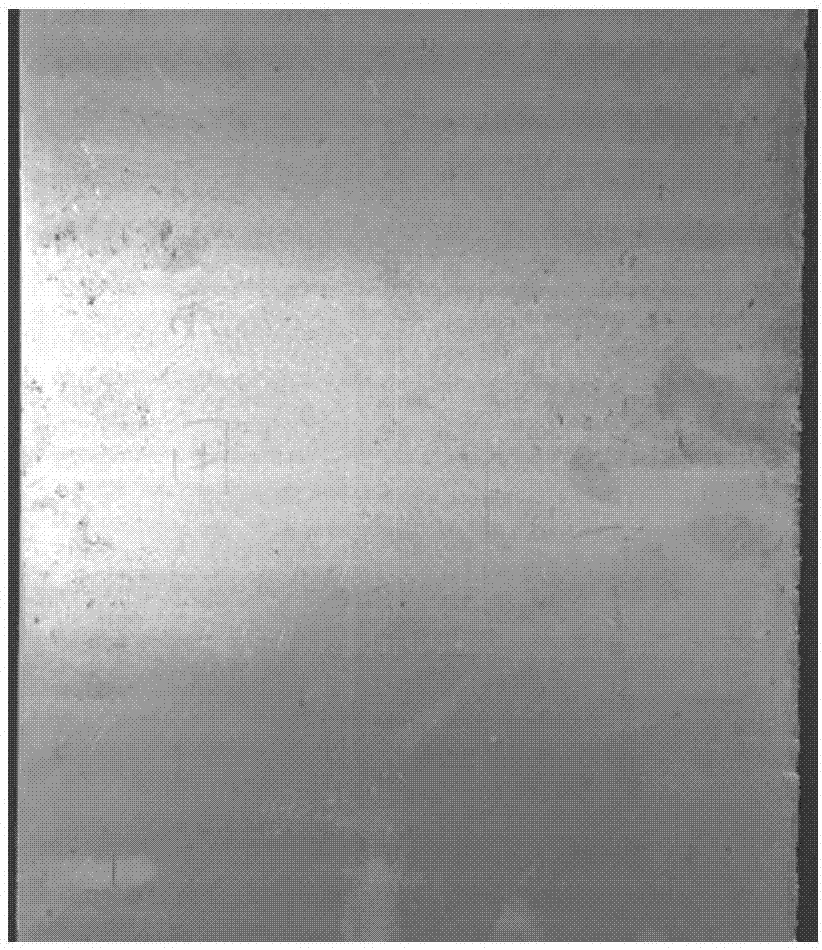
本发明涉及一种合金板、卷的制造方法,尤其涉及一种制造镁合金板、卷的方法。
背景技术:
镁及其合金是最轻的金属结构材料,密度仅为钢的1/4,铝的2/3,镁及其合金有比强度、比刚度高、电磁屏蔽性能优良、散热性好、减震性能好等优点。由于纯镁的强度低,铸态在室温下的拉伸屈服强度仅有21mpa,而合金化可有效提高其力学性能,因此实际应用的都是镁合金。镁合金板、卷(卷是为了便于贮存和运输)在3c产品外壳、印刷蚀刻板、led灯罩、镁电池等领域有广泛的应用前景。例如,一些品牌的平板电脑外壳就是采用镁合金制造;欧美国家的印刷用蚀刻板大多是镁合金板;镁合金板还被制作镁电池,作为应急灯、鱼雷的电源。目前,国内外都研究开发高质量镁合金板材尤其是镁合金薄板的制备工艺。金属板、卷如钢、铝的板、卷,大都是采用轧制的方法生产,镁板、卷也不例外。对于镁板、卷,目前的制备方法是:先将镁合金铸造成棒材,然后将棒材挤压成较厚的板,随后将挤压得到的厚板通过多道次轧制逐步减小板材厚度到设定值,最终切成片或者卷曲成卷;另外一种方法是采用半连续铸造得到较厚的镁合金扁锭,表面扒皮后直接进行多道次轧制,使厚度逐步减小至设定值。但是,无论采用上述哪种工艺,在轧制过程中镁板都极易发生边裂,导致得到的镁板、卷质量低,实际成品宽幅减小,材料的使用率低。导致镁合金在轧制过程中容易产生边裂的主要原因有三个:一是.镁的晶体结构为密排六方结构(即hcp结构),滑移系数量远少于钢铁、铝等金属,塑性变形能力差。二是,挤压及轧制会导致镁板形成很强的基面织构,即晶粒的基面(0001)逐渐平行于板面。沿(0001)基面的变形容易,而垂直于基面方向变形非常困难。轧制时主要是板材厚度方向受压,变形方向垂直于(0001)面,所以(0001)基面平行于板面会极度弱化板材沿厚度方向的变形能力,这也会提高板材边裂的倾向。三是,晶粒粗大。虽然zr是镁基体非常有效的晶粒细化剂,但是无法用于细化含有al、mn等元素的镁合金,因为zr会与al、mn等元素反应形成稳定的金属间化合物,失去细化效果。常用的商业镁合金如az31(mg-3al-1zn-0.2mn,质量百分比)含有al或mn元素,使得铸锭无法采用zr进行晶粒细化,目前还未有有效的晶粒细化剂,导致铸造锭晶粒粗大,即使挤压成板后,晶粒仍然粗细不均,有很多大晶粒存在。此外,张力也是影响镁合金轧制板材质量的重要因素。因为在轧制时镁板温度越高,其强度越低,若不对板材施加张力,板材极易弯曲,因此需要在轧制变形过程中对镁板(带)施加张力。但是由于镁板材强度较低,若施加的张力过大,板材会被拉变形、甚至被拉断。因此,在镁板轧制过程中,需要精确控制张力的范围。目前的镁板的生产方法,需要多道次轧制时,是在每道次结束后,将镁板重新回炉加热到设定温度到设定温度后再进行轧制,未对镁板施加张力。这种单机架反复咬入的无张力轧制方式不可避免地导致厚度方向的尺寸精度低,板材的厚度不均、板材不平整、易翘曲、易产生波浪纹路。近年来,一些消除镁合金板材、卷边裂的方法被陆续开发、报道。例如:公开号为cn102000695a,公开日为2011年4月6日,名称为“金属板材的轧制方法”的中国专利文献公开了一种金属板材的轧制方法。