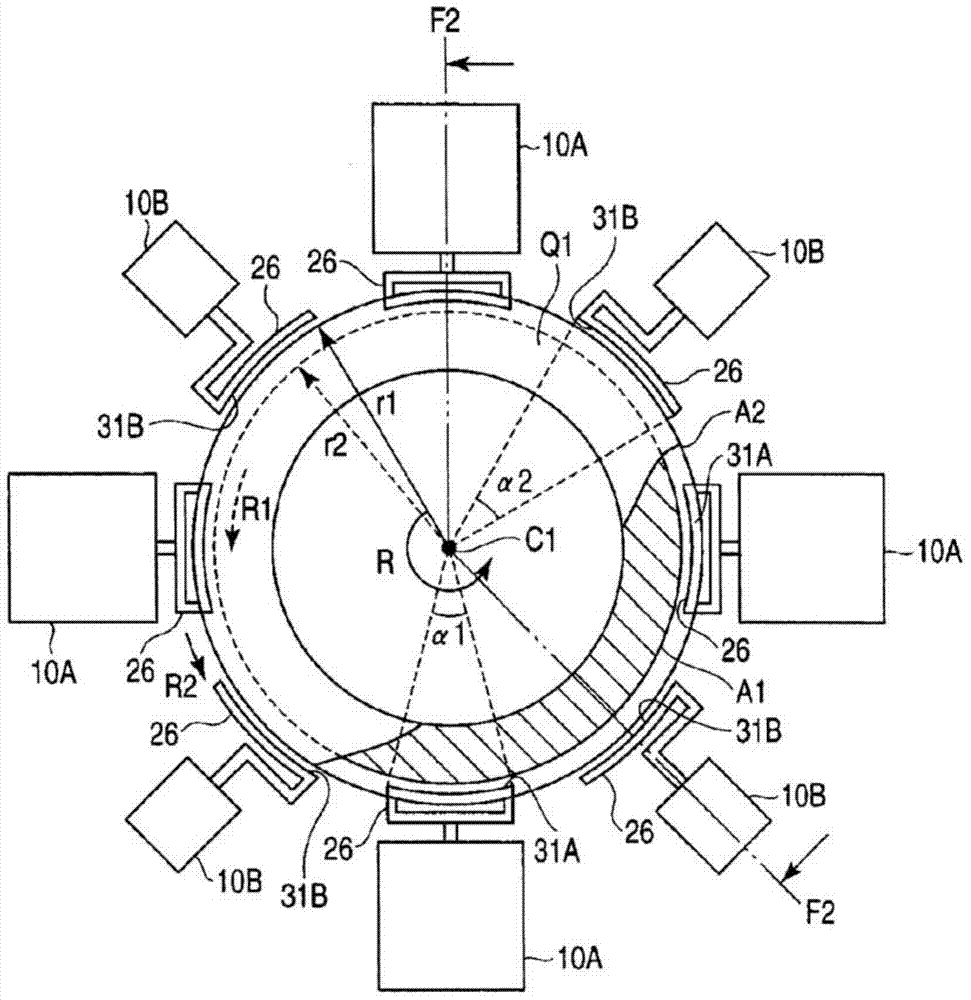
感应加热淬火装置、感应加热淬火方法、感应加热线圈、热处理装置及热处理方法本申请是基于2012年1月30日提出的PCT/JP2010/062847(中国国家申请号201080033937.9)申请(感应加热淬火装置、感应加热淬火方法、感应加热线圈、热处理装置及热处理方法)的分案申请,以下引用其内容。技术领域本发明涉及一种感应加热淬火装置、感应加热淬火方法、感应加热线圈、热处理装置及热处理方法,特别地,涉及一种在提高热处理效率的同时进行均匀处理的技术。
背景技术:已知一种在对金属部件进行高频淬火等热处理的感应加热淬火方法中,使用与被处理部整个区域正对的感应加热线圈集中进行处理的单次加热方式的热处理装置(例如日本特开2005-120415号公报、日本特开2002-174251、日本特开2004-44802)。在上述单次加热方式的热处理装置中,感应加热线圈构成与被处理部整个区域对应的形状。例如在被处理部为圆周形状的情况下,使圆环状的感应加热线圈与被处理部正对,在被处理部为平面状的情况下,使平板状的感应加热线圈与被处理部正对。在上述单次加热方式的加热装置中,由于使用与处理对象物及被处理部的形状及大小对应的感应加热线圈,所以在处理对象物及被处理部较大的情况下,需要大型的感应加热线圈,另外,需要高输出的电力。另一方面,已知一种移动式的热处理装置,其一边使仅与被处理部的一部分正对的感应加热线圈相对于被处理部进行相对移动,一边依次进行加热处理及冷却处理(例如,日本特开2005-89803号公报,日本特开昭60-116724号公报)。在上述移动式的热处理装置中,感应加热线圈构成与被处理部的一部分对应的形状。
技术实现要素:在上述感应加热的技术中,存在下述问题。即,在上述单次加热方式的感应加热淬火装置中,需要使用与被处理部的大小及形状对应的感应加热线圈,因此,在例如被处理部的形状复杂的情况下,感应加热线圈的形状及条件设定变得复杂,难以实现或不可能实现。另外,在被处理部较大的情况下,存在下述问题,即,需要大型的感应加热线圈,需要高输出的电力。此外,在处理对象物中由于感应加热时的热膨胀等而产生变形的情况下,难以适当维持感应加热线圈和处理对象物之间的尺寸。因此,由于需要预先将感应加热线圈设定得较大,所以产生加热效率变差的问题。另一方面,在上述移动式的热处理方法中,在感应加热线圈构成为与被处理部的一部分对应的形状的情况下,单位时间的处理面积较小,处理时间变长,处理效率变差。另外,在一边连续进行加热处理及冷却处理一边移动的情况下,在将例如环状的被处理部作为对象时,存在下述问题,即,在处理的开始部和末端部的分界处产生无法得到所需硬度的软区(softzone)。因此,本发明的目的在于,提供一种不需要高电力就可以容易地实现所期望的加热区域的热处理的技术、可以进行均匀处理的技术、即使是大型的处理对象物也可以提高感应加热时的热处理效率的技术。本发明的一个方式所涉及的感应加热线圈的特征在于,具有加热导体部,其与被处理部的至少一部分相对,一边相对于所述被处理部相对地旋转移动,一边进行所述被处理部的热处理,并与所述旋转的轴向相交叉地配置,所述加热导体部,通过多个弯曲部、和导体部分而形成锯齿形状,所述多个弯曲部以彼此相对的朝向沿所述旋转的周向连续地配置,所述导体部分配置在该相对的弯曲部之间,并与该周向相交叉地延伸,并且,所述弯曲部是向与所述周向相交叉的方向的外侧开口的弯曲部、以及向径向内侧开口的弯曲部,所述导体部分弯曲形成为,与该导体部分的延伸设置方向正交的截面积固定地形成,并且,位于距离所述旋转移动的中心较远的位置而朝向所述径向内侧开口的所述弯曲部侧的所述周向的长度,与位于距离所述旋转移动的中心较近的位置而朝向外侧开口的所述弯曲部侧的所述周向的长度相比更长。