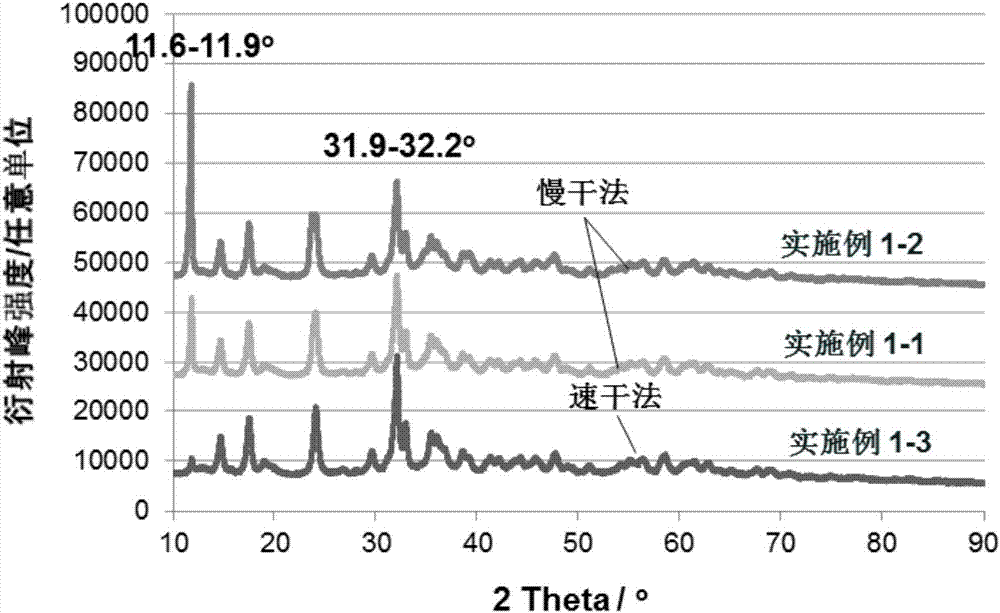
本发明涉及催化剂制备领域,具体地,涉及一种调控cu系催化剂前驱体晶相结晶度的方法、由所述方法调控得到的cu系催化剂前驱体、一种制备cu系催化剂的方法以及由该方法制备得到的cu系催化剂。
背景技术:
甲醇作为c1化学中的重要成员,被广泛地用于包括合成甲醛、乙酸、甲基叔丁基醚及其它精细化学品的基础化工原料中,近年来它也被应用于车用非化石燃料领域。全球范围内的甲醇需求量及年产能也在逐年攀升。研究开发出高活性、稳定性及长寿命的甲醇催化剂是保证甲醇产能与需求相匹配的关键。甲醇的工业合成方法主要是以含有少量co2的合成气(h2和co)为原料,在一定的温度(200~300℃)及压力(50~300bar)下合成。工业甲醇合成催化剂含主要成分cu、zn、al以及第四组分0-5%的mn、mg或zr中的一种或几种,由含金属盐离子的硝酸盐或硫酸盐与含碱金属离子的碳酸盐或碳酸氢盐采用并流共沉淀法制备。spencer教授等人(appliedcatalysisa:general,85(1992)1-11)认为在并流共沉淀过程中,cu/zno催化剂的活性前驱体铜盐首先形成蓝色的无定型的碱式碳酸铜、锌母体[(cu1-xznx)2co3(oh)2](x=0.33)。后随老化过程的进行转化为蓝绿色高cu/zn比的[cu5-xznx(co3)2(oh)6],然后释放出部分co2,后逐步转变为蓝绿色结晶态的碱式碳酸铜、锌[(cu1-xznx)2co3(oh)2](x=0.33)。此过程进行较快,需要将分离出的中间体进行快速洗涤及分析方可得到。但如未经洗涤过程将加速老化,无法捕捉到中间体。kondrat等人最近发表到nature上的文章(nature531,(2016)83–87)也支持形成无定型cu/zn催化剂前驱体的说法,并且他们成功地使用超临界反溶剂法合成了无定型的cu/zn催化剂前驱体,该无定型的cu/zn催化剂前驱体包含结构(cu,zn)7(co3)5(oh)4·5h2o,该无定型结构在低温水气变换反应中表现出良好的活性和稳定性,优于工业催化剂。kowalik等人(journalofmolecularcatalysisa:chemical392(2014)127-133)在研究cu/zno/al2o3体系催化剂时发现在老化初期(1h),沉淀主要以绿铜锌矿为主[cu2zn3(co3)2(oh)6],当老化时间延长至10h以上可以观测到主晶相为类水滑石[cuxzn6-xal2(oh)16(co3)4·h2o]。洗涤焙烧后的催化剂显示,绿铜锌矿相为主要成分的催化剂较类水滑石相为主要成分的催化剂有更大的cu表面、更高的甲醇合成活性,所以形成绿铜锌矿是甲醇合成催化剂前驱体的关键组分。cn103480377a描述了一种铜系甲醇合成催化剂的制备方法,其中,含cu、zn二元母体浆料采用晶种[cu2co3(oh)2]诱导沉淀法制备甲醇合成催化剂,该母体浆料与载体浆料al(oh)3混合打浆、抽滤洗涤、干燥、焙烧、成型破碎和活化后得高活性cu/zno/al2o3催化剂。使用该现有技术制备的催化剂具有母体料浆老化时间短、甲醇合成活性高和热稳定性好的特点。上述技术文献中虽合成并解释了共沉淀过程中所产生的物相,但未曾提及有效调节前驱体中主要物相结晶度的方法,且现有的文献仅涉及使用晶种诱导结晶法得到高效催化剂的方法。技术实现要素:本发明的目的是通过控制干燥cu系催化剂前驱体的方式和条件以调控cu系催化剂前驱体晶相结晶度,从而有效调控共沉淀前驱体混合物中不同物相的结晶度,进而增大催化剂的比表面积、活性及稳定性。