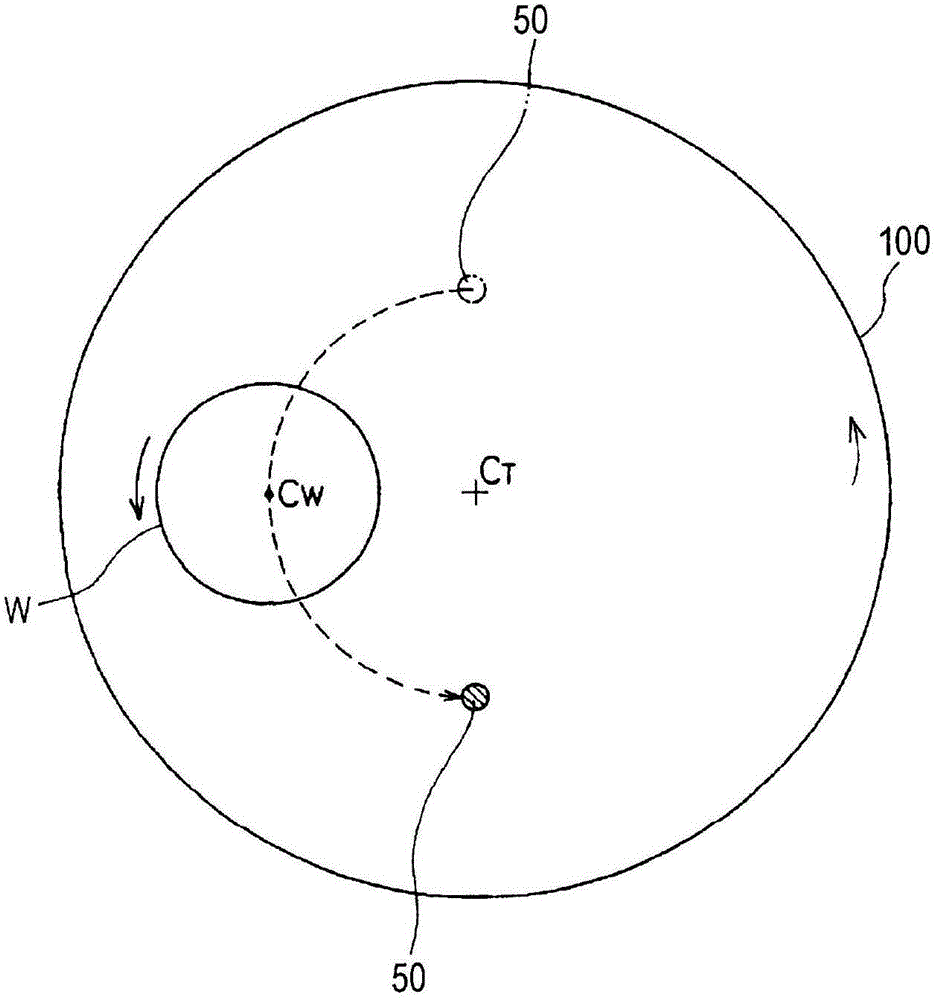
本发明涉及适宜检测形成于半导体晶片等基板表面的金属膜(或导电性膜)的涡电流传感器。此外,本发明涉及对形成于基板表面的金属膜(或导电性膜)通过涡电流传感器进行监视的同时研磨基板而除去金属膜(或导电性膜)的研磨方法及装置。
背景技术:近年来,伴随半导体设备的高集成化、高密度化,电路的配线越来越微细化,多层配线的层数也在增加。要在追求电路微细化的同时实现多层配线,由于会承袭下侧层的表面凹凸的同时阶差会变得更大,因此,随着配线层数的增加,形成薄膜时对于阶差形状的膜覆盖性(台阶覆盖率)变差。因此,为了进行多层配线,必须改善该台阶覆盖率,通过适当的工艺进行平坦化处理。此外,由于在光蚀刻微细化的同时焦点深度会变浅,因此,为了使得半导体设备的表面凹凸阶差在焦点深度以下,必须对半导体设备表面进行平坦化处理。因此,半导体设备的制造工序中,半导体设备表面的平坦化技术变得越来越重要。该平坦化技术中,最重要的技术是化学机械抛光(CMP(ChemicalMechanicalPolishing))。该化学机械抛光,是使用研磨装置,将含有二氧化硅(SiO2)等砂粒的研磨液提供给研磨垫等研磨面上的同时,令半导体晶片等基板在研磨面滑动接触而进行研磨。进行上述的多层配线时,预先在基板上的绝缘层(介电材料)形成规定样式的配线用沟槽,令基板浸渍在电镀液中,进行例如铜(Cu)的无电解或电解电镀,形成Cu层,然后通过CMP工艺,仅残留形成在配线用沟槽内的Cu层,选择性除去不要的部分。此时,研磨不充分、Cu层残留在绝缘层(氧化膜)上的话,电路的分离难以顺利进行,会引起短路。相反,过度研磨时,配线用沟槽内的Cu层与绝缘层同时被研磨的话,电路电阻会上升,整个半导体基板必须废弃,会造成巨大的损失。该情况不限于Cu层,在形成Al层等其他金属膜、对该金属膜通过CMP工艺研磨的情况下也相同。进行上述的CMP工艺的研磨装置,具备:具有由研磨垫构成的研磨面的研磨台、用于支承半导体晶片(基板)的被称为顶环或研磨头等的基板支承装置。使用此种研磨装置进行半导体晶片的研磨,通过基板支承装置支承半导体晶片的同时,将该半导体晶片对着研磨面以规定的压力按压而进行研磨,除去半导体晶片上的金属膜。研磨工序终了后,在半导体晶片内存在金属残膜的状态下进入下一工序的话,会引起短路等问题,因而半导体晶片变得无法使用。因此,研磨工序终了后,通过使晶片从研磨垫(研磨面)离开、检查有无金属残膜,从而可以进行残膜确认,但检査需要时间,因而存在晶片处理能力下降的问题。实施检査后,晶片上检测到残膜的情况下,必须进行再研磨,但晶片离开研磨垫后,要实施研磨,存在每片晶片的处理时间增加的问题。即,存在生产量下降的问题。本件申请人为了解决上述的金属残膜检査及检査后的再研磨所伴随的生产量下降的问题,先于日本特开2011-23579号中提出了,通过在研磨中检查半导体晶片等基板上是否有金属膜(或导电性膜)残膜而可以缩短检査时间、检测到残膜时直接实施追加研磨而可以缩短处理时间的研磨方法及研磨装置。现有技术文献专利文献专利文献1:日本特开2011-23579号公报