本发明的一个方式所涉及的感应加热淬火方法,具有移动加热工序,在该工序中,将多个加热线圈分别与被处理部的至少一部分相对,一边针对所述被处理部实施由所述多个加热线圈进行的热处理,一边使所述被处理部和所述加热线圈沿着所述被处理部的周向相对移动,其中,所述多个加热线圈具有加热导体部,该加热导体部对与处理对象物的被处理部的周向相交叉的轴向的不同部分分别进行感应加热,由所述多个加热线圈的加热导体部进行加热的所述被处理部的各个区域,形成1个连续的加热区域,所述多个加热线圈中的至少1个具有形成为下述锯齿形状的加热导体部,即,将向所述轴向的一侧开口的曲部和向所述轴向的另一侧开口的曲部,以彼此相对的朝向,沿所述周向连续配置。本发明的一个方式所涉及的感应加热线圈的特征在于,具有加热导体部,其与被处理部的至少一部分相对,一边相对于所述被处理部相对地旋转移动,一边进行所述被处理部的热处理,所述加热导体部具有导体部分,其构成为,与所述旋转的周向相交叉而延伸,并且距离所述旋转移动的中心较远的部位中的所述周向的长度与距离所述中心较近的部位中的所述周向的长度相比更长。本发明的另一个方式所涉及的热处理方法的特征在于,具有移动加热工序,在该工序中,将所述感应加热线圈与所述被处理部相对,一边利用感应加热对所述被处理部进行加热,一边使所述被处理部相对于所述感应加热线圈沿着所述周向相对移动。本发明的一个方式所涉及的感应加热线圈的特征在于,具有加热导体部,其由导体部件形成,形成为将向第1方向的一侧开口的曲部和向所述第1方向的另一侧开口的曲部以彼此相对的朝向沿与所述第1方向相交叉的第2方向连续配置的锯齿形状。本发明的一个方式所涉及的热处理装置的特征在于,具有:所述感应加热线圈;高频电源,其与所述感应加热线圈连接;以及移动单元,其使所述被处理部相对于所述感应加热线圈沿所述第2方向相对移动。本发明的一个方式所涉及的热处理方法的特征在于,具有下述工序,即:移动加热工序,在该工序中,将所述感应加热线圈与形成沿所述第2方向连续的无接头的环状的所述被处理部中的一部分相对,一边利用感应加热对所述被处理部进行加热,一边使所述被处理部相对于所述感应加热线圈沿着所述第2方向相对移动;以及冷却工序,在该工序中,在对所述被处理部的所述第2方向上的整个行程进行加热处理后,对所述被处理部进行冷却。附图说明图1是将本发明的第1实施方式所涉及的感应加热淬火装置沿图2中的F2-F2线切断并沿箭头方向观察的剖面图。图2是表示本实施方式所涉及的感应加热淬火装置的俯视图。图3是表示本实施方式所涉及的第1感应加热淬火装置的俯视图。图4是表示本实施方式所涉及的第1加热线圈的正视图。图5是表示本实施方式所涉及的第2感应加热淬火装置的俯视图。图6是表示本实施方式所涉及的第2加热线圈的正视图。图7是表示本实施方式所涉及的加热线圈的剖面构造的说明图。图8是本实施方式所涉及的第1及第2加热区域的说明图。图9是本实施方式所涉及的第3加热区域的说明图。图10是表示本发明的第2实施方式所涉及的感应加热淬火装置的加热导体部的结构的说明图。图11是表示该感应加热淬火装置的加热导体部分的结构的说明图。图12是表示本发明的第3实施方式所涉及的感应加热淬火装置的说明图。图13是表示本发明的第4实施方式所涉及的感应加热淬火装置的要部的说明图。图14是表示本发明的第5实施方式所涉及的感应加热淬火装置的说明图。图15是组装在本发明的第6实施方式所涉及的感应加热淬火装置中的加热线圈的说明图。图16是组装在本发明的第7实施方式所涉及的感应加热淬火装置中的加热线圈的正视图。图17是表示本发明的第8实施方式所涉及的感应加热淬火装置的说明图。图18是表示本发明的第9实施方式所涉及的感应加热淬火装置的说明图。图19是表示本发明的第10实施方式所涉及的感应加热淬火装置的说明图。