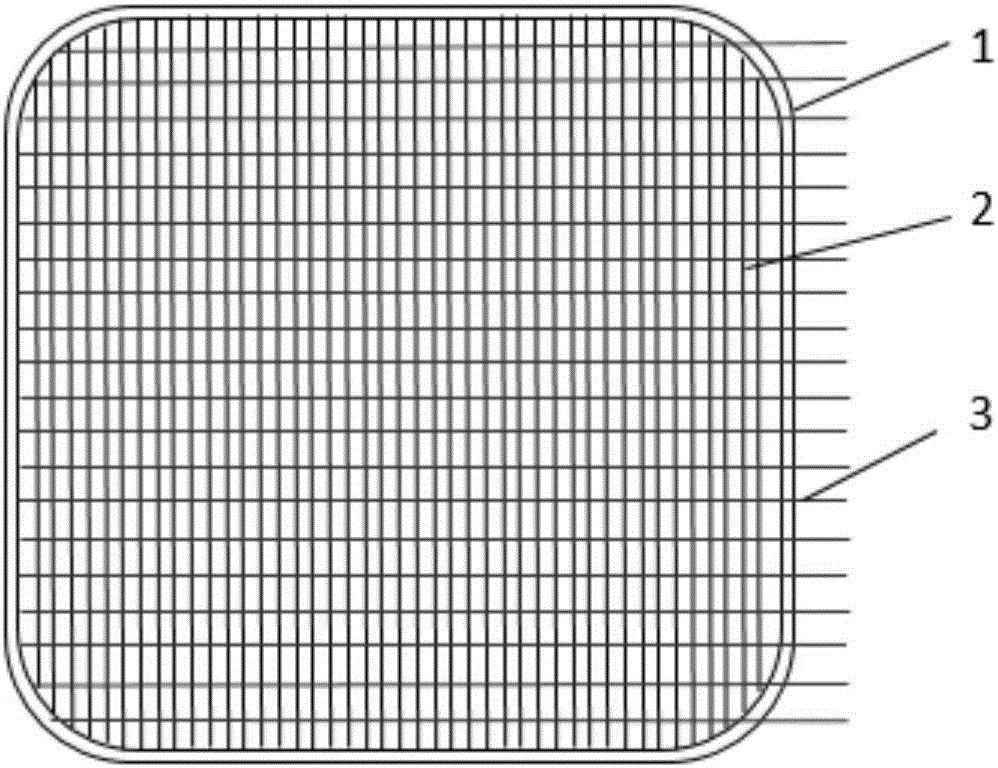
本发明涉及一种双面晶体硅异质结无主栅太阳能电池片的封装方法,属于高效双面SHJ电池的制造领域。
背景技术:
:晶体硅异质结太阳电池(SiliconHeterojunctionSolarCell,简称SHJ)综合了晶体硅的稳定性和非晶硅材料宽带隙的优点,大幅度提高了电池的开路电压,提高了晶硅电池转换效率。SHJ电池具有普通晶硅和非晶电池所不具备的特点,一是电池的温度稳定性好,与普通单晶硅电池-0.5%/℃的温度系数相比,SHJSHJ电池的温度系数可达到-0.25%/℃,使得电池即使在光照升温情况下仍有好的输出;二是不会出现类似非晶硅太阳能电池转换效率因光照而衰退的现象。SHJ电池具有转换效率高,电池工艺简便快速的特点。但其技术门槛和材料成本高,特别是成本制约了SHJ的迅速发展。其电极金属化采用的是低温银浆,由于低温银浆固化后体电阻率高,必须印刷足够的银浆以降低栅线内阻,银浆耗量高达0.1g/W,是普通晶硅电池的4-5倍。所以如何降低银耗量是促进SHJ电池发展的关键之一。其次,SHJ电池的焊接工艺也是一大难点。因为SHJ用的电极银浆采用低温固化,银粉未经烧结,焊接难度比高温烧结银浆大,电极表面黏锡不佳,焊接时易虚焊,拉力值也小于2牛;同时在200℃左右的焊接温度下,已固化树脂也容易与ITO表面发生脱离。另外,焊接时必须用到的助焊剂松香类物质,在后续层压工艺中会导致EVA膜鼓泡。公布号CN102794246A的发明专利《一种用于在导电丝表面裹覆导电浆料的裹浆机构以及裹浆方法》。通过裹浆设备在导电丝表面裹覆导电浆,通过裹有导电浆的导电丝线代替主栅及主栅焊接,串联起电池片。由于该方法是在铜丝上裹导电浆,导电浆的成本高用量大,并且要配有特殊的裹浆机构,因此制作成本较高。现有国外先进的无主栅电池互联技术有通过表面涂敷有低温合金的圆形铜线将电池片进行互联。铜线预排布在聚合物薄膜上,然后铜线和聚合物薄膜一起铺设于电池片上进行层压。铜线表面的低温合金在层压过程中熔化,使铜线粘结在电池片上。由于该方法引入了较为昂贵的低温合金材料、其它的配套封装材料以及相关设备,因此目前该方法制造成本相对较高。技术实现要素:本发明提供一种双面晶体硅异质结无主栅太阳能电池片的封装方法SHJSHJ,本发明改变SHJSHJ电池封装工艺,大幅减少银浆用量,同时不再对银浆高要求,降低生产成本,并解决电池焊接性差的问题。