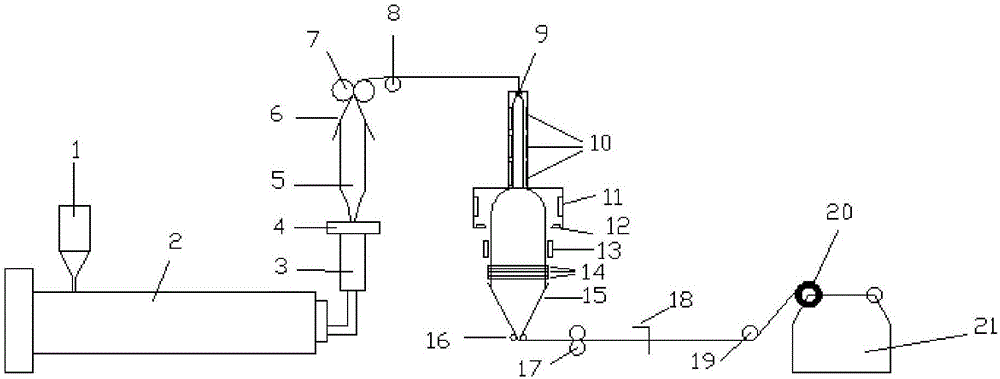
本发明属于高分子材料制造
技术领域:
,具体涉及静态混合器及PVC热收缩膜吹塑成型制备方法。
背景技术:
:PVC热收缩膜的收缩率、收缩力适中,透明度好,力学性能优异,性价比高,广泛应用于日化产品、电子电器、塑胶五金、玻璃陶瓷等商品的包装。其不仅对包装物具有很好的保护作用,而且还使商品外形更加鲜明美观,提升商品包装档次,是目前较理想的薄膜类包装材料。PVC热收缩膜成型方式可以归为两大类,即吹塑(二次吹胀)成型和压延(流延)拉伸成型。吹塑成型,加工设备简单,投资省,所生产的薄膜品种更换灵活,更适合通用收缩包装材料的加工生产。压延(流延)拉伸成型方式,加工精细,薄膜产品宽幅大,厚薄均匀度好,但设备多,流程长,投资大,运行费用高。塑料薄膜金属化,使薄膜具有金属光泽,美感膜表面,装饰效果好,综合性能优异,气密、阻隔、遮光、防静电等性能都超过非金属化塑料薄膜。PVC金属化热收缩膜,集合了两种薄膜的包装装饰优势,进一步提升了薄膜装潢作用,赋予包装物更优美、靓丽的外观形象,彰显商品高档品质。塑料薄膜金属化分为表面金属化和全金属化。表面金属化可采用涂装、喷涂、化学镀、电镀、蒸镀等技术手段实现。由于金属与塑料之间粘附力弱,涂装和喷涂的金属层容易产生脱落,影响金属化性能和效果。而化学镀、电镀之前,则需要对薄膜表面进行脱脂处理,处理温度会比较高,一般在70~80℃,该温度下,PVC热收缩膜的大部分收缩率会丧失。塑料薄膜表面蒸镀,金属蒸汽同样具有高温特性,蒸镀过程中将使收缩膜的收缩效能丧失,无法得到满意的PVC金属化热收缩薄膜。因此,在配方中添加金属粉,通过混合、熔融塑化成型为具有收缩功能的薄膜产品,成为制备PVC金属化热收缩膜的首选成型方法。金属化塑料薄膜制备中所使用的金属粉颜料,多为软金属,如最常用的铝粉(银色)、铜锌粉(金色),一般为微米级的细粉末,易产生团聚,分散性差。同时,加工中的高剪切力,会使金属颜料变形,影响颜料颗粒的定向排列效果,从而产生色相和色泽差异,造成金属化薄膜质量问题。此外,金属粉用量少,一般为0.5~2.0质量份(100份PVC树脂),且其物性与PVC热收缩膜配方体系其它组分差异大,相容性差,不易共混分散均匀。因此,在混合、加工过程中,既要降低金属粉的剪切损伤,又要保证金属粉颜料在PVC体系中有好的分散效果,成为制约PVC金属化热收缩膜加工的主要问题和生产瓶颈。普通PVC热收缩吹膜机组,按照二次吹胀的加热方式不同,有水浴加热,如图1所示和红外线烘箱加热如图2所示两种方式。水浴加热温度更均匀,薄膜收缩率控制更精准,是PVC热收缩印刷膜、收缩套管膜及高品质收缩包装膜的主要加工方式。众所周知,由挤出机螺杆进入吹膜机头的熔体,即使有微小的温度和组份不均匀,都会导致薄膜产品厚薄差异,着色不均匀,甚至机械性能下降等缺陷。技术实现要素:本发明要解决的技术问题是提供静态混合器,克服上述缺陷,解决金属粉有剪切损伤、金属粉颜料在PVC体系中分散效果差、薄膜产品厚薄差异大、着色不均匀、机械性能差等问题。为解决上述技术问题,本发明提供静态混合器,包括圆筒、加热元件、扭曲元件和固定元件,所述固定元件包括第一固定件和第二固定件,所述第一固定件设置于所述圆筒的一端,所述第一固定件连接挤出机的机筒和所述圆筒,所述第二固定件设置于所述圆筒的另一端,所述第二固定件连接吹膜机头的连接段和所述圆筒,所述加热元件套设于所述圆筒的外筒壁,所述扭曲元件插设于所述圆筒内。作为本发明所述静态混合器的一种优选方案,所述扭曲元件包括第一扭曲元件和第二扭曲元件,所述第一扭曲元件和第二扭曲元件交错设置。