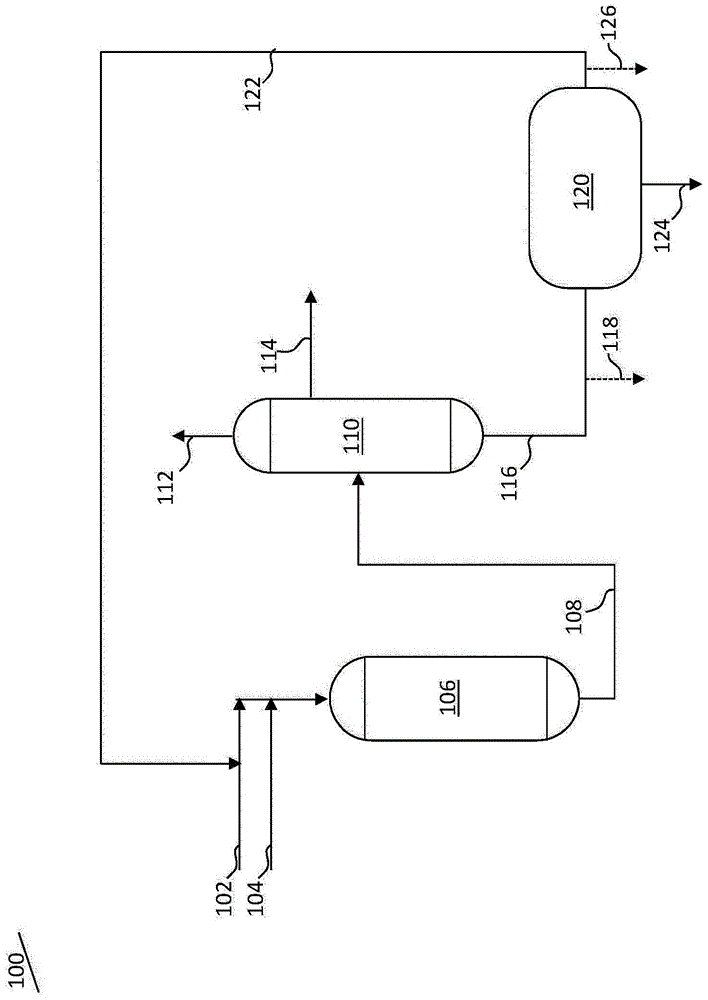
本申请要求2017年1月4日提交的美国临时专利申请号62/442228的优先权,其内容以其全部通过引用结合至本文。发明背景发明领域本发明涉及一种加氢裂化方法,并且特别是这样的加氢裂化方法,其包括使用离子液体和固体吸附剂从再循环流中分离重质多核芳烃。相关技术的描述加氢裂化工艺在商业上用于许多炼油厂。它们用于处理在传统加氢裂化单元中约370-520℃的范围内沸腾以及在渣油加氢裂化单元中在520℃及以上沸腾的各种进料。通常,加氢裂化工艺将进料分子裂解成具有更高平均挥发性和经济价值的较小(即,较轻的)分子。此外,加氢裂化工艺典型地通过增加氢碳比以及通过除去有机硫和有机氮化合物而改进烃原料的质量。源于加氢裂化工艺的显著的经济效益已经导致工艺改进和更活性的催化剂的实质性发展。除了含硫和含氮化合物之外,典型的加氢裂化原料流(例如真空瓦斯油(vgo))含有少量的多核芳族(pna)化合物,即含有少于7个稠合苯环的那些。在原料流在高温和高压下经受加氢处理时,重质多核芳族(hpna)化合物(即含有7个或更多个稠合苯环的那些)倾向于形成并以高浓度存在于未经转化的加氢裂化器塔底物中。出于这个原因,pna化合物被定义为是hpna的前体,并且所述前体的量和类型通常与原料的类型及其沸程有关。hpna使工艺装置结垢并且缩短了催化剂寿命。重质原料流如脱金属油(dmo)或脱沥青油(dao)具有比vgo原料流高得多的氮、硫和pna化合物的浓度。这些杂质可通过要求更高的操作温度、更高的氢分压或另外的反应器/催化剂体积来降低加氢裂化单元的整体效率。另外,高浓度的杂质可加速催化剂失活。三种主要的加氢裂化工艺方案包括单级一次通过加氢裂化、具有或不具有再循环的串流加氢裂化和两级再循环加氢裂化。单级一次通过加氢裂化是最简单的加氢裂化器配置,并且典型地在比加氢处理工艺更苛刻且不如传统全压加氢裂化工艺苛刻的操作条件下发生。其使用一个或多个用于处理步骤和裂化反应二者的反应器,因此催化剂必须能够进行加氢处理和加氢裂化二者。这种配置是有成本效益的,但是典型地导致相对低的产品收率(例如最大转化率约60%)。单级加氢裂化经常设计成使在单或双催化剂体系上的中间馏分油收率最大化。双催化剂体系可以用于叠置床层配置或两种不同的反应器。将流出物送到分馏塔以分离h2s、nh3、轻质气体(c1-c4)、在36-370℃的温度范围内沸腾的石脑油和柴油产品。沸点高于370℃的烃典型地是未经转化的塔底物,其在单级系统中被送到其他炼油厂操作如流化催化裂化单元。具有或不具有再循环的串流加氢裂化是最常用的配置之一。其使用一个反应器(含有处理催化剂和裂化催化剂二者)或两个或更多个反应器以用于处理反应步骤和裂化反应步骤二者。在串流配置中,将来自第一反应区的全部加氢裂化的产品流(其包括轻质气体(典型地为c1-c4、h2s、nh3)和所有剩余的烃)送到第二反应区。将来自分馏塔的未经转化的塔底物再循环回第一反应器中以用于进一步裂化。这种配置将重质原油馏分(即真空瓦斯油)转化成轻质产品,并且潜在地最大化了石脑油、喷气燃料或柴油的收率,这取决于蒸馏段中所用的再循环切割点。两级再循环加氢裂化使用两个反应器,并且将来自分馏塔的未经转化的塔底物送到第二反应器以用于进一步裂化。由于第一反应器完成了加氢处理和加氢裂化二者,因此到第二反应器的进料几乎没有氨和硫化氢。这允许使用容易被硫或氮化合物中毒的高性能沸石催化剂。一种典型的加氢裂化原料是名义沸腾范围为370-565℃的真空瓦斯油流。dmo或dao单独或与真空瓦斯油的共混物在加氢裂化单元中处理。例如一种典型的加氢裂化单元处理含有用于优化操作的10v%-25v%的dmo或dao的真空瓦斯油。也可以处理未经稀释的100%dmo或dao,但是典型地在更苛刻的条件下进行,因为dmo或dao流含有比vgo流更大百分比的氮化合物如2000ppmwvs.1000ppmw,和更高的微碳残留物(mcr)含量(10w%vs.<1w%)。到加氢裂化单元的共混原料中的dmo或dao含量可通过增加现有单元的操作温度或反应器/催化剂体积,或通过增加新建单元的氢分压要求或反应器/催化剂体积来降低所述单元的整体效率。这些杂质还可降低加氢裂化流出物中期望的中间烃产品的质量。当dmo或dao在加氢裂化器中处理时,可以需要进一步处理加氢裂化反应器流出物以满足炼油厂燃料规格,这取决于炼油厂配置。当加氢裂化单元以其期望的模式操作时,也就是说,排出高质量流出物产品流时,其流出物可以用于共混并产生汽油、煤油和柴油燃料以满足已经确立的燃料规格。形成hpna化合物是一种不期望的在再循环加氢裂化器中发生的副反应。hpna分子通过如下方式形成:较大的氢化芳族分子的脱氢或现有hpna分子上的侧链环化随后脱氢,随反应温度增加有利于脱氢。hpna形成取决于许多已知的因素,包括原料类型、催化剂选择、处理配置和操作条件。由于hpna分子在再循环系统中聚集并且然后引起装置结垢,因此在加氢裂化工艺中必须控制hpna形成。各种hpna化合物的形成速率随着更高的转化和更重质的原料而增加。装置的结垢可以并不明显,直到大量的hpna在再循环液体回路中聚集。hpna形成的问题是炼油厂从业者普遍关注的问题,并且炼油厂操作者已经开发了各种除去方法以减少其影响。分离或处理加氢裂化工艺中所形成的重质多核芳烃的现有技术的方法包括吸附、氢化、萃取、溶剂脱沥青和净化(purging),或将再循环流的一部分从系统中“抽出(bleeding)”以减少hpna化合物的积聚并且在炼油厂的其他地方裂化或利用所抽出的流。在分开的单元中处理加氢裂化器塔底物以消除hpna并且将无hpna的塔底物再循环回加氢裂化反应器中。如上所述,当以再循环模式操作加氢裂化单元时一种可替代的方案是净化一定量的再循环液体以降低随新鲜进料而引入的hpna化合物的浓度,尽管净化将转化率降低至低于100%。积聚问题的另一解决方案是通过将hpna送到专用真空塔来消除hpna,所述专用真空塔有效地分馏了98–99%的再循环流,将大部分的hpna留在塔底部以用于作为分馏塔塔底物从系统排出。这种可替代方案带来了另外的资金成本和专用分馏塔的操作花费。如本文中所用,术语加氢裂化单元再循环流与术语加氢裂化器再循环流、加氢裂化器塔底物、加氢裂化器未经转化的材料以及分馏塔塔底物同义。如本文中所用,缩写表达“hpna”表示“重质多核芳烃”,并且“hpna/hpna前体”和“hpna和hpna前体”表示“hpna化合物和hpna前体”。“hpna”和“hpna化合物”可互换使用。为了以后描述中方便,将理解,提及hpna化合物时还包括hpna前体。因此存在的问题是提供一种从加氢裂化单元的塔底物再循环流中除去hpna化合物的方法,所述方法与现有技术的工艺相比更有效且更有成本效益。发明的概述根据本发明的方法,处理加氢处理的塔底物馏分以转化并分离hpna化合物,并且产生hpna减少的加氢处理的塔底物流以有效用于再循环,例如在单一加氢裂化反应器(串流一次通过加氢裂化单元操作)或两级加氢裂化单元操作的配置中再循环。