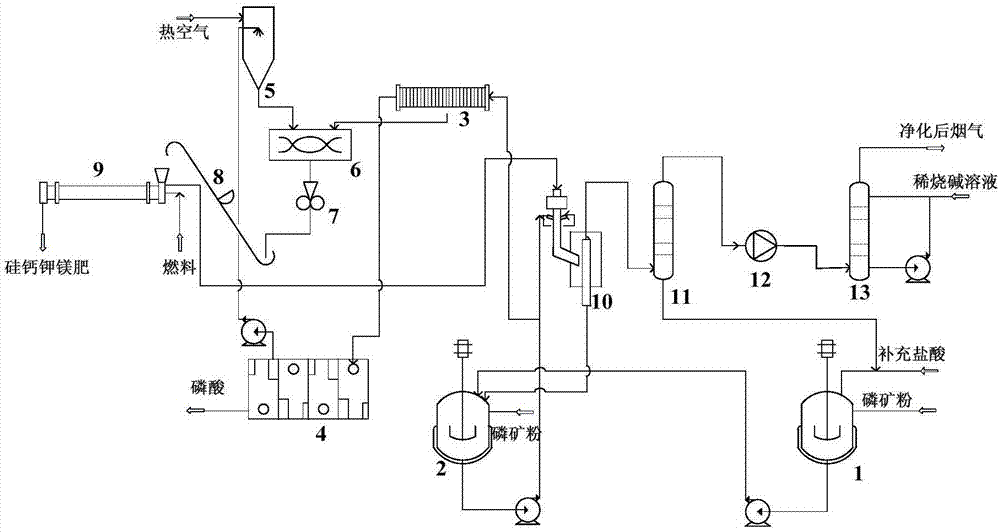
本发明属于磷化工生产
技术领域:
,涉及一种由磷矿制备磷酸和硅钙钾镁肥的系统及方法。
背景技术:
无机磷化学工业包括磷酸盐等无机磷化物的生产,是重要的化学工业系列产品之一。目前,我国已建立起较为完善的磷化工生产体系,基本能够满足经济增长和生产水平提高的需求,并有大量产品出口,成为世界上第一大磷化工生产国、消费国和出口国。然而,磷化工的生产仍存在着严重的环境问题,据统计,每生产1吨含100%p2o5的磷酸将产生5-6吨磷石膏,磷石膏中除含有caso4外,还含有未分解的磷矿,未洗涤脱除的磷酸、氟化钙、铁铝化合物、酸不溶物、有机质等多种杂质,这些杂质严重制约了磷石膏的利用。目前,绝大部分磷石膏被当作废物丢弃,不仅占用大量土地,而且堆场投资大、运营费高,更浪费了宝贵的硫资源,特别是严重污染环境。目前,全国湿法磷酸生产能力约546万吨,每年的磷石膏废渣量达2500-3000万吨,占地达2000公顷,仅渣场投资估算达10亿元。从环保和技术安全角度看,磷石膏废渣处理和减排已迫在眉睫。鉴于目前湿法磷酸副产磷石膏的环境问题,行业研究者一直在寻求湿法磷酸源头减排清洁技术。cn101456545a公开了一种用中低品位磷矿生产重过磷酸钙联产氯化钙的方法,该方法包括两部分,其一分别为磷矿粉1用盐酸酸解、酸解液部分萃取、萃取有机相反萃制备磷酸、萃余水相与石灰乳反应得到磷酸氢钙和氯化钙;其二为磷矿粉2与上述所得磷酸酸解,再加入上述所得磷酸氢钙,反应得到重过磷酸钙;虽然上述方法可以得到重过磷酸钙和氯化钙,但制备过程较为复杂,所得产品纯度不足,且盐酸利用率低。cn101774556a公开了一种盐酸分解中低品位磷矿制备工业级和食品级磷酸的方法,该方法依次包括盐酸酸解磷矿粉、萃取除铁、制备稀磷酸、制备工业级磷酸和制备食品级磷酸,其中,由稀磷酸制备工业级磷酸步骤包括浓缩、脱砷脱重金属、脱色、过滤、深脱色和调节浓度等,制备食品级磷酸时还包括深脱氟的步骤;该方法能够得到高纯磷酸,但该方法制备过程较为复杂,仍有有害固体废弃物产生,未能充分利用磷矿资源。综上所述,磷矿资源的高效利用和磷化工的清洁生产还需寻求新的工艺过程,提高原料利用率,从源头上消减废弃物的排放。技术实现要素:针对现有技术存在的问题,本发明的目的在于提供一种由磷矿制备磷酸和硅钙钾镁肥的系统及方法,本发明利用盐酸对磷矿粉进行分解,得到磷酸等高值化产品,再通过中间产物与钾长石的煅烧,得到硅钙钾镁肥和含hcl气体,通过吸收实现盐酸的循环,整体实现了磷矿资源的综合利用;所述方法不产生固体废弃物,为磷酸生产的清洁技术,为磷矿的综合利用提供了一条新途径。为达此目的,本发明采用以下技术方案:一方面,本发明提供了一种由磷矿制备磷酸和硅钙钾镁肥的系统,所述系统包括酸浸单元、固液分离装置、萃取装置、造粒单元、焙烧装置、盐酸吸收单元和尾气净化装置;其中,所述酸浸单元的液体出口分别与固液分离装置和盐酸吸收单元的液体入口相连,所述固液分离装置的液体出口与萃取装置的液体入口相连,所述萃取装置的萃取液出口得到磷酸,所述萃取装置的萃余液出口和固液分离装置的固体出口均与造粒单元相连,所述造粒单元的固体出口与焙烧装置的固体入口相连,所述焙烧装置的固体出口得到硅钙钾镁肥,所述焙烧装置的气体出口与盐酸吸收单元的气体入口相连,所述盐酸吸收单元的液体出口与酸浸单元的液体入口相连,所述盐酸吸收单元的气体出口与尾气净化装置的气体入口相连。本发明中,所述系统也可以称为装置、设备或者生产装置以及其的组合等。