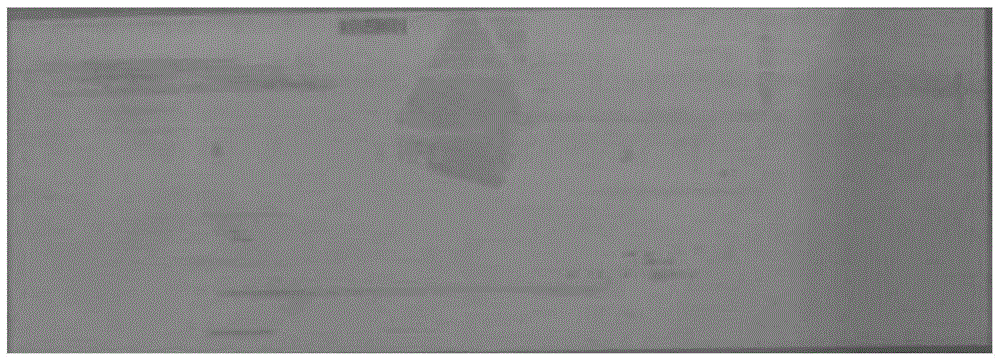
本申请涉及印制电路板领域,尤其是涉及金属材料的表面预处理方法和pcb板的生产工艺。
背景技术:
:印制电路板(pcb,printedcircuitboard),又称为印刷电路板或印刷线路板。铜箔是印制电路板的主要原料,铜箔的性能与其表面处理密切相关。在印制电路板制程,铜表面预处理贯穿了整个工艺流程。随着5g(第五代通讯)技术的发展,高频信号在传输过程中要求低损耗甚至无损耗,因而对铜表面质量的要求也越来越高。传统的铜表面预处理工艺主要分为两类:第一类是采用超粗化、蚀刻等化学方法,通过铜与酸在氧化剂参与下发生化学腐蚀,增大铜面的粗糙度,从而增强结合力。第二类是通过磨刷、火山灰处理等物理方法来摩擦铜表面,同样是通过增大铜面的粗糙度来增强结合力。然而,铜面粗糙度的增加会导致高频信号在传送过程中产生大量衰减,不利于高频信号的传输。技术实现要素:本申请旨在至少解决现有技术中存在的技术问题之一。为此,本申请提出一种无需增加表面粗糙度的金属材料的表面预处理方法和pcb板的生产工艺。本申请的第一方面,提供金属材料的表面预处理方法,该方法包括以下步骤:将0.3~0.6wt%的键合剂溶液与金属材料接触。根据本申请实施例的表面预处理方法,至少具有如下有益效果:通过键合剂与金属材料的表面接触,键合剂分子中的一官能团与金属材料中的金属原子以配位键方式紧密结合而在表面形成一层均匀的单分子膜;而键合剂分子的另一官能团暴露在表面,该官能团能够与树脂单体/聚合物发生聚合反应,将树脂牢牢的黏附在金属材料表面,从而获得更高的结合力。通过这种方法,在不改变金属材料表面的粗糙度的同时使金属材料的表面结合力有了很大的提升。另外,当键合剂溶液的浓度过低时,形成的单分子膜不均匀,结合力较差,容易出现甩落;而键合剂的浓度如果过高的话,则会形成多层的键合剂膜层,先形成的膜层会对后形成的膜层造成遮挡,使部分膜层无法与金属材料结合导致结合力下降。因而,利用0.3~0.6wt%的键合剂溶液可以在金属材料表面最大化结合力等性能。另一方面,该前处理方法无需在前处理前预留出待腐蚀或打磨的金属层,使用中也不会对金属材料的表面产生任何损伤。相比传统工艺的诸多弊端,该方法极大地缩短了工艺流程,降低了工艺成本。根据本申请的一些实施例,键合剂溶液和金属材料的接触时间为35~60s。键合剂溶液和金属材料反应形成的膜层随着接触时间的变长逐渐变得更完全、更均匀,从而获得更好的结合力;但接触时间过长不仅无法获得更进一步的提升反而影响工艺流程的进行。根据本申请的一些实施例,键合剂溶液中的键合剂包括缓蚀剂、络合剂和无机酸。根据本申请的一些实施例,缓蚀剂为苯并三氮唑。根据本申请的一些实施例,金属材料在与键合剂溶液接触前,还包括入料、酸洗、一次水洗的步骤;金属材料在与键合剂溶液接触后,还包括二次水洗、干燥的步骤。根据本申请的一些实施例,入料时的传送速度为1.5~2.0m/min。根据本申请的一些实施例,酸洗采用3~6wt%的硫酸溶液;优选的,酸洗时温度为37~43℃、压力为0.8~1.8kg/cm2。根据本申请的一些实施例,一次水洗和二次水洗采用溢流水洗。为避免工业过程中的各种杂质残留,保证清洗的洁净度,水洗过程中采用溢流水洗以获得尽可能好的水洗效果。根据本申请的一些实施例,一次水洗采用三段溢流水洗。根据本申请的一些实施例,一次水洗时压力为0.8~1.8kg/cm2。根据本申请的一些实施例,二次水洗采用两段溢流水洗。根据本申请的一些实施例,二次水洗时压力为0.8~1.8kg/cm2。根据本申请的一些实施例,干燥后,对金属材料进行贴膜或防焊印刷。