加氢裂化单元塔底物再循环流以及优选的新鲜的加氢裂化单元进料是在两种可替代的方法之一中处理,所述方法采用吸附和萃取二者以在两个分立的步骤中除去hpna化合物。在所述方法的一种实施方案中,第一吸附步骤从加氢裂化器塔底物再循环流中除去大部分的hpna化合物并且第二离子液体萃取步骤除去剩余的hpna化合物。在所述方法的第二实施方案中,第一离子液体萃取步骤从塔底物再循环流中除去大部分的hpna化合物并且第二吸附步骤除去剩余的hpna化合物。实施方案1:吸附、随后离子液体萃取。在所述实施方案中,再循环流优选地与新鲜的进料合并,并且将合并的原料流送到吸附塔以除去hpna化合物和hpna前体。然后将来自吸附塔的流出物送到萃取器以用一种或多种离子液体萃取剩余的hpna化合物和hpna前体。将经萃取的hpna和hpna前体与离子液体一起送到分离器以使用有机极性溶剂分离hpna和前体,并且回收所述离子液体。然后将溶剂在溶剂回收单元中回收并且再循环到萃取器。然后将基本上没有游离hpna化合物的经处理的流送到液-液分离器以分离任何剩余的离子液体和hpna化合物并且回收无hpna的流。实施方案2:离子液体萃取、随后吸附。在所述实施方案中,再循环流优选地与原料流合并,并且被送到萃取器并与一种或多种离子液体混合。将经萃取的hpna和hpna前体与离子液体一起送到分离器以使用有机极性溶剂分离hpna和前体,并且回收所述离子液体。溶剂然后在溶剂回收单元中回收并且再循环到萃取器。然后将hpna含量降低的经处理的流送到液-液分离器以分离任何剩余的离子液体和hpna化合物并且回收hpna含量降低的流。在离子液体和溶剂分离后,将经处理的烃流送到吸附塔以除去剩余的hpna化合物和hpna前体。以上从塔底物馏分中分离hpna化合物的方法可以使用单一反应器或多个反应器以“一次通过”配置整合到加氢处理操作中。另外,以上从塔底物馏分中分离hpna化合物的方法可以被整合到两级加氢处理配置中。尽管已经结合加氢裂化单元的再循环流的处理描述了所述方法,但是不含或含有低浓度的hpna化合物和/或hpna前体的经处理的流可以可替代地被送到fcc单元。hpna处置通过上述萃取/吸附步骤的任一组合回收的hpna化合物可以在延迟焦化器中被进一步处理以产生高质量焦炭,和/或可以被气化以产生氢、蒸汽和电,和/或可以被送到燃料油池作为共混组分,和/或可以被送到流化催化裂化(fcc)单元以形成fcc原料流的一小部分并且最终作为焦炭沉积在催化剂上,所述焦炭将在催化剂再生步骤中燃烧以产生热,和/或可以被送到沥青池。在上述可替代的吸附/萃取方法的实践中,优选的是原料中的金属通过在含有hdm催化剂(其具有大孔体积和尺寸)的加氢脱金属(hdm)床中预处理来除去。将理解,进料中的硫和氮化合物在加氢裂化单元的第一级中除去。离子液体可以是通式q+a-的非水离子液体。所述a-离子选自卤素阴离子、硝酸根、硫酸根、磷酸根、乙酸根、卤代乙酸根、四氟硼酸根、四氯硼酸根、六氟磷酸根、六氟锑酸根、氟磺酸根、烷基磺酸根、全氟烷基磺酸根、双(全氟烷基磺酰基)酰胺、式c(cf3so2)3-的三-三氟甲磺酰基甲基化物、未取代的芳烃磺酸根、卤素或卤代烷基取代的芳烃磺酸根、四苯基硼酸根阴离子和具有取代的芳核的四苯基硼酸根阴离子。所述q+离子可以是任何合适的铵阳离子、阳离子或锍阳离子。季铵和/或q+离子可以具有通式nr1r2r3r4+,其中r1、r2、r3和r4相同或不同并且选自氢和具有1-30个碳原子的烃基,除了nh4+阳离子之外;和pr1r2r3r4+,其中r1、r2、r3和r4相同或不同并且选自氢和具有1-30个碳原子的烃基。所述q+离子可以具有通式r1r2n=cr3r4+,其中r1、r2、r3和r4相同或不同并且选自氢和具有1-30个碳原子的烃基。所述q+离子可以具有通式r1r2p=cr3r4+,其中r1、r2、r3和r4相同或不同并且选自氢和具有1-30个碳原子的烃基。所述q+离子可以是含氮的杂环化合物,其包括1个、2个或3个氮原子并且具有含4-10个原子的环状化合物。所述q+离子可以具有选自以下结构的通式结构,其中r1、r2、r3,r4和r5相同或不同并且表示氢或具有1-30个碳原子的烃基。所述q+离子可以是含磷化合物。所述q+离子可以具有从以下结构的组中选择的通用结构式。所述q+季铵或阳离子还可以对应于以下通用结构式之一:r1r2+n=cr3--r5--r3c=n+r1r2,和r1r2+p=cr3--r5--r3c=p+r1r2其中r1、r2和r3相同或不同,并且表示氢或具有1-30个碳原子的烃基,并且r5表示亚烷基或亚苯基。锍阳离子可以具有通式:sr1r2r3+其中r1、r2和r3是相同或不同的具有1-12个碳原子的烃基。特别适合用于本发明方法的离子液体包括六氟磷酸n-丁基-吡啶四氟硼酸n-乙基-吡啶氟磺酸吡啶四氟硼酸丁基-3-甲基-1-咪唑丁基-3-甲基-1-咪唑双-三氟甲烷-磺酰基酰胺、三乙基锍双-三氟甲烷-磺酰基酰胺、六氟锑酸丁基-3-甲基-1-咪唑六氟磷酸丁基-3-甲基-1-咪唑三氟乙酸丁基-3-甲基-1-咪唑三氟甲基磺酸丁基-3-甲基-1-咪唑丁基-3-甲基-1-咪唑双(三氟甲基磺酰基)-酰胺、六氟磷酸三甲基-苯基铵、四氟硼酸四丁基及其组合。离子液体萃取方法可以在20-200℃的温度和1-30bar的压力下进行,其中离子液体与hpna的摩尔比是1:1-10:1。lhsv范围可以是0.5-10h-1。使用离子液体处理加氢裂化单元的烃流出物以基于其6元环结构萃取各种有机硫和有机氮苯并噻吩化合物的类似方法是已知的。这样的方法公开在标题为“ionicliquiddesulfurizationprocessincorporatedinalowpressureseparator”的美国专利8758600和标题为“ionicliquiddesulfurizationprocessincorporatedinacontactvessel”的美国专利8992767中,其公开内容以其全部通过引用结合至本文。合适的萃取器包括离心接触器和接触塔如板式塔、喷洒塔、填料塔、转盘塔和脉冲塔。适合用于所述方法的吸附塔可以是填料床塔或淤浆床塔。吸附床可以在20-200℃的温度和1-30bar的压力下操作。合适的吸附剂包括天然粘土并且优选凹凸棒石粘土、氧化铝、二氧化硅、活性炭、天然和合成沸石、用过的催化剂、二氧化硅-二氧化钛和二氧化钛。用于所述方法的合适的有机极性溶剂可以基于其hildebrand溶解度因子或基于其二维溶解度因子来选择。整体hildebrand溶解度参数是一种公知的极性的量度,并且已经对许多化合物进行了计算。参见journalofpainttechnology,第39卷,第505期(1967年2月)。溶剂还可以基于其二维溶解度(包含络合溶解度参数和场力溶解度参数)参数来选择。参见例如i.a.wiehe,ind.&eng.res.,34(1995),661。描述氢键键合和电子给体-受体相互作用的络合溶解度参数分量度量了一个分子的原子和不同分子的第二原子之间特定取向所需的相互作用能量。描述范德华力和偶极相互作用的场力溶解度参数度量了不被分子的取向变化所破坏的液体的相互作用能量。