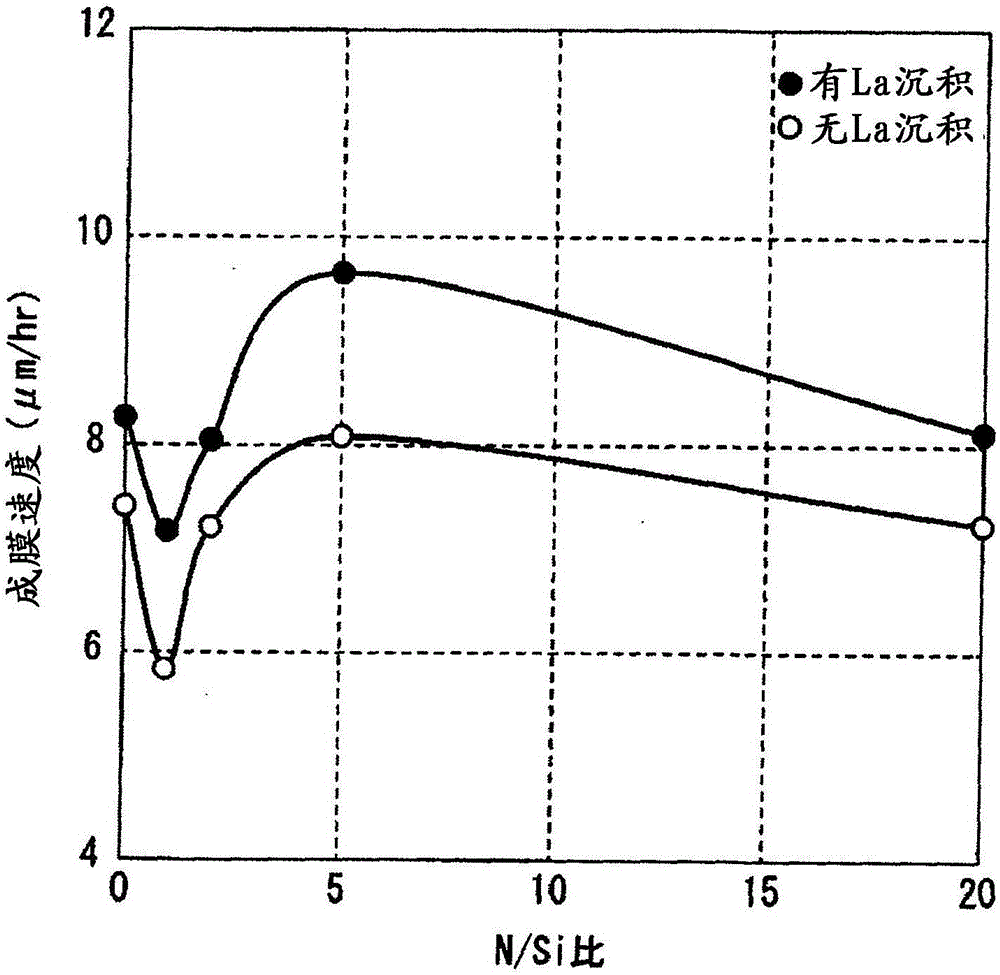
本发明涉及在SiC基板上制造SiC晶体的方法。本发明特别涉及N掺杂的SiC晶体的制造方法。
背景技术:
:为了在SiC基板上形成SiC晶体,通常应用CVD法。在CVD法中,一边向反应室内供给原料气体,一边加热SiC基板及支持该SiC基板的基座,在气相中引起化学反应,从而使SiC晶体气相生长。作为将特定的元素掺杂在SiC晶体中的方法,大致有2种方法。第1种方法为如下方法:作为在CVD法中使用的原料气体所包含的元素,除了Si和C以外,还加入特定的元素作为掺杂剂元素,使掺杂了特定元素的SiC晶体气相生长。第2种方法为如下方法:在CVD法中使用的原料气体中不加入特定的元素作为掺杂剂元素,首先,通过CVD法使未掺杂特定元素的SiC晶体气相生长;然后,使用离子注入法将特定的元素掺杂在该SiC晶体中。作为使用CVD法使以特定元素掺杂的SiC晶体气相生长的方法,例如,在专利文献1中,公开了如下方法:使用除了Si和C以外还包含N作为掺杂剂元素的原料气体,在SiC基板上使N掺杂的SiC晶体气相生长。另外,作为原料气体,公开了Si系气体、C系气体与N2气体的混合气体。此外,作为Si系气体,公开了甲硅烷气体和二氯硅烷气体,作为C系气体,公开了丙烷气体和甲烷气体。在专利文献1所公开的方法中,使以较低浓度的N掺杂的SiC晶体气相生长。具体而言,N施主浓度为2.0×1015原子/cm3以上且小于5.0×1016原子/cm3。现有技术文献专利文献专利文献1:特开2013-211500号公报技术实现要素:发明所要解决的课题在专利文献1所公开的方法中,难以将N掺杂在SiC晶体中。因此,为了将N施主浓度提高至1×1017原子/cm3~9×1017原子/cm3,需要使原料气体中的N2气体量为Si系气体和C系气体的合计量的20倍左右。另外,在专利文献1所公开的方法中,难以仅对SiC晶体的一部分区域提高N施主浓度。另一方面,在仅对SiC晶体的一部分区域提高N施主浓度的情况下,通过离子注入法进行N的掺杂。即,仅在一部分区域中进行N的离子注入。但是,由于离子注入是将高能离子从晶体外部向晶体中注入的方法,因此,易于对SiC晶体的结构带来损伤。即,易于产生层叠缺陷、基底面位错的扩张、BPD半环(halfloop)和点缺陷。其结果,用作元件时的性能易于下降。为了防止该性能下降,通常进行使晶体结构恢复的热处理。但是,由于该热处理,会导致SiC晶体的品质下降,工时也增加。本发明的目的在于,提供一种可有效将N掺杂的SiC晶体的制造方法。另外,本发明的目的在于,提供一种可以仅对SiC晶体的一部分区域提高N施主浓度而不对SiC晶体的结构带来损伤的SiC晶体的制造方法。用于解决课题的手段本发明人进行了专心研究,结果想到本发明。本发明的主旨如下所述。〈1〉SiC晶体的制造方法,其为供给含Si、C及N的原料气体 从而使N掺杂的SiC晶体在SiC基板上气相生长的SiC晶体的制造方法,其中,所述SiC基板为在表面沉积有La、Ce或Ti的SiC基板,或者为离子注入有La、Ce或Ti的SiC基板。〈2〉〈1〉项中记载的方法,其中,仅在所述SiC基板的表面的一部分沉积有La、Ce或Ti,或者离子注入有La、Ce或Ti。〈3〉〈1〉或〈2〉项中记载的方法,其中,通过蒸镀法、溅射法或CVD法沉积所述La、Ce或Ti。〈4〉〈1〉~〈3〉任一项中记载的方法,还包括:在所述气相生长后,除去所沉积的La、Ce或Ti。〈5〉〈1〉或〈2〉项中记载的方法,还包括:在所述离子注入后、所述原料气体的供给前,对离子注入的所述SiC基板进行退火处理。〈6〉〈1〉~〈5〉任一项中记载的方法,还包括:在所述气相生长的过程中,在所述SiC晶体的表面沉积La、Ce或Ti,或者离子注入La、Ce或Ti。发明效果根据本发明,可提供一种能够有效将N掺杂的SiC晶体的制造方法。此外,根据本发明,可提供一种能够仅对SiC晶体的一部分区域提高N施主浓度而不对SiC晶体的结构带来损伤的SiC晶体的制造方法。附图说明图1是示出原料气体的N2浓度与Nd’/Nd(由一定量的La的沉积带来的N施主浓度的提高率)的关系的图。图2是比较了有无La的沉积时,原料气体的N/Si比与N掺杂的SiC晶体的成膜速度的关系的图。图3是示出本发明的实施方式中,仅在SiC基板的表面的一部分沉积了La的实施方式的一例的图。图4是示出整理了有无La的沉积时,原料气体的N2气体浓度与N施主浓度的关系的结果的图。图5是示出SiC基板表面的La浓度与N施主浓度(在一定量的N2气体供给下)的关系的图。图6是示出SiC基板表面的La浓度与Nd’/Nd(由La的沉积带来的N施主浓度的提高率)的关系的图。