本发明中,采用所述系统处理磷矿资源,利用盐酸对磷矿粉进行酸浸处理,所得氯化钙和磷酸混合溶液经萃取后得到磷酸,氯化钙、酸浸处理剩余固体渣以及钾长石共同造粒后焙烧处理,得到硅钙钾镁肥和含hcl烟气,烟气与酸浸液接触既可实现降温,也能通过hcl的吸收实现盐酸循环,从而在整体上实现磷矿资源的综合利用,同时无固体废弃物产生,实现磷酸清洁生产。以下作为本发明优选的技术方案,但不作为本发明提供的技术方案的限制,通过以下技术方案,可以更好地达到和实现本发明的技术目的和有益效果。作为本发明优选的技术方案,所述酸浸单元包括一级酸浸釜和二级酸浸釜,所述一级酸浸釜的液体出口与二级酸浸釜的液体入口相连。优选地,所述造粒单元包括喷雾造粒塔和造粒装置,所述喷雾造粒塔的入口与萃取装置的萃余液出口相连,所述喷雾造粒塔的固体出口和固液分离装置的固体出口均与造粒装置的固体入口相连。优选地,所述造粒单元还包括混合装置,所述喷雾造粒塔的固体出口和固液分离装置的固体出口均与混合装置相连,所述混合装置的固体出口与造粒装置相连。本发明中,造粒单元主要分为两步造粒,先是氯化钙溶液经过喷雾造粒得到氯化钙颗粒,再与酸浸处理后的固体渣、钾长石等混合造粒,作为焙烧处理的原料,以充分利用磷矿和钾长石中的营养元素。优选地,所述盐酸吸收单元包括浓缩装置和盐酸吸收塔,所述浓缩装置的气体入口与焙烧装置的气体出口相连,所述浓缩装置的气体出口与盐酸吸收塔的气体入口相连,所述盐酸吸收塔的气体出口与尾气净化装置的气体入口相连。优选地,所述浓缩装置的液体出口与二级酸浸釜的液体入口相连,所述盐酸吸收塔的液体出口与一级酸浸釜的液体入口相连。本发明中,进入盐酸吸收单元中浓缩装置的液体为二级酸浸釜的反应液,与焙烧产生的烟气接触,在降低烟气的温度过程中减少酸浸液中的水分,提高酸浸液浓度,同时也可以吸收部分hcl气体形成盐酸,返回二级酸浸釜,提高磷矿粉的反应程度;再设置盐酸吸收塔,也可吸收烟气中的hcl气体返回一级酸浸釜,实现盐酸循环。作为本发明优选的技术方案,所述一级酸浸釜和二级酸浸釜之间、二级酸浸釜和固液分离装置之间、萃取装置和喷雾造粒塔之间、尾气净化装置的底部和顶部之间均设有泵。优选地,所述造粒装置和焙烧装置之间设有提升机。优选地,所述盐酸吸收塔和尾气净化装置之间设有风机。作为本发明优选的技术方案,所述一级酸浸釜和二级酸浸釜为耐氢氟酸和耐盐酸材质。优选地,所述固液分离装置包括压滤机。优选地,所述萃取装置包括混合澄清槽。优选地,所述造粒装置包括圆盘造粒机。优选地,所述焙烧装置包括回转窑。另一方面,本发明提供了一种采用上述系统制备磷酸和硅钙钾镁肥的方法,所述方法包括以下步骤:(1)将磷矿粉与盐酸混合后发生酸浸反应,得到反应浆液;(2)将步骤(1)得到的反应浆液经浓缩处理后进行固液分离,得到氯化钙和磷酸混合液以及固体渣,所得混合液进行萃取处理,得到磷酸和氯化钙溶液;(3)将钾长石、步骤(2)得到的固体渣和氯化钙混合进行造粒,然后进行焙烧处理,得到硅钙钾镁肥和含hcl烟气;(4)将步骤(3)得到的含hcl烟气与步骤(1)得到的反应浆液混合吸收hcl,所得吸收液返回步骤(1),hcl被吸收后的烟气进行净化处理后排放。作为本发明优选的技术方案,步骤(1)所述磷矿粉的组成以氧化物形式表示主要包括p2o5和cao。优选地,所述磷矿粉中p2o5的质量含量为25~35wt%,例如25wt%、26wt%、27wt%、28wt%、30wt%、32wt%、34wt%、或35wt%等,但并不仅限于所列举的数值,该数值范围内其他未列举的数值同样适用。