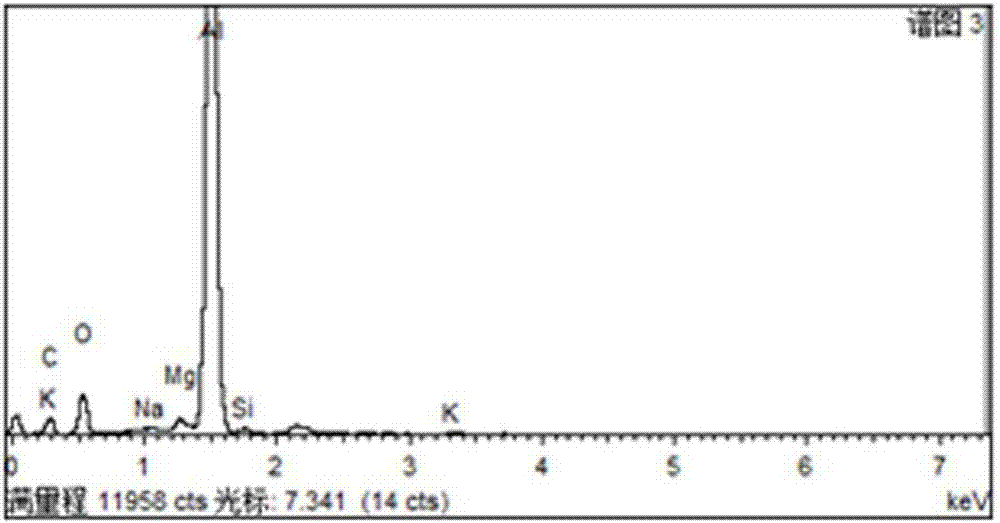
本发明属于电炉、转炉炉衬及钢包包衬用高级耐火材料及其制备
技术领域:
,具体涉及一种不烧铝镁碳砖及其制备方法。
背景技术:
:铝镁碳砖是以al2o3,mgo和c为主要成分的含碳耐火材料,含al2o360%~69%,mgo7%~14%,c5%~12%。具有较好的抗渣侵蚀性和抗热震性,有微量的重烧膨胀,主要用于电炉、转炉炉衬及钢包包衬。现有的铝镁碳砖虽然满足一定的使用要求,但是仍存在价格昂贵,使用寿命短等问题。因此如何降低成本,开发高效使用寿命长绿色环保的耐火材料,一直是耐火行业高度重视的技术经济问题。目前为减少雾霾保护环境,铝镁碳砖的制备方法中,烧成砖过程选用天然气替代燃油提供热能,因此烧成过程需要大量的天然气提供热能,每吨砖烧成所需要的天然气的成本约为600-800元,产品成本仍然较高,在烧成过程中天然气的燃烧仍然产生一定量的温室气体,对地球整体的温室效应会有影响。天然气虽然是无色无味的,但是当天然气在封闭环境里聚集达到一定的比例时会触发威力巨大的爆炸,因此用天然气提供热能存在一定的安全隐患,并且在制备环节中的细节掌握的比较粗糙,制备出的成型砖坯外形和致密度存在不足。因此,研制一种制备方法简单安全、成本低、无需高温烧成、密度大、强度高、耐腐蚀性强且抗熔融金属和抗氧化能力强、节能减排的不烧铝镁碳砖是非常必要的。技术实现要素:针对现有技术存在的问题,本发明的目的在于提供一种不烧铝镁碳砖及其制备方法。本发明一种不烧铝镁碳砖具有密度大、强度高、高温热震稳定性好、抗氧化能力强等优点;本发明制备方法简单、无需高温烧成、成本低、节能、制备安全。为解决上述技术问题,本发明采用的技术方案为。一种不烧铝镁碳砖,其特征在于:包括骨料、粉料、添加剂和结合剂,所述骨料的原料按重量份数组成如下:棕刚玉(al2o3≥94.5%,粒度0.1-1mm)和或特级矾土(al2o3≥88%,粒度1-5mm)60-70份;所述粉料的原料按重量份数组成如下:镁铝尖晶石(mgo≥33%,al2o3≥65%,粒度300-400目)1-3份,高纯镁砂(mgo≥97%,粒度300-400目,颗粒体积密度≥3.28g.cm-3,含水量≤4%)9-11份,亚白刚玉(al2o3≥97%,粒度300-400目)11-13份;添加剂2-4份;石墨(c≥97%,含水量≤0.5%)5-7份,高温沥青(软化≥150℃,残碳≥50%,粒度200目)1-3份,稀土氧化物(粒度300-350目)0.2-0.5份,陶瓷结合剂3-5份,络合镁铝胶结剂3-4份,水1-3份。本发明的一种优选方案,包括骨料、粉料、添加剂和结合剂,所述骨料的原料按重量份数组成如下:特级矾土(al2o3≥88%,粒度1-5mm)53份,棕刚玉(al2o33≥94.5%,粒度0.1-1mm)12份;所述粉料的原料按重量份数组成如下:镁铝尖晶石(mgo≥33%,al2o3≥65%,粒度300-400目)2份,高纯镁砂(mgo≥97%,粒度300-400目,颗粒体积密度≥3.28g.cm-3,含水量≤4%)10份,亚白刚玉(al2o3≥97%,粒度300-400目)12份;添加剂3份;石墨(c≥97%,含水量≤0.5%)6份,高温沥青(软化≥150℃,残碳≥50%,粒度200目)2份,稀土氧化物(粒度300-350目)0.4份,陶瓷结合剂4份,络合镁铝胶结剂3.5份,水1-3份。