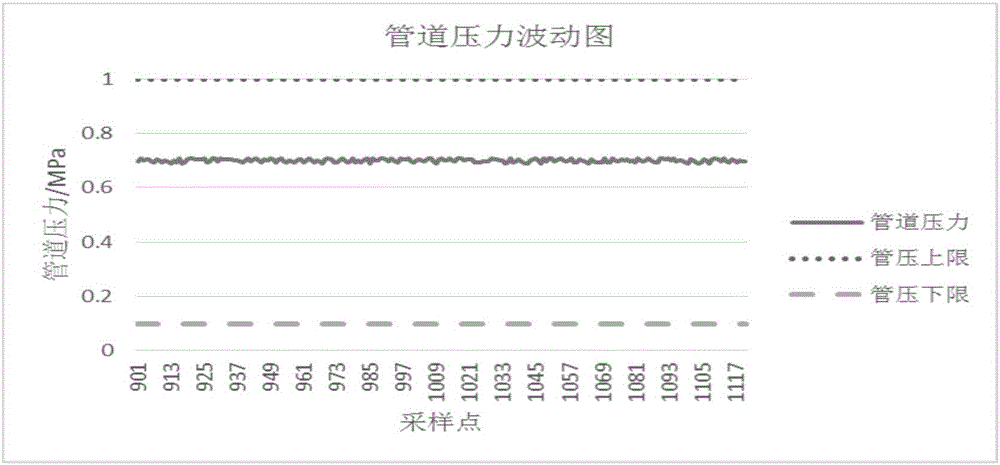
本发明属于仪表异常检测技术领域,具体涉及一种热量表耐久性冷热冲击试验异常点检测方法。
背景技术:在我国,实际使用热量表进行分户计量从开始试点至今已有十多年时间,热量表的安装使用数量已很庞大。从日常检测统计情况看,热量表产品质量存在的问题主要表现在长期可靠性方面。关于热量表的耐久性研究,仅限于理论方面和学习理解。具体试验主要是局限于300h试验,且积累的数据也不很充分。现有的耐久性试验装置也是一些简单的试验装置,不能完全满足基于欧洲标准EN1434-4:2007《热量表第四章:型式批准测试》和国家标准对热量表耐久性试验方法的要求。再者,耐久性试验过程时间长、流量周期变化跨度大、一个故障异常可能导致整个耐久性试验的失败,造成巨大的经济损失和人员安全隐患,而在这方面的研究,国内外鲜有探索。故过程故障异常点监控及报警处理尤为重要。因此,研究一种热量表耐久性冷热冲击试验过程监控故障异常点的在线检测方法,具有重要的现实必要性。
技术实现要素:本发明的目的就是为了克服上述现有技术存在的不足而提供一种热量表耐久性冷热冲击试验异常点检测方法,本发明的检测方法可靠性高、安全性好、操作方便并可对热量表耐久性冷热冲击试验过程监控故障异常点进行在线检测。为了实现上述目的,本发明所采用的技术方案由以下步骤组成:(1)以采样周期ts为间隔对热量表耐久性试验过程状态参数进行采集,热量表耐久性试验过程状态参数包括被检热量表的瞬时流量、累积流量、累积热量、标准流量计的瞬时流量、累积流量、前管路温度、管路压力、后管路温度、压力、前后管路温差、水箱温度以及液位;(2)根据步骤(1)所采集的热量表耐久性试验过程状态参数,建立试验过程状态参数数据集,记当前采样次数为k,k≥1;采样时间t=kts,单位:s;2.1)瞬时流量数据集qc={qce1(i),qce2(i)},单位:L/h;其中,qce1(i)为当前采集到的标准流量计的瞬时流量,qce2(i)为当前采集到的被检热量表的瞬时流量,1≤i≤k;2.2)累积流量数据集qL={qLe1(i),qLe2(i)},单位:m3;其中,1≤i≤k,qLe1(i)为当前采集到的标准流量计的累积流量,qLe2(i)为当前采集到的被检热量表的累积流量;2.3)温度数据集T={Tc11(i),Tc12(i),TΔ1c(i),Tc21(i),Tc22(i),TΔ2c(i),Tc31(i),Tc32(i)},单位:℃;其中,1≤i≤k,Tc11(i)为当前采集到的被检热量表进口温度,Tc12(i)为当前采集到的被检热量表的出口温度;TΔ1c(i)当前采集到的被检热量表的进出口温差,Tc21(i)为当前采集到的前管路温度,Tc22(i)为当前采集到的后管路温度;TΔ2c(i)当前采集到的前后管路温差,Tc31(i)为当前采集到的热水箱温度,Tc32(i)为当前采集到的冷水箱温度;2.4)累积热量数据集QL={QLe1(i-j),QLe2(i-j)}其中,1≤j≤i≤k,QLe1(i-j)为t(i)~t(j)时间段内根据采集到的标准流量计的累积流量及供回水端的温差所计算得到的标准累积热量,QLe2(i-j)为t(i)~t(j)时间段内采集到的被检热量表的累积热量;2.5)管路压力数据集P={Ph1(i),Ph2(i)},单位:MPa;其中,1≤i≤k,Ph1(i)为当前采集到的前管路压力,Ph2(i)为当前采集到的后管路压力;2.6)液位数据集L={L1(i),L2(i)},单位:m;其中,1≤i≤k,L1(i)为当前采集到的热水箱液位,L2(i)为当前采集到的冷水箱液位;2.7)软件流量某阶段设定值为qyushe,单位:L/h;水温的