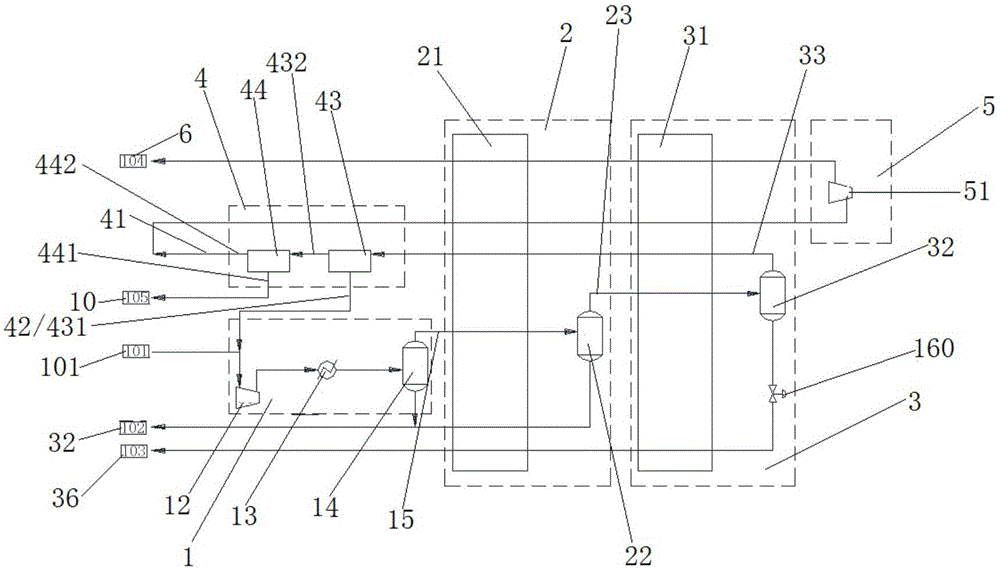
本发明属于化工及石化
技术领域:
,具体涉及一种聚烯烃尾气回收方法。
背景技术:
:在聚烯烃生产过程中,从反应器、闪蒸罐、脱气仓等装置排放的气体(一般称为尾气)中含有大量惰性气体(例如氮气、饱和烃)以及未反应的烯烃单体等其他气体,其中的烃类具有非常高的经济价值,而氮气经提纯后亦可循环使用(例如作为脱气仓吹扫气)。传统的尾气回收工艺一般采用压缩冷凝法,其是利用各种组分的沸点不同,通过降低温度使部分气体液化而实现分离,由于该法在要求高的回收率时能耗较高,投资较大,不能完全满足人们的要求。为此,人们陆续开发了以膜、变压吸附为代表的分离因子更大、效率更高的方法(例如US6706857、US5769927),这些方法通常需要和压缩冷凝法进行组合,其原因是分离得到的产品是气相,其纯度或压力达不到直接回用的要求。此外,人们对于通过温度降低实现液化的方法也进行了改进,最突出的改进是利用透平膨胀或节流膨胀实现自深冷的技术(例如CN201310444283)。人们也发现各种方法的不同组合方式所产生的效果不同,即从分离工程角度看,分离序列的设计至关重要。不同分离序列所产生的回收率、产品纯度、能耗、投资可能差异很大。遗憾的是,现有技术仅仅对现有各种分离技术进行简单的组合,并没有对最优的分离序列进行深入的开发,因而各种问题。CN200910038599.7公开了一种聚乙烯装置尾气完全回收利用的方法,该流程的分离序列为压缩冷凝分离、烃膜分离、变压吸附分离。然而该方法无法将重烃和轻烃分离,且得到的烃类浓度也不高;氮气和氢气无法分离,造成当氢气浓度较高时,氮气无法作为脱气仓吹扫气循环使用;另外从变压吸附出来渗余气仍然具有较高的压力,该方法没有有效利用,导致该方法工艺能耗也较高。CN201310444283公开了一种用于在烯烃聚合物生产中回收排放气的系统和方法,该流程的分离序列为压缩冷凝分离、氢膜分离、自深冷分离,该工艺提到了用氢膜对尾气进行氢气分离,从而提高氮气的纯度,使回收氮气能作为脱气仓吹扫气循环使用,由于其氢膜分离设置自深冷分离前,导致氢气透过膜的同时,大量的烃类组分也随之透过,导致烃类回收率降低;另外后续自深冷分离中,其本质仅为一次气液平衡分离,由于平衡分离温度的限制,导致分离罐顶部出来的氮气仍含有少量烃类,无法处理,不能得到较高纯度的氮气。US5769927公开了一种烯烃回收工艺,该流程的分离序列为:压缩冷凝分离、膜分离。受限于烃膜组件的使用条件,该工艺的冷凝温度较高(约-30℃),通过冷凝分离能将部分重烃分离出来,但是大量轻烃需要通过后续烃膜分离工序进行分离。而该工艺将烃膜分离的轻烃全部返回压缩机,该流程唯一烃类分离出口只有压缩冷凝分离中的分离罐处,这样的分离序列设置会造成膜分离返回压缩机的气体循环量很大,且压缩冷凝前气相中烃类含量需累积的很高,排放气回收系统原始进料中的烃类才能在此处全部冷凝下来,压缩机功耗急剧增大。另外在聚烯烃尾气的回收应用中,该工艺没有对重烃和轻烃进行分离,变无法对重烃和轻烃进行分别回收;没有对氮气和氢气进行分离,使得氮气不宜作为脱气仓吹扫氮气循环使用,因为氢气的循环累积会对脱气仓的生产运行带来安全隐患。CN201510294040.6公开了一种气相法聚烯烃排放气尾气的回收方法,该流程的分离序列为压缩冷凝分离、普通深冷分离、烃膜和氢膜分离、自深冷分离。