进一步的,所述添加剂为碳化硅本发明的另一种优选方案,包括骨料、粉料、添加剂和结合剂,所述骨料的原料按重量份数组成如下:棕刚玉(al2o33≥94.5%,粒度0.1-1mm)65份;所述粉料的原料按重量份数组成如下:镁铝尖晶石(mgo≥33%,al2o3≥65%,粒度300-400目)2份,高纯镁砂(mgo≥97%,粒度300-400目,颗粒体积密度≥3.28g.cm-3,含水量≤4%)10份,亚白刚玉(al2o3≥97%,粒度300-400目)12份;添加剂3份;石墨(c≥97%,含水量≤0.5%)6份,高温沥青(软化≥150℃,残碳≥50%,粒度200目)2份,稀土氧化物(粒度300-350目)0.4份,陶瓷结合剂4份,络合镁铝胶结剂3.5份,水1-3份。进一步的,所述添加剂为金属铝粉和金属硅粉,所述金属铝粉和所述金属硅粉的重量份数比为1:1。本发明的第三种优选方案,所述高纯度镁砂包括高纯度电熔镁砂(mgo≥97%,粒度300-400目,颗粒体积密度≥3.45g.cm-3,含水量≤4%)和高纯度烧结镁砂(mgo≥97%,粒度300-400目,颗粒体积密度≥3.28g.cm-3,含水量≤4%),所述高纯度电熔镁砂和所述高纯度烧结镁砂的重量份数比为1:1。本发明的第四种优选方案,所述添加剂为碳化硅(sic≥97%,粒度200目)、金属铝粉(al≥98%,粒度200目)和金属硅粉(si≥98%,粒度200目)中的一种或两种。本发明的第五种优选方案,所述稀土氧化物为氧化铈、氧化镨、氧化镧和氧化铷中的一种或两种。本发明的第六种优选方案,所述特级矾土(粒度1-3mm)与所述特级矾土(粒度3-5mm)的重量份数比为8-9:4-5。一种不烧铝镁碳砖的制备方法,步骤如下:(1)原料加工骨料:按重量份数秤取棕刚玉和或特级矾土,放入颚式破碎机中进行破碎,破碎成大颗粒后经对辊破碎,再用振动筛筛出粒度为0.1-5mm的骨料,破粉碎加工换料时,先将料仓和破粉碎设备系统的积存料清除干净;粉料:按重量份数秤取高纯度电熔镁砂、高纯度烧结镁砂、镁铝尖晶石和亚白刚玉放入颚式破碎机中进行破碎,破碎成大颗粒后经对辊破碎,再振动筛分制得粒度1-5mm的颗粒,再放入雷蒙磨中制得150目细粉,再加入球磨机中进行球磨,球磨转速200-250r/min,球磨时间20-30min,制得粉料粒度300-400目;按重量份数秤取添加剂、高温沥青、稀土氧化物和陶瓷结合剂加入上述粉料中支撑预混粉料;(2)混料将配制的骨料放入泥料混炼机中,混炼转速20-30r/min,混炼时间2-3min;加入2/3重量份数的络合镁铝胶结剂,在搅拌时加水至结合剂形成浆料包裹在骨料表面,混炼转速20-30r/min,搅拌时间4-5min;加入石墨,混炼转速20-30r/min,搅拌时间4-5min;加入预混粉料,混炼转速20-30r/min,搅拌时间7-8min;加入1/3重量份数的络合镁铝胶结剂,混炼转速20-30r/min,搅拌时间7-8min,冬季料温不低于20℃,夏季料温不高于45℃;(3)成型:称量一定量的混料放入压机中成型,压机压力为700吨~1000吨,入模混料要前后扒平,四角充实,采取先轻后重,第一、二锤吊锤操作、出模排气,出模排气次数为3-5次,再3~5锤抬高锤头重击,成型体密≥3.32/g.cm3;(4)干燥:将成型的复合砖坯放入电加热干燥装置进行干燥,升温温度20-55℃,加热时间3h;保持温度55±10℃,加热时间3h;升温温度55-100℃,加热时间3h;保持温度100±15℃,加热时间4h;升温温度100~210℃,加热时间6h;保持温度210±10℃,加热时间5h;即得成品。