极性溶剂进一步定义为具有大于约8.5的整体溶解度参数或大于1的络合溶解度参数以及大于8的场力参数。满足所期望的最小溶解度参数的极性溶剂的实例是甲苯(8.91)、苯(9.15)、二甲苯(8.85)和四氢呋喃(9.52)。以下实施例中所用的优选的极性溶剂是甲苯和四氢呋喃。附图说明以下将参考附图进一步详细描述本发明,附图中相同或类似的元件由相同的编号来引用,并且其中:图1是一种整合的加氢裂化单元操作的实施方案的工艺流程图;图2是一种整合的串流加氢处理系统的工艺流程图;图3是一种具有再循环的整合的两级加氢加氢处理系统的工艺流程图;图4是确认并示出各种重质多核芳族化合物的结构的表,所述重质多核芳族化合物典型的是在加氢裂化方法期间所产生的那些;图5是一种用于实践本发明的系统和方法的实施方案的工艺流程图,其中吸附之后是离子液体萃取;和图6是另一种用于实践本发明的系统和方法的实施方案的工艺流程图,其中离子萃取先于吸附步骤。发明的详细描述提供整合的方法和系统以改进加氢裂化操作的效率。下述方法和系统有效处理获自各种源的宽范围的初始原料,例如一种或多种的直馏真空瓦斯油、处理的真空瓦斯油、来自溶剂脱金属操作的脱金属油、来自溶剂脱沥青操作的脱沥青油、来自焦化器操作的焦化器瓦斯油、来自流化催化裂化操作的环状油(包括重质环状油)、和来自减粘裂化操作的减粘裂化油。所述原料流通常具有约350-800℃、350-700℃、350-600℃或350-565℃的沸点。如本文中所用,“hpna化合物”是指具有7个或更多个环的稠合的多环芳族化合物,例如包括但不限于晕苯(c24h12)、苯并晕苯(c28h14)、二苯并晕苯(c32h16)和卵苯(c32h14)。以下示出了7环芳族分子晕苯。所述芳族结构可以具有连接到其上的烷基或环烷环。晕苯具有24个碳原子和12个氢原子。它的双键当量(dbe)是19。dbe基于双键数目和环数目之和来计算。例如晕苯的dbe值是19(例如7个环+12个双键)。hpna化合物通常具有17和更高的dbe值。具有再循环的单反应器图1是一种整合的加氢处理系统100的实施方案的工艺流程图,所述加氢处理系统100包括反应区106、分馏区110和hpna分离区120。反应区106通常包括一个或多个入口,其与初始原料源102、氢气源104和hpna分离区120流体连通,以接收包含塔底物流116的全部或一部分的再循环流。反应区106的一个或多个出口(其排出流出物流108)与分馏区110的一个或多个入口流体连通,任选地具有一个或多个高压和低压分离级以用于回收再循环氢(未示出)。分馏区110包括一个或多个出口以用于排出气体112,典型地为h2、h2s、nh3和轻质烃(c1-c4);一个或多个出口以用于回收产品114如在36-370℃的温度范围内沸腾的石脑油和柴油产品;和一个或多个出口以用于排出包括在约370℃之上沸腾的烃塔底物116。在某些实施方案中,塔底物116的温度切割点以及相应产品114的终馏点是这样的范围,其对应于下游操作所期望的汽油、煤油和/或柴油产品沸点范围的上限温度范围。分馏塔塔底物出口116与本文中所述的hpna分离区120流体连通,其通常包括用于排出hpna减少的分馏塔塔底物122的出口和用于排出含有hpna化合物的hpna/hpna前体流124的出口。排出hpna减少的分馏塔塔底物122的出口与一个或多个反应区106的入口流体连通以用于再循环所述流的全部或一部分。在某些实施方案中,抽出流118从hpna分离区120上游的塔底物116中抽出。在另外的实施方案中,除了或代替抽出流118,抽出流126从hpna分离区120下游的hpna减少的分馏塔塔底物122中抽出。这些抽出流的任一或二者是富氢的,并且因而可以与某些燃料油池有效地整合,或用作流化催化裂化或蒸汽裂化工艺的进料(未示出)。在系统100的操作中,将原料流102和氢流104加入到反应区106。氢流104提供了一定量的氢以有效支持所必需的加氢裂化程度、进料类型和其他因素,并且可以是包括以下的任何组合:补充的氢、来自反应区106和分馏区110之间的任选的气体分离子系统(未示出)的再循环氢、和/或来源于分馏塔气体流112。在用于回收再循环氢的一个或多个任选的高压和低压分离级之后,反应流出物流108含有转化的、部分转化的和未经转化的烃,其包括在反应区106中形成的hpna化合物。将反应流出物流108送到分馏区110,以回收气体和液体产品和副产品112、114,并且分离含有hpna化合物的塔底物馏分116。将典型地含有h2、h2s、nh3和轻质烃(c1-c4)的气体流112排出并回收,并且可以进一步如本领域已知的那样进行处理,包括回收再循环氢。一种或多种裂化产品流114从分馏塔合适的出口排出,并且可以在下游炼油厂操作中进一步处理和/或共混以产生汽油、煤油和/或柴油燃料或其他石化产品。在某些实施方案(未示出)中,分馏区110可以作为闪蒸容器操作以在合适的切割点(例如对应于下游操作所期望的汽油、煤油和/或柴油产品的上限温度范围的范围)分离重质组分。在某些实施方案中,合适的切割点是350-450℃、360-450℃、370-450℃、350-400℃、360-400℃、370-400℃、350-380℃、或360-380℃。将来源于反应流出物的分馏塔塔底物流116的全部或一部分(其包括在反应区106中形成的hpna化合物)送到hpna分离区120以用于进行处理。在某些实施方案中,将来自反应流出物的分馏塔塔底物的一部分作为抽出流118除去。抽出流118可以是分馏塔塔底物116的约0-10v%、1-10v%、1-5v%或1-3v%。加氢处理的流出物分馏塔塔底物中的hpna化合物的浓度在hpna分离区120中降低以产生hpna减少的分馏塔塔底物流122,其再循环到反应区106。在某些实施方案中,代替或与抽出流118一起,hpna减少的分馏塔塔底物流122的一部分作为抽出流126从再循环回路除去。抽出流126可以是hpna减少的分馏塔塔底物流122的约0-10v%、1-10v%、1-5v%或1-3v%。含有hpna化合物的排出流124从hpna分离区120中除去。反应区106可以含有串联和/或并联排列的一种或多种固定床、沸腾床、淤浆床、移动床、连续搅拌槽(cstr)或管式反应器。一种或多种反应器通常在对于期望的转化率、特定反应器类型、进料特性和期望的产品分布来说有效的条件下操作。例如这些条件可以包括约300-500℃、330-500℃、300-475℃、330-475℃、300-475℃或330-450℃的反应温度;约60-300bar、60-200bar、60-180bar、100-300bar、100-200bar、100-180bar、130-300bar、130-200bar、或130-180bar的反应压力;最高约2500标准升/升烃进料(slt/lt),在某些实施方案中是约800-2000slt/lt、800-1500slt/lt、1000-2000slt/lt、或1000-1500slt/lt的氢进料速率;以及约0.1-10h-1、0.1-5h-1、0.1-2h-1、0.25-10h-1、0.25-5h-1、0.25-2h-1、0.5-10h-1、0.5-5h-1、或0.5-2h-1的进料速率。