图20是表示本发明的第11实施方式所涉及的感应加热淬火装置的说明图。图21是表示本发明的第12实施方式所涉及的感应加热淬火装置的说明图。图22是表示本发明的第13实施方式所涉及的感应加热淬火装置的说明图。图23是表示本实施方式所涉及的感应加热装置的俯视图。图24是表示本实施方式所涉及的加热线圈的斜视图。图25是本实施方式所涉及的加热线圈的导体部分的说明图。图26是表示本实施方式所涉及的加热线圈的剖面构造的说明图。图27是表示本发明的第14实施方式所涉及的感应加热装置的加热线圈的斜视图。图28是表示该加热线圈的俯视图。图29是表示该加热线圈的侧视图。图30是表示该加热线圈的导体部分的结构的说明图。图31是表示本发明的第15实施方式所涉及的感应加热淬火装置的说明图。图32是表示本发明的第16实施方式所涉及的导体部分的结构的说明图。图33是表示本发明的第17实施方式所涉及的导体部分的结构的说明图。图34是表示本发明的第18实施方式所涉及的热处理装置的说明图。图35是表示本实施方式所涉及的热处理装置的俯视图。图36是表示本实施方式所涉及的热处理装置的侧视图。图37是表示本实施方式所涉及的热处理装置的正视图。图38是表示本实施方式所涉及的加热线圈的剖面构造的说明图。图39是本发明的第19实施方式所涉及的热处理装置的说明图。图40是本发明的第20实施方式所涉及的热处理装置的说明图。图41是本发明的第21实施方式所涉及的热处理装置的说明图。图42是本发明的第22实施方式所涉及的热处理装置的说明图。图43是本发明的第23实施方式所涉及的热处理装置的说明图。具体实施方式下面,说明本发明的各实施方式。此外,图中箭头X、Y、Z分别表示彼此正交的3个方向。另外,在各图中,为了说明而适当地将结构扩大、缩小或省略而示出。[第1实施方式]下面,参照图1至图9,说明本发明的第1实施方式所涉及的感应加热淬火装置、以及感应加热淬火方法。图1是表示本实施方式所涉及的感应加热淬火装置1的结构的剖面图,图2是俯视图。如图1及图2所示,感应加热淬火装置1具有下述部件而构成,即:移动支撑部(移动单元),其可移动地支撑作为处理对象物的工件Q1;各加热装置10A、10B,其分别在工件Q1的外周配置多个;以及冷却部13(冷却单元),其在工件Q1的加热处理工序之后,对工件Q1进行冷却。设置在下方的冷却部13构成为筒状,包围在加热处理后移动至下方的工件Q1的外侧,对配置在内侧空间13a中的工件Q1进行冷却。在本实施方式中,使用例如具有台阶的圆筒形状的工件Q1,将该工件的带台阶的外周面作为被处理部A。作为处理对象物的一个例子的工件Q1是以轴C1为中心的带台阶的圆筒状部件,在轴向中央形成向内侧凹下的凹部Q1a,在轴向两端形成有向外侧凸出的凸部Q1b。例如,在这里,使用凸部外侧半径r1=1800mm、凹部外侧半径r2=1780mm、内径半径r3=1700mm、轴向(第1方向)长度h1=250mm的工件Q1。此外,外侧壁厚δ1=100mm,内侧壁厚δ2=80mm。一边使工件Q1以轴C1为中心进行旋转移动,一边利用沿工件Q1周围的规定路径配置的多个第1加热装置10A和多个第2加热装置10B,对以无接头的环状即圆形状相连续的被处理部A,在环的连续方向即周向整个区域上进行加热。在被处理部A中,将轴向中央的凹部Q1a的外周面区域作为第1区域A1,将轴向两端的一对凸部Q1b的外周面区域作为第2区域A2。第1区域A1和第2区域A2在处理对象物的轴向上彼此分离,并且在径向上也彼此分离。第1区域A1是轴向长度h2=150mm的圆形带状区域,一对第2区域A2分别为轴向长度h3=50mm的圆形带状区域。如图2所示,多个第1加热装置10A在沿周向的路径中,分别配置在以中心角90度彼此分离的4个部位处。