优选地,所述磷矿粉中cao的质量含量为45~51wt%,例如45wt%、46wt%、47wt%、48wt%、49wt%、50wt%或51wt%等,但并不仅限于所列举的数值,该数值范围内其他未列举的数值同样适用。优选地,所述磷矿粉的粒径为30~60目,例如30目、35目、40目、45目、50目、55目或60目等,但并不仅限于所列举的数值,该数值范围内其他未列举的数值同样适用。优选地,步骤(1)所述盐酸的质量浓度为18~22wt%,例如18wt%、18.5wt%、19wt%、19.5wt%、20wt%、20.5wt%、21wt%、21.5wt%或22wt%等,但并不仅限于所列举的数值,该数值范围内其他未列举的数值同样适用。优选地,所述磷矿粉中cao与盐酸加入量的摩尔比为1:(2.0~2.1)。例如1:2.0、1:2.02、1:2.04、1:2.06、1:2.06或1:2.1等,但并不仅限于所列举的数值,该数值范围内其他未列举的数值同样适用。本发明中,磷矿粉中主要反应成分为cao和p2o5,与盐酸反应生成cacl2和h3po4,反应物比例以cao和盐酸的摩尔比来确定,实际加入量可以稍高于两者的理论摩尔比1:2,有助于磷矿粉充分分解。优选地,步骤(1)所述酸浸反应分别在一级酸浸釜和二级酸浸釜内进行。优选地,所述一级酸浸釜内的反应温度为65~85℃,例如65℃、70℃、75℃、80℃或85℃等,但并不仅限于所列举的数值,该数值范围内其他未列举的数值同样适用。优选地,所述二级酸浸釜内的反应温度为75~90℃,例如75℃、78℃、80℃、83℃、85℃、88℃或90℃等,但并不仅限于所列举的数值,该数值范围内其他未列举的数值同样适用。作为本发明优选的技术方案,步骤(2)所述浓缩处理在盐酸吸收单元中的浓缩装置内进行。优选地,步骤(2)所述萃取处理所用的萃取剂为醇类。优选地,所述醇类包括正丁醇、正戊醇或异戊醇中任意一种或至少两种的组合,所述组合典型但非限制性实例有:正丁醇和异戊醇的组合,正戊醇和异戊醇的组合,正丁醇、正戊醇和异戊醇的组合等,优选为正丁醇和异戊醇的组合或正戊醇和异戊醇的组合。优选地,所述萃取剂与步骤(2)所述混合液的体积比为(2~5):1,例如2:1、2.5:1、3:1、3.5:1、4:1、4.5:1或5:1等,但并不仅限于所列举的数值,该数值范围内其他未列举的数值同样适用。优选地,步骤(2)所述萃取处理的级数至少为四级,例如四级、五级、六级或七级等,但并不仅限于所列举的数值,该数值范围内其他未列举的数值同样适用。优选地,步骤(2)所述萃取处理后得到的含磷酸萃取液再经反萃处理得到磷酸。作为本发明优选的技术方案,步骤(2)得到的氯化钙溶液先进行喷雾造粒,得到氯化钙颗粒。优选地,所述喷雾造粒在喷雾造粒塔内进行。优选地,所述喷雾造粒塔的热源为热空气。优选地,所述喷雾造粒塔内的温度为150~200℃,例如150℃、160℃、170℃、180℃、190℃或200℃等,但并不仅限于所列举的数值,该数值范围内其他未列举的数值同样适用。优选地,步骤(3)所述固体渣、氯化钙和钾长石的质量比为1:(4~5):(3~4),例如1:4:3、1:4.5:3、1:5:3、1:4:4、1:4.5:4或1:5:4等,但并不仅限于所列举的数值,该数值范围内其他未列举的数值同样适用。