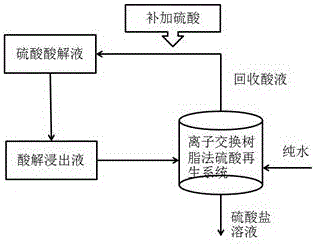
本发明属于化学工程领域,涉及以工业钛渣为原料,经与氢氧化钠混合后还原焙烧、洗涤、浸出、水解、焙烧制备锐钛矿型二氧化钛,以及各原料循环利用、废液处理的方法,具体为一种利用钛渣为原料制备锐钛矿型二氧化钛的方法。
背景技术:
:二氧化钛(钛白粉)作为一种重要的化工原料,不仅广泛应用于油漆、化妆品、造纸、化纤、橡胶等工业领域,还可作为一种重要的光催化催化剂及催化剂载体材料,是选择性还原脱硝(SCR)催化剂载体的最佳选择。二氧化钛的生产主要有两种工艺,硫酸法和氯化法:硫酸法的主要原料是硫酸和钛精矿等,生产出来的产品质量低,品种单一,环境污染严重。国内约95%的钛白粉生产企业采用传统硫酸法生产工艺。氯化法钛白粉生产工艺生产过程环保,产品质量较高,是国际公认的替代硫酸法的新一代先进技术。在欧美发达国家,氯化法的比例则更高,美国早在2006年就关闭了国内最后一家硫酸法钛白粉工厂。国内学术界也主张发展氯化法淘汰硫酸法。但是,氯化法生产钛白粉在国内推广困难重重,对氯化法的争议很大:其一,氯化法的主要原料是高钛渣和氯气等,目前国内的钛资源岩矿虽然很多,但高品质的砂矿少,要适应氯化法生产工艺,还需要将钛精矿提炼成高钛渣,这样一来,氯化法的生产流程就相当复杂,且成本颇高;其二,氯化法工艺对生产技术和装备材质的要求都非常高,而国内绝大多数钛白粉企业达不到这种技术水平;其三,氯化法产生废水废渣排放虽然较硫酸法少,但其废物比硫酸法产生的废物毒性更大、更难处理;其四,硫酸法钛白粉在某些领域有特殊应用,是氯化法所不能代替的,如SCR脱硝催化剂用二氧化钛等。技术实现要素:本发明的目的在于针对以上问题,提供一种利用钛渣为原料制备锐钛矿型二氧化钛的方法及系统。该方法操作简单,不产生废水、废气、废渣,生产出的二氧化钛具有高纯度、高比表面积等特点,生产出的产品不仅可直接作为选择性催化还原脱硝催化剂载体用,推进SCR脱硝技术的发展,缓解氮氧化物(NOx)对环境造成的污染,还可用于光催化催化剂、功能纤维、精细陶瓷、高档汽车面漆及化妆品等领域。本发明目的通过下述技术方案来实现:一种利用钛渣为原料制备锐钛矿型二氧化钛的方法,该方法包括以下步骤:(1)钛渣研磨与还原焙烧:将钛渣研磨至粒径为5μm-20μm,与氢氧化钠以质量比1:1.1-1.8的比例混合均匀后进行还原焙烧,还原焙烧温度400℃-600℃,还原焙烧时间2h-6h。(2)还原焙烧后钛渣的水洗:将还原焙烧后的钛渣以蒸馏水反复清洗、过滤,直至洗出液呈中性,得到碱性水洗滤液和滤渣(钛渣),并将滤渣烘干。(3)水洗滤液除杂:碱性水洗滤液通过纳滤膜组件除去水洗液中的Na2MnO4、Na2SiO3、NaAlO2等杂质,杂质的截留率>99%,操作温度为常温,操作压力为0.3MPa-0.7MPa。(4)碱性滤液蒸发结晶:除去杂质后的碱性水洗滤液,采用MVR蒸发器蒸发至NaOH的wt≥60%后,结晶制得NaOH晶体,循环使用。(5)钛渣酸解浸出:将烘干后的钛渣加入稀硫酸在常压下进行酸解浸出,得到酸解浸出液,采用稀硫酸的质量浓度为15%-55%,浸出温度90℃-105℃,浸出时间1.5h-4h。