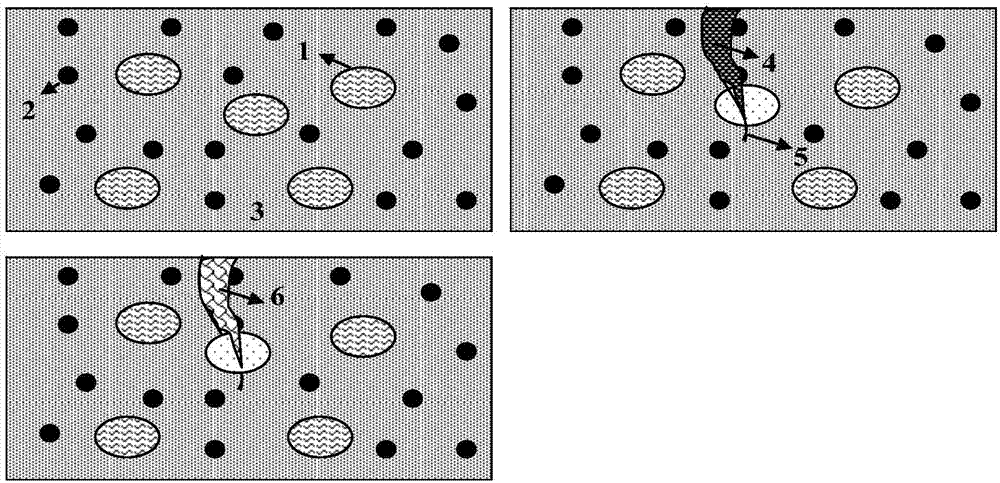
本发明属于功能高分子复合材料制备
技术领域:
,尤其涉及一种微胶囊自修复碳纤维复合材料汽车件及其制备方法。
背景技术:
:碳纤维复合材料具有比强度和比模量高、质轻、耐腐蚀、耐疲劳、热膨胀系数小等优异的特点而使其在汽车工业中得到应用。但是,碳纤维复合材料在使用过程中及周围环境温度、湿度等因素作用下,不可避免地会产生局部损伤和微裂纹,导致力学性能下降或功能丧失。肉眼能发现的分层或由冲击所导致的宏观裂纹可通过手工修复,而树脂基体裂纹往往在本体深处出现,如基体微开裂等微观范围的损伤就很难被发现。如果当材料发生破坏时会有胶粘剂随之释放出来,将材料微裂纹粘合在一起,阻止材料进一步破坏和力学性能下降,这样可解决复合材料修复问题。鉴于此,高分子自修复材料随之诞生,其自修复功能是通过在树脂基体中埋植含有修复剂的微胶囊来实现,在外力作用下,裂纹附近的微胶囊破裂,在毛细管力作用下修复剂迅速渗透微裂纹,在催化剂或固化剂作用下发生聚合反应,将裂纹粘接在一起,从而实现复合材料修复。发明专利cn104877309a公开了一种基于表面改性微胶囊化的自修复复合材料及其制备方法,该方法分别将环氧树脂和固化剂微胶囊化并埋植于复合材料树脂基体中,其微胶囊囊壁材料为脲醛树脂或密胺树脂,气味较大,存在游离甲醛,不适于汽车件气味性要求;发明专利cn103694635a公开了一种基于微胶囊化的环氧树脂及超强酸固化剂的室温快速自修复复合材料,固化剂与环氧树脂分别进行微胶囊化,制备工艺需要采用-80℃超低温环境,工艺复杂,难以实现应用,且所采用超强酸五氟化砷等具有毒性,对人身健康及环境不利。技术实现要素:为解决上述技术问题,本发明提供了一种自修复碳纤维复合材料件及其制备方法,结合脲醛树脂和三聚氰胺甲醛树脂的优点,采用脲、三聚氰胺、甲醛混合制备改性脲醛树脂微胶囊体系,得到耐候、耐水性好,安全环保、修复率高的微胶囊自修复体系。本发明采取的技术方案为:一种自修复碳纤维复合材料件的制备方法,所述制备方法包括以下步骤:(1)制备微胶囊;(2)将微胶囊分散于环氧树脂中,并加入潜伏性固化剂或催化剂,50~60℃加热反应30~60分钟,再加入环氧树脂固化剂,搅拌均匀,得到混合树脂;(3)将步骤(2)得到的混合树脂固化即可制得自修复碳纤维复合材料件。所述微胶囊的制备方法为:(1-1)将脲、三聚氰胺、甲醛按照质量比1.67~2.86:1:8.37~10.94搅拌混合均匀,在碱性条件下加热反应1~2小时,加入混合溶液质量的0.81~4.4倍的水稀释,得到溶液一;(1-2)将囊芯和水按照质量比1:4~6的比例混合,得到混合溶液,然后加入乳化剂搅拌混合,乳化1~2小时,乳化后加入消泡剂,静置10~50分钟,得到溶液二;(1-3)将溶液一与溶液二混合,其中溶液一与溶液二的质量比为0.66~0.93:1,室温下搅拌混合均匀,然后加入稀酸调节溶液ph值为3.5~5.0,升温至45~60℃搅拌反应1.5~3小时,得到溶液三;(1-4)将溶液三分离,洗涤,干燥,得到微胶囊。