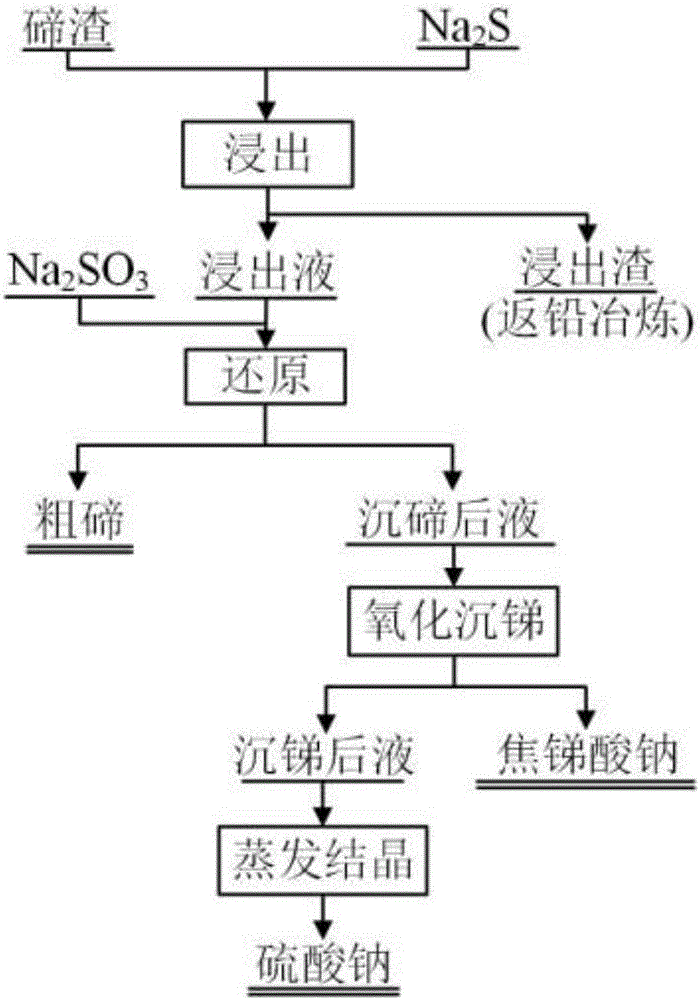
本发明涉及冶金
技术领域:
,尤其涉及一种从碲渣中选择性分离回收碲和锑的方法。
背景技术:
:碲属于稀散元素,被誉为“现代工业、国防与尖端技术的维生素,创造人间奇迹的桥梁”,是当代高技术新材料的支撑材料。碲及其化合物广泛应用于电子技术、冶金、通讯、航天、能源、医药等领域,如碲化铅是制冷的良好材料;碲化铅和碲化铋是用于制作感光器和温差发电的主要材料;工业纯碲广泛用作合金添加剂,以改良钢的机械加工性能;另外,碲的化合物还可以制成各种触媒,用于石油裂化、煤氢化、脱氯等过程,还可用于医药杀菌剂、玻璃着色剂、陶瓷等。碲渣主要来源于铜、铅阳极泥火法处理过程及粗铋碱性精炼过程。从碲渣中回收碲的方法主要有碱浸法、加压碱浸、酸浸、加压酸浸、铜粉置换、氯化法和溶剂萃取法等。碲的化学性质比较特殊,具有明显的两性特征,易分散,故其回收率低,并且存在操作危险、对设备以及材质要求高。目前,工业上主要采用破碎→球磨→水浸→中和沉碲→煅烧→电解的方法回收碲,但该过程碲的浸出率仅为70%左右,且工艺冗长复杂。中国发明专利公开号CN104762471A,公开了中南大学刘伟锋等人提出的一种碲渣强化浸出的方法。将硫化钠、亚硫酸钠和硫代硫酸钠中的二种或三种配制成溶液,把碲渣按一定液固比加入溶液中,通入氮气作为保护气氛,在高温高压下,使MeTeO3和MeTeO4等难溶物转化为可溶的Na2TeO3,并使溶液的重金属离子生成MeS沉淀进入浸出渣,最后采用真空过滤实现固液分离,浸出液碲锭,浸出渣再回收其他有价金属。此发明专利在高温高压下浸出碲,存在能耗高、操作危险、对设备以及材质要求高的缺陷。中国发明专利公开号CN1821060A,云南冶金集团总公司王吉坤提出的采用加压酸浸工艺从铜阳极泥中浸出碲的方法。该方法主要是将调浆好的铜阳极泥在高压釜中控温100-180℃,通入气体氧化介质,维持压力0.5-1.6MPa直接进行硫酸浸出回收碲。此发明专利采用酸性气氛,在高温高压下浸出碲,存在操作危险、对设备以及材质要求高的缺陷。技术实现要素:本发明所要解决的技术问题是,克服以上
背景技术:
中提到的不足和缺陷,提供一种分离效果好、选择性好、工艺简单、对设备要求不高的从碲渣中选择性分离回收碲和锑的方法。为解决上述技术问题,本发明提出的技术方案为:一种从碲渣中选择性分离回收碲和锑的方法,包括以下步骤:(1)将碲渣加入到硫化钠溶液中,搅拌浸出后过滤,得到浸出液和浸出渣;(2)向步骤(1)所得浸出液中加入亚硫酸钠进行反应,反应结束后过滤,得到粗碲和沉碲后液;(3)向步骤(2)所得沉碲后液中加入双氧水进行反应,反应完成后过滤,得到焦锑酸钠和沉锑后液。先将碲渣加入到硫化钠溶液中搅拌浸出,碲渣中不溶性的碲酸钠和锑酸钠可与硫化钠反应生成可溶性的硫代碲酸钠和硫代锑酸钠进入浸出液中;而铅、铋等则生成硫化沉淀富集于浸出渣中,实现了碲渣中碲和锑的高效浸出。该步骤发生的主要化学反应如下:Na2TeO4+4Na2S+4H2O→Na2TeS4+8NaOHNaSb(OH)6+4Na2S→Na3SbS4+6NaOHPbO+Na2S+H2O→PbS+2NaOH浸出渣可利用传统还原熔炼方法实现铅和铋的回收。向含碲和锑的浸出液中加入亚硫酸钠,浸出液中的硫代碲酸钠能被亚硫酸钠快速还原,生成碲单质,经过滤后得到粗碲和沉碲后液,实现了碲的选择性还原回收。该步骤发生的主要化学反应如下:Na2TeS4+3Na2SO3→3Na2S2O3+Na2S+Te↓沉碲后液中含有锑,再向沉碲后液中加入双氧水,沉碲后液中的硫代锑酸钠在双氧水的氧化作用下,生成焦锑酸钠。