图7是示出整理了有无Ce的离子注入时,原料气体的N2气体浓度与N施主浓度的关系的结果的图。图8是示出原料气体的N2浓度与Nd’/Nd(由Ce的离子注入带来的N施主浓度的提高率)的关系的图。图9是示出SiC基板表面的Ce浓度与Nd’/Nd(由Ce的沉积带来的N施主浓度的提高率)的关系的图。图10是示出在SiC基板中离子注入了Ce时的Ce浓度的深度方向的分布的图。图11是示出整理了有无Ce离子注入时,原料气体的N/Si比与N施主浓度的关系的结果的图。图12是整理了有无Ce离子注入时,原料气体的N/Si比与N掺杂的SiC晶体的生长速度的关系的图。附图标记说明10SiC基板20La沉积区域30N掺杂了的SiC晶体30a高氮浓度部30b低氮浓度部40绝缘膜50a源电极50b漏电极50c栅电极60水平式MESFET晶体管具体实施方式以下,对根据本发明的SiC晶体的制造方法的实施方式进行详细说明。予以说明,以下示出的实施方式不限定本发明。根据本发明的SiC晶体的制造方法供给含Si、C及N的原料气体,从而使N掺杂的SiC晶体在SiC基板上气相生长。此时,可使用通常的CVD装置。含Si、C及N的原料气体可以与通常的CVD法同样。例如,可使用含Si气体、含C气体与含N气体的混合气体。作为含Si气体,例如可举出SiCH3H3(单甲基硅烷)气体、SiH4(硅烷)气体或SiH2Cl2(二氯硅烷)等,也可以将它们组合。作为含C气体,可举出CH4(甲烷)气体、乙烷(C2H6)气体或C3H8(丙烷)气体,也可以将它们组合。作为含N气体,可举出N2气体或NH3气体等,也可以将它们组合。可将含Si、C及N的原料气体与载气一起向CVD装置的反应室供给。作为载气,有H2气体或Ar气体等,也可以将它们组合。予以说明,在使用载气的情况下,各气体的浓度(体积%)以含Si、C及N的原料气体与载气的合计作为整体。例如,在将SiCH3H3气体、CH4气体及N2气体的混合气体作为原料气体并使用载气的情形时的N2气体浓度(体积%)为:[(N2气体的体积)/{(SiCH3H3气体的体积)+(CH4气体的体积)+(N2气体的体积)+(载气的体积)}]×100。在使用常规的SiC基板、即表面未沉积有La的SiC基板的情况下,掺杂了N的SiC晶体从SiC基板的表面不断地气相生长。但是,由于Si、C和N之间的化学反应性,N的掺杂效率低。在本发明中,使用表面沉积有La、Ce或Ti的SiC基板,或者离子注入有La、Ce或Ti的SiC基板。以下的说明以La为中心进行说明,但关于Ce或Ti也同样。关于其原因,在后描述。(使用表面沉积有La的SiC基板的情形)首先,对使用表面沉积有La的SiC基板的情形进行说明。得到 沉积了La的SiC基板的方法不特别限定。例如可举出通过蒸镀法、溅射法或CVD法将La沉积于SiC基板的表面的方法。在通过任一方法将La沉积的情况下,在其沉积后,也可以在H2气氛下进行热处理,洗净La层的表面。温度和时间适当地确定即可,但温度优选为1550~1750℃,时间优选为10~60分钟。如果为1550℃以上,则H2气体活化,洗净效果提高。更优选为1575℃以上、1600℃以上或1625℃以上。另一方面,如果为1750℃以下,不会出现由SiC的蚀刻效应的增大引起的生长速度下降的问题。更优选为1725℃以下、1700℃以下或1675℃以下。在向表面沉积有La的SiC基板供给含Si、C及N的原料气体时,该气体在沉积于SiC基板表面的各个La之间通过。然后,N掺杂的SiC晶体以进入SiC基板与La之间的方式进行气相生长。此时,La存在于N掺杂的SiC晶体的表面。这样,N掺杂的SiC晶体不断地进行气相生长。根据WebElementsPeriodicTable(http://www.webelements.com/),Si的共价键半径为116pm,另外,C的共价键半径为75pm,与此相对,La的共价键半径为180pm。即,La的共价键半径大于Si和C中的任一者的共价键半径。因此,与以置换型或侵入型的方式在Si与C的晶格内存在相比,La在Si与C的晶格外存在更稳定。由此,掺杂了N的SiC晶体在SiC基板与La之间持续气相生长。而且,由于在Si、C及N之间,化学反应性因La而提高,因此N的掺杂效率高。在此,将使用表面未沉积有La的SiC基板时的N施主浓度设为Nd、将使用表面沉积有La的SiC基板时的N施主浓度设为Nd’而考虑Nd’/Nd。予以说明,由于未掺杂N而气相生长的SiC晶体的载流子浓度为1014原子/cm3级,因此当在1015~1018原子/cm3的范围内进行控制的情况下,N施主浓度等于n型载流子浓度。如果含Si、C和N的原料气体中的N的浓度增加,则N施主浓 度也增加。