所述步骤(1-1)中:所述甲醛为质量百分比为37%的甲醛水溶液;所述搅拌采用磁力搅拌,其转速为300~1200转/分钟,搅拌时间为5~15分钟;所述碱性条件为ph值8~9,采用三乙醇胺或1~10wt%的na2co3溶液或naoh溶液进行ph值调节;所述加热反应的条件为:先以1.5~3℃/分钟的速度缓慢加热至65℃~85℃,并在恒定温度65℃~85℃下加热1~2小时;所述水为去离子水或蒸馏水。所述步骤(1-2)中:所述囊芯为苯乙烯、环氧树脂或双环戊二烯;所述乳化剂的重量是混合溶液重量的0.5~1.5%;所述乳化剂为十二烷基苯磺酸钠、十二烷基硫酸钠、span-80、tween-80、op-10、阿拉伯树胶、苯乙烯马来酸酐共聚物中的一种或两种及以上的混合物,优选为十二烷基苯磺酸钠、span-80、tween-80和阿拉伯树胶。所述消泡剂的重量是混合溶液重量的0.01~0.10%;所述消泡剂为高碳醇类消泡剂,优选c7~c9的醇,如正辛醇、异辛醇;所述溶液二为水包油型乳化液;所述水为去离子水或蒸馏水;所述搅拌为磁力搅拌或无级电机带动搅拌,搅拌速度300~600转/分钟。所述步骤(1-3)中:所述搅拌的速度为300~600转/分钟;所述稀酸为浓度为5~10%的盐酸溶液或硫酸溶液;所述升温是指升温速率为1.5~3℃/分钟。所述步骤(1-4)中:所述微胶囊的粒径为20~220μm;所述分离是指离心分离、过滤常规分离方法;所述洗涤所用溶剂为去离子水、蒸馏水、乙醇、丙酮中的一种或几种;所述干燥为50~60℃烘箱干燥、50~60℃真空干燥箱干燥,或者冷冻干燥机干燥,干燥时间30~90分钟。所述步骤(2)中,所述微胶囊的重量为环氧树脂重量的1~6%;所述潜伏性固化剂的重量为环氧树脂重量的1~4%;所述催化剂的重量为环氧树脂重量的6~15%;所述环氧树脂固化剂的重量为微胶囊、环氧树脂和潜伏性固化剂三者重量之和的10~40%,或者,所述环氧树脂固化剂的重量为微胶囊、环氧树脂和催化剂三者重量之和的10~40%。所述环氧树脂为5222环氧树脂、3234环氧树脂、5224环氧树脂和5228环氧树脂中的一种。所述环氧树脂固化剂为脂肪胺类、芳香胺类、改性胺类和酸酐类固化剂中的一种。所述脂肪胺类固化剂优选为二乙撑三胺或三乙撑四胺;所述芳香胺类固化剂优选为苯二甲胺、间苯二甲胺或二氨基二苯基甲烷;所述改性胺类固化剂优选为120固化剂、593固化剂或703固化剂;所述酸酐类固化剂优选为顺丁烯二酸酐、邻苯二甲酸酐或十二烯基琥珀酸酐。所述潜伏性固化剂为咪唑类衍生物、三氯化硼-单乙胺络合物、双氰胺、癸二酸二酰肼中的一种;所述催化剂为苯基亚甲基双(三环己基磷)二氯化钌。所述步骤(3)中,固化的温度为80~120℃,固化时间为1~3小时。所述步骤(3)进一步包括,用洁模溶剂清洁模具面,洁模后擦涂脱模剂,除去多余的脱模剂后按照一定的铺层角度铺叠碳布,然后合模,注入步骤(2)得到的产物,在80~120℃下加热1~3小时固化,固化后得到具有自修复功能的碳纤维复合材料件。所述洁模溶剂为无水乙醇、丙酮、乙醚等有机溶剂中的一种或两种及以上;所用脱模剂为脱模蜡。本发明还提供了一种根据上述制备方法制备得到的自修复碳纤维复合材料件。