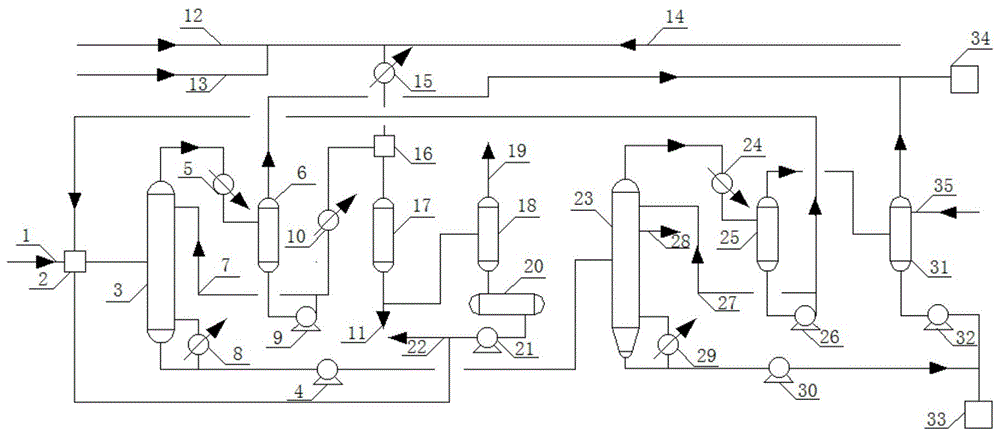
本实用新型涉及一种经过正丁烷氧化-有机溶剂吸收解析后的粗顺酐连续精馏装置,属于顺酐精馏分离领域。
背景技术:
:顺酐又名马来酸酐、失水苹果酸酐,是目前世界上仅次于苯酐和醋酐的第三大酸酐。国内顺酐的生产方法按原料路线可分为苯氧化法、正丁烷氧化法。正丁烷氧化法具有环境污染小、碳原子利用率高、原料来源广泛且价格低廉等优点,近年来正逐步取代苯氧化法成为顺酐主导生产工艺。随着顺酐生产大规模集约化的发展,顺酐后处理越来越倾向于采用溶剂吸收-解析的技术工艺,典型的溶剂吸收解析工艺有亨斯曼工艺、Conser工艺以及ALMA工艺,前两者采用邻苯二甲酸二丁酯(DBP)作溶剂,后者采用六氢邻苯二甲酸二异丁酯(DIBE)作溶剂。关于氧化工艺与吸收解析工艺已有很多研究成果见诸报道,工业应用结果也较为平稳。经过吸收解析后的粗顺酐物料中含有乙酸、丙烯酸、苯酐、焦油等杂质,其中乙酸和丙烯酸是正丁烷氧化副产物,而苯酐、焦油则是解析过程中各组分裂解、聚合的产物,目前工业上多采用连续精馏的方法,首先脱除沸点低于顺酐的乙酸和丙烯酸,然后脱除重组分,从而得到精顺酐。顺酐中的丙烯酸是一种热敏性化合物,其羧基位置上具有不饱和双键,化学性质非常活泼。在粗顺酐脱轻组分塔精馏段、塔顶馏出线、塔顶冷凝器处,随着丙烯酸浓度的增加,其分子碰撞的几率增大,丙烯酸极易发生迈克尔加成反应生成二聚物和三聚物,这些低聚物会进一步发生自由基聚合反应生成高分子聚合物,所生成的聚合物会堵塞管道、塔板和泵体,对装置和工艺生产的平稳运行能造成严重影响。此外,粗顺酐中的苯酐、焦油类物质极易在精制塔塔釜内累积并在塔釜再沸器内结焦,导致换热效果变差。现有技术中,有采用向脱轻组分塔塔顶馏出线加注阻聚剂的方法,阻聚剂通过与丙烯酸形成稳定的大分子化合物来终止链增长反应,但生成的大分子化合物会在后续精制塔累积并结焦,造成后果严重,通常使用的阻聚剂为对苯二酚、对羟基苯甲醚或吩噻嗪。若采用溶剂吸收的方法回收塔釜物料中的顺酐,生成的大分子化合物会导致溶剂处理成本的增加。技术实现要素:针对现有技术的不足,本实用新型的目的是:提供一种粗顺酐连续精馏装置,能实现粗顺酐精馏装置长周期稳定运行,且具有设计科学,结构合理,操作弹性大,经济性能好的特点。同时,本实用新型还提供一种采用粗顺酐连续精馏装置的工艺方法,科学合理,简单易行。为解决上述问题,本实用新型所采取的技术方案为:分布器一端连接有粗顺酐线,另一端通过管路与脱轻组分塔连接,脱轻组分塔顶部通过管路依次与脱轻组分塔塔顶冷凝器、脱轻组分塔回流罐和真空系统连接;脱轻组分塔回流罐底端通过管路依次与脱轻组分塔回流泵、预热器、混合器、加氢反应器、气液分离罐、丙酸罐、丙酸泵和丙酸外采线连接;丙酸泵出口通过管路与分布器底部相连接;脱轻组分塔底端通过管路依次与脱轻组分塔塔釜泵、精制塔、精制塔塔顶冷凝器、精制塔回流罐、尾气洗涤塔和真空系统相连接;尾气洗涤塔上端与溶剂线连接,底部通过管路依次与尾气洗涤塔塔釜泵和吸收解析单元解析塔连接;精制塔回流罐底部通过精制塔回流泵与分布器顶部相连接;加氢反应器底部设置有再生尾气线,气液分离罐顶部设置有加氢尾气线。