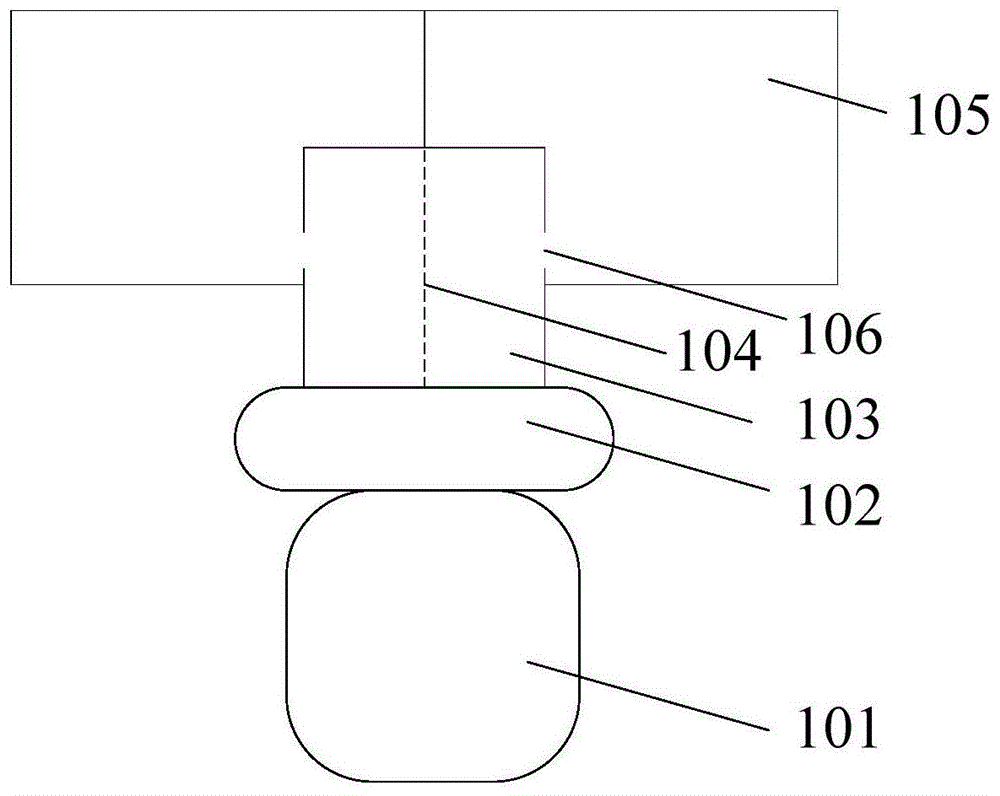
本申请涉及半导体器件制造领域,尤其涉及一种抽气装置、抽气方法以及多腔等离子体处理器。
背景技术:
:在半导体器件的制备过程中,可以在真空环境下对器件进行处理,例如半导体器件中薄膜的形成、对薄膜的等离子体刻蚀等,因此对半导体器件进行处理时,半导体器件可以置于腔体中,腔体通常会连接抽气装置而实现真空,从而为半导体器件提供真空环境。目前,可以为多个腔体配置一套抽气装置,从而同时为多个腔体提供真空环境,具体的,多个腔体可以分别与中空的混合腔连接,混合腔连接摆阀,摆阀与真空泵连接,在摆阀具有一定开度时,真空泵可以为混合腔提供低气压,多个腔体中的空气、反应废弃、带电粒子等流向低压的混合腔,这样,多个腔体中的气压随之降低。然而这种降低多个腔体的方法中,多个腔体中的气体流向低压的混合区域,可能会由于热运动而产生互窜,导致腔体内的气体氛围以及气压状态受其他腔体的影响,这样不利于腔体环境的稳定,影响该腔体内进行的半导体器件处理质量。技术实现要素:有鉴于此,本申请实施例提供了一种抽气方法及装置,能够提供稳定的腔体环境,提高腔体内进行的半导体器件的处理质量。一种抽气装置,其特征在于,包括:真空泵、摆阀、混合腔以及所述混合腔中的分隔部件;所述分隔部件将所述混合腔分为多个子腔体,所述多个子腔体用于分别连接多个待处理腔体;所述摆阀连接所述混合腔和所述真空泵;所述摆阀包括阀板和摆阀主体;所述分隔部件与所述摆阀连接,在所述摆阀具有摆阀开口时,所述分隔部件将所述摆阀开口分为多个子开口,所述多个子开口分别正对所述多个子腔体;所述摆阀开口由所述阀板相对于所述摆阀主体的旋转形成,所述分隔部件的形状根据所述阀板的旋转路径确定。可选的,对应于所述摆阀开口的多个面积,所述多个子开口之间的面积差异小于或等于预设值。可选的,所述预设值小于或等于10%。可选的,多个子腔体、所述子开口和所述待处理腔体的数量为2,所述分隔部件为挡板。可选的,所述挡板在垂直所述摆阀开口所在平面的平面内呈现为直线、曲线或折线。可选的,所述分隔部件在与所述摆阀连接的平面内的形状根据所述阀板的旋转路径确定。可选的,所述分隔部件在与所述摆阀连接的平面内呈现为曲线,所述曲线为以所述阀板的旋转中心为圆心、以所述旋转中心与所述摆阀中心的距离为半径的圆弧。可选的,所述分隔部件在与所述摆阀连接的平面内呈现为折线,形成所述折线的各个线段与所述阀板的旋转中心的距离一致,所述折线经过所述摆阀中心。可选的,所述分隔部件在与所述摆阀连接的平面内呈现为直线,所述直线经过摆阀中心且与所述摆阀中心与所述阀板的旋转中心的连线垂直。可选的,所述摆阀开口的面积基于所述待处理腔体的气压要求确定。一种抽气方法,其特征在于,利用如上述的抽气装置,所述方法包括:基于所述待处理腔体的气压要求确定所述摆阀开口的面积,以便利用所述真空泵降低所述待处理腔体的气压。本申请实施例提供了一种多腔等离子体处理器,包括多个相邻排列的等离子体处理腔体,以及所述的抽气装置。与现有技术相比,本申请至少具有以下优点:本申请实施例提供了一种抽气装置、抽气方法以及多腔等离子体处理器,其中抽气装置包括:真空泵、摆阀、混合腔以及混合腔中的分隔部件,分隔部件将混合腔分为多个子腔体,每一个子腔体分别连接一个待处理腔体,摆阀连接混合腔和真空泵,摆阀包括阀板和摆阀主体,分隔部件与摆阀连接,在摆阀具有摆阀开口时,分隔部件将摆阀开口分为多个子开口,每一个子开口分别正对一个子腔体,摆阀开口由阀板相对于摆阀主体的旋转形成,分隔部件的形状根据阀板的旋转路径确定。