本发明采用改性脲醛树脂为囊壁,以苯乙烯、环氧树脂、双环戊二烯为芯材,制备平均粒径为20~220μm的微胶囊,将微胶囊和催化剂或潜伏性固化剂分散于热固性树脂基体中,采用该分散有微胶囊和催化剂或潜伏性固化剂的树脂制备碳纤维复合材料件。采用该方法制备的碳纤维复合材料件具有可自动修复树脂基体微裂纹功效,无需传统的复杂修复工艺,可室温下自动修复。相对于现有技术,本发明具备以下优点:本发明采用苯乙烯、环氧树脂或双环戊二烯为囊芯,将囊芯和固化剂或催化剂埋植于碳纤维复合材料树脂基体中,得到可室温下具有自修复能力的复合材料件。当该复合材料件受到损伤出现微裂纹时,微胶囊破裂并释放出囊芯修复材料,囊芯修复材料在毛细管力作用下快速渗透微裂纹,并与固化剂或催化剂接触,进而触发聚合反应,囊芯修复材料在微裂纹处形成高度交联的聚合物,实现微裂纹修复,修复率在70%以上。附图说明图1自修复碳纤维复合材料件制备流程;图2自修复碳纤维复合材料件的自修复示意图,1-微胶囊;2-潜伏性固化剂或催化剂;3-树脂基体;4-芯材;5-微裂纹;6-修复后的高度交联树脂。具体实施方式下面结合实施例1~6对本发明进行详细说明。本发明所用的各原料的型号及生产厂家如表1所示。表1原料及生产厂家实施例1一种自修复碳纤维复合材料件的制备方法,包括以下步骤:(1)制备微胶囊(1-1)将脲、三聚氰胺和甲醛按照质量比1.67:1:9.65混合,得到混合溶液,然后采用磁力搅拌在1200转/分钟下搅拌5分钟,搅拌后,向溶液中滴加三乙醇胺,控制溶液ph值在8.3,然后以1.5℃/分钟的加热速率缓慢加热,并在恒定温度65℃加热2小时,然后向其中加入去离子水进行稀释,去离子水加入量为混合溶液质量的0.81倍,冷却至室温后得到溶液一;(1-2)将苯乙烯、去离子水按照1:4的比例混合成混合液,然后加入0.5%混合液重量的十二烷基苯磺酸钠,在300转/分钟的搅拌速度下搅拌1.5小时,然后加入占混合溶液总重量百分比为0.015%的正辛醇消泡,静置10分钟后得到溶液二;(1-3)将上述溶液一和溶液二按照质量比0.66:1混合,并在室温下以300转/分钟的转速搅拌,搅拌均匀后,加入5wt%的硫酸调节溶液ph值至5.0,然后在持续搅拌的情况下,以1.5℃/分钟的升温速率缓慢升温至50℃,并在此温度下持续反应3小时,得到溶液三;(1-4)将溶液三离心分离、丙酮洗涤后再次离心分离,分离产物在50℃烘箱中干燥60分钟,得到平均粒径为120μm的微胶囊;(2)将所得微胶囊加入碳纤维复合材料制备所用的5222环氧树脂中,分散均匀,然后加入苯基亚甲基双(三环己基磷)二氯化钌,分散均匀,得到混合物;所述微胶囊的重量为环氧树脂重量的1%;苯基亚甲基双(三环己基磷)二氯化钌的重量为环氧树脂重量的6%;然后将该混合物在50℃下加热60分钟,再加入二乙撑三胺,混合物与二乙撑三胺的质量比为100:11,搅拌均匀;(3)分别用无水乙醇和丙酮对模具面进行清洁,待溶剂完全挥发后涂脱模蜡,并用无纺布将多余脱模蜡擦去,然后将裁剪好的碳布按照设计的铺层方式[(±45)/(±45)/(±45)/(±45)]进行铺叠,合模,然后将步骤(2)得到的产物注入模具中,在100℃下加热1小时固化,固化后,按照gb/t1451-2005《纤维增强塑料简支梁式冲击韧性试验方法》中规定的方法进行制样和冲击韧性测试,冲击后得到空白样的冲击韧性,然后将冲击后的试样夹紧固定,室温下放置24小时后再次进行冲击试验,得到的冲击韧性与空白样冲击韧性的比值为修复率。