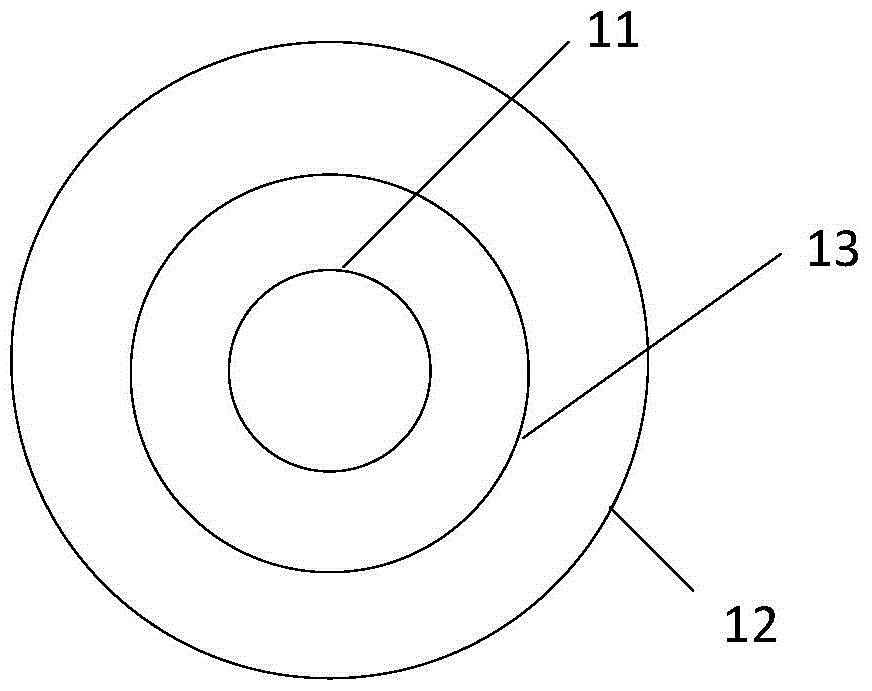
本发明涉及一种环型多层套管膜反应器以及采用该反应器进行(甲基)丙烯酸与C1-C4醇的酯化反应生产(甲基)丙烯酸酯的方法。
背景技术:(甲基)丙烯酸酯是一种大宗化工原料,其自聚或共聚形成的(甲基)丙烯酸酯类树脂被广泛用于涂料、胶黏剂、有机玻璃、纺织等的生产。(甲基)丙烯酸酯类可以由(甲基)丙烯酸和醇通过酸类催化剂催化进行酯化反应得到。酯化反应是一个可逆反应,因此转化率只能在一个平衡值以下,这取决于平衡常数。为提高转化率,一种方法可以使一种原料醇或酸大大过量的方法。这种方法往往导致副产物增多,选择性下降,对后续精制也带来一定困难;另一种方法是移除生成的水(例如专利200910012161.1的方法),这种方法较为有效。通常酯化反应除水的方法有直接蒸馏除水和加共沸剂脱水(如甲苯、环己烷等)。这些方法能耗较高,脱水效果不理想,共沸剂对环境污染较大。利用膜技术渗透汽化脱水是近些年新兴的脱水技术,这一技术已经在溶剂脱水方面有了很大的进展,但应用于酯化反应鲜有报道。生产(甲基)丙烯酸酯的主流工艺有无机酸催化(例如埃勒夫阿托化学专利95109453.X)、有机酸催化(例如巴斯夫专利200610073923.5),固体酸催化(例如中石化专利201110255431.9)及阳离子树脂催化剂催化酯化反应(例如触媒专利200710112480)。无机酸(如浓硫酸)及有机酸(如对甲苯磺酸)都属于均相催化剂,均相催化具有传质效果好、反应快等优点,但是强酸对设备具有很强的腐蚀。固体催化剂可以避免强酸与设备的直接接触,能大大降低催化剂对设备的腐蚀。采用固体催化剂生产制备(甲基)丙烯酸酯类的设备有几个问题,第一,采用固定床设备无法实现连续脱水,从而造成酯化反应的转化率低;第二,固体催化剂不流动使物料易形成沟流,导致催化剂利用效率低,传质效果较差;第三,(甲基)丙烯酸含有不饱和双键,容易产生聚合物,一般酯化设备的阻聚空气是从单点或几点加入,阻聚空气在反应体系中分布不均匀;第四,采用固体催化剂的酯化反应,醇类在催化剂表面吸附生成醚类杂质。针对以上问题,需要寻求一种新的制备(甲基)丙烯酸酯反应器,既能实现连续脱水,又能使固体催化剂与物料进行有效接触,且能够尽力避免副反应的发生。
技术实现要素:本发明的一个目的在于提供一种环型多层套管膜反应器,以克服现有酯化反应设备的种种不足。该反应器能够实现在酯化反应过程中连续脱水,降低了除水的能耗,并能提高原料与催化剂的传质效果,减少了醚类杂质的生成。本发明的另一个目的在于提供采用上述反应器生产(甲基)丙烯酸酯的方法,可有效提高酯化反应转化率,较少醚类副产。为实现上述目的,本发明的技术方案如下:一种环型多层套管膜反应器,主体是环型三层套管结构,包括由内而外同轴设置的内膜套管、中膜套管、外套管,内膜套管和中膜套管外部通过支撑网固定支撑,内膜套管上开设有一个水蒸汽出口,中膜套管上开设有一个进料口和一个出料口,外套管上开设有一个空气入口,中膜套管内腔设置有混合构件,在中膜套管出料口处安装有分离网,分离网固定在膜套管内壁上,在进料口和出料口之间(优选中间)安装单向阀,单向阀作用为保证流体从进料口沿环型反应器流动至出料口,且其允许固体催化剂通过。