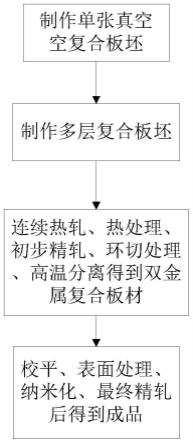
1.本发明属于复合板材制备技术领域,涉及一种层状结构复合板材的生产制备方法。
背景技术:2.随着工业生产、能源开发、工程建设等相关技术领域的飞速发展和进步,高性能金属材料的用量和消耗与日俱增,若使用单一的高性能材料将造成巨大的材料消耗和浪费,因此对节能环保、性能可靠的新型先进复合材料的需求就显得尤为迫切。双金属或多金属层状结构复合材料是将强度、熔点、热膨胀系数、耐腐蚀性、耐磨性、超导性等差异极为悬殊的多种金属采用特殊技术冶金结合在一起形成,集不同材料优点于一身,可充分发挥不同材料特性,可极大节约稀贵金属消耗和浪费,同时可最大程度降低工程建设成本和特种装备制造成本,还可以提高设备使用寿命,在各领域有广阔应用前景和市场。例如纯钛或钛合金/碳钢层状结构复合板材、不锈钢/碳钢层状结构复合板材等具有巨大成本优势,在环保、经济和实用性方面成效显著,其卓越的耐腐蚀性能在海洋工程及舰船领域、航空航天领域、军工领域、化工领域等将发挥重要作用。
3.目前较为常用的复合板材复合技术有爆炸焊、爆炸焊+热轧、热轧等方式,但均存在各自的缺点和不足,例如,爆炸焊容易引起复合界面硬度超标,且具有较大的形变应力,极易引起应力腐蚀开裂而降低复合板材性能;热轧复合技术虽然不会存在硬度超标的问题,但会因为材料之间物理、化学特性的巨大差异以及界面气泡、缺陷等问题使得结合界面之间存在未结合区即结合率很难达到100%,影响质量;而爆炸焊+热轧技术虽然能缓解界面硬度、应力腐蚀开裂、界面结合率等问题,但同时带来环境污染大、能源消耗大、生产效率低、质量不稳定等问题。
技术实现要素:4.本发明的目的是提供一种层状结构金属复合板材的生产制备方法,解决现有层状结构金属复合板材制备技术中存在的复合界面硬度超标、抗应力腐蚀开裂能力差、结合率偏低、生产效率不高的问题。
5.本发明所采用的技术方案是:
6.层状结构复合板材的生产制备方法,具体步骤为:
7.步骤1,制作单张复合板坯;
8.步骤2,采用单张复合板坯制作多层复合板坯;
9.步骤3,对多层复合板坯依次进行连续热轧、热处理、初步精轧、环切处理、对称分离得到双金属复合板材;
10.步骤4,对双金属复合板材依次进行校平、表面处理、纳米化、最终精轧后得到成品。
11.步骤1包括:
12.步骤1.1,基材板坯两端面对称位置钻小孔;
13.步骤1.2,基材板坯、复材板坯表面精细化处理并叠层放置;其中基材板坯为q235、q345、x52、x60、x65、x70、x80、x90或x100碳素结构钢中的一种、压力容器钢或高强韧性管线钢,复材板坯使用304、304l、316、316l、n08825、n06625奥氏体不锈钢的一种;
14.步骤1.3,采用机械式压力机均匀作用于叠层复合板坯上,压力≥50吨;
15.步骤1.4,采用熔化极气体保护焊对叠层坯料复合界面外围实施周向封焊;
16.步骤1.5,通过预留小孔抽真空管路进行层间抽真空同时增大压力机压力≥60吨并保持时间≥10min。
17.步骤2中的多层复合板坯为成对真空复合板坯或组合式叠层复合板坯,其中成对真空复合板坯的制作方式为:
18.步骤2.1,将两块规格尺寸相同、基/复材匹配相同的真空复合板坯按照复层在里基层在外的方式叠放在一起,并在两复层之间整面铺设专用耐高温薄膜;
19.步骤2.2,采用机械式压力机均匀作用于叠层复合板坯上,压力≥60吨;
20.步骤2.3,采用熔化极气体保护焊将叠层组合好的两块真空复合板坯在界面处周向封焊,将中间的两复层板坯料完全包裹在里面,待封焊完毕制成一副成对真空复合板坯;
21.若将制作好的一副成对真空复合板坯再两两组合中间界面用耐高温薄膜隔离,周向封焊后就可以制作得到一副拥有四张真空复合板坯的组合式叠层复合板坯。
22.步骤3包括:
23.步骤3.1,连续热轧:经过连续控热、控轧,使得复合板坯在长、宽、厚三个方向发生不同程度变形,实现复层与基层的复合,界面间结合率≥98%,单个不结合区尺寸≤20mm2,在单张复合板壁厚尺寸接近目标规格尺寸(总厚度误差≤3.0mm);
24.步骤3.2,热处理,将连续控热、控轧后的复合板整体在850~900℃的环境中进行热处理,持续保温20~30min,确保基、复层的冶金结合,剪切强度≥260mpa。
25.步骤3.3,初步精轧,采用在线中低温连续轧制对复合板厚度尺寸进行初始精度控制,使总厚度误差≤2.0mm;