本发明中,磷矿粉反应后剩余的固体渣包括二氧化硅,还有形成的氯化钙颗粒,只采用这两者焙烧,所得产物作为肥料缺乏钾、镁等必需元素,再加入钾长石共同焙烧,由于钾长石中包括二氧化硅、氧化钾和氧化镁等组分,可以生成硅钙钾镁肥,所述硅钙钾镁肥是一种枸溶性缓释肥,肥效损失少,对土壤能起到很好的调理作用,特别适用于弱酸性土壤。优选地,所述造粒在造粒装置内进行。优选地,所述焙烧处理在焙烧装置内进行。优选地,所述焙烧装置内的温度为850~900℃,例如850℃、860℃、870℃、880℃、890℃或900℃等,但并不仅限于所列举的数值,该数值范围内其他未列举的数值同样适用。优选地,所述焙烧装置的燃料为天然气和/或煤气。作为本发明优选的技术方案,步骤(4)所述含hcl烟气依次在浓缩装置内被步骤(1)得到的反应浆液吸收、在盐酸吸收塔内被水吸收。优选地,所述浓缩装置内的吸收液返回二级酸浸釜,盐酸吸收塔内的吸收液返回一级酸浸釜。优选地,所述烟气离开浓缩装置时的温度为85~95℃,例如85℃、86℃、88℃、90℃、92℃或95℃等,但并不仅限于所列举的数值,该数值范围内其他未列举的数值同样适用。优选地,所述净化处理在尾气净化装置内进行。优选地,所述净化处理所用洗涤液为烧碱溶液。优选地,所述洗涤液循环使用至ph值为6~8,例如6、6.5、7、7.5或8等,但并不仅限于所列举的数值,该数值范围内其他未列举的数值同样适用。作为本发明优选的技术方案,所述方法包括以下步骤:(1)将粒径为30~60目的磷矿粉与盐酸混合后分别在一级酸浸釜和二级酸浸釜内发生酸浸反应,所述磷矿粉中cao与盐酸加入量的摩尔比为1:(2.0~2.1),一级酸浸釜内的反应温度为65~85℃,二级酸浸釜内的反应温度为75~90℃,得到反应浆液;(2)将步骤(1)得到的反应浆液先与含hcl烟气接触进行浓缩处理,再进行固液分离,得到氯化钙和磷酸混合液以及固体渣,所得混合液进行萃取处理,以醇类为萃取剂,萃取剂与混合液的体积比为(2~5):1,得到含磷酸萃取液和氯化钙溶液,所述含磷酸萃取液经反萃处理得到磷酸;(3)将步骤(2)得到的氯化钙溶液先在喷雾造粒塔内进行喷雾造粒,喷雾造粒塔内的温度为150~200℃,得到氯化钙颗粒,再将氯化钙颗粒、钾长石、和步骤(2)得到的固体渣以质量比为(4~5):(3~4):1混合进行造粒,然后在焙烧装置内进行焙烧处理,焙烧装置内的温度为850~900℃,得到硅钙钾镁肥和含hcl烟气;(4)将步骤(3)得到的含hcl烟气与步骤(1)得到的反应浆液在浓缩装置内混合吸收hcl,烟气离开浓缩装置时的温度为85~95℃,然后进入盐酸吸收塔进行吸收,所述浓缩装置内的吸收液返回步骤(1)所述二级酸浸釜,盐酸吸收塔内的吸收液返回步骤(1)所述一级酸浸釜,hcl被吸收后的烟气用烧碱溶液进行净化处理后排放。与现有技术相比,本发明具有以下有益效果:(1)本发明通过系统装置间的搭配与连接,利用盐酸处理磷矿粉生产磷酸和硅钙钾镁肥,所得磷酸经净化提纯后的纯度高达85%以上,所用盐酸可以再生循环利用,尾气中hcl含量低于10ppm;(2)本发明工艺过程无固液废弃物产生,也无传统磷化工副产物磷石膏的产生,为湿法磷酸清洁生产工艺。附图说明图1是本发明实施例1提供的由磷矿制备磷酸和硅钙钾镁肥系统的装置连接示意图;图2是本发明实施例4提供的由磷矿制备磷酸和硅钙钾镁肥方法的工艺流程图;其中,1-一级酸浸釜,2-二级酸浸釜,3-固液分离装置,4-萃取装置,5-喷雾造粒塔,6-混合装置,7-造粒装置,8-提升机,9-焙烧装置,10-浓缩装置,11-盐酸吸收塔,12-风机,13-尾气净化装置。具体实施方式为更好地说明本发明,便于理解本发明的技术方案,下面对本发明以具体实施方式进一步详细说明。