在该专利文献所公开技术方案中,描述了一种通过沿板材横向施加压应力或沿板材法向的拉应力的预处理,在200-400℃时使板材沿横向产生1-20%的塑性变形来改变板材的织构取向,从而减弱或者消除了基面织构,提高板材的轧制成形性,减少板材在轧制过程中的边裂,提高了轧制工作效率;在立辊处理后,该技术方案采用的单机架多道次反复咬入的往复无张力轧制方式生产镁板。然而,该专利文献所公开的技术方案存在如下缺点:1)该技术方案对横向微小变形处理是否能够改善边裂,以及横向变形后,在200-400℃以外的温度进行不同时间的预处理能否改善边裂情况未做描述;2)由于该专利文献中的轧辊的温度要求在200-400℃以内,温度高,导致其轧辊的损耗大;3)由于该专利文献中的技术方案采用反复咬入方式,因而,将不可避免地导致厚度方向的尺寸精度低,板材的厚度不均;4)由于该专利文献中的技术方案采用无张力轧制,而无张力轧制的结果容易导致板形不良,板材不平整、易翘曲、有波浪;5)由于该专利文献采用单机架反复轧制的方式,由于板带越轧越薄,因此其需要的产线就会很长;6)由于采用反复咬入,因而,轧机频繁启停导致生产效率低。此外,该专利文献并未记载如何获得镁板来料问题。公开号为cn104889160a,公开日为2015年9月9日,名称为“一种宽幅镁合金厚板边部多向预变形轧制方法与装置”的中国专利文献公开了一种宽幅镁合金厚板边部多向预变形轧制方向与装置,采用在板材宽度和厚度方向同步施加压应力的协调轧制方法。该专利文献所公开的设备由四辊轧机、轧前立辊/斜辊组合装置、轧后斜辊/立辊组合装置组合。在该专利文献所公开的技术方案中,通过对镁板边部施加多辊多向的压力变形,从而限制轧制过程中镁板宽展,获得良好板形,减小边部裂纹产生及扩展,提高镁合金板材的成材率。然而,该技术方案工艺复杂,需要经过多道交替轧制,效率低。公开号为cn105057364a,公开日为2015年11月18日,名称为“一种镁合金板材轧制边裂预判及控制方法”的中国专利文献公开了一种镁合金板材轧制边裂预判及控制方法。在该专利文献所公开的技术方案中记载了镁合金板材轧制时发生边裂的预判标准,根据标准选择合适的压下量。对于轧制时工艺方法,以及如何通过工艺改进消除边裂,该专利文献并没有详细披露。鉴于镁合金板、卷的用途及广泛应用前景,以及目前已有的镁合金轧制易产生边裂、板形差、生产效率低、板材尺寸精度低的问题,期望获得一种制造镁合金板、卷的方法,采用该方法所制得的镁合金板、卷质量高,板形好,该方法工艺简单,工作效率高。技术实现要素:本发明的目的之一在于提供一种制造高质量镁合金板、卷的方法,采用该方法所制备的高质量镁合金板、卷厚度均匀,板形平整,不易产生翘曲、波浪纹路,满足生产应用需要。此外,该方法工艺简单、轧制效率高,所获得的高质量镁合金板、卷板材利用率高。为了实现上述目的,本发明提出了一种制造高质量镁合金板、卷的方法,包括步骤:(1)立辊微侧压:采用立辊在室温至500℃的范围内向镁合金来料在宽度方向上的边部施加侧压力,以使宽度方向上的两侧中的每一侧的边部均产生0.5-8.0mm的横向挤压变形量;(2)退火:退火温度为200-500℃,保温时间为0.1-60min;(3)采用多机架连续轧机进行连续轧制:控制轧制速度为5-50m/min,在整个轧制过程中对镁合金轧制板施加5-50mpa的张力;(4)剪切制成镁合金板,或者剪切得到镁合金板并将镁合金板卷取成镁合金卷。在本发明所述的制造高质量镁合金板、卷的方法中,在轧制前,采用立辊微侧压对轧制用的镁合金来料进行处理。