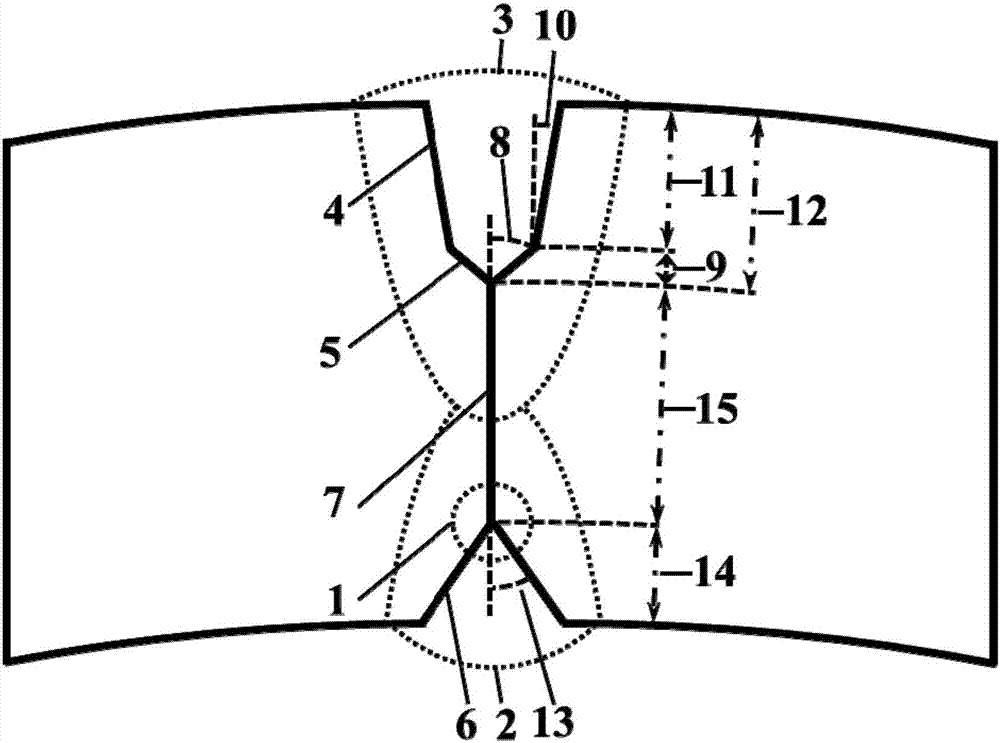
本发明属于机械设备制造领域,具体地,涉及一种螺旋埋弧焊管的制造方法,用作石油天然气输送,适用于Φ1422mm×21.4mm的X80管线钢螺旋焊管的制造。
背景技术:随着西气东输等管线工程的实施,管线钢自2000年以来在国内飞速发展,目前国内管线钢的制造水平已经居于世界前列。现阶段,正在铺设的输气管线主要应用的是X80管线钢。目前生产的X80管线钢母材的各项性能指标都能达到标准要求,但其焊接过程中仍存在很多问题;并且,在输油输气管线中,焊缝长度所占比例较大,因此焊接接头的性能将会直接决定整条管线的安全性和可靠性。焊接接头的性能主要由焊接热影响区及焊缝金属的性能决定。目前,管线钢制管焊接过程中,焊缝金属的强度和韧性有较好的匹配,并不成为降低焊接接头性能的主要因素。而热影响区的性能并不稳定,尤其是冲击韧性测试过程中经常有低值出现。焊接热影响区的性能主要由母材的成分及焊接工艺决定。现今生产的管线钢大部分都采用低碳/超低碳、高锰、高铌的微合金化设计,母材成分差别并不大。因此要提高焊接热影响区的性能,主要靠改进焊接工艺来实现。制管的焊接工艺目前大部分采用双面自动埋弧焊,以螺旋焊管和直缝焊管为主。螺旋焊管和直缝焊管各有优缺点。螺旋焊管的最大优点是它对原料的适应性和经济性,西气东输一线便主要采用螺旋焊管。螺旋焊管可以通过成型角的调整,使用不同宽度的带钢生产同一口径的钢管。反之,也可以采用同一宽度的板材生产不同口径的钢管。因此能够大大降低对原料的宽度和储备数量要求,从而大幅度地降低了原料采购成本。螺旋焊管一般采用三辊弯板机构连续成型,边成型边焊接的生产方式,工艺流程短,设备造价比ERW和直缝埋弧焊管都低得多。螺旋焊管也有其自身的缺点。螺旋焊管的成型质量受带钢月形弯的影响较大,带钢月形弯会造成螺旋焊管管径和焊接间隙的变化,容易造成管径超差、错边和焊接烧穿等缺陷;钢管焊缝较长,出现焊接缺陷的几率较大;未采用低残余应力成型技术的螺旋焊管管体残余拉应力较大,几何尺寸精度较差。但经过多年的技术改进,特别是西气东输工程干线钢管国产化的攻关和大批量生产实践,应用了带钢铣边、低残余应力成型、高韧性焊接材料和多丝焊接、管端整径和无损检测等先进工艺技术和装备,使我国高压输送用螺旋焊管的生产技术和产品质量有了质的飞跃。