在使用相对较低的氢分压值的系统中,hpna化合物具有相对更大的聚集倾向,这归因于对于裂化反应而言氢的不可利用性。操作者典型地必须平衡hpna化合物的聚集与增加的氢消耗的更高成本。然而,当再循环中的hpna化合物如在本发明方法中那样被除去时,可以增加催化剂的寿命周期。用于反应区106的催化剂含有选自iupac元素周期表第6-10族的一种或多种活性金属组分。在某些实施方案中,活性金属组分是钴、镍、钨和钼中的一种或多种。一种或多种活性金属组分典型地沉积或引入到载体上,所述载体可以是无定形和/或结构化的如氧化铝、二氧化硅-氧化铝、二氧化硅、二氧化钛、二氧化钛-二氧化硅、二氧化钛-硅酸盐或沸石。在使用沸石基催化剂的实施方案中,hpna化合物具有相对更高的在再循环流中聚集的倾向,这归因于这些较大的分子不能扩散到催化剂的孔结构中,特别是在反应器中相对较低的氢分压水平下。然而,根据本文中的方法,通过从再循环流中除去hpna化合物,增加了这样的沸石催化剂的寿命周期。具有再循环的串流图2是另一种整合的加氢裂化单元操作系统200的实施方案的工艺流程图,作为串流加氢裂化系统操作的系统200具有到第一反应区、第二反应区或第一和第二反应区二者的再循环。通常,系统200包括第一反应区228、第二反应区232、分馏区210和hpna分离区220。第一反应区228通常包括一个或多个与初始原料源202、氢气源204和任选的hpna分离区220流体连通的入口,以接收包含hpna减少的反应区塔底物流222的全部或一部分的再循环流。第一反应区228的一个或多个出口(其排出流出物流230)与第二反应区232的一个或多个入口流体连通。在某些实施方案中,将流出物230送到第二反应区232,而不分离任何多余的氢和轻质气体。在任选的实施方案中,在第一和第二反应区228、232之间提供一个或多个高压和低压分离级以用于回收再循环氢(未示出)。第二反应区232通常包括一个或多个与第一反应区228的一个或多个出口、任选的另外的氢气源205和任选的hpna分离区220流体连通的入口,以接收包含hpna减少的反应区塔底物流222的全部或一部分的再循环流。第二反应区232的一个或多个出口(其排出流出物流234)与分馏区210的一个或多个入口流体连通(任选地在第二反应区232和分馏区210之间具有一个或多个高压和低压分离级以用于回收再循环氢,未示出)。分馏区210包括一个或多个用于排出气体212(典型地是h2s、nh3和轻质烃(c1-c4))的出口;一个或多个用于回收产品214(如在36-370℃的温度范围内沸腾的石脑油和柴油产品)的出口;和一个或多个用于排出塔底物216(其包括沸点高于约370℃的烃)的出口。在某些实施方案中,塔底物216的温度切割点(和相应的产品214的终馏点)是350-400℃或360-400℃。分馏区210塔底物出口与本文中所述的hpna分离区220流体连通,所述hpna分离区220通常包括用于排放hpna减少的分馏塔塔底物222的出口和用于排放含有hpna化合物的流224的出口。排放hpna减少的分馏塔塔底物222的出口与反应区228和/或232的一个或多个入口流体连通,以用于再循环所述流的全部或一部分。在某些实施方案中,抽出流218是从hpna分离区220上游的塔底物216中抽出的。在另外的实施方案中,除了或代替抽出流218,抽出流226是从hpna分离区220下游的hpna减少的分馏塔塔底物222中抽出的。这些抽出流的任一或二者是富氢的,并且因此可以与某些燃料油池有效地整合,或用作流化催化裂化或蒸汽裂化工艺的进料(未示出)。在系统200的操作中,将原料流202和氢流204加入到反应区228。氢流204包括有效量的氢以支持所必需的加氢裂化程度、进料类型和其他因素,并且可以是包括以下的任何组合:补充的氢、来自反应区228和232之间的任选的气体分离子系统(未示出)的再循环氢、来自反应区232和分馏塔210之间的任选的气体分离子系统(未示出)的再循环氢,和/或来源于分馏塔气体流212。第一反应区228在用于生产反应流出物流230的有效条件下操作,(任选地在用于回收再循环氢的一个或多个高压或低压分离级之后)将所述反应流出物流230任选地与另外的氢流205一起送到第二反应区232。第二反应区232在用于生产反应流出物流234的有效条件下操作,所述反应流出物流234含有转化的、部分转化的和未经转化的烃。反应流出物流进一步包括在反应区228和/或232中形成的hpna化合物。将反应流出物流234送到分馏区210,通常以回收气体和液体产品和副产品,并且分离含有hpna化合物的塔底物馏分。典型地含有h2、h2s、nh3和轻质烃(c1-c4)的气体流212被排出和回收,并且可以进一步如本领域中已知的那样进行处理,包括回收再循环氢。一种或多种裂化产品流214从分馏塔适当的出口排出,并且可以在下游炼油厂操作中进一步处理和/或共混以产生汽油、煤油和/或柴油燃料或其他石化产品。在某些实施方案(未示出)中,分馏区210可以作为闪蒸容器操作以在合适的切割点(例如对应于下游操作所期望的汽油、煤油和/或柴油产品的上限温度范围的范围)分离重质组分。在某些实施方案中,合适的切割点是350-450℃、360-450℃、370-450℃、350-400℃、360-400℃、370-400℃、350-380℃、或360-380℃。将来自反应流出物的分馏塔塔底物流216的全部或一部分(其包括在反应区228和/或232中形成的hpna化合物)送到hpna分离区220以用于进行处理。在某些实施方案中,将来自反应流出物的分馏塔塔底物的一部分作为抽出流218除去。抽出流218可以是分馏塔塔底物216的约0-10v%、1-10v%、1-5v%或1-3v%。分馏塔塔底物中的hpna化合物的浓度在hpna分离区220中降低以产生hpna减少的分馏塔塔底物流222。含有hpna化合物的排出流224从hpna分离区220中除去。在某些实施方案中,代替或与抽出流218一起,hpna减少的分馏塔塔底物流222的一部分作为抽出流226从再循环回路中除去。抽出流226可以是hpna减少的分馏塔塔底物流222的约0-10v%、1-10v%、1-5v%或1-3v%。因此,将hpna减少的分馏塔塔底物流222的全部或一部分再循环到第二反应区232作为流222a,再循环到第一反应区228作为流222b,或再循环到第一和第二反应区228和232二者。例如流222b包含0-100v%、在某些实施方案中为0-约80v%且在进一步的实施方案中为0-约50v%的再循环到区228的流222,并且流222a包含0-100v%、在某些实施方案中为0-约80v%且在进一步的实施方案中为0-约50v%的再循环到区232的流222。第一反应区228可以含有串联和/或并联排列的一种或多种固定床、沸腾床、淤浆床、移动床、连续搅拌槽(cstr)或管式反应器。一种或多种反应器通常在对于第一反应区228中期望的转化率、特定反应器类型、进料特性和所期望的产品分布来说有效的条件下操作。