但下述的实施例仅仅是本发明的简易例子,并不代表或限制本发明的权利保护范围,本发明保护范围以权利要求书为准。本发明所用原料包括磷矿粉和钾长石,所得产物为磷酸和硅钙钾镁肥,其中,磷矿粉来自贵州开磷集团,其主要组分组成表1所示;表1磷矿粉主要组分组成表成分caop2o5sio2al2o3mgofe2o3f其他组成(wt%)45-5125-3510-131.0-3.51.5-2.51.5-2.02.0-3.02.0-3.5所用钾长石来自贵州福泉,其主要组分组成表2所示;表2钾长石主要组分组成表成分sio2k2ona2oal2o3mgofe2o3cao其他组成(wt%)60-6312-150.3-0.515-170.5-1.01.0-2.02.0-3.02.0-3.0工业磷酸国家标准gb/t2091-2008的技术指标如表3所示。表3工业磷酸的技术指标以下为本发明典型但非限制性实施例:实施例1:本实施例提供了一种由磷矿制备磷酸和硅钙钾镁肥的系统,所述系统的装置连接示意图如图1所示,包括酸浸单元、固液分离装置3、萃取装置4、造粒单元、焙烧装置9、盐酸吸收单元和尾气净化装置13;所述酸浸单元的液体出口分别与固液分离装置3和盐酸吸收单元的液体入口相连,所述固液分离装置3的液体出口与萃取装置4的液体入口相连,所述萃取装置4的萃取液出口得到磷酸,所述萃取装置4的萃余液出口和固液分离装置3的固体出口均与造粒单元相连,所述造粒单元的固体出口与焙烧装置9的固体入口相连,所述焙烧装置9的固体出口得到硅钙钾镁肥,所述焙烧装置9的气体出口与盐酸吸收单元的气体入口相连,所述盐酸吸收单元的液体出口与酸浸单元的液体入口相连,所述盐酸吸收单元的气体出口与尾气净化装置13的气体入口相连。其中,所述固液分离装置3为压滤机;所述萃取装置4为混合澄清槽;所述焙烧装置9包括回转窑。所述酸浸单元包括一级酸浸釜1和二级酸浸釜2,所述一级酸浸釜1的液体出口与二级酸浸釜2的液体入口相连。所述造粒单元包括喷雾造粒塔5和造粒装置7,所述喷雾造粒塔5的入口与萃取装置4的萃余液出口相连,所述喷雾造粒塔5的固体出口和固液分离装置3的固体出口均与造粒装置7的固体入口相连;所述造粒装置7为圆盘造粒机。所述造粒单元还包括混合装置6,所述喷雾造粒塔5的固体出口和固液分离装置3的固体出口均与混合装置6相连,所述混合装置6的固体出口与造粒装置7相连。所述盐酸吸收单元包括浓缩装置10和盐酸吸收塔11,所述浓缩装置10的气体入口与焙烧装置9的气体出口相连,所述浓缩装置10的气体出口与盐酸吸收塔11的气体入口相连,所述盐酸吸收塔11的气体出口与尾气净化装置13的气体入口相连,所述浓缩装置10的液体出口与二级酸浸釜2的液体入口相连,所述盐酸吸收塔11的液体出口与一级酸浸釜1的液体入口相连。所述一级酸浸釜1和二级酸浸釜2之间、二级酸浸釜2和固液分离装置3之间、萃取装置4和喷雾造粒塔5之间、尾气净化装置13的底部和顶部之间均设有泵;所述造粒装置7和焙烧装置9之间设有提升机8;所述盐酸吸收塔11和尾气净化装置13之间设有风机12。本实施例中,按照所述系统可以制备得到磷酸和硅钙钾镁肥,工艺过程主要为:首先,磷矿粉和盐酸在酸浸釜内混合发生酸浸反应,采用两级酸浸,同时反应过程中将反应浆液与焙烧装置9产生的烟气在浓缩装置10内混合接触,可以浓缩反应浆液,吸收hcl补充盐酸,从而提高磷矿粉的转化率;其次,酸浸反应后固液分离,氯化钙与磷酸的混合液进行萃取处理得到磷酸和氯化钙溶液,氯化钙溶液喷雾造粒得到氯化钙颗粒,再与酸浸固体渣、钾长石混合造粒后进行焙烧,得到硅钙钾镁肥,同时产生的烟气中的hcl依次在浓缩装置10、盐酸吸收塔11内被吸收,得到的盐酸返回酸浸釜,实现盐酸循环,最后烟气净化处理后排放。