本实施例所得自修复复合材料的自修复率达到78%。实施例2一种自修复碳纤维复合材料件的制备方法,包括以下步骤:(1)制备微胶囊(1-1)将脲、三聚氰胺和甲醛按照质量比1.90:1:8.37混合,得到混合溶液,然后采用磁力搅拌在1000转/分钟下搅拌8分钟,搅拌后,向溶液中滴加1wt%naoh溶液,控制溶液ph值在8.0,然后以2℃/分钟的加热速率缓慢加热,并在恒定温度70℃加热2小时,然后向其中加入去离子水进行稀释,去离子水加入量为混合溶液质量的1倍,冷却至室温后得到溶液一;(1-2)将苯乙烯、去离子水按照1:4的比例混合成混合液,然后加入1.0%混合液重量的span-80,在500转/分钟的搅拌速度下搅拌1.5小时,然后加入占混合溶液总重量百分比为0.01%的正辛醇消泡,静置30分钟后得到溶液二;(1-3)将上述溶液一和溶液二按照质量比0.8:1混合,并在室温下以500转/分钟的转速搅拌,搅拌均匀后,加入10wt%的硫酸调节溶液ph值至5.0,然后在持续搅拌的情况下,以2℃/分钟的升温速率缓慢升温至60℃,并在此温度下持续反应2.5小时,得到溶液三;(1-4)将溶液三离心分离、分别用乙醇和丙酮洗涤后再次离心分离,分离产物在60℃烘箱中干燥40分钟,得到平均粒径为145μm的微胶囊;(2)将所得微胶囊加入碳纤维复合材料制备所用的3234环氧树脂中,分散均匀,然后加入苯基亚甲基双(三环己基磷)二氯化钌,分散均匀,得到混合物;所述微胶囊的重量为环氧树脂重量的2%;苯基亚甲基双(三环己基磷)二氯化钌的重量为环氧树脂重量的10%;然后将该混合物在60℃下加热30分钟,再加入间苯二甲胺,混合物与间苯二甲胺的质量比为100:15,搅拌均匀;(3)用丙酮对模具面进行清洁,待溶剂完全挥发后涂脱模蜡,并用无纺布将多余脱模蜡擦去,然后将裁剪好的碳布按照设计的铺层方式[(±45)/(±45)/(±45)/(±45)]进行铺叠,合模,然后将步骤(2)得到的产物注入模具中,在120℃下加热3小时固化,固化后,按照gb/t1451-2005《纤维增强塑料简支梁式冲击韧性试验方法》中规定的方法进行制样和冲击韧性测试,冲击后得到空白样的冲击韧性,然后将冲击后的试样夹紧固定,室温下放置24小时后再次进行冲击试验,得到的冲击韧性与空白样冲击韧性的比值为修复率。本实施例所得自修复复合材料的自修复率达到85%。实施例3一种自修复碳纤维复合材料件的制备方法,包括以下步骤:(1)制备微胶囊(1-1)将脲、三聚氰胺和甲醛按照质量比2.38:1:8.37混合,得到混合溶液,然后采用磁力搅拌在800转/分钟下搅拌10分钟,搅拌后,向溶液中滴加10wt%na2co3溶液,控制溶液ph值在9,然后以3℃/分钟的加热速率缓慢加热,并在恒定温度70℃加热1小时,然后向其中加入去离子水进行稀释,去离子水加入量为混合溶液质量的2倍,冷却至室温后得到溶液一;(1-2)将双环戊二烯、去离子水按照1:5的比例混合成混合液,然后加入1.0%混合液重量的阿拉伯树胶与tween-80的混合乳化剂,阿拉伯树胶