例如这些条件可以包括约300-500℃、330-500℃、300-475℃、330-475℃、300-475℃或330-450℃的反应温度;约60-300bar、60-200bar、60-180bar、100-300bar、100-200bar、100-180bar、130-300bar、130-200bar、或130-180bar的反应压力;最高约2500slt/lt、在某些实施方案中是约800-2000slt/lt、800-1500slt/lt、1000-2000slt/lt、或1000-1500slt/lt的氢进料速率;和约0.1-10h-1、0.1-5h-1、0.1-2h-1、0.25-10h-1、0.25-5h-1、0.25-2h-1、0.5-10h-1、0.5-5h-1、或0.5-2h-1的进料速率。用于第一反应区228的催化剂含有选自iupac元素周期表第6-10族的一种或多种活性金属组分。在某些实施方案中,活性金属组分是钴、镍、钨和钼中的一种或多种。一种或多种活性金属组分典型地沉积或引入到载体上,所述载体可以是无定形和/或结构化的如氧化铝、二氧化硅-氧化铝、二氧化硅、二氧化钛、二氧化钛-二氧化硅、二氧化钛-硅酸盐或沸石。在使用沸石基催化剂的实施方案中,hpna化合物具有相对更高的在再循环流中聚集的倾向,这归因于这些较大分子不能扩散到催化剂的孔结构中,特别是在反应器中相对较低的氢分压水平下。然而,根据本文的方法,通过从实施方案(其中将hpna减少的塔底物再循环到第一反应区228)的再循环流中除去hpna化合物,增加了这样的沸石催化剂的寿命周期。第二反应区232可以含有串联和/或并联排列的一种或多种固定床、沸腾床、淤浆床、移动床、连续搅拌槽(cstr)或管式反应器。一种或多种反应器通常在对于特定的反应器类型、进料特性和期望的产品分布来说有效的条件下操作。例如这些条件可以包括约300-500℃、330-500℃、300-475℃、330-475℃、300-475℃或330-450℃的反应温度;约60-300bar、60-200bar、60-180bar、100-300bar、100-200bar、100-180bar、130-300bar、130-200bar、或130-180bar的反应压力;最高约2500slt/lt、在某些实施方案中是约800-2000slt/lt、800-1500slt/lt、1000-2000slt/lt、或1000-1500slt/lt的氢进料速率;和约0.1-10h-1、0.1-5h-1、0.1-2h-1、0.25-10h-1、0.25-5h-1、0.25-2h-1、0.5-10h-1、0.5-5h-1、或0.5-2h-1的进料速率。第二反应区232中所用的催化剂含有选自iupac元素周期表第6-10族的一种或多种活性金属组分。在某些实施方案中,活性金属组分是钴、镍、钨和钼中的一种或多种。在其中第一反应区减少了污染物如硫和氮以便硫化氢和氨在第二反应区中最小化的实施方案中,作为加氢催化剂有效的活性金属组分可以包括一种或多种单独的或与其他活性金属组合的贵金属如铂或钯。一种或多种活性金属组分典型地沉积或引入到载体上,所述载体可以是无定形和/或结构化的如氧化铝、二氧化硅-氧化铝、二氧化硅、二氧化钛、二氧化钛-二氧化硅、二氧化钛-硅酸盐或沸石。在使用沸石基催化剂的实施方案中,hpna化合物具有相对更高的在再循环流中聚集的倾向,这归因于这些较大的分子不能扩散到催化剂的孔结构中,特别是在反应器中相对较低的氢分压水平下。然而,根据本文的方法,通过从实施方案(其中将hpna减少的塔底物再循环到第二反应区232)的再循环流中除去hpna化合物,增加了这样的沸石催化剂的寿命周期。具有再循环的两级图3是另一种整合的加氢裂化单元操作系统300的实施方案的工艺流程图,系统300作为具有再循环的两级加氢裂化系统操作。通常,系统300包括第一反应区336、第二反应区340、分馏区310和hpna分离区320。第一反应区336通常包括一个或多个入口,其与初始原料源302和氢气源304流体连通。第一反应区336的一个或多个出口(其排出流出物流338)与分馏区310的一个或多个入口流体连通(任选地在第一反应区336和分馏区310之间具有一个或多个高压或低压分离级以用于回收再循环氢,未示出)。分馏区310包括一个或多个用于排放气体312(典型的是h2s、nh3和轻质烃(c1-c4))的出口;一个或多个用于回收产品314(如在36-370℃的温度范围内沸腾的石脑油和柴油产品)的出口;和一个或多个用于排放塔底物316(其包括沸点高于约370℃的烃)的出口。在某些实施方案中,塔底物316的切割点(和相应的产品314的终馏点)是这样的范围,其对应于下游操作所期望的汽油、煤油和/或柴油产品沸点范围的上限温度范围。分馏区310塔底物出口与本文中所述的hpna分离区320流体连通,hpna分离区320通常包括用于排放hpna减少的分馏塔塔底物322的出口和用于排放含有hpna化合物的流324的出口。排放hpna减少的分馏塔塔底物322的出口与第二反应区340的一个或多个入口流体连通,以用于再循环流322的全部或一部分的322a的再循环。在某些任选的实施方案中(如图3中的虚线所示),一部分的322b与第一反应区336的一个或多个入口流体连通。在某些实施方案中,抽出流318是从hpna分离区320上游的塔底物316中抽出的。在另外的实施方案中,除了或代替抽出流318,抽出流326是从hpna分离区320下游的hpna减少的分馏塔塔底物322中抽出的。这些抽出流的任一或二者是富氢的,并且因而可以与某些燃料油池有效地整合,或用作流化催化裂化或蒸汽裂化工艺的进料(未示出)。第二反应区340通常包括一个或多个入口,其与hpna分离区320的一个或多个出口流体连通以接收hpna减少的分馏塔塔底物322和氢气源306。第二反应区340的一个或多个出口(其排出流出物流342)与分馏区310的一个或多个入口流体连通(任选地在第二反应区340和分馏区310之间具有一个或多个高压或低压分离级以用于回收再循环氢,未示出)。在系统300的操作中,将原料流302和氢流304加入到反应区336。氢流304包括有效量的氢以支持所必需的加氢裂化程度、进料类型和其他因素,并且可以是包括以下的任何组合:补充的氢、来自第一反应区336和分馏区310之间的任选的气体分离子系统(未示出)的再循环氢、来自第二反应区340和分馏区310之间的任选的气体分离子系统(未示出)的再循环氢、和/或来源于分馏塔气体流312。第一反应区336在用于生产反应流出物流338的有效条件下操作,(任选地在用于回收再循环氢的一个或多个高压或低压分离级之后)将反应流出物流338送到分馏区310。将反应流出物流338送到分馏区310,通常以回收气体和液体产品和副产品,并且分离含有hpna化合物的塔底物馏分。将气体流312(典型的含有h2、h2s、nh3和轻质烃(c1-c4))排出并回收,并且可以如本领域中已知的那样进一步处理,包括回收再循环氢。