某阶段设定值Tyushe,单位:℃;管路中水温的设定最大值θmax,单位:℃;管路中水温的设定最小值θmin,单位:℃;系统运行时管路中压力的允许最大值Phigh,单位:MPa;系统运行时管路中压力的允许最小值Plow,单位:MPa;水箱中水位的最大允许值Lhigh,单位:m;水箱中水位的最小允许值Llow,单位:m;(3)对步骤(2)的各试验过程状态参数数据集进行状态参数特征提取,即:最大值max={qcmax,qLmax,QLmax,Tmax,Pmax,Lmax};最小值min={qcmin,qLmin,QLmin,Tmin,Pmin,Lmin};平均值中位值方差σ={σ(qc),σ(qL),σ(QL),σ(T),σ(P),σ(L)};(4)当选择4000次冷热冲击试验时,流量恒定,温度周期变化,先是θmax的高温水以qs流量对被检热量表进行热冲击试验2.5分钟,接着是θmin的低温水以qs流量对被检热量表进行冷冲击试验2.5分钟,如此循环进行4000个周期,每个周期持续5分钟,总耗时20000分钟;(5)建立4000次冷热冲击试验的状态特征参数模型管路压力P满足集合OGYmax∩OGYmin,其中:集合OGYmax:Pmax≤Phigh集合OGYmin:Pmin≥Plow水箱液位L满足集合OSWmax∩OSWmin,其中:集合OSWmax:Lmax≤Lhigh集合OSWmin:Lmin≥Llowqyushe=qs,瞬时流量qc满足集合OCLSmax∩OCLSmin∩OLELS1∩OLELS2,则供水系统处于稳定状态;集合OCLSmax:qcmax≤qyushe集合OCLSmin:qcmin≥qyushe(1-5%)集合OLELS1:σ(qce1)≤0.5%×qyushe集合OLELS2:被检热量表的累积流量qLe2满足集合OLJ,集合OLJ为:5.1)当Tyushe=θmax时,管路中水流温度T满足集合OGLGWG∩OGLGWD∩OGLGWC,则水温正常;集合OGLGWG:(Tc2max≤θmax)∪(Tc3max≤θmax)集合OGLGWD:(Tc2min≥θmax-5℃)∪(Tc3min≥θmaxx-5℃)集合OGLGWC:|Tc21(i)-Tc22(i)|≤5℃5.2)当Tyushe=θmin时,管路中水流温度T满足集合OGLDWG∩OGLDWD∩OGLDWC,认为水温正常集合OGLDWG:(Tc2max≤θmin)∪(Tc3max≤θmin)集合OGLDWD:(Tc2min≥θmin+5℃)∪(Tc3min≥θmin+5℃)集合OGLDWC:|Tc21(i)-Tc22(i)|≤5℃(6)根据步骤(3)所提取的各状态参数的特征值,结合步骤(5)建立的各个温度状态的特征参数模型进行异常判定,即:其中:f(μ,σ,max,min,Med,Desc,Asc)为异常点检测函数,1表示正常,0表示异常,E3为试验方法3,即4000次冷热冲击试验下的所有特征参数集合,X3为试验方法3下的当前特征参数集合;E3=(OGYmax∩OGYmin)∩(OSWmax∩OSWmin)∩(OCLPmax∩OCLPmin∩OLELP1∩OLELP2)∩(OLJ)∩((OGLGWG∩OGLGWD∩OGLGWC)∪(OGLDWG∩OGLDWD∩OGLDWC))若检测数据结果为异常,则获取其异常点的所有特征值,加入到异常数据集中,异常数据集记录了过程状态参数在不同工况状态下采用不同特征提取方法所检测出的异常点的集合,并对异常点进行验证。