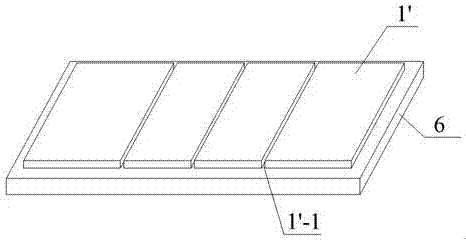
本发明公开了一种硅基薄膜太阳能电池良品率提升,更趋于技术创新的细化、细微的改进,属于太阳能电池制造技术领域。
背景技术:商业化生产的薄膜太阳能电池基本分为硅基薄膜、碲化镉、铜铟镓硒三类。其中硅基薄膜太阳能电池最廉价相对性价比最合理。从应用角度硅基薄膜太阳能电池又分为弱光和强光两大类。照度万级LUX以上为强光型硅基薄膜太阳能电池,适合户外环境下使用。照度几千LUX以下为弱光型硅基薄膜太阳能电池,产品适合应用在光线较弱的环境。非晶硅太阳能电池伴随着液晶显示技术的发展广泛应用于消费类电子产品做电池芯片、传感器等。强光型硅基薄膜太阳能电池和碲化镉、铜铟镓硒薄膜太阳能电池一样能,用于光伏(PV)电站和光伏建筑一体化(BIPV)。中国发明专利ZL95104992.5是一种在弱光环境下使用的非晶硅太阳能电池,该发明解决了非晶硅薄膜太阳能电池制造中诸多技术难题和工艺问题,但仍存在一个提高良品率和外观质量等问题。目前,主导薄膜太阳能电池(以下简称电池板,电池或电池芯片)市场的硅基薄膜太阳能电池其性价比合理,市场潜力大,但仍面临着产品的良品率的再提升和外观质量问题,需要突破技术瓶颈、创新才能达到目的。如硅基薄膜太阳能电池仍存在一个漏电问题,有时出现电压跳变等现象,使电压不够稳定。究其原因和加工过程有关,前电极图形内的导电膜会产生毛刺和碎屑,致使相邻电池节之间导电膜的绝缘隔离间距减小。另外,膜脱落和电极附着力差与薄膜太阳能电池衬底(或称基片)附着力性能有关。如弱光型非晶太阳能电池,漏电流大,在无光照射情况下,正向施加1.7V直流电压,漏电流远大于0.3微安。具统计,批量生产时,通常大约有5%的电池芯片的铜浆电极附着力达不到0.6公斤,膜会脱落,严重的会导致非晶硅太阳能电池完全失效。产品外观质量,主要集中在表面出现“麻点”。ITO透明导电膜上存在脏污漏电还与ITO导电膜的隔离线暴露在外沾染脏污或空气中潮湿污物,也都会导致漏电。另外,碳浆背电极与保护背漆层没有完全重合,导致碳浆背电极边沿暴露在外也会产生漏电。只有附着力达到0.6公斤及以上,铜浆电极才不易脱落。
技术实现要素:本发明通过以上对现有技术存在的主要问题的分析和研究,并通过工业试验,对亟待要解决的产品质量难题,提供了技术解决方案。本发明的目的是:进一步细化完善硅基薄膜太阳能电池前电极电图形,克服由膜层脱落而导致电压不稳定;减小漏电流;消除产品外观表面出现的“麻点”提高产品良品率。本发明的另一个目的是:解决弱光条件下非晶硅太阳能电池漏电流大的技术难题,改变硅基薄膜太阳能电池P层内部杂质缺陷密度,显著减小漏电流,改善电池性能。本发明的又一个目的是:改善非晶硅太阳能电池的背电极结构,增强电池池背电极包括由背电极引出的铜浆电极附着力,降低生产成本。为实现本发明提出的任务和目的,提供技术解决支持方案:一种硅基薄膜太阳能电池,包括基片,前电极,PIN光电转化层和背电极,其技术特征在于所说的前电极是透明导电膜前电极图形阵列,至少包括ITO、ZnO,、石墨烯透明导电膜中的一种,所说前电极图形阵列包覆在透明基片上,包括基片的边沿;所说的PIN光电转化层是硅基非晶硅层,前电极图形阵列还包括防漏电的隔离线或前电极边缘的绝缘线,贯通PIN非晶硅层的各种通孔;所说的PIN非晶硅N层的背电极是复合金属背电极或碳浆电极中的一种;所说的碳浆电极是有背漆保护层的PIN非晶硅N层背电极,其上引出铜浆电极覆盖在背漆保护层开口处的背漆保护面和碳浆电极面上,以增强铜浆电极的附着力防止膜层脱落。