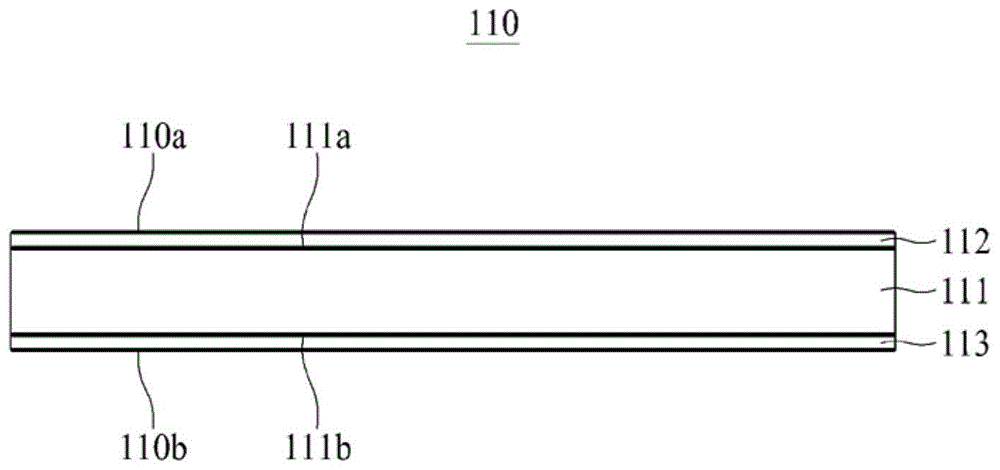
本发明涉及一种电解铜箔,更具体而言,涉及一种与锂二次电池的活性物质具有高附着力的电解铜箔。
背景技术:
:随着智能电话、笔记本等便携式家电的广泛使用以及混合动力汽车的普及,对锂电池的需求正在急剧增加。在锂二次电池中,阳极集电体一般由电解铜箔制成。电解铜箔通过利用电镀法的制箔工艺制造,从而在制造的电解铜箔的一个面上形成具有较低粗糙度的光泽表面(shinysurface),并且在另一个面上形成具有相对较高粗糙度的无光泽表面(mattesurface)。在电解铜箔的无光泽表面上涂覆有诸如碳(carbon)系浆料的活性物质。在锂二次电池中,活性物质与用作集电体的电解铜箔之间的附着力取决于电解铜箔的表面状态,且通过该附着力可以确定锂二次电池的容量和产率。尤其,如果集电体与活性物质之间的附着力低,则在二次电池的寿命周期期间活性物质从集电体分离,从而可能引起诸如内部短路的问题。同时,众所周知,电解铜箔表面上呈亲水性的氧会提高与活性材料的附着力。然而,铜箔表面层的氧具有增加表面电阻的缺点。因此,为了制造具有可靠性的锂二次电池,需要控制铜箔表面层。技术实现要素:发明所要解决的问题为了实现所述技术课题,本发明的目的在于,提供一种锂二次电池用电解铜箔,该电解铜箔与活性物质具有高附着力,并且具有低电阻。另外,本发明的目的在于,提供一种电解铜箔,该电解铜箔具有表现出高附着力和低电阻的表面氧层分布。另外,本发明的目的在于,提供一种制造上述电解铜箔的方法。另外,本发明的目的在于,提供一种锂二次电池用阳极,其包括上述的电解铜箔,并且具有高放电容量保持率。解决问题的技术方案为了解决上述技术课题,本发明提供了一种具有第一暴露表面和与所述第一暴露表面相对的第二暴露表面的电解铜箔,其特征在于,包括:位于所述第一暴露表面处的第一保护层;位于所述第二暴露表面处的第二保护层;以及介于所述第一保护层和所述第二保护层之间的铜膜,其中,位于所述第二暴露表面处的含氧部厚度ot不小于1.5nm且小于8.0nm,位于所述第二暴露表面处的含氧部厚度是第二保护层的一部分的sio2转化厚度,且所述第二保护层的一部分是通过aes(俄歇电子能谱)从所述第二暴露表面测量的氧成分浓度不小于10原子%的部分。在本发明中,所述第一保护层和第二保护层优选包含铬酸盐。另外,从所述第二暴露表面测量的氧成分浓度表现出随着从所述第二暴露表面的深度变深而增加然后降低的趋势。在本发明的一个实施例中,含氧部厚度优选为小于8.0nm。另外,在本发明的一个实施例中,所述电解铜箔在110℃热处理10分钟之后的断裂强度优选为25kgf/mm2至57kgf/mm2。另外,根据本发明的一个实施例,所述第一暴露表面的含氧部厚度与所述第二暴露表面的含氧部厚度之差优选为不大于5.8nm。为了解决所述另一技术课题,本发明提供一种制造电解铜箔的方法,该方法包括:向在电解槽中的电解液内彼此隔开配置的阳极板和旋转阴极滚筒之间施加电流,以在所述旋转阴极滚筒上电镀铜膜;卷绕所述铜膜;以及将所述铜膜浸入抗腐蚀处理溶液中进行抗腐蚀处理,其中,在进行所述抗腐蚀处理时,将空气注入到所述抗腐蚀处理溶液。此时,空气的注入可以通过鼓风机进行。另外,优选将所述抗腐蚀处理溶液的溶存氧量保持在3ppm至12ppm。另外,在本发明中,优选将所述电解液的tic浓度保持在0.05g/l以下,将fe浓度保持在0.3g/l以下。