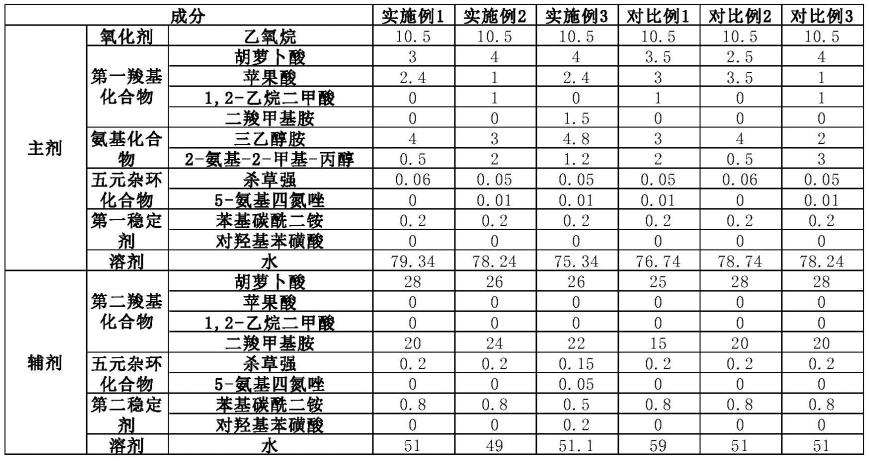
1.本发明涉及蚀刻液领域,尤其涉及ipcc23f1领域,更具体地,涉及一种高铜离子负载的铜金属蚀刻液组合物及其应用。
背景技术:2.现有刻蚀过程中,面板厂商为了缩短制程工艺,降低生产成本,采用4道光罩工艺,其中s/d(源极/漏极)线与半导体a-si层采用一道mask(掩膜程序),那么该s/d线需经过两次蚀刻,这就导致s/d线会有很大的线宽损失,极易引发倒角。
3.现有技术中,申请公布号为cn112522705a的专利申请文件,公开了用于铜钼膜层的蚀刻剂与铜钼膜层的蚀刻方法,通过控制螯合剂和无机酸的比例,从而能获得较小的坡度角,且不会出现金属残留现象,但是其条宽损失较多,且对铜离子的吸附较低。
4.申请公布号为cn113355673a的专利申请文件,公开了一种铜、钛叠层金属蚀刻液及制备方法和实时净化系统,通过过氧化物、氟源和抑制剂共同作用,提高了蚀刻效果的同时,抑制了裂缝的产生,但是原料中加入了一定量的氟离子,氟离子不仅可能与基板发生反应,且对环境不友好,不仅影响了操作人员的身体健康,还增加了废水处理成本。
5.铜和钼的天然化学属性导致了钼和铜两种金属存在巨大的蚀刻速率差异。二者相互叠加后,蚀刻前期,铜蚀刻速率大于钼蚀刻速率,这就导致线宽损失较大时,基板表面仍存在钼残留;蚀刻后期(特别是s/d线二次蚀刻),由于电化学效应,钼层不断向铜层转移电子,导致钼层的蚀刻速率大于铜层,由此产生倒角,导致当站线路存在断路风险,而且会引发后续膜层爬坡断线,影响良率。无钼残与产生倒角的蚀刻时间称为生产窗口。上述原因导致了铜钼叠层结构的蚀刻液的生产窗口极窄。而铜钼层间容易因电化学反应产生裂缝,导致金属线存在尖端放电现象,引发不同导线存在静电击穿现象。
技术实现要素:6.为了解决上述问题,本发明第一方面,提供了一种高铜离子负载的铜金属蚀刻液组合物,包括:主剂和辅剂。
7.优选的,所述主剂,按重量百分比计,其制备原料包括:氧化剂1-20%、第一羧基化合物1-15%、氨基化合物1-15%、第一稳定剂0.01-5%、五元杂环化合物0.01-1%、溶剂补充余量。
8.进一步优选的,所述主剂,按重量百分比计,其制备原料包括:氧化剂8-12%、第一羧基化合物2-10%、氨基化合物2-10%、第一稳定剂0.1-1%、五元杂环化合物0.01-0.1%、溶剂补充余量。
9.优选的,所述氧化剂为无机过氧化物、次氯酸盐、氯酸盐、重铬酸盐、高锰酸盐、高氯酸盐、硝酸盐中的一种或多种;进一步优选的,为无机过氧化物。
10.优选的,所述无机过氧化物为过氧化钠、乙氧烷、过氧化镁、过氧化钙中的一种或多种;进一步优选的,为乙氧烷。
11.优选的,所述第一羧基化合物含有至少两个羧基。
12.优选的,所述第一羧基化合物为草酸、癸二酸、漆树酸、胡萝卜酸、1,2-乙烷二甲酸、壬二酸、苹果酸、柠檬酸、二羧甲基胺中的一种或多种;进一步优选的,为胡萝卜酸和苹果酸或/和1,2-乙烷二甲酸或/和二羧甲基胺。
13.优选的,按重量比计,所述胡萝卜酸:苹果酸或/和1,2-乙烷二甲酸或/和二羧甲基胺为(1-5):1;进一步优选的,为(1-3):1。
