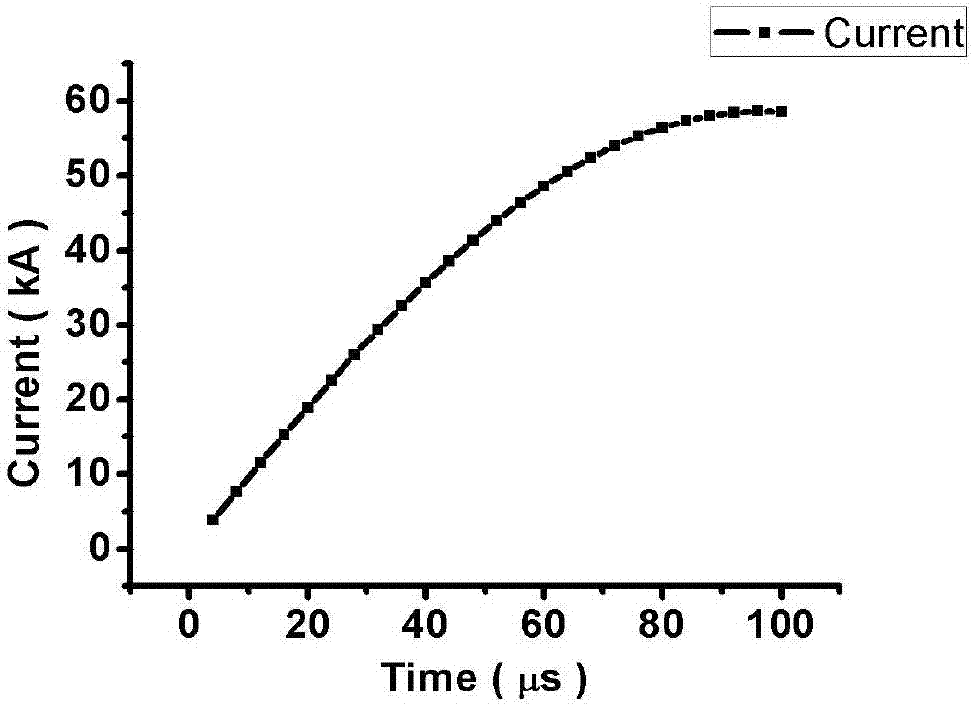
本实用新型属于金属成形制造
技术领域:
,更具体地,涉及一种匀压力电磁成形的装置和匀压力线圈。
背景技术:
:电磁成形是变化的磁场与金属材料中感应涡流相互作用、产生瞬间电磁冲击力而导致的一种高速变形,作为一种高能高速率成形技术,电磁成形在提高铝合金等轻质合金材料成形制造水平、突破一些关键技术瓶颈方面潜力巨大。在电磁成形中,用于平板电磁成形的一般为平面螺旋线圈,但平面螺旋线圈在工件上产生的电磁力分布不均匀,制约了它的应用范围。匀压力线圈作为一种新型线圈,能够在工件上形成比较均匀的电磁力,成形效率比平螺旋线圈更高,在成形车门型腔、手机壳和燃料电池板等组件上具有显著优势,因此受到了广泛的关注。图1为匀压力线圈原理图,在线圈外面有一个凹形导电通道,导电通道和线圈之间绝缘良好并且和成形工件组成了一个封闭的回路。当电容放电时,在工作线圈中产生变化的电流,同时在外面的回路中感应出方向相反的感应电流。由于工件与导电通道形成了回路,因此工件中的感应电流方向、大小相同,所受到的电磁力比较均匀,再加上感应电流回路完全环绕线圈,所以磁场能量损失较小,效率较高。在目前有关匀压力线圈的研究中,为了确保足够的结构强度,使线圈在电磁成形过程中不至于应力过大而变形,常将铜块或铜合金块直接进行切割得到线圈。这种方法通过线圈自身的强度来保证整体结构的强度,因而得到的匀压力线圈必须要有较厚的线圈横截面,使得线圈中电流密度较小,进而导致工件受到的电磁力较小,限制了线圈的成形效率。此外,将铜块切割为匀压力线圈形状技术复杂、切割耗时较长。这些技术缺陷直接制约了匀压力线圈的应用以及相关领域的研究和发展。技术实现要素:针对现有技术的缺陷,本实用新型的目的在于提供一种匀压力电磁成形的装置,旨在解决现有技术中线圈的成形效率低的问题。本实用新型提供了一种匀压力电磁成形的装置,包括:导电通道、线圈和工件;U形导电通道设置在线圈的上方包围线圈,工件设置在线圈的下方,工件与导电通道形成电流回路;线圈包括:导线,环氧板和加固材料;由环氧板构成的骨架为导线提供支撑;加固材料设置在导线外侧作为外加固层,用于提供足够的强度;工作时,受线圈中变化电流的影响,工件与导电通道中感应出了涡流,形成了电流回路,且工件中的感应电流方向、大小相同,则工件受到的电磁力比较均匀;由于线圈选用较薄的紫铜导线缠绕多层多匝而成,因此工件中所受电磁力更大,成形效率更高;为保证线圈强度,将加固材料分别沿着线圈导线绕制的方向和垂直于导线绕制的方向进行缠绕加固,实现高强高效匀压力电磁成形。更进一步地,导线为任意横截面积(不小于最小横截面积)的紫铜导线。更进一步地,当导线的厚度小于透入深度时,导线越薄电流密度越大,感应产生的电流密度也越大,工件上所受电磁力越大,成形效率更高;其中,电流在铜上的透入深度f为电流频率,μ为磁导率,γ为电导率。更进一步地,导线的横截面积其中,ΔT为铜导线最大温升,ρ1为铜的电阻率,c为比热容,ρ2为铜的质量密度,trise为线圈电流波形第一个上升沿时间,I(t)为线圈电流与时间的关系,t为时间。更进一步地,加固材料沿着导线绕制的方向和垂直于导线绕制的方向分别进行缠绕加固。更进一步地,加固材料为玻璃纤维或柴龙(zylon)。