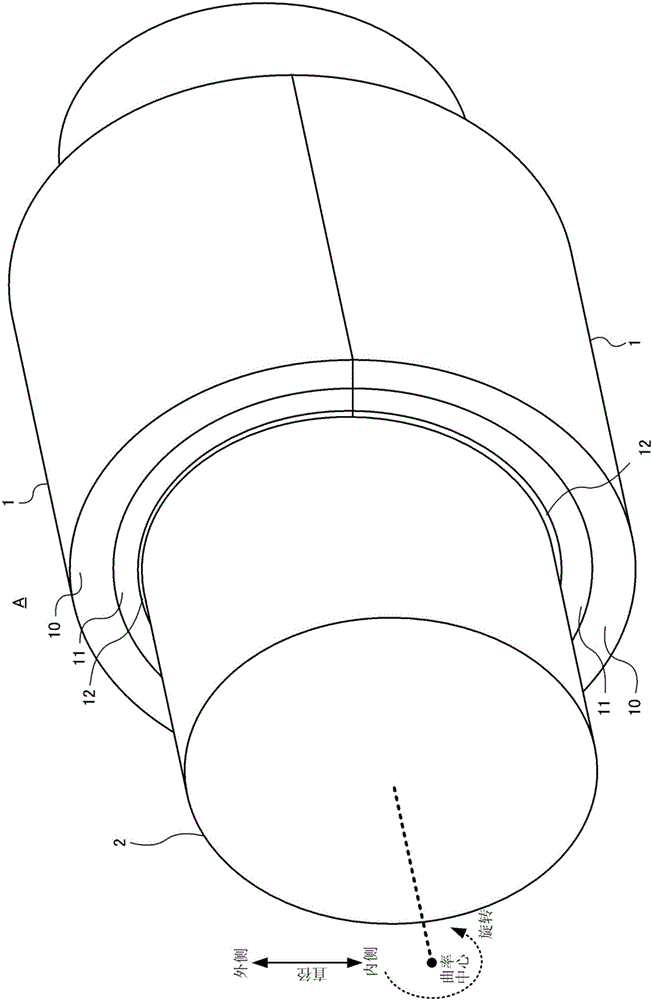
本发明涉及配合轴在滑动面上滑动的滑动构件和滑动轴承。
背景技术:
:已知如下技术:在Cu合金上形成Bi覆盖层,使配合构件在该覆盖层上滑动(参照专利文献1)。在专利文献1中,在Bi覆盖层的下层形成Ag中间层。由此,能提高由Bi产生的磨合性,并且能通过Ag防止疲劳断裂。现有技术文献专利文献专利文献1:日本特开2006-266445号公报技术实现要素:发明所要解决的问题然而,在专利文献1中,存在如下问题:覆盖层的Bi的结晶组织是柱状晶,在柱状晶的晶粒边界容易产生解理断裂。特别是,在Bi的结晶粒径小的情况下,存在如下问题:在疲劳时容易产生晶粒边界处的解理断裂。本发明是鉴于所述问题而完成的,其目的在于提供一种能防止疲劳时的滑动面的解理断裂的技术。用于解决问题的方案为了达成所述目的,在本发明的滑动构件和滑动轴承中,在基层上形成有覆盖材料的覆盖层,所述覆盖材料的覆盖层具有配合构件的滑动面。而且,覆盖层具有晶粒的粒径为大于等于3μm且小于等于7μm的覆盖材料的结晶组织。如此,通过将覆盖材料的晶粒的粒径设为大于等于3μm,能促进疲劳时的晶粒内的位错。即,通过促进晶粒内的位错的移动,能增大覆盖层的延展性,能防止疲劳时的解理断裂。另一方面,通过将覆盖材料的晶粒设为小于等于7μm,能防止由于强度下降,反而疲劳断裂得到促进。图1是表示结晶粒径与屈服应力的关系的图表(引用:T.G.Nieh,LawrenceLivermoreNationalLab)。如该图所示,结晶粒径在10~20nm左右屈服应力变得最大,并且在与该结晶粒径相比结晶粒径变大的区域中,根据Hall-Petch(霍尔-佩奇)关系,结晶粒径越大,屈服应力越减小。在屈服应力服从Hall-Petch关系的结晶粒径的区域中,虽然覆盖层提前屈服,但在粒径大的晶粒内容易使位错移动,能使覆盖层塑性变形。即,能利用比使晶界解理的应力小的应力使覆盖层塑性变形,能防止覆盖层的解理断裂。此外,覆盖材料可以是Bi、Sn、Pb、In或者Sb。Bi、Sn、Pb、In、Sb均硬度(例如莫氏硬度)较小,适合作为覆盖材料。此外,即使在具备本发明的特征的滑动轴承中,也可发挥以上所说明的本发明的效果。附图说明图1是表示结晶粒径与屈服应力的关系的图表。图2是本发明实施方式的滑动构件的立体图。图3的(3A)是疲劳试验的示意图,(3B)是疲劳损伤面积率的图表。具体实施方式在此,按照下述顺序对本发明的实施方式加以说明。(1)第一实施方式:(1-1)滑动构件的构成:(1-2)计量方法:(1-3)滑动构件的制造方法:(2)实验结果:(3)其他实施方式:(1)第一实施方式:(1-1)滑动构件的构成:图2是本发明的一实施方式的滑动构件1的立体图。滑动构件1包含:里衬金属10、衬里(lining)11和涂层(overlay)12。