与现有技术不同的是,立辊微侧压对镁合金来料宽度方向上的两侧中的每一侧的边部均产生0.5-8.0mm的横向挤压变形量,横向挤压变形量与镁合金来料的宽幅无关。其中,立辊微侧压采用快速压下的方法,变形主要发生在镁合金来料边部,且变形量小,不影响镁合金来料的整体平整度,轧制前不需要对镁合金来料进行平整加工例如铣面,因而,使得本发明所述的方法操作简单,效率高。立辊微侧压后使得镁合金来料边部的晶粒取向发生变化,降低基面织构强度,提高了其塑性变形能力。此外,立辊微侧压后,由于镁合金来料局部变形量大,在后续退火步骤中,晶粒发生再结晶,晶粒细化。由于晶粒细化会明显提高材料的塑性变形能力,因此,立辊微侧压后对镁合金来料进行退火处理,以进一步提高其边部的塑性变形能力。然而,由于退火工艺会影响再结晶的程度和晶粒尺寸,因此,对退火温度及其保温时间进行了进一步的限定。当退火温度低于200℃或保温时间低于0.1min时,晶粒再结晶不完全,大部分区域不能发生再结晶;当退火温度高于500℃或保温时间超过60min时,再结晶后晶粒会进一步粗化,晶粒重新长大,也不利于轧制变形,并且能耗高。因此,在本发明所述的技术方案中控制退火温度在200~500℃,保温时间在0.1~60min,以保证镁合金来料边部充分再结晶、同时未发生晶粒粗化,以提高边部的塑性变形能力。此外,本发明所述的技术方案选择立辊微侧压后的退火处理温度为200-500℃,保温时间为0.1-60min,是因为退火温度和保温时间相互影响,具体来说退火温度低,需要长时间保温才能时边部的晶粒充分再结晶;退火温度高时,只需保温较短时间即可使边部充分再结晶,且保温时间不宜过长,否则会使边部晶粒粗大。此外,为了避免单机架多道次反复咬入的往复无张力轧制的方式导致厚度方向的尺寸精度低、板材的厚度不均、板材易翘曲、有波浪纹路等缺点,在本发明所述的技术方案中采用多机架连续轧制的工艺轧制镁合金板、卷,因而,本发明所述的技术方案无需反复咬入。在轧制过程中,由于镁合金的室温塑性低,通常需要加热到200℃以上才能进行轧制。目前常用的轧制速度小于5m/min。发明人经过大量研究发现,采用快速轧制的方法,也就是控制轧制速度在5-50m/min有利于提高轧制效率;此外,采用快速轧制的方法制备的镁合金板的晶粒尺寸更加细小。因而,本发明所述的技术方案中采用快速轧制以有利于提高轧制效率和镁合金板的力学性能。在本发明所述的方法的步骤(3)中,在整个轧制过程中对镁合金轧制板施加5-50mpa的张力。为了保证镁合金轧制板的厚度均匀、平整,因而,在轧制过程中对镁合金轧制板施加张力。张力过小,则平整效果不佳;张力过大,则容易将镁合金轧制板拉断。此外,施加张力的值还与镁合金轧制板的截面、温度有关。因此,综合上述因素,本发明所述的方法在整个轧制过程中对镁合金轧制板的张力控制在5-50mpa。在本发明所述的方法的步骤(4)中,根据各实施方式的具体情况,按照需求,将镁合金板切割成所需要的尺寸,或者直接用卷取机将镁合金板卷曲成镁合金卷。进一步地,在本发明所述的方法中,在所述步骤(3)和步骤(4)之间还具有步骤(3a)轧后退火:退火温度为150-400℃,保温时间为0.1-60min。步骤(3a)的轧后退火过程使得所述的镁合金板材强度下降,但有利于提高镁合金板材的塑性。根据各实施例的具体情况,对镁合金板进行轧后退火或对镁合金卷进行轧后处理包括辅助加热、吹风冷却,控制镁合金卷的温度在100-400℃,处理时间为卷取所需时间。