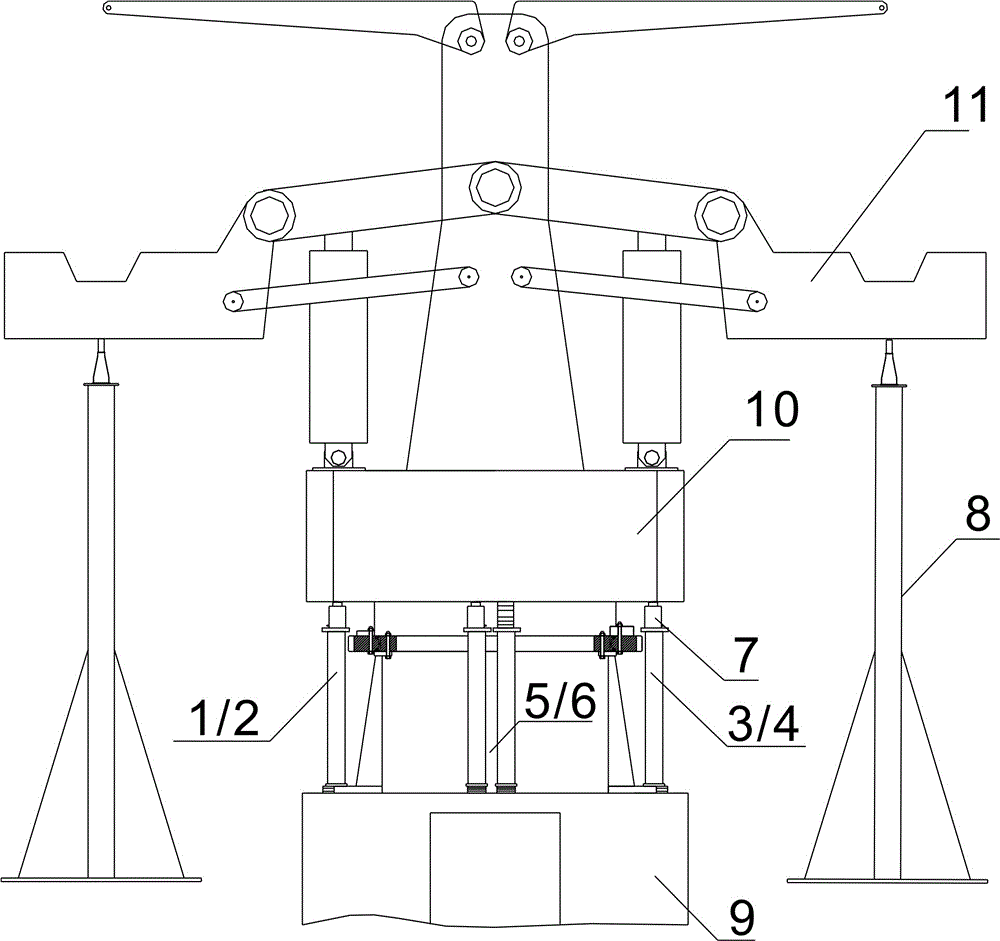
本发明涉及连铸机设备安装方法,尤其涉及一种连铸系统中大包回转台旋转轴承更换的方法。
背景技术:大包回转台是连铸机系统中的主要设备之一,长时间负荷运行使得旋转轴承需要拆卸更换。由于大包回转台设计在行车轨道梁的下方,回转台轴承安装在底座与回转体之间,轴承上面的设备通常有一百多吨。传统的轴承拆换方法是这样的,设计制作专用吊具,使用钢水接受跨和浇铸跨的两台桥式起重机配合倒链等工具共同抬吊依次拆卸叉臂、顶升液压缸、回转体等设备,或者使用一台大规格的汽车吊配合浇铸跨的行车共同抬吊拆卸设备。设备重量大,且处于高空作业施工,安全风险高,同时,制作吊具费工费时,施工成本较高。由于使用双机抬吊的方式,占用了钢水接受跨的桥式起重机,影响炼钢车间的正常生产。
技术实现要素:本发明要解决的技术问题在于提供一种原地顶升工艺更换大包回转台轴承的方法,该方法省时、省力,机械费、材料费用少。本发明解决其技术问题所采用的技术方案是:一种大包回转台轴承更换的方法,包括以下步骤:步骤1:关联设备的保护性拆除及辅助支柱的准备:1.1)拆卸刹车盘、齿护罩和传动电机减速机,对干涉支柱安装位置的水平护罩进行切割;1.2)根据需要底座内的滑环和旋转给油器拆卸,限位的拆卸,轴承和底座的联接螺栓部分拆卸;1.3)定位安装顶升支柱的:安装的顶升支柱共八件,其中与浇铸线垂直的方向布置四件主液压千斤顶,分别为1号主液压千斤顶至4号主液压千斤顶,型号为200t;沿浇铸方向的支柱设置两个辅助千斤顶,分别为5号液压千斤顶和6号液压千斤顶,作为辅助支撑;在大包回转台叉臂下方各设置一组支柱,为稳定性支架,每组支架有两个顶升点,共设置4台50t机械千斤顶,两个顶升点之间用槽钢连接;其中,与浇铸线垂直的方向布置的支柱定位尺寸要准确,防止轴承拉出时受阻卡;支柱设置的垂直度要求为1/1000,柱顶板的水平度要求为0.5/1000。为防止顶升中心偏移,支柱底部、中部与底座体焊接,支柱底与基础接触面用斜垫铁楔紧,增加稳定性。1.4)为主液压千斤顶设置扁担梁:在200t液压千斤顶受顶部位,级包臂升降油缸座处,并排焊接放置两根预先设计制作250×250×2500mmH型钢,作为同一侧两件主液压千斤顶的扁担梁;1.5)防止包臂升降:将包臂升降架上部用20#槽钢焊死,4台50t机械千斤顶支柱8起到扶稳作用;步骤2:大包回转台上部设备顶升步骤:2.1)检查准备:对1号主液压千斤顶至4号主液压千斤顶4台200t主液压顶、2台辅助液压千斤顶设置完毕后,进行检查确认,叉臂下方设置的4台50t机械千斤顶就位,每个保护柱头垫上垫板;所有顶受力,保护柱顶塞入垫板外加一对斜垫板;检查支柱承载力整体稳定无异常;2.2)拆松齿轮与上回转体的联接螺帽:拆卸轴承与底座的连接螺栓,其中留下8条螺栓不卸螺帽,以便上部回