本发明的反应器中,所述的中膜套管内腔的混合构件包含推进式翅片和螺旋轨道,螺旋轨道围绕在内膜套管外侧,螺旋轨道在内膜套管轴截面上的投影与内膜套管轴线的夹角为α,α=15-30°,推进式翅片绕螺旋轨道运动。本发明的反应器中,所述的混合构件的推进式翅片由中心圈和位于中心圈圆周上的6~12片翅片构成,翅片在中心圈圆周上均匀或不均匀分布,优选均匀分布,所述的螺旋轨道穿过翅片中心圈,且螺旋轨道的外边缘与翅片中心圈内周贴合,使得中心圈紧扣在螺旋轨道上滑行推进,绕螺旋轨道运动。所述的混合构件的翅片推进结构,在流体推动下,双轴旋转推进。首先推进翅片沿螺旋轨道旋转推进,推进翅片本身也沿中心圈中轴自旋转推进。双旋转模式能有效混合催化剂和反应物料,防止催化剂沉降,有效提高反应的转化率,并且在应用在酯化反应时降低了醚类杂质的生成,其主要由于良好的混合效果,改变了醇类在固体催化剂表面的原有扩散和吸附过程,使化学反应选择性更偏向于酯化反应。本发明的反应器中,推进式翅片和螺旋轨道材质为碳钢、304、316或316L中的一种。本发明的反应器中,所述的的内膜套管和中膜套管主体为陶瓷膜组件,该陶瓷膜组件的立体形状是锥体、棱台、圆台、圆柱体、正方体或者长方体,优选圆柱体形式。陶瓷膜组件主要由陶瓷膜、耐压壳体、密封结构组成。陶瓷膜是主要的分离结构,材质是由Al2O3、SiO2、ZrO2或TiO2中材料中的一种经高温烧结制成,内膜套管和中膜套管的陶瓷膜组件的陶瓷膜为孔径0.3-1nm的纳滤膜;耐压壳体是316L材质的不锈钢壳体,密封材质用于组件连接密封。外套管主体为不锈钢材质,立体形状是锥体、棱台、圆台、圆柱体、正方体或者长方体,优选圆柱体形式。在本发明所述的反应器应用于酯化反应时,内膜套管作为渗透汽化水蒸气通道,可与负压抽吸系统相连接。内膜套管能够承受10~500kpa压力,优选为20~400kpa。中膜套管作为反应物料及产物进出通道,中膜套管能承受100~600kpa压力,优选为150~500kpa。外套管作为热空气进出通道,并能承受100~1000kpa压力,优选为150~500kpa,进一步优选为200~400kpa。本发明的反应器中,优选地,反应器主体水平放置,内膜套管、中膜套管、外套管径向截面的直径比为1:(2~6):(3~10),优选为1:(3~5):(6~7)。本发明的反应器中,所述的支撑网紧密包裹在内膜套管和中膜套管外部,支撑网网孔大小为0.1~1cm,优选为0.3~0.6cm,支撑网材质为碳钢、304、316或316L中的一种。采用本发明的反应器制备(甲基)丙烯酸酯的方法,包括以下步骤:(甲基)丙烯酸与C1~C4的醇通过原料泵输送至静态混合器混合均匀后,通过原料泵输送至换热器,预热到一定温度后,经过进料口进入环型多层套管膜反应器的中膜套管内腔,在混合构件的混合作用下,和装于中膜套管内的固体催化剂一起循环流动,原料经固体催化剂催化进行酯化反应,生成的水通过陶瓷膜组件渗透汽化进入内膜套管内腔而实现连续脱除,经水蒸汽出口通过负压抽吸排出系统并经冷凝器冷凝。空气经过预热器预热到一定温度后,通过空气入口进入外套管内腔,进入外套管内腔的热空气通过陶瓷膜组件均匀渗透到中膜套管内腔的反应物料内,既能实现反应物料均匀受热并维持酯化反应温度,同时能实现阻聚空气在物料中的均匀分布,减少(甲基)丙烯酸酯化过程中聚合物的生成。