本发明的有益效果:(1)性能优越。本发明不烧铝镁碳砖采用络合镁铝胶结剂与陶瓷结合剂,由表3和表4对比可知本发明的性能远高于现有的铝镁碳砖的性能指标,具有纯度高,密度大,强度高、气孔率小,收缩率低、抗渣侵蚀性强、抗氧化能力强等优点。本发明采用的络合镁铝胶结剂其主要成分是mgo和al2o3,是纳米技术制作的粉体,用作本发明结合剂时,不会引入杂质成分,在常温下水化后具有胶结作用,干燥后,形成穿插式的结构镶嵌在颗粒与细粉之间,使本发明具有理想的结合强度。(2)降低成本。本发明的制备方法在电加热干燥装置200℃以内烘烤进行对复合砖的干燥即得性能优越的成品,与高温烧结相比,本发明的制备过程中的成本降低500-550元/吨(天燃气砖烧成成本600元/吨左右,免烧烘烤成本50-100元/吨。)为社会节约巨大的经济成本,同时创造出巨大的经济效益,影响巨大。(3)节能无安全隐患。本发明在制备过程中不采用天然气提供热能高温烧结,采用电能低温烘烤技术,克服了天然气的价格贵和天然气燃烧后的产生的co2温室效应等一系列问题。络合镁铝胶结剂是采用先进科技,无毒无味,节能环保;本发明与传统镁铬砖相比,配料中不加入含铬的原料,不污染环境,工人工作条件大为改善;并且不存在天然气会引发的任何安全隐患问题。(4)制备方法提高砖的成型效果。本发明能够保证砖坯致密度好,防止产生层裂,出模砖坯结构均匀,没有粗颗粒集中在边角部位的现象,表面没有明显的麻点、白点、层裂和飞边。在储存和运输的过程中保护的非常周密,提高成型的完成度。附图说明图1为本发明的实施例1制备的不烧铝镁碳砖抛光的(300x,20μm)的扫描电镜图。图2为本发明的实施例1制备的不烧铝镁碳砖抛光的xrd图。具体实施方式为了进一步理解本发明,下面结合实施例对本发明优选实施方案进行描述,但是应当理解,这些描述只是为进一步说明本发明的特征和优点,而不是对本发明权利要求的限制。实施例1。分别按以下表1中指定的各组分秤取原料,制备方法如下。(1)原料加工骨料:按重量份数秤取棕刚玉和或特级矾土,放入颚式破碎机中进行破碎,破碎成大颗粒后经对辊破碎,再用振动筛筛出粒度为0.1-5mm的骨料,破粉碎加工换料时,先将料仓和破粉碎设备系统的积存料清除干净。粉料:按重量份数秤取高纯度电熔镁砂、高纯度烧结镁砂、镁铝尖晶石和亚白刚玉放入颚式破碎机中进行破碎,破碎成大颗粒后经对辊破碎,再振动筛分制得粒度1-5mm的颗粒,再放入雷蒙磨中制得150目细粉,再加入球磨机中进行球磨,球磨转速200-250r/min,球磨时间20-30min,制得粉料粒度300-400目;按重量份数秤取添加剂、、高温沥青、稀土氧化物和陶瓷结合剂加入上述粉料中支撑预混粉料。(2)混料将配制的骨料放入泥料混炼机中,混炼转速20-30r/min,混炼时间2-3min;加入2/3重量份数的络合镁铝胶结剂,在搅拌时加水至结合剂形成浆料包裹在骨料表面,混炼转速20-30r/min,搅拌时间4-5min;加入石墨,混炼转速20-30r/min,搅拌时间4-5min;加入预混粉料,混炼转速20-30r/min,搅拌时间7-8min;加入1/3重量份数的络合镁铝胶结剂,混炼转速20-30r/min,搅拌时间7-8min,冬季料温不低于20℃,夏季料温不高于45℃。