因此,只要考虑Nd’/Nd,就可纯粹地评价由使用表面沉积有La的SiC基板带来的N施主浓度的提高效果,而不受到含Si、C及N的原料气体中的N的浓度增加的影响。即,Nd’/Nd意味着由La的沉积带来的N施主浓度的提高率。图1是示出在沉积了一定量(一定厚度0.5nm)的La的条件下,含Si、C及N的原料气体的N2浓度(在图1中,为了便于书写,简单称作“原料气体的N2浓度”)与Nd’/Nd的关系的一例的图。由图1可知,Nd’/Nd的值大致一定,与含Si、C及N的原料气体的N2浓度无关。因此可认为,通过使用表面沉积有La的SiC基板,N的掺杂效率提高。这意味着通过La的沉积,Si、C和N之间的化学反应性提高。从N掺杂的SiC晶体的成膜速度的观点来说明该化学反应性的提高。图2是示出比较了在使用表面沉积有La的SiC基板时与使用表面未沉积有La的SiC基板时,含Si原料气体与含N原料气体的浓度比N/Si比与N掺杂的SiC晶体的成膜速度的关系的一例的图。予以说明,在图2中,为了便于书写,将含Si、C及N的原料气体的N/Si比简单称作“N/Si比”,将N掺杂的SiC晶体的成膜速度简单地称作“成膜速度”,将“使用表面沉积有La的SiC基板时”称作“有La沉积”,将“使用表面未沉积有La的SiC基板时”称作“无La沉积”。由图2可知,在使用表面沉积有La的SiC的基板时,SiC晶体的成膜速度提高。因此可认为,通过La的沉积,Si、C和N之间的化学反应性提高。如目前为止已说明的那样,在使用表面沉积有La的SiC基板时,得到了N掺杂的SiC晶体中的N的掺杂效率和成膜速度提高的作用效果。接着,对该作用效果与La的沉积量的关联进行说明。关于La的沉积量,优选每单位面积沉积有1×1012原子/cm2以上的La。如果为1×1012原子/cm2以上,则各个La彼此的间隔不过度分开,因此可在沉积了La的区域内均匀地得到上述作用效果。更优选 为5×1012原子/cm2以上或1×1013原子/cm2以上。另一方面,优选每单位面积沉积有1×1016原子/cm2以下的La。如果为1×1016原子/cm2以下,则上述作用效果不饱和。更优选为5×1015原子/cm2以下或1×1015原子/cm2以下。予以说明,将1×1012~1×1016原子/cm2换算成La的沉积厚度时,为3×10-4~3.7nm。而且,相对于表面露出的Si原子和C原子的总数1000个,1×1012原子/cm2相当于沉积有1个La。另外,用进行X射线光电子分光分析(XPS:X-RayPhotoelectronSpectroscopyanalysis)时的测定值表示沉积的La时,相当于0.01~100原子%。作为参考,关于含Si、C及N的原料气体的N浓度,以N2气体为例进行附带说明。如图1所示,Nd’/Nd为大致一定,与含Si、C及N的原料气体的N2气体浓度无关。这表示N掺杂效率为大致一定,与原料气体的N2气体浓度无关。根据本发明,由于可通过少的N2气体的供给量而得到大于以往的N施主浓度,因此不需要供给过度的N2气体。(使用离子注入有La的SiC基板的情形)接着,对使用离子注入有La的SiC基板的情形进行说明。由于La的原子量大,因此相对于加速电压,射程变小。因此,即使加速电压为170keV,射程也停留在55nm左右。如果La的离子注入深度为距SiC基板的表面100nm以下,则可得到La在SiC基板的表面附近沉积、即,与La在SiC基板的表面存在相同的作用效果。为了使N掺杂的SiC晶体气相生长,对离子注入有La的SiC基板进行加热。如果La的离子注入深度为距SiC基板的表面100nm以下,则可认为通过该加热,被离子注入的La的至少一部分被退火,从而偏在于SiC基板的表面。如上所述,由于La的原子量大,因此,即使加速电压为170keV,射程也停留在55nm左右。因此,不易将La离子注入距SiC基板的表面较深的位置,同时,La的共价键半径大于Si及C中的任一者的共价键半径,因此通过退火处理,La易于偏在于SiC基板表面。退火处理的条件适当确定即可,但温度优选为1550~1750℃,时间优选为10~60分钟。如果为1550℃以上,则可较容易地使较多的La偏在(segregated)于SiC基板表面。另一方面,如果为1750℃以下,则可抑制由蒸发引起的表面La浓度的下降。予以说明,由于通过使SiC晶体气相生长时的升温,可得到与退火同样的效果,因此也可以不另外实施退火。另一方面,由于La的蒸气压较低,因此即使在蒸发易于进行的低压(1.33kPa(10托))的H2气流气氛下进行退火持续3小时,也不会导致La全部蒸发。如目前为止已说明的那样,La的离子注入深度为距SiC基板的表面100nm以下即可。