实施例2:本实施例提供了一种由磷矿制备磷酸和硅钙钾镁肥的系统,所述系统参照实施例1,区别仅在于:所述酸浸单元仅包括一级酸浸釜1,所述一级酸浸釜1的液体出口分别与固液分离装置3和盐酸吸收单元的液体入口相连,所述浓缩装置10的液体出口和盐酸吸收塔11的液体出口均与一级酸浸釜1的液体入口相连。本实施例中,所述系统的工艺运行过程基本与实施例1相同,其中只采用一个酸浸釜,酸浸反应达到相同转化率所需的时间延长,影响酸浸单元与后续单元的连贯性,从而不利于整个系统装置的连续运行,系统的运行效率有所降低。实施例3:本实施例提供了一种由磷矿制备磷酸和硅钙钾镁肥的系统,所述系统参照实施例1,区别仅在于:所述盐酸吸收单元不包括浓缩装置10,所述二级酸浸釜2的液体出口只与固液分离装置3相连,所述焙烧装置9的气体出口直接与盐酸吸收塔11的气体入口相连。本实施例中,所述系统的工艺运行过程基本与实施例1相同,但由于未设置浓缩装置10,即不将反应浆液用焙烧产生的烟气浓缩,磷矿粉达到相同转化率所需时间延长,烟气中的hcl基本需要由盐酸吸收塔11吸收,所需的装置和材料成本也相应提高,整个系统的运行效率降低。实施例4:本实施例提供了一种由磷矿制备磷酸和硅钙钾镁肥的方法,所述方法采用实施例1中的系统进行,所述方法的工艺流程图如图2所示,包括以下步骤:(1)将粒径为30目的磷矿粉2000kg和水500kg加入到一级酸浸釜1内,其中磷矿粉中p2o5含量为25wt%,氧化钙含量为51wt%,搅拌化浆,再加入36wt%盐酸3693kg和水,使得反应釜中盐酸的浓度为18wt%,此时氧化钙与氯化氢的摩尔比为1:2.0,发生一级酸浸反应,反应时间为30min,反应温度为65℃;将反应后溶液送入二级酸浸釜2,再加入粒径为40目的磷矿粉2000kg,其中p2o5含量为31wt%,氧化钙含量为49wt%,所述浓缩装置10的返回液中盐酸浓度为20wt%,温度为40℃,盐酸质量为6515kg,此时氧化钙与氯化氢的摩尔比为1:2.04,二级酸浸反应的时间为20min,反应温度为75℃,得到反应浆液;(2)将步骤(1)得到的反应浆液进行固液分离,得到氯化钙和磷酸混合液以及固体渣,所得混合液以正丁醇与异戊醇的混合醇为萃取剂进行萃取处理,萃取剂与混合液的体积比为2:1,得到含磷酸萃取液和氯化钙溶液,所述含磷酸萃取液经反萃处理得到质量含量为12.5wt%的稀磷酸10400kg,所得稀磷酸经多效蒸发回收盐酸和萃取剂,得到浓磷酸1500kg;(3)步骤(2)得到氯化钙溶液15750kg,其中氯化钙含量为25.1wt%,先在喷雾造粒塔5内在150℃条件下进行喷雾造粒,得到含水氯化钙颗粒4920kg,氯化钙含量为80.0wt%,步骤(2)得到的固体渣为860kg,其中含水为30.0wt%,将上述固体渣860kg、氯化钙颗粒3440kg和钾长石2580kg混合进行造粒,然后在焙烧装置9内850℃条件下进行焙烧处理,得到硅钙钾镁肥4570kg和含hcl烟气;(4)将步骤(3)得到的含hcl烟气与步骤(1)中反应过程的浆液在浓缩装置10内混合吸收hcl,烟气离开浓缩装置10时的温度为85℃,浓缩后的浆液返回二级酸浸釜2,然后烟气进入盐酸吸收塔11进行吸收,所得吸收液返回一级酸浸釜1,剩余烟气用10wt%烧碱溶液进行净化处理后达标排放,烟气处理后所用净化液ph为6.0。