本发明的方案还包括硅基薄膜太阳能电池制备方法,其技术特征是用ITO、ZnO,、石墨烯透明导电膜其中的一种透明导电膜在基片上制备制备前电极图形阵列,透明导电膜,包括,所说透明包覆在透明基片上,包括基片的边沿;包括在导电玻璃基片或导电聚酰亚基片导电膜上形成前电极图形,其技术特征在于制备前电极图形方法包括激光刻划和丝网印刷;选择丝网印刷前电极图形,在相邻连接的图形之间均设有一定宽度的隔离线以防漏电;单元电池周边有增强附着力的ITO导电膜以防膜层脱落;采用清洗法消除前电极导电图形表面“麻点”可,包括水清洗,超声波清洗;PIN的N层背电极层选碳浆电极,用铜浆电极作背电极引出,背漆保护层包覆碳浆电极层。实施本发明积极效果是通过技术创新,突破了传统设计思路,极大地提高升了非晶硅太阳能电池良品率和外观质量,消除了前电极麻点,漏电流明显著减少,电压稳定,生产成本降低。常规弱光型非晶硅太阳能电池工艺的ITO透明导电膜前电极的四周边沿被除掉,导致在无ITO膜的四周边沿的非晶硅膜容易脱落,进一步引发ITO透明导电膜前电极隔离线上的非晶硅脱落,本发明改变ITO透明导电膜前电极的结构,保留非晶硅太阳能电池四周边沿的ITO膜,不被去除,就能解决非晶硅膜层不脱落的问题。弱光型非晶硅太阳能电池P层非晶硅往往是采用重掺杂制备的,通常硼与硅的掺杂比在1%甚至更高,这样将导致p层内部杂质缺陷密度很大,产生大量的载流子复合中心,显著增加电池内部的漏电流。本发明采用合适的硅烷和三甲基硼烷的流量配比,在保证电池开路电压不变的情况下,使硼的掺杂比小于1%,大大减少了p层内部杂质缺陷密度,显著减小了漏电流。通常弱光型非晶硅太阳能电池的背电极是采用碳浆导电层,铜浆电极作引出电极,为了对碳浆背电极进行保护,在其上要制作一层背漆保护层,然后再在背漆保护层预留的开口上制作一层铜浆电极层。通常一般设计人员的思路是尽量增大铜浆电极与碳浆背电极层的接触面积,以便尽可能地减小接触电阻,而铜浆是比较昂贵的材料,其面积不可做得很大,因此设计的铜浆电极尽量与碳浆背电极接触面积大,而与背漆保护层的接触面积尽量小,以节省成本。但这样设计有约5%的电池片的铜浆电极附着力达不到0.6公斤,导致铜浆电极容易脱落。通过试验我们发现铜浆电极在背漆保护层上的附着力比铜浆电极在碳浆背电极上的附着力大,另一方面经过仔细分析我们认为,非晶硅薄膜是一种半绝缘材料,其电子迁移率低,通常不超过0.5cm2/v.s,因此非晶硅太阳能电池的内阻大,其串联电阻(包括体电阻,碳浆背电极横向电阻和透明导电膜前电极的横向电阻)也大,且远大于铜浆电极和碳浆背电极的接触电阻,因此即使减小铜浆电极和碳浆背电极的接触面积也不会对非晶硅太阳能电池的电性能产生影响,基于此分析,在保持铜浆电极面积不变的情况下,缩小保护背漆层上的开口面积,减小铜浆电极和碳浆背电极的接触面积,相应增大了铜浆电极和保护背漆层的接触面积,因铜浆电极与背漆保护层结合力良好,使铜浆电极的附着力显著增加,可使全部电池片的铜浆电极附着力达到0.6公斤以上,铜浆电极牢固不易脱落。