从该观点考虑,关于离子注入时的加速电压,优选为15~170keV。如果为15keV以上,则可将La离子有效注入SiC基板。另一方面,如果为170keV以下,则离子的射程不超过100nm。另外,将La离子注入SiC基板时使用的装置不特别限定。例如可使用高电流离子注入装置、中电流离子注入装置或高能离子注入装置。(气相生长过程中的La的沉积或离子注入)在N掺杂的SiC晶体的气相生长的过程中(中途),也可以在该SiC晶体的表面再沉积或离子注入La。若这样操作的话,可使在再沉积或离子注入La之后所气相生长的SiC晶体的N施主浓度与在再沉积或离子注入La之前所气相生长的SiC晶体的N施主浓度为不同浓度。予以说明,在N掺杂的SiC晶体的气相生长的过程中,再沉积或离子注入了的La当然也存在于在该沉积或离子注入后所气相生长的SiC晶体的表面。当在N掺杂的SiC晶体的气相生长进行中再使La进一步沉积的情况下,可以中断含Si、C及N的原料气体的供给而沉积La,也可以一边使N掺杂的SiC晶体气相生长、一边使La沉积。作为一边使N掺杂的SiC晶体气相生长、一边使La沉积的方法,在供给含Si、C及N的原料气体的过程中,替代为含Si、C、N及La的原料气体来 继续进行气相生长。(沉积了的La的除去)在使N掺杂的SiC晶体气相生长后,在该SiC晶体的表面残留有所沉积的La。在将SiC晶体安装于电极等以形成元件时,通过去除该所沉积的La,可充分发挥N掺杂的SiC晶体具有的原本特性。除去的方法不特别限定,但优选不使N掺杂的SiC晶体变质的方法。例如,为CMP研磨、抛光和蚀刻。另外,更优选在除去后易于确保N掺杂的SiC晶体的平坦度的方法。例如,为CMP研磨或抛光。(仅表面的一部分沉积有La的SiC基板)在仅SiC基板的表面的一部分沉积有La时,关于N掺杂的SiC晶体,可使La的沉积区域的N施主浓度高于其它部分的N施主浓度。图3是示出本发明的实施方式中,使N掺杂的SiC晶体在仅表面的一部分沉积有La的SiC基板上气相生长的一例的图。图3(a)是示出仅表面的一部分沉积有La的SiC基板的截面的示意图。图3(b)是示出使N掺杂的SiC晶体在图3(a)的SiC基板上气相生长后的截面的示意图。图3(c)是示出将存在于N掺杂的SiC晶体的表面的La除去之后的截面的示意图。图3(d)是示出将N掺杂的SiC晶体的表面平坦化之后的截面的示意图。图3(e)是示出在图3(d)的SiC基板上安装绝缘膜和各电极并形成水平式MESFET晶体管之后的截面的示意图。如图3(a)所示,仅SiC基板10的表面的一部分形成有La沉积区域20。沉积方法可以为目前为止说明的任一方法。将如图3(a)所示的SiC基板装入反应室(未图示),向反应室供给含Si、C及N的原料气体。由此,如图3(b)所示,对于La沉积区域20和La沉积区域20以外的区域的两者,使N掺杂的SiC晶体30气相生长。La沉积区域20存在于N掺杂的SiC晶体30的与SiC基板10相反的一侧的表面。即,在SiC基板10和La沉积区域20夹持的部分,使N掺杂的SiC晶体30气相生长。由此,在N掺杂的SiC晶体30中,在SiC基板10和La沉积区 域20之间所夹持的部分作为高氮浓度部30a而成膜。另一方面,SiC基板10和La沉积区域20之间所夹持的部分以外的区域作为低氮浓度部30b而成膜。另外,由于La沉积区域20的作用,高氮浓度部30a的成膜速度高于低氮浓度部30b的成膜速度。其结果,与低氮浓度部30b相比,将高氮浓度部30a较厚地成膜。如图3(c)所示,也可以在使N掺杂的SiC晶体30气相生长之后,除去La沉积区域20。除去的原因和方法与目前为止的说明同样。由于与低氮浓度部30b相比,高氮浓度部30a较厚地成膜,因此出于元件设计的方便,如图3(d)所示,也可以通过研磨等将高氮浓度部30a与低氮浓度部30b平坦化。在元件的制作时,为了得到所期望的特性,例如如图3(e)所示,可安装绝缘膜和各电极。例如,首先,在将N掺杂的SiC晶体30平坦化了的面上形成绝缘膜40。绝缘膜40的形成方法可以为常规方法。另外,绝缘膜40只要可确保绝缘性就不限定材质,例如为SiO2。其后,除去绝缘膜40中被覆高氮浓度部30a的部分,使SiC晶体30露出。除去方法可以为常规方法,例如为湿式蚀刻或干式蚀刻。然后,在SiC晶体30的露出部形成源电极50a和漏电极50b。形成方法不特别限定,但例如有电子束蒸镀法。也可以将所形成的源电极50a和漏电极50b在1000℃左右的氩气气氛下加热10分钟左右,形成欧姆电极。接着,在绝缘部40中的被覆低氮浓度部30b的部分的一部分上形成栅电极50c。形成方法不特别限定,但可通过电子束蒸镀来形成Ti、Pt或Au。