该步骤发生的主要化学反应如下:Na3SbS4+16H2O2+6NaOH→NaSb(OH)6↓+4Na2SO4+16H2O该方法可选择性分离回收碲渣中的碲和锑,使碲和锑大部分进入浸出液中,而铅和铋等有价金属全部富集于浸出渣中,分离效果好,且无需在高温高压下进行浸出,能耗低、危险性小、对设备的要求较低。硫化钠浸出液中的碲利用亚硫酸钠在碱性条件下进行选择性一步还原制备粗碲产品,反应快速高效,选择性良好,有效避免了传统碲生产过程中净化、中和沉淀、煅烧、造液等工序,大大缩短了碲的工艺流程。而沉碲后液利用双氧水氧化,得到锑酸钠产品,实现了碲和锑的选择性分离。采用该方法,在步骤(1)中碲选择性浸出过程,碲浸出率达94%以上,锑的浸出率达95%以上;在步骤(2)中碲的选择性还原过程中,碲的还原率达98%以上,所得粗碲的纯度达99%以上。作为对上述技术方案的进一步优化:优选的,步骤(1)中,将碲渣加入到硫化钠溶液中之前,先将碲渣磨细,然后过孔径为75-150μm的筛网;步骤(1)、步骤(2)和步骤(3)中,所述过滤均为真空抽滤。在加硫化钠浸出之前,先将碲渣磨细、过筛,有利于提高碲和锑的浸出率。所有过滤均采用真空抽滤方式,可提高过滤效率,缩短过滤时间。更优选的,将步骤(3)所得沉锑后液进行蒸发结晶,得到硫酸钠,提高了资源利用率,并降低了后续处理难度。优选的,步骤(1)中,所述硫化钠溶液的浓度为100-200g/L,硫化钠的浓度对碲和锑的浸出效果有很大影响,当硫化钠浓度为0<C(Na2S)<40g/L时,碲的浸出率由18%快速升高至95%,而锑的浸出率几乎为零;当40g/L<C(Na2S)<100g/L时锑的浸出率由零升高至96%,当C(Na2S)>200g/L时,碲和锑的浸出率维持不变,而硫化钠浓度过高会导致生产成本升高。因此,将硫化钠溶液的浓度控制在100-200g/L,可在步骤(1)中将碲渣中的碲和锑进行高效浸出。所述硫化钠溶液的体积与碲渣的质量的液固比为4.5-10L/kg。液固比过小时,浸出效果不好,碲和锑的浸出率偏低,而液固比过高则会导致废水量增加,不利于生产。优选固液比为4.5-10L/kg既可以保证浸出效果,又不至于增加过多废水。更优选的,步骤(1)中,浸出的温度控制在80-95℃,浸出的温度对锑的浸出效果影响很大,而对碲的浸出效果影响很小。当浸出温度为常温时,碲的浸出率可达到92%,随着温度的升高,碲的浸出率增加不明显;而对于锑,当浸出温度为常温时,锑的浸出率几乎为零,随着温度升高至80-95℃,锑的浸出率达到95%左右。因此,本发明将浸出的温度控制在80-95℃,可以确保在步骤(1)中同时将碲和锑高效浸出。浸出的时间控制在60-120min,一般地,浸出时间越长,反应越彻底,但是,当反应完成后再继续浸出会大大延长生产周期,不利于提高生产效率。优选的,步骤(2)中,所述亚硫酸钠的过量系数为1.5-2.0。该过量系数由化学方程式:Na2TeS4+3Na2SO3→3Na2S2O3+Na2S+Te↓计算得到,由溶液中碲的浓度和体积算出需要消耗的亚硫酸钠的理论量。过量系数即为理论量的倍数。亚硫酸钠的过量系数过低时碲的还原不彻底,反应不完全,而过量系数过高,则会造成试剂的浪费,生产成本过高。综合考虑,选择过量系数为1.5-2.0较为合适。更优选的,步骤(2)中,所述反应的温度控制在25℃-90℃,反应的时间控制在15-120min。优选的,步骤(3)中,所述双氧水的过量系数为1.8-2.2。