该装置通过调节阀板相对于摆阀主体的旋转调节摆阀开口的面积,根据阀板的旋转路径确定分隔部件的形状,从而确定摆阀开口中与子腔体正对的子开口的面积,进而利用真空泵为与子腔体连接的待处理腔体提供低气压,同时由于阀板将混合腔分隔开,可以避免不同的待处理腔体内的气体发生互窜的问题,提高腔体环境的稳定性以及在待处理腔体内进行的半导体器件的处理质量。附图说明为了更清楚地说明本申请实施例或现有技术中的技术方案,下面将对实施例或现有技术描述中所需要使用的附图作简单地介绍,显而易见地,下面描述中的附图仅仅是本申请中记载的一些实施例,对于本领域普通技术人员来讲,在不付出创造性劳动的前提下,还可以根据这些附图获得其它的附图。图1为本申请实施例提供的一种抽气装置的结构示意图;图2(a)、图2(b)和图2(c)为本申请实施例提供的一种摆阀的不同开度的示意图;图3(a)、图3(b)和图3(c)为本申请实施例提供的另一种摆阀的不同开度的示意图;图4为本申请实施例提供的待处理腔体内气压比值的折线图。具体实施方式为使本发明的上述目的、特征和优点能够更加明显易懂,下面结合附图对本发明的具体实施方式做详细的说明。在下面的描述中阐述了很多具体细节以便于充分理解本发明,但是本发明还可以采用其它不同于在此描述的其它方式来实施,本领域技术人员可以在不违背本发明内涵的情况下做类似推广,因此本发明不受下面公开的具体实施例的限制。其次,本发明结合示意图进行详细描述,在详述本发明实施例时,为便于说明,表示器件结构的剖面图会不依一般比例作局部放大,而且所述示意图只是示例,其在此不应限制本发明保护的范围。此外,在实际制作中应包含长度、宽度及深度的三维空间尺寸。目前,在半导体器件的制备过程中,可以在真空环境下对器件进行处理,通常可以通过连接抽气装置,来为半导体器件所处的腔体提供真空环境,具体实施时,可以为多个腔体提供一套抽气装置,该抽气装置可以同时为降低多个腔体的真空度。多个腔体分别与中空的混合腔连接,混合腔连接摆阀,摆阀连接真空泵,在摆阀具有一定开度时,真空泵可以通过摆阀开口为混合腔提供低气压,多个腔体中的气体流向混合腔,从而同时降低多个腔体中的气压。然而,在降低多个腔体的气压的方法中,多个腔体中的气体流向低压的混合区域时,可能会由于热运动而产生互窜,导致不同腔体内的气压氛围以及气压状态相互影响,不利于腔体环境的稳定,影响该腔体内进行的半导体器件的处理质量。为了解决以上技术问题,本申请实施例提供了一种抽气装置,包括:真空泵、摆阀、混合腔以及混合腔中的分隔部件,分隔部件将混合腔分为多个子腔体,多个子腔体用于分别连接多个待处理腔体,摆阀连接混合腔和真空泵,摆阀包括阀板和摆阀主体,分隔部件与摆阀连接,在摆阀具有摆阀开口时,分隔部件将摆阀开口分为多个子开口,多个子开口分别正对多个子腔体,摆阀开口由阀板相对于摆阀主体的旋转形成,分隔部件的形状根据阀板的旋转路径确定。该装置通过分隔部件将混合腔分为多个子腔体,每一个子腔体与一个待处理腔体连接,待处理腔体内的气体分别流向混合腔中对应的子腔体,使得不同的待处理腔体内的气体不会发生互窜。混合腔和真空泵之间连接有摆阀,摆阀包括阀板和摆阀主体,摆阀具有摆阀开口时,真空泵通过摆阀开口抽取混合腔内的气体,降低混合腔内的气压,从而降低待处理腔体内的气压。