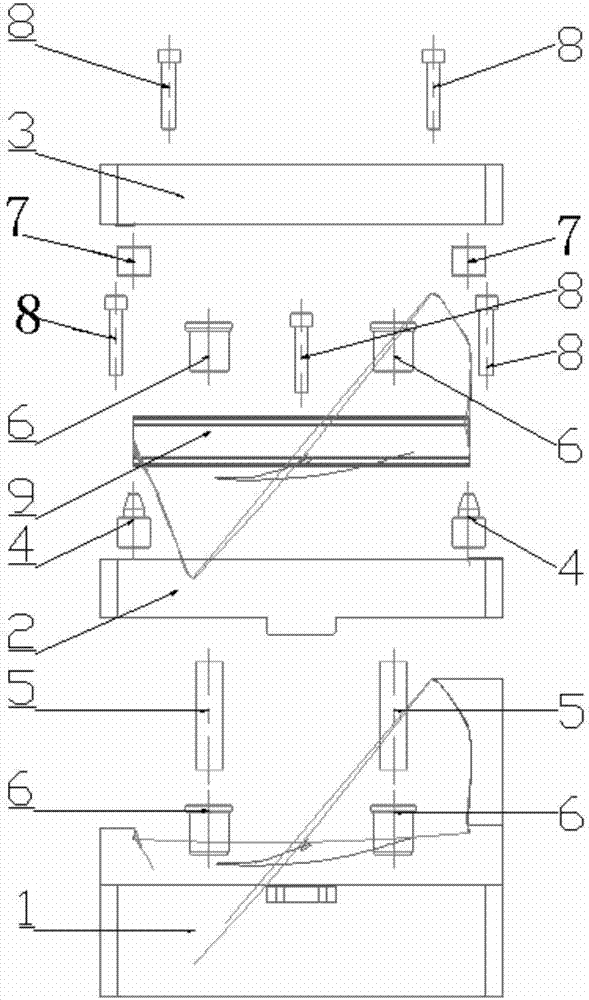
本发明涉及航空工艺装备结构设计与制造技术领域,具体地说,涉及一种用于精密制造航空发动机复合材料风扇叶片的金属模具。
背景技术:在航空工业领域,广泛使用的发动机主要是涡扇发动机。发动机叶片为薄壁结构件,具有复杂的自由曲面,设计要求精度高、重量轻。尤其是当第四代航空发动机要求具有更高的推重比时,传统的金属材料已远远无法满足其要求,甚至是钛合金等轻质金属材料也已显得力不从心。因此,亟需一种具有良好物理、化学性能的更为轻质的材料来替代现有材料。碳纤维增强树脂基复合材料的日渐成熟为高推重比航空发动机的研制成功带来了可能。但碳纤维增强树脂基复合材料属于难加工材料,如果像金属材料那样采用数控切削毛坯件的方式加工出复合材料风扇叶片,不但在成本上难以接受,最终制件的加工质量也无法保证。在现有碳纤维增强树脂基复合材料风扇叶片的制造方法中,利用模具铺层,采用热压罐固化成型工艺是公认最好的制造方法。由于航空发动机复合材料风扇叶片为薄壁结构,具有以叶片榫根至叶尖方向为轴呈中间厚两边薄的复杂的自由曲面,并具有弯、扭、掠形的表面特点,设计精度要求非常高,尤其是与叶盘相连接的榫根部位,其设计精度要求更高。并且碳纤维增强树脂基复合材料为难加工材料,现有的数控加工技术很难加工出符合要求的航空发动机复合材料风扇叶片;如何在满足设计精度的前提下在现有加工模具经验的基础上,制造出符合要求的碳纤维增强树脂基复合材料风扇叶片模具,提高生产效率,降低生产成本,在新一代高推重比航空发动机的研制过程中具有非常重要的意义。
技术实现要素:为了避免现有技术存在的不足,本发明提出一种航空发动机复合材料风扇叶片成型模具,该成型模具不仅可提高航空发动机复合材料风扇叶片的加工效率,而且可降低航空发动机复合材料风扇叶片的生产成本;成型模具结构简单,安装拆装方便,可多次使用而不影响其生产精度。本发明解决其技术问题所采用的技术方案是:包括叶身模具、榫根下模、榫根上模、锥形定位销、定位销、翻边衬套、衬套、螺栓,所述叶身模具为开模,叶身模具上表面以叶片榫根至叶尖方向为轴形成中间厚两边薄的复杂自由曲面,叶身模具末端凸出段中间部位有用于榫根下模限位的凹槽,两个翻边衬套嵌入在叶身模具末端凸出段内;所述榫根下模与榫根上模为闭模,榫根下模下端面有与叶身模具末端凹槽配合的凸台,榫根下模与叶身模具通过对称分布的翻边衬套、定位销和螺栓限位、固连,两个翻边衬套嵌入在榫根下模内,榫根上模与榫根下模通过衬套、锥形定位销和螺栓限位、固连,两个衬套分别嵌入在榫根上模内;所述叶身模具水平固定在工作台上,叶片铺层位于叶身模具上表面,其中叶身模具铺层尾端高度与榫根下模铺层和叶身模具铺层交界处高度相等。榫根下模、榫根上模与叶身模具同轴安装。有益效果本发明提出的一种航空发动机复合材料风扇叶片成型模具,由叶身模具、榫根下模、榫根上模三部分组成;其中,叶身模具为开模,榫根下模、榫根上模为闭模,叶身的上表面形成复杂自由曲面,榫根下模、榫根上模与叶身模具末端凸出段相层叠、可拆卸。榫根下模、榫根上模与叶身模具之间通过限位凹槽、多个衬套、定位销与螺栓连接固定,且成型模具安装拆卸、方便。