该专利已经提出,在分离序列中加入烃膜分离,然而上述分离序列的设置,会导致烃膜分离处理量很大,因为在普通深冷分离序列后,气相中仍含有大量的烃类,导致烃膜返回压缩机气量非常大,能耗很大;其次由于由于平衡分离温度的限制,气体经烃膜、氢膜分离后,进入深冷分离,只有在更低的分离温度下,才能得到高纯度的氮气,因此该深冷分离序列中的设备投资、运行能耗都会比前述专利中的深冷分离工序要高;另外该专利自身也指出在普通深冷分离工序中,当尾气中烃类浓度不高时,需额外补充冷量,遗憾的是,聚烯烃尾气中烃类含量一般均较低,因此该方法需要额外补充低温冷量。受限于膜组件使用温度条件,普通深冷分离温度不能太低,导致在普通深冷分离工序中烃类回收量不多,因此其后的烃膜分离工序主要作用为分离烃类而不是提纯氮气。尽管氢膜分离工序设置在烃膜分离工序后,然而由于烃膜分离并未完全分离烃类,因此氢膜分离工序中仍会有一定量的烃类随渗透侧的氢气排放至火炬,从而造成烃类的损失。US6706857公开了一种烯烃单质的回收方法,该工艺的分离序列为:深冷分离、变压吸附分离,该工艺主要是将变压吸附应用在了聚烯烃尾气领域,并对吸附剂做出了一些规定。但其深冷分离工序采用额外冷量进行深冷分离,能耗很大,显然不经济;依据该专利的描述,其变压吸附分离工序的设置主要也是起分离烃类的作用,因此其返回压缩机的气量会很大,压缩机能耗会增加很多;该专利的实施例中尾气不含重烃,而实际上目前聚烯烃工艺(包括聚乙烯和聚丙烯工艺)很多都含有重烃组分,因此该工艺无法将重烃和轻烃分离;另外该工艺无法将氢气和氮气分离,从而获得较纯的氮气。US574350公开了一种从聚烯烃尾气中回收烃类的工艺,该工艺的分离序列主要为压缩冷凝分离、油吸收分离、深冷分离。油吸收的本质也是气液平衡,因此除非找到一种高效吸收剂,才能有效吸收尾气中的烃类,这种高效吸收剂应具有两个特点:一是对烃类具有良好的吸收效果;二是该吸收剂本身为难挥发物质。然而该专利并没有提到这类吸收剂,而是采用重烃之类作为吸收剂,因此油吸收效果并不好。在深冷分离中,与前述专利CN201310444283一样,分离罐顶部出来的氮气仍含有少量烃类,无法进一步处理,不能得到较高纯度的氮气。此外该工艺也没有对氮气中的氢气进行分离操作。针对现有技术存在的问题,本发明提供了一种聚烯烃尾气回收方法。技术实现要素:本发明的聚烯烃尾气回收方法能够降低压缩机的能耗,能够有效提高氮气和烃类的纯度及氮气和烃类的回收率,有助于节省能耗和投资,降低了物耗。为实现上述目的,本发明提出了一种聚烯烃尾气回收方法,其中,所述聚烯烃尾气回收方法包括:其依次包括压缩冷却分离工序、重烃分离工序、轻烃分离工序、氮气提纯工序和透平膨胀工序;所述氮气提纯工序中包含膜分离过程;所述轻烃分离工序中至少包括一个气液分离过程,所述气液分离过程得到的第一气体与所述轻烃分离工序中的物流换热升温后,进入所述重烃分离工序进一步升温,升温后的所述第一气体进入所述氮气提纯工序,所述氮气提纯工序中的膜分离后的第一输出气依次进入所述重烃分离工序和所述轻烃分离工序与其中的物流换热降温,降温后的所述第一输出气体进入所述透平膨胀工序。如上所述的聚烯烃尾气回收方法,其中,所述压缩冷却分离工序、所述重烃分离工序、所述轻烃分离工序、所述氮气提纯工序和所述透平膨胀工序中的至少一个工序使用外部冷却介质进行冷却,所述外部冷却介质的温度高于或等于外部环境温度。如上所述的聚烯烃尾气回收方法,其中,所述压缩冷却分离工序包括:尾气及循环物料共同进入压缩机增压后,再进入冷却器进行冷却,所述冷却器的冷却介质是循环水或空气。