技术实现要素:发明所要解决的问题先前提案的日本特开2011-23579号中,将与半导体晶片等基板上所形成的Cu等金属膜反应的涡电流传感器配置在研磨台内,在基板的研磨中,伴随研磨台的旋转,涡电流传感器在通过基板下方的期间,在基板的金属膜反应而输出规定的电压值,因此,监视该输出而检测金属膜被除去。此时,要进行研磨、检测金属薄膜,通过令涡电流传感器的振荡频率上升、令涡电流传感器的内部电路的放大率提升、或者令涡电流传感器的励磁电压上升而进行。此外,在被研磨的金属膜的下层存在不同材质的金属膜时,进行研磨、检测不同材质的金属膜(或导电性膜)时,也同样地通过令涡电流传感器的振荡频率上升等改变传感器灵敏度而进行。涡电流传感器的振荡频率,必须设定为低于线圈自身的电感、静电容量所决定的线圈共振频率。振荡频率设定为接近共振频率的话,特性的稳定性存在问题。此外,提升了涡电流传感器的内部电路的放大率时,存在电路噪音影响变大的问题。另外,令涡电流传感器的励磁电压上升时,特性的稳定性存在问题。此外,为了检测上述的不同膜质、膜厚,除了改变涡电流传感器的传感器灵敏度的方法以外,也可在研磨台内的不同位置设置灵敏度不同的多个传感器和种类不同的多个传感器。但是,在不同位置设置多个传感器时,传感器通过基板下方的轨迹不同,多个传感器是在基板被研磨面上的不同位置点进行测量,存在难以正确判断同一轨迹上的膜厚的问题。本发明鉴于上述情况而作出,目的是提供无需提升涡电流传感器的振荡频率、内部电路的放大率及励磁电压,并且即使不在研磨台内的不同位置设置灵敏度不同的多个传感器,也可以正确检测半导体晶片等基板上的金属薄膜(或导电性薄膜)的涡电流传感器。此外,本发明的目的是提供通过使用涡电流传感器检查研磨中的基板上是否存在金属膜(或导电性膜)的残膜而可以缩短检査时间、检测到残膜时通过直接实施追加研磨而可以缩短处理时间的研磨方法及研磨装置。解决问题的手段为达成上述目的,本发明的涡电流传感器的第1形态,是一种涡电流传感器,其特征在于,配置于形成有金属膜或导电性膜的基板的附近,检测所述金属膜或导电性膜上形成的涡电流,其构成为,将卷绕了导线或导电体的尺寸不同的多个线圈互相分离配置为外侧的线圈包围内侧的线圈,使所述多个线圈各自分别检测所述金属膜或导电性膜上形成的涡电流。本发明的涡电流传感器的第2形态,是一种涡电流传感器,其特征在于,配置于形成有金属膜或导电性膜的基板的附近,检测所述金属膜或导电性膜上形成的涡电流,其构成为,将卷绕了导线或导电体的尺寸不同的多个线圈对于基板在垂直方向上下配置,使所述多个线圈各自分别检测所述金属膜或导电性膜上形成的涡电流。根据本发明的第1形态及第2形态,由于涡电流传感器中的涡电流检测用的多个线圈由尺寸小的线圈和尺寸大的线圈构成,因此可以分别检测包含基板上的微细区域(第1区域)和含有该微细区域(第1区域)的较宽区域(第2区域)的2个以上区域的涡电流。