为了实现上述目的,第一方面,本发明提供一种调控cu系催化剂前驱体晶相结晶度的方法,包括:将经共沉淀法制备得到的cu系催化剂前驱体依次进行洗涤和干燥,通过控制所述干燥的过程来调控所述cu系催化剂前驱体的晶相结晶度至包含5~80重量%的结晶相类水滑石,所述结晶相类水滑石的含量以结晶相类水滑石和非结晶相类水滑石总重量为基准,所述干燥的方式为慢干法或速干法,所述慢干法的步骤包括将洗涤后的cu系催化剂前驱体在40~120℃下干燥10~100h;所述速干法的步骤包括将洗涤后的cu系催化剂前驱体在入口温度为140~200℃下,以10~50ml/min的流量引入至喷雾干燥器中进行干燥。第二方面,本发明提供一种由前述第一方面所述的方法调控得到的cu系催化剂前驱体。第三方面,本发明提供一种制备cu系催化剂的方法,包括:将前述第二方面所述的cu系催化剂前驱体进行焙烧。第四方面,本发明提供一种由前述第三方面所述的方法制备得到的cu系催化剂。采用本发明前述的方法能够有效调控cu系催化剂前驱体的晶相结晶度,从而有效调控共沉淀前驱体混合物中不同物相的结晶度,进而增大催化剂的比表面积、活性及稳定性。本发明提供的前述调控方法操作方便,工艺简单。本发明的其它特征和优点将在随后的具体实施方式部分予以详细说明。附图说明附图是用来提供对本发明的进一步理解,并且构成说明书的一部分,与下面的具体实施方式一起用于解释本发明,但并不构成对本发明的限制。在附图中:图1是实施例1-1、实施例1-2、实施例1-3制备得到的催化剂的xrd图。图2是实施例2-1、实施例2-1制备得到的催化剂的xrd图。具体实施方式以下对本发明的具体实施方式进行详细说明。应当理解的是,此处所描述的具体实施方式仅用于说明和解释本发明,并不用于限制本发明。在本文中所披露的范围的端点和任何值都不限于该精确的范围或值,这些范围或值应当理解为包含接近这些范围或值的值。对于数值范围来说,各个范围的端点值之间、各个范围的端点值和单独的点值之间,以及单独的点值之间可以彼此组合而得到一个或多个新的数值范围,这些数值范围应被视为在本文中具体公开。第一方面,本发明提供一种调控cu系催化剂前驱体晶相结晶度的方法,包括:将经共沉淀法制备得到的cu系催化剂前驱体依次进行洗涤和干燥,通过控制所述干燥的过程来调控所述cu系催化剂前驱体的晶相结晶度至包含5~80重量%的结晶相类水滑石,所述结晶相类水滑石的含量以结晶相类水滑石和非结晶相类水滑石总重量为基准,所述干燥的方式为慢干法或速干法,所述慢干法的步骤包括将洗涤后的cu系催化剂前驱体在40~120℃下干燥10~100h;所述速干法的步骤包括将洗涤后的cu系催化剂前驱体在入口温度为140~200℃下,以10~50ml/min的流量引入至喷雾干燥器中进行干燥。优选情况下,在所述速干法的步骤中,所述干燥的时间为1.0~1.5s。在所述速干法的步骤中,最大空气流量可以为35m3/h。优选情况下,通过控制所述干燥的过程来调控所述cu系催化剂前驱体的晶相结晶度至包含10~70重量%的结晶相类水滑石;更优选地,通过控制所述干燥的过程来调控所述cu系催化剂前驱体的晶相结晶度至包含30~70重量%的结晶相类水滑石。本发明通过控制cu系催化剂制备过程中的干燥工艺能够有效调控cu系催化剂前驱体晶相结晶度,从而有效调控共沉淀前驱体混合物中不同物相的结晶度,进而增大催化剂的比表面积、活性及稳定性。根据一种优选的具体实施方式,在所述慢干法的干燥方式中,所述干燥的步骤包括:先将洗涤后的cu系催化剂前驱体在40~90℃下进行第一干燥;然后将第一干燥后的cu系催化剂前驱体升温至在不超过120℃的温度下进行第二干燥。优选地,所述第一干燥的时间为10~90h,所述第二干燥的时间为2~20h,且所述第一干燥和所述第二干燥的总时间为12~100h。