m+6×123m+7m),标准横断面尺寸46.0×10.6m,钢壳管节总重约37万吨,混凝土约90万m³。钢壳混凝土沉管作为一种新型的跨海隧道结构,具有如下普通钢筋混凝土沉管不可比拟的优点:具有优良的防水性能,不存在因混凝土开裂引起渗、漏水问题;结构断面尺寸小,结构工程量、基槽和航道开挖量小;结构承载力强、整体性好,对地基适应能力强;混凝土可浮态浇筑,无需庞大的干坞结构,临时设施简单、规模小;钢壳可提前加工,与混凝土施工形成流水作业,且无需模板、钢筋等施工环节,工艺简单、施工高效、进度快。深中通道钢壳沉管具有结构复杂、尺寸大的特点,要实现自密实混凝土免振捣、自填充,以及与钢壳长期协同受力,面临关键技术难题如下:(1)钢壳沉管混凝土具有大断面、免振捣、自填充的特点,若混凝土流动性不足,则混凝土很难完全填充钢壳,形成局部空洞;若粘聚性不足,流动性稍大,则容易造成浆骨分离,同时,浇筑速率过快,混凝土中气泡未能及时排出,容易在表面聚集,在钢壳与混凝土结合面形成大面积气孔和蜂窝麻面。(2)自密实混凝土水胶比低、胶凝材料用量高,容易导致混凝土早期收缩大,容易造成钢壳与混凝土脱空现象。(3)浮态浇筑工艺可能导致混凝土分层,造成浮浆或浆骨分离等现象;高温天气下,浇筑间隔期间容易发生假凝现象。技术实现要素:本实用新型要解决的技术问题是,针对现有技术存在的上述缺陷,提供了一种钢壳混凝土的定速调节下料装置,实现了程序化控制混凝土灌注速率,使得混凝土灌注过程掺入的气泡数量可控,气泡排出也更充分,大大降低了钢壳混凝土的脱空风险,提高了产品合格率,保障了工程质量。本实用新型为解决上述技术问题所采用的技术方案是:一种钢壳混凝土的定速调节下料装置,包括浇筑台车框架、料斗、定速下料模块,料斗固定于浇筑台车框架上,定速下料模块与料斗出料口连接;其中,浇筑台车框架包括控制机箱、双向轮;定速下料模块由下料阀、齿轮下料器、减速变频器、丝杆升降机和两台电机组成,下料阀内部结构包括下料挡板和驱动轴,丝杆升降机顶端设置一台电机,丝杆升降机铰链接驱动轴,驱动轴连接下料挡板,齿轮下料器内部设置有叶片,叶片端头部位搭接橡胶挡板,齿轮下料器一侧设置减速变频器,减速变频器一侧设置电机,下料阀设置于料斗下方,齿轮下料器设置于下料阀下方,齿轮下料器下端的出口连接有出料口。按照上述技术方案,下料阀设置于料斗下方,起开关料斗的作用。按照上述技术方案,电机的转速可以控制丝杆升降机的运动。按照上述技术方案,丝杆升降机通过驱动轴可以控制下料挡板,调整下料口的大小。按照上述技术方案,通过减速变频器的频率调节电机转速,可以控制齿轮下料器内叶片转速。按照上述技术方案,通过调节齿轮下料器内叶片转速可调节混凝土浇筑速度,减速变频器及控制系统集成在浇筑台车框架的控制机箱内。按照上述技术方案,丝杆升降机其控制系统集成在浇筑台车框架的控制机箱内。按照上述技术方案,所述智能浇筑料斗其混凝土浇筑速度通过变频器调节齿轮下料器转速,可精确控制混凝土下料速度在5m3/h-50m3/h范围内,且下料速率稳定,误差在5%以内。按照上述技术方案,通过变频器的调节,齿轮下料器可按设定程序自动控制混凝土下料速度,下料速度稳定,满足自密实混凝土下料要求。采用以上所述的钢壳混凝土的定速调节下料装置的灌注方法,包括以下步骤:1)浇筑台车框架和料斗与定速下料模块安装连接;2)对定速下料模块中下料阀和齿轮下料器的设备运转功能系统进行检测;3)将混凝土泵送装入至料斗中;4)通过浇筑台车框架底部四个双向轮的自行走,将下料口定位至浇筑点;5)通过对控制机箱丝杆升降机的遥控操作,下料阀内部的下料挡板打开,使混凝土灌注至齿轮下料器内部;6)通过对控制机箱减速变频器的遥控操作,带动齿轮下料器内叶片旋转,使混凝土被叶片带动至下料口,混凝土的灌注速率随叶片旋转速度而保持特定的灌注量,混凝土灌注至距离钢壳顶面15cm~25cm时,再次对减速变频器遥控操作,使叶片运转速度降低,这样,混凝土的灌注速率就同步降低。