作为本发明所述静态混合器的一种优选方案,所述第一扭曲元件和第二扭曲元件之间的夹角为90度。作为本发明所述静态混合器的一种优选方案,所述第一扭曲元件和第二扭曲元件均为螺旋状,所述第一扭曲元件和第二扭曲元件的螺旋旋转方向相反。作为本发明所述静态混合器的一种优选方案,所述加热元件为带状加热器,其缠绕于所述圆筒的外筒壁上。作为本发明所述静态混合器的一种优选方案,所述圆筒的直径与所述挤出机的机筒的直径相同,所述圆筒的长度为所述挤出机的螺杆直径的3~5倍。本发明还提供一种PVC热收缩膜吹塑成型制备方法,包括:(1)按配方称取原料;(2)将所述原料加入高速混合机中混合,在温度为125~130℃的条件下出料,制得高温捏合料;(3)将所述高温捏合料放入冷却混合机冷却到50℃以下,制成干混料;(4)将所述干混料熟化静置8小时以上,得到熟化后的混料;(5)将所述混料放入挤出机中熔融塑化,得到熔体;(6)使用权利要求1~6任意一项所述的静态混合器将熔体均质化,制得均质熔体;(7)吹膜机头将所述均质熔体吹胀成筒状薄膜,即第一膜泡,所述吹膜机头的温度为200~210℃,然后自然风风环冷却;(8)在75-85℃的温度条件下二次加热、再次吹胀成第二膜泡、冷却定型,获得收缩率;(9)牵引、收卷,获得筒状膜卷的半成品;(10)将所述半成品分切、检验、包装,制成PVC金属化热收缩膜成品。作为本发明所述PVC热收缩膜吹塑成型制备方法的一种优选方案,步骤(1)中,所述配方按质量份计,PVC树脂为100份、有机锡为2.0-2.5份、增塑剂为4.0-6.0份、增韧剂为6.0-8.0份、促进塑化型加工助剂为2.5-3.0份、润滑型加工助剂为0.8-1.2份、内润滑剂为1.0-1.3份、外润滑剂为0.8-1.1份、金属粉颜料为0.5-2.0份、消光粉为0.3-0.5份。作为本发明所述PVC热收缩膜吹塑成型制备方法的一种优选方案,步骤(5)中,所述挤出机温度分设为五个阶段:第一阶段160~165℃、第二阶段170~175℃、第三阶段180~185℃、第四阶段190~195℃、第五阶段195~200℃。作为本发明所述PVC热收缩膜吹塑成型制备方法的一种优选方案,步骤(6)中,所述静态混合器的温度为190~200℃。与现有技术相比,本发明提出的静态混合器,利用静态混合器的混合作用与机械搅拌的不同原理,在强化混合过程中,利用静态混合器特殊结构,促进熔体混合、均化,避免金属粉的剪切损伤。本发明提出的PVC热收缩膜吹塑成型制备方法所制得的PVC热收缩膜相比普通PVC热收缩膜,PVC金属化热收缩膜配方在保持良好稳定性、加工性,以及力学性刚柔平衡的基础上,通过添加一定量的润滑型加工助剂,并提高加工助剂总用量,增加润滑剂配比,提升干混料和熔体的流动性能,降低设备对物料的剪切和摩擦,提高金属粉在PVC配方体系的分散均匀性,保证PVC收缩膜金属颜色的一致性。附图说明为了更清楚地说明本发明实施例的技术方案,下面将对实施例描述中所需要使用的附图作简单地介绍,显而易见地,下面描述中的附图仅仅是本发明的一些实施例,对于本领域普通技术人员来讲,在不付出创造性劳动性的前提下,还可以根据这些附图获得其它的附图。其中,图1为现有技术中二次水浴加热PVC热收缩膜的流程示意图;图2为现有技术中远红外线二次加热吹膜法制作PVC热收缩膜的流程示意图;图3为本发明的静态混合器的结构示意图。