所述的脱轻组分塔回流泵通过脱轻组分塔回流线和脱轻组分塔上端相连接;脱轻组分塔下端设置有脱轻组分塔再沸器;精制塔回流泵通过精制塔回流线与精制塔上端相连接;精制塔一端设置有精顺酐侧采线;精制塔底部通过管路依次与精制塔塔釜泵和吸收解析单元解析塔连接,精制塔下端设置有精制塔再沸器;混合器顶部通过管路依次与加热器和氢气线连接,加热器同时与空气线和氮气线相连接。所述的脱轻组分塔精馏段采用筛板塔盘,共4-10块,每块塔板上游上凸成斜台状鼓泡促进器,鼓泡促进器迎液侧没有鼓泡孔,背液侧上设置有鼓泡孔;筛孔上设置有金字塔形帽罩,金字塔形帽罩由四块三角形喷射板以及一块正方形顶板构成,喷射板上设有喷射孔;在横、纵两个排列方向上相邻金字塔形帽罩的喷射孔处于不同的水平面上。鼓泡促进器的位置高于塔板,鼓泡孔上的液层薄,压头小,背液侧压力较迎液侧低,气体容易通过,形成良好的鼓泡,促进气液接触传质,使液相各组分形成湍流,以此克服因死区或层流而导致的丙烯酸聚合的问题。在精馏过程中,塔板上的液体自帽罩底隙四周进入罩内,气体则自塔板下方经筛孔进入罩体中,将液体拉膜并粉碎成诸多细小液滴,气液混合物在泡罩内上升过程中由于流道截面积变小,产生缩流,压力能部分转化为动能,使气液混合物流速加快,气液混合物自喷射板上的喷射孔喷射而出,上升碰撞到顶板后将部分折返,返回的气体及液滴与后续上升的气液混合物激烈碰撞、混合,气液混合物中的大液滴回落至液层中,经帽罩底隙再被压入罩体进行循环,而气体则上升到帽罩上方并上升至上一层塔板,进行下一步传热、传质,帽罩结构将气液二相接触传质区域发展成为罩内、罩外、罩顶三个空间范围,并对气液两相形成强烈的扰动,使板式塔塔板空间全用于传质,能有效消除死区或平流,减缓丙烯酸聚合速度,具有良好的抗有机物自聚堵塞和固体悬浮颗粒堵塞的能力,克服了传统浮阀塔盘、小孔径筛孔塔板存在的操作弹性小、易堵塞及大孔径筛孔塔盘传质传热效果差的难题。所述喷射孔巧妙的位置设计能有效消除喷射孔工作时存在的“对喷现象”,避免雾沫夹带,降低能耗,从而提高塔板开孔率,使塔板面积得到充分利用,有效减小分离塔每层塔板上气液返混,减小分离塔每层塔板上液面梯度,降低阻力,提高塔板效率。所述的脱轻组分塔的精馏段塔盘降液管、塔板底面、脱轻组分塔塔顶馏出线管内、脱轻组分塔塔顶冷却器与塔顶馏出液接触部分都涂覆有碳氟聚合物。所述的碳氟聚合物为聚四氟乙烯、聚偏氟乙烯或三氟氯乙烯聚合物中的一种。涂覆聚合物能使覆盖的表面形成一个不润湿表面,使易生成聚合物的液体凝聚成小液滴而不粘附在这个表面上,由于自身重力的作用,小液滴迅速从表面脱落下来,因为丙烯酸单体或其低聚物在被覆盖的表面上停留时间很短,所以抑制了聚合反应的发生。所述的脱轻组分塔提馏段采用不锈钢波纹丝网填料,填料层直径为1.5-2.5m,填料层高度为2.0-4.0m,填料层上部有再分布器,下部有液体收集器。填料层位于粗顺酐线与塔体连接处下方、塔釜再沸器气相线与塔体连接处上方。采用不锈钢波纹丝网填料能有效降低物料停留时间,减缓丙烯酸聚合,此外,该填料还有较高的阻止液体夹带雾沫的能力。