为了解决所述又一技术课题,本发明提供一种锂二次电池用阳极,该阳极包括:集电体,包括具有第一表面和与所述第一表面相对的第二表面的电解铜箔;以及位于所述第一表面和所述第二表面上的阳极活性物质层,其中所述电解铜箔包括:位于所述第一表面处的第一保护层;位于所述第二表面处的第二保护层;以及介于所述第一保护层和所述第二保护层之间的铜膜,其中,位于所述第二表面处的含氧部厚度ot不小于1.5nm,位于所述第二表面处的含氧部厚度是第二保护层的一部分的sio2转化厚度,且所述第二保护层的一部分是通过aes(俄歇电子能谱)从所述第二表面测量的氧成分浓度不小于10原子%的部分。发明效果根据本发明,能够提供一种锂二次电池用电解铜箔集电体,其与活性物质具有高附着力,并且具有低电阻。另外,本发明能够提供一种电解铜箔集电体,其表面氧浓度分布被调节为与活性物质具有高附着力。另外,本发明能够提供一种具有高放电容量保持率的锂二次电池的阳极。附图说明图1是示出根据本发明实施例的电解铜箔的截面结构的示意图。图2是示出根据本发明实施例的锂二次电池用阳极的截面结构的示意图。图3示意性地示出制造本发明的电解铜箔的装置。图4是示出使用aes装置对实施例1的电解铜箔的m表面进行测量而得到的各成分的浓度分布的图。图5是示出根据本发明的一个实施例使用aes装置对电解铜箔的m表面进行测量而得到的氧浓度分布的图。具体实施方式下面,参照附图描述本发明的优选实施例。图1是示出根据本发明实施例的电解铜箔的截面结构的示意图。参照图1,电解铜箔110具有第一暴露表面110a和与所述第一暴露表面110a相对的第二暴露表面110b,并且包括:形成所述第一暴露表面110a的第一保护层112;形成所述第二暴露表面110b的第二保护层113;以及位于所述第一保护层112和第二保护层113之间的铜膜111。在本发明中,所述电解铜箔110具有预定厚度,例如4μm至30μm的厚度。在铜箔的厚度小于4μm的情况下,导致电池制造工艺中的操作性降低,在铜箔的厚度大于30μm的情况下,当制造锂二次电池时,因铜箔较厚的厚度而难以实现高容量。所述铜膜111通过电镀形成在旋转阴极滚筒上,并且具有光泽表面(s表面)111a和无光泽表面(m表面)111b,其中,在电镀过程中与所述旋转阴极滚筒直接接触的表面为光泽表面(s表面)111a,其相对面为无光泽表面(m表面)111b。优选地,所述第一保护层112和第二保护层113包括抗腐蚀涂层。所述抗腐蚀涂层包含铬酸盐(chromate)化合物。所述第一保护层112和第二保护层113防止所述铜膜111被氧化和腐蚀,并提高了活性物质的附着力。在本发明中,所述电解铜箔的厚度方向的氧成分分布具有以下特征。所述电解铜箔的m表面111b上的含氧部厚度ot优选不小于1.5nm。在此,所述m表面111b处的含氧部厚度ot是所述第二保护层113的一部分的sio2转化厚度,所述第二保护层113的一部分是通过aes(俄歇电子能谱)从m表面111b测量的氧成分浓度不小于10原子%的部分。另外,所述m表面111b处的含氧部厚度优选小于8.0nm。在含氧部厚度小于1.5nm的情况下,赋予表面亲水性的氧的活性位点数不足,使阳极材料不能在铜箔表面提供足够的附着力,因此阳极材料容易从铜箔分离,当制造锂二次电池之后进行充电/放电评价时,电池的充电效率迅速降低。在含氧部厚度大于8.0nm的情况下,铜箔表面的电阻增加,因此在制造锂二次电池之后,因高电阻而使充电效率降低。