根据本申请的一些实施例,该金属材料包括铜材料层,具体可以是铜材或覆有铜层的其它材料。本申请的第二方面,提供pcb板的生产工艺。该生产工艺采用上述的表面预处理方法对基板进行表面预处理。本申请的附加方面和优点将在下面的描述中部分给出,部分将从下面的描述中变得明显,或通过本申请的实践了解到。附图说明下面结合附图和实施例对本申请做进一步的说明,其中:图1~图4是本申请中采用不同浓度键合剂对铜表面进行预处理得到的产品的甩膜图片。图5和图6是本申请中采用不同浓度键合剂对铜表面进行预处理得到的产品的aoi扫描的缺陷照片,其中,图5是开路照片,图6是缺口照片。具体实施方式以下将结合实施例对本申请的构思及产生的技术效果进行清楚、完整地描述,以充分地理解本申请的目的、特征和效果。显然,所描述的实施例只是本申请的一部分实施例,而不是全部实施例,基于本申请的实施例,本领域的技术人员在不付出创造性劳动的前提下所获得的其他实施例,均属于本申请保护的范围。下面详细描述本申请的实施例,所述实施例的示例在附图中示出。下面通过参考附图描述的实施例是示例性的,仅用于解释本申请,而不能理解为对本申请的限制。在本申请的描述中,若干的含义是一个以上,多个的含义是两个以上,大于、小于、超过等理解为不包括本数,以上、以下、以内等理解为包括本数。如果有描述到第一、第二只是用于区分技术特征为目的,而不能理解为指示或暗示相对重要性或者隐含指明所指示的技术特征的数量或者隐含指明所指示的技术特征的先后关系。本申请的描述中,除非另有明确的限定,设置、安装、连接等词语应做广义理解,所属
技术领域:
技术人员可以结合技术方案的具体内容合理确定上述词语在本申请中的具体含义。本申请的描述中,参考术语“一个实施例”、“一些实施例”、“示意性实施例”、“示例”、“具体示例”、或“一些示例”等的描述意指结合该实施例或示例描述的具体特征、结构、材料或者特点包含于本申请的至少一个实施例或示例中。在本说明书中,对上述术语的示意性表述不一定指的是相同的实施例或示例。而且,描述的具体特征、结构、材料或者特点可以在任何的一个或多个实施例或示例中以合适的方式结合。以下实施例中的键合剂采用昆山长优电子材料有限公司生产的ba-1001铜面键合剂,该产品中包含缓蚀剂、络合剂和无机酸,缓蚀剂为苯并三氮唑。实施例1本实施例提供一种pcb基板的表面预处理方法,该方法包括以下步骤:s1:入板,选用内层含铜芯板、外层板电或蚀刻后形成铜面的pcb板,水平投入预处理生产线,传送速度控制在1.5~2.0m/min。s2:酸洗,使用稀硫酸浓度为3~6%的酸洗液酸洗,酸洗时控制温度为37~43℃,控制压力为0.8~1.8kg/cm2。s3:一次水洗,采用三段溢流水洗,每段溢流水洗缸体体积为100l,水洗压力控制在0.8~1.8kg/cm2。s4:键合剂处理,在ph值5.5~6.5范围下,控制温度为25~28℃,采用浓度为0.3~0.6wt%的键合剂溶液与水洗后的pcb板的铜面接触35~60s。s5:二次水洗,采用两段溢流水洗,每段溢流水洗缸体体积为100l,水洗压力控制在0.8~1.8kg/cm2。s6:烘干,包括吸水海绵、强风吹干和热风吹干三个步骤。首先以干净湿润的吸水海绵将板面水分去除并分布均匀,然后以强力冷风将板面和孔内的水吹离板面,最后以热风将板面彻底烘干,烘干温度控制在80~95℃。在将pcb基板烘干后,还可以进行干、湿膜贴膜或者防焊印刷。在上述表面处理方法中,通过酸洗除去pcb基板表面的油脂和轻微的氧化层,随后通过一次水洗去除pcb基板残留的酸液和油脂。在使用键合剂处理后二次水洗水洗后去除pcb基板的残留键合剂,清洁板面。