由此制作的图3(e)的水平式MESFET晶体管60为元件的一例,可适当改变高氮浓度部30a与低氮浓度部30b的数量和位置关系来制作不同类型的元件。例如,为MOSFET晶体管、垂直式和水平式的元件,以及二极管。在这些元件中,在仅将想得到欧姆特性的部分作为La沉积区域 20而将高氮浓度部30a成膜时,可得到能够显著降低接触电阻的元件。(仅表面的一部分离子注入有La的SiC基板)可将La离子注入相当于图3中的La沉积区域20的部分来形成离子注入部(未图示)。然后,通过退火或CVD时的加热,离子注入部(未图示)的La偏在于SiC基板10的表面,形成了La偏在的区域(未图示)。La偏在的区域(未图示)形成时的截面与仅SiC基板10的表面的一部分沉积了La沉积区域20的状态相同(参照图3(a))。其后,与使用仅表面的一部分沉积有La的SiC基板的情形同样。(表面沉积有Ce或Ti的SiC基板或离子注入有Ce或Ti的SiC基板)目前为止,对使用表面沉积有La的SiC基板或离子注入有La的SiC基板的情形进行了说明。根据WebElementsPeriodicTable(http://www.webelements.com/),Si、C、La、Ce和Ti的共价键半径分别为116pm、75pm、180pm、163pm和136pm。因此,虽然Ce和Ti的共价键半径小于La的共价键半径,但Ce和Ti的共价键半径都大于Si和C的共价键半径。另外,由于Ce及Ti的蒸气压与La同等,因此可将用于使SiC晶体气相生长的CVD条件、特别是关于温度设为与La同等。即,可在La、Ce和Ti不熔融或不蒸发的温度下进行CVD。因此,与La同样,对于N掺杂的SiC晶体,Ce或Ti具有促进N施主浓度和成膜速度的增加的作用效果。因此,表面沉积有La的SiC基板或离子注入有La的SiC基板也可以为表面沉积有Ce或Ti的SiC基板或者离子注入有La、Ce或Ti的SiC基板。目前为止,作为使SiC晶体气相生长的方法,对使用通常的CVD法的实施方式进行了说明,但也可以使用其它气相生长方法。例如,由于La、Ce和Ti的蒸气压低,因此可以使用表面沉积有La、Ce或Ti的SiC基板或离子注入有La、Ce或Ti的SiC基板,通过将气氛压力设为大气压左右、将气氛温度设为2000℃左右的高温CVD法使SiC 晶体气相生长。另外,由于La、Ce和Ti的蒸气压低,可以与上述同样,使用表面沉积有La、Ce或Ti的SiC籽晶(seed)或离子注入有La、Ce或Ti的SiC籽晶,通过升华法使SiC晶体气相生长。即,本发明除了常规CVD法以外也可应用高温CVD法和升华法。而且,SiC晶体可以为外延生长的晶体,也可以为非外延生长的晶体。进而,气相生长的SiC晶体不限于薄膜,可以为厚的层状,也可以为块状那样的结晶体。(实施例1)以下,通过实施例进一步具体说明本发明。予以说明,本发明不受以下实施例中使用的条件所限定。(实施例1a的试样制作)通过蒸镀法在SiC基板的整个表面沉积La。沉积厚度为0.5nm。La的沉积量以每单位面积的原子个数计为1.3×1015原子/cm2。将该沉积了La的SiC基板在1.33kPa(10托)、1650℃的氢气氛下处理30分钟,洗净La的表面。接着,将沉积了La的SiC基板装入反应室。然后,将含Si、C及N的原料气体(以下,简单称作“原料气体”)与作为载气的H2气体一同向反应室供给,制作实施例1a的N掺杂的SiC晶体(以下,简单称作“SiC晶体”)。作为原料气体,将SiCH3H3、CH4气体和N2气体混合后供给。SiCH3H3气体、CH4气体和N2气体的浓度分别为0.055%、0.028%和0.33%。予以说明,将各气体浓度设为相对于SiCH3H3气体、CH4气体、N2气体和H2气体的合计的体积%。(比较例1a的试样制作)除了使用未沉积La的SiC基板以外,在与实施例1a同样的条件下,制作比较例1a的SiC晶体。(试样的评价方法)对于实施例1a和比较例1a的SiC晶体进行二次离子质量分析(SIMS:SecondaryIonMassSpectrometry)。(评价结果)关于N施主浓度,在实施例1a的SiC晶体中,以1.4×1017~3.4×1017原子/cm3的范围分布。另一方面,在比较例1a的SiC晶体中,任一部位均为0.5×1017原子/cm3以下。在实施例1a的SiC晶体中,La的浓度在SiC基板的表面附近为1×1019原子/cm3,在SiC晶体中为二次离子质量分析的测定极限以下(5×1013原子/cm3以下)。另一方面,在比较例1a的SiC晶体中,La的浓度在SiC基板的表面和SiC晶体中均为二次离子质量分析的测定极限以下。