本发明是通过以下技术方案实现的:一种双面晶体硅异质结无主栅太阳能电池片的封装方法SHJ,其特征在于,所述方法包括以下步骤:1)自制或外购市售的带有经一次印刷的细栅线的无主栅SHJ电池片,其中,平行排列的细栅线宽度小于50μm,数量为60-120根,印刷用银浆的银含量为70-90%,优选为银含量约为80%的银浆;2)将直径为10-80μm的铜丝镀上厚度为0-1.5μm的金属防氧化层,然后:当细栅线的高度大于铜丝直径时,先在垂直于细栅线的方向上铺设铜丝,铜丝与栅线的接触点为结点,将热压敏胶或光敏胶沿铜丝方向覆盖在铜丝和电池片上后,将胶体固化;所述热压敏胶或光敏胶为透明的环氧树脂、丙烯酸树脂、酚醛树脂、硅胶、聚对苯二甲酸乙二醇酯中的一种或两种或两种以上的混合其中,胶宽大于或等于铜丝直径的1.5-2倍,胶体的涂覆方法为选自丝网印刷、钢板印刷、涂布法、转移印法中的一种,优选转移印法,胶体固化温度为150-200℃;当细栅线的高度小于或等于铜丝直径时,预先在铜丝与栅线结点处点上圆形图案的固化导电浆或黏贴上导电胶带,铺设铜丝,在200℃以下进行热压固化;其中,固化导电浆为低固银浆、铜浆、锡浆中的一种,优选低固导电银浆,导电胶带优选各向同性导电胶,圆形图案的直径大于或等于铜丝直径;3)在200℃下,将铜丝与电池片进行热压,完成双面晶体硅异质结无主栅太阳能电池片的封装。上述铜丝铺设数量为20-80根。附图说明图1为无主栅SHJSHJ电池片上排列细栅线的示意图。其中,1:ITO导电玻璃层,2:细栅线。图2为铺设铜丝后的无主栅SHJSHJ电池片示意图。其中,1:ITO导电玻璃层,2:细栅线,3:铜丝。图3:为实施例1的转移印工艺示意图。其中,4:热压敏胶,5:离型纸,6:对齐用准线。图4为实施例1转移印法的铜丝与细栅线结点横截面示意图。其中,1:ITO导电玻璃层,2:细栅线,3:铜丝,4:热压敏胶。图5为实施例2丝网印刷工艺示意图。其中,7:导电浆。图6为实施例2丝网印刷法的铜丝与细栅线结点横截面示意图。其中,1:ITO导电玻璃层,2:细栅线,3:铜丝,7:导电浆。有益效果使用本发明的方法制备无主栅SHJ电池具有如下优势:1.由于采用了多条铜丝代替主栅的结构,银浆金属化工艺中无需印刷主栅,无需二次印刷,电池片上银用量降低。2.由于铜丝的密集分布,细栅线的传输距离缩短,因此对SHJ电池用银浆的电性能降低,对银粉的规格要求及含量的要求都降低。3.不引入低温合金,无需在铜丝上裹导电浆,采用透明固化胶或者是各向同性或各项异性导电胶更节省成本。4.此工艺仍然能够保留金属化工艺,使金属化工艺与封装工艺保持独立性,因此针对电池片的电性能测试仍可以进行,电池片品质控制工序不受影响,有利于生产者对生产质量的把控。5.铜丝通过胶体固定,因此封装工艺中不再需要热焊接,全部工艺均在低于200℃下进行,因此不会破坏电池结构。6.因为不需要焊接,所以没有应力点,可以大大减少碎片率,同时因为铜丝数量多,即使电池片有隐裂或破损,仍能确保较高的组件效率。7.