第2加热装置10B在沿周向的路径中,配置在以中心角90度彼此分离的4个部位处,以在各自的部位处与上下一对的凸部Q1b对应的方式,沿轴向各并列配置2个。第1加热装置10A和第2加热装置10B彼此沿周向及轴向分离而交替配置。与第1区域A1相对地确保规定的间隙尺寸G1而配置第1加热装置10A的第1加热导体部31A。第1加热装置10A重点对工件Q1的外周的被处理部A中的第1区域A1进行感应加热。与第2区域A2相对地确保规定的间隙尺寸G2而配置第2加热装置10B的加热导体部31B。第2加热装置10B重点对第2区域A2进行感应加热。在本实施方式中,以轴C1为中心而将沿工件Q1的外周面的周向R设为第1方向,将工件Q1的轴向即Z方向设为第2方向。此外,由于工件Q1为台阶形状,所以第1加热导体部和第2加热导体部的周向R的半径尺寸不同,但通过使工件Q1以轴C1为中心旋转,从而沿两者的周向移动。将包含周向R1及R2的路径规定为移动路径,并且将包含R1及R2在内且以C1为中心的旋转方向设为第2方向R。周向R1的半径是凹部Q1a的外径尺寸的半径尺寸r2与间隙尺寸G1相加后的值,为r2+G1。周向R2的半径为凸部Q1b的外径尺寸的半径尺寸r1与间隙尺寸G2相加后的值,为r1+G2。如图1至图4所示,多个第1加热装置10A及第2加热装置10B分别具有下述部件而构成:作为电源供给单元的高频电源21;导线22、23,其与高频电源21连接;隔板28,其具有与导线22、23连接的一对导电板24、25;感应加热线圈26,其两端分别与一对导电板24、25连接;以及芯部27,其配置在感应加热线圈26的加热导体部31A、31B的背面侧。加热装置10A的感应加热线圈26具有与工件Q1的第1区域A1相对的锯齿形状的加热导体部31A、与加热导体部31A的一端侧31a相连续的第1连接导体部32、与加热导体部31A的另一端侧31b相连续的第2连接导体部33,它们分别连续地一体形成。如图4所示,第1加热装置10A的加热导体部31A形成锯齿形状,即,多个コ字状的弯曲部34、35朝向Z方向的中央开口,交替以彼此相对的朝向沿周向R而连续配置多个。弯曲部34形成朝向下方开口的コ字形状,弯曲部35形成朝向上方开口的コ字形状。相邻的线圈的间隔R5设定为,大于或等于线圈宽度即R4的尺寸的1倍且小于或等于2倍。在这里,作为一个例子,将4个加热导体部31A的第2方向的尺寸L1的合计设定为第1区域A1的第2方向的整个周长的尺寸的1/3左右。即,对于1个加热导体部31A,将第2方向相对于第1区域A1的尺寸比例即覆盖率设定为1/12,将中心角α1设定为30度。如图5及图6所示,第2加热装置10B的感应加热线圈26具有:与工件Q1的第2区域A2相对的发夹形状的加热导体部31B、与加热导体部31B的一端侧31a相连续的第1连接导体部32、与加热导体部31B的另一端侧31b相连续的第2连接导体部33,它们相连续地一体形成。加热导体部31B构成为,在正面观察下,从图6中左侧的一端侧31a开始,以矩形的环箍形状弯曲,使另一端侧31b向一端侧31a的图中下方弯回,图中左侧的两端31a、31b与连接导体部32、33相连续。此外,第2加热装置10B的覆盖率并不限于与第1加热装置10A相同,可以与工件的形状对应而变化。在各加热装置10A、10B中,第1连接导体部32和第2连接导体部33隔着隔板28配置。隔板28构成为,将分别形成矩形平板状的一对导电板24、25和夹持在上述一对导电板24、25之间的矩形平板状的绝缘板38重叠配置,并且上述导电板24、25及绝缘板38经由绝缘衬套39而利用螺栓41及螺母42固定。各导电板24、25经由导线22、23与高频电源21连接。在第1连接导体部32及第2连接导体部33的端部上,分别设置有用于连接冷却液用软管等部件的联接器36、36(仅图示出一个)。如图7中该剖面所示,感应加热线圈26由铜等材质形成为例如矩形的中空形状。