因此,可以比较基板上的2个以上的重叠区域在同一时点分别检测到的涡电流,可以高精度地检测金属膜或导电性膜。根据本发明的优选形态,其特征在于,所述多个线圈,由线圈外径小的线圈和线圈外径大的线圈构成,或者将线圈的内径与外径的算术平均定义为线圈中心直径的话,由线圈中心直径小的线圈和线圈中心直径大的线圈构成。根据本发明的优选形态,其特征在于,将所述线圈外径小的线圈和所述线圈外径大的线圈各自多个串联连接,被串联连接的线圈外径小的线圈和被串联连接的线圈外径大的线圈配置为任意一方夹着另一方。根据本发明的优选形态,其特征在于,将所述线圈中心直径小的线圈和所述线圈中心直径大的线圈各自多个串联连接,被串联连接的线圈中心直径小的线圈和被串联连接的线圈中心直径大的线圈配置为任意一方夹着另一方。根据本发明的优选形态,其特征在于,所述多个线圈构成分别检测所述金属膜或导电性膜上形成的涡电流的检测线圈。根据本发明的优选形态,其特征在于,所述涡电流传感器,具备有与交流信号源相连接、在所述金属膜或导电性膜上形成涡电流的多个励磁线圈,多个励磁线圈互相分离配置为外侧的励磁线圈包围内侧的励磁线圈。根据本发明的优选形态,其特征在于,所述涡电流传感器,具备有与交流信号源相连接、在所述金属膜或导电性膜上形成涡电流的多个励磁线圈,多个励磁线圈对于基板在垂直方向上下配置。根据本发明,由于涡电流传感器中的多个励磁线圈由尺寸小的线圈和尺寸大的线圈构成,因此可以在包含基板上的微细区域(第1区域)和含有该微细区域(第1区域)的较宽区域(第2区域)的2个以上的区域分别形成涡电流。根据本发明的优选形态,其特征在于,所述涡电流传感器,具备有与所述多个检测线圈各自串联连接的多个虚设线圈,多个虚设线圈互相分离配置为外侧的虚设线圈包围内侧的虚设线圈。根据本发明的优选形态,其特征在于,所述涡电流传感器,具备有与所述多个检测线圈各自串联连接的多个虚设线圈,多个虚设线圈对于基板在垂直方向上下配置。根据本发明的优选形态,其特征在于,所述多个检测线圈的至少1个,将“列”定义为对于基板的垂直方向、“层”定义为对于基板的平行方向时,由线材或导电体卷绕为1列多层的线圈构成。根据本发明,由于涡电流传感器中的多个检测线圈的至少1个由线材或导电体卷绕为1列多层的线圈构成,因此检测线圈可靠近基板,此外,由于可以减小线路容量,传感器灵敏度变好。因此,无需令涡电流传感器的振荡频率、内部电路的放大率及励磁电压上升即可检测基板上的金属薄膜或导电性薄膜。所述检测线圈,既可以通过与基板的金属膜或导电性膜的形成面平行地将线材或导电体多层卷绕为螺旋状,从而使得列方向的厚度仅为线材或导电体的直径大小并为扁平,也可以通过将线材或导电体多层卷绕为螺旋状时令其弯曲着逐渐接近(或远离)基板,从而使得列方向具有线材或导电体的直径大小所规定的厚度。