以上所说电压不稳定的原因有三个方面,一是由于电池片边均有ITO膜,在由大板电池板切割成电池片时,相邻节的ITO膜易产生毛刺或碎屑使相邻节ITO膜的隔离线间距减小,造成漏电的可能性大大增加;二是边沿的ITO膜的隔离线暴露在外,在电池片运输过程中,隔离线上沾染的脏污或空气中潮湿污物导致漏电;三是碳浆背电极与保护背漆层没有完全重合,导致碳浆背电极边沿暴露在外,也会因隔离线上沾染的脏污或空气中潮湿污物导致漏电。通常弱光型非晶硅太阳能电池的工作电流为几十微安,因此如果漏电流达到了1微安,就会对其电压产生比较大影响,而相邻两节间的电压为0.8V,根据欧姆定律R=U/I,R=0.8/(1x10-6)=0.8x106Ω,也就是说,如果相邻两节间的绝缘电阻小到0.8x106Ω即0.8MΩ,就会对电池电压产生比较大的影响,通常在实际生产中切割电池片时产生的ITO膜毛刺或碎屑的长度小于0.3mm,假如ITO毛刺长度达到0.28mm其宽度为0.001mm,正好将相邻两节ITO膜相连起来,而实际使用的ITO膜的厚度约为77nm,ITO膜的电阻率为3.85x10-4Ω·cm,根据电阻公式R=ρL/S可计算出毛刺的电阻为:R=3.85x10-4x0.28x10-1/(0.001x10-1x77x10-7)=1.4x104Ω,此电阻远小于上述0.8x106Ω,该毛刺引起的漏电流远大于1微安,将严重影响电压,因此ITO透明导电膜的隔离线宽度定在0.3mm以上,同时考虑到隔离线太宽会减小电池的有效面积,本发明的隔离线宽度为0.3~0.6mm;另一方面将保护背漆层设计成比碳浆背电极面积更大,使之完全覆盖碳浆背电极。通过以上措施消除了电池电压不稳定现象。本发明以弱光型硅基薄膜太阳能电池为例详细的技术内容如下:采用14英寸x16英寸的ITO透明导电玻璃,可在其上排布制作许多弱光型非晶硅太阳能电池片。首先制作ITO透明导电膜前电极图形。在ITO透明导电玻璃上丝网印刷一层耐酸油墨作为掩膜层,通过湿法化学腐蚀法形成所需ITO前电极图形,相邻节透明导电膜前电极之间的隔离线宽在0.4mm~0.6mm范围。去除耐酸油墨后,进行清洗,为消除麻点,采用独特的清洗溶液配方和工艺,先进行除油,采用氢氧化钠和磷酸钠的混合溶液,重量配比为水:氢氧化钠:磷酸钠=(135~155):(1~3):(3~5),将去除耐酸油墨的ITO玻璃放入配好的溶液中,浸泡2~10分钟,溶液温度控制在45~50摄氏度;之后进行超声清洗,超声清洗液采用独特配方,重量配比为水:特选清洗粉=(1200~1400):(6~8),将去油后的ITO玻璃放入配好的溶液中,超声清洗40~80分钟,溶液温度控制在45~60摄氏度;ITO玻璃再经自动清洗机进行后清洗,清洗完后放入沉积夹具和真空室沉积P,I,N层非晶硅。为了减小弱光型非晶硅太阳能电池的漏电流,P层非晶硅采用了特殊的沉积工艺参数和原料气体流量配比,流量配比为:三甲基硼烷:甲烷:硅烷:氢气=(5~7):(30~40):(60~65):(15~17),其中三甲基硼烷的浓度为3%,即三甲基硼烷:(三甲基硼烷+硅烷)=3%,沉积温度225摄氏度,沉积压力60Pa,放电功率85W;之后采用激光刻划非晶硅膜,接着依次丝网印刷碳浆制作碳浆背电极,丝网印刷背漆制作背漆保护层,为了消除电压不稳定现象,将背漆保护层做得比碳浆背电极大,以完全覆盖碳浆背电极,考虑到丝网印刷有一定的偏移公差,背漆保护层比碳浆背电极四周大0.5~2mm。