反应后的料液一部分在中膜套管内腔循环流动,另一部分通过反应器的出料口经分离网分离固体催化剂后,流出反应器。循环的料液与流出的料液的体积比为4:1~8:1本发明方法中,所述的固体催化剂为阳离子交换树脂或固体酸催化剂,催化剂空速为3~5h-1,按进料丙烯酸质量计,进料(甲基)丙烯酸与C1~C4的醇的摩尔比1:(0.5~2.0),优选1:(0.7~1.5),更优选为1:(0.8~1.3)。本发明方法中,甲基)丙烯酸与C1~C4的醇物料在反应器中的停留时间为1~8h,优选为2~5h。本发明方法中,(甲基)丙烯酸与C1~C4的醇的混合进料液预热后的温度为60~120℃,优选为70~100℃;进入外套管内腔热空气的温度为60~120℃,优选为70~100℃;反应器中膜套管内部反应温度为60~120℃,优选为70~100℃;内膜套管内腔压力为20~40kpa,中膜套管内腔压力为100~400kpa,外套管内腔压力为100~400kpa,外套管内腔压力高于中膜套管内腔压力5~15kpa。本发明的积极效果在于:第一,在反应器中使用固体催化剂,降低了均相催化剂对设备的腐蚀;第二,利用陶瓷膜渗透汽化脱水技术,能够实现在酯化反应过程中连续脱水,降低了除水的能耗,同时提高了(甲基)丙烯酸酯化反应的转化率和选择性;第三,固体催化剂在反应器内的循环流动形式,避免物料通过催化剂时形成沟流,提高传质效果;第四,实现了(甲基)丙烯酸酯化过程中阻聚空气的连续均匀加入;第五,反应器的混合构件减少了醚类杂质的生成。附图说明图1为(甲基)丙烯酸酯化反应的反应流程示意图。图2为环形多层套管膜反应器套管结构的径向截面图。图3为环形多层套管膜反应器套管结构的轴向截面图。图4为环形多层套管膜反应器内的混合构件的示意图。其中1为(甲基)丙烯酸原料罐,2为醇原料罐,3为静态混合器,4为流量计,5为预热器,6为生成水储罐,7为反应器,8为缓冲罐,9为真空泵,10为冷凝器,11为内膜套管,12为外套管,13为中膜套管,14-1为翅片推进器,14-2为螺旋轨道,15为空气入口,16为进料口,17为单向阀,18为出料口,19为水蒸汽出口。具体实施方式以下结合附图及实施例对本发明做进一步的说明。产物采用气相色谱分析,气相色谱分析条件如下:色谱柱:安捷伦HP-5(规格为30m×0.32mm×0.25mm),进样口温度:280℃,分流比:20:1柱流量:2ml/min,柱温:50℃,保持2min,5℃/min升高到80℃,保持5min,15℃/min升高到280℃,保持5min,检测器温度:280℃,H2流量:30ml/min,空气流量:400ml/min。(甲基)丙烯酸酯化反应的反应流程如图1所示,(甲基)丙烯酸与醇分别从(甲基)丙烯酸原料罐1,和醇原料罐2流出经过静态混合器3混合后通过流量计4控制流量后进入预热器5预热,预热后的物料进入反应器7。如图2-4所示,反应器7是环型三层套管结构,包括由内而外同轴设置的内膜套管11、中膜套管13和外套管12,内膜套管11设有一个水蒸汽出口19;中膜套管13设有一个进料口16和一个出料口18;在进料口16和出料口18之间安装有单向阀17;外套管12设有一个空气入口15。