进一步,上述步骤(5)中根据异常值在连续的采样周期内是否连续出现,异常值可分为两种情况:(1)可恢复性异常点在连续的采样周期内偶尔出现的异常点为可恢复的异常点,当出现可恢复性异常点时,查看环境、M-Bus接线良好与否、管道是否有堵塞物;(2)不可恢复性异常点在连续的采样周期内连续出现的异常点为不可恢复异常点,当出现不可恢复性异常点时,查看热量表、传感器、调节阀、电动阀是否发生故障,管道是否泄漏等,根据实际情况报警。进一步,上述步骤(5)中异常点验证方法为:(1)对于可恢复性异常点,依据拉依达准则判定验证当前采集的状态参数是否为异常值,当满足3σ准则集合OJYZ时,XT为正常值;当不满足3σ准则集合OJYZ时,XT为异常值;集合OJYZ:XT为当前采集的状态参数;XT为该参数在采样时间段内的平均值,包括当前量;s(XT)为该参数采样时间段内的历史实验偏差,包括当前量;(2)对于不可恢复性异常点,在试验结束后进行相关检定或校准。本发明所涉及的热量表耐久性冷热冲击试验异常点检测方法,能够对热量表耐久性冷热冲击试验过程监控故障异常点进行实时在线检测,有效提高了对试验过程的全程监控能力,提升了对故障异常点的精细化检测水平,检测过程自动化控制,节约人力成本,操作方便、可靠性高、使用寿命长、安全性好、检测结果可靠性高,有力促进对装置及其热量表的故障诊断及预测,避免因故障异常点导致的巨大经济损失及人员安全隐患,对提升产品计量保障能力及检验检测能力具有重要的意义。附图说明图1为实施例1的异常点检测流程图。图2为管道压力曲线图。图3为水箱液位曲线图。图4为标准流量计最大流量点瞬时流量误差图。图5为4000次冷热冲击试验时间管道水温。具体实施方式下面结合附图和具体实施例对本发明的技术方案进一步详细说明。本实施例所述的热量表耐久性试验,通过设置热水测试循环和冷水测试循环,能够实现“4000次冷热冲击试验”,有效提高了热量表耐久性试验的检测效率和国产热量表生命周期的试验能力。结合图1,用本实施例的热量表耐久性试验装置对热量表进行4000次冷热冲击试验时,所选热量表为等级3级的DN25热量表,其过程故障异常点的检测由以下步骤实现:(1)以采样周期ts=5s为间隔对热量表耐久性试验过程状态参数,即被检热量表的瞬时流量、累积流量、累积热量、标准流量计的瞬时流量、累积流量、前管路温度、管路压力、后管路温度、压力、前后管路温差、水箱温度以及液位等。(2)根据步骤(1)所采集的热量表耐久性试验过程状态参数,建立试验过程状态参数数据集,记当前采样次数为k,k≥1;采样时间t=kts,则所建立的试验过程状态参数数据集包括:2.1)瞬时流量数据集qc={qce1(i),qce2(i)},单位:L/h;其中,qce1(i)为当前采集到的标准流量计的瞬时流量,qce2(i)为当前采集到的被检热量表的瞬时流量,1≤i≤k;2.2)累积流量数据集qL={qLe1(i),qLe2(i)},单位:m3;其中,1≤i≤k,qLe1(i)为当前采集到的标准流量计的累积流量,qLe2(i)为当前采集到的被检热量表的累积流量;2.3)温度数据集T={Tc11(i),Tc12(i),TΔ1c(i),Tc21(i),Tc22(i),TΔ2c(i),Tc31(i),Tc32(i)},单位:℃;其中,1≤i≤k,Tc11(i)为当前采集到的被检热量表进口温度,Tc12(i)为当前采集到的被检热量表的出口温度;TΔ1c(i)当前采集到的被检热量表的进出口温差,Tc21(i)为当前采集到的前管路温度,Tc22(i)为当前采集到的后管路温度;TΔ2c(i)当前采集到的前后管路温差,Tc31(i)为当前采集到的热水箱温度,Tc32(i)为当前采集到的冷水箱温度;2.4)累积热量数据集QL={QLe1(i-j),QLe2(i-j)}其中,1≤j≤i≤k,QLe1(i-j)为t(i)~t(j)时间段内根据采集到的标准流量计的累积流量及供回水端的温差所计算得到的标准累积热量