本实用新型提供了一种匀压力线圈,包括:导线,环氧板和加固材料;由环氧板构成的骨架为导线提供支撑;加固材料设置在导线外侧作为外加固层,用于提供足够的强度。更进一步地,加固材料沿着导线绕制方向和垂直于导线绕制方向分别进行缠绕加固。更进一步地,加固材料为玻璃纤维或柴龙zylon。更进一步地,导线为任意横截面积的紫铜导线。本实用新型提供了一种基于上述的获取方法得到的匀压力线圈,包括:导线,环氧板和加固材料;由环氧板构成的骨架为导线提供支撑;加固材料设置在导线外侧作为外加固层,用于提供足够的强度。通过本实用新型所构思的以上技术方案,与现有技术相比,由于采用环氧板作为内支撑;在绕制工艺上缠绕加固材料进行外加固,并分别沿着导线绕制方向和垂直于导线绕制方向缠绕,在各个方向上为线圈提供了充足的强度,极大的提高了线圈的整体强度,譬如S-2玻璃纤维极限强度为4.9GPa左右,远大于各种铜类的极限强度。且在本实用新型中,由于单匝导线更薄,最大限度的降低了集肤效应的影响,节省的空间用于绕制的多层线圈具有更高的成形效率。结构更灵活,可以根据实际需要采用任意横截面积(不小于最小横截面积)的铜导线绕制任意匝数与层数的线圈。本实用新型采用铜导线绕制线圈的方式更加简单,高效。附图说明图1是匀压力线圈的原理示意图;图2是一次采用匀压力线圈进行电磁成形实验的电流时间关系图;图3是三种线圈在工件上正中心一点处产生的电磁力大小对比图;图4是本实用新型所述的一种单层匀压力线圈横截面示意图。在所有附图中,其中:1为导电通道,2为线圈,3为工件,2-1为导线,2-2为环氧板,2-3为玻璃纤维。具体实施方式为了使本实用新型的目的、技术方案及优点更加清楚明白,以下结合附图及实施例,对本实用新型进行进一步详细说明。应当理解,此处所描述的具体实施例仅仅用以解释本实用新型,并不用于限定本实用新型。针对上述问题,本实用新型提供了一种具有高强度的绕制匀压力线圈的方法,旨在解决现有技术中线圈电流密度较小、成形效率较低、线圈加工复杂以及加工时间较长的技术问题。本实用新型中,为了提高成形效率,不再采用铜块切割获取匀压力线圈,而是选用较薄的紫铜导线(单玻璃丝包聚酰亚胺薄膜绕包扁铜线)缠绕形成多层多匝的匀压力线圈;同时,由于薄导线自身强度较低无法承受电磁成形过程中的电磁力,选用特定的加固材料作为外加固,环氧板作为内支撑来提高线圈整体的强度。根据电磁感应定律,工件上所受到的电磁力为:其中为工件中的感应电流,为线圈在工件处产生的磁场与工件内涡流在同一点产生的磁场矢量和。感应电流密度越大,工件上所受电磁力也就越大,成形效率越高。根据集肤效应,电流在铜上的透入深度为:其中,f为电流频率,μ为磁导率,γ为电导率。对于电磁成形而言,以一次典型的电磁成形实验为例,线圈内电流大小如图2所示,μ铜=μ0=4π×10-7H/m,γ铜=5.8×107S/m,带入式(2)得透入深度为1.33mm。因此对于多层线圈,当导线厚度大于透入深度时,多出来的部分不但对成形没有帮助,反而使得内层导线离工件更远,降低成形效率;当导线厚度小于透入深度时,导线越薄,电流密度越大,因而感应产生的电流密度也越大,工件上所受电磁力越大,成形效率更高。