实施例2本实施例提供一种pcb板的生产工艺,包括以下步骤:步骤1:采用实施例1中的表面预处理方法对pcb基板进行表面预处理。步骤2:使用油墨涂布轮在预处理后的pcb基板的表面涂设感光油墨层,并对感光油墨层进行烘烤干燥处理。步骤3:将干燥完成的pcb基板进行菲林曝光处理。步骤4:将pcb基板置于显影机中进行显影处理,显影出多余的线路。步骤5:经人工目检后,将pcb基板置于蚀刻机中蚀刻除去多余的线路,最后除去表面的感光油墨层,清洗、烘干。其中,在pcb板的生产过程中,其上的线型可以是直线、斜线、拐角线、圆弧等线型。线宽/间距可以控制在30/30μm、50/50μm、70/70μm、80/80μm、90/90μm、100/100μm等不同范围。实施例3对比实验分别使用浓度为0.1wt%、0.3wt%、0.6wt%、0.9wt%的键合剂溶液采用实施例2中的方法生产pcb板,线宽/间距设置为70/70μm。对生产出的pcb板的性能进行比较,包括以下测试内容:1.甩膜检查:目视检查显影后板面,出现甩膜(结合力不良)即判定不合格;2.aoi扫描:统计aoi(自动光学检查)扫描缺陷,缺陷点数越多,结合力越差;3.线宽测量:蚀刻后取切片测量线宽是否在要求公差范围内。甩膜检测结果见表1和图1~4,图1~图4是键合剂浓度分别为0.1wt%、0.3wt%、0.6wt%、0.9wt%时,对铜表面进行预处理得到的产品的甩膜图片。表1.甩膜检测结果键合剂浓度结果0.1甩膜0.3未甩膜0.6未甩膜0.9甩膜从表1和图1~4的结果可以看出,当键合剂浓度控制在0.3~0.6wt%时,不会出现甩膜,而当键合剂浓度低于0.3%,形成的单分子膜不均匀,与干膜结合不牢固,显影后干膜容易甩落;在键合剂浓度高于0.6%时,形成多层的键合剂膜层,从而出现第一层的膜层挡住第二层,多层的一端因连接不到铜而导致键合剂的附着力下降,同样导致甩膜。aoi扫描结果见表2和图5、图6,图5和图6分别是aoi扫描过程中开路和缺口照片。表2.aoi扫描结果从表2中可以看出,当键合剂浓度控制在0.3~0.6wt%时,出现缺口和开路的缺陷情况明显比键合剂浓度小于0.3wt%或大于0.6wt%时更少,表明通过对键合剂浓度的控制可以有效改善其缺陷情况。线宽测量结果见表3(单位:μm)。表3.线宽测量结果从线宽测量结果可以看到,线宽满足设计值公差(70μm)+/-20%范围内的相关要求。综合上述结果可以看到,显影后浓度0.1%和0.9%的键合剂出现甩膜,浓度0.3%和0.6%的键合剂未甩膜;扫描缺陷点数从少到多为:0.6%键合剂<0.3%键合剂<0.1%键合剂<0.9%键合剂;线宽满足设计值公差+/-20%范围内。因此,浓度0.3%和0.6%的键合剂与铜面结合良好,满足前处理生产对铜面结合力的要求;浓度0.1%和0.9%的键合剂与铜面结合不良,不满足前处理生产对铜面结合力的要求。采用键合剂工艺对铜表面进行预处理,既不改变铜表面的粗糙度,也不会对铜面产生任何损伤,进而不会影响5g产品中高频信号的传输速度。键合剂可以直接在洁净铜面上使用,不必再进行任何铜面粗化处理。键合剂处理完之后,只需进行一般的水洗烘干即可进入后制程工序。因而极大地缩短了工艺流程,降低了工艺成本。而且键合剂废液可按一般酸性废液处理,不会产生高铜高酸废水或废渣,实现了环保高效的生产。上面结合附图对本申请实施例作了详细说明,但是本申请不限于上述实施例,在所属
技术领域:
普通技术人员所具备的知识范围内,还可以在不脱离本申请宗旨的前提下作出各种变化。此外,在不冲突的情况下,本申请的实施例及实施例中的特征可以相互组合。当前第1页12