如上所述的聚烯烃尾气回收方法,其中,所述重烃分离工序包括:从所述压缩冷却分离工序输出的第一尾气进入第一多流股换热器,所述第一尾气降温至重烃分离温度后,进入至少一个第一气液分离罐分离出重烃。如上所述的聚烯烃尾气回收方法,其中,所述第一多流股换热器为板翅式、绕管式换热器或二者的组合。如上所述的聚烯烃尾气回收方法,其中,所述轻烃分离工序包括:从所述重烃分离工序输出的第二尾气进入第二多流股换热器,所述第二尾气降温至轻烃分离温度后,进入至少一个第二气液分离罐分离出轻烃。如上所述的聚烯烃尾气回收方法,其中,所述第二多流股换热器为板翅式、绕管式换热器或二者的组合。如上所述的聚烯烃尾气回收方法,其中,从所述膜分离过程输出的第二输出气返回至所述压缩冷却分离工序中的所述压缩机入口或返回至排放气存储器,所述膜分离过程包括至少一组烃膜分离组件和或至少一组氢膜分离组件或所述第一气体依次进入所述氢膜分离组件和所述烃膜分离组件。如上所述的聚烯烃尾气回收方法,其中,所述膜分离过程包括一组烃膜分离组件和一组氢膜分离组件,所述第一气体依次进入所述烃膜分离组件和所述氢膜分离组件。如上所述的一种聚烯烃尾气回收方法,其中,所述尾气进入所述压缩冷却分离工序后,所述尾气先进入干燥设备进行干燥处理,再进入所述重烃分离工序。本发明通过对压缩冷却分离工序、重烃分离工序、轻烃分离工序、氮气提纯工序和透平膨胀工序合理安排,提出了最优的分离序列,从而能显著降低压缩机能耗,同时不需要外部输入低于环境温度的冷却介质,氮气和烃类的纯度以及回收率都得到提高,节省了能耗和投资,以及降低了物耗。附图说明在此描述的附图仅用于解释目的,而不意图以任何方式来限制本发明公开的范围。另外,图中的各部件的形状和比例尺寸等仅为示意性的,用于帮助对本发明的理解,并不是具体限定本发明各部件的形状和比例尺寸。本领域的技术人员在本发明的教导下,可以根据具体情况选择各种可能的形状和比例尺寸来实施本发明。图1为本发明的聚烯烃尾气回收方法的工艺示意图(一);图2为本发明的聚烯烃尾气回收方法的工艺示意图(二);图3为本发明的聚烯烃尾气回收方法的工艺示意图(三)。具体实施方式结合附图和本发明具体实施方式的描述,能够更加清楚地了解本发明的细节。但是,在此描述的本发明的具体实施方式,仅用于解释本发明的目的,而不能以任何方式理解成是对本发明的限制。在本发明的教导下,技术人员可以构想基于本发明的任意可能的变形,这些都应被视为属于本发明的范围,下面将结合附图对本发明作进一步说明。图1至图3分别为本发明的聚烯烃尾气回收方法的工艺示意图(一)、聚烯烃尾气回收方法的工艺示意图(二)和聚烯烃尾气回收方法的工艺示意图(三)。需要在此说明的是,在本发明中轻烃指C2Hn、C3Hn物质、重烃指C4+Hn等物质。如图1至图3所述,一种聚烯烃尾气回收方法,其中,其依次包括压缩冷却分离工序1、重烃分离工序2、轻烃分离工序3、氮气提纯工序4和透平膨胀工序5,其中,氮气提纯工序4中包含膜分离过程;轻烃分离工序3中至少包括一个气液分离过程,该气液分离过程得到的第一气体33与轻烃分离工序3中的物流换热升温后,进入重烃分离工序2进一步升温,升温后的第一气体33进入氮气提纯工序4,氮气提纯工序4中的膜分离后的第一输出气依次进入重烃分离工序2和轻烃分离工序3与其中的物流换热降温,降温后的第一输出气体进入透平膨胀工序5。