由这些结果确认了可通过La的沉积来提高N施主浓度。另外,确认了当在SiC基板的表面沉积了La的情况下,可使SiC晶体在SiC基板和La之间气相生长。(实施例2)(实施例2a~2d的试样制作)通过蒸镀法在SiC基板的整个表面沉积La。沉积厚度为0.5nm。La的沉积量以每单位面积的原子个数计为1.3×1015原子/cm2。将该沉积了La的SiC基板在1.33kPa(10托)、1650℃的氢气氛下处理30分钟,洗净La的表面。接着,将沉积了La的SiC基板装入反应室。然后,将原料气体与作为载气的H2气体一同向反应室供给,制作实施例2a、2b、2c和2d的SiC晶体。作为原料气体,将SiCH3H3气体、CH4气体和N2气体混合后供给。SiCH3H3气体的浓度在实施例2a~2d中均为0.055%。CH4气体的浓度在实施例2a~2d中均为0.028%。关于N2气体的浓度,实施例2a为0.066%,实施例2b为0.13%,实施例2c为0.33%,实施例2d为1.3%。予以说明,将各气体浓度设为相对于SiCH3H3气体、CH4气体、N2气体和H2气体的合计的体积%。(比较例2a~2d的试样制作)除了使用未沉积La的SiC基板以外,在与实施例2a同样的条件下,制作比较例2a的SiC晶体。同样地,相对于实施例2b制作比较 例2b的SiC晶体,相对于实施例2c制作比较例2c的SiC晶体,以及相对于实施例2d制作比较例2d的SiC晶体。(试样的评价方法)关于实施例2a~2d和比较例2a~2d的SiC晶体,利用C-V(容量-电压特性)法来测定N施主浓度。另外,关于实施例2a~2d,在使SiC晶体气相生长后,测定试样表面的La浓度。在测定时,使用アルバック·ファイ社制的X射线光电子分光分析装置Model1600。在测定时,使试样表面的法线方向与检测器的法线方向为45度。(评价结果)将N施主浓度的测定结果示于图4。横轴表示原料气体中加入的N2气体浓度,纵轴表示N施主浓度。黑色圆圈表示实施例2a~2d的测定结果,白色圆圈表示比较例2a~2d的测定结果。由图4可确认:可通过La来提高N施主浓度。但是,在图4中,包括由La引起的N施主浓度的提高以及由提高原料气体的N2气体浓度引起的N施主浓度提高两方面。因此,考虑Nd’/Nd(Nd’为实施例2a~2d的N施主浓度,Nd为比较例2a~2d的N施主浓度),已经说明了如图1那样的概括。由图1可确认,相对于原料气体中加入的N2气体的浓度,可通过La使N施主浓度以一定比例提高。即,确认了可通过La提高将N掺杂至SiC晶体的效率。进而,关于实施例2a~2d,SiC晶体气相生长后的试样表面的La浓度均为0.5原子%。由此可确认沉积于SiC基板的La偏在于SiC晶体的表面。即,确认了可使SiC晶体在SiC基板与La之间气相生长。(实施例3)(实施例3a和3b的制作)在SiC基板的整个表面沉积La。以在对其表面进行X射线光电子分光分析时,以La浓度成为0.1原子%的方式通过DC溅射法(氩气体气氛,室温)形成了La。予以说明,以每单位面积的原子个数计, 0.1原子%相当于9.6×1012原子/cm2。将该沉积了La的SiC基板装入反应室,将原料气体与作为载气的H2气体一同向反应室供给,制作实施例3a的SiC晶体。作为原料气体,将SiCH3H3气体、CH4气体和N2气体混合并供给。SiCH3H3气体、CH4气体和N2气体的浓度分别为0.055%、0.028%和0.33%。予以说明,将各气体浓度设为相对于SiCH3H3气体、CH4气体、N2气体和H2气体的合计的体积%。另外,在沉积La时,以在对其表面进行X射线光电子分光分析时成为0.5原子%的方式沉积La,除此以外,在与实施例3a相同的条件下,制作实施例3b的SiC晶体。予以说明,以每单位面积的原子个数计,0.5原子%相当于4.8×1013原子/cm2。(比较例3a的试样制作)为了将未沉积La时的N施主浓度设为Nd、将沉积了La时的N施主浓度设为Nd’而考虑Nd’/Nd,使用未沉积La的SiC基板,除此以外,在与实施例3a和3b相同的条件下制作比较例3a的SiC晶体。(试样的评价方法)关于实施例3a及3b和比较例3a的SiC晶体,通过C-V(容量-电压特性)法测定N施主浓度,求出Nd’/Nd。(评价结果)将N施主浓度的测定结果示于图5和图6。关于图5,横轴表示SiC基板表面的La浓度,纵轴表示N施主浓度。关于图6,横轴表示SiC基板表面的La浓度,纵轴表示Nd’/Nd。由图5和图6可确认:La浓度增加时,可提高N施主浓度。当使SiC晶体在未沉积La的SiC基板上气相生长时,N施主浓度Nd(0)与N的供给量成比例。将其以式子表示时为如下。