而分隔部件与摆阀连接,将摆阀开口分为多个子开口,子开口正对子腔体,这样真空泵可以通过各个子开口分别抽取正对的子腔体中的气体,分别降低各个子腔体的气压,以及与子腔体连接的待处理腔室的气压。本申请实施例中,可以通过阀板相对于摆阀主体的旋转路径确定分隔部件的形状,从而确定每一个子开口在摆阀开口中的相对面积,子开口对应于子腔体,子腔体连接待处理腔体,子开口的面积影响待处理腔体的低压状态,子开口面积越大,待处理腔体内的气压越低,因而,可以通过确定分隔部件的形状来确定子开口在摆阀开口中的相对面积,从而确定各个待处理腔体内的气压状态。为了更好地理解本申请的技术方案和技术效果,以下将结合附图对具体的实施例进行详细的描述。参考图1所示,为本申请实施例提供的一种抽气装置,包括:真空泵101、摆阀102、混合腔103以及混合腔103中的分隔部件104,分隔部件104将混合腔103分为多个子腔体,多个子腔体分别连接多个待处理腔体105。待处理腔体105是半导体器件的形成过程中的反应腔,在半导体器件的制造过程中,需要对待处理腔室105进行真空处理,从而降低待处理腔室105的真空度;当然,待处理腔体105也可以是其他场景下需要提供真空环境的腔体,在此不做限制。待处理腔体105的数量可以为两个,也可以是两个以上。多个待处理腔体105可以是不同的反应腔,也可以是同一反应腔中的多个反应室,多个反应室可以同时进行相同的工艺流程,也可以进行不同的工艺流程,多个待处理腔体105中可以具有相同的气压,也可以具有不同的气压。举例来说,多个待处理腔体105可以都是对薄膜的等离子体刻蚀的反应腔,在刻蚀的过程中,需要保持反应腔的低气压。具体的,等离子体在电场的作用下向薄膜运动,刻蚀薄膜表面,刻蚀过程中产生的气体需要抽取到待处理腔体105之外,防止待处理腔体105内的气压增大而影响等离子体的刻蚀效果。本申请实施例中,待处理腔体105可以与混合腔103通过连接孔106连接,参考图1所示,混合腔103可以连接真空泵101,利用真空泵101为混合腔103提供低压环境,这样待处理腔体105中的气压会通过连接孔106流向混合腔103,实现了对待处理腔体105的降压。混合腔103和真空泵101可以通过摆阀102连接,通过摆阀102控制混合腔103和真空泵101是否连通,在摆阀具有一定开口时,混合腔103和真空泵101连通,摆阀开口越大,混合腔103和真空泵之间的通道截面积越大。待处理腔体105内的气体在混合腔103内汇合被真空泵101抽取,从而降低待处理腔体105内的气压,而通过在混合腔103和真空泵101之间设置摆阀102,实现待处理腔体105内压力的控制。摆阀102可以包括阀板112和摆阀主体122,参考图图2(a)、图2(b)和图2(c)、图3(a)、图3(b)和图3(c)所示,阀板112和摆阀主体122之间具有固定点,阀板112可以以固定点为中心相对于摆阀主体122旋转运动,在阀板112与摆阀主体122不完全重合时,摆阀102产生摆阀开口,在阀板112和摆阀主体122之间具有位置100时,摆阀具有较小的摆阀开口,而从位置100至位置900,随着阀板112的旋转,阀板112和摆阀主体122的重合面积越来越小,摆阀开口越来越大。真空泵101通过摆阀开口抽取混合腔103内的气体,实现多个待处理腔体105的降压,可以理解的是,降压后的多个待处理腔体105中的气压可以是相同的。