所述的混合器包括液体通道、气体通道以及连接件,连接件上有纳米孔,氢气通过纳米孔进入液体物料;所述的纳米孔孔径为20-200nm。纳米孔使气液两相在纳米级范围内分散,从而促进丙烯酸和氢气在催化剂活性位上吸附,提高加氢活性;此外,丙烯酸加氢是一个放热反应,高温容易导致丙烯酸聚合,在纳米孔的作用下,丙酸、丙烯酸和氢气能在纳米级范围内完全分散,丙烯酸得以有效“隔绝”,避免其在加氢过程中聚合。所述的精制塔为填料塔,共有三个填料层,填料层为不锈钢波纹丝网,填料层直径为2.0-3.5m,第一填料层高度为1.0-2.0m,第二填料层高度为5.0-7.0m,第三填料层高度为1.0-2.0m,每个填料层上部有再分布器,下部有液体收集器;其中,第一填料层位于精制塔回流线与塔体连接处下方,位于精顺酐侧采线与塔体连接处上方;第二填料层位于精顺酐侧采线与塔体连接处下方,位于进料线与塔体连接处上方;第三填料层位于进料线与塔体连接处下方,精制塔再沸器气相线与塔体连接处上方。选用不锈钢波纹填料能降低塔压降,进而降低塔釜温度,减少焦油聚合程度。所述的精制塔液体收集器的槽口直径小于填料直径,能缩短塔釜物料在塔釜的停留时间,减少聚合物的生成。所述的尾气洗涤塔为填料塔,填料层为不锈钢波纹丝网,填料层直径为0.5-1.5m,填料层高度为1-2m;填料层上部有再分布器,下部有液体收集器,填料层位于气相进料线与塔体连接处上方、溶剂线与塔体连接处下方。所述的脱轻组分塔再沸器、精制塔再沸器都采用膜式再沸器;脱轻组分塔塔顶冷凝器、精制塔塔顶冷凝器均为列管式或板式换热器中的一种。鉴于丙酸与丙烯酸沸点和饱和蒸气压都很接近,但丙酸中又不存在容易引发聚合的乙烯基官能团,因此利用此特性,向粗顺酐中添加丙酸,丙酸的“惰性”将丙烯酸分子隔离开,从而克服了丙烯酸自聚的难题。脱轻组分塔塔顶馏出物是丙酸、丙烯酸、乙酸及微量顺酐。这部分物料一部分回流,一部分进入加氢反应器,在反应器内,乙酸呈现“反应惰性”,而因为顺酐加氢的反应位垒较高,在加氢反应中,顺酐也呈现“反应惰性”。物料进入加氢反应器内,在催化剂的作用下,丙烯酸与氢气发生如下反应:CH2=CH-COOH+H2→CH3-CH2-COOH(主反应);CH2=CH-COOH+3H2→CH2=CH-CH3+2H2O(副反应);CH2=CH-COOH+4H2→CH3-CH2-CH3+2H2O(副反应);反应后的气液混合物进入气液分离罐分离,反应副产的丙烯、丙烷及未反应的氢气外排,液相产物丙酸返回粗顺酐线作为稀释物料再次使用。本实用新型所述的采用粗顺酐连续精馏装置的工艺方法,包括以下步骤:(1)粗顺酐沿着粗顺酐线经过分布器进入脱轻组分塔,利用各组分挥发度的差异进行分离,由真空系统维持塔系负压,塔顶得到的轻组分经脱轻组分塔塔顶冷凝器冷凝后进入脱轻组分塔回流罐,回流液经过脱轻组分塔回流泵加压后,一部分沿着脱轻组分塔回流线返回脱轻组分塔第一层塔盘,另一部分经预热器加热后,进入混合器;氢气线内氢气通过加热器预热后进入混合器,与脱轻组分塔回流泵外采物料混合,然后再进入加氢反应器,在催化剂的作用