其中:1为料斗、2为挤出机、3为吹膜机头、4为冷却风环、5为第一膜泡、6为第一人字板、7为第一牵引辊、8为第一导辊、9为第二牵引辊、10为远红外加热装置、11为辅助加热装置、12为上冷却风环、13为下冷却风环、14为稳泡装置、15为第二人字板、16为第三牵引辊、17为热定型辊、18为冷却装置、19为第二导辊、20为膜卷、21为卷曲装置、22为第二膜泡、23为定径冷却套、24为加热水箱、25为圆筒、26为加热元件、27为扭曲元件、271为第一扭曲元件、272为第二扭曲元件、281为第一固定件、282为第二固定件、29为热电偶孔。具体实施方式本发明所述的静态混合器,其包括:圆筒25、加热元件26、扭曲元件27和固定元件(未图示)。为使本发明的上述目的、特征和优点能够更加明显易懂,下面结合具体实施方式对本发明作进一步详细的说明。首先,此处所称的“一个实施例”或“实施例”是指可包含于本发明至少一个实现方式中的特定特征、结构或特性。在本说明书中不同地方出现的“在一个实施例中”并非均指同一个实施例,也不是单独的或选择性的与其他实施例互相排斥的实施例。其次,本发明利用结构示意图等进行详细描述,在详述本发明实施例时,为便于说明,表示静态混合器结构的示意图会不依一般比例作局部放大,而且所述示意图只是实例,其在此不应限制本发明保护的范围。此外,在实际制作中应包含长度、宽度及深度的三维空间。请参阅图3,图3为本发明的静态混合器的结构示意图。如图3所示,在普通PVC热收缩吹膜机组的挤出机和吹膜机头中间,增设直径与挤出机机筒相同、长度为3~5D(挤出机螺杆直径)的静态混合器,所述静态混合器是包括圆筒25、加热元件26、扭曲元件27和固定元件,固定元件包括第一固定件281和第二固定件282,第一固定件281和第二固定件282分别设置于圆筒25的两端,第一固定件281连接挤出机的机筒和圆筒,第二固定件282连接吹膜机头的连接段和圆筒25,即静态混合器与螺杆头部的连接采用组合式,静态混合器组装后,与机筒一起连接,静态混合器另一端通过法兰与吹膜机头连接段相连。加热元件26套设于圆筒25的外筒壁,扭曲元件插设于圆筒25内。静态混合器不属于螺杆主体,是一组设在机头和螺杆之间的固定原件。本发明中采用的静态混合器是在一段圆筒内,镶嵌安装着一系列串联并彼此接触的若干扭曲元件,即第一扭曲元件271和第二扭曲元件272,这些固定元件按不同方向相对交错,互成90°,第一扭曲元件271和第二扭曲元件272均为螺旋状,第一扭曲元件271和第二扭曲元件272的螺旋旋转方向相反。加热元件26为带状加热器,其缠绕于圆筒25的外筒壁上。在带状加热器之间,圆筒25的外筒壁上还设有热电偶孔29。静态混合器不是依靠机械运动部件的运动,给予熔体(流体)能量而促进混合的,而是在熔体输送过程中,通过扭曲元件,将熔体分割成若干股料流,使其顺着扭曲元件所形成的流道流动,同时料流还相对于扭曲元件的螺旋曲线做回转流动,熔体的翻转导致了径向混合,提升了熔体混合均化效果。熔体在静态混合器中,是依靠自身的流动能量而进行混合的,故剪切作用相对较低,不会对金属颜料粉造成进一步剪切损伤。因此,本发明是利用静态混合器的混合作用与机械搅拌的不同原理,在强化混合过程中,利用静态混合器特殊结构,促进熔体混合、均化,避免金属粉的剪切损伤。下面介绍需利用上述静态混合器的PVC热收缩膜吹塑成型制备方法:1、按照配方称取PVC树脂、金属粉颜料及其它助剂;2、加入高速混合机捏合(混合),出料温度125~130℃;3、冷却混合机冷却到50℃以下,制成干混料;4、干混料熟化(静置)8小时以上;5、挤出机熔融塑化,挤出机温度:160~165℃、170~175℃、180~185℃、190~195℃、195~200℃;6、静态混合器熔体均质化,静态混合器长度3~5D,温度190~200℃;7、吹膜机头吹胀成筒状薄膜(一泡),机头温度200~210℃,自然风风环冷却;8、二次加热(75-85℃)、再次吹胀成二泡、冷却定型,获得收缩率;9、牵引、收卷,获得筒状膜卷(半成品);10、分切、检验、包装,制成PVC金属化热收缩膜成品。