根据本发明的优选形态,其特征在于,所述多个励磁线圈的至少1个,将“列”定义为对于基板的垂直方向、“层”定义为对于基板的平行方向时,由线材或导电体卷绕为1列多层的线圈构成。根据本发明,通过涡电流传感器中的多个励磁线圈的至少1个由线材或导电体卷绕为1列多层的线圈构成,即使线圈的电感变大,静电容量也不会变大,因此可以得到较高的共振频率,因而即使令振荡频率上升也可进行稳定的薄膜检测。此外,根据本发明,由于涡电流传感器中的多个励磁线圈的至少1个由线材或导电体卷绕为1列多层的线圈构成,因此励磁线圈可以靠近基板,涡电流会在基板上流动,传感器灵敏度变好。根据本发明的优选形态,其特征在于,所述多个虚设线圈的至少1个,将“列”定义为对于基板的垂直方向、“层”定义为对于基板的平行方向时,由线材或导电体卷绕为1列多层的线圈构成。根据本发明的优选形态,其特征在于,所述检测线圈、所述励磁线圈及所述虚设线圈的至少1个,通过将线材或导电体卷绕为1列多层的所述线圈多个串联连接构成。根据本发明,通过将1列多层的线圈多个串联连接,线圈的合成电感为多个线圈的电感与邻接的线圈间的互感之和,因此,伴随着线圈的合成电感的上升,线圈整体的传感器输出值增加,可良好地进行金属膜或导电性膜的检测。根据本发明的优选形态,其特征在于,所述励磁线圈,随着接近半径方向外侧,成弯曲靠近基板。根据本发明,励磁线圈是,半径方向内侧向虚设线圈一侧凹下、随着靠近半径方向外侧而弯曲为凹球面状接近检测线圈一侧、卷绕了线材或导电体的线圈。如此,通过令振荡线圈弯曲为凹球面状,可使得振荡磁场向中央部收敛,提升传感器灵敏度。根据本发明的优选形态,其特征在于,所述检测线圈、所述励磁线圈及所述虚设线圈被收置于由高磁导率材料形成的筒状部件内。根据本发明,来自励磁线圈的磁通量,可通过位于励磁线圈周围的高磁导率材料的筒状部件内,获取在测定对象的金属膜或导电性膜内通过的路径(磁路)。因此,磁通量通过设置环境的部件内时不会衰减,可在金属膜或导电性膜的内部有效产生涡电流,可高灵敏度测定金属膜或导电性膜。本发明的研磨方法的第1形态,是一种研磨方法,其特征在于,向旋转的研磨台上的研磨面按压研磨对象基板,研磨基板上的金属膜或导电性膜,所述基板的研磨中,伴随所述研磨台的旋转,通过设置在该研磨台上的涡电流传感器扫描基板的被研磨面,监视通过扫描所述基板的被研磨面而得到的所述涡电流传感器的输出,根据该涡电流传感器的输出变化而监视所述金属膜或导电性膜的膜厚,所述涡电流传感器具备有卷绕了导线或导电体的尺寸不同的多个线圈,所述多个线圈各自分别检测包含基板被研磨面上的第1区域和含有该第1区域、大于第1区域的第2区域的2个以上区域的涡电流。根据本发明的研磨方法的第1形态,涡电流传感器在伴随研磨台的旋转而通过基板下方的期间,与基板的金属膜或导电性膜反应而输出规定的电压值等,由此监视涡电流传感器的输出、监视所述金属膜或导电性膜的膜厚。此时,多个线圈描绘相同的通过轨迹而扫描基板被研磨面上,多个线圈可在相同的通过轨迹上、在相同的时点连续测量基板上的金属膜或导电性膜。