具体的,压缩冷却分离工序1包括:尾气101及循环物料共同进入压缩机12增压,推荐的压缩机12出口压力为0.8MPa~2.5MPa,再进入冷却器13进行冷却,在一具体实施例中,冷却器13的冷却介质是循环水或空气。进一步地,尾气101进入压缩冷却分离工序1后,尾气101先进入干燥设备(图中未示出干燥设备)进行干燥处理,再进入重烃分离工序2。干燥器的干燥效果应保证后续轻烃分离工序3不产生冰堵现象,由于在低温环境下,尾气101中含有少量水时,设备会产生冰堵现象,因此,通过增加干燥器可以防止冰堵现象的发生。进一步地,在本发明中,冷却器13通过缓冲罐14后再进入重烃分离工序2中,以实现向重烃分离工序2中平稳地输送烯烃尾气,当然,缓冲罐14的出液端口可与重烃回收装置32连通,以实现初步回收重烃的目的。在一具体实施例中,冷却器13与缓冲罐14之间设有干燥器(图中未示出干燥器),且干燥器的干燥效果应保证后续轻烃分离工序3不产生冰堵现象,由于在低温环境下,尾气中含有少量水时,设备会产生冰堵现象,因此,通过增加干燥器可以防止冰堵现象的发生。压缩机12将原料尾气101压缩至一定压力(例如0.8MPa~2.5MPa),可采用循环水或空气冷却至略高于环境温度(例如40℃)。如原料尾气含少量水分,则可设置干燥装置进行除水操作,以防止冰堵现象的发生。具体的,重烃分离工序2包括:从压缩冷却分离工序1输出的第一尾气15进入第一多流股换热器21,第一尾气15降温至重烃分离温度后,进入至少一个第一气液分离罐22分离出重烃,从第一气液分离罐22顶部输出的第二尾气23进入到轻烃分离工序3中,从第一气液分离罐22底部分离出的重烃经过第一多流股换热器21提供冷量后再进入到重烃回收装置32中,以实现回收重烃。进一步地,第一多流股换热器21为板翅式、绕管式换热器或二者的组合,当然也可用多个普通换热器替代。来自压缩冷却分离工序1的物流进入第一多流股换热器21,利用后续的透平膨胀工序5提供的冷量在第二气液分离罐22中进行重烃分离,液相经节流闪蒸后返回第一多流股换热器21提供冷量,分离温度应根据重烃的分压、沸点、回收率等因素决定,推荐的分离温度为-20℃~-70℃。在此时分离重烃也能改善后续轻烃分离工序中重烃冰堵问题。具体的,轻烃分离工序3包括:从重烃分离工序2输出的第二尾气23进入第二多流股换热器31,第二尾气23降温至轻烃分离温度后,进入至少一个第二气液分离罐32分离出轻烃。进一步地,第二多流股换热器31为板翅式、绕管式换热器或二者的组合,当然也可用多个普通换热器替代。第一气液分离罐23顶部出来的物流进入第二多流股换热器31,利用后续的透平膨胀工序5提供的冷量在第二气液分离罐32中进行轻烃分离;第二气液分离罐32底部中分离出的液相经节流闪蒸后依次返回第二多流股换热器31和第一多流股换热器21提供冷量,然后该液相进入到轻烃回收装置36中,从而实现轻烃的回收,第二气液分离罐32顶部出来的气相33(即为第一气体33)依次返回至第二多流股换热器31和第一多流股换热器21进行复热操作,从而实现由气液分离过程中得到的第一气体33与轻烃分离工序3中的物流换热升温后,进入重烃分离工序2进一步升温,升温后的第一气体33进入氮气提纯工序4。其中,第二气液分离罐32的分离温度应根据轻烃的分压、沸点、回收率等因素决定,推荐的分离温度为-90℃~-140℃。