另外,在本发明中,电解铜箔的m表面111b和s表面111a上的含氧部厚度ot之差优选为不大于5.8nm。所述s表面111a上的含氧部厚度ot与所述m表面111b上的含氧部厚度ot相似,是指所述第一保护层112的一部分的sio2转化厚度,其中,通过aes从所述s表面111a的表面测量的氧成分的浓度不小于10原子%。如果m表面111b和s表面111a上的含氧部厚度之差(氧厚度差)大于5.8nm,则在铜箔的两个表面涂覆阳极材料并进行干燥之后,在铜箔的两个表面上制得的极板因铜箔与阳极材料之间的附着力之差而发生弯曲,并且在锂二次电池的卷对卷(rolltoroll)工艺中发生折叠。在本发明中,所述电解铜箔在110℃下热处理10分钟之后的断裂强度优选为25kgf/mm2至57kgf/mm2。在断裂强度低于25kgf/mm2的情况下,当通过使用含有si的活性材料来制造锂二次电池并进行充电/放电评价时,由于铜箔自身的强度不足而发生断线,继而迅速降低充电效率。在断裂强度高于57kgf/mm2的情况下,铜箔的拉伸特性明显降低,从而当对锂二次电池实施充电/放电评价时,铜箔可能因不能承受体积膨胀而导致电极断线,继而迅速降低充电效率。另外,在本发明中,所述电解铜箔在宽度方向上的重量偏差优选为小于5%。如果重量偏差大于5%,则在制造铜箔和锂二次电池的过程中可能发生褶皱。另外,在本发明中,m表面111b的表面分布中的最大高度(rp)优选在0.36μm至1.69μm的范围内。如果电解铜箔的表面分布中的最大高度低于0.36μm,则铜箔表面不能充分地提供能够均匀地涂覆活性物质的活性位点,因此活性物质不能被均匀地在其上涂覆。另外,如果最大高度高于1.69μm,则因铜箔表面的峰的高度过高而导致活性物质的涂覆不均匀,从而发生与上述相同的现象,并且由于活性物质的不均匀涂覆,导致活性物质在电极表面局部脱离。可选地,在本发明中,所述第一保护层112和第二保护层113还可以包括粗糙化处理层。所述粗糙化处理层可以通过电镀铜、钴以及镍中的一种或电镀它们中的两种以上的合金来形成,并且可以夹设在所述抗腐蚀涂层和铜膜之间。图2是示出根据本发明实施例的锂二次电池用阳极的截面结构的示意图。参照图2,如结合图1所描述,具有第一表面110a和第二表面110b的电解铜箔110包括:形成所述第一表面110a的第一保护层112;形成所述第二表面110b的第二保护层113;以及介于所述第一保护层112和第二保护层113之间的铜膜111。在所述第一保护层112和第二保护层113上设置有阳极活性物质层120。所述阳极活性物质层120可以包含石墨、焦炭等的碳系化合物。另外,所述阳极活性物质层120的活性物质可以包括选自于由si、ge、sn、li、zn、mg、cd、ce、ni以及fe构成的组中的至少一种金属;包含该金属的合金;或包含该金属的化合物。另外,所述阳极活性物质层120的活性物质可以是所述金属和碳的复合体。另外,所述阳极活性物质层120还可以包括导电材料和粘合剂。图3示意性地示出制造本发明的电解铜箔的装置。在图3的制造电解铜箔的装置中,示出了包括制箔步骤(film-formingstep)和后续的抗腐蚀处理步骤的一系列卷对卷工艺。如图3所示,在电解槽10内的电解液20中设置有彼此隔开配置的阳极板30和旋转阴极滚筒40。旋转阴极滚筒40沿预定方向旋转,并且,当施加电流时,通过以阴极滚筒40和阳极板30之间的电解液20为介质进行通电来执行电镀。电镀到阴极滚筒40表面的铜膜100被导辊50卷绕。