叶身模具上表面以叶片榫根至叶尖方向为轴形成中间厚两边薄的复杂自由曲面,具有弯、扭、掠形的表面特点,满足航空发动机风扇叶片对气动外形的要求;榫根下模与榫根上模通过设计进一步提高了加工精度,并且通过限位凹槽、衬套、定位销与螺栓之间的相互配合,使得叶身模具、榫根下模、榫根上模三个部分能够准确固定并获得足够、均匀的压力,其不但能避免榫根的错位,同时能减小榫根的损伤。本发明航空发动机复合材料风扇叶片成型模具,在满足制造精度的前提下,不仅可提高航空发动机复合材料风扇叶片的加工效率和精度,而且可降低航空发动机复合材料风扇叶片的生产成本。成型模具结构简单、拆装方便,可多次使用而不影响其生产精度。附图说明下面结合附图和实施方式对本发明一种航空发动机复合材料风扇叶片成型模具作进一步的详细说明。图1为本发明复合材料风扇叶片成型模具结构示意图。图2为本发明复合材料风扇叶片成型模具右视图。图中:1.叶身模具2.榫根下模3.榫根上模4.锥形定位销5.定位销6.翻边衬套7.衬套8.螺栓9.叶片具体实施方式本实施例是一种航空发动机复合材料风扇叶片成型模具。参阅图1、图2,航空发动机复合材料风扇叶片成型模具由叶身模具1、榫根下模2、榫根上模3、锥形定位销4、定位销5、翻边衬套6、衬套7、螺栓8和叶片9组成;航空发动机复合材料风扇叶片成型模具有开模与闭模两部分,其中,叶身模具1为开模,榫根下模2与榫根上模3为闭模。叶身模具1表面以叶片榫根至叶尖方向为轴形成中间厚两边薄的复杂自由曲面,叶身模具1末端凸出段中间部位有用于榫根下模2限位的凹槽,两个翻边衬套6嵌入在叶身模具1末端凸出段内。榫根下模2下端面有与叶身模具1末端凹槽配合的凸台,榫根下模2与叶身模具1通过对称分布的翻边衬套6、定位销5和螺栓8限位、固定连接,两个翻边衬套6嵌入在榫根下模2内。榫根上模3与榫根下模2通过衬套7、锥形定位销4和螺栓8限位、固定连接,两个衬套7分别嵌入在榫根上模3内。叶身模具1水平固定安装在工作台上;叶片铺层位于叶身模具1上表面,其中,叶身模具1铺层尾端高度与榫根下模2铺层和叶身模具1铺层交界处高度相等。本实施例中,叶身模具1水平固定在工作台面上,当进行叶片9铺层操作时,将榫根上模3拆卸下来,榫根下模2通过对称分布的翻边衬套6、定位销5和螺栓8被紧紧固定在叶身模具1末端凸出段上;当拧紧螺栓8时,恰好可保证叶身模具1铺层部分尾端高度与榫根下模2铺层部分和叶身模具1铺层部分交界处具有相等的高度,可保证叶片9的叶身部分与榫根部分能够平滑的过渡。叶身模具1铺层的表面以叶片9榫根至叶尖方向为轴形成中间厚两边薄的复杂自由曲面,具有弯、扭、掠形的表面特点,满足航空发动机风扇叶片9对气动外形的要求。成型模具装配时,榫根下模、榫根上模与叶身模具同轴安装。限位凹槽、四个翻边衬套6、两个定位销5与螺栓钉8将叶身模具1和榫根下模2限位、固定,其中,两个翻边衬套6内嵌于叶身模具1末端凸出段内,另外两个翻边衬套6内嵌于榫根下模2内;两个衬套7、两个锥形定位销4与螺栓8将榫根下模2和榫根上模3限位、固定,两个衬套7分别内嵌于榫根上模3内。榫根下模2与榫根上模3通过设计提高了加工精度,并且通过限位凹槽、衬套7、定位销5与螺栓8之间的配合使得榫根下模2、榫根上模3与叶身模具1三个部分能准确固定并获得足够均匀的压力,且可防止叶身模具1、榫根下模2和榫根上模3的随机移动,避免榫根的错位,减小榫根的损伤。