注意:混练好的泥料应充分润滑,不得有干状细粉、泥团、泥饼等。根据泥料的“干”、“湿”情况,可酌情增、减结合剂用量。判断泥料干湿程度的经验规则为:“手捏成团,一按即散”;混料时加入液体结合剂必须缓慢、均匀,不得过急或过快,以免造成泥料不匀或结团;在混料工序产生的废料可按相同材质搭配混料,不得集中使用,回收料与细粉一起加入,加入量不超过总混量的15%;混练好的泥料放入集装袋,并困料1-2小时后成型。(3)成型:称量一定量的混料放入压机中成型,压机压力为700吨~1000吨,入模混料要前后扒平,四角充实,采取先轻后重,第一、二锤吊锤操作、出模排气,出模排气次数为3-5次,再3~5锤抬高锤头重击,成型体密≥3.32/g.cm3;注意:砖模锥度为0.6%,模壁衬板与底板之间的间隙不得大于0.5mm。放尺率为0。新装模具及交接班开机时,压第一、二块砖必须认真检查,确保砖型尺寸与图纸相符,出模砖坯要轻拿轻放,为保证砖坯致密度,防止产生层裂,入模泥料要准确称量,颗粒均匀。出模砖坯要结构均匀,不允许有粗颗粒集中在边角部位的现象,以及表面明显的麻点、白点、层裂和飞边。砖坯外形应符合表2,砖坯间距保留在5-10mm。(4)干燥:将成型的复合砖坯放入电加热干燥装置进行干燥,升温温度20-55℃,加热时间3h;保持温度55±10℃,加热时间3h;升温温度55-100℃,加热时间3h;保持温度100±15℃,加热时间4h;升温温度100~210℃,加热时间6h;保持温度210±10℃,加热时间5h,共计24h;即得成品。注意:未经热处理的砖坯在外存放时间不得超过5d。(5)成品质量检查与包装:质检人员按标准要求对入库成品进行外观检查,成品经检查合格包装入库,同时按牌号取样送检,作理化性能检测,废品按材质分类,集中处理;采用内层塑料薄膜和外层纸箱的防潮包装,每箱重量不超过2.0吨。(6)存放与运输:产品按用户、牌号、品种分类码放于仓库,防止受潮。发给用户时,应做到先入库的先发。成品出厂应附有质量证明书,说明产品牌号、规格、检验结果。货送到用户后,同样要入库存放,防止受潮。本发明实施例1的制备成品对其进行物理力学性能指标检验。在表3中列出了测试结果。本发明实施例1的制备成品对其进行电镜扫描,结果如附图1所示;对其进行x衍射检测,结果如附图2所示。实施例2。按以下表1中指定的各组分含量重复实施例1的方法,在表3中列出了测试结果。实施例3。按以下表1中指定的各组分含量重复实施例1的方法,在表3中列出了测试结果。对比例1。按以下表1中指定的各组分含量重复实施例1的方法,唯一不同的是在制备方法步骤4中增加干燥升温温度至1400℃,加热时间5h,在表3中列出了测试结果。对比例2。按以下表1中指定的各组分含量重复实施例2的方法,唯一不同的是在制备方法步骤4中增加干燥升温温度至1400℃,加热时间5h,在表3中列出了测试结果。对比例3。按以下表1中指定的各组分含量重复实施例3的方法,唯一不同的是在制备方法步骤4中增加干燥升温温度至1400℃,加热时间5h,在表3中列出了测试结果。表1本发明实施例1-3的原料配比表。表2砖坯外形应符合的规定数据表。一、性能检测。