转体起升时带起轴承;2.3)进行大包回转台上部设备顶升:顶升顺序和要求:给4台200t主液压顶和2台副液压顶编号,主液压顶:西侧1、2号,东侧3、4号;副液压顶:南侧5号,北侧6号;2.4)首先启动1、2号主千斤顶,顶升高度以5mm~10mm为一个步进单位;每顶升一步,在保护支柱同时加入垫板楔紧;随后启动3、4号主千斤顶,顶升高度以5mm~10mm为一个步进单位。每顶升一步,在保护支柱同时加入垫板楔紧,用尺控制顶升量;5、6号辅助支柱的顶升方式与1、2、3、4号千斤顶相同的方式操作顶升;4台叉臂下方的50t机械千斤顶(8)紧跟随上升,起到扶稳作用;2.5)修正步骤:以上步骤2.2)至2.4)为一个循环操作;进行了三个循环操作后使用尺测量底座法兰与刹车盘法兰之间四个垂直方向距离,应当保持一致没有大的偏差,如出现大的偏差应即时修正,直到顶升到所需的高度;步骤3:大包回转台轴承更换步骤:3.1)顶升到预先设定的高度后,全面检查顶架整体结构的稳定性,如无异常拆离北侧的辅助支柱;用浇铸跨行车将预先设计制作的滑道吊入底座法兰口上,用3台10t机械千斤顶顶住轴承,然后拆卸先前预留的8条螺栓,操作机械千斤顶将轴承回落到滑道小车上;最后使用1台2t手拉葫芦将其拉出吊走;3.2)拆卸过渡齿轮,清洗检查各法兰接合面,装入新的过渡齿轮;3.3)将新的轴承放置于滑道小车上,再用1台2t手拉葫芦将其拉入,用3台10t机械千斤顶顶起,轴承穿入所有的连接螺栓;恢复北侧拆离的支柱;对所有的螺栓初步紧固;步骤4:上部设备回落就位,回落过程按以下要求操作:4.1)、4台50t机械千斤顶和保护支柱,每次必须留20mm空间距离。5、6号200t液压顶和保护支柱每次必须留15mm空间距离;4.2)、1、2液压千斤顶是以10mm为单位回落,两个保护支柱顶部必须保证只有10mm空间距离;所述空间距离用斜垫铁和钢板调整;4.3)、回落过程主要是4台200t主液压顶工作。所以控制好下降量很重要,同一侧的千斤顶操作时做到动作同步,防止设备中心出现较大的偏移。及时修正底座法兰口到刹车盘法兰口的距离,重复上述步骤。4.4)、当达到底座法兰口100mm高度时法兰表面清理,穿好能穿上的连接螺栓;如果轴承中心与底座的中心有偏移,可将底座法兰面与轴承之间垫上等高的8组钢板,钢板之间涂上干油,整个回转体落于8组钢板上。在底座内部直径方向,架设一个50t机械千斤顶,根据实际方向调整螺栓孔穿好全部螺栓;200t主液压顶微微顶升,撤出8组钢板,继续回落,直到完全回落到位。步骤5:已拆设备恢复5.1)根据螺栓力矩要求紧固所有的两层螺栓;5.2)回装刹车盘、传动减速机,齿轮加润滑脂,对传动装置加油,恢复保护罩,恢复液压系统;5.3)拆除包臂升降架上部焊接的20#槽钢,拆除各支柱。本发明产生的有益效果是:(1)节省施工周期:不需要制作专用吊具,节省材料采购、吊具的制作周期,无需使用钢水接受跨行车,不受行车使用调配的限制。