下,丙烯酸与氢气反应,反应产物进入气液分离罐,未反应的氢气、丙烯、丙烷等气体沿着加氢尾气线外排,丙酸沿着管线进入丙酸罐,经丙酸泵加压后,一部分沿着丙酸外采线外排,另一部分沿管线返回分布器;(2)脱轻组分塔塔底物料进入精制塔进一步分离,塔顶馏出物经精制塔塔顶冷凝器冷凝后进入精制塔回流罐,在真空系统的作用下,未冷凝的气相进入尾气洗涤塔下端,溶剂沿着溶剂线进入尾气洗涤塔上端,气液两相在尾气洗涤塔内逆流接触,在溶剂的萃取作用下,尾气中的顺酐进入溶剂相,然后经尾气洗涤塔塔釜泵加压后,外采至吸收解析单元解析塔;精制塔回流罐内的液相经过精制塔回流泵加压后,一部分沿着精制塔回流线返回精制塔,另一部分返回分布器;精顺酐经精顺酐侧采线外采,塔底物料经过精制塔塔釜泵加压后,外采至吸收解析单元解析塔;(3)加氢反应进行一段时间后,催化剂会因活性位覆盖而失活,需要再生催化剂:首先引入热氮气吹扫床层,然后引入热空气,最后引入活化气活化催化剂;整个过程通过加热器控制反应器温度,吹扫气、焙烧气和活化气通过再生尾气线外排,活化完毕后向加氢反应器中引入原料及氢气进行反应。所述的步骤1中,脱轻组分塔进料塔板处丙酸与丙烯酸的质量比为20-200:1;脱轻组分塔顶压力为-100—-70KPa,塔底压力为-90—-60KPa,脱轻组分塔回流比为0.7-4:1。所述的步骤2中,精制塔塔顶压力为-100—-70KPa,塔底压力为-95—-65KPa;精制塔回流比为5-20:1。所述的脱轻组分塔塔顶温度为110-140℃,塔釜温度为140-170℃;精制塔塔顶温度为110-130℃,塔釜温度为120-140℃;精制塔侧采温度为112-132℃;尾气洗涤塔温度为60-80℃;尾气洗涤塔中溶剂与尾气中顺酐的质量比为0.2-1:1。加氢反应过程中,氢气与丙烯酸、丙酸通过混合器混合,加氢过程中丙烯酸、氢气与丙酸的摩尔比为1:1-100:1-100,优选1:1-20:10-40。丙酸和氢气能及时带走反应放出的热,起到“热载体”的作用,能有效避免因高温而导致的副反应。所述的加氢反应条件为:反应压力1-2MPa,反应温度40-80℃,丙烯酸体积空速为0.1-2h-1,进料中氢气与丙烯酸的摩尔比为1-100:1,优选1-20:1。加氢催化剂为负载型催化剂,活性组分为含量0.2-1wt.%的钯、铂、镍、钼或钌中的一种或几种;载体为氧化铝或氧化硅,催化剂的比表面积为50-150m2/g,孔径为10-50nm。所述的步骤3中,吹扫温度为60-200℃,焙烧温度为300-400℃。催化剂新剂或再生后的催化剂的活性组分为氧化态,反应前需要引还原气活化催化剂,活化气是氢气或氢气/氮气混合气中的一种;活化温度为200-350℃,活化压力为0-0.2MPa,氢气体积空速为1000-1500h-1。精制塔塔釜物料组成为顺酐与重组分,这部分物料返回吸收解析单元解析塔,利用沸点的不同分离顺酐与重组分,高沸点焦油类化合物进入溶剂相,然后经溶剂处理单元脱除。精制塔塔釜采出线中的物料进入吸收解析单元解析塔,通过降低塔釜温度、提高精制塔塔釜采出线外采量的方法,降低塔釜温度,缩短塔釜物料中焦油在塔釜的停留时间,减少结焦物的生成。