(6)酸解浸出液再生:将酸解浸出液通过离子交换树脂再生系统进行再生,再生后硫酸溶液质量浓度12%-45%,硫酸回收率>85%,回收的硫酸溶液循环利用,并将硫酸盐溶液进行水解。(7)硫酸盐溶液水解:将硫酸盐溶液加入还原铁粉将Fe3+全部还原为Fe2+后,加入氢氧化钠进行中和、水解,直至pH=2-2.5时,Ti4+以偏钛酸的形式完全沉淀析出,Fe、Ca、Mg等杂质以硫酸盐的形式留在液相中,实现杂质与Ti的选择性分离。(8)偏钛酸颗粒后处理:将偏钛酸颗粒清洗干净、过滤、烘干,并于450℃~650℃下焙烧2h~4h得到锐钛矿型二氧化钛。本发明的钛渣是指钒钛铁矿冶炼后的高炉含钛废渣、高钛高炉水淬渣或冶炼海绵钛高钛渣等,钛渣中TiO2的质量分数为46%~85%。与现有技术相比,本发明的具体有益效果体现在:(一)、可以实现资源的充分利用,使得TiO2含量较低的低品位钛渣能够得到更充分的利用。(二)、节能环保。本发明可大幅降低酸解过程中硫酸的浓度及使用量,且消耗的硫酸及氢氧化钠,均可实现资源循环利用,杜绝环境污染。(三)、本发明制得的锐钛型二氧化钛品质高,其一次粒子粒径≤10nm,比表面积180m2/g~220m2/g,二氧化钛纯度>95%,可应用于脱硝催化剂载体、光催化催化剂、功能纤维、精细陶瓷、高档汽车面漆及化妆品等高端领域。(四)、本发明制备二氧化钛的方法,操作简单,全程无高温、高压操作,避免了传统钛渣酸解过程中的高耗能、高风险操作,易于工业化生产。(五)、本发明采用一种新型的硫酸法生产二氧化钛方法,既解决了硫酸法硫酸消耗量大、能耗高、产品品质低的问题,又可避免氯化法原料价格高、工艺复杂,以及产生毒性大、难处理的三废的不利影响。附图说明图1为本发明所述的一种以工业钛渣为原料制备锐钛矿型二氧化钛的生产方法的工艺流程图;图2为本发明中所述的硫酸浸出液的离子交换树脂再生系统示意图。具体实施方式本说明书中公开的所有特征,或公开的所有方法或过程中的步骤,除了互相排斥的特征和/或步骤以外,均可以以任何方式组合。本说明书(包括任何附加权利要求、摘要)中公开的任一特征,除非特别叙述,均可被其他等效或具有类似目的的替代特征加以替换。即,除非特别叙述,每个特征只是一系列等效或类似特征中的一个例子而已。实施例1:以下%无特别说明,均为质量百分含量符号。本发明对比例和实施例中所用的钛渣主要成分如表1所示,余量为杂质。表1钛渣主要成分的百分含量(%)成分CaOMgOAl2O3Fe2O3MnOTiO2ZrO2SiO2含量(mass.%)1.516.344.047.820.9968.430.077.68实施例1:将钛渣研磨至粒径为5μm-20μm,与氢氧化钠以质量比1:1.2的比例混合均匀后进行还原焙烧,还原焙烧温度600℃,还原焙烧时间6h。将还原焙烧后的钛渣用蒸馏水反复清洗、过滤,直至洗出液呈中性,收集碱性水洗滤液和滤渣(钛渣),并将滤渣在105℃下烘干。碱性水洗滤液通过纳滤膜组件除去水洗液中的Na2MnO4、Na2SiO3、NaAlO2等杂质,杂质去除率99.5%,操作温度为常温,操作压力为0.6MPa。除杂后的碱性水洗滤液采用MVR蒸发器蒸发至NaOH质量浓度为60%后,结晶、压滤制得NaOH晶体。