滑动构件1是将中空状的圆筒在径向上二等分的呈对开状的金属构件,剖面是半圆弧状。通过组合两个滑动构件1成为圆筒状,形成滑动轴承A。滑动轴承A在形成于内部的中空部分轴支承圆柱状的配合轴2(发动机的曲轴)。配合轴2的外径形成为略小于滑动轴承A的内径。向形成于配合轴2的外周面与滑动轴承A的内周面之间的间隙供给润滑油(发动机油)。此时,配合轴2的外周面在滑动轴承A的内周面上滑动。滑动构件1具有如下构造:按照远离曲率中心的顺序,依次层叠有里衬金属10、衬里11和涂层12。因此,里衬金属10构成滑动构件1的最外层,涂层12构成滑动构件1的最内层。里衬金属10、衬里11和涂层12分别在圆周方向上具有一定的厚度。里衬金属10的厚度是1.3mm,衬里11的厚度是0.2mm,涂层12的厚度是12μm。涂层12的曲率中心侧的表面的半径(滑动构件1的内径)是40mm。以下,所谓的“内侧”是指滑动构件1的曲率中心侧,所谓的“外侧”是指滑动构件1的曲率中心的相反侧。涂层12的内侧的表面构成配合轴2的滑动面。里衬金属10由钢形成,所述钢含有0.15wt%的C,含有0.06wt%的Mn,剩余部分由Fe构成。需要说明的是,里衬金属10由能介由衬里11和涂层12支承来自配合轴2的荷载的材料形成即可,也可以不由钢来形成。衬里11是层叠于里衬金属10的内侧的层,构成本发明的基层。衬里11含有10wt%的Sn,含有8wt%的Bi,剩余部分由Cu和不可避免的杂质形成。衬里11的不可避免的杂质是Mg、Ti、B、Pb、Cr等,是精炼或者废料中混入的杂质。不可避免的杂质的含量在整体中小于等于1.0wt%。涂层12是层叠于衬里11的内侧的表面上的层,构成本发明的覆盖层。涂层12由Bi和不可避免的杂质构成。不可避免的杂质的含量为小于等于1.0wt%。本实施方式中,涂层12具有由Bi的晶粒构成的结晶组织,构成涂层12的Bi的晶粒的平均粒径是4μm。对以上说明的滑动构件1进行疲劳试验的结果是,疲劳损伤面积率为10%,良好。通过将涂层12的晶粒的粒径设为4μm,能促进在疲劳时晶粒内的位错,能防止晶界处的解理断裂。即,通过促进晶粒内的位错的移动,能增大涂层12整体的延展性,能防止在疲劳时的解理断裂。此外,通过将覆盖材料的晶粒的粒径设为7μm,能防止由于强度下降反而疲劳断裂得到促进。(1-2)计量方法:通过以下方法计量在上述实施方式中示出的各数值。利用ICP发射光谱分析装置(岛津制作所制ICPS-8100)计量构成滑动构件1的各层的元素的质量。各层的厚度按以下顺序进行计量。首先,利用截面离子抛光仪(日本电子制IB-09010CP)研磨滑动构件1的径向的剖面。然后,利用电子显微镜(日本电子制JSM-6610A)以7000倍的倍率对滑动构件1的剖面进行拍摄,由此获得观察图像(反射电子像)的图像数据。然后,利用图像解析装置(NIRECO公司制LUZEXAP)对观察图像进行解析,由此计量膜厚。