双氧水的过量系数由以下化学方程式计算得到:Na3SbS4+16H2O2+6NaOH→NaSb(OH)6↓+4Na2SO4+16H2O由溶液中锑的浓度和体积算出需要消耗的双氧水的理论量。过量系数即为理论量的倍数。更优选的,步骤(3)中,所述反应的温度控制在20℃-30℃,反应的时间控制在100-140min。优选的,所述碲渣为粗铋碱性精炼过程产生的碲渣,其主要包含的化学元素为锑、碲、铅、钠、铋和铁。与现有技术相比,本发明的优点在于:(1)本发明采用硫化钠溶液处理碲渣,可实现碲渣中碲、锑的高效浸出,且铅、铋等有价金属则富集在浸出渣中,分离富集效果好。(2)本发明采用亚硫酸钠在碱性条件下,直接选择性还原回收含碲和锑的浸出液中的碲,一步制备得到粗碲产品,反应快速高效,选择性良好,有效避免了传统碲生产过程中净化、中和沉淀、煅烧、造液等工序,大大缩短了碲的工艺流程。(3)本发明无需在高温高压下进行浸出,能耗低、危险性小、对设备要求较低。(4)本发明将沉碲后液利用双氧水氧化,得到焦锑酸钠产品,实现了碲和锑的选择性分离,将沉锑后液进行蒸发结晶,得到硫酸钠,提高了资源利用率。(5)采用本发明的方法,在硫化钠选择性浸出碲和锑过程中,碲的浸出率达94%以上,锑的浸出率达95%以上;在亚硫酸钠选择性还原碲的过程中,碲的还原率达98%以上,所得粗碲的纯度达99%以上。附图说明为了更清楚地说明本发明实施例或现有技术中的技术方案,下面将对实施例或现有技术描述中所需要使用的附图作简单地介绍,显而易见地,下面描述中的附图是本发明的一些实施例,对于本领域普通技术人员来讲,在不付出创造性劳动的前提下,还可以根据这些附图获得其他的附图。图1为本发明的工艺流程图。图2为本发明所用原料碲渣的XRD图谱。图3为本发明实施例1中得到的浸出渣的XRD图谱。图4为本发明实施例1中得到的粗碲的XRD图谱。图5为本发明实施例1中得到的焦锑酸钠的XRD图谱。图6为本发明实施例1中得到的硫酸钠的XRD图谱。具体实施方式为了便于理解本发明,下文将结合说明书附图和较佳的实施例对本发明作更全面、细致地描述,但本发明的保护范围并不限于以下具体的实施例。除非另有定义,下文中所使用的所有专业术语与本领域技术人员通常理解的含义相同。本文中所使用的专业术语只是为了描述具体实施例的目的,并不是旨在限制本发明的保护范围。除非另有特别说明,本发明中用到的各种原材料、试剂、仪器和设备等均可通过市场购买得到或者可通过现有方法制备得到。实施例1:一种本发明的从碲渣中选择性分离回收碲和锑的方法,该碲渣为粗铋碱性精炼过程产生的碲渣,其主要化学组成如表1所示,其XRD图谱如图2所示。表1碲渣的化学组成表元素SbTePbNaBiFe含量(ωt%)23.0611.6013.707.165.212.16该方法的工艺流程图如图1所示,主要包括以下步骤:(1)将如表1所示化学组成的碲渣磨细至100%过孔径为75μm-150μm的筛网,然后将过筛后的碲渣加入配制的浓度为100g/L的硫化钠溶液中(硫化钠溶液的体积和碲渣的质量比值为10L/kg),搅拌浸出,浸出过程中的温度为90℃,浸出时间为90min,浸出完成后采用真空抽滤方液固分离,得到浸出液和浸出渣(其XRD图谱见图3),浸出渣利用传统的还原熔炼方法回收其中的铅和铋;(2)将步骤(1)后的浸出液加入亚硫酸钠进行还原,所加亚硫酸钠的过量系数为2.0倍,反应温度为25℃,反应时间为15min,还原反应完成后采用真空抽滤方式液固分离,得到沉碲后液和粗碲(其XRD图谱见图4);(3)步骤(2)所得沉碲后液采用双氧水氧化沉锑,所加双氧水的过量系数为2.0倍,反应温度为25℃,反应时间为120min,氧化反应完成后采用真空抽滤方式液固分离,得到沉锑后液和焦锑酸钠(其XRD图谱见图5);(4)对步骤(3)所得沉锑后液进行蒸发冷却结晶,得到硫酸钠(其XRD图谱见图6)。