7)混凝土灌注满钢壳后,关闭控制机箱,停止混凝土灌注。按照上述技术方案,所述的步骤6)中,通过减速变频器调节叶片转速,使钢壳混凝土灌注速率为:混凝土从钢壳底部灌注至钢壳中部时的灌注速度为25m3/h~35m3/h,混凝土从钢壳中部灌注至距离钢壳顶部15cm~25cm时灌注速度为15m3/h~25m3/h,混凝土从距离钢壳顶部15cm~25cm至钢壳灌满时的灌注速度为5m3/h~10m3/h。按照上述技术方案,所述灌注的混凝土为自密实混凝土。本实用新型具有以下有益效果:通过本装置,实现向钢壳中灌注混凝土时,自动、准确的调节灌注速率,速度的可控减少了混凝土中气泡数量,克服了浇筑后期混凝土面层不平整导致空气无法排除的缺点。智能控制系统提高了泵送施工的工作效率和产能,减少了人力、材料等产品生产成本,降低了具有高度重复性和一致性的施工时的不合格率,解决了由于浇筑速率不可控而导致钢壳混凝土面层的局部空洞、大面积气孔和蜂窝麻面富集难题,减少了缺陷,降低了质量风险,全自动化的浇筑设备,更是提高了施工工效,节省了工期,节约了成本,尤其适用于大型钢壳结构混凝土的灌注。附图说明图1是本实用新型实施例中钢壳混凝土的定速调节下料装置的结构示意图;图2是本实用新型实施例中钢壳混凝土的定速调节下料装置的结构示意图;图中,1-料斗,1-料斗,2-台车框架,201-控制机箱,202-双向轮,3-定速下料模块,301-下料阀,3011-下料挡板,3012-驱动轴,3013-丝杆升降机,3014-电机一,302-齿轮下料器,3021-叶片,3022-橡胶挡板,3023-减速变频器,3024-电机二,4-下料口,5-出料口。具体实施方式下面结合附图和实施例对本实用新型进行详细说明。参照图1~图2所示,本实用新型提供的一个实施例中的钢壳混凝土的定速调节下料装置,包括料斗1、浇筑台车框架2、定速下料模块3,料斗1固定于浇筑台车框架2上,定速下料模块3与料斗下料口4连接。其中,浇筑台车框架2包括控制机箱201、双向轮202,控制机箱201设置在台车框架2上,底部设置四个双向轮202。定速下料模块3由下料阀301、齿轮下料器302、减速变频器9、丝杆升降机3013,电机一3014,电机二3024组成,下料阀301内部结构包括下料挡板3011和驱动轴3012,丝杆升降机3013顶端设置电机二3024,丝杆升降机3013铰链接驱动轴3012,驱动轴3012连接下料挡板3011,齿轮下料器302内部设置有叶片3021,叶片3021端头部位搭接橡胶挡板3022,齿轮下料器302一侧设置减速变频器9,减速变频器9一侧设置电机一3014,下料阀301设置于料斗1的下料口4下方,齿轮下料器302设置于下料阀301下方,齿轮下料器302下端的出口连接有出料口5。进一步地,浇筑台车框架2由型钢焊接成型,底部设置四个双向轮202。进一步地,下料阀301设置于料斗1的下料口4下方,起开关料斗1的作用。进一步地,调整电机二3024的转速可以控制丝杆升降机3013的运动速率。进一步地,丝杆升降机3013通过驱动轴3012可以控制下料挡板3011,调整下料口4的大小。进一步地,通过减速变频器9的频率调节电机一3014的转速,可以控制齿轮下料器302内叶片3021的旋转速率。进一步地,通过调节齿轮下料器302内叶片3021转速可调节混凝土浇筑速度,减速变频器9及控制系统集成在浇筑台车框架2的控制机箱201内。进一步地,丝杆升降机3013的控制系统集成在浇筑台车框架2的控制机箱201内。