一种或多种裂化产品流314从分馏塔适当的出口排出,并且可以在下游炼油厂操作中进一步处理和/或共混以产生汽油、煤油和/或柴油燃料或其他石化产品。在某些实施方案(未示出)中,分馏区310可以作为闪蒸容器操作以在合适的切割点(例如对应于下游操作所期望的汽油、煤油和/或柴油产品的上限温度范围的范围)分离重质组分。在某些实施方案中,合适的切割点是350-450℃、360-450℃、370-450℃、350-400℃、360-400℃、370-400℃、350-380℃、或360-380℃。将来自反应流出物的分馏塔塔底物流316的全部或一部分(其包括在反应区336中形成的hpna化合物)送到hpna分离区320以用于进行处理。在某些实施方案中,来自反应流出物的分馏塔塔底物的一部分作为抽出流318除去。抽出流318可以是分馏塔塔底物316的约0-10v%、1-10v%、1-5v%或1-3v%。分馏塔塔底物中的hpna化合物的浓度在hpna分离区320中降低以产生hpna减少的分馏塔塔底物流322。含有hpna化合物的排出流324是从hpna分离区320中除去的。在某些实施方案中,代替或与抽出流318一起,hpna减少的分馏塔塔底物流322的一部分作为抽出流326从再循环回路中除去。抽出流326可以是hpna减少的分馏塔塔底物流322的约0-10v%、1-10v%、1-5v%或1-3v%。因此,将hpna减少的分馏塔塔底物流322的全部或一部分送到第二反应区340作为流322a。在某些实施方案中,将hpna减少的分馏塔塔底物流322的全部或一部分再循环到第二反应区340作为流322a,再循环到第一反应区336作为流322b,或再循环到第一和第二反应区336和340二者。例如再循环到区336的流322b包含0-100v%、0-约80v%或0-约50v%的流322,并且再循环到区340的流322a包含0-100v%、0-约80v%或0-约50v%的再循环到区340的流322。第二反应区340在对于生产反应流出物流342来说有效的条件下操作,所述反应流出物流342包含转化的、部分转化的和未经转化的烃。第二级将反应流出物流342送到分馏区310(任选地通过一个或多个气体分离器以回收再循环氢并除去某些轻质气体)。第一反应区336可以含有串联和/或并联排列的一种或多种固定床、沸腾床、淤浆床、移动床、连续搅拌槽(cstr)或管式反应器。一种或多种反应器通常在对于第一反应区336中的转化率、特定反应器类型、进料特性和期望的产品分布来说有效的条件下操作。例如这些条件可以包括约300-500℃、330-500℃、300-475℃、330-475℃、300-475℃或330-450℃的反应温度;约60-300bar、60-200bar、60-180bar、100-300bar、100-200bar、100-180bar、130-300bar、130-200bar、或130-180bar的反应压力;最高约2500slt/lt、在某些实施方案中是约800-2000slt/lt、800-1500slt/lt、1000-2000slt/lt、或1000-1500slt/lt的氢进料速率;和约0.1-10h-1、0.1-5h-1、0.1-2h-1、0.25-10h-1、0.25-5h-1、0.25-2h-1、0.5-10h-1、0.5-5h-1、或0.5-2h-1的进料速率。第一反应区336中所用的催化剂含有选自iupac元素周期表第6-10族的一种或多种活性金属组分。在某些实施方案中,活性金属组分是钴、镍、钨和钼中的一种或多种,其典型地沉积或引入到载体上,所述载体可以是无定形和/或结构化的如氧化铝、二氧化硅-氧化铝、二氧化硅、二氧化钛、二氧化钛-二氧化硅、二氧化钛-硅酸盐、或沸石。在使用沸石基催化剂的实施方案中,hpna化合物具有相对更高的在再循环流中聚集的倾向,这归因于这些较大的分子不能扩散到催化剂的孔结构中,特别是在反应器中相对较低的氢分压水平下。然而,根据本文的方法,通过从实施方案(其中将hpna减少的塔底物再循环到第一反应区336)中的再循环流中除去hpna化合物,增加了这样的沸石催化剂的寿命周期。第二反应区340可以含有串联和/或并联排列的一种或多种固定床、沸腾床、淤浆床、移动床、连续搅拌槽(cstr)或管式反应器。一种或多种反应器在对于特定反应器类型、进料特性和期望的产品分布来说有效的条件下操作。例如这些条件可以包括约300-500℃、330-500℃、300-475℃、330-475℃、300-475℃或330-450℃的反应温度;约60-300bar、60-200bar、60-180bar、100-300bar、100-200bar、100-180bar、130-300bar、130-200bar、或130-180bar的反应压力;最高约2500slt/lt、在某些实施方案中是约800-2000slt/lt、800-1500slt/lt、1000-2000slt/lt、或1000-1500slt/lt的氢进料速率;和约0.1-10h-1、0.1-5h-1、0.1-2h-1、0.25-10h-1、0.25-5h-1、0.25-2h-1、0.5-10h-1、0.5-5h-1、或0.5-2h-1的进料速率。第二反应区340中所用的催化剂含有选自iupac元素周期表第6-10族的一种或多种活性金属组分。在某些实施方案中,所述活性金属组分是钴、镍、钨和钼中的一种或多种。在其中第一反应区减少了污染物如硫和氮以便硫化氢和氨在第二反应区中最小化的实施方案中,作为加氢催化剂有效的活性金属组分可以包括一种或多种单独的或与其他活性金属组合的贵金属如铂或钯。一种或多种活性金属组分典型地沉积或引入到载体上,所述载体可以是无定形和/或结构化的如氧化铝、二氧化硅-氧化铝、二氧化硅、二氧化钛、二氧化钛-二氧化硅、二氧化钛-硅酸盐、或沸石。在使用沸石基催化剂的实施方案中,hpna化合物具有相对更高的在再循环流中聚集的倾向,这归因于这些较大的分子不能扩散到催化剂的孔结构中,特别是在反应器中相对较低的氢分压水平下。然而,根据本文的方法,通过从实施方案(其中将hpna减少的塔底物再循环到第二反应区340)中的再循环流中除去hpna化合物,增加了这样的沸石催化剂的寿命周期。如上所述,重质多核芳族化合物的形成是加氢裂化单元从业者的一个主要关心的问题。所有已知的加氢裂化工艺和催化剂经受导致形成重质多核芳族(hpna)化合物的不期望的副反应,所述重质多核芳族(hpna)化合物聚集在未经转化的油再循环流中。这些化合物几乎不可能通过加氢裂化反应转化,并且表现出在再循环油流中积聚至高浓度水平的强烈倾向。随着浓度积聚,反应器系统的性能连续下降,这导致低效和不经济的状态。这些问题通过本发明的方法,通过吸附和离子液体萃取从再循环流中除去hpna分子得以解决。经处理的再循环流(其基本上没有hpna或具有减少的hpna)将延长加氢裂化单元的有效运行、催化剂活性、稳定性并增加产品收率和质量。