按照以下顺序计量涂层12中的Bi晶粒的平均粒径。首先,利用截面离子抛光仪研磨涂层12的任意剖面。利用电子显微镜(日本电子制JSM-6610A)以7000倍的倍率对涂层12的剖面中面积为0.02mm2的任意观察视野范围(长度0.1mm×宽度0.2mm的矩形范围)进行拍摄,由此获得观察图像(反射电子像)的图像数据。然后,在观察图像中进行切片法,由此计量Bi晶粒的粒径。该切片法中,用形成于观察图像上的线段所通过的晶粒的数量去除该线段的长度,由此计量该线段上的晶粒的粒径。进而,对多个线段的每一个线段进行计量,将所计量的晶粒的粒径的算术平均值(合计值/线段数)作为平均粒径。疲劳损伤面积率按照以下的顺序计量。首先,通过图3A示出的疲劳试验装置进行疲劳试验。如图3A所示,准备在长度方向的两端形成有圆柱状的贯通孔的连杆R,在一端的贯通孔轴支承试验轴H(淡的剖面线)。需要说明的是,在轴支承试验轴H的连杆R的贯通孔的内周面形成与滑动构件1同样的涂层12(深的剖面线)。在试验轴H的轴向上的连杆R的两外侧轴支承试验轴H,以3000转/分钟的转速使试验轴H旋转。将试验轴H相反侧的连杆R的端部连结于在连杆R的长度方向上往复移动(3000往复/分钟)的移动体F,将该移动体F的往复荷载设为50MPa。此外,向连杆R与试验轴H之间供给120℃的发动机油。通过持续以上的状态50小时,进行涂层12的疲劳试验。然后,在疲劳试验后,以从与该表面正交的直线上的位置、将该直线作为主光轴的方式拍摄涂层12的内侧的表面(滑动面),获得作为该拍摄的图像的评价图像。然后,利用双筒望远镜(放大镜)观察并确定评价图像上所呈现的涂层12的表面中的损伤的部分,将作为该损伤的部分的面积的损伤部面积除以在评价图像所呈现的涂层12的整个表面的面积,将所获得的值的百分率作为疲劳损伤面积率来进行计量。(1-3)滑动构件的制造方法:首先,准备具有与里衬金属10相同厚度的低碳钢的平面板。接着,在由低碳钢形成的平面板上喷洒构成衬里11的材料的粉末。具体而言,按照上述衬里11中的各成分的质量比混合Cu粉末、Bi粉末和Sn粉末并喷洒于低碳钢的平面板上。只要能满足衬里11中的各成分的质量比即可,也可以将Cu-Bi、Cu-Sn等合金粉末喷洒于低碳钢的平面板上。粉末的粒径通过试验用筛子(JISZ8801)调整为小于等于150μm。接着,对低碳钢的平面板、喷洒于该平面板上的粉末进行烧结。控制烧结温度为700~1000℃,在惰性气氛中烧结。烧结后进行冷却。当结束冷却时,在低碳钢的平面板上形成有Cu合金层。该Cu合金层包含冷却过程中析出的软质Bi粒子。接着,对形成有Cu合金层的低碳钢进行冲压加工,以便形成将中空状的圆筒在径向上二等分的形状。这时,以使低碳钢的外径与滑动构件1的外径一致的方式进行冲压加工。接着,对在里衬金属10上所形成的Cu合金层的表面进行切削加工。