为实现上述目的,除选用粒径适宜,表面处理的金属粉颜料外,配方设计时,适当提高内外润滑剂的用量,以此减小物料在混合和加工中的内外摩擦力;加工助剂采用促进塑化型和润滑型两种ACR组合形式,并大幅提高总用量,以此提高PVC配方体系熔体的润滑性和流动性,提高金属粉在熔体中分散效果,降低熔体塑化输送中的机械剪切力,从而实现降低金属粉剪切损伤,保证金属粉颜料在PVC体系中良好分散效果的配方设计目的。另外,为了尽量消除金属粉色泽差异,配方中还添加一定比例的消光粉配合金属粉使用,用量为0.3~0.5质量份。PVC金属化热收缩膜具体配方比例及与普通PVC热收缩膜配方对比情况如下表1.表1金属化和非金属化PVC热收缩膜配方对比情况下面介绍上述设备及配方所制得的产品的具体实施例:实施例1:产品:银色PVC热收缩膜,薄膜折径780mm,厚度0.07mm,收缩率:横向48~50%,纵向0~3%。配方设备:挤出机:Ф65单螺杆挤出机,L/D=29:1,螺杆为带混炼头的屏障型结构。静态混合器:长度260mm;吹膜机头:口模直径Ф130;二次吹胀:水浴加热工艺:捏合(高速混合)出料温度:130℃;冷却混合出料温度:50℃干混料静置8小时。挤出机塑化挤出:挤出机12345温度,℃163172185190198挤出机转速:45rpm静态混合器:温度:190℃吹膜机头:连接段温度:190℃,195℃;机头温度:200℃,202℃;二次加热水箱水浴温度:78℃定型套水温:16℃实施例2:产品:银色PVC热收缩膜,薄膜折径920mm,厚度0.075mm,收缩率:横向45~48%,纵向10~15%。配方:设备:挤出机:Ф70单螺杆挤出机,L/D=29:1,螺杆为带混炼头的屏障型结构。静态混合器:长度210mm;吹膜机头:口模直径Ф150;二次吹胀:红外线烘箱加热工艺:捏合(高速混合)出料温度:130℃;冷却混合出料温度:48℃干混料静置8小时挤出机塑化挤出:挤出机12345温度,℃165175187193200挤出机转速:48rpm静态混合器:温度:198℃吹膜机头:连接段温度:195℃,199℃;机头温度:200℃,205℃;二次加热水箱烘箱温度:83℃冷却风环风温:23℃实施例3金色PVC热收缩膜,薄膜折径550mm,厚度0.07mm,收缩率:横向45~48%,纵向0~5%。配方:原辅材料名称牌号配比(质量份)PVC树脂SG-5100有机锡7282.1增塑剂DOTP4.0增韧剂MBSB-5228.0促进塑化型加工助剂ACRK-120N3.0润滑型ACRK-175P1.2内润滑剂RGH-41.2外润滑剂AC-629A0.8金粉ResistCT0.5消光粉TS-1000.3设备:挤出机:Ф55单螺杆挤出机,L/D=26.5:1,螺杆为带混炼头的屏障型结构。静态混合器:长度275mm;吹膜机头:口模直径Ф110;二次吹胀:水浴加热工艺:捏合(高速混合)出料温度:130℃;冷却混合出料温度:50℃干混料静置8小时挤出机塑化挤出:挤出机转速:42rpm静态混合器:温度:195℃吹膜机头:连接段温度:195℃,200℃;机头温度:200℃,205℃;二次加热水箱水浴温度:80℃定型套水温:15℃应说明的是,以上实施例仅用以说明本发明的技术方案而非限制,尽管参照较佳实施例对本发明进行了详细说明,本领域的普通技术人员应当理解,可以对本发明的技术方案进行修改或者等同替换,而不脱离本发明技术方案的精神和范围,其均应涵盖在本发明的权利要求范围当中。当前第1页1 2 3