该中空部分26a成为冷却液流动的通路。芯部27由硅钢板、树脂羧基铁芯、铁氧体(Ferrite)等具有高磁导率的材料构成,配置在加热导体部31A、31B的背面侧。芯部27形成与加热导体部31A、31B的两侧部及后方壁部一体设置的剖面コ字形状。图1所示的移动支撑部11具有使工件Q1在设置于规定位置的状态下以轴C1为中心旋转移动的功能。此时,移动支撑部11进行控制,将加热导体部31A和第1区域A1之间的间隙尺寸G1维持为规定值,并且将加热导体部31B和第2区域A2之间的间隙尺寸G2维持为规定值。如上所示,第1加热导体部31A和第2加热导体部31B具有彼此不同的形状,并且沿轴向分离,各区域A1、A2的大小、形状及位置也相互不同。因此,如图8所示,以凹部Q1a的Z方向中央部为中心而形成的第1加热区域P1、和以上下一对的凸部Q1b的Z方向中央为中心而形成第2加热区域P2,将轴向上不同的加热区域作为对象。下面,说明本实施方式所涉及的感应加热淬火方法。本实施方式的感应加热淬火方法由下述工序构成,即:移动加热工序,在该工序中,一边将被处理部A加热,一边使被处理部A和加热导体部31A、31B相对移动;以及冷却工序,在该工序中,在移动加热工序后对被处理部A进行冷却。在移动加热工序中,使第1加热导体部31A与作为被处理部A的一部分的第1区域A1相对,并且使具有与第1加热导体部31A的第1加热区域P1不同的第2加热区域P2的第2加热导体部31B,与作为被处理部A的至少一部分的第2区域A2相对,一边利用第1加热导体部31A及第2加热导体部31B对被处理部A进行加热,一边使区域A1、A2相对于第1加热导体部31A及第2加热导体部31B沿规定的第2方向R相对移动。具体地说,在使加热导体部31A、31B分别与第1区域A1、A2相对的状态下,如果使高频电源21成为接通状态,则高频电流经由导线22、第1导电板24、第1连接导体部32、加热导体部31、第2连接导体部33、第2导电板25及导线23的顺序,返回高频电源21。此时,在加热导体部31A、31B中,高频电流从一端31a侧向另一端31b侧流动,在加热导体部31A、31B的表面产生感应电流,分别重点对相对配置的区域A1、A2进行加热。这样,在轴向及径向上分离一定距离的多个部位被同时加热。即,在彼此分离的各部位处,对各自相对的工件Q1的表面实施加热处理。在进行该加热处理的同时,利用移动支撑部11,在将间隙尺寸G1、G2维持为规定值的状态下,使工件Q1以轴C1为中心进行旋转,从而使被处理部A相对于加热导体部31A、31B沿第2方向R以规定的速度相对移动。例如,在这里,一边维持电力为100~150kW,维持间隙尺寸G1、G2=2.5mm,一边以200~300mm/sec的速度相对移动。利用该移动加热工序,在被处理部A的各部位上,按顺序实施由所述第1加热导体部进行的第1热处理、和由所述第2加热导体部进行的第2加热。在这里,通过使工件Q1旋转90度,从而在被处理部A的整个外周上分别进行第1及第2加热。由多个加热导体部31A、31B加热的被处理部A的各个加热区域P1、P2形成1个连续的加热区域P3。因此,如图8及图9所示,将第1及第2加热区域P1、P2合成,作为所期望的第3加热区域P3进行热处理。然后,在对被处理部的所述第2方向上的全部行程进行移动加热工序后,移动支撑部11使工件Q1沿轴向移动至下方的冷却部13。冷却部13对配置在由冷却套管围绕的冷却区域即空间13a中的工件Q1,利用冷却液进行冷却(冷却工序)。根据本实施方式所涉及的感应加热线圈、感应加热淬火装置及感应加热淬火方法,可以得到下述效果。根据上述实施方式,通过将多个加热导体部31A、31B组合而进行热处理,从而可以将位置不同的多个加热区域合成而得到1个连续的加热区域,因此,可以以简单的结构实现所期望的加热区域的热处理。