在具体的实施例中,摆阀开口可以基于多个待处理腔体105的气压要求确定,在待处理腔体105内需要较大的气压时,设置较小的摆阀开口,在待处理腔体105内需要较小的气压时,设置较大的摆阀开口。然而,上述对多个待处理腔体105进行降压的过程中,由于多个待处理腔体105中的气体流向低压的混合腔103而在混合腔103中汇合,若多个待处理腔体105内的压力不同,例如多个待处理腔体105中的一部分腔体内不进行刻蚀或镀膜处理而存在较低的气压,另一部分腔体需要进行刻蚀或镀膜处理而存在较高的气压,或者多个待处理腔体105分别进行不同的操作处理导致内部气压不同,此时多个待处理腔体105中的气体会在混合腔103中汇合后,由于热运动可能产生互窜,导致多个待处理腔体105之间的气压氛围以及气压状态相互影响,不利于待处理腔体105中的环境稳定性。因此,本申请实施例中,可以利用分隔部件104将混合腔103分为多个子腔体,每一个子腔体分别连接一个待处理腔体105,待处理腔体105中的气体流向与其连接的子腔体后被抽走,这样待处理腔体105内的气体在流向混合腔103后不会发生互窜,相互之间不会影响。分隔部件104还可以与摆阀102连接,在摆阀102具有摆阀开口时,分隔部件104将摆阀开口分为多个子开口,多个子开口分别正对多个子腔体。摆阀102与真空泵101连接,在摆阀102具有摆阀开口时,真空泵101可以通过正对子腔体的子开口抽取混合腔103中各个子腔体的气体,从而分别对与子腔体连接的待处理腔体105进行降压。本申请实施例中,可以根据待处理腔体105内所需的气压确定各个子开口的相对面积,多个子开口的面积可以相同也可以不同,例如多个待处理腔体内105进行不同的处理操作时需要不同的气压,可以将多个子开口的面积设置为不同的面积,当然,多个子开口的面积可以具有大致相同的比值,在多个待处理腔体105内进行相同的操作处理时需要相同大小的气压,可以将多个子开口的面积设置为大致相同的面积。在具体的实施例中,多个子开口之间的面积差异小于或等于预设值,这样多个待处理腔体105内的气压也大致相同。在本实施例中,预设值可以小于或等于10%,例如可以为5%,3%或1%等。在本申请实施例中,可以根据阀板112的旋转路径确定分隔部件104的形状,例如根据阀板112的旋转中心以及摆阀102的中心确定分隔部件104的形状,分隔部件104的形状决定了多个子开口之间的相对面积,而摆阀102中阀板112和摆阀主体122之间的位置关系决定了多个子开口的总面积大小,进而确定与子开口正对的子腔体连接的待处理腔室105的气压。作为一种示例,在本实施例中,多个子腔体、子开口和待处理腔体的数量可以为2,分隔部件104为挡板,挡板在垂直摆阀开口所在平面的平面内可以呈现的形状不影响子开口的相对面积,因此可以为直线、曲线或折线,例如挡板可以为垂直摆阀102设置的平面板或曲面板。可以理解的是,挡板在垂直摆阀开口所在平面内的平面内呈现的形状,影响多个子腔体的相对体积,例如曲面板的形状影响分隔后的两个子腔体的实际体积。挡板在与摆阀连接的平面内可以呈现为直线、曲线或折线,挡板的形状影响各个子开口的相对面积,下面进行具体说明。挡板在与摆阀连接的平面内可以呈现为直线,参考图2(a)、图2(b)和图2(c)所示,为本申请实施例中一种摆阀102不同开度的示意图,虚线表示挡板相对于摆阀102的位置,其中,阀板112与摆阀主体122的各个相对位置下,与两个子腔体正对的摆阀开口中的子开口面积可以不同,挡板104竖直平分混合腔103形成两个子腔体,且竖直平分摆阀开口形成两个子开口,从图2(a)、图2(b)和图2(c)中可以看出,直线左侧的子开口对应左侧的子腔体,直线右侧的子开口对应右侧的子腔体。