26.步骤3.4,环切处理,采用高能电子束沿着距离边部200mm位置处环向切割;
27.步骤3.5,对称分离,从耐高温薄膜处分离开得到双金属复合板材。
28.步骤4包括:
29.步骤4.1,校平,采用中低温连续辊压校平法对双金属复合板材进行校平;温度《300℃;
30.步骤4.2,表面处理,外表面进行去毛刺、去杂物处理同时进行外表面研磨,表面粗糙度要求达到10级,复层壁厚误差≤0.5mm;
31.步骤4.3,纳米化,采用激光冲击强化技术进行基层材料外表面纳米化处理,表层纳米晶层深度≤0.5mm,基层壁厚误差≤0.5mm。
32.步骤4.4,最终精轧,采用在线连续冷轧对复合板规格尺寸进行最终精度控制,使得复合板总壁厚达到产品壁厚规格要求,总壁厚误差《0.1mm。
33.本发明的有益效果是:
34.本发明提供了一种层状结构复合板材的生产制备方法,该技术方法可靠,具有很强的实用性,本发明中所提出的层状结构复合板生产制备步骤和具体工序均基于层状结构
复合板材的高质量生产和高效率生产,确保层状结构复合板材具有优良的综合力学性能,耐腐蚀性能或耐磨性能,以及抗疲劳破坏能力。
附图说明
35.图1为本发明的流程图;
36.图2为单张真空复合板坯的结构示意图;
37.图3为成对真空复合板坯的结构示意图;
38.图4为组合式叠层复合板坯的结构示意图。
39.图中,1.复层板坯,2.第一道封焊焊缝,3.基层板坯,4.抽真空管路,5.单张真空复合板坯,6.第二道封焊焊缝,7.成对真空复合板坯,8.第三道封焊焊缝。
具体实施方式
40.下面结合附图和具体实施方式对本发明进行详细说明。
41.本发明层状结构复合板材的生产制备方法,具体步骤为:
42.步骤1,制作单张复合板坯5,如图2;
43.步骤2,采用单张复合板坯5制作成对复合板坯7如图3或制作多层复合板坯如图4;
44.步骤3,对多层复合板坯图3或图4依次进行连续热轧、热处理、初步精轧、环切、对称分离得到双金属复合板材;
45.步骤4,对双金属复合板材依次进行校平、表面处理、纳米化、最终精轧后得到成品。
46.其中步骤1包括:
47.步骤1.1,基材板坯两端面对称位置钻小孔;
48.步骤1.2,基材板坯3和复材板坯1表面精细化处理后叠层放置;
49.其中基材板坯3为q235、q345、x52、x60、x65、x70、x80、x90或x100碳素结构钢中的一种、压力容器钢或高强韧性管线钢,复材板坯1使用304、304l、316、316l、n08825、n06625奥氏体不锈钢的一种。
50.步骤1.3,采用机械式压力机均匀作用于叠层复合板坯上,压力≥50吨;
51.步骤1.4,采用熔化极气体保护焊对叠层坯料复合界面外围实施周向封焊,形成第一道封焊焊缝2;
52.步骤1.5,通过预留小孔的抽真空管路4进行层间抽真空同时增大压力机压力≥60吨并保持时间≥10min。
53.其中步骤2中的多层复合板坯为成对真空复合板坯7或组合式叠层复合板坯,结构分别如图3和图4,其中成对真空复合板坯7的制作方式为:
54.步骤2.1,将两块规格尺寸相同、基/复材匹配相同的真空复合板坯按照复层在里基层在外的方式叠放在一起,并在两复层之间整面铺设专用耐高温薄膜;
55.步骤2.2,采用机械式压力机均匀作用于叠层复合板坯上,压力≥60吨;
56.步骤2.3,采用熔化极气体保护焊将组合好的两块真空复合板坯在界面处周向封焊,形成第二道封焊焊缝6,将中间的两复层板坯料完全包裹在里面,待封焊完毕制成一副成对真空复合板坯7;
57.若将制作好的一副成对真空复合板坯7再两两组合中间界面用耐高温薄膜隔离,周向封焊后就可以制作得到一副拥有四张真空复合板坯的组合式叠层复合板坯,此时两层真空复合板坯7留有第三道封焊焊缝8。
58.所述步骤3包括:
59.步骤3.1,连续热轧,经过连续控热、控轧,使得复合板坯在长、宽、厚三个方向发生不同程度变形,实现复层与基层的复合,界面间结合率≥98%,单个不结合区尺寸≤20mm2,单张复合板壁厚尺寸(包括基层厚度尺寸、复层厚度尺寸)接近目标规格尺寸且总厚度误差≤3.0mm;
60.步骤3.2,热处理,将连续控热、控轧后的复合板整体置于850~900℃的热处理房内,持续保温20~30min,确保基、复层的冶金结合,剪切强度≥260mpa,上述操作能够确保复合板性能(包括强度、塑性、韧性、硬度、抗腐蚀性、耐磨性等)达到相关标准要求。