接着丝网印刷铜浆制作铜浆电极,为了增加铜浆电极的附着力,采用增大铜浆电极与背漆保护层的接触面积,相应减小铜浆电极与碳浆背电极的接触面积。铜浆电极长x宽范围为(1.3~1.6)x(2.6~3.5)mm,铜浆电极的边长比背漆开口的边长大1mm以上,铜浆电极的宽比背漆开口的宽大0.6mm以上。附图说明本发明的工作原理结合附图作进一步说明:图1、是本发明硅基非晶硅太阳能电池结构的剖面示意图。其中用ITO透明导电膜作前电极1,PIN硅基非晶硅层2,碳浆电极3,背漆保护层4,铜浆电极5,5-1作为负电极引出,5-2作为正电极引出,基片6是玻璃,2-2选则在一节不再光电转换的PIN非晶硅层,其中将ITO透明导电膜前电极1引到PIN非晶硅层2的N层为正电极3-2。图2、是现有技术ITO透明导电膜的前电极剖面示意图。其中玻璃基片6,ITO透明导电膜前电极1’,ITO透明导电膜前电极的隔离线1’-1。从图中可以看到玻璃基片四周没有ITO透明导电膜,这种设计后续会出现玻璃基片周边沿区域非晶硅严重脱膜,进而引起ITO透明导电膜前电极隔离线上的非晶硅膜脱落,导致太阳能电池失效。附图3、是本发明图1中ITO透明导电膜前电极图形1示意图。其中6为玻璃基片,ITO透明导电膜前电极1,ITO透明导电膜前电极1的隔离线1-1,从图中可以看到玻璃基片6四周边沿的ITO透明导电膜被保留,可有效防止后续非晶硅膜的脱落。可以看到本发明ITO透明导电膜前电极1的隔离线1-1宽度(0.4~0.6mm)比现有技术的隔离线(0.3mm以下)1’-1宽,以减小因切割产生图2导电膜碎屑和毛刺或污物导致漏电的可能性。图4、是本发明图1中背电极的碳浆电极3的剖面示意图。其中6为玻璃基片,ITO透明导电膜前电极1,ITO透明导电膜前电极1的隔离线1-1,从图中可以看到玻璃基片6四周边沿的ITO透明导电膜被保留,可有效防止后续非晶硅膜的脱落。可以看到本发明ITO透明导电膜前电极1的隔离线1-1宽度(0.4~0.6mm)比现有技术的隔离线(0.3mm以下)1’-1宽,以减小因切割产生图2导电膜碎屑和毛刺或污物导致漏电的可能性。图5、是本发明图1中背漆保护层4、碳桨电极3剖面示意图。其中玻璃基片6,背漆保护层4,4-1,4-2皆为背漆开口。通过背漆开口4-1铜浆电极引出负电极,通过背漆开口4-2铜浆电极引出正电极。图6、是常规弱光型非晶硅太阳能电池的背漆保护层和碳浆背电极叠合在一起的图示。其中6是玻璃基片,3’是碳浆背电极,4是背漆保护层,5是铜浆电极。由于丝网印刷存在偏移公差,使得是生产时背漆保护层4不能完全覆盖住碳浆背电极3’,未被覆盖住的碳浆背电极3’边沿处的隔离线易被脏污沾染导致漏电,是使电压不稳定的原因之一。图7、是图1中的铜浆电极5的背漆保护层4和碳浆电极3的剖面示意图。图A放大圆圈内表示铜浆电极5分别在背漆保护层4和碳浆电极3引出的正电极3-2,玻璃基片6,碳浆背电极3,背漆保护层4,铜浆电极5,碳浆电极3比背漆保护层4面积小,因此即使丝网印刷有偏移公差,背漆保护层4也能在四周边沿完全覆盖包住碳浆背电极3,可减小产生电压不稳定的几率,铜浆电极5覆盖在背漆开口4-1、4-2上(见图5),铜浆电极5与背漆保护层4相接触区域的面积比常规非晶硅太阳能电池的铜浆电极与背漆保护层相接触区域面积大,使得所有单元电池的铜浆电极附着力都到0.6公斤以上,铜浆电极非常牢固不易脱落,显示背漆保护层保住碳浆背电极边沿位置。