即使在被处理部的形状复杂的情况下,也可以以简单的结构实现均匀的所期望的热处理。另外,通过使对轴向上较大的区域即第1区域A1进行加热的第1加热导体部31A,形成为连续具有多个曲部的锯齿形状,从而可以确保强磁场,并且得到良好的温度特性。因此,可以以较少的电力进行高速且均匀的热处理。在使用本实施方式所涉及的锯齿形状的加热导体部31,以电力100kW而在第1区域A1的表面达到温度为850度的情况下,可以以200~300mm/sec的速度,加热时间=300s而实现。即,通过使用具有锯齿形状的加热导体部31的感应加热线圈26,从而可以利用例如作为与第1区域A1对应的发夹状的感应加热线圈无法实现的移动式的局部加热而实现大型工件的热处理。在例如以发夹状的感应加热线圈进行的平面(端面)加热中,线圈效率为30~40%,但在上述锯齿形状的感应加热线圈中,线圈效率超过70%。另外,通过使用上述高效率的加热线圈,在被处理部A为环状的情况下,可以实现处理开始端及结束端中没有软区的均匀的热处理。因此,例如在将滚动轴承作为工件,将转动体所通过的轨道面作为被处理部A的情况下,可以形成没有软区的均匀的硬化层,因此,可以得到特别良好的特性。由于在一边仅与被处理部A的一部分相对一边相对移动的同时,进行加热处理,所以即使在被处理部A及工件Q1为大型的情况下,也可以将加热导体部31的尺寸抑制得较小,可以使各加热装置10A、10B小型。因此,可以降低所需的电力,并且将制造成本抑制得较低。另外,由于在一边仅与被处理部A的一部分相对一边相对移动的同时,进行加热处理,所以在将具有圆形等弯曲部的部件作为工件的情况下,即使由于热膨胀等原因使工件变形,也可以容易地维持适当的间隙尺寸。例如,在使用与圆形的被处理部对应的圆环状的感应加热线圈,以单次加热方式进行热处理的情况下,由于热膨胀而会使工件变形,所以需要预先将感应加热线圈设定得较大,因此,存在加热效率较差的问题,但在如本实施方式所示覆盖率较小的情况下,仅调整与工件之间的配置就可以维持适当的间隙。[第2实施方式]下面,参照图10及图11,说明本发明的第2实施方式所涉及的感应加热淬火装置2。此外,由于除了工件Q2及加热导体部31的形状之外,与上述第1实施方式相同,所以省略共通的说明。此外,工件Q2形成为具有圆环状的平面部的圆筒状形状。图10是表示本实施方式所涉及的感应加热淬火装置2的配置的俯视图,图11是表示该感应加热淬火装置2的加热导体部31的形状的说明图。在本实施方式中,如图10所示,工件Q2形成为上下的端面为平面状的圆筒形状,将该端面作为被处理部A。另外,第1加热装置10A的加热导体部31,将多个的弯曲部134、135均以彼此相对的朝向沿周向R连续地配置多个,并且形成为在相对的弯曲部134、135之间分别配置弯曲的导体部分136的锯齿形状。多个弯曲部134形成为朝向与移动方向相交叉的方向的一侧即外侧开口的弯曲形状,弯曲部135形成为朝向另一侧即径向内侧开口的弯曲形状。如图10及11所示,多个导体部分136构成为,与周向R相交叉并延伸,并且距离作为旋转中心的轴C1较远的部位中的周向长度与距离轴C1较近的部位中的周向长度相比更长,周向上的长度与所述周向的速度相对应而形成。导体部分136通过在保持与其延伸设置方向正交的截面积及剖面形状固定的情况下,弯曲为使距离轴C1较远的部位中的延伸设置角度与距离轴C1较近的部位中的延伸设置角度相比,相对于周向R的角度较小,从而使周向的速度与长度对应。在本实施方式中,多个导体部分136在径向上划分为3个部分,其中心线C2在相邻的部分的边界处,分别以α1=α2=150度弯曲。该中心线沿着各部分的延伸设置方向。