本发明的方法和系统可以作为加氢裂化系统(例如以上参考图1、2和/或3所描述的)下游整合的吸附和萃取操作而有利地安装于现有炼油厂中,以便从再循环流中除去hpna化合物从而为用于从再循环流中除去hpna化合物的炼油厂加氢裂化单元操作提供灵活性,并且避免净化再循环流的一部分的需要,由此改进单元操作的整体效率。整合到本文中所述的加氢裂化系统100、200和300中的hpna分离区120、220和320及其对本领域技术人员来说显而易见的变化有效地从塔底物再循环流中除去hpna化合物。这些塔底物馏分含有在反应区中形成的hpna化合物,并且在hpna分离区中处理以分离hpna化合物并产生hpna减少的加氢裂化的塔底物流。根据本文的各种实施方案,含有hpna化合物的加氢裂化的塔底物馏分以任一次序(即与实施方案1或实施方案2一致)在适于除去hpna的反应条件下经受离子液体萃取和吸附,并形成hpna减少的加氢裂化塔底物馏分。所述塔底物馏分主要是环烷烃和石蜡烃。参见图5,图示了一种用于从加氢裂化器再循环流和进料中除去hpna的方法和系统500,其包括吸附区、离子液体萃取器区和分离区。将理解,所述方法和系统500可以是上述120、220或320中的任何一种。吸附区510包括入口,以用于接收富含hpna/hpna前体的加氢裂化器渣油进料116、216或316和加氢裂化器塔底物再循环流503。将来自吸附塔510的流出物512(其已经除去了hpna和hpna前体的大部分)送到萃取器560的入口。萃取器560也具有用于接收由一种或多种离子液体组成的离子液体流542的入口。萃取器560用离子液体从烃油中萃取剩余的hpna/hpna前体。将来自萃取器560的经萃取的hpna/hpna前体与离子液体经由流524送到溶剂萃取器540的入口。萃取器540使用经由溶剂流562引入的有机极性溶剂,以将hpna/hpna前体从离子液体中分离。将回收的离子液体经由流542再循环到萃取器560。将剩余的溶剂和hpna/hpna前体从溶剂萃取器540经由流544送到溶剂回收单元550,在这里回收所述溶剂并且经由流554再循环回溶剂萃取器540。剩余的hpna/hpna前体经由流124、224或324从溶剂回收单元回收。将基本上没有hpna/hpna前体或离子液体的经处理的流522从萃取器560送到液-液分离器530。将任何剩余的离子液体和hpna/hpna前体从剩下的烃流中分离,并且经由流534从液-液分离器530排出。hpna化合物和hpna前体和离子液体流534在被送到溶剂萃取器540之前与hpna/hpna前体和离子液体流524混合。hpna减少的分馏塔塔底物122、222或322则基本上没有hpna/hpna前体并且可以被回收作为到加氢裂化单元的进料(未示出)。参见图6,图示了一种用于从加氢裂化器进料除去hpna化合物和hpna前体的方法和系统600。所述系统包括离子液体萃取区、吸附区和分离区。将理解,所述方法和系统600可以是上述120、220或320中的任何一种。所述离子液体萃取区包括萃取器660,其具有用于接收富含hpna化合物和hpna前体的加氢裂化器渣油进料116、216或316,离子液体流642以及加氢裂化器塔底物再循环流603的入口。萃取器660用离子液体萃取hpna化合物和hpna前体的大部分。将来自萃取器660的经萃取的hpna/hpna前体与离子液体经由流624送到溶剂萃取器640的入口。萃取器640使用经由溶剂流662引入的极性有机溶剂,以将hpna/hpna前体从离子液体中分离。将经回收的离子液体经由流642再循环到萃取器660。剩余的溶剂和hpna/hpna前体从溶剂萃取器640经由流644送到溶剂回收单元650,在这里回收所述溶剂,并且经由流654再循环回溶剂萃取器640。剩余的hpna/hpna前体经由流124、224或324从溶剂回收单元回收。将已经除去hpna/hpna前体和离子液体的大部分的经处理的流622从萃取器660送到液-液分离器630。剩余的离子液体和hpna/hpna前体从烃流中分离并且经由流334从液-液分离器630中排出。hpna/hpna前体和离子液体流334在被送到溶剂萃取器340之前与hpna/hpna前体和离子液体流624混合。将hpna/hpna前体含量明显降低的流632送到吸附塔610以除去任何剩余的hpna/hpna前体或离子液体。将来自吸附塔610的分馏塔塔底物流122、222或322(其基本上没有hpna/hpna前体)回收以用作到加氢裂化单元的进料。实施例以下的实验室实施例证实所述方法在从加氢裂化器塔底物中分离hpna化合物和前体中的有效性。实施例1离子液体萃取将80g的加氢裂化单元塔底物和20g的离子液体六氟磷酸1-丁基-3-甲基咪唑的混合物加热到50℃并且在50℃下连续搅拌30分钟。其后伴随搅拌将100毫升戊烷加入到混合物中以确保成分的充分接触。将混合物转移至分液漏斗以分离离子液体和油-戊烷混合物。在旋转蒸发器中将戊烷从油-戊烷混合物中蒸发,并且回收经处理的加氢裂化单元塔底物流。实施例的物料平衡显示在表1中。实施例2离子液体萃取,随后吸附将80g的加氢裂化单元塔底物和20g的离子液体六氟磷酸1-丁基-3-甲基咪唑的混合物加热到50℃并且在50℃下连续搅拌30分钟。其后伴随搅拌将100毫升戊烷加入到混合物中以确保成分的充分接触。将混合物转移至分液漏斗以分离离子液体和油-戊烷混合物。将油-戊烷混合物送过含有60g凹凸棒石粘土的塔。收集塔流出物并且加入更多的戊烷,直到从所述塔获得无色的流出物。戊烷在旋转蒸发器中蒸发,并且获得经处理的加氢裂化器塔底物流。这个实施例的物料平衡显示在表1中。实施例3吸附,随后离子液体萃取将80g的加氢裂化单元塔底物和100毫升戊烷的混合物搅拌以溶解所述油。将所述溶液送过含有60g凹凸棒石粘土的塔。收集塔流出物并且加入更多的戊烷,直到从所述塔获得无色的流出物,收集全部的塔流出物并与20g的离子液体六氟磷酸1-丁基-3-甲基咪唑混合。将所述混合物加热并在50℃下伴随连续搅拌保持30分钟。将混合物转移至分液漏斗以用于将离子液体从油相中分离。戊烷在旋转蒸发器中蒸发,并且回收经处理的加氢裂化器塔底物流。这个实施例的物料平衡显示在表1中。表1-物料平衡如上所述,所采用的离子液体是六氟磷酸1-丁基-3-甲基咪唑使用高压液相色谱法(hplc)分析来自实施例1和2的产品的hpna分子。结果汇总在表2、3和4中。这些分子的结构显示在图4中。表2-实施例1的hpna分布表3-实施例2的hpna分布hpna环数进料产品除去率ppmwppmww%苯并二萘嵌苯61540126617.8晕苯720113533.1甲基晕苯720411145.4萘并晕苯7794938.1二苯并晕苯926485.1卵苯1015288.6总计2065.0156724.1表4-实施例3的hpna分布hpna环数进料产品除去率ppmwppmww%苯并二萘嵌苯61540109928.6晕苯720110348.8甲基晕苯72048757.5萘并晕苯7793851.5二苯并晕苯926390.2卵苯1015192.6总计2065133135.5在加氢裂化单元中最难以处理的hpna化合物是由10个或更多个稠合芳族环形成的分子。