本实施例步骤(1)中碲和锑的选择性浸出过程中,碲的浸出率达94.33%,锑的浸出率达95.67%;而铅和铋不浸出。步骤(2)中的碲选择性还原过程中,碲的还原率达98.90%,所得粗碲的纯度达99.36%。实施例2:一种本发明的从碲渣中选择性分离回收碲和锑的方法,该碲渣为粗铋碱性精炼过程产生的碲渣,其主要化学组成如表1所示。该方法的工艺流程图如图1所示,主要包括以下步骤:(1)将如表1所示化学组成的碲渣磨细至100%过孔径为75μm-150μm的筛网,然后将过筛后的碲渣加入配制的浓度为150g/L的硫化钠溶液中(硫化钠溶液的体积和碲渣的质量比值为8L/kg),搅拌浸出,浸出过程中的温度为95℃,浸出时间为120min,浸出完成后采用真空抽滤方液固分离,得到浸出液和浸出渣,浸出渣利用传统的还原熔炼方法回收其中的铅和铋;(2)将步骤(1)后的浸出液加入亚硫酸钠进行还原,所加亚硫酸钠的过量系数为1.5倍,反应温度为60℃,反应时间为60min,还原反应完成后采用真空抽滤方式液固分离,得到沉碲后液和粗碲;(3)步骤(2)所得沉碲后液采用双氧水氧化沉锑,所加双氧水的过量系数为2.0倍,反应温度为25℃,反应时间为120min,氧化反应完成后采用真空抽滤方式液固分离,得到沉锑后液和焦锑酸钠;(4)对步骤(3)所得沉锑后液进行蒸发冷却结晶,得到硫酸钠。本实施例步骤(1)中碲和锑的选择性浸出过程中,碲的浸出率达95.64%,锑的浸出率达96.78%;而铅和铋不浸出。步骤(2)中的碲选择性还原过程中,碲的还原率达98.58%,所得粗碲的纯度达99.28%。实施例3:一种本发明的从碲渣中选择性分离回收碲和锑的方法,该碲渣为粗铋碱性精炼过程产生的碲渣,其主要化学组成如表1所示。该方法的工艺流程图如图1所示,主要包括以下步骤:(1)将如表1所示化学组成的碲渣磨细至100%过孔径为75μm-150μm的筛网,然后将过筛后的碲渣加入配制的浓度为200g/L的硫化钠溶液中(硫化钠溶液的体积和碲渣的质量比值为4.5L/kg),搅拌浸出,浸出过程中的温度为80℃,浸出时间为60min,浸出完成后采用真空抽滤方液固分离,得到浸出液和浸出渣,浸出渣利用传统的还原熔炼方法回收其中的铅和铋;(2)将步骤(1)后的浸出液加入亚硫酸钠进行还原,所加亚硫酸钠的过量系数为1.8倍,反应温度为90℃,反应时间为120min,还原反应完成后采用真空抽滤方式液固分离,得到沉碲后液和粗碲;(3)步骤(2)所得沉碲后液采用双氧水氧化沉锑,所加双氧水的过量系数为2.0倍,反应温度为25℃,反应时间为120min,氧化反应完成后采用真空抽滤方式液固分离,得到沉锑后液和焦锑酸钠;(4)对步骤(3)所得沉锑后液进行蒸发冷却结晶,得到硫酸钠。本实施例步骤(1)中碲和锑的选择性浸出过程中,碲的浸出率达95.56%,锑的浸出率达96.63%;而铅和铋不浸出。步骤(2)中的碲选择性还原过程中,碲的还原率达99.15%,所得粗碲的纯度达99.41%。以上所述仅为本发明的优选实施例而已,并不用于限制本发明,对于本领域的技术人员来说,本发明可以有各种更改和变化。凡在本发明的精神和原则之内,所作的任何修改、等同替换、改进等,均应包含在本发明的保护范围之内。当前第1页1 2 3