图8、是本发明实施例6圆形透明导电膜前电极的剖面示意图。其中玻璃基片6D,ZnO透明导电膜前电极1D,相邻节ZnO透明导电膜前电极间的隔离线1D-1,ZnO透明导电膜前电极边沿的绝缘线1D-2,用于切割ZnO透明导电膜前电极1D和背电极时防止搭接在一起导致短路。图9、是本发明实施例6激光刻除PIN膜的剖面示意图。其中PIN非晶硅基薄膜2D,PIN非晶硅基薄的激光打孔形成的刻划线2D-1,作为相邻单节电池间正负电极串联通道,玻璃基片6D,ZnO透明导电膜前电极1D,相邻节ZnO透明导电膜前电极间的隔离线1D-1。图10、是本发明实施例6前电极和金属背电极剖面示意图。ZnO透明导电膜前电极1D、相邻节ZnO透明导电膜前电极间的隔离线1D-1,激光刻划复合背电极3D是银膜和镍铜合金的复合膜,激光贯穿刻划非晶硅基薄膜和复合背电极形成的激光刻划线3D-1,单节电池间的隔离线2D,非晶硅基薄膜,玻璃基片6D。图11、是本发明实施例6的透明视窗的剖面示意图。圆形非晶硅太阳能单元电池制作完背漆保护层并去除中央圆形区域的非晶硅基薄膜和背电极形成透明视窗后的剖面示意图,其中背漆保护层4D,背漆开口4D-1,焊接正负极引线之用,是PIN非晶硅基薄膜2D,玻璃基片6D,ZnO透明导电膜前电极1D,相邻节ZnO透明导电膜前电极间的隔离线1D-1,透明视窗2D-2。图12、是本发明实施例7第一次冲孔形成的导流孔的示意图。柔性非晶硅和非晶硅锗叠层太阳能电池第一次冲孔后的示意图。其中聚酰亚胺柔性基片6R,第一次冲孔形成的导流孔,用于将背电极引到聚酰亚胺柔性基片背面。图13、是本发明实施例7的第一次冲孔示意图。柔性非晶硅和非晶硅锗叠层太阳能电池第一次冲孔后在聚酰亚胺柔性基片正面镀连续溅镀金属铝膜,银膜和ITO透明导电膜和在聚酰亚胺柔性基片背面溅镀金属铝膜后的剖面图,其中金属铝膜3R-1,金属银膜3R-2,ITO透明导电膜3R-3,导流孔被上述各层膜填充后导流孔3R-4,聚酰亚胺柔性基片6R,第一次冲孔形成的导流孔6R-1是,聚酰亚胺柔性基片背面的金属铝膜7R。图14、是本发明实施例7的第二次冲孔剖面图示意图。是柔性非晶硅和非晶硅锗叠层太阳能电池第二次冲孔后形成汇流孔3R-5,用于汇集电流藉此将相邻单节电池正负极相串联。图15、是本发明实施例7的柔性非晶硅和非晶硅锗叠的面示意图。柔性非晶硅和非晶硅锗叠层沉积成硅基薄膜后的N型非晶硅膜2R-N1,本征非晶硅锗膜2R-I1,P型非晶硅膜2R-P1,N型氧化硅(SiOx)2R-N2,是本征非晶硅锗膜2R-I2,P型非晶硅膜2R-P2,经硅基薄膜填充后的导流孔2R-1,经硅基薄膜填充后的汇流孔2R-2。图16、是本发明实施例7的激光刻划后的剖面示意图。柔性非晶硅和非晶硅锗叠层太阳能电池沉积完ITO透明导电膜并经激光刻划后,其中ITO透明导电膜1R,作为前电极,经ITO透明导电膜填充的汇流孔1R-1,是激光贯穿刻划复合背电极,硅基薄膜和ITO透明导电膜形成的隔离线3R-6,聚酰亚胺柔性基片背面的金属铝膜用激光刻划隔离线7R-1。图17、是本发明实施例7的层压封装完后的剖面示意图。柔性非晶硅和非晶硅锗叠层太阳能电池层压封装完后,其中PET(聚对苯二甲酸乙二醇酯)4R,正负极引出涂锡带5R,ETFE(乙烯-四氟乙烯共聚物)8R是,EVA(乙烯-醋酸乙烯共聚物)9R是。