进一步地,浇筑台车框架2的结构组成为角钢、钢管和钢板。进一步地,浇筑台车框架2的外形尺寸为2.4m*2.4m*3.2m,料斗1的尺寸为2.4m*2.4m*2.1m,体积约9m3。进一步地,电机一3014和电机二3024设计功率为11kw(变频调速),混凝土输送量为5m3/h-50m3/h。进一步地,智能浇筑料斗其混凝土浇筑速度通过变频器调节齿轮下料器302转速,可精确控制混凝土下料速度在5m3/h-50m3/h范围内,且下料速率稳定,误差在5%以内。进一步地,通过变频器的调节,齿轮下料器302可按设定程序自动控制混凝土下料速度,下料速度稳定,满足自密实混凝土下料要求。采用以上所述的钢壳混凝土的定速调节下料装置的灌注方法,包括以下步骤:1)浇筑台车框架2和料斗1与定速下料模块3安装连接;2)对定速下料模块6中下料阀301和齿轮下料器302的设备运转功能系统进行检测;3)将混凝土泵送装入至料斗1中;4)通过浇筑台车框架2底部四个双向轮202的行走移动,将出料口5定位至浇筑点;5)通过对控制机箱201的丝杆升降机3013遥控操作,下料阀301内部的下料挡板3011打开,使混凝土灌注到齿轮下料器302内部;6)通过对控制机箱201的减速变频器9遥控操作,带动齿轮下料器302内的叶片3021旋转,使混凝土被叶片3021带动至出料口5,混凝土的灌注速率随叶片3021旋转速度而保持特定的灌注量,混凝土灌注至距离钢壳顶面15cm~25cm时,再次对减速变频器9遥控操作,使叶片3021运转速率降低,这样,混凝土的灌注速率就同步降低。7)混凝土灌注满钢壳后,关闭控制机箱201,停止混凝土灌注。进一步地,所述步骤7)之后,还包括以下步骤:8)24h后拆模观察浇筑效果,浇筑外观达到预期效果,高性能自密实混凝土填充密实,混凝土表面无结构性缺陷。进一步地,所述的步骤6)中,通过减速变频器9调节叶片3021转速,使钢壳混凝土灌注速率为:混凝土从钢壳底部灌注至钢壳中部时的灌注速度为25m3/h~35m3/h,混凝土从钢壳中部灌注至距离钢壳顶部15cm~25cm时灌注速度为15m3/h~25m3/h,混凝土从距离钢壳顶部15cm~25cm至钢壳灌满时的灌注速度为5m3/h~10m3/h。进一步地,在所述步骤6)中,进行混凝土灌注过程中严格控制灌注速率,灌注速率过快严重影响混凝土的填充效果及气泡的排除,灌注速率过慢严重影响浇筑的工效,为了有效控制浇筑速度,采用泵机将混凝土泵送装入料斗1中,通过料斗1缓存及对定速下料模块3的运行控制放料速度,混凝土的灌注速率具体如下:灌注壳体底面时控制灌注速度在25m3/h~35m3/h,灌注壳体的中间部分时控制灌注速度在15m3/h~25m3/h,直至灌注离顶面20cm时控制灌注速度在5m3/h~10m3/h。进一步地,灌注的混凝土为自密实混凝土,充分发挥自密实混凝土的高流动性、抗离析、低热以及高体积稳定等优良工作性能,保证钢壳混凝土的填充密实。高性能自密实混凝土的制备,需要采用自主研发的复合型碱水剂,根据环境温度、原材料波动范围等,调整其配合比,使自密实混凝土性能满足表1相关指标:表1自密实混凝土性能指标参数指标要求备注混凝土标号满足设计要求/混凝土新拌扩展度(mm)650±50保持时间≥1.5hv型漏斗流速时间(s)5~15保持时间≥1.5hl型仪测试h2/h1≥0.8保持时间≥1.5h混凝土表观密度(kg/m3)2300~2400/新拌混凝土含气量(%)≤5.0/骨料最大粒径(mm)20/以上所述仅是本实用新型的优选实施方式,应当指出,对于本
技术领域:
的普通技术人员来说,在不脱离本实用新型技术原理的前提下,还可以做出若干改进和替换,这些改进和替换也应视为本实用新型的保护范围。当前第1页1 2 3