本申请实施例中,可以对不同摆阀开度下摆阀开口以及子开口的面积进行测量,可以理解的是,不同的摆阀开度对应不同的摆阀开口面积,摆阀开度越大,摆阀开口面积越大。参考表1所示,为不同摆阀开度下摆阀开口的面积(openarea),以及两个子开口面积s1和s2的示意图,面积的单位均为mm2。其中,不同摆阀开度可以通过阀板112与摆阀主体122的相对位置(bladeposition)表示,包括位置100、200、300、400、500、600、700、800、900,s1为挡板右侧的子开口的面积,s2为挡板左侧的子开口的面积,s1+s2为摆阀开口的面积,s1/(s1+s2)表示s1占摆阀开口面积的比例。很明显,s1的面积小于s2的面积,在摆阀开口面积较小时,这种差异更加明显。表1不同摆阀开度下摆阀开口以及子开口的面积位置1002003004005006007008009001000s1+s22646.513684.925249.83643146899.856415.964756.77168276865.479422.6s1212.73187.37682.113031.118796.924564.529938.734546.938013.839711.3s22433.810497.617567.723399.928102.931851.43481837135.138851.639711.3s1/(s1+s2)8.04%23.29%30.42%35.77%40.08%43.54%46.23%48.19%49.46%50.00%在本申请实施例中,为了保持待处理腔室105的无氧环境,还可以向待处理腔室105通入气体,例如可以为氮气(n2)、氩气(ar)等,因此可以进一步测量不同摆阀(pendulumvalve,pv)开度下,不同的气体流速下对应的两个待处理腔体105内的气压,参考表2所示,为不同摆阀开度下不同氮气流速对应的待处理腔体的气压,这里以位置100、300、500、700、900为例进行说明,氮气流量的单位为标准立方厘米每分钟(standardcubiccentimeterperminute,sccm),气压单位为mtorr,其中,“/”前的是与s2正对的子腔体连接的待处理腔体的气压,“/”后的是与s1正对的子腔体连接的待处理腔体的气压,由此可知,与s1正对的子腔体连接的待处理腔体的气压始终大于或等于与s2正对的子腔体连接的待处理腔体的气压。由此可知,隔板的存在导致两个待处理腔体105的气压在一些摆阀开度下产生了差异,且摆阀开度越小,气压差异越明显,例如在位置300的压力差达到7.5%。表2不同摆阀开度下不同气体流速对应的待处理腔体的气压本申请实施例中,还可以根据阀板112的旋转路径确定分隔部件104在与摆阀102连接的平面内的形状和位置,从而更加合理分配各个子开口的面积,分别满足待处理腔体105内的气压需求。具体的,可以令各个子开口的面积在不同的摆阀开度下具有固定的比值,这样可以稳定的为每个待处理腔体105提高低压环境,例如可以令各个子开口的面积保持在1:1,这样可以使每个待处理腔体105的气压相等。下面对于如何实现各个子开口的面积比例为1:1的情况,本领域技术可以根据实际情况基于阀板112的旋转路径设计其他形状的挡板,以使各个子开口的面积保持在其他比值。