具体实施方式例1、本发明实施例图3,图5、图7具体制作方法如下:制备前电极图形在356x406平方毫米的ITO透明导电玻璃上按照弱光型非晶硅太阳能电池需要设计前电极图形(单元电池由四个单节电池串联组成,整个ITO透明导电玻璃上以单元电池长宽尺寸为周期阵列排布)采用丝网印刷方法印刷一层耐酸油墨,并固化作为腐蚀掩膜层,接着将固化耐酸油墨的ITO透明导电玻璃,放入三氯化铁,盐酸和水的混合溶液中进行腐蚀,将裸露的ITO透明导电膜腐蚀掉,形成ITO透明导电膜前电极1,相邻节ITO透明导电膜前电极间的隔离线1-1的宽度为0.5mm;水清洗将腐蚀完的透明导电玻璃放入氢氧化钠溶液中去除耐酸油墨,并用自来水进行冲洗干净,接着将ITO透明导电玻璃放入氢氧化钠和磷酸钠的混合溶液中进行除油,混合溶液的重量配比为水:氢氧化钠:磷酸钠=144:2.6:3.5,将除去耐酸油墨的ITO玻璃放入配好的溶液中,浸泡10分钟,溶液温度控制在45~50摄氏度;超声清洗将除油后的ITO透明导电玻璃放入独特配方的清洗液中进行超声清洗,清洗液重量配比为水:清洗物质=1450:6.5,将去油后的ITO玻璃放入配好的溶液中,超声清洗80分钟,溶液温度控制在45~60摄氏度,之后用自动清洗机和纯水进行后清洗,并经风刀吹干待用;PIN非晶硅膜沉积将清洗好的ITO透明导电玻璃,装入沉积夹具中并放入真空室中采用等离子体化学气相沉积法进行PIN非晶硅膜沉积,其中P层非晶硅采用特殊沉积工艺参数和原料气体流量配比,流量配比为:三甲基硼烷:甲烷:硅烷:氢气=7:30:60:15,沉积温度200~250摄氏度,沉积压力50~70Pa,放电功率80~90W,沉积时间85~95秒;激光刻划隔离线绿激光刻划非晶硅膜,形成连接相邻两节单节电池的激光打孔刻划线,每束激光功率为0.4~0.6瓦,激光刻划线宽0.1~0.2mm,在刻划的同时进行强力吸尘,防止因刻划形成的非晶硅碎屑散落到激光打孔刻划的隔离线内影响电池性能;背电极形成依次丝网印刷碳浆并烘干固化成碳浆背电极3,固化温度控制在145~155摄氏度,固化时间为55~65分钟;丝网印刷背漆并烘干固化形成背漆保护层4,固化温度控制在135~145摄氏度,固化时间为40分钟,以消除漏电和电压不稳定隐患,背漆保护层4比碳浆背电极3四周大1mm目的使背漆保护层4能可靠地覆盖碳浆背电极3;背电极引出在背漆开口4-1处丝网印刷铜浆,并烘干固化形成铜浆电极5,分两步进行固化,首先在75~85摄氏度下恒温75~85分钟,然后再升高温度至145~155摄氏度,恒温35~45分钟。其中背漆开口4-1长宽为1.8x0.7mm,铜浆电极5长宽为2.9x1.4mm,可使所有单元电池的铜浆电极5附着力达到0.6公斤。最后进行切割,按检验标准测试,合格后包装入库。实施例2制作步骤与实施例1相同。仅改变水清洗环节中的工艺参数:将腐蚀完的透明导电玻璃放入氢氧化钠溶液中去除耐酸油墨,并用自来水进行冲洗干净,接着将去除耐酸油墨的ITO透明导电玻璃放入氢氧化钠和磷酸钠的混合溶液中进行除油,混合溶液的重量配比为水:氢氧化钠:磷酸钠=150:2.0:5.0,将去除耐酸油墨的ITO玻璃放入配好的溶液中,浸泡10分钟,溶液温度控制在45~50摄氏度;实施例3制作环节与实施例1相同。