14.申请人意外发现,选用重量比为(1-4):1的胡萝卜酸和苹果酸或/和1,2-乙烷二甲酸或/和二羧甲基胺共同作为羧基化合物,不仅能够促进氧化剂对基底的刻蚀,还能够提高体系的稳定性。这可能是由于一方面羧基化合物的加入提供了酸性环境,方便了氧化剂与金属铜和钼发生反应而实现刻蚀,另一方面,羧基化合物中含有多个羧基,能够与铜离子形成相应的配合产物,避免了因铜离子量过多而加速乙氧烷分解,乙氧烷分解过快不仅影响了刻蚀体系的稳定性,还会导致蚀刻不均匀,影响蚀刻形貌,容易出现倒角、条宽损失过大、坡度角过大或者过小等现象。但是在酸性条件下,羧基化合物与铜离子生成的配合产物在蚀刻液中的溶解性不佳,容易在表面形成残留,影响产品质量。
15.优选的,所述氨基化合物为二乙氨基丙胺、丙二胺、三乙醇胺、二乙醇胺、异丙醇胺、2-氨基-2-甲基-丙醇、二甲基乙醇胺;进一步优选的,为三乙醇胺和2-氨基-2-甲基-丙醇。
16.优选的,所述三乙醇胺和2-氨基-2-甲基-丙醇的重量比为(1-10):1。
17.申请人发现,选用重量比为(1-10):1的三乙醇胺和2-氨基-2-甲基-丙醇作为氨基化合物,不仅能够缓解蚀刻后表面金属残留的现象,还能进一步维持蚀刻体系的稳定性。这可能是由于一方面,氨基化合物中的羟基不仅能够与羧基化合物共同调节体系的酸碱度,电负性较强的氮原子还能够猝灭乙氧烷分解产生的羟基自由基,从而减缓了乙氧烷的分解速率,从而进一步维持了蚀刻体系的稳定性。
18.优选的,所述第一稳定剂为2-羟基膦酰基乙酸、羟基乙叉二膦酸、苯基碳酰二铵、有硅酸钠、乙二胺四醋酸钠盐、焦磷酸钠、对羟基苯磺酸、膦酸丁胺-1,2,4三羧酸中的一种或多种;进一步优选的,为苯基碳酰二铵。
19.优选的,所述五元杂环化合物的环中至少含有两个杂原子。
20.优选的,所述杂原子中至少一个是氮原子。
21.优选的,所述五元杂环化合物为1,2,4-三唑、3-巯基-1,2,4-三氮唑、杀草强、3-甲基-1h-1,2,4-噻唑、5-氨基四氮唑中的一种或多种;进一步优选的,为杀草强和5-氨基四氮唑。
22.在一些优选的方案中,选用重量比为(1-6):(0-1)的杀草强和5-氨基四氮唑作为五元杂环化合物应用于蚀刻液中,能够与表面的金属原子结合形成阻断膜,阻断刻蚀液接触膜层结构,保护了局部结构,防止刻蚀的深入,而由于铜钼等金属原子之间存在性质差异,对其的保护也存在差异,从而使得刻蚀后形貌既具有较低的cd-loss,还具有合适的坡度角。
23.优选的,所述杀草强和5-氨基四氮唑的重量比为(1-6):(0-1)。
24.优选的,所述溶剂为去离子水。
25.优选的,所述辅剂,按重量百分比计,其制备原料包括:第二羧基化合物30-60%、
第二稳定剂0.01-5%、五元杂环化合物0.01-1%、溶剂补充余量。
26.进一步优选的,所述辅剂,按重量百分比计,其制备原料包括:第二羧基化合物40-55%、第二稳定剂0.01-1%、五元杂环化合物0.05-0.5%、溶剂补充余量。
27.优选的,所述第二羧基化合物为葡萄糖酸、氨基甲酸、氨基乙酸、乙二酸、胡萝卜酸、1,2-乙烷二甲酸、苹果酸、柠檬酸、二羧甲基胺、三乙酸胺、酒石酸中的一种或多种;进一步优选的,为胡萝卜酸和苹果酸或/和1,2-乙烷二甲酸或/和二羧甲基胺。
28.优选的,按重量比计,所述胡萝卜酸:苹果酸或/和1,2-乙烷二甲酸或/和二羧甲基胺为(1-5):1;进一步优选的,为(1-2):1。