(2)节约投资:无需购买吊具制作材料及下料制作,节省人工费及材料费用,不使用双机(汽车吊和行车)抬吊,节省了机械台班费用。(3)适用范围广:由于省时、省力和节约投资,因此可适用于大包回转台检修、更换,并且不影响现有生产。附图说明下面将结合附图及实施例对本发明作进一步说明,附图中:图1是本发明实施例的顶升支架布置图;图2是本发明实施例的轴承顶升的布置图;图3是本发明实施例的轴承更换的布置图;图中:1-1号主液压千斤顶,2-2号主液压千斤顶,3-3号主液压千斤顶,4-4号主液压千斤顶,5-辅助液压千斤顶,6-辅助液压千斤顶,7-H型钢,8-机械千斤顶,9-底座,10-上部设备,11-大包回转台叉臂,12-滑道,13-滑道小车,14-机械千斤顶,15-手拉葫芦。具体实施方式为了使本发明的目的、技术方案及优点更加清楚明白,以下结合附图及实施例,对本发明进行进一步详细说明。应当理解,此处所描述的具体实施例仅用以解释本发明,并不用于限定本发明。如图1和图2所示,1、一种大包回转台轴承更换的方法,包括以下步骤:步骤1:关联设备的保护性拆除及辅助支柱的准备:1.1)拆卸刹车盘、齿护罩和传动电机减速机,对干涉支柱安装位置的水平护罩进行切割;1.2)根据需要底座内的滑环和旋转给油器拆卸,限位的拆卸,轴承和底座的联接螺栓部分拆卸;1.3)定位安装顶升支柱:安装的顶升支柱共八件,其中与浇铸线垂直的方向布置四件主液压千斤顶,分别为1号主液压千斤顶至4号主液压千斤顶,型号为200t;沿浇铸方向的支柱设置两个辅助千斤顶,分别为5号液压千斤顶和6号液压千斤顶,作为辅助支撑;在大包回转台叉臂11下方各设置一组支柱,为稳定性支架,每组支架有两个顶升点,共设置4台50t机械千斤顶,两个顶升点之间用槽钢连接;1.4)为主液压千斤顶设置扁担梁:在200t液压千斤顶受顶部位,即包臂升降油缸座处,并排焊接放置两根预先设计制作250×250×2500mmH型钢7,作为同一侧两件主液压千斤顶的扁担梁。1.5)防止包臂升降:将包臂升降架上部用20#槽钢焊死,4台50t机械千斤顶支柱8起到扶稳作用;步骤2:大包回转台上部设备顶升2.1)检查准备:对1~4号4台200t主液压千斤顶(1、2、3、4),2台辅助液压千斤顶(5、6)设置完毕后,进行检查确认,叉臂下方设置的4台50t机械千斤顶8就位,每个保护柱头垫上垫板;所有顶受力,保护柱顶塞入垫板外加一对斜垫板;检查支柱承载力整体稳定无异常;2.2)拆松齿轮与上回转体的联接螺帽:拆卸轴承底座与更换轴承的连接螺栓,其中留下8条螺栓不卸螺帽,以便上部回转体起升时带起轴承;2.3)进行大包回转台上部设备顶升:顶升顺序和要求:给4台200t主液压顶(1、2、3、4)和2台副液压顶(5、6)编号,主液压顶:西侧为1、2号主液压顶1、2,东侧3、4号主液压顶3、4;副液压顶:南侧5号主液压顶5,北侧6号主液压顶6;2.4)首先启动1、2号主千斤顶,顶升高度以5mm~10mm为一个步进单位;每顶升一步,在保护支柱同时加入垫板楔紧;随后启动3、4号主千斤顶,顶升高度以5mm~10mm为一个步进单位。