本发明的方法同样适用于普通N型双面电池,材料、工艺均与SHJ电池一致。具体实施方式下面通过附图和具体实施方式对本发明做进一步阐述。对比例1使用现有技术中常见四主栅工艺制备SHJ电池,经过二次丝网印刷工艺将银含量为90%银浆印刷在电池片上,然后在200℃下进行热固化制得电极,焊接后将电池片制成组件。对比例2、将银含量为90%的银浆经单次丝网印刷工艺印刷在电池片上,然后在200℃下进行热固化制得细栅线。电池片通过表面涂敷有低温合金的圆形铜线进行互联。所述低温合金为无铅的铋铟银锡的合金。铜线预排布在聚合物薄膜上在圆形铜线表面涂覆低温合金,将铜线预排布在聚合物薄膜上,然后将铜线和聚合物薄膜一起铺设于电池片上,在200℃下进行层压,通过铜线表面的低温合金的熔化,使铜线粘结在电池片上。实施例1将银含量为90%的银浆经单次丝网印刷工艺印刷在电池片上,然后在200℃下进行热固化制得细栅线。然后在垂直于细栅线的方向上铺设铜丝。通过转移印工艺,将铜丝固定在电池片上。在转移印法中,丙烯酸树脂型热压敏胶预先加载在离型纸正面上,涂覆的胶宽为铜丝直径的1.5倍,离型纸的背面如图3所示,标有基准线便于对齐。基准线可以是电池片宽度位置、起始铜丝位置、终止铜丝位置、机台宽度位置等,根据实际定位方式来设计。此带胶离型纸为卷筒状,便于连续化生产。铺设铜丝后,将离型纸带胶面覆盖在铜丝和电池片上,对齐基准线,用表面平整光滑且导热良好的设备对铜丝与电池片进行热压,使固化胶固化。此时铜丝与细栅线接触处横截面如图4所示。固化后的高透胶能防止铜丝表面与空气中的氧气接触。胶体的涂覆也可通过丝网印刷、钢板印刷,涂布法,制得细栅线后,铺设铜丝,用表面平整光滑的且导热良好的设备对铜丝与电池片施压,使铜丝与细栅线形成如图5所示的结构。实施例2将银含量为80%的银浆经单次丝网印刷工艺印刷在电池片上,然后在200℃下进行热固化制得细栅线后,在与铜丝接触的点上继续通过丝网印刷工艺用低固导电银浆印出一个圆形接触点,接触点直径略大于等于铜丝直径。所用浆料为低固导电浆,印刷完成后,然后铺设铜丝,用表面平整光滑且导热良好的设备对铜丝与电池片在200℃下进行热压,使银浆固化。表1单片SHJ电池片材料参数及测试结果对比见下表:表2SHJ电池组件电性能测试结果对比如下表所示:方案VocIscFFModuleEff对比例11111对比例2+0.6%+2.9%+1.8%+2.6%实施例1+0.7%+4.1%+1.8%+3.5%实施例2+0.6%+3.8%+2.5%+3.8%与对比例1相比,实施例1与实施例2极大地节省了银浆的用量;与对比例2相比,不用引入昂贵的低温合金材料,因此真正实现了成本降低。同时,通过对组件的性能测试可知,以对比例1为基线,实施例1与实施例2的组件效率有显著提升。当前第1页1 2 3