将烘干后的钛渣加入质量浓度为45%稀硫酸在常压、105℃下进行酸解浸出4h,得到酸解浸出液。将酸解浸出液通过离子交换树脂再生系统进行再生,再生后硫酸溶液质量浓度为38%,硫酸回收率85%,回收的硫酸溶液循环利用,并将硫酸盐溶液进行水解。将硫酸盐溶液加入还原铁粉将Fe3+全部还原为Fe2+后,加入氢氧化钠进行中和、水解,直至pH=2-2.5时,Ti4+以偏钛酸的形式完全沉淀析出,Fe2+、Ca2+、Mg2+等杂质以硫酸盐的形式留在液相中。将偏钛酸颗粒清洗干净、过滤,在95℃烘干4h,并于550℃下焙烧4h得到锐钛矿型二氧化钛。二氧化钛总收率为96.1%,二氧化钛纯度97.8%,比表面积192m2/g。实施例2:将钛渣研磨至粒径为5μm-20μm,与氢氧化钠以质量比1:1.6的比例混合均匀后进行还原焙烧,还原焙烧温度600℃,还原焙烧时间4h。将还原焙烧后的钛渣用蒸馏水反复清洗、过滤,直至洗出液呈中性,收集碱性水洗滤液和滤渣(钛渣),并将滤渣在105℃下烘干,碱性水洗滤液通过纳滤膜组件除去水洗液中的Na2MnO4、Na2SiO3、NaAlO2等杂质,杂质去除率99.5%,操作温度为常温,操作压力为0.6Mpa。除杂后的碱性水洗滤液采用MVR蒸发器蒸发至NaOH质量浓度为60%后,结晶、压滤制得NaOH晶体。将烘干后的钛渣加入质量浓度为50%稀硫酸在常压、105℃下进行酸解浸出4h,得到酸解浸出液。将酸解浸出液通过离子交换树脂再生系统进行再生,再生后硫酸溶液质量浓度41%,硫酸回收率85%,回收的硫酸溶液循环利用,并将硫酸盐溶液进行水解。将硫酸盐溶液加入还原铁粉将Fe3+全部还原为Fe2+后,加入氢氧化钠进行中和、水解,直至pH=2-2.5时,Ti4+以偏钛酸的形式完全沉淀析出,Fe2+、Ca2+、Mg2+等杂质以硫酸盐的形式留在液相中。将偏钛酸颗粒清洗干净、过滤,在95℃烘干4h,并于550℃下焙烧4h得到锐钛矿型二氧化钛。二氧化钛总收率为98.3%,二氧化钛纯度98.1%,比表面积218m2/g。对比例1:将钛渣研磨至粒径为5μm-20μm,加入浓度为92%硫酸,加热至220℃进行酸解,酸解时间3.5h。分离出不溶残渣后,向溶液中加入还原铁粉将Fe3+全部还原为Fe2+后,缓慢加入NaOH,直至pH=2-2.5时,Ti4+以偏钛酸的形式完全沉淀析出,杂质以硫酸盐的形式留在液相中。过滤收集沉淀的偏钛酸颗粒,清洗干净、过滤,在95℃烘干4h,并于550℃下焙烧4h得到锐钛矿型二氧化钛。二氧化钛总收率91.3%,二氧化钛纯度为92.7%,比表面积为69m2/g。对比例2:将10mL钛酸丁酯缓慢加入搅拌的无水乙醇中,加入1g聚乙二醇。继续搅拌10min,将1.6mL去离子水加入到无水乙醇中,形成滴加液,并逐滴加入到上述溶液中,搅拌形成透明的溶胶。静置胶化,并在100℃条件下干燥。形成溶胶后,在高温条件下脱除有机模板剂,得到纳米二氧化钛颗粒。二氧化钛比表面积为146m2/g。本发明并不局限于上述实施例中记载,本发明可扩展到强放热的气液两相化学反应釜。也可扩展到任何在本说明书中披露的新特征或任何新的组合,以及披露的任一新的方法或过程的步骤或任何新的组合。当前第1页1 2 3