1、对实施例1-3和对比例1-3制备的不烧铝镁碳砖进行性能检测,结果如表3。表3本发明的实施例1-3和对比例1-3的理化指标。2、目前市面上的不同型号镁碳砖性能指标如表4。表4目前市面上的不同型号镁碳砖性能指标。由表3和表4可知,本发明制备的不烧铝镁碳砖的体积密度>3.20g.cm-3,气孔率<14%,目前市面上的不同型号镁碳砖性能指标中体积密度≥2.65g.cm-3之间,气孔率≤21%之间,由此可见,本发明的体积密度大于目前市面上的不同型号镁碳砖性能指标中体积密度,气孔率小于不同型号镁碳砖性能指标中气孔率,说明本发明耐腐蚀性强且抗熔融金属和抗氧化能力强;本发明的200℃×24h的耐压强度为70mpa以上,高温抗折强度(1450℃×1h)≥9mpa,目前市面上的不同型号镁碳砖性能指标中常温耐压强度在40mpa以上,由此可见,本发明的耐压强度大于目前市面上的不同型号镁碳砖性能指标中耐压强度;本发明的0.2mpa荷重软化开始温度≥1680℃,目前市面上的不同型号镁碳砖性能指标中0.2mpa荷重软化开始温度≥1420℃,本发明的0.2mpa荷重软化开始温度大于目前市面上的不同型号镁碳砖性能指标中的0.2mpa荷重软化开始温度,由此可见,本发明的抵抗高温应力的性能高,常温耐压强度大,高温抗折强度大。由表3可知,本发明200℃烘烤24h脱水制备出的不烧铝镁碳砖的常温耐压强度>70mpa,这是由于水化结合作用使本发明具有较高的常温耐压强度;本发明在1400℃的烧结是纳米陶瓷过渡烧结的作用使不烧铝镁碳砖的高温抗折强度>9mpa;本发明在使用过程中具有边运用边烧结的特点。3、对本发明的实施例1制备的成品进行电镜扫描,结果如图1。附图1是本发明实施例1制备的成品的电镜扫描图,可以看出本发明通过添加陶瓷结合剂颗粒堆积紧密,烧结性能也明显改善,通过采用陶瓷烧结技术低温、中温、高温耐压强度及抗折强度均有所提高。4、对本发明的实施例1制备的成品进行x衍射检测,结果如附图2所示。(1)检测条件与检测结果如下。谱图处理结果:可能被忽略的峰:2.134,9.704kev;处理选项:oxygen按化学计量法(已归一化);重复次数=4;标准样品如表5所示;xrd检测结果如表6和图2所示。表5。ccaco31-jun-199912:00amnaalbite1-jun-199912:00ammgmgo1-jun-199912:00amalal2o31-jun-199912:00amsisio21-jun-199912:00amkmad-10feldspar1-jun-199912:00am表6。元素重量百分比/%原子百分比/%化合物百分比/%化学式ck9.3914.0634.39co2nak0.140.110.18na2omgk0.370.280.62mgoalk33.8522.5763.97al2o3sik0.310.200.67sio2kk0.140.060.17k2oo55.8062.73总量100.00根据表5-6和图1-2所知,采用本发明的配方和制备方法可以制备出纯度高、结合强度高的不烧铝镁碳砖。可以理解的是,以上关于本发明的具体描述,仅用于说明本发明而并非受限于本发明实施例所描述的技术方案,本领域的普通技术人员应当理解,仍然可以对本发明进行修改或等同替换,以达到相同的技术效果;只要满足使用需要,都在本发明的保护范围之内。当前第1页12