每顶升一步,在保护支柱同时加入垫板楔紧,用尺控制顶升量。5、6号辅助支柱的顶升方式与1、2、3、4号千斤顶相同的方式操作顶升;4台叉臂下方的50t机械千斤顶8紧跟随上升,起到扶稳作用;2.5)修正步骤:以上步骤2.2)至2.4)为一个循环操作;进行了三个循环操作后使用尺测量底座法兰与刹车盘法兰之间四个垂直方向距离,应当保持一致没有大的偏差,如出现大的偏差应即时修正,直到顶升到所需的高度;步骤3:如图3所示,大包回转台轴承更换步骤:3.1)顶升到预先设定的高度后,全面检查顶架整体结构的稳定性,如无异常拆离北侧的辅助支柱6;用浇铸跨行车将预先设计制作的滑道12吊入底座法兰口上,用3台10t机械千斤顶14顶住轴承,然后拆卸先前预留的8条螺栓,操作机械千斤顶14将轴承回落到滑道小车13上;最后使用1台2t手拉葫芦15将其拉出吊走;3.2)拆卸过渡齿轮,清洗检查各法兰接合面,装入新的过渡齿轮;3.3)将新的轴承放置于滑道小车13上,再用1台2t手拉葫芦将其拉入,用3台10t机械千斤顶顶起,轴承穿入所有的连接螺栓;恢复北侧拆离的支柱;对所有的螺栓初步紧固;步骤4:上部设备10回落就位,回落过程按以下要求操作:4.1)、4台50t机械千斤顶和保护支柱8,每次必须留20mm空间距离。5、6号200t液压顶和保护支柱每次必须留15mm空间距离。4.2)、1、2液压千斤顶是以10mm为单位回落,两个保护支柱顶部必须保证只有10mm空间距离。用斜垫铁和钢板调整(控制了下降的量)4.3)、回落过程主要是4台200t主液压顶(1、2、3、4)工作。所以控制好下降量很重要,同一侧的千斤顶操作时做到动作同步,防止设备中心出现较大的偏移。及时修正底座法兰口到刹车盘法兰口的距离,重复上述步骤。4.4)、当达到底座法兰口100mm高度时法兰表面清理,穿好能穿上的螺栓。如果轴承中心与底座9的中心有偏移,可将底座法兰面与轴承之间垫上等高的8组钢板,钢板之间涂上干油,整个回转体落于8组钢板上。在底座内部直径方向,架设一个50t机械千斤顶,根据实际方向调整螺栓孔穿好全部螺栓。200t主液压顶微微顶升,撤出8组钢板,继续回落,直到完全回落到位。步骤5:已拆设备恢复:5.1)根据螺栓力矩要求紧固所有的两层螺栓。5.2)回装刹车盘、传动减速机,齿轮加润滑脂,对传动装置加油,恢复保护罩,恢复液压系统。5.3)拆除包臂升降架上部焊接的20#槽钢,拆除各支柱。应当理解的是,对本领域普通技术人员来说,可以根据上述说明加以改进或变换,而所有这些改进和变换都应属于本发明所附权利要求的保护范围。