径向内侧的第1部分136a相对于周向R形成θ1=90度的角度,中间的第2部分136b以相对于周向R形成θ2=60度的角度的方式倾斜,最外侧的第3部分136c以相对于周向R形成θ3=30度的角度的方式倾斜。即,形成θ1>θ2>θ3。例如,在这里,以工件的最内侧的点P1和最外侧的点P3这2个部位为基准而进行尺寸设定。如果将与第1部分136a相对的被处理部A1上的某一基准点P1的旋转半径(距离轴心C1的距离)设为r4,将与第3部分136c相对的被处理部A1上的某一基准点P3的旋转半径(距离轴心C1的距离)设为r5,将与P1相对的第1部分136a的周向尺寸设为L1,将与P3相对的第3部分136c的周向尺寸设为L3,则导体部分136设定为L1:L3≒r4:r5,与作为旋转中心的轴C1相距的距离和周向尺寸对应。在此情况下,如果将P1和P3作为基准,则相对于与旋转直径成正比的周向速度,周向尺寸(距离)成为反比,通过的时间即加热时间保持固定。另外,中间的第2部分136b的尺寸L2以成为L1和L3之间的尺寸的方式,设定为L1<L2<L3。在本实施方式中,也可以得到与上述第1实施方式相同的效果。另外,由于本实施方式的感应加热淬火装置2设定为,在以轴C1为中心而使工件Q2旋转移动的情况下,在工件Q2横穿通过加热导体部31的速度较快的外周侧,与速度较慢的内侧相比,加热导体部31的移动方向的尺寸较大,所以可以使通过的时间均匀化,使热处理时间均匀化。[第3实施方式]下面,参照图12,说明本发明的第3实施方式所涉及的感应加热淬火装置2。此外,由于除了工件Q3的形状和加热导体部31沿着工件Q3的倾斜面这一点之外,与上述实施方式相同,所以省略共通的说明。感应加热淬火装置2的俯视图与图10相同,加热导体部31的俯视图与图11相同,所以省略。在本实施方式中,如图12所示,工件Q3形成为上下的外周面倾斜的鼓形状,将其外周面设为被处理部A。将工件Q3的倾斜的上外周面设为第1区域A1,将倾斜的下外周面设为第2区域A2。本实施方式所涉及的感应加热淬火装置3构成为具有:第1加热装置10A,其对上表面的第1区域A1进行感应加热;以及第2加热装置10A,其对下表面的第2区域A2进行感应加热。本实施方式的加热导体部31A均构成为,相对于轴向及周向倾斜,分别沿着工件Q3的上下外周面。如图10所示,第1加热装置10A的加热导体部31A将多个弯曲部134、135均以彼此相对的朝向沿周向R连续地配置多个,并且形成为在相对的弯曲部134、135之间分别配置弯曲的导体部分136的锯齿形状。多个弯曲部134形成为朝向与移动方向相交叉的方向的一侧即外侧开口的弯曲形状,弯曲部135形成为朝向另一侧即径向内侧开口的弯曲形状。多个导体部分136构成为,与周向R相交叉并延伸,并且距离作为旋转中心的轴C1较远的部位中的周向长度与距离轴C1较近的部位中的周向长度相比更长,周向上的长度与所述周向的速度相对应而形成。导体部分136通过在保持与其延伸设置方向正交的截面积及剖面形状固定的情况下,弯曲为使距离轴C1较远的部位中的延伸设置角度与距离轴C1较近的部位中的延伸设置角度相比,相对于周向R的角度较小,从而使周向的速度与长度对应。在本实施方式中,也可以得到与上述第1实施方式相同的效果。[第4实施方式]下面,参照图13,说明本发明的第4实施方式所涉及的感应加热淬火装置3。图13是表示本实施方式所涉及的感应加热淬火装置的配置的说明图。此外,由于除了工件Q4的形状之外与上述第2实施方式相同,所以省略共通的说明。工件Q4为中空体状,具有相对于轴向及周向倾斜的内周面。本实施方式的加热导体部31A均构成为,相对于轴向及周向倾斜,分别沿着工件Q4的上下内周面。如图10所示,第1加热装置10A的加热导体部31A将多个弯曲部134、135均以彼此相对的朝向沿周向R连续地配置多个,并且形成为在相对的弯曲部134、135之间分别配置弯曲的导体部分136的锯齿形状。