更优选地,所述第一干燥的时间为15~90h,所述第二干燥的时间为2~20h,且所述第一干燥和所述第二干燥的总时间为17~100h。特别优选地,所述第一干燥的时间为20~90h,所述第二干燥的时间为2~20h,且所述第一干燥和所述第二干燥的总时间为22~100h。根据另一种优选的具体实施方式,在所述慢干法的干燥方式中,所述干燥的步骤包括:将洗涤后的cu系催化剂前驱体在100~120℃下干燥10~80h,更优选地,在100~120℃下干燥12~80h,特别优选地,在100~120℃下干燥15~80h。优选地,在所述速干法的干燥方式中,所述cu系催化剂前驱体在进入喷雾干燥器之前的固含量为1~15重量%。优选地,所述洗涤在超声条件下进行。优选地,所述超声的条件包括:频率为20~80khz,时间为2~20min。所述洗涤可以采用常规的布氏漏斗加超声进行。本发明的发明人发现,在调控cu系催化剂前驱体晶相结晶度的过程中,通过控制洗涤所述经共沉淀法制备得到的cu系催化剂前驱体的条件为在超声存在下进行时,也能够影响cu系催化剂前驱体晶相结晶度,从而进一步影响催化剂的活性、稳定性及寿命。特别地,通过控制所述超声的频率为20~80khz,时间为2~20min,配合采用本发明的慢干法或者速干法进行干燥时,获得的cu系催化剂前驱体晶相结晶度最佳,由此进一步获得的催化剂的比表面积更大,催化性能更好,特别适合于制备甲醇合成催化剂。本发明的所述cu系催化剂前驱体可以为制备甲醇的催化剂。优选情况下,所述cu系催化剂前驱体中含有cu、zn、al和任选含有的选自mn、mg和zr中的一种或两种以上的助剂。也就是说,本发明的所述cu系催化剂前驱体中可以含有助剂,也可以不含有助剂。优选地,所述共沉淀法制备cu系催化剂前驱体的步骤包括:将含有cu元素、zn元素、al元素和任选含有的选自mn、mg和zr中的一种或两种以上的助剂元素的溶液a与含有碱金属的碳酸盐或碳酸氢盐的溶液b进行共沉淀。所述溶液a可以为上述含有cu元素、zn元素、al元素的硝酸盐、醋酸盐等形式。优选地,所述共沉淀的条件包括:温度为60~90℃,沉淀终点ph值为7-9。本发明中,为了调控所述cu系催化剂前驱体晶相结晶度,对所述溶液a和溶液b中的物质含量及其浓度并没有特别的限定,本领域技术人员可以根据本领域内制备催化剂时常规使用的物质含量及其浓度进行选择。并且,本领域技术人员也可以根据制备的催化剂中所需要的活性物质的含量以及结合溶液a和溶液b的化学计量关系来确定溶液a和溶液b中的物质含量以及浓度。优选地,所述共沉淀法制备cu系催化剂前驱体的步骤进一步包括:将所述溶液a与所述溶液b共沉淀后所得的混合物进行陈化和过滤。优选地,所述陈化的条件包括:温度为60~90℃,时间为1~24h。第二方面,本发明提供了一种由前述第一方面所述的方法调控得到的cu系催化剂前驱体。第三方面,本发明提供了一种制备cu系催化剂的方法,包括:将前述第二方面所述的cu系催化剂前驱体进行焙烧。优选地,所述焙烧的条件包括:温度为300~600℃,时间为2~6h。第四方面,本发明提供了一种由前述第三方面所述的方法制备得到的cu系催化剂。优选地,该cu系催化剂为催化甲醇合成的催化剂。在含主要成分cu、zn、al以及任选含有的第四组分(mn、mg和zr中的一种或两种以上,0-5重量%,以催化剂的总重量为基准)的催化甲醇合成的催化剂中,经由并流共沉淀法合成后,在x射线粉末衍射中可以观测到cu系催化剂前驱体中含有绿铜锌矿[cu2zn3(co3)2(oh)6]和类水滑石[cuxzn6-xal2(oh)16(co3)4·h2o]两种主要物相。