内膜套管11和中膜套管13外部加装支撑网用于固定支撑。支撑网网孔大小为0.5cm,支撑网材质为316L。中膜套管13内部设置混合构件,其由316L材质推进式翅片14-1和螺旋轨道14-2组成。推进式翅片14-1由中心圈和位于中心圈圆周上的9个翅片构成,翅片在中心圈圆周上均匀分布,螺旋轨道14-2穿过翅片中心圈。螺旋轨道14-2围绕在内膜套管11外侧,其在内膜套管11轴截面上的投影与内膜套管轴线的夹角α=15°。中膜套管13内部循环流动固体催化剂。内膜套管和中膜套管的陶瓷膜组件的立体形状为圆柱形,由南京久吾高科生产,型号为JWCM01*12,其中的陶瓷膜为单通道或多通道的孔径为0.3nm的纳滤膜,材质为ZrO2。反应物料通过进料口16进入反应器7的中膜套管13内腔,在混合构件的混合作用下,和固体催化剂一起循环流动。原料经固体催化剂催化进行酯化反应,生成的水通过陶瓷膜组件渗透汽化进入内膜套管11内腔而实现连续脱除,经水蒸汽出口19通过负压抽吸排出系统(缓冲罐8、真空泵9)并经冷凝器10冷凝。空气经过预热器5预热到一定温度后,进入反应器7的外套管12内腔。进入外套管12内腔的热空气通过陶瓷膜组件均匀渗透到中膜套管13内腔的反应物料内,既能实现反应物料均匀受热并维持酯化反应温度,同时能实现阻聚空气在物料中的均匀分布,减少(甲基)丙烯酸酯化过程中聚合物的生成。反应后的料液一部分在中膜套管13内腔循环流动,另一部分通过反应器7的出料口16经催化剂分离网分离固体催化剂后,流出反应器,循环料液与流出料液的体积比为4:1。实施例1利用本发明提供的环型多层套管反应器进行丙烯酸和甲醇的酯化反应,生成丙烯酸甲酯。反应器7水平放置,径向截面长度为0.92m,三层套管由内而外直径依次为0.1m,0.48m,0.6m。中膜套管13内部循环流动陶氏化学生产的Amberlyst25wet阳离子树脂催化剂,丙烯酸质量空速为3.65h-1。将摩尔比1.12:1的丙烯酸和甲醇通过静态混合器3混合均匀,以10kg/h的速度通过原料泵输送至预热器5预热到75℃,然后进入反应器7的中膜套管13内。内膜套管11内部压力为30KPa,中膜套管13内部压力为300KPa,外套管12通入预热到75℃的空气,压力为310kpa。原料在反应器中的停留时间为2.9h。经过2.9h的酯化反应,甲醇的转化率达到72.4%,丙烯酸甲酯的选择性达到97.6%,反应器出料中大分子聚合物含量0.09wt%,二甲醚杂质含量120ppm。对比例1利用通用的固定床反应器进行丙烯酸和甲醇的酯化反应,生成丙烯酸甲酯。固定床反应器为高度0.92m,直径0.48m的立式容器。在固定床内部散堆装填Amberlyst25wet阳离子树脂催化剂,丙烯酸质量空速为3.65h-1。将摩尔比1.12:1的丙烯酸和甲醇通过静态混合器混合均匀,以10kg/h的速度通过原料泵输送至预热器预热到75℃,然后进入固定床反应器内。固定床反应器内部压力为300kpa。原料在反应器中的停留时间为2.9h。经过2.9h的酯化反应,甲醇的转化率达到60.7%,丙烯酸甲酯的选择性达到97.2%,反应器出料中大分子聚合物含量0.32wt%,二甲醚杂质含量430ppm。实施例2利用本发明提供的环型多层套管反应器进行丙烯酸和乙醇的酯化反应,生成丙烯酸乙酯。