与现有技术相比,本实用新型具有如下有益效果:1.所述的粗顺酐连续精馏装置,设计科学,结构合理,能实现粗顺酐精馏装置长周期稳定运行,具有操作弹性大、经济性能好的优点;还能有效克服丙烯酸挂堵,焦油结焦的问题,且精馏过程不会二次污染顺酐,得到的精顺酐收率高,纯度高。附图说明图1是粗顺酐连续精馏装置的结构示意图;图2是筛板塔盘的塔板结构示意图;图3是金字塔形帽罩的结构示意图;图4是金字塔形帽罩的俯视结构示意图;图中,1-粗顺酐线;2-分布器;3-脱轻组分塔;4-脱轻组分塔塔釜泵;5-脱轻组分塔塔顶冷凝器;6-脱轻组分塔回流罐;7-脱轻组分塔回流罐;8-脱轻组分塔再沸器;9-脱轻组分塔回流泵;10-预热器;11-再生尾气线;12-空气线;13-氮气线;14-氢气线;15-加热器;16-混合器;17-加氢反应器;18-气液分离罐;19-加氢尾气线;20-丙酸罐;21-丙酸泵;22-丙酸外采线;23-精制塔;24-精制塔塔顶冷凝器;25-精制塔回流罐;26-精制塔回流泵;27-精制塔回流线;28-精顺酐侧采线;29-精制塔再沸器;30-精制塔塔釜泵;31-尾气洗涤塔;32-尾气洗涤塔塔釜泵;33-吸收解析单元解析塔;34-真空系统;35-溶剂线;36-脱轻组分塔塔体;37-鼓泡孔;38-鼓泡促进器;39-金字塔形帽罩;40-降液管;41-筛孔;42-塔板;43-顶板;44-喷射板;45-喷射孔。具体实施方式下面结合附图说明和实施例对本实用新型做进一步的说明。实施例1所述的粗顺酐连续精馏装置,分布器2一端连接有粗顺酐线1,另一端通过管路与脱轻组分塔3连接,脱轻组分塔3顶部通过管路依次与脱轻组分塔塔顶冷凝器5、脱轻组分塔回流罐6和真空系统34连接;脱轻组分塔回流罐6底端通过管路依次与脱轻组分塔回流泵9、预热器10、混合器16、加氢反应器17、气液分离罐18、丙酸罐20、丙酸泵21和酸外采线22连接;酸泵21出口通过管路与分布器2底部相连接;脱轻组分塔3底端通过管路依次与脱轻组分塔塔釜泵4、精制塔23、精制塔塔顶冷凝器24、精制塔回流罐25、尾气洗涤塔31和真空系统34相连接;尾气洗涤塔31上端与溶剂线35连接,底部通过管路依次与尾气洗涤塔塔釜泵32和吸收解析单元解析塔33连接;精制塔回流罐25底部通过精制塔回流泵26与分布器2顶部相连接;加氢反应器17底部设置有再生尾气线11,气液分离罐顶部设置有加氢尾气线19。所述的脱轻组分塔回流泵9通过脱轻组分塔回流线7和脱轻组分塔3上端相连接;脱轻组分塔下端设置有脱轻组分塔再沸器8;精制塔回流泵26通过精制塔回流线27与精制塔23上端相连接;精制塔23一端设置有精顺酐侧采线28;精制塔23底部通过管路依次与精制塔塔釜泵30和吸收解析单元解析塔连接,精制塔下端设置有精制塔再沸器29;混合器16顶部通过管路依次与加热器15和氢气线14连接,加热器15同时与空气线12和氮气线13相连接。