优选地,在催化甲醇合成的催化剂中,以所述cu系催化剂的总重量为基准,所述cu元素的含量为50~70重量%,zn元素的含量为20~40重量%,al元素的含量为5~15重量%,任选含有的助剂元素的总含量为0~5重量%。根据一种优选的具体实施方式,本发明提供一种制备催化甲醇合成的催化剂的方法,包括:(1)将含有cu元素、zn元素、al元素和任选含有的选自mn、mg和zr中的一种或两种以上的助剂元素的溶液a与含有碱金属的碳酸盐或碳酸氢盐的溶液b进行共沉淀,得到混合物;(2)将步骤(1)得到的所述混合物依次进行陈化和过滤,得到cu系催化剂前驱体;(3)将步骤(2)得到的所述cu系催化剂前驱体依次进行洗涤和干燥,所述干燥的方式为慢干法或速干法,所述慢干法的步骤包括将洗涤后的cu系催化剂前驱体在40~120℃下干燥10~100h;所述速干法的步骤包括将洗涤后的cu系催化剂前驱体在入口温度为140~200℃下,以10~50ml/min的流量引入至喷雾干燥器中进行干燥;(4)将经步骤(3)得到的cu系催化剂前驱体进行焙烧和成型。本发明提供的前述工艺制备得到的催化甲醇合成的催化剂比表面积大,活性高且稳定性好。综上,在相同的沉淀条件下,本发明通过控制干燥工艺条件或者洗涤工艺和干燥工艺能够调控共沉淀中所形成的催化剂前驱体的结晶度,进而得到较大的比表面积、高活性及稳定性的催化剂。以下将通过实施例对本发明进行详细描述。以下实施例中,在没有特别说明的情况下,使用的各种原料均来自商购。实施例1将含有2.2kg硝酸铜、1.0kg硝酸锌、0.8kg硝酸铝以及0.07kg硝酸镁的混合物溶于5.5l去离子水中,制成7.5l的水溶液,记作溶液a;将1.6kg碳酸钠溶于6.8l去离子水中,制成7.5l溶液,记作溶液b;将溶液a和溶液b预热至70℃,待用。在搅拌下,将溶液a与溶液b进行并流共沉淀,沉淀过程中控制温度为80℃,沉淀终点的ph值控制在8。将沉淀好的悬浮液在80℃下老化4h,然后通过布氏漏斗进行过滤,得到催化剂前驱体。实施例1-1将实施例1制备得到的催化剂前驱体直接水洗至电导率小于50μs/cm,收集滤饼置于250ml的坩埚内,然后直接转移至烘箱,设定烘箱干燥温度为110℃,在此温度下干燥18h。然后将干燥的催化剂前驱体破碎至2mm左右的颗粒并转移至马弗炉内焙烧3h,焙烧温度为400℃。经成型后备用。其中,图1中示出了通过本实施例的慢干法制备得到的催化剂的xrd图。衍射峰位在11.6-11.9°为类水滑石的主峰,晶面(003),衍射峰位在31.9-32.2°为铜锌孔雀石的主峰,混合物。实施例1-2将实施例1制备得到的催化剂前驱体水洗至电导率小于50μs/cm,并且在水洗打浆过程中加入10min的超声震荡(频率为40khz);收集滤饼置于250ml的坩埚内,然后直接转移至烘箱,设定烘箱干燥温度为110℃,在此温度下干燥18h。然后将干燥的催化剂前驱体破碎至2mm左右的颗粒并转移至马弗炉内焙烧3h,焙烧温度为400℃。经成型后备用。其中,图1中示出了通过本实施例的慢干法制备得到的催化剂的xrd图。实施例1-3将实施例1制备得到的催化剂前驱体直接水洗至电导率小于50μs/cm,收集滤饼置于500ml的烧杯内,加水100ml,形成固含量为10重量%的悬浊液,使用喷雾干燥法进行干燥除水,设定蠕动泵流量为25ml/min、干燥器入口温度为150℃,然后将干燥的催化剂前驱体直接转移至马弗炉内焙烧3h,焙烧温度为400℃。经成型后备用。其中,图1中示出了通过本实施例的速干法制备得到的催化剂的xrd图。实施例2将含有276g硝酸铜、128g硝酸锌、104g硝酸铝以及9g硝酸镁的混合物溶于去离子水中,制成670ml的水溶液,记作溶液a;将204g碳酸钠溶于去离子水中,制成670ml的水溶液,记作溶液b;将溶液a和溶液b预热至60℃,待用。