为了证实采用薄铜导线绕制的线圈成形效率更高,此处对线圈横截面尺寸为4mm×1mm的单层线圈,4mm×4mm的单层线圈与4mm×1mm的双层线圈进行分析,线圈匝数均为16匝,匝间距均为0.5mm。3种线圈电感求得如表1所示,在160μF、10kV电源下对线圈放电(线路电阻10mΩ,线路电感5μH),得到的工件上中心点的电磁力随时间变化的曲线图如图3所示,由图3可知4mm×1mm的双层线圈在工件上产生的电磁力最大,4mm×4mm的单层线圈在工件上产生的电磁力最小,因此本文提出的采用薄铜导线绕制的多层线圈成形效率更高。表1不同横截面线圈电感值4mm×1mm,一层4mm×4mm,一层4mm×1mm,双层电感(μH)5.013.9817.6然而,薄铜导线并不是越薄越好,考虑到发热问题,薄铜导线的温升不能超过规定值,因此导线的横截面积不能低于某一特定值。铜导线的温度指数根据其包含的聚酰亚胺薄膜和粘结漆的温度指数来决定,取其中最低的温度指数。根据方程组(3):可得导线的截面积的表达式(4):其中,R为导线电阻,ρ1为电阻率,L为导线长度,A为导线横截面积,Q为导线产生的热量,I为导线内电流大小,t为通流时间,ΔT为导线温升,c为导线材料比热容,m为导线质量,ρ2为导线材料质量密度。考虑到单玻璃丝包聚酰亚胺薄膜绕包扁铜线耐受温度为155℃,因此在室温条件下,温升ΔT≤130℃,其他常数如铜导线电阻率ρ1=1.75×10-8Ω·m,,比热容c=0.39×103J/(kg·℃),紫铜质量密度ρ2=8.92×103kg/m3。根据图2的电流数据,对式(4)做定积分,可得:因此,电磁绕组线最小横截面积为2.6mm2。为实现上述目的,按照上述思想,提供了一种具有高强度的用于电磁成形的匀压力线圈获取方法,具体可以通过匀压力电磁成形的装置来实现匀压力线圈的获取,其中匀压力电磁成形的装置包括:导电通道1、线圈2、工件3;导电通道1设置在线圈2的上方,工件3设置在线圈2的下方,与导电通道形成电流回路;线圈2由导线2-1,环氧板2-2,加固材料2-3组成,环氧板2-2固定在导线内层作为支撑,导线可以采用任意截面积(不小于最小横截面积)的紫铜导线,而不是必须采用铜块进行切割,加固材料在导线外层作为外加固层,为了对线圈提供足够的强度,加固材料需分别沿着导线绕制的方向和垂直于导线绕制的方向分别进行缠绕加固。在本实用新型中,用于磁体绕制的加固材料可以有多种,具体可以为玻璃纤维或柴龙(zylon)等。在本实用新型中,多层多匝匀压力线圈获取方法具体包括如下步骤:(1)将环氧板固定在绕线机上,由于匝间距越小,工件上的受力越均匀,再加上铜导线外层的漆包线厚度为0.25mm,因此将铜导线按照0.5mm的最小匝间距缠绕在环氧轴心上;(2)选用用于紧固线圈的W19环氧树脂,按照胺的用量(phr)=胺当量×环氧值配置固化剂(W19环氧树脂及其固化剂配比如表2所示),其中phr指每100份树脂所需固化剂的质量份数,胺当量=胺的相对分子量÷胺中活泼氢的个数,环氧值指100g环氧树脂中所含环氧基团的物质的量。随后将配置好的环氧树脂均匀的涂抹在缠绕好的导线上;(3)涂抹完环氧树脂后,根据仿真时线圈所受最大强度选择加固材料,常用加固材料及其强度如表3所示。随后将加固材料沿着导线绕制方向与垂直于导线绕制方向分别在线圈上均匀的缠绕一层;(4)重复步骤(2),在加固材料上均匀的涂抹环氧树脂,完成一层导线的绕制;(5)重复步骤(1)-(4),完成多层多匝匀压力线圈的绕制。