与tween-80质量比为3:1,在450转/分钟的搅拌速度下搅拌1.5小时,然后加入占混合溶液总重量百分比为0.03%的正辛醇消泡,静置30分钟后得到溶液二;(1-3)将上述溶液一和溶液二按照质量比0.93:1混合,并在室温下以500转/分钟的转速搅拌,搅拌均匀后,加入8wt%的硫酸调节溶液ph值至5.0,然后在持续搅拌的情况下,以2℃/分钟的升温速率缓慢升温至60℃,并在此温度下持续反应2.5小时,得到溶液三;(1-4)将溶液三离心分离、用丙酮洗涤后再次离心分离,分离产物在50℃真空干燥烘箱中干燥30分钟,得到平均粒径为195μm的微胶囊;(2)将所得微胶囊加入碳纤维复合材料制备所用的5224环氧树脂中,分散均匀,然后加入苯基亚甲基双(三环己基磷)二氯化钌,分散均匀,得到混合物;所述微胶囊的重量为环氧树脂重量的1.8%;苯基亚甲基双(三环己基磷)二氯化钌的重量为环氧树脂重量的15%;然后将该混合物在50℃下加热50分钟,再加入793固化剂,混合物与793固化剂的质量比为100:30,搅拌均匀;(3)用丙酮对模具面进行清洁,待溶剂完全挥发后涂脱模蜡,并用无纺布将多余脱模蜡擦去,然后将裁剪好的碳布按照设计的铺层方式[(±45)/(±45)/(±45)/(±45)]进行铺叠,合模,然后将步骤(2)得到的产物注入模具中,在90℃下加热3小时固化,固化后,按照gb/t1451-2005《纤维增强塑料简支梁式冲击韧性试验方法》中规定的方法进行制样和冲击韧性测试,冲击后得到空白样的冲击韧性,然后将冲击后的试样夹紧固定,室温下放置24小时后再次进行冲击试验,得到的冲击韧性与空白样冲击韧性的比值为修复率。本实施例所得自修复复合材料的自修复率达到89%。实施例4一种自修复碳纤维复合材料件的制备方法,包括以下步骤:(1)制备微胶囊(1-1)将脲、三聚氰胺和甲醛按照质量比2.38:1:10.94混合,得到混合溶液,然后采用磁力搅拌在300转/分钟下搅拌15分钟,搅拌后,向溶液中滴加三乙醇胺,控制溶液ph值在8.3,然后以2.5℃/分钟的加热速率缓慢加热,并在恒定温度75℃加热1.5小时,然后向其中加入蒸馏水进行稀释,蒸馏水加入量为混合溶液质量的3倍,冷却至室温后得到溶液一;(1-2)将e-51环氧树脂、去离子水按照1:6的比例混合成混合液,然后加入0.5%混合液重量的阿拉伯树胶与span-80的混合乳化剂,阿拉伯树胶与span-80质量比为2.5:1,在500转/分钟的搅拌速度下搅拌1.5小时,然后加入占混合溶液总重量百分比为0.05%的异辛醇消泡,静置30分钟后得到溶液二;(1-3)将上述溶液一和溶液二按照质量比0.93:1混合,并在室温下以500转/分钟的转速搅拌,搅拌均匀后,加入8wt%的盐酸调节溶液ph值至4.2,然后在持续搅拌的情况下,以2.5℃/分钟的升温速率缓慢升温至50℃,并在此温度下持续反应2.5小时,得到溶液三;(1-4)将溶液三离心分离、用丙酮洗涤后再次离心分离,分离产物在50℃真空干燥烘箱中干燥30分钟,得到平均粒径为20μm的微胶囊;(2)将所得微胶囊加入碳纤维复合材料制备所用的5228环氧树脂中,分散均匀,然后加入咪唑类衍生物2mz-azine,分散均匀,得到