进一步地,如图3所示,第二气液分离罐32中分离出的液相依次进入第三气液分离罐161和第四气液分离罐162再到轻烃回收装置36,其中,从第三气液分离罐161顶部出来气体返回至压缩机12,第三气液分离罐161分离出的液相依次经第二多流股换热器31和第一多流股换热器21之后再进入到第四气液分离罐162中,且第四气液分离罐162的顶部出来气体进入到到轻烃回收装置36中,第四气液分离罐162分离出的液体返回至压缩机12,通过这样的设置方式能够够进一步地提高回收的轻烃的纯度。具体的,在本发明中,氮气提纯工序4中的膜分离后的第一输出气41(也可称为渗余气体41)依次进入第一多流股换热器21和第二多流股换热器31,从而实现第一输出气41与重烃分离工序2和轻烃分离工序3中的物流换热降温,降温后的第一输出气体41进入透平膨胀工序5,氮气提纯工序4中的膜分离过程输出的第二输出气42返回至压缩冷却分离工序1中的压缩机12入口,从而实现气体的充分回收利用,在本发明中,膜分离过程包括至少一组烃膜分离组件43和/或至少一组氢膜分离组件44。在一具体实施例中,膜分离过程包括一组烃膜分离组件43和一组氢膜分离组件44,第一气体33依次进入烃膜分离组件43和氢膜分离组件44,当然第一气体33也可以依次进入氢膜分离组件44和烃膜分离组件43,也即烃膜分离组件43及氢膜分离组件44的顺序可以调整,烃膜分离组件43在前或者氢膜分离组件44在前都可以,在此不做具体限制。烃膜分离组件43内部包括烃膜,其中,在本发明中,烃膜为烃类组分渗透速率高于氢气、氮气组分的膜,可选用橡胶态高分子膜,如有机硅氧烷类高分子膜等,烃类组分在此类材料的渗透速率高于氢气、氮气等气体,氢膜分离组件44内部包括氢膜,在本发明中,氢膜为氢气组分渗透速率高于氮气、烃类组分的膜,可选用玻璃态高分子膜,如聚酰亚胺膜、聚芳酰胺膜、聚砜膜等,氢气在此类材料的渗透速率高于氮气、烃类等气体。上述烃膜分离组件43和氢膜分离组件44的结构为螺旋卷式膜组件、板框式膜组件、中空纤维膜组件中的任意一种。在一具体实施例中,氢膜分离组件44的渗透气441与排放气存储器10相连通,烃膜分离组件43的渗透气431可与排放气存储器10相连通(如图2所示),或者与压缩机12的进气端相连通(如图1或图3所示),其中,烃膜分离组件43的渗透气431与排放气存储器10气连通时可降低压缩机12的能耗,但造成烃类损耗适当增加,烃膜分离组件43的渗透气431与压缩机12的进气端相连通,可降低烃类损耗,但会适当增加压缩机12的能耗。当烃膜分离组件43的渗透气431中的烃类含量较高时,可将该渗透气431与压缩机12相连通,当烃膜分离组件43的渗透气431中的烃类含量较低时,可将渗透气431与排放气存储器10相连通,即烃膜分离组件43的渗透气431可根据实际情况选择与排放气存储器10或压缩机12中的一个相连通。烃膜分离组件43的渗余气432进入到氢膜分离组件44中,氢膜分离组件44的渗余气442即为本发明中的氮气提纯工序4中的膜分离后的第一输出气41。复热后的第一气体33进入烃膜分离过程,将烃膜分离后的渗透侧气体431(主要含烃类)返回至压缩机12入口,烃膜分离后的渗余气432进入氢膜分离过程,将氢膜分离后的渗透侧气体441返回至排放气存储器10,氢膜分离后的渗余气442(主要是高纯氮气)依次进入重烃分离工序2和轻烃分离工序1进行降温。具体的,在本发明中,渗余气442依次通过第一多流股换热器21和第二多流股换热器31进行降温。如果烃膜分离过程的渗余气进入氢膜分离过程,则因氢气的累积问题,氢膜渗透侧气体需排至本系统外,即渗透侧气体441返回至排放气存储器10。