所述的脱轻组分塔3的精馏段采用筛板塔盘,共4-10块,每块塔板42上游上凸成斜台状鼓泡促进器38,鼓泡促进器38迎液侧没有鼓泡孔37,背液侧上设置有鼓泡孔37;筛孔41上设置有金字塔形帽罩39,金字塔形帽罩39由四块三角形喷射板44以及一块正方形顶板43构成,喷射板44上设有喷射孔45;在横、纵两个排列方向上相邻金字塔形帽罩39的喷射孔45处于不同的水平面上。所述的脱轻组分塔的精馏段塔盘降液管、塔板底面、脱轻组分塔塔顶馏出线管内、脱轻组分塔塔顶冷却器和塔顶馏出液接触部分都涂覆有聚四氟乙烯。脱轻组分塔的提馏段采用不锈钢波纹丝网填料,填料层直径为1.5m,填料层高度为2.0m,填料为不锈钢波纹丝网。所述的填料层上部有再分布器,下部有液体收集器,填料层位于粗顺酐线1与塔体连接处下方,塔釜再沸器气相线与塔体连接处上方。所述的精制塔23为填料塔,共有三个填料层,填料层为不锈钢波纹丝网,填料层直径为2.0-3.5m,第一填料层高度为1.0-2.0m,第二填料层高度为5.0-7.0m,第三填料层高度为1.0-2.0m,每个填料层上部有再分布器,下部有液体收集器;其中,第一填料层位于精制塔回流线27与塔体连接处下方,位于精顺酐侧采线28与塔体连接处上方;第二填料层位于精顺酐侧采线28与塔体连接处下方,位于进料线与塔体连接处上方;第三填料层位于进料线与塔体连接处下方,精制塔再沸器29气相线与塔体连接处上方。精制塔液体收集槽直径小于填料直径。所述的混合器16包括液体通道、气体通道以及连接件,连接件上有纳米孔,氢气通过纳米孔进入液体物料,纳米孔的孔径为20nm。所述的脱轻组分塔再沸器8与精制塔再沸器29采用膜式再沸器,脱轻组分塔塔顶冷凝器5与精制塔塔顶冷凝器24为列管式换热器。所述的尾气洗涤塔31为填料塔,填料为不锈钢波纹丝网,填料层直径为0.5-1.5m,填料层高度为1-2m;填料层上部有再分布器,下部有液体收集器,填料层位于气相进料线与塔体连接处上方、溶剂线35与塔体连接处下方。来自吸收解析单元的粗顺酐物料组成如表1所示;在脱轻组分塔中添加丙酸,通过调节,使进入脱轻组分塔进料塔塔板处的丙酸与丙烯酸的质量比为20:1,物料组成如表2所示:表1粗顺酐物料组成成分H2O乙酸丙烯酸顺酐重组分组成(wt.%)0.100.301.2098.300.10表2进入脱轻组分塔的物料组成成分H2O乙酸丙酸丙烯酸顺酐重组分组成(wt.%)0.080.2419.400.9779.230.08所述的采用粗顺酐连续精馏装置的工艺方法,包括如下步骤:(1)粗顺酐物料沿着粗顺酐线1经过分布器2进入脱轻组分塔3,在脱轻组分塔再沸器8的热驱动作用下,利用各组分挥发度的差异进行分离,由真空系统34维持塔系负压,塔顶得到的轻组分经脱轻组分塔塔顶冷凝器5冷凝后进入脱轻组分塔回流罐6,回流液经过脱轻组分塔回流泵9加压后,一部分沿着脱轻组分塔回流线返回脱轻组分塔3第一层塔盘,另一部分经预热器10加热后,进入混合器16;脱轻组分塔塔顶压力为-70KPa,塔底压力为-60Kpa,塔顶温度为110℃,塔釜温度为140℃,回流比为4。