目前,螺旋焊管采用的坡口形式大部分为双Y型坡口,如说明书附图1所示。内焊道2、外焊道3的坡口张开角度9和7大多为30~40°,内坡口张开角度9比外坡口张开角度7略大(0~5°左右),内坡口深度10和外坡口深度8也大多近似相等,钝边的长度11视板厚决定。对应此种坡口形式的内外焊道的焊接线能量也大致相当,根据实际生产情况在20~40kJ/cm不等。以某钢管厂生产的X80管线钢螺旋焊管(板厚21.4mm)为例,外坡口张开角度7为30±2°,外坡口深度8为6.5±1mm;内坡口张开角度9为35±2°,内坡口深度10为5.4±1mm;钝边厚度11为9.5±1mm。对应的焊接工艺参数,内外焊道的焊接线能量为25~35kJ/cm左右。此种双道次焊接的焊接工艺由于内外焊道的热影响区相互交叉,不可避免地会产生临界粗晶区。临界粗晶区组织由粗大的原奥氏体晶粒加上沿晶界连续分布的M-A组元组成,晶粒内部的组织为粗大的上贝氏体或者粒状贝氏体。临界粗晶区可导致焊接热影响区的冲击韧性显著下降,使得焊接接头的整体性能低于相关标准的要求,实际生产中夏比冲击测试出现的低值大部分在50J以下。因此,此种焊接工艺急需改进,从而提高管线钢双面螺旋埋弧自动焊焊接热影响区的整体性能。
技术实现要素:为克服现有螺旋焊管制造方法存在的缺陷,本发明提供一种X80管线钢螺旋焊管的制造方法,该方法适用于Φ1422mm×21.4mm的X80管线钢螺旋焊管的制造。为实现上述目的,本发明采用下述方案:X80管线钢螺旋焊管的制造方法,工艺步骤如下:1、X80管线钢板卷的开卷与矫平2、铣边3、预弯4、成型5、预焊6、内焊7、外焊8、管端扩径9、产品检验。相对于现有技术,本发明具有如下有益效果:通过对焊接坡口形式进行全新设计,将传统的双Y型坡口改为内焊道Y型、外焊道复合型坡口,并加大外焊道的坡口深度、减小内焊道的坡口深度,从而对内、外焊道的焊接线能量进行了重新分配,增大外焊道焊接线能量,减小内焊道线能量。内焊道线能量的减小能够显著降低热影响区临界粗晶区的晶粒尺寸,有助于链状M-A组元分布的离散化,同时还能减小M-A组元的尺寸,从而使得焊接热影响区的韧性有明显的提升。另外,虽然外...