第一输出气41返回至重烃分离工序2和轻烃分离工序3进行降温后进入透平膨胀工序5中的透平膨胀机51进行膨胀,膨胀后的气体返回轻烃分离工序3和重烃分离工序2提供低温冷量,从而实现使气体的冷量得到充分利用,有利于降低能耗,然后该气体进入氮气回收装置6中。进一步地,在本发明中,压缩冷却分离工序1、重烃分离工序2、轻烃分离工序3、氮气提纯工序4和透平膨胀工序5中的至少一个工序使用外部冷却介质进行冷却,且外部冷却介质的温度高于或等于外部环境温度,从而有利于降低能耗。在一具体实施例中,只有压缩冷却分离工序1使用外部冷却介质进行冷却,其他工序并没有使用外部冷却介质进行冷却。当然,在本发明中,压缩冷却分离工序1、重烃分离工序2、轻烃分离工序3、氮气提纯工序4和透平膨胀工序5中的所有工序也可以不使用外部冷却介质。本发明的重烃分离工序2和轻烃分离工序3中的低温冷量完全来自透平膨胀工序5中的膨胀冷量,仅在压缩冷却分离工序1中采用了不低于环境温度的外部冷却介质,即该外部冷却介质的温度大于或等于环境温度,而对于其他工艺来说,要达到相同烃类、氮气纯度和回收率,必须要加入外部低温冷却介质。本发明将烃类分离分为重烃分离工序2和轻烃分离工序3,主要目的如下:1、实现重烃和轻烃的分离;2、防止重烃在轻烃分离工序3中冰堵。需要说明的是,如尾气中重烃含量较少,不会在轻烃分离工序3中产生冰堵现象,且工艺无需将重烃和轻烃分离,则重烃分离工序2可取消,即取消本发明的重烃分离工序2,其中,轻烃分离工序3可称为烃类分离工序。需要进一步说明的是,图2所示的工艺为:烃膜的渗透气431直接排至本系统外,不返回压缩机12,这样会降低压缩机12的能耗,烃类损耗会适当增加。图3所示的工艺为:第二气液分离罐32底部出来的液相经节流阀160节流后进入第三气液分离罐161(或称为闪蒸罐)进行气液分离,气相返回压缩机12;液相依次经第二多流股换热器31和第一多流股换热器21换热后进入第四气液分离罐162进行进一步地气液分离,第四气液分离罐162的顶部出来气体进入到到轻烃回收装置36中,第四气液分离罐162分离出的液体返回至压缩机12,通过这样的设置方式能够够进一步地提高回收的轻烃的纯度。本文中的循环物料是指重烃分离工序2、轻烃分离工序3和氮气提纯工序4中再次返回至压缩机12的物料。图1至图3中,在第一多流股换热器21和第二多流股换热器31中,物料从左向右的过程为降温过程,物料从右向左的过程为升温过程。本文中的气液分离罐分离出的气相出口设在气液分离罐的顶部,气液分离罐分离出的液相出口设在气液分离罐的底部。将本发明的聚烯烃尾气回收方法应用在一实际现场中,并与之前的回收系统进行对比。实施例一某石化企业聚乙烯装置高压凝液罐后尾气温度:-10℃,压力:1.2MPaG,因为该尾气已经具有一定的压力,不再增设压缩机。采用附图3的工艺流程,为了说明分离序列的重要性,对比例采用CN201310444283的工艺,其分离工序可概括为压缩冷却分离工序、氢膜分离工序、重烃分离工序、轻烃分离工序的工艺。对比例和实施例的结果如表1所示。将对比例和实施例的结果进行对比,对比分析结果如表2所示。表1对比例和实施例一结果表2对比结果名称轻烃纯度(%)烃类回收率(%)氮气纯度(%)氮气回收率(%)排放气流量(kg/h)对比例91.7398.3688.7290.26215.07实施例98.5699.8897.8990.91174.65本实施例是聚乙烯尾气的回收,由表2可以看出,在不增加能耗的情况下,本实施例的所有指标均优于对比例,特别是氮气纯度和轻烃纯度远高于对比例。