,QLe2(i-j)为t(i)~t(j)时间段内采集到的被检热量表的累积热量;2.5)管路压力数据集P={Ph1(i),Ph2(i)},单位:MPa;其中,1≤i≤k,Ph1(i)为当前采集到的前管路压力,Ph2(i)为当前采集到的后管路压力;2.6)液位数据集L={L1(i),L2(i)},单位:m;其中,1≤i≤k,L1(i)为当前采集到的热水箱液位,L2(i)为当前采集到的冷水箱液位;2.7)软件流量某阶段设定值为qyushe,单位:L/h;水温的某阶段设定值Tyushe,单位:℃;管路中水温的设定最大值θmax,单位:℃;管路中水温的设定最小值θmin,单位:℃;系统运行时管路中压力的允许最大值Phigh,单位:MPa;系统运行时管路中压力的允许最小值Plow,单位:MPa;水箱中水位的最大允许值Lhigh,单位:m;水箱中水位的最小允许值Llow,单位:m。(3)对步骤(2)采集的各试验过程状态参数数据集,进行状态参数特征提取,即:最大值max={qcmax,qLmax,QLmax,Tmax,Pmax,Lmax};最小值min={qcmin,qLmin,QLmin,Tmin,Pmin,Lmin};平均值中位值方差σ={σ(qc),σ(qL),σ(QL),σ(T),σ(P),σ(L)};表1为各试验过程状态参数数据集特征简介名称介绍检测意义最大值Max数据中最大可达值检测数值过高异常最小值Min数据中最小可达值检测数值过低异常平均值Avg所有数据的平均值检测数据集中程度异常中位值Med一组数据中居于中间的一个值检测数据集中程度异常方差Stdev所有数据的方差值检测数据变化程度异常常等(4)依据欧洲耐久性标准和我国的热量表标准,4000次冷热冲击试验,即先是95℃的高温水以qs=7000L/h流量对被检热量表进行热冲击试验,紧接着是20℃的低温水以qs=7000L/h流量对被检热量表进行冷冲击试验,如此循环进行4000个周期,每个周期持续5分钟,总耗时20000分钟。工控机通过采集卡对状态参数进行周期性检测,并记录预处理采样数据,令数据集D={qc,qL,QL,T,P,L},当前采样次数为k,当前状态参数数据集为D(i),数据集D中每一个数组都由M个元素构成,其中i={k-M+1,k-M+2,...,k},D(i)|i<=0=0;每一组每隔5秒更新增加一个元素。(5)建立4000次冷热冲击试验的状态特征参数模型,具体如下:管路压力P满足集合OGYmax∩OGYmin,管路某段时间内的压力监控参见图2;其中:集合OGYmax:Pmax≤1.0MPa集合OGYmin:Pmin≥0.1MPa水箱液位L满足集合OSWmax∩OSWmin,水箱某段时间内的液位监控参见图3;其中:集合OSWmax:Lmax≤0.65m集合OSWmin:Lmin≥0.50mqyushe=qs=7000L/h,每隔5s检查被检测热量表和标准流量计的瞬时流量qc是否满足集合OCLSmax∩OCLSmin,则供水系统处于稳定状态;标准流量计某段时间的瞬时流量监控图参见图4。集合OCLSmax:qc1max≤7000(1+5%)L/h=7350L/h集合OCLSmin:qc1min≥7000(1-5%)L/h=6650L/h检查标准流量计是否满足集合OLELS1:集合OLELS1:σ(qce1)≤0.5%×7000L/h=35L/h检查被检测热量表是否满足集合OLELS2:集合OLELS2:被检热量表的累积流量qLe2满足集合OLJ,集合OLJ为:当Tyushe=θmax时,管路中水流温度Tc2和水箱中水温Tc3均满足集合OGLGWG∩OGLGWD∩OGLGWC,则水温正常;管路某段时间内的水温监控参见图5;管路前水温与管路后水温之差