Nd(0)=A[N]在此,A为比例常数,[N]为向反应室供给的气体中的N2气体浓度。另一方面,当使SiC晶体在沉积了La的SiC基板上气相生长时, N施主浓度Nd([La])相对于[La]和[N]线性地增加。其中,[La]为SiC基板表面的La浓度(原子%)。将其以式子表示时为如下。Nd([La])=(B[La]+1)Nd(0)在此,B为常数。将[La]=0.1和[La]=0.5代入上式时,为:Nd(0.1)=(B×0.1+1)Nd(0)(a1)Nd(0.5)=(B×0.5+1)Nd(0)(b1)。在此,根据图5,为:Nd(0.1)×3.3=Nd(0.5)(c1)。将(c1)代入(a1)和(b1)时,成为:3.3×(B×0.1+1)Nd(0)=(B×0.5+1)Nd(0),在对B求解时,成为:3.3×(B×0.1+1)=(B×0.5+1),B=13.5。即,得到下式。Nd([La])=(13.5×[La]+1)Nd(0)由此可知,当使1原子%的La沉积在SiC基板的表面上时,可使N施主浓度为以往的14.5倍。(实施例4)(实施例4a~4c的试样制作)在SiC基板的整个表面以Ce的离子注入量成为6.1×1013原子/cm2的方式,使加速电压为15~170keV的范围,多次进行离子注入。通过如此地进行离子注入,可得到在SiC基板的表面附近具有比较均匀的浓度分布的离子注入区域,即盒型分布(boxprofile)。通过这些多次的离子注入,距SiC基板的表面10~70nm范围内的Ce浓度为1×1019原子/cm3。将该离子注入了Ce的SiC基板在1.33kPa(10托)、1650℃的氢气氛下处理30分钟(退火),使Ce层偏在于SiC基板表面。在使不均匀分布后,对Ce偏在的部分的表面进行X射线光电子分光分析,结果Ce浓度为0.6原子%。予以说明,在分析时使用アルバック·フ ァイ社制的X射线光电子分光分析装置Model1600。另外,使试样表面的法线方向与检测器的法线方向为45度来进行测定。接着,将离子注入了Ce的SiC基板装入反应室。然后,将原料气体与作为载气的H2气体一同向反应室供给。作为原料气体,将SiCH3H3气体、CH4气体和N2气体混合后供给。SiCH3H3气体的浓度在实施例4a~4c中均为0.055%。CH4气体的浓度在实施例4a~4c中均为0.028%。关于N2气体的浓度,实施例4a为0.11%,实施例4b为0.28%,实施例4c为1.1%。予以说明,将各气体浓度设为相对于SiCH3H3气体、CH4气体、N2气体和H2气体的合计的体积%。(比较例4a~4c的SiC晶体的制作)除了使用未离子注入Ce的SiC基板以外,在与实施例4a相同的条件下制作比较例4a的SiC晶体。同样地,相对于实施例4b制作比较例4b的SiC晶体,相对于实施例4c制作比较例4c的SiC晶体。(试样的评价方法)对于实施例4a~4c和比较例4a~4c的SiC晶体,通过C-V(容量-电压特性)法测定N施主浓度。另外,关于实施例4a~4c的SiC晶体,在使SiC晶体气相生长后,测定试样表面的Ce浓度。测定方法与在使Ce不均匀分布于表面后进行测定的方法同样。(评价结果)将N施主浓度的测定结果示于图7。横轴表示原料气体中加入的N2气体的浓度,纵轴表示N施主浓度。黑方块表示实施例4a~4c的测定结果,白色圆圈表示比较例4a~4c的测定结果。由图7可确认:通过Ce可提高N施主浓度。但是,在图7中,包括由Ce引起的N施主浓度的提高以及由提高原料气体的N2气体浓度引起的N施主浓度提高两方面。因此,考虑Nd’/Nd(Nd为比较例4a~4c的N施主浓度,Nd’为实施例4a~4c的N施主浓度),与图1同样,在图8中为概括。由图8可确认:相对于原料气体的N2气体浓度,可通过Ce使N 施主浓度以一定的比例提高。即,可确认:通过Ce,可提高将N掺杂至SiC晶体的效率。另外,关于实施例4a~4c,SiC晶体气相生长后的试样表面的Ce浓度均为0.2原子%。由此可确认:在SiC基板中离子注入的Ce偏在于SiC晶体的表面。即,确认了可使SiC晶体在SiC基板和Ce之间气相生长。予以说明,偏在于SiC基板的表面附近的Ce由于使SiC晶体气相生长时的加热而稍许蒸发,在SiC晶体气相生长的前后,Ce从SiC晶体脱落。由此,Ce浓度从0.5原子%减少至0.2原子%。(实施例5)(实施例5a~5c的SiC晶体的制作)在SiC基板的整个表面沉积Ce。以在对其表面进行X射线光电子分光分析时,Ce浓度成为0.2原子%的方式形成了Ce。予以说明,以每单位面积的原子个数计,0.2原子%相当于1.9×1013原子/cm2。接着,将该沉积了Ce的SiC基板装入反应室,将原料气体与作为载气的H2气体一同向反应室供给,制作实施例5a的SiC晶体。