氢气线14内氢气通过加热器15预热后进入混合器16,与脱轻组分塔回流泵9外采物料混合,然后再进入加氢反应器17,在催化剂的作用下,丙烯酸与氢气反应,反应产物进入气液分离罐18,未反应的氢气、丙烯、丙烷等气体沿着加氢尾气线19外排,丙酸沿着管线进入丙酸罐20,经丙酸泵21加压后,一部分沿着丙酸外采线22外排,另一部分沿管线返回分布器2;其中,加氢反应条件为:反应压力2Mpa,反应温度40℃,丙烯酸体积空速为2h-1,进料中氢气与丙烯酸的摩尔比为20;加氢催化剂为负载型催化剂,活性组分是钯,催化剂载体为氧化硅,活性组分含量共计1wt%,催化剂的比表面积为50m2/g,孔径为50nm。此时,丙烯酸转化率为99.8%,产物丙酸选择性为99.5%。分离后,脱轻组分塔塔顶馏出物、塔底物组料组成如表3、表4所示:表3脱轻组分塔塔顶馏出物组成成分乙酸丙酸丙烯酸顺酐组成(wt.%)1.1492.384.620.23表4脱轻组分塔塔底物料组成成分丙酸丙烯酸顺酐重组分组成(wt.%)0.200.0299.660.12(2)脱轻组分塔3塔底物料进入精制塔23进一步分离,塔顶馏出物经精制塔塔顶冷凝器24冷凝后进入精制塔25,在真空系统34的作用下,未冷凝的气相进入尾气洗涤塔31下端,溶剂沿着溶剂线35进入尾气洗涤塔31上端,气液两相在尾气洗涤塔31内逆流接触,在溶剂的萃取作用下,尾气中的顺酐进入溶剂相,然后经尾气洗涤塔塔釜泵32加压后,外采至吸收解析单元解析塔33;精制塔回流罐25内的液相经过精制塔回流泵26加压后,一部分沿着精制塔回流线27返回精制塔23,另一部分返回分布器2;精顺酐经精顺酐侧采线28外采,塔底物料经过精制塔塔釜泵30加压后,外采至吸收解析单元解析塔33;其中,精制塔23塔顶压力为-70KPa,塔底压力为-65KPa,塔顶温度为110℃,塔釜温度为120℃,侧采温度为112℃,精制塔回流比为5;尾气洗涤塔温度为60℃,溶剂与尾气中顺酐质量比为0.2,此时,尾气中顺酐回收率为99.9%。(3)加氢反应进行一段时间后,催化剂会因活性位覆盖而失活,需要再生催化剂:首先引入热氮气吹扫床层,然后引入热空气,最后引入活化气活化催化剂;整个过程通过加热器控制反应器温度,吹扫气、焙烧气和活化气通过再生尾气线外排,活化完毕后向加氢反应器中引入原料及氢气进行反应。步骤3中,吹扫温度为100℃,焙烧温度为350℃。催化剂新剂或再生后的催化剂的活性组分为氧化态,反应前需要引还原气活化催化剂,活化气是氢气;活化温度为200℃,活化压力为-0.2MPa,氢气体积空速为1500h-1。分离后,精制塔塔顶馏出物、精制塔采出物组成分别如表5、6、7所示:表5精制塔塔顶馏出物组成成分丙酸丙烯酸顺酐组成(wt.%)0.210.0299.77表6精制塔侧采采出物组成成分顺酐组成(wt.%)99.92表7精制塔塔釜采出物组成成分顺酐重组分组成(wt.%)99.880.12本实施例中,装置连续平稳运行了10个月,脱轻组分塔塔压差维持在10-20KPa,没有发生大的波动,塔顶、塔底采出物组成平稳,这说明脱轻组分塔塔板没有发生丙烯酸挂堵,没有影响传热传质。精制塔塔底再沸器加热介质流量稳定,这说明没有发生因焦油类物质结焦而导致的精制塔再沸器传热效果差的问题。加氢反应器运转周期为8个月。当前第1页1 2 3