本实施例中,步骤(2)所得产物磷酸的组成如表4所示,其各项技术指标均优于表3中国家标准85%磷酸的各项指标,所得磷酸为高纯磷酸;步骤(3)所得产物硅钙钾镁肥的组成如表5所示;步骤(4)净化后的烟气中氯化氢含量低于10ppm。表4实施例4所得磷酸的组成表5实施例4所得硅钙钾镁肥的组成成分sio2k2oal2o3mgofe2o3cao其他组成(wt%)44.86.89.82.22.031.52.9本实施例中,经计算单程磷酸收率为85%,这是因为在蒸发过程中一部分磷酸以磷酸蒸汽形式与水和游离hcl一起蒸出,该部分磷酸可通过浓缩装置10加以回收,另一部分磷酸存在于氯化钙溶液和固体渣中,通过焙烧处理进入烟气中,与hcl共同回收后返回酸浸,故系统内的磷理论上无损失,循环总收率为100%。实施例5:本实施例提供了一种由磷矿制备磷酸和硅钙钾镁肥的方法,所述方法采用实施例1中的系统进行,所述方法包括以下步骤:(1)将粒径为40目的磷矿粉2000kg加入到一级酸浸釜1内,其中磷矿粉中p2o5含量为27wt%,氧化钙含量为50wt%,加入来自盐酸吸收塔11的盐酸6269.5kg,反应釜中盐酸的浓度为21wt%,此时氧化钙与氯化氢的摩尔比为1:2.02,发生一级酸浸反应,反应时间为30min,反应温度为75℃;将反应后溶液送入二级酸浸釜2,再加入粒径为50目的磷矿粉2000kg,其中p2o5含量为33wt%,氧化钙含量为48wt%,所述浓缩装置10的返回液中盐酸浓度为22wt%,温度为50℃,盐酸质量为5858.9kg,此时氧化钙与氯化氢的摩尔比为1:2.06,二级酸浸反应的时间为20min,反应温度为80℃,得到反应浆液;(2)将步骤(1)得到的反应浆液进行固液分离,得到氯化钙和磷酸混合液以及固体渣,所得混合液以正戊醇与异戊醇的混合醇为萃取剂进行萃取处理,萃取剂与混合液的体积比为3:1,得到含磷酸萃取液和氯化钙溶液,所述含磷酸萃取液经反萃处理得到质量含量为15.1wt%的稀磷酸9800kg,所得稀磷酸经多效蒸发回收盐酸和萃取剂,得到浓磷酸1735kg;(3)步骤(2)得到氯化钙溶液15050kg,其中氯化钙含量为25.8wt%,先在喷雾造粒塔5内在180℃条件下进行喷雾造粒,得到含水氯化钙颗粒4550kg,氯化钙含量为85.0wt%,步骤(2)得到的固体渣为850kg,其中含水为29.8wt%,将上述固体渣850kg、氯化钙颗粒3400kg和钾长石3400kg混合进行造粒,然后在焙烧装置9内870℃条件下进行焙烧处理,得到硅钙钾镁肥5450kg和含hcl烟气;(4)将步骤(3)得到的含hcl烟气与步骤(1)中反应过程的浆液在浓缩装置10内混合吸收hcl,烟气离开浓缩装置10时的温度为90℃,浓缩后的浆液返回二级酸浸釜2,然后烟气进入盐酸吸收塔11进行吸收,所得吸收液返回一级酸浸釜1,剩余烟气用10wt%烧碱溶液进行净化处理后达标排放,烟气处理后所用净化液ph为7.0。本实施例中,步骤(2)所得产物磷酸的组成如表6所示,其各项技术指标均优于表3中国家标准85%磷酸的各项指标,所得磷酸为高纯磷酸;步骤(3)所得产物硅钙钾镁肥的组成如表7所示;步骤(4)净化后的烟气中氯化氢含量低于7ppm。本实施例中,经计算单程磷酸收率为89%,但整个系统内的磷理论上无损失,循环总收率为100%。