反应器7水平放置,径向截面长度为0.92m,三层套管由内而外直径依次为0.1m,0.6m,1m。中膜套管13内部循环流动Amberlyst25wet阳离子树脂催化剂,丙烯酸质量空速为3.65h-1。将摩尔比1.10:1的丙烯酸和乙醇通过静态混合器3混合均匀,以10kg/h的速度通过原料泵输送至预热器5预热到80℃,然后进入反应器7的中膜套13管内。内膜套管11内部压力为40KPa,中膜套管13内部压力为150KPa,外套管12通入预热到80℃的空气,压力为160kpa。原料在反应器7中的停留时间为2.3h,经过2.3h的酯化反应,乙醇的转化率达到78.4%,丙烯酸乙酯的选择性达到95.1%,反应器出料中大分子聚合物含量0.10wt%,二乙醚杂质含量90ppm。对比例2利用通用的固定床反应器进行丙烯酸和乙醇的酯化反应,生成丙烯酸乙酯。固定床反应器为高度0.92m,直径0.48m的立式容器。在固定床内部散堆装填Amberlyst25wet树脂催化剂,丙烯酸质量空速为3.65h-1。将摩尔比1.10:1的丙烯酸和乙醇通过静态混合器混合均匀,以10kg/h的速度通过原料泵输送至预热器预热到80℃,然后进入固定床反应器内。固定床反应器内部压力为160kpa。原料在反应器中的停留时间为2.3h。经过2.3h的酯化反应,乙醇的转化率达到67.0%,丙烯酸乙酯的选择性达到94.3%,反应器出料中大分子聚合物含量0.41wt%,二乙醚杂质含量380ppm。实施例3利用本发明提供的环型多层套管反应器进行丙烯酸和正丁醇的酯化反应,生成丙烯酸丁酯。反应器7水平放置,径向截面长度为0.92m,三层套管由内而外直径依次为0.1m,0.3m,0.7m。中膜套管13内部循环流动陶氏生产的Amberlyst39wet阳离子树脂催化剂,丙烯酸质量空速为3.65h-1。将摩尔比1:1.20的丙烯酸和丁醇通过静态混合器3混合均匀,以10kg/h的速度通过原料泵输送至预热器5,预热到95℃,然后进入反应器7内的中膜套管13内。内膜套管11内部压力为20KPa,中膜套管13内部压力为350KPa,外套管通入预热到95℃的空气,压力为360kpa。原料在反应器7中的停留时间为3h。经过3h的酯化反应,丙烯酸的转化率达到68.3%,丙烯酸丁酯的选择性达到98.7%,反应器出料中大分子聚合物含量0.12wt%,二丁醚杂质含量150ppm。对比例3利用通用的全混流式搅拌床反应器,进行丙烯酸和正丁醇的酯化反应,生成丙烯酸丁酯,在搅拌床反应器顶部连接分水器进行连续脱水。反应器为0.05m3的圆柱体容器。反应器的高径比为1.5:1,装填陶氏生产的Amberlyst39wet树脂催化剂,丙烯酸质量空速为3.65h-1。将摩尔比1:1.20的丙烯酸和丁醇通过静态混合器混合均匀,以10kg/h的速度通过原料泵输送至预热器预热到95℃,然后进入搅拌床反应器内,搅拌床内部压力为20KPa,折叶搅拌桨转速为100r/min,原料在反应器中的停留时间为3h。经过3h的酯化反应,丙烯酸的转化率达到50.4%,丙烯酸丁酯的选择性达到97.5%,反应器出料中大分子聚合物含量0.56%,二丁醚杂质含量510ppm。表1环型多层套管膜反应器与通用反应器酯化效果对比