仅改变超声清洗环节的工艺参数:将除油后的ITO透明导电玻璃放入独特配方的清洗液中进行超声清洗,清洗液重量配比为水:清洗物质=1200:8.0,将去油后的ITO玻璃放入配好的溶液中,超声清洗80分钟,溶液温度控制在45~60摄氏度,之后用自动清洗机和纯水进行后清洗,并经风刀吹干待用;实施例4制作步骤与实施例1相同。仅改变PIN非晶硅膜沉积骤中的工艺参数:将后清洗好的ITO透明导电玻璃,装入沉积夹具中并放入真空室中进行P,I,N非晶硅膜沉积,其中P层非晶硅采用特殊的沉积工艺参数和原料气体流量配比,流量配比为:三甲基硼烷:甲烷:硅烷:氢气=5:40:65:17,沉积温度200~250摄氏度,沉积压力50~70Pa,放电功率80~90W,沉积时间85~95秒;实施例5制作步骤与实施例1相同,仅改变背电极形成中的工艺参数:依次丝网印刷碳浆并烘干固化成碳浆背电极3,固化温度控制在145~155摄氏度,固化时间为55~65分钟,丝网印刷背漆并烘干固化形成背漆保护层4,固化温度控制在135~145摄氏度,固化时间为50分钟,为消除漏电隐患,背漆保护层4比碳浆背电极3四周大0.6mm,使背漆保护层4能可靠地覆盖碳浆背电极3,如图5所示;背电极引出如图7所示。在背漆开口4-1处丝网印刷铜浆,并烘干固化形成铜浆电极5,分两步进行固化,首先在75~85摄氏度下恒温75~85分钟,然后再升高温度至145~155摄氏度,恒温35~45分钟。其中背漆开口4-1长宽为2.0x0.9mm,铜浆电极长5宽为3.0x1.8mm,可使所有单元电池的铜浆电极5附着力达到0.6公斤以上。最后进行切割,按检验标准测试,合格后包装入库。实施例6见附图8~11:此实施例例为圆形非晶硅太阳能电池,主要用于太阳能手表,制作如下:制备前电极图形在356x406平方毫米的ZnO透明导电玻璃上按照非晶硅太阳能电池需要的图形(单元电池为圆形,由四个单节电池串联组成,每个单节电池为圆弧形状,中间为圆形的透明视窗,整个ZnO透明导电玻璃上以单元电池尺寸为周期阵列排布单元电池)采用耐酸油墨作为掩膜,湿法化学腐蚀ZnO透明导电膜,形成ZnO透明导电膜前电极1D,四周的ZnO透明导电膜是保留的,相邻节ZnO透明导电膜前电极间的隔离线1D-1的宽度为0.6mm;其中绝缘线1D-2,宽度0.3mm,是防止在切割时ZnO透明导电膜前电极和背电极搭接在一起导致短路。除耐酸油墨接着去除耐酸油墨,除油及超声清洗后,再用自动清洗机和纯水进行清洗,并经风刀吹干待用;PIN非晶硅基薄膜沉积将清洗好的ZnO透明导电玻璃,装入沉积夹具中并放入真空室中采用等离子体化学气相沉积法进行PIN非晶硅基薄膜沉积,其中N为N型氧化硅(SiOx),以增加对短波段光的反射,提高叠层电池的短路电流。N型氧化硅(SiOx)的沉积气体流量比为:CO2:SiH4=0.5,射频电源放电功率90W,沉积温度220摄氏度;激光刻划采用绿激光刻划非晶硅基薄膜,形成连接相邻两节单节电池的激光打孔刻划线2D-1,每束激光功率为0.5瓦,激光刻划线宽0.2mm,在刻划的同时进行强力吸尘,防止因刻划形成的非晶硅基薄膜碎屑散落到激光打孔刻划线影响电池性能;制备复合背电极采用平面磁控溅射法依次溅镀ZnO膜,银膜和镍铜合金膜,厚度分别为100nm,80nm和120nm,形成复合背电极3D,以增加对光的反射,提高电池转换效率。