进一步地,在本发明所述的方法中,在所述步骤(3)中,加热至200-500℃进行轧制,轧制压下量为10-70%。在本发明所述的技术方案中,提高每道次轧制的压下量从而提高轧制效率。进一步地,在本发明所述的方法中,在所述步骤(3)中,采用加热装置使轧辊的温度保持在100-300℃。由于镁合金在轧制过程中散热快,因而,轧制时将轧辊加热到100-300℃,以降低镁合金在轧制过程中的散热速度。进一步地,在本发明所述的方法中,在所述步骤(3)中,在各轧制道次的至少其中之一之后对镁合金轧制板进行立辊微侧压,并在立辊微侧压步骤后进行立辊微侧压后退火,其中立辊微侧压是指采用立辊在室温至500℃的范围内向镁合金轧制板在宽度方向上的边部施加侧压力,以使宽度方向上的两侧中的每一侧的边部均产生0.5-8.0mm的横向挤压变形量,所述立辊微侧压后退火的退火温度为200-500℃,保温时间0.1-60min。进一步地,在本发明所述的方法中,在所述步骤(3)中,在多机架连续轧机的各机架之间对镁合金轧制板进行在线补热,以维持轧制温度。这是因为:轧制过程中,(0001)基面会逐渐平行于基面,降低镁合金沿厚度方向的变形能力,因此,需根据需求在各轧制道次之间再次进行立辊微侧压。在各机架之间对镁合金轧制板进行在线补热。进一步地,在本发明所述的方法中,在所述步骤(4)中,卷取温度为100-400℃。进一步地,在本发明所述的方法中,所述镁合金来料选自:镁合金粗轧板、挤压板、铸造扁锭或经过开卷的镁合金卷。相较于现有技术,本发明采用微小的绝对压下量,即针对所有宽幅的板,横向挤压变形量为0.5-8.0mm,因而,使得其变形量小,不会导致板材发生剧烈变形从而影响后续轧制。此外,由于压下量与镁合金来料的宽幅无关,使得本发明所述的方法操作简单,通用性强,可消除或大幅度减少镁合金板材轧制过程中容易产生的边裂,提高板材的有效利用率。此外,本发明所述的制造高质量镁合金板、卷的方法优化了立辊微侧压后的热处理工艺,采用多机架连续轧机进行轧制,有效提高了生产效率,并且避免了反复咬入导致的尺寸精度降低、成品厚度不均的问题。另外,本发明所述的高质量镁合金板、卷的方法轧制效率高,所得到的高质量镁合金板、卷厚度均匀,板形平整,不易产生翘曲、波浪纹路,满足生产应用需要。附图说明图1为实施例1的经立辊微侧压的az31b粗轧板轧制后的板材形貌图。图2为实施例2的经立辊微侧压的az31b板卷轧制后的板材形貌图。图3为对比例1的未经立辊微侧压的az31b粗轧板轧制后的板材形貌图。图4为实施例1的立辊微侧压处理前的az31b粗轧板的基面织构图。图5为实施例1的立辊微侧压处理后的az31b粗轧板的基面织构图。图6为实施例2的立辊微侧压处理后的az31b板卷的基面织构图。图7为实施例3的立辊微侧压处理前的az31b铸造扁锭边部的金相组织照片。图8为实施例3的经立辊微侧压处理后随后500℃保温10min后的az31b铸造扁锭边部的金相组织照片。图9为实施例4的立辊微侧压处理前的镁合金挤压板的基面织构图。图10为实施例4的立辊微侧压处理后的镁合金挤压板的基面织构图。图11为实施例4的轧制后的高质量镁合金板的金相组织照片。图12为对比例7的轧制后的常规镁合金板的金相组织照片。图13为实施例4的镁合金挤压板轧制后的板材形貌图。图14为对比例8的镁合金挤压板轧制后的板材形貌图。