满足集合OGLGWC1;其中:集合OGLGWG:(Tc2max≤95℃)∪(Tc3max≤95℃)集合OGLGWD:(Tc2min≥90℃)∪(Tc3min≥90℃)集合OGLGWC:|Tc21(i)-Tc22(i)|≤5℃当Tyushe=θmin时,管路中水流温度T满足集合OGLDWG∩OGLDWD∩OGLDWC,认为水温正常;集合OGLDWD:(Tc2max≤25℃)∪(Tc3max≤25℃)集合OGLDWD:(Tc2min≥20℃)∪(Tc3min≥20℃)集合OGLDWC:|Tc21(i)-Tc22(i)|≤5℃(6)根据步骤(3)所提取的各状态参数的特征值,结合步骤(5)建立的各个温度状态的特征参数模型进行异常判定;其中:f(μ,σ,max,min,Med,Desc,Asc)为异常点检测函数,1表示正常,0表示异常,E3为试验方法3,即4000次冷热冲击试验下的所有特征参数集合,X3为试验方法3下的当前特征参数集合;E3=(OGYmax∩OGYmin)∩(OSWmax∩OSWmin)∩(OCLSmax∩OCLSmin∩OLELS1∩OLELS2)∩(OLJ)∩((OGLGWG∩OGLGWD∩OGLGWC)∪(OGLDWG∩OGLDWD∩OGLDWC))若检测数据结果为异常,则获取其异常点的所有特征值,并将异常点的所有特征值加入到异常数据集中,异常数据集记录了过程状态参数在不同工况状态下采用不同特征提取方法所检测出的异常点的集合,根据异常值在连续的采样周期内是否连续出现,异常值可分为两种情况:在连续的采样周期内偶尔出现的异常点为可恢复的异常点,当出现可恢复性异常点时,查看环境、M-Bus接线良好与否、管道是否有堵塞物;在连续的采样周期内连续出现的异常点为不可恢复异常点,当出现不可恢复性异常点时,查看热量表、传感器、调节阀、电动阀是否发生故障,管道是否泄漏等,根据实际情况报警。对异常点一一进行验证,异常验证的方法如下:(1)对于可恢复性异常点,依据拉依达准则判定验证当前采集的状态参数是否为异常值,当满足3σ准则集合OJYZ时,XT为正常值;当不满足3σ准则集合OJYZ时,XT为异常值;集合OJYZ:XT为当前采集的状态参数;为该参数在采样时间段内的平均值,包括当前量;s(XT)为该参数采样时间段内的历史实验偏差,包括当前量;(2)对于不可恢复性异常点,在试验结束后进行相关检定或校准。如热量表在试验过程出现连续的不可恢复性异常点,可立即终止试验后,送到检定部门进行检定验证。其他表则继续未完成的试验。如传感器在试验过程出现连续的不可恢复性异常点,可立即终止试验后,送到校准部门进行校准验证。被检测表在传感器检定后合格再重新安装后或跟换新的传感器继续试验。本实施例的试验结果分析如下:(1)试验样表说明试验样表为DN25热量表,等级3,厂家西安诺文电子科技股份有限公司、沈阳航发热计量技术有限公司、龙口博思达仪器仪表公司、西安旌旗电子股份有限公司、陕西米特智能科技有限公司、西安北斗星数码信息股份有限公司。共12块表,每个厂家各2块表,试验编号随机分配1~12。(2)结果说明(2.1)可恢复性异常点在4000次冷热冲击试验中,总共出现可恢复性异常点53处,且相隔间接大。原因可能是流量切换时水流状态的急速变化、环境的不确定影响等。把异常值代入集合OJYZ中验证,可发现,通过验证的39个,还有14个3σ准则未检测出。可见本检测方法相比3σ准则更为精准可靠。(2.2)不可恢复性异常点3#、7#表在3500次的时候不再计量,且开始漏水。5#、6#、12#表流量误差明显正方向偏离,且在3300次后负方向变大,变差超差。本发明可以对故障异常点的精细化检测,能够对热量表耐久性冷热冲击试验过程监控故障异常点进行实时在线检测。