混合物;所述微胶囊的重量为环氧树脂重量的1.5%;咪唑类衍生物2mz-azine的重量为环氧树脂重量的4%;然后将该混合物在50℃下加热40分钟,再加入793固化剂,混合物与793固化剂的质量比为100:30,搅拌均匀;(3)用丙酮对模具面进行清洁,待溶剂完全挥发后涂脱模蜡,并用无纺布将多余脱模蜡擦去,然后将裁剪好的碳布按照设计的铺层方式[(±45)/(±45)/(±45)/(±45)]进行铺叠,合模,然后将步骤(2)得到的产物注入模具中,在90℃下加热3小时固化,固化后,按照gb/t1451-2005《纤维增强塑料简支梁式冲击韧性试验方法》中规定的方法进行制样和冲击韧性测试,冲击后得到空白样的冲击韧性,然后将冲击后的试样夹紧固定,室温下放置24小时后再次进行冲击试验,得到的冲击韧性与空白样冲击韧性的比值为修复率。本实施例所得自修复复合材料的自修复率达到85%。实施例5一种自修复碳纤维复合材料件的制备方法,包括以下步骤:(1)制备微胶囊(1-1)将脲、三聚氰胺和甲醛按照质量比2.86:1:8.37混合,得到混合溶液,然后采用磁力搅拌在400转/分钟下搅拌15分钟,搅拌后,向溶液中滴加三乙醇胺,控制溶液ph值在8.6,然后以2.0℃/分钟的加热速率缓慢加热,并在恒定温度85℃加热1.0小时,然后向其中加入蒸馏水进行稀释,蒸馏水加入量为混合溶液质量的2.5倍,冷却至室温后得到溶液一;(1-2)将5222环氧树脂、去离子水按照1:4的比例混合成混合液,然后加入1.3%混合液重量的阿拉伯树胶与十二烷基苯磺酸钠的混合乳化剂,阿拉伯树胶与十二烷基苯磺酸钠的质量比为2.5:1,在500转/分钟的搅拌速度下搅拌1.5小时,然后加入占混合溶液总重量百分比为0.08%的异辛醇消泡,静置30分钟后得到溶液二;(1-3)将上述溶液一和溶液二按照质量比0.85:1混合,并在室温下以500转/分钟的转速搅拌,搅拌均匀后,加入7wt%的盐酸调节溶液ph值至4.2,然后在持续搅拌的情况下,以2.0℃/分钟的升温速率缓慢升温至50℃,并在此温度下持续反应2.5小时,得到溶液三;(1-4)将溶液三离心分离、用丙酮洗涤后再次离心分离,分离产物在50℃真空干燥烘箱中干燥30分钟,得到平均粒径为75μm的微胶囊;(2)将所得微胶囊加入碳纤维复合材料制备所用的5222环氧树脂中,分散均匀,然后加入咪唑类衍生物2mz-azine,分散均匀,得到混合物;所述微胶囊的重量为环氧树脂重量的1.0%;咪唑类衍生物2mz-azine的重量为环氧树脂重量的4%;然后将该混合物在50℃下加热40分钟,再加入591固化剂,混合物与591固化剂的质量比为100:25,搅拌均匀;(3)用丙酮对模具面进行清洁,待溶剂完全挥发后涂脱模蜡,并用无纺布将多余脱模蜡擦去,然后将裁剪好的碳布按照设计的铺层方式[(±45)/(±45)/(±45)/(±45)]进行铺叠,合模,然后将步骤(2)得到的产物注入模具中,在100℃下加热2.5小时固化,固化后,按照gb/t1451-2005《纤维增强塑料简支梁式冲击韧性试验方法》中规定的方法进行制样和冲击韧性测试,冲击后得到空白样的冲击韧性,然后将冲击后的试样夹紧固定,室温下放置24小时后再次进行冲击试验,得到的冲击韧性与空白样冲击韧性的比值为修复率。