作为一种可能的实现方式,分隔部件104也可以在与摆阀102连接的平面内呈现为直线,直线经过摆阀102中心且与摆阀102中心与阀板112的旋转中心的连线垂直,该直线将摆阀开口分割为两部分,而由于直线的位置与摆阀的旋转中心相关,对于不同大小的摆阀开口,分隔而成子开口的相对面积较为接近,多个待处理腔体105的气压也较为接近。作为再一种可能的实现方式,分隔部件104可以在与摆阀102连接的平面内呈现为折线,形成所述折线的各个线段与所述阀板112的旋转中心的距离一致,折线经过摆阀102中心。该折线将摆阀开口分割为两部分,同时对于不同大小的摆阀开口,分隔而成子开口的相对面积较为接近,多个待处理腔体105的气压也较为接近。作为另一种可能的实现方式,分隔部件104在与摆阀102连接的平面内呈现为曲线,该曲线可以为以阀板112的旋转中心为圆心、以旋转中心和摆阀102中心的距离为半径的圆弧。参考图4所示,为本申请实施例中摆阀102的示意图,中间的曲线表示挡板相对于摆阀102的位置,其中阀板112与摆阀主体122的各个相对位置下,与两个子腔体正对的摆阀开口中的子开口面积可以不同,挡板平分混合腔103形成两个字腔体,且平分摆阀开口形成两个子开口,从图4可以看出,曲线左侧的子开口对应左侧的子腔体,曲线右侧的子开口对应右侧的子腔体,在摆阀开口的开度不同的情况下,两个子腔体相对的子开口的面积大小保持相同或相近。本申请实施例中,可以对不同摆阀开度下摆阀开口以及子开口的面积进行测量,参考表3所示,表3为不同摆阀开度下下摆阀开口的面积(openarea),以及两个子开口面积s1和s2的示意图,面积的单位均为mm2。其中,不同摆阀开度可以通过阀板112与摆阀主体122的相对位置(bladeposition)表示,包括位置100、200、300、400、500、600、700、800、900,s1为挡板右侧的子开口的面积,s2为挡板左侧的子开口的面积,s1+s2为摆阀开口的面积,s1/(s1+s2)表示s1占摆阀开口面积的比例。由此可以看出,两个子开口面积s1和s2基本相同,可以为多个待处理腔体105提供基本一致的气压环境。表3不同摆阀开度下摆阀开口以及子开口的面积位置1002003004005006007008009001000s1+s22646.513684.925249.83643146899.856415.964756.77168276865.479422.6s11571.827427.1413229.218800.823949.728636.73274936155.338691.639922.2s21074.726257.7412020.617630.222950.127779.232007.835526.738173.939500.4s1/(s1+s2)59.39%54.27%52.39%51.61%51.07%50.76%50.57%50.44%50.34%50.27%在本申请实施例中,为了保持待处理腔室105的无氧环境,还可以向待处理腔室105通入气体,例如可以为氮气(n2)、氩气(ar)等,因此可以进一步测量不同摆阀开度下,不同气体流速下对应的两个待处理腔体105内的气压,参考表4所示,为不同摆阀开度下不同氮气流速对应的待处理腔体的气压,这里以位置100、300、500、700、900为例进行说明,氮气流量的单位为sccm,气压单位为mtorr,其中,“/”前的是与s2正对的子腔体连接的待处理腔体的气压,“/”后的是与s1正对的子腔体连接的待处理腔体的气压,由此可知,与s1正对的子腔体连接的待处理腔体的气压始终接近于与s2正对的子腔体连接的待处理腔体的气压。