在搅拌下,将溶液a与溶液b进行并流共沉淀,沉淀过程中控制温度为70℃,沉淀终点的ph值控制在7.5。将沉淀好的悬浮液在70℃下老化2h,然后通过布氏漏斗进行过滤,得到催化剂前驱体。实施例2-1将实施例2制备得到的催化剂前驱体直接水洗至电导率小于50μs/cm,收集滤饼置于250ml的坩埚内,然后直接转移至80℃的烘箱干燥12h,然后将烘箱升温到120℃干燥3h。然后将干燥的催化剂前驱体破碎至2mm左右的颗粒并转移至马弗炉内焙烧3h,焙烧温度为400℃。经成型后备用。其中,图2中示出了通过本实施例的慢干法制备得到的催化剂的xrd图。实施例2-2将实施例2制备得到的催化剂前驱体直接水洗至电导率小于50μs/cm,收集滤饼置于250ml的坩埚内,然后直接转移至50℃的烘箱干燥65h,然后将烘箱升温到120℃干燥3h。然后将干燥的催化剂前驱体破碎至2mm左右的颗粒并转移至马弗炉内焙烧3h,焙烧温度为400℃。经成型后备用。其中,图2中示出了通过本实施例的慢干法制备得到的催化剂的xrd图。对比实施例1-1和实施例1-3的xrd图可以看出,本发明的两种不同的干燥方法可以有效的调节类水滑石及铜锌孔雀石的结晶度。并且结合测试例的结果可以看出,对结晶度的调节结果能够反映到相应催化剂比表面积值、孔容的调节,对合成气制甲醇反应的初活性也有很大的影响。对比实施例2-1和实施例2-1的xrd图可以看出,采用相同干燥方法、不同的干燥温度也可以调节催化剂前驱体混合晶相的结晶度。结合测试例的结果可以看出,对结晶度的调节结果能够反映到相应催化剂比表面积值、孔容的调节,对合成气制甲醇反应的初活性也有很大的影响。对比例1将实施例2制备得到的催化剂前驱体直接水洗至电导率小于50μs/cm,收集滤饼置于250ml的坩埚内,然后转移至120℃的烘箱干燥4h。然后将干燥的催化剂前驱体破碎至2mm左右的颗粒并转移至马弗炉内焙烧3h,焙烧温度为400℃。经成型后备用。测试例活性测试:采用固定床连续流动反应器,催化剂装填量1g,粒度范围0.425~0.85mm,使用相同颗粒度范围的石英砂作为稀释剂及恒温区固定填料,催化剂在体积分数为5%的h2/n2的低氢气氛中程序升温还原,后通入合成气(以体积分数计算):co为13%,h2为80%,co2为2%进行甲醇合成反应,操作条件控制为:压力为5mpa,温度为230℃,空速为10000h-1。催化剂的初活性以co转化率达到稳定状态开始计算,约在开始进行反应后的20-24h。催化剂样品的比表面积、孔容及活性测试结果列于表1。表1催化剂样品来源比表面积(m2/g)孔容(cm3/g)co平衡转化率%实施例1-196.70.3652实施例1-295.20.3654实施例1-385.50.3945实施例2-189.00.3960实施例2-298.40.4667对比例136.20.2036从表1的结果可以看出,本发明通过控制干燥工艺或干燥工艺和洗涤工艺能够调控cu系催化剂前驱体晶相结晶度,从而有效调控共沉淀前驱体混合物中不同物相的结晶度,进而增大催化剂的比表面积、活性及稳定性。以上详细描述了本发明的优选实施方式,但是,本发明并不限于上述实施方式中的具体细节,在本发明的技术构思范围内,可以对本发明的技术方案进行多种简单变型,这些简单变型均属于本发明的保护范围。另外需要说明的是,在上述具体实施方式中所描述的各个具体技术特征,在不矛盾的情况下,可以通过任何合适的方式进行组合,为了避免不必要的重复,本发明对各种可能的组合方式不再另行说明。此外,本发明的各种不同的实施方式之间也可以进行任意组合,只要其不违背本发明的思想,其同样应当视为本发明所公开的内容。当前第1页12