本实施例所得自修复复合材料的自修复率达到82%。实施例6一种自修复碳纤维复合材料件的制备方法,包括以下步骤:(1)制备微胶囊(1-1)将脲、三聚氰胺和甲醛按照质量比2.86:1:10.94混合,得到混合溶液,然后采用磁力搅拌在400转/分钟下搅拌15分钟,搅拌后,向溶液中滴加三乙醇胺,控制溶液ph值在8.1,然后以1.5℃/分钟的加热速率缓慢加热,并在恒定温度80℃加热1.0小时,然后向其中加入去离子水进行稀释,蒸馏水加入量为混合溶液质量的1.5倍,冷却至室温后得到溶液一;(1-2)将5228环氧树脂、去离子水按照1:4的比例混合成混合液,然后加入0.8%混合液重量的阿拉伯树胶与op-10的混合乳化剂,阿拉伯树胶与op-10的质量比为1:1,在500转/分钟的搅拌速度下搅拌1.5小时,然后加入占混合溶液总重量百分比为0.10%的异辛醇消泡,静置30分钟后得到溶液二;(1-3)将上述溶液一和溶液二按照质量比0.85:1混合,并在室温下以500转/分钟的转速搅拌,搅拌均匀后,加入10wt%的盐酸调节溶液ph值至4.2,然后在持续搅拌的情况下,以2.0℃/分钟的升温速率缓慢升温至50℃,并在此温度下持续反应2.5小时,得到溶液三;(1-4)将溶液三离心分离、用丙酮洗涤后再次离心分离,分离产物在50℃真空干燥烘箱中干燥30分钟,得到平均粒径为220μm的微胶囊;(2)将所得微胶囊加入碳纤维复合材料制备所用的5222环氧树脂中,分散均匀,然后加入三氯化硼-单乙胺络合物,分散均匀,得到混合物;所述微胶囊的重量为环氧树脂重量的1.0%;三氯化硼-单乙胺络合物重量为环氧树脂重量的4%;然后将该混合物在50℃下加热40分钟,再加入591固化剂,混合物与591固化剂的质量比为100:25,搅拌均匀;(3)用丙酮对模具面进行清洁,待溶剂完全挥发后涂脱模蜡,并用无纺布将多余脱模蜡擦去,然后将裁剪好的碳布按照设计的铺层方式[(±45)/(±45)/(±45)/(±45)]进行铺叠,合模,然后将步骤(2)得到的产物注入模具中,在100℃下加热2.5小时固化,固化后,按照gb/t1451-2005《纤维增强塑料简支梁式冲击韧性试验方法》中规定的方法进行制样和冲击韧性测试,冲击后得到空白样的冲击韧性,然后将冲击后的试样夹紧固定,室温下放置24小时后再次进行冲击试验,得到的冲击韧性与空白样冲击韧性的比值为修复率。本实施例所得自修复复合材料的自修复率达到88%。以上各实施例得到的自修复碳纤维复合材料件的性能测试结果如表2所示表2修复前后冲击韧性及修复率实施例空白样冲击韧性kj/m2修复后冲击韧性kj/m2修复率%实施例1212.700165.17978实施例2215.035182.12485实施例3230.696204.22289实施例4216.666184.19285实施例5213.255175.66282实施例6214.143187.39288上述参照实施例对自修复碳纤维复合材料件及其制备方法进行的详细描述,是说明性的而不是限定性的,可按照所限定范围列举出若干个实施例,因此在不脱离本发明总体构思下的变化和修改,应属本发明的保护范围之内。当前第1页12