即,同一通过轨迹上,可由一方的线圈检测目标金属膜或导电性膜的微细区域(第1区域)的涡电流而测量金属膜或导电性膜,另一方的线圈检测含有所述微细区域(第1区域)的较宽区域(第2区域)的涡电流而测量金属膜或导电性膜。本发明的研磨方法的第2形态,其特征在于,向旋转的研磨台上的研磨面按压研磨对象基板时,对每个基板被研磨面区域独立控制按压力的同时按压基板,从而研磨基板上的金属膜或导电性膜的研磨方法中,所述基板的研磨中,伴随所述研磨台的旋转,通过设置于该研磨台的涡电流传感器扫描基板的被研磨面,监视扫描所述基板被研磨面而得到的所述涡电流传感器的输出,根据该涡电流传感器的输出变化,监视所述金属膜或导电性膜的膜厚,所述涡电流传感器具备有卷绕了导线或导电体的尺寸不同的多个线圈,所述多个线圈各自在每个基板被研磨面区域分别检测涡电流。根据本发明的研磨方法的第2形态,由于涡电流传感器在伴随研磨台的旋转、通过基板下方的期间,与基板的金属膜或导电性膜反应而输出规定的电压值等,因而监视涡电流传感器的输出,监视所述金属膜或导电性膜的膜厚。此时,多个线圈描绘相同的通过轨迹、扫描基板被研磨面上,多个线圈可在相同的通过轨迹上、于相同的时点连续测量基板上的金属膜或导电性膜。此时,所述多个线圈可各自在每个基板被研磨面区域分别检测涡电流,因此,可在每个基板被研磨面区域(例如,基板的边缘部、基板的中央部)测量金属膜或导电性膜的同时,扩大基板边缘部的检测范围。然后,反馈测量结果,对每个基板被研磨面的区域控制研磨压力,可实现期望的研磨剖面。根据本发明的优选形态,其特征在于,所述多个线圈构成分别检测所述金属膜或导电性膜上形成的涡电流的检测线圈。根据本发明的优选形态,其特征在于,所述多个线圈各自由外径大的传感器和外径小的传感器构成,监视所述外径大的传感器的输出,根据输出的变化检测研磨终点,在检测到所述研磨终点后,监视所述外径小的传感器的输出,检测残留在部分基板上的膜,进行残膜监视。根据本发明,具备有外径大的检测线圈的传感器作为低灵敏度的传感器发挥作用,可正确检测基板被研磨面整体的残膜,可稳定进行研磨终点的检测。具备有外径小的检测线圈的传感器作为高灵敏度的传感器发挥作用,在目标金属膜或导电性膜变薄和金属膜或导电性膜的面积变小时也可进行检测,可以进行基板被研磨面上的详细的残膜分布检测及基板边缘部分的薄膜检测。根据本发明的优选形态,其特征在于,所述多个线圈,将线圈的内径与外径的算术平均定义为线圈中心直径的话,由线圈中心直径小的线圈和线圈中心直径大的线圈构成,具备有所述线圈中心直径小的线圈的传感器构成传感器径小的传感器,具备有所述线圈中心直径大的线圈的传感器构成传感器径大的传感器,监视所述线圈中心直径大的传感器的输出,根据输出的变化检测研磨终点,检测到所述研磨终点后,监视所述线圈中心直径小的传感器的输出,检测残留在部分基板上的膜,进行残膜监视。