由此说明了不同分离序列会造成截然不同的分离效果。实施例二某企业聚丙烯尾气进入压缩机前温度:42℃,压力:1.16barA,采用附图3的工艺流程,对比例仍采用CN201310444283的工艺,其分离序列为压缩冷却分离、氢膜分离、重烃分离、轻烃分离的工艺,该工艺如要得到高纯度氮气,必须要采用更低的温度,无论从投资、能耗上还是从烃类纯度、氮气回收率上看,都是不合适的,因此本实施例和对比例在保证压缩机能耗一致的前提下进行了对比,对比例结果如表3所示,实施例结果如表4所示。将表3和表4的结果进行对比,对比结果如表5所示。表3对比例结果表4实施例二结果表5对比结果名称轻烃纯度(wt%)烃类回收率(wt%)氮气纯度(wt%)氮气回收率(wt%)排放气流量(kg/h)对比例99.2894.3798.8489.3248实施例99.4199.8699.590230在压缩机能耗一致的情况下,本工艺的实施例,所有指标均优于对比例,特别是烃类回收率和氮气纯度这两个指标有了较大的提高。实施例三某企业聚丙烯尾气进入压缩机前温度:40℃,压力:1.2barA,本实施例的对比例采用US5769927的工艺,为了便于对比,在该工艺基础上增加氢膜分离,分离序列为压缩冷却分离、烃膜、氢膜分离的分离序列,本实施例和对比例均以得到氮气纯度为99.5%的高纯氮作为比较条件,对比例和实施例结果如表6所示。表6对比例和实施例三结果表7能耗对比结果压缩机功耗(kw)冷凝器功耗(kw)备注对比例17541930冷凝器需采用冰机制冷到-30℃实施例900901仅用循环水冷却到40℃即可从上表可以看出,同样得到纯度为99.5%的氮气,采用分离序列为压缩冷却分离工序、烃膜分离、氢膜分离的对比例,其压缩机进口流量和出口压力都要高于实施例1,因此其压缩机功耗功耗远远大于实施例1,而且对比例需采用额外冷源将压缩后尾气冷凝到-30℃左右才能将烃类回收,相对于实施例1的循环水来说,又增加了很多能耗,另外对比例也未将重烃和轻烃分离。从上述三个实施例可以看出,本发明的聚烯烃尾气回收系统能够实现显著降低压缩机能耗,同时不需要外部输入低于环境温度的冷却介质,氮气和烃类的纯度以及氮气和烃类的回收率都提高,节省了能耗和投资以及降低了物耗的优点。本发明的重烃分离工序2和轻烃分离工序3中的低温冷量完全来自透平膨胀工序5中的膨胀冷量,仅在压缩冷却分离工序1中采用了不低于环境温度的外部冷却介质,而对于其他工艺来说,要达到相同烃类、氮气纯度和回收率,必须要加入外部低温冷却介质。本发明将烃类分离分为重烃分离工序和轻烃分离工序,主要目的如下:1、实现重烃和轻烃的分离;2、防止重烃在轻烃分离工序中冰堵。本发明通过对压缩冷却分离工序、透平膨胀工序、烃分离工序和氮气提纯工序合理安排,提出了最优的分离序列,从而实现显著降低压缩机能耗,同时不需要外部输入低于环境温度的冷却介质,氮气和烃类的纯度以及氮气和烃类的回收率都提高,节省了能耗和投资以及降低了物耗。虽然已经参考优选实施例对本发明进行了描述,但在不脱离本发明的范围的情况下,可以对其进行各种改进并且可以用等效物替换其中的部件。尤其是,只要不存在结构冲突,各个实施例中所提到的各项技术特征均可以任意方式组合起来。本发明并不局限于文中公开的特定实施例,而是包括落入权利要求的范围内的所有技术方案。当前第1页1 2 3