由此可知,不同气体流速下两个待处理腔体105内的气压基本相同,压力差小于2%。表4不同摆阀开度下不同氮气流速对应的待处理腔体的气压本实施例中,还测量了利用不同挡板之后两个待处理腔体105中的气压的比值状态,并将气压比值绘制成折线图,参考图4所示,为本申请实施例中不同挡板能够实现的待处理腔体的气压比值,可以看出,挡板在摆阀102连接的平面内呈现为曲线时,两个待处理腔体105内的气压差在2%内,挡板竖直平分摆阀主体122时,两个待处理腔体105内的气压差达到7.5%,因此可以利用曲面板作为挡板,从而为多个待处理腔体105提供相同或相近的气压环境。参考表5所示,为利用不同挡板时,多个工艺条件下刻蚀速率的比对情况,包括仅源电源(sourceonly)的工艺条件、高气压低偏压的工艺条件和标准氧化物(oxidestd)的工艺条件,其中a1和a2分别表示待处理腔体105中与s1正对的子腔体连接的待处理腔体和与s2正对的子腔体连接的待处理腔体的刻蚀速率,mismatch分别表示了a1和a2的差异值,其中,现有技术为平面板竖直平分摆阀开口时的测试结果,本申请为以曲面板平分摆阀开口为例的测试结果,可以看出,平面板竖直平分摆阀开口时两个待处理腔体105内的刻蚀速率差高达1.89%,而曲面板平分摆阀开口时,两个待处理腔体105内的刻蚀速率差在1%内。表5利用不同挡板,多个工艺条件下刻蚀速率的比对本申请实施例提供了一种抽气装置,包括:真空泵、摆阀、混合腔以及混合腔中的分隔部件,分隔部件将混合腔分为多个子腔体,每一个子腔体分别连接一个待处理腔体,摆阀连接混合腔和真空泵,摆阀包括阀板和摆阀主体,分隔部件与摆阀连接,在摆阀具有摆阀开口时,分隔部件将摆阀开口分为多个子开口,每一个子开口分别正对一个子腔体,摆阀开口由阀板相对于摆阀主体的旋转形成,分隔部件的形状根据阀板的旋转路径确定。该装置通过调节阀板相对于摆阀主体的旋转调节摆阀开口面积,根据阀板的旋转路径确定分隔部件的形状,从而确定摆阀开口中与子腔体正对的子开口的面积,进而利用真空泵为与子腔体连接的待处理腔体提供低气压,同时由于阀板将混合腔分隔开,可以避免不同的待处理腔体内的气体发生互窜的问题,提高腔体环境的稳定性以及在待处理腔体内进行的半导体器件的处理质量。上述对本申请实施例的抽气装置进行了详细描述,此外,本申请还提供了利用上述抽气装置进行抽气处理的抽气方法,包括:基于所述待处理腔体105的气压要求确定摆阀开口,以便利用真空泵101降低所示待处理腔体105的气压。本申请还提供了一种多腔等离子体处理器,包括:多个相邻排布的等离子体处理腔体,以及上述所述的抽气装置。以上所述,仅是本申请的较佳实施例而已,并非对本申请作任何形式上的限制。虽然本申请已以较佳实施例揭露如上,然而并非用以限定本申请。任何熟悉本领域的技术人员,在不脱离本申请技术方案范围情况下,都可利用上述揭示的方法和技术内容对本申请技术方案做出许多可能的变动和修饰,或修改为等同变化的等效实施例。因此,凡是未脱离本申请技术方案的内容,依据本申请的技术实质对以上实施例所做的任何简单修改、等同变化及修饰,均仍属于本申请技术方案保护的范围内。当前第1页12