根据本发明,具备有线圈中心直径大的检测线圈的传感器作为低灵敏度的传感器发挥作用,可正确检测基板被研磨面整体的残膜,可稳定进行研磨终点的检测。具备有线圈中心直径小的检测线圈的传感器作为高灵敏度的传感器发挥作用,在目标金属膜或导电性膜变薄和金属膜或导电性膜的面积变小时也可进行检测,可以进行基板被研磨面上的详细的残膜分布检测及基板边缘部分的薄膜检测。发明效果本发明具有以下列举的效果。(1)涡电流传感器中的涡电流检测用的多个线圈由外径(或线圈中心直径)小的线圈和外径(或线圈中心直径)大的线圈构成,因此,可以分别检测包含基板上的微细区域(第1区域)和含有该微细区域(第1区域)的较宽区域(第2区域)的2个以上区域的涡电流。因此,可以比较基板上的2个以上的重叠区域在同一时点分别检测到的涡电流,可以高精度地检测金属膜或导电性膜。(2)具备有外径(或线圈中心直径)小的检测线圈的传感器作为高灵敏度的传感器发挥作用,在目标金属膜或导电性膜变薄和金属膜或导电性膜的面积变小时也可进行检测,可以进行基板被研磨面上的详细的残膜分布检测及基板边缘部分的薄膜检测。另一方面,具备有外径(或线圈中心直径)大的检测线圈的传感器作为低灵敏度的传感器发挥作用,可正确检测基板被研磨面整体的残膜,可稳定进行研磨终点的检测。(3)多个线圈可各自在每个基板被研磨面区域分别检测涡电流,因此,可在每个基板被研磨面区域(例如,基板的边缘部、基板的中央部)测量金属膜或导电性膜的同时,扩大基板边缘部的检测范围。然后,反馈测量结果,对每个基板被研磨面的区域控制研磨压力,可实现期望的研磨剖面。(4)由于涡电流传感器中的检测线圈由线材或导电体卷绕为1列多层的线圈构成,因此检测线圈可靠近基板,此外,由于可以减小线路容量,传感器灵敏度变好。因此,无需令涡电流传感器的振荡频率、内部电路的放大率及励磁电压上升即可检测半导体晶片等基板上的金属薄膜或导电性薄膜。(5)在研磨中检查基板上是否存在金属膜或导电性膜等的残膜,检测到残膜时,通过直接实施追加研磨,可缩短处理时间,此外,检测到残膜时,通过管理CMP工艺整体的控制装置对追加研磨时间和残膜状況进行管理,可将下次的研磨对象的研磨条件变更为最适合的。附图说明图1是显示本发明涉及的研磨装置的整体构成的概略图。图2是显示研磨台、涡电流传感器与半导体晶片的关系的平面图。图3是显示涡电流传感器的基本构成的图,图3(a)是表示涡电流传感器的基本构成的框图,图3(b)是涡电流传感器的等效电路图。图4(a)、(b)、(c)是显示以往的涡电流传感器的传感器线圈与本发明的涡电流传感器的传感器线圈的对比图,图4(a)是显示以往的涡电流传感器中使用的传感器线圈的构成例的概略图,图4(b)是显示本发明的涡电流传感器的传感器线圈的构成例的概略图,图4(c)是显示本发明的涡电流传感器的检测线圈的模式平面图。图5(a)、(b)是显示1列N层的线圈m个串联连接的形态的示意图。图6是显示本发明的涡电流传感器的传感器线圈与半导体晶片(基板)的位置关系的模式立面图。图7是显示1列N层卷绕的线圈的其他卷绕方式的概略图。