表6实施例5所得磷酸的组成表7实施例5所得硅钙钾镁肥的组成成分sio2k2oal2o3mgofe2o3cao其他组成(wt%)47.19.49.72.52.328.30.7实施例6:本实施例提供了一种由磷矿制备磷酸和硅钙钾镁肥的方法,所述方法采用实施例1中的系统进行,所述方法包括以下步骤:(1)将粒径为60目的磷矿粉2000kg加入到一级酸浸釜1内,其中磷矿粉中p2o5含量为29wt%,氧化钙含量为50wt%,加入来自盐酸吸收塔11的盐酸7135.3kg,反应釜中盐酸的浓度为19wt%,此时氧化钙与氯化氢的摩尔比为1:2.08,发生一级酸浸反应,反应时间为30min,反应温度为85℃;将反应后溶液送入二级酸浸釜2,再加入粒径为60目的磷矿粉2000kg,其中p2o5含量为33wt%,氧化钙含量为47wt%,所述浓缩装置10的返回液中盐酸浓度为22wt%,温度为55℃,盐酸质量为5848.3kg,此时氧化钙与氯化氢的摩尔比为1:2.1,二级酸浸反应的时间为20min,反应温度为90℃,得到反应浆液;(2)将步骤(1)得到的反应浆液进行固液分离,得到氯化钙和磷酸混合液以及固体渣,所得混合液以正丁醇与异戊醇的混合醇为萃取剂进行萃取处理,萃取剂与混合液的体积比为5:1,得到含磷酸萃取液和氯化钙溶液,所述含磷酸萃取液经反萃处理得到质量含量为13.8wt%的稀磷酸11280kg,所得稀磷酸经多效蒸发回收盐酸和萃取剂,得到浓磷酸1832kg;(3)步骤(2)得到氯化钙溶液15080kg,其中氯化钙含量为25.5wt%,先在喷雾造粒塔5内在200℃条件下进行喷雾造粒,得到含水氯化钙颗粒4355kg,氯化钙含量为88.2wt%,步骤(2)得到的固体渣为870kg,其中含水为30.3wt%,将上述固体渣870kg、氯化钙颗粒4350kg和钾长石3480kg混合进行造粒,然后在焙烧装置9内900℃条件下进行焙烧处理,得到硅钙钾镁肥6020kg和含hcl烟气;(4)将步骤(3)得到的含hcl烟气与步骤(1)中反应过程的浆液在浓缩装置10内混合吸收hcl,烟气离开浓缩装置10时的温度为95℃,浓缩后的浆液返回二级酸浸釜2,然后烟气进入盐酸吸收塔11进行吸收,所得吸收液返回一级酸浸釜1,剩余烟气用10wt%烧碱溶液进行净化处理后达标排放,烟气处理后所用净化液ph为8.0。本实施例中,步骤(2)所得产物磷酸的组成如表8所示,其各项技术指标均优于表3中国家标准85%磷酸的各项指标,所得磷酸为高纯磷酸;步骤(3)所得产物硅钙钾镁肥的组成如表9所示;步骤(4)净化后的烟气中氯化氢含量低于5ppm。本实施例中,经计算单程磷酸收率为91%,但整个系统内的磷理论上无损失,循环总收率为100%。表8实施例6所得磷酸的组成表9实施例6所得硅钙钾镁肥的组成成分sio2k2oal2o3mgofe2o3cao其他组成(wt%)42.78.89.61.91.833.31.9综合上述实施例可以看出,本发明通过系统装置间的搭配与连接,利用盐酸处理磷矿粉生产磷酸和硅钙钾镁肥,所得磷酸的纯度高达85%以上,所用盐酸可以再生循环利用,尾气中hcl含量低于10ppm;所述工艺方法无固液废弃物产生,也无传统磷化工副产物磷石膏的产生,为湿法磷酸清洁生产工艺,为磷矿的综合利用提供了一条新途径。申请人声明,本发明通过上述实施例来说明本发明的详细系统与工艺方法,但本发明并不局限于上述详细系统与方法,即不意味着本发明必须依赖上述详细系统与方法才能实施。所属
技术领域:
的技术人员应该明了,对本发明的任何改进,对本发明系统装置和工艺方法的等效替换及辅助装置、成分的添加、具体方式的选择等,均落在本发明的保护范围和公开范围之内。当前第1页12