多个弯曲部134形成为朝向与移动方向相交叉的方向的一侧即外侧开口的弯曲形状,弯曲部135形成为朝向另一侧即径向内侧开口的弯曲形状。多个导体部分136构成为,与周向R相交叉并延伸,并且距离作为旋转中心的轴C1较远的部位中的周向长度,与距离轴C1较近的部位中的周向长度相比更长,周向上的长度与所述周向的速度相对应而形成。导体部分136通过在保持与其延伸设置方向正交的截面积及剖面形状固定的情况下,弯曲为使距离轴C1较远的部位中的延伸设置角度与距离轴C1较近的部位中的延伸设置角度相比,相对于周向R的角度较小,从而使周向的速度与长度对应。在本实施方式中,也可以得到与上述第1~3实施方式相同的效果。[第5实施方式]下面,参照图14,说明本发明的第5实施方式所涉及的感应加热淬火装置4。此外,由于除了工件Q5的形状及被处理部A倾斜这一点之外,与上述第1实施方式相同,所以省略共通的说明。图14是表示本实施方式所涉及的感应加热淬火装置4的配置的侧视图。在本实施方式中,如图14所示,将带台阶的剖面梯形形状的工件Q5的周面设为被处理部A。将轴向中央部分的外周面设为第1区域A1,将轴向两端中向外侧凸出的台阶部分的外周面设为第2区域A2。感应加热淬火装置4具有:第1加热装置10A,其对轴向中央部分的第1被处理部A1进行感应加热;以及第2加热装置10B,其对轴向两端的2个部位的第2被处理部A2进行感应加热。区域A1、A2形成相对于轴倾斜的面,与转动中心之间的距离变化。本实施方式的加热导体部31A、31B构成为,均相对于轴向及周向倾斜,沿着工件Q5的上下外周面。加热导体部31A的形状例如使用与第3实施方式相同的加热导体部31A。即,形成为下述锯齿形状,即,沿轴向倾斜,并且具有相对的弯曲部134、135,导体部分136在保持与其延伸设置方向正交的截面积及剖面的形状固定的情况下,弯曲为使距离轴C1较远的部位中的延伸设置角度,与距离轴C1较近的部位中的延伸设置角度相比,相对于周向R的角度较小。在本实施方式中,也可以得到与上述第1~4实施方式相同的效果。在上述实施方式中,作为弯曲部,例示了以剖面コ字状弯曲为矩形的弯曲部34、35,但并不限定于此。[第6实施方式]在图15中,作为本发明的第6实施方式,也可以应用具有弯曲为半圆周状的形状的弯曲部(曲部)34、35的构造的第1加热导体部31C。在本实施方式中,也可以得到与上述第1~5实施方式相同的效果。[第7实施方式]作为本发明的第7实施方式,如图16所示,也可以应用具有弯曲为梯形形状的弯曲部34、35的构造的第1加热导体部31D。在本实施方式中,也可以得到与上述第1~5实施方式相同的效果。此外,也可以不采用上述弯曲形状,而形成如第1实施方式所示的锯齿形状。在上述实施方式中,举出通过使工件Q1旋转而进行相对移动的例子,但并不限定于此,也可以通过使加热导体部31A、31B侧移动而进行相对移动。[第8实施方式]在上述第1~5实施方式中,例示了将第1加热装置10A及第2加热装置10B分别配置在4个部位处的情况,但并不限定于此。图17概略地示出作为本发明的第8实施方式而将第1加热装置10A及第2加热装置10B分别配置2个的情况下的位置关系。在本实施方式中,也可以得到与上述第1~5实施方式相同的效果。[第9实施方式]图18概略地示出作为本发明的第9实施方式而将第1加热装置10A及第2加热装置10B分别配置3个的情况下的位置关系。在本实施方式中,也可以得到与上述第1~5实施方式相同的效果。[第10实施方式]图19概略地示出作为本发明的第10实施方式而将第1加热装置10A及第2加热装置10B分别配置5个的情况下的位置关系。在本实施方式中,也可以得到与上述第1~5实施方式相同的效果。[第11实施方式]图20概略地示出作为本发明的第11实施方式而将第1加热装置10A及第2加热装置10B分别...