可以使用硫酸铜镀液、焦磷酸铜镀液或氨基磺酸铜镀液等作为沉积所述电解铜箔的电解液20。在本发明中,优选使用硫酸铜镀液作为电解液。此时,所述阳极板30可以包括彼此电绝缘的第一阳极板31和第二阳极板32。此时,由所述阳极板30,即由所述第一阳极板31和第二阳极板32中的每一个提供的电流密度可以是40a/dm2至80a/dm2。电流密度越高,表面电镀越均匀,因此铜箔的平均rp降低。在电流密度高于80a/dm2的情况下,rp低于所要求的下限,另一方面,在rp低于40a/dm2的情况下,电镀被粗略地进行,rp高于所要求的规格上限。在本发明的一个实施例中,所述电解液20可以包含70g/l至90g/l的铜离子、80g/l至120g/l的硫酸。在本发明中,电解液中的总无机碳(totalinorganiccarbon;tic)含量应保持在0.05g/l以下,fe含量应保持在0.3g/l以下。如果tic浓度大于0.05g/l,则无机有机成分促进镀层生长,从而降低断裂强度。另外,如果fe的浓度大于0.3g/l,则fe成分与铜共沉积,由此生成的合金会将断裂强度过度提高。另外,在制箔步骤中,所述电解液60优选保持在50℃至60℃,并且向所述电解槽10内供应的所述电解液20的流量优选保持在40m3/小时至46m3/小时的范围内。在所述电解液20的流量不超过40m3/小时的情况下,不能将铜离子充分地供应到旋转阴极滚筒40表面,从而使电镀薄膜不均匀地形成,在所述电解液20的流量超过46m3/小时的情况下,通过过滤器的电解液20的流速过快,从而导致过滤器的寿命大幅缩短。由导辊80将通过电镀制造的铜膜投入到抗腐蚀处理槽50。在本发明中,抗腐蚀处理溶液60包含铬酸盐。可以使用诸如m2cr2o7(其中,m是单价金属)的重铬酸盐或诸如cro3的铬酸与碱金属氢氧化物和酸的混合水溶液。另外,处理溶液还可以包含诸如zno或znso4·7h2o等的锌盐。根据需要,所述抗腐蚀处理溶液还可以包含有机添加剂。在本发明的一个实施例中,为了将铜箔的表面上的含氧部厚度保持在适当范围内,将抗腐蚀液的溶存氧量保持在一定水平。为此,在抗腐蚀处理槽设置有鼓风机70。通过控制鼓风机70的流量来控制抗腐蚀处理溶液60中的溶存氧量。如后述的本发明的实施例所述,溶存氧量保持在3ppm至12ppm的范围。在本发明中,抗腐蚀处理可以通过铜膜的简单浸渍或电沉积来进行,优选通过电沉积来进行。同时,在抗腐蚀处理步骤中,与暴露在所述抗腐蚀液60中的相对面(例如,m表面111b)相比,与所述导辊接触的铜膜111的表面(例如,s表面111a)涂覆较少的抗腐蚀处理溶液60。其结果,铜膜111的s表面111a与m表面111b上的电沉积量之差可能会导致电解铜箔110的折叠和/或卷曲(起皱)。因此,在本发明中,可以使铜膜与所述导辊接触的时间最小化,例如,优选使用水平抗腐蚀处理等方法。下面,将详细描述本发明的优选实施例。<电解铜箔的制造>使用如图3所示的装置使在电解槽内的电解液中隔开配置的阳极板和旋转阴极滚筒之间通电流,由此在所述旋转阴极滚筒上形成了铜膜。电解液由75g/l的铜离子和100g/l的硫酸制成。在不同的条件(不同的电解液的tic含量和fe含量)下制造铜膜。所述电解液保持在约55℃,电流密度为60a/dm2,并且电解液流量为42m3/小时。接着,通过如下所述的方式制备了抗腐蚀液。首先,将cro3粉末分散到水溶液中,使cr离子的浓度达到2.2g/l。