具体实施方式下面将结合说明书附图和具体的实施例对本发明所述的制造高质量镁合金板、卷的方法做进一步的解释和说明,然而该解释和说明并不对本发明的技术方案构成不当限定。实施例1-6和对比例1-8实施例1-6的高质量镁合金板、卷采用以下步骤制得:(1)立辊微侧压:采用立辊在室温至500℃的范围内向镁合金来料在宽度方向上的边部施加侧压力,以使宽度方向上的两侧中的每一侧的边部均产生0.5-8.0mm的横向挤压变形量;(2)退火:退火温度为200-500℃,保温时间为0.1-60min;(3)采用多机架连续轧机进行连续轧制;(4)剪切制成镁合金板,或者剪切得到镁合金板并将镁合金板卷取成镁合金卷。上述实施例中所涉及的步骤中具体工艺参数参见表1。需要说明的是,实施例5和实施例6在步骤(3)还具有轧后退火,具体步骤为:实施例5将镁合金来料分切成镁片,镁片在退火温度200℃保温5min;实施例6采用卷取机将镁合金来料卷成镁卷,卷取过程中通过控制温度操作例如风冷、电阻加热将镁卷温度维持在100℃,卷取时间即为保温时间。在实施例3的步骤(3)中,采用四机架连续四道次轧制,每道次的压下量如表1所示;第一道次轧制前,为了让料顺利咬入到轧机中,将料的咬入端加工成楔形。每道次之间对镁合金板进行感应加热至500℃,进行重新立辊微侧压处理,横向挤压变形量为5mm,保温10min后进入下一道次。轧制过程中保持张力值为8mpa。在实施例4-6的步骤(3)中,采用四机架连续四道次轧制,每道次的压下量如表1所示;每道次之间对镁合金板进行感应加热,进行重新立辊微侧压处理、并保温,然后进入下一道次,温度和横向挤压变形量及保温时间等参数如表1所示。表1.注:表中“-”表示实施过程中没有该步骤,因而,也没有该步骤相对应的参数值。需要说明的是,为了与实施例作为对比,设计了与实施例1-6相对应的对比例1-6,其参数设置与实施例1-6均一一对应,所区别的是对比例1-6均为未采用立辊微侧压处理。另外,还为实施例4设计了对比例7和8,对比例7、8均未采用立辊微侧压处理、且其轧制速度为2m/min,此外,对比例8未采用微张力系统,也就说对比例8在多机架连续轧机过程中未施加5-50mpa的张力。将实施例4-6和对比例4-6进行厚度检测,检测结果显示,实施例4-6的所制得的镁合金板、卷厚度均匀性好,厚度范围为0.40-0.43mm,浮动范围0.03mm;对比例4-6所制得的常规镁合金板、卷的厚度范围为0.38-0.47mm,浮动范围0.09mm。由此可见,实施例4-6由于采用本发明所述的多机架连续轧制制备,因而制备所得的镁合金板材尺寸更加稳定。将实施例4-6和对比例4-6沿轧制方向进行室温力学性能测试,测试结果列于表2。表2.屈服强度(mpa)抗拉强度(mpa)延展率(%)实施例428434215实施例524130722实施例626732118对比例423531915对比例521430215对比例621923013由表2可以看出,实施例4-6的屈服强度、抗拉强度以及延伸率总体显著优于各对比例,由此可以看出,发明所述方法可以制备出更高质量和拉伸性能的镁合金板卷的。图1为实施例1的经立辊微侧压的az31b粗轧板轧制后的板材形貌图。图2为实施例2的经立辊微侧压的az31b板卷轧制后的板材形貌图。图3为对比例1的未经立辊微侧压的az31b粗轧板轧制后的板材形貌图。