29.优选的,所述第二稳定剂为2-羟基膦酰基乙酸、羟基乙叉二膦酸、苯基碳酰二铵、有硅酸钠、乙二胺四醋酸钠盐、焦磷酸钠、对羟基苯磺酸、膦酸丁胺-1,2,4三羧酸中的一种或多种;进一步优选的,为苯基碳酰二铵和对羟基苯磺酸。
30.优选的,所述苯基碳酰二铵和对羟基苯磺酸的重量比为(5-8):(0-2)
31.优选的,所述高铜离子负载的铜金属蚀刻液组合物,其制备方法包括如下步骤:将主剂原料和辅剂原料按重量比分别在20-45℃之间混合搅拌30-60min,分别得到主剂和辅剂;
32.优选的,所述高铜离子负载的铜金属蚀刻液组合物,使用时使用主剂进行刻蚀,随着蚀刻的进行,铜离子每升高100ppm,向体系中补加0.1%-0.15%主剂重量的辅剂。
33.申请人意外发现,当铜离子每升高100ppm,向体系中补加0.1%-0.15%主剂重量的辅剂,能够延长高铜离子负载的铜金属蚀刻液组合物的寿命。这可能是由于当铜离子浓度升高时,加入一定量的辅剂一方面可以补充蚀刻过程所需要的羧基化合物,另一方面能够降低体系中铜离子的浓度,起到一定的稀释作用,从而增加了蚀刻液组合物的寿命,在高浓度的铜离子体系中也可以继续进行蚀刻。
34.本发明第二方面提供了一种高铜离子负载的铜金属蚀刻液组合物的应用,将如上所述的高铜离子负载的铜金属蚀刻液组合物对导电金属薄膜进行蚀刻。
35.优选的,所述蚀刻时间为100-120s,蚀刻温度为30-34℃。
36.优选的,所述导电金属薄膜由上、下两层金属膜构成;所述下层金属膜紧贴基底。
37.优选的,所述上层金属膜选自铜及其合金、铝及其合金中的一种或多种。
38.优选的,所述下层金属膜选自钼及其合金、钛及其合金中的一种或多种。
39.优选的,所述上层金属膜的厚度为
40.优选的,所述下层金属膜的厚度为
41.有益效果:
42.1、通过选用重量比为(1-4):1的胡萝卜酸和苹果酸或/和1,2-乙烷二甲酸或/和二羧甲基胺共同作为羧基化合物,不仅能够促进氧化剂对基底的刻蚀,还能够提高体系的稳定性。
43.2、通过选用重量比为(1-10):1的三乙醇胺和2-氨基-2-甲基-丙醇作为氨基化合物,不仅能够缓解蚀刻后表面金属残留的现象,还能进一步维持蚀刻体系的稳定性。
44.3、通过选用杀草强作为五元杂环化合物应用于蚀刻液中,能够与表面的金属原子结合形成阻断膜,阻断刻蚀液接触膜层结构,保护了局部结构,防止刻蚀的深入,而由于铜钼等金属原子之间存在性质差异,对其的保护也存在差异,从而使得刻蚀后形貌既具有较
低的cd-loss(线宽损失),还具有合适的坡度角。
45.4、铜离子每升高100ppm,向体系中补加0.1%-0.15%主剂重量的辅剂,能够延长高铜离子负载的铜金属蚀刻液组合物的寿命。
46.5、本技术所制备的高铜离子负载的铜金属蚀刻液组合物无氟无磷,环境友好,废液处理成本低,采用固定比例范围的第一羧基化合物和氨基化合物搭配使用,完美解决了金属界面处的倒角和裂缝问题,蚀刻出来的金属层具有良好的蚀刻形貌,且铜离子负载能力可达15000ppm,蚀刻寿命内线宽损失和坡度角变异量小,蚀刻特性稳定性优异。
附图说明
47.图1为本发明实施例1的蚀刻液在铜离子浓度为0ppm时蚀刻断面的sem图;
48.图2为本发明实施例1的蚀刻液在铜离子浓度为5000ppm时蚀刻断面的sem图;