此时,抗腐蚀溶液的ph保持在1.8至2.2。另外,以0.2g/l至0.4g/l的量添加柠檬酸。用硫酸或氢氧化钠水溶液调节了所制备的抗腐蚀溶液的ph。通过使用鼓风机向所制备的抗腐蚀溶液注入不同量的空气,来实现具有不同溶存氧量的抗腐蚀溶液,并且将制造的铜膜在常温(30℃)下浸入具有不同溶存氧量的抗腐蚀溶液中10秒。使用日本toadkk公司的溶存氧测量计测量了抗腐蚀处理溶液中的溶存氧量。接着,通过干燥所述氧化铬溶液来在所述铜膜的两个表面上形成抗腐蚀涂层,由此制造了具有4μm的厚度的电解铜箔。所制造的铜箔的制箔和抗腐蚀处理条件如下表1所示。[表1]tic(g/l)fe(g/l)溶存氧量(ppm)实施例10.020.123.2实施例20.020.1211.7实施例30.040.127.5实施例40.020.297.5比较例10.020.122.7比较例20.020.1212.5比较例30.060.127.5比较例40.020.347.5接着,测量了所制造的电解铜箔的特性。测量方法如下:断裂强度使用utm抓住电解铜箔样品的两端拉伸,然后测量了断裂时的强度。样品的宽度为12.7mm,夹具之间的距离为50mm,测量速度为50mm/min。m表面上的含氧部厚度ot使用由ulvac-phiinc提供的aes分析装置的phi700模型,在以下条件下分析了所制造的电解铜箔的m表面的氧浓度的深度分布。电子能量分析器:筒镜分析器(cma)电子束能量:5kev目标电流:10na离子能量,溅射速度:2kvar,/min(sio2转化)离子束斑尺寸:2×2mm2含氧部厚度ot:根据以下公式(sio2转化标准),利用溅射蚀刻时间求得了通过aes测量氧浓度的深度。[公式1]sio2转化深度=溅射蚀刻时间(min)×溅射速度(/min)将测量的氧浓度为10原子%的点的转化深度作为含氧部厚度ot。m表面与s表面上的含氧部厚度差(otd)通过与上述相同的方法求得s表面的ot,并且计算了m表面与s表面的ot差。是否发生折叠用肉眼观察了在二次电池的卷对卷工艺中,电解铜箔是否发生折叠。<阳极的制造>用在前述的实施例1-4和比较例1-4中制造的电解铜箔准备了宽度为10cm的集电体。集电体上的阳极活性物质使用了以9:1的重量比混合的碳和sio2。此时,将2重量份的sbr(苯乙烯-丁二烯橡胶)和2重量份的cmc(羧甲基纤维素)与100重量份的阳极活性物质混合,并使用蒸馏水作为溶剂制备浆料,使用刮刀以60μm厚度涂抹阳极活性物质,在120℃下干燥之后,在1吨/cm2的压力下施压,由此制造了阳极。<锂二次电池的制造>将作为溶质的lipf6以1m的浓度溶解在以1:2的比例混合碳酸乙烯酯(ec)和碳酸甲乙酯(emc)的非水性有机溶剂中制成碱性电解液,然后,通过混合99.5重量%该碱性电解液和0.5重量%的琥珀酸酐来制备了非水性电解液。将锂锰氧化物li1.1mn1.85al0.05o4和具有正交晶体结构的锂锰氧化物o-limno2以90:10的重量比混合,由此制备了阴极活性物质。将所述阴极活性物质、炭黑以及作为粘合剂的聚(偏二氟乙烯)(pvdf)以85:10:5的重量比与作为有机溶剂的nmp混合,由此制备了浆料。将制备的浆料涂抹到厚度为20μm的al箔两面之后,进行干燥,由此制造了阴极。利用制造的阴极、阳极以及电解液来制造锂二次电池单元,并且对制造的二次电池的特性进行了评价。