这时,以使在里衬金属10上所形成的Cu合金层的厚度与衬里11相同的方式控制切削量。由此,能通过切削加工后的Cu合金层形成衬里11。切削加工例如通过设有由烧结金刚石形成的切削工具件的车床来进行。接着,通过电镀,在衬里11的表面上层叠仅12μm厚的作为覆盖材料的Bi,由此形成涂层12。Bi的电镀顺序如下。首先,在电解液中向衬里11的表面通入电流,由此对衬里11的表面进行脱脂。接着,对衬里11的表面进行水洗。进而,通过对衬里11的表面进行酸洗,去除不需要的氧化物。之后,对衬里11的表面再次进行水洗。当完成以上的前处理时,通过向浸渍于电镀液的衬里11供给电流,进行Bi的电镀。涂层12中的Bi的电镀条件如下。电镀液的组成设为含有Bi浓度:40~60g/L,有机磺酸:25~100g/L,添加剂:0.5~50g/L。电镀液的温度调整在40~60℃之间。进而,向衬里11供给的电流采用占空比为50%的矩形脉冲电流,其平均电流密度设为4~8A/dm2。层叠了涂层12之后,进行水洗和干燥,完成滑动构件1。通过进一步地将两个滑动构件1组合成圆筒状,形成滑动轴承A。(2)实验结果:[表1]样品平均拉径[μm]疲劳损伤率[%]12.5382312341045145716表1表示按涂层12中的Bi的平均粒径对疲劳损伤面积率进行计量的结果。按照与上述的制造方法同样的方法,制造Bi的平均粒径不同的样品1~5(样品3是所述实施方式)。不过,通过调整涂层12的电镀中的电流密度,调整Bi的平均粒径。由于具有涂层12的电镀中的电流密度越大、Bi的平均粒径越大的性质,因此,目标平均粒径越大,将电流密度调整得越大。图3B是按Bi的平均粒径来表示疲劳损伤面积率的图表。如该图所示可知,通过在Bi的平均粒径为2~3μm的区域增大平均粒径,急剧地抑制疲劳损伤面积。此外,可知通过在Bi的平均粒径为大于等于4μm的区域增大平均粒径,疲劳损伤面积稍微增大。推定这是由于当Bi的平均粒径变大时,强度下降导致的。因此,可知为了获得作为滑动轴承A所需的耐疲劳性,理想的是将Bi的平均粒径设为大于等于3μm且小于等于7μm。(3)其他实施方式:在所述实施方式中,对构成轴支承发动机的曲轴的滑动轴承A的滑动构件1进行了例示,但通过本发明的滑动构件1也可以形成其他用途的滑动轴承A。例如,通过本发明的滑动构件1可以形成变速器用的齿轮衬套(gearbush)、活塞销衬套/毂(boss)衬套等。此外,衬里11的基质(matrix)不限于Cu合金,根据配合轴2的硬度来选择基质的材料即可。此外,覆盖材料只要是比衬里11软的材料即可,例如可以是Pb、Sn、In、Sb的任一种。即使在Pb、Sn、In、Sb中,也能通过增大晶粒的粒径来提高延展性。附图标记说明:1:滑动构件2:配合轴10:里衬金属11:衬里11b:Bi粒子12:涂层当前第1页1 2 3