61.步骤3.3,初步精轧,在200~240℃温度范围采用在线连续轧制对复合板厚度尺寸进行初始精度控制,使总厚度误差≤2.0mm;
62.步骤3.4,环切处理,采用高能电子束沿着距离边部200mm位置处环向切割;
63.步骤3.5,对称分离,从耐高温薄膜处分离开得到双金属复合板材。
64.所述步骤4包括:
65.步骤4.1,校平,在80~100℃温度范围采用连续辊压校平法对双金属复合板材进行校平;
66.步骤4.2,表面处理,外表面进行去毛刺、去杂物处理同时进行外表面研磨,表面粗糙度要求达到10级,复层304壁厚误差≤0.5mm;
67.步骤4.3,纳米化,采用激光冲击强化技术进行基层材料外表面纳米化处理,表层纳米晶层深度≤0.5mm,基层壁厚误差≤0.5mm。
68.步骤4.4,最终精轧,采用在线连续冷轧对复合板规格尺寸进行最终精度控制,使得复合板总厚达到产品壁厚规格要求,总壁厚误差《0.1mm。
69.实施例1
70.步骤1采用如下工序进行单张真空复合板坯的制作;
71.①
基层板坯3两端面对称位置钻小孔
→②
基层板坯3、复层板坯1表面精细化处理并叠层放置
→③
采用机械式压力机(压力=50吨)均匀作用于叠层复合板坯上
→④
采用熔化极气体保护焊对叠层坯料复合界面外围实施周向封焊
→⑤
通过小孔进行层间抽真空同时增大压力机压力到60吨并保持10min。
72.步骤2采用如下工序进行成对真空复合板坯7的制作;
73.①
将两块基/复材匹配为sus304/q345、规格尺寸为长
×
宽
×
厚=4000mm
×
1000mm
×
(4.2+28.8)mm的真空复合板坯按照sus304在里q345b在外的方式叠放在一起同时在两复层sus304之间整面铺设专用耐高温薄膜
→②
采用机械式压力机(压力=60吨)均匀作用于叠层复合板坯上
→③
采用熔化极气体保护焊将组合好的两块真空复合板坯在界面处周向封焊,将中间的两复层sus304板坯料完全包裹在里面。
74.步骤3,
75.步骤3.1在1100~1150℃温度范围采用连续热轧,经过连续控热、控轧,使得复合板坯在长、宽、厚三个方向发生不同程度变形,实现界面间结合率100%。在单张复合板壁厚
尺寸(包括基层厚度尺寸、复层厚度尺寸)接近目标规格尺寸长
×
宽
×
厚=10000mm
×
1650mm
×
(7+1)mm(总壁厚误差范围≤3.0mm)时结束连续热轧。
76.步骤3.2,将sus304/q345b复合板整体置于880℃的热处理房内,持续保温25min,实现基、复层的冶金结合,剪切强度≥260mpa,复合板屈服强度≥370mpa、抗拉强度≥400mpa、正反弯曲拉伸面无裂纹、-10℃下冲击吸收功≥60j、界面处维氏硬度≤240hv10、复层sus304抗腐蚀性能:
①
晶间腐蚀试验
②
氢致开裂试验
③
硫化物应力腐蚀试验
④
点蚀试验
⑤
氯化物应力腐蚀试验均满足相关标准要求。
77.步骤3.3在210℃下对sus304/q345复合板整体进行在线连续轧制,总壁厚尺寸初始精度控制误差≤2.0mm。
78.步骤3.4采用高能电子束沿着距离边部200mm位置处环向切割。
79.步骤3.5将环向切割后的叠层复合板从耐高温薄膜处分离开得到2副sus304/q345双金属复合板材。
80.步骤4
81.步骤4.1在85℃下采用连续辊压校平法对分离得到的sus304/q345双金属复合板材进行校平。
82.步骤4.2对复层材料sus304的外表面进行去毛刺、去杂物处理同时进行外表面研磨,表面粗糙度要求达到10级,复层sus304壁厚误差≤0.5mm;
83.步骤4.3采用激光冲击强化技术进行基层材料q345外表面纳米化处理,表层纳米晶层深度≤0.5mm,基层壁厚误差≤0.5mm。
84.步骤4.4采用在线连续冷轧对sus304/q345复合板厚度尺寸进行最终精度控制,使得复合板总厚达到产品壁厚规格要求,总误差《0.1mm。
85.对本实施例成品sus304/q345复合板材进行系列检验,具体如下:
86.复合界面间结合率≥98%、单个不结合区尺寸≤20mm2、剪切强度≥260mpa、屈服强度≥370mpa、抗拉强度≥400mpa、正反弯曲拉伸面无裂纹、-10℃下冲击吸收功≥60j、界面处维氏硬度≤240hv10、复层sus304抗腐蚀性能:
①
晶间腐蚀试验
②
氢致开裂试验
③
硫化物应力腐蚀试验
④
点蚀试验
⑤
氯化物应力腐蚀试验均满足相关标准要求。
87.表1本发明q345/2205复合板材的各种性能指标
88.