使用4.3v充电/3.4v放电操作电压测量了由阳极、电解液以及阴极制造的电池的容量,为了评价高温寿命,在50℃的高温下,以0.2c的充电/放电速度进行了500次充电/放电实验,从而计算了放电容量保持率。在此,放电容量保持率是每个样品测量5次的算数平均值。在以下表2中示出了实施例1-4和比较例1-4的电解铜箔的特性。另外,整理并示出了将相应电解铜箔作为集电体制造的锂二次电池单元的放电容量保持率。[表2]首先,参照表1和表2,比较除了溶存氧量以外的条件相同的实施例1和比较例1,可见实施例1的ot高于比较例1。这表示,与比较例1相比,实施例1的电解铜箔可以在表面上提供更多的氧活性位点。另外,实施例1显示出不小于90%的放电容量保持率,而比较例1的放电容量保持率具有小于90%的值,由此,在比较例1的情况下,阳极材料不能在铜箔表面形成足够的附着力,因此在反复的充电/放电评价时充电效率急剧下降。另外,比较在较高溶存氧量条件下制造的实施例2和比较例2可知,溶存氧量相对较低的实施例2(11.7ppm)的ot低于比较例2(12.5ppm)的ot。另外,示出了与使用比较例2的集电体制造的电池相比,使用实施例2的集电体制造的电池具有更高的放电容量保持率。因此,可以确认到过高的ot水平增加了铜箔表面电阻,从而降低了放电容量保持率。图4是示出使用aes装置对实施例1的电解铜箔m表面进行测量而得到的各个成分的浓度分布的图,图5是示出使用aes装置对实施例1、2以及比较例2的电解铜箔的m表面进行测量而得到的氧浓度分布的图。参照图5可知,在比较例1的情况下氧浓度从表面迅速降低,并且在大致1.3nm的转化深度附近,降低到小于10原子%。另一方面,在实施例1和2的电解铜箔的情况下,在表面和ot之间的厚度范围内,氧浓度在表面表现出稍微升高然后降低的倾向,并且在降低区间的氧浓度的降低斜率也趋于平缓。如以上描述的实施例和比较例中所述,本发明中的优选ot范围优选为1.5nm至8.0nm。再次参照表1和表2观察在相同的溶存氧量条件(7.5ppm)下的实施例3和比较例3的特性数据可知,在比较例3的情况下,随着tic的含量小幅增加,断裂强度减小到小于25kg/mm2。另外,在比较例3的情况下,由于铜箔本身的强度不足,从而在使用混合有si的阳极材料时会产生断线,因此,当进行充电/放电评价时,充电效率急剧降低。同时,实施例4和比较例4是电解液(镀液)中的fe浓度不同的情况,如比较例4,当fe浓度为0.3g/l以上时,断裂强度大于57kg/mm2,在该情况下,铜箔的拉伸特性被明显降低,由此,当进行充电/放电评价时,铜箔不能承受其体积膨胀而导致电极断线,因此充电效率急剧降低。同时,实施例1至4示出了otd较低的值,而比较例1-4示出了otd不低于5.9的较高值。由此在比较例1-4都观察到了折叠现象。如上所述的较高的otd值可能导致在铜箔的两个表面涂覆阳极材料并进行干燥之后,由于铜箔和阳极材料之间的附着力之差而使制造的极板发生弯曲,并且可能是锂二次电池的卷对卷工艺中发生折叠的主要原因。以上,通过本发明的实施例描述了本发明,但是前述的实施例仅是通过举例描述本发明的技术思想,本发明所属
技术领域:
的普通技术人员应当理解,在不超出本发明的基本特征的范围内,可以进行各种修改和变形。因此,本发明中公开的实施例并非用于限制本发明的技术思想,而是用于描述,本发明的技术思想的范围并不限于这些实施例。本发明的保护范围应基于所附权利要求书来解释,并且与其在同等范围内的所有技术思想应当被解释为包括在本发明的权利范围内。当前第1页12