如表2中上述,在离子液体萃取后10环卵苯的除去率仅为12w%。然而,当将吸附步骤加入到两级处理中的离子液体萃取步骤中时,从加氢裂化塔底物流中除去了多达92w%的卵苯。上述方法的结合的吸附随后是萃取步骤以及萃取随后是吸附步骤在除去基本上所有的hpna化合物和hpna前体方面都是高效且有效的,而没有显著损失进料和/或加氢裂化器塔底物再循环流。以上并且在附图中已经描述了本发明的方法和系统;然而,改进对于本领域技术人员来说是显而易见的,并且本发明的保护范围由随后的权利要求所确定。权利要求书(按照条约第19条的修改)1.一种处理含有重质多核芳族(hpna)化合物和hpna前体的加氢裂化单元塔底物再循环流以降低hpna化合物和前体含量的方法,所述方法包括:a.使塔底物再循环流与有效量的吸附剂材料在吸附容器中接触,以产生hpna化合物和hpna前体含量降低的经吸附剂处理的塔底物再循环流;b.回收并将所回收的经吸附剂处理的塔底物再循环流与一种或多种离子液体引入到萃取单元中预定的时间,以萃取hpna化合物和hpna前体并且产生萃取单元流出物流和经处理的流;c.从萃取单元回收含有经萃取的hpna化合物和hpna前体和所述一种或多种离子液体的混合物的流出物流并将其引入到分离单元以用于与有机极性溶剂接触;d.将所述混合物在所述分离单元中保持足以在极性溶剂中形成hpna化合物和hpna前体的溶液的时间;e.从所述分离单元回收所述一种或多种离子液体,以用于在萃取单元中再利用;f.将含有hpna化合物和hpna前体的溶剂转移至溶剂回收单元并且回收溶剂流,以用于在分离单元中再利用;g.将剩余的经处理的流从萃取单元转移至液-液分离器并且作为以下分开的流回收:(i)hpna化合物含量明显降低的经处理的烃流,(ii)残留离子液体,和(iii)hpna化合物和hpna前体。2.权利要求1的方法,其中将新鲜的加氢裂化单元进料与所述加氢裂化单元塔底物再循环流合并,并且处理经合并的流。3.权利要求1的方法,其中所述一种或多种离子液体具有通式q+a-,其中所述a-离子选自卤素阴离子、硝酸根、硫酸根、磷酸根、乙酸根、卤代乙酸根、四氟硼酸根、四氯硼酸根、六氟磷酸根、六氟锑酸根、氟磺酸根、烷基磺酸根、全氟烷基磺酸根、双(全氟烷基磺酰基)酰胺、式c(cf3so2)3-的三-三氟甲磺酰基甲基化物、未取代的芳烃磺酸根、卤素或卤代烷基取代的芳烃磺酸根,和其中所述q+离子是将与a-离子形成液体化合物的铵阳离子、阳离子或锍阳离子。4.权利要求3的方法,其中所述一种或多种离子液体选自六氟磷酸n-丁基-吡啶四氟硼酸n-乙基-吡啶氟磺酸吡啶四氟硼酸丁基-3-甲基-1-咪唑丁基-3-甲基-1-咪唑双-三氟甲烷-磺酰基酰胺、三乙基锍双-三氟甲烷-磺酰基酰胺、六氟锑酸丁基-3-甲基-1-咪唑六氟磷酸丁基-3-甲基-1-咪唑三氟乙酸丁基-3-甲基-1-咪唑三氟甲基磺酸丁基-3-甲基-1-咪唑丁基-3-甲基-1-咪唑双(三氟甲基磺酰基)-酰胺、六氟磷酸三甲基-苯基铵、四氟硼酸四丁基及其混合物。5.权利要求1的方法,其中所述萃取单元在20-200℃的温度、1-30bar的压力下,并且在1:1-10:1的离子液体与hpna的摩尔比下操作。6.权利要求1的方法,其中所述萃取单元选自板式塔、喷洒塔、填料塔、转盘塔和脉冲塔。7.权利要求1的方法,其中所述吸附剂材料处于填料床或淤浆床形式的吸附塔中。8.权利要求7的方法,其中所述吸附塔在20-200℃的温度和1-30bar的压力下操作。9.权利要求1的方法,其中所述吸附剂材料选自凹凸棒石粘土、氧化铝、二氧化硅、活性炭、天然和合成沸石、用过的催化剂、二氧化硅-二氧化钛和二氧化钛。10.权利要求1的方法,其中所述有机极性溶剂具有大于约8.5的整体溶解度参数。11.权利要求9的方法,其中所述有机极性溶剂选自甲苯、苯、二甲苯、四氢呋喃及其混合物。12.一种处理含有重质多核芳族(hpna)化合物和hpna前体的加氢裂化单元塔底物再循环流以降低hpna化合物和前体含量的方法,所述方法包括:a.将塔底物再循环流与一种或多种离子液体引入到萃取单元预定的时间段,以萃取hpna化合物和hpna前体并且产生萃取单元流出物流和经处理的流;b.将含有经萃取的hpna化合物和hpna前体和所述一种或多种离子液体的萃取单元流出物流引入到分离单元,以用于与有机极性溶剂接触;c.将所述分离单元中的液体混合足以在极性溶剂中形成hpna化合物和hpna前体的溶液的时间;d.从所述分离单元回收所述一种或多种离子液体,以用于在萃取单元中再利用;e.将含有hpna化合物和hpna前体的溶剂转移至溶剂回收单元并且回收溶剂流以用于在分离单元中再利用;f.将剩余的经处理的流从所述萃取单元转移至液-液分离器并且作为以下分开的流回收:(i)hpna化合物和hpna前体含量明显降低的经处理的烃再循环流,(ii)残留离子液体,和(iii)hpna化合物和hpna前体;g.使经处理的烃再循环流与有效量的吸附剂材料接触以产生经吸附剂处理的烃再循环流;和h.回收hpna化合物含量降低的经吸附剂处理的再循环流。13.权利要求12的方法,其中将新鲜的加氢裂化单元进料与所述加氢裂化单元塔底物再循环流合并,并且处理经合并的流。14.权利要求12的方法,其中所述一种或多种离子液体具有通式q+a-,其中所述a-离子选自卤素阴离子、硝酸根、硫酸根、磷酸根、乙酸根、卤代乙酸根、四氟硼酸根、四氯硼酸根、六氟磷酸根、六氟锑酸根、氟磺酸根、烷基磺酸根、全氟烷基磺酸根、双(全氟烷基磺酰基)酰胺、式c(cf3so2)3-的三-三氟甲磺酰基甲基化物、未取代的芳烃磺酸根、卤素或卤代烷基取代的芳烃磺酸根,和其中所述q+离子是将与a-离子形成液体化合物的铵阳离子、阳离子或锍阳离子。15.权利要求14的方法,其中所述一种或多种离子液体选自六氟磷酸n-丁基-吡啶四氟硼酸n-乙基-吡啶氟磺酸吡啶四氟硼酸丁基-3-甲基-1-咪唑丁基-3-甲基-1-咪唑双-三氟甲烷-磺酰基酰胺、三乙基锍双-三氟甲烷-磺酰基酰胺、六氟锑酸丁基-3-甲基-1-咪唑六氟磷酸丁基-3-甲基-1-咪唑三氟乙酸丁基-3-甲基-1-咪唑三氟甲基磺酸丁基-3-甲基-1-咪唑丁基-3-甲基-1-咪唑双(三氟甲基磺酰基)-酰胺、六氟磷酸三甲基-苯基铵、四氟硼酸四丁基及其混合物。16.权利要求12的方法,其中所述萃取单元在20-200℃的温度、1-30bar的压力下,以及在1:1-10:1的离子液体与hpna的摩尔比下操作。17.权利要求12的方法,其中所述萃取单元选自板式塔、喷洒塔、填料塔、转盘塔和脉冲塔。18.权利要求12的方法,其中所述吸附剂材料处于填料床或淤浆床形式的吸附塔中。19.权利要求18的方法,其中所述吸附塔在20-200℃的温度和1-30bar的压力下操作。20.权利要求12的方法,其中所述吸附剂材料选自凹凸棒石粘土、氧化铝、二氧化硅、活性炭、天然和合成沸石、用过的催化剂、二氧化硅-二氧化钛和二氧化钛。21.权利要求12的方法,其中所述有机极性溶剂具有大于约8.5的整体溶解度参数。22.权利要求21的方法,其中所述有机极性溶剂选自甲苯、苯、二甲苯、四氢呋喃及其混合物。当前第1页12