49.图3为本发明实施例1的蚀刻液在铜离子浓度为10000ppm时蚀刻断面的sem图;
50.图4为本发明实施例1的蚀刻液在铜离子浓度为15000ppm时蚀刻断面的sem图;
51.图5为本发明实施例2的蚀刻液在铜离子浓度为0ppm时蚀刻断面的sem图;
52.图6为本发明实施例2的蚀刻液在铜离子浓度为5000ppm时蚀刻断面的sem图;
53.图7为本发明实施例2的蚀刻液在铜离子浓度为10000ppm时蚀刻断面的sem图;
54.图8为本发明实施例2的蚀刻液在铜离子浓度为15000ppm时蚀刻断面的sem图;
55.图9为本发明实施例3的蚀刻液在铜离子浓度为0ppm时蚀刻断面的sem图;
56.图10为本发明实施例3的蚀刻液在铜离子浓度为5000ppm时蚀刻断面的sem图;
57.图11为本发明实施例3的蚀刻液在铜离子浓度为10000ppm时蚀刻断面的sem图;
58.图12为本发明实施例3的蚀刻液在铜离子浓度为15000ppm时蚀刻断面的sem图;
59.图13为本发明对比例1的蚀刻液在铜离子浓度为0ppm时蚀刻断面的sem图;
60.图14为本发明对比例1的蚀刻液在铜离子浓度为5000ppm时蚀刻断面的sem图;
61.图15为本发明对比例1的蚀刻液在铜离子浓度为10000ppm时蚀刻断面的sem图;
62.图16为本发明对比例1的蚀刻液在铜离子浓度为15000ppm时蚀刻断面的sem图;
63.图17为本发明对比例2的蚀刻液在铜离子浓度为0ppm时蚀刻断面的sem图;
64.图18为本发明对比例2的蚀刻液在铜离子浓度为5000ppm时蚀刻断面的sem图;
65.图19为本发明对比例2的蚀刻液在铜离子浓度为10000ppm时蚀刻断面的sem图;
66.图20为本发明对比例2的蚀刻液在铜离子浓度为15000ppm时蚀刻断面的sem图;
67.图21为本发明对比例3的蚀刻液在铜离子浓度为0ppm时蚀刻断面的sem图;
68.图22为本发明对比例3的蚀刻液在铜离子浓度为5000ppm时蚀刻断面的sem图;
69.图23为本发明对比例3的蚀刻液在铜离子浓度为10000ppm时蚀刻断面的sem图;
70.图24为本发明对比例3的蚀刻液在铜离子浓度为15000ppm时蚀刻断面的sem图。
具体实施方式
71.实施例
72.本发明的实施例1-3和对比例1-3分别提供了一种高铜离子负载的铜金属蚀刻液组合物,其具体成份见表1,其中单位为重量份。
73.表1具体成分表
[0074][0075]
分别使用实施例1-3和对比例1-3所述的成分原料,按重量比分别在35℃之间混合搅拌40min,分别得到主剂和辅剂。
[0076]
将其分别对导电金属薄膜进行蚀刻,蚀刻条件和结果见表2。其中,cd-loss(线宽损失)和坡度角由扫描电子显微镜观察蚀刻断面所得。最高铜负载指的是在保证正常的蚀刻条件下,蚀刻液中所能承载的铜离子最高浓度。
[0077]
图1-24分别为实施例1-3和对比例1-3的蚀刻液在铜离子浓度为0ppm、5000ppm、10000ppm、15000ppm时蚀刻断面的sem图,从图中可以看出,使用实施例1-3得到的蚀刻液蚀刻层无金属残留、无倒角、无裂缝。使用对比例1-3得到的蚀刻液蚀刻层无金属残留、无裂缝,但是有倒角。
[0078]
表2蚀刻条件和蚀刻效果
[0079]