激光贯穿刻划隔离线3D-1采用绿激光贯穿刻划非晶硅基薄膜2D和复合背电极3D,形成节与节之间的隔离线3D-1,每束激光功率为1.0瓦并调整好激光频率,激光刻划线宽0.5mm,在刻划的同时进行强力吸尘,防止因刻划形成的非晶硅基薄膜碎屑散落到隔离线影响电池性能;形成透明视窗采用激光刻划方法将设计需要透明的区域上的非晶硅基薄膜及复合背电极去除,形成透明视窗,每束激光功率7W,红外激光波长为1064nm。丝网印刷背漆并烘干固化形成背漆保护层4D,固化温度控制在135~145摄氏度,固化时间为40分钟,背漆开口4D-1为焊接正负极引线之用;最后进行切割,按检验标准测试,合格后包装入库。实施例7此例为柔性非晶硅和非晶硅锗叠层太阳能电池,见附图12至17图:柔性基片第一次冲孔在356x406平方毫米的聚酰亚胺柔性基片6R上按照非晶硅太阳能电池需要的图形(此例中,沿宽度566mm方向等分分成40节,整个单元电池有40个单节电池内部组成。每个单元电池为矩形形状。)沿宽度方向的两侧边沿距边沿10mm出进行第一次冲孔,作为导流孔6R-1,孔径2.5mm,相邻孔间距9mm,并用纯水冲洗干净吹干;制备复合背电极3R采用平面磁控溅射法在已冲孔的聚酰亚胺柔性基片上正面连续溅镀金属铝膜,银膜和ITO透明导电膜,作为复合背电极3R,,以增加对入射光的反射;并在背面溅镀金属铝膜7R;第二次冲孔将已溅镀金属膜的聚酰亚胺柔性基片沿长度方向进行第二次冲孔,作为汇流孔3R-5,孔径1.5mm,相邻孔间距5mm,并用纯水冲洗干净和吹干;气相沉积光电转换层将已第二次冲孔的聚酰亚胺柔性基片装入沉积夹具中并放入真空室中采用等离子体化学气相沉积法进行连续两个子电池N1,I1,P1和N2,I2,P2硅基薄膜沉积,构成非晶硅非晶硅锗叠层电池光电转换层主体2R,其中I1为本征非晶硅锗膜,N1为N型非晶硅膜,P1为P型非晶硅膜,I2为本征非晶硅膜,P2为P型非晶硅膜,N2为N型氧化硅(SiOx),以增加对短波段光的反射,提高叠层电池的短路电流。N型氧化硅(SiOx)的沉积气体流量比为:CO2:SiH4=0.4,射频电源放电功率90W,沉积温度200摄氏度;平面磁控溅射采用平面磁控溅射法在沉积完硅基薄膜的聚酰亚胺柔性基片上溅镀ITO透明导电膜作为前电极1R,在基片背面溅镀一层金属铝膜以形成正负极的内部互连;采用绿激光将ITO透明导电膜,所有硅基薄膜层和复合背电极层贯穿刻划形成隔离线3R-6,同时将背面的金属铝膜按相应图形进行错位刻划形成隔离线7R-1,最终形成相邻单节电池内部串联的单元电池。每束激光功率为0.6瓦,激光刻划隔离线宽0.5mm,在刻划的同时进行强力吸尘,防止因刻划形成的非晶硅基薄膜碎屑散落到激光打刻划线影响电池性能;将已做好的单元电池用涂锡带把正负电极引出5R,并在其正面铺上EVA(乙烯-醋酸乙烯共聚物)9R和ETFE(乙烯-四氟乙烯共聚物)8R,在背面铺设EVA(乙烯-醋酸乙烯共聚物)9R和PET(聚对苯二甲酸乙二醇酯)4R,然后放入层压机进行层压封装,层压温度140摄氏度,层压时间50分钟。层压后进行修边,检测,至此全部制作过程完成。以上结合附图对本发明创造的实施例作了详细说明,但本发明创造的并不限于上述实施例,在本领域普通技术人员所具备的的知识范围内还可以,在不脱离本发明创造宗旨的前提下作出各种变化。