作为原料气体,将SiCH3H3气体、CH4气体和N2气体混合后供给。SiCH3H3气体和CH4气体的浓度分别为0.055%和0.028%。予以说明,将各气体浓度设为相对于SiCH3H3气体、CH4气体、N2气体和H2气体的合计的体积%。另外,沉积Ce并以对其表面进行X射线光电子分光分析时成为0.7原子%的方式进行沉积,除此以外,在与实施例5a相同的条件下制作实施例5b的SiC晶体。予以说明,以每单位面积的原子个数计,0.7原子%相当于6.7×1013原子/cm2。进一步地,沉积Ce并以对其表面进行X射线光电子分光分析时成为1.0原子%的方式进行沉积,除此以外,在与实施例5a相同的条件下制作实施例5c的SiC晶体。予以说明,以每单位面积的原子个数计,1.0原子%相当于9.6×1013原子/cm2。(比较例5a的试样制作)为了将未沉积Ce时的N施主浓度设为Nd、将沉积了Ce时的N 施主浓度设为Nd’而考虑Nd’/Nd,使用未沉积Ce的SiC基板,除此以外,在与实施例5a~5c相同的条件下制作比较例5a的SiC晶体。(试样的评价方法)关于实施例5a~5c和比较例5a的SiC晶体,通过C-V(容量-电压特性)法测定N施主浓度,求出Nd’/Nd。(评价结果)将N施主浓度的测定结果示于图9。横轴表示SiC基板表面的Ce浓度,纵轴表示Nd’/Nd。由图9确认了:Ce浓度增加时,可提高N施主浓度。(实施例6)(实施例6a的试样制作)在4H-SiC基板的整个表面离子注入Ce。离子注入的条件如表1所示。表1的条件是以在完全进行这些条件时,在距表面约50nm的深度注入较多Ce的方式确定的。【表1】加速电压(keV)离子注入量(原子/cm2)1703.20×1013901.22×1013500.92×1013250.50×1013150.30×1013图10是示出离子注入后的Ce浓度的深度方向的分布的图。横轴表示距表面的深度,纵轴表示Ce浓度。予以说明,Ce浓度通过二次离子质量分析来测定。由图10可知,可确认在距4H-SiC基板的表面约50nm(0.05μm)的位置存在Ce浓度的峰。使用离子注入了Ce的该SiC基板而不进行退火处理。将图10中示出的4H-SiC基板装入反应室,将8ccm的单甲基硅烷气体、以C/Si比计为2的C3H8气体和N2气体与作为载气的H2气体一同向反应室供给。生长温度为1500℃,反应室内压力为11kPa。 另外,根据试样,通过N/Si比使N2气体量变化。(比较例6a的试样制作)除了使用未离子注入Ce的SiC基板以外,在与实施例6a相同的条件下制作比较例6a的SiC晶体。(试样的评价方法)通过电子束蒸镀法,在实施例6a和比较例6a的SiC晶体上形成厚度100nm的Ni电极,制作肖特基二极管,通过C-V(容量-电压特性)法测定N施主浓度。(评价结果)将N施主浓度的测定结果示于图11。横轴表示N/Si比(氮/硅比),纵轴表示N施主浓度。由图11确认了:即使在通过离子注入形成Ce,其后不进行退火处理而使SiC晶体气相生长的情况下,也可使N施主浓度提高。另外,在使SiC晶体气相生长时,测定了其生长速度。将其结果示于图12。横轴表示N/Si比(氮/硅比),纵轴表示生长速度。由图12确认了通过离子注入Ce,可使SiC晶体的气相生长的速度提高。(实施例7)(实施例7a的试样制作)通过蒸镀法在SiC基板的整个表面沉积Ti。以每单位面积的原子个数计,Ti的沉积量为2×1011原子/cm2。将该沉积了Ti的SiC基板在1.33kPa(10托)、1650℃的氢气氛下处理30分钟,洗净Ti的表面。接着,将沉积了Ti的SiC基板装入反应室。然后,将原料气体与作为载气的H2气体一同向反应室供给,制作实施例7a的SiC晶体。作为原料气体,将SiH4气体和C3H8气体混合后供给。相对于H2气体,以20ccm供给40%的SiH4气体,以100ccm供给N2气体,并在11kPa下以30slm供给H2气体。C3H8气体以C/Si计为0.75。(比较例7a的试样制作)除了使用未沉积Ti的SiC基板以外,在与实施例7a相同的条件 下制作比较例7a的SiC晶体。(试样的评价方法)关于实施例7a和比较例7a的SiC晶体,通过C-V(容量-电压特性)法测定N施主浓度。(评价结果)实施例7a的N施主浓度为2×1017原子/cm3。另一方面,比较例7a的N施主浓度为1×1017原子/cm3。由这些结果确认了:通过Ti层,可提高N施主浓度。由以上结果可确认本发明的效果。产业上的利用可能性根据本发明,易于将N掺杂至SiC晶体,其结果,可与以往相比提高SiC晶体中的N施主浓度。因此,本发明在产业上的利用可能性大。当前第1页1 2 3