对比图1、图2和图3可以看出,图1和图2中的板材边缘未出现边裂或只有微小的边裂,而图3中对比例1的az31b粗轧板的板材边缘边裂明显,其它实施例与对比例也具有相同情况,即实施例的板材边缘未出现边裂或只有微小的边裂,而对比例的板材边缘边裂明显。由此可以说明,立辊微侧压大大改善了边部的边裂情况。图4为实施例1的立辊微侧压处理前的az31b粗轧板的基面织构图。图5为实施例1的立辊微侧压处理后的az31b粗轧板的基面织构图。图6为实施例2的立辊微侧压处理后的az31b板卷的基面织构图。由图4可以看出,立辊微侧压处理前的az31b粗轧板板材边部晶粒的(0001)面主要平行于板面,织构很强。对比图4、图5和图6可以看出,在立辊微侧压处理后,织构强度明显减弱,很多晶粒的(0001)面偏离了板面(参见图5和图6)。由此可以看出,在轧制过程中由于立辊微侧压处理使得边部的晶粒更容易沿着厚度方向发生变形,沿厚度方向的塑性变形能力提高。图4、图5和图6中,rd是指轧制方向,td是指轧件的横向方向。图7为实施例3的立辊微侧压处理前的az31b铸造扁锭边部的金相组织照片。如图7所示,立辊微侧压处理前的az31b铸造扁锭边部晶粒尺寸粗大,晶粒尺寸大多在100μm以上,只有很少量的小晶粒存在。图8为实施例3的经立辊微侧压处理后随后500℃保温10min后的az31b铸造扁锭边部的金相组织照片。如图8所示,经立辊微侧压处理后随后500℃保温10min后的az31b铸造扁锭边部由很多细小的晶粒和少量的大晶粒组成,小晶粒占总面积的60%左右,小晶粒的尺寸在1~15μm。这是因为在立辊微侧压处理后,晶粒中有大量的畸变能,在高温下会发生再结晶,形成细小的晶粒。细晶强化是提高金属材料强度、塑性的有效途径。因此,在立辊微侧压、保温后,az31b铸造扁锭边部晶粒明显细化,使得实施例3的塑性变形能力提高,在采用大压下量轧制时,边部未出现裂纹。图9为实施例4的立辊微侧压处理前的镁合金挤压板的基面织构图。由图9可以看出,立辊微侧压处理前的mg-1.1zn-0.36ca-0.28mn挤压板边部晶粒的(0001)面主要垂直于横向(td方向),织构很强。图10为实施例4的立辊微侧压处理后的镁合金挤压板的基面织构图。如图10所示,经立辊微侧压处理后,晶粒的(0001)面主要垂直于轧制方向(rd方向)。当晶粒的(0001)面垂直于轧制方向(rd方向)时,较其垂直于横向(td方向)时,在轧制过程中开裂倾向更小。因此,对挤压板进行立辊微侧压处理后,其边部在轧制过程中变形能力也提高,沿厚度方向的塑性变形能力提高。图11为实施例4的轧制后的高质量镁合金板的金相组织照片。图12为对比例7的轧制后的常规镁合金板的金相组织照片。对比图11和图12可以看出,由于实施例4采用轧制速度为10m/min,而对比例采用轧制速度为2m/min,因而,实施例4的高质量镁合金板的晶粒尺寸较对比例7的常规镁合金板细小,因而,实施例4的力学性能较对比例7更强。图13为实施例4的镁合金挤压板轧制后的板材形貌图。图14为对比例8的镁合金挤压板轧制后的板材形貌图。对比图13和图14可以看出,实施例4由于施加张力,因而板材平整,而对比例8未施加张力,因而其板材上有波浪纹路,不平整。由此可看出,张力能够大幅度改善板材板形。需要注意的是,以上列举的仅为本发明的具体实施例,显然本发明不限于以上实施例,随之有着许多的类似变化。本领域的技术人员如果从本发明公开的内容直接导出或联想到的所有变形,均应属于本发明的保护范围。当前第1页12