表2W19环氧树脂及其固化剂配比表3用于线圈加固的加固材料S-2玻璃纤维柴龙(Zylon)抗拉强度(GPa)4.95.8弹性模量(GPa)87280延展率(%)42.5总体而言,本实用新型所构思的以上技术方案与现有技术相比,有如下优点:(1)线圈强度更高,在结构设计方面采用环氧板作为内支撑;在绕制工艺上缠绕加固材料进行外加固,并分别沿着导线绕制方向和垂直于导线绕制方向缠绕,在各个方向上为线圈提供了充足的强度,极大的提高了线圈的整体强度,譬如S-2玻璃纤维极限强度为4.9GPa左右,远大于各种铜类的极限强度。(2)线圈成形效率更高。由于单匝导线更薄,最大限度的降低了集肤效应的影响,节省的空间用于绕制的多层线圈具有更高的成形效率。结构更灵活。可以根据实际需要采用任意横截面积(不小于最小横截面积)的铜导线绕制任意匝数与层数的线圈。(3)线圈加工简单。相比于采用铜块进行线切割,采用铜导线绕制线圈的方式更加简单,高效。为了使本实用新型的目的、技术方案及优点更加清楚明白,以下结合图4及具体实施例进一步详细说明如下:如图4所示,为本实用新型提供的一种双层匀压力线圈横截面示意图,其中导线2-1为铜导线,加固材料2-3为玻璃纤维,图中由环氧板2-2构成的骨架为导线提供支撑。以该双层匀压力线圈为例,线圈具体绕制过程如下:步骤一:将环氧板固定在绕线机上,将铜导线按照设定好的匝间距缠绕在环氧轴心上。步骤二:选用W19环氧树脂,按表2中比例要求配好固化剂,若固化剂太少,则环氧树脂无法固化,随后缠绕的玻璃纤维无法紧固在线圈上,使线圈强度降低;若固化剂太多,则在绕制线圈的过程中环氧树脂便已固化,影响线圈的制作过程。将配好固化剂的环氧树脂均匀地涂抹在缠绕好的导线上,由于环氧树脂分子链中固有的极性羟基和醚键的存在,使其对各种物质具有很高的粘附力,再加上固化时环氧树脂的收缩性低,产生的内应力小,这也有助于提高粘附强度;此外,在环氧树脂固化之前,由于环氧/固化剂体系存在大量带有极性或强极性官能基的低分子化合物,此时它们的电气性能都很差,随着固化反应的进行,活性基团大量消耗,分子量逐渐增大,以至三度交联网逐渐形成,在这个过程中,它们的电绝缘能力得到了极大的提高。因此固化之后的环氧树脂粘附性强并且介电性能良好,能够很好地固定住线圈导线并提供足够的绝缘强度。步骤三:涂抹完环氧树脂后,再沿着导线绕制方向和垂直于导线绕制方向上均匀缠绕一层玻璃纤维,使玻璃纤维能够均匀地在各个方向上为线圈提供机械强度并保证线圈表面平整。步骤四:交替重复步骤二与步骤三若干次,次数根据具体实验中线圈所需承受的最大电磁力决定。若次数太少,会导致强度不够线圈胀裂;若次数太多,则由于玻璃纤维层过厚使得线圈导线与工件间距离过远而降低成形效率;5-8次,以提供足够的机械强度。步骤五:在玻璃纤维上均匀的涂抹环氧树脂,保证玻璃纤维完全粘附在导线上。到此一层导线便绕制完成。步骤六:重复步骤一至五,完成第二层导线的绕制。本领域的技术人员容易理解,以上所述仅为本实用新型的较佳实施例而已,并不用以限制本实用新型,凡在本实用新型的精神和原则之内所作的任何修改、等同替换和改进等,均应包含在本实用新型的保护范围之内。当前第1页1 2 3