图8是显示1列N层卷绕的线圈的其他卷绕方式的概略图。图9是显示1列N层卷绕的线圈的其他卷绕方式的概略图。图10(a)、(b)是显示1列N层卷绕的线圈中令电感(线圈的L)变化的例子的概略图。图11(a)是显示本发明的涡电流传感器中使用的传感器线圈的其他构成例的概略图,图11(b)是显示图11(a)所示的传感器线圈的励磁线圈的模式平面图。图12(a)、(b)是显示本发明的涡电流传感器中使用的传感器线圈的其他构成例的图,图12(a)是显示内侧的传感器线圈由卷成螺线状的线圈构成、外侧的传感器线圈由卷成螺旋形的线圈构成的例子的概略图,图12(b)是显示内侧的传感器线圈由卷成螺旋形的线圈构成、外侧的传感器线圈由卷成螺线状的线圈构成的例子的概略图。图13是显示本发明的涡电流传感器中使用的传感器线圈的其他构成例的图,是内侧的传感器线圈及外侧的传感器线圈中的各线圈由卷成螺线状的线圈构成的例子的概略图。图14是显示传感器线圈中的同一种类的线圈相互的线圈位置重叠配置的构成例子的概略图。图15(a)、(b)、(c)是显示1列N层的线圈2个串联连接的具体形态的概略图。图16(a)、(b)是显示线圈的中心直径有大小时2个线圈串联连接的形态的概略图。图17是显示传感器线圈的各线圈中励磁线圈的形状为凹球面状的例子的概略图。图18是显示图4(b)所示的传感器线圈的周围配置有由高磁导率材料构成的筒状部件的例子的概略图。图19是显示卷为螺旋形的3个检测线圈成同心圆状配置的例子的概略图。图20是显示传感器线圈中的各线圈的电路构成的概略图。图21是显示涡电流传感器的同步检波电路的框图。图22是显示具备有涡电流传感器的研磨装置的主要构成的图,图22(a)是显示包含涡电流传感器的控制部的整体构成的图,图22(b)是显示涡电流传感器部分的放大截面图。图23(a)是显示涡电流传感器扫描(scan)半导体晶片的表面(被研磨面)时的轨迹与涡电流传感器的输出的关系的图,图23(b)是显示半导体晶片的研磨开始时的涡电流传感器的输出的图,图23(c)是显示从半导体晶片的研磨开始至规定时间后的涡电流传感器的输出的图。图24是显示从半导体晶片的研磨开始至半导体晶片上中心部的金属膜(或导电性膜)消除(变无)为止的研磨工序与涡电流传感器的输出的关系的图。图25是显示半导体晶片上的金属膜(或导电性膜)的研磨工序及监视工序的顺序的流程图。图26是显示通过监视涡电流传感器中的传感器径小的传感器得到的输出值以检测局部残膜发生时,晶片下层的金属配线等的影响的图。图27是显示涡电流传感器扫描半导体晶片上的轨迹的示意图。图28是显示涡电流传感器扫描半导体晶片上的轨迹的示意图。图29是显示涡电流传感器扫描半导体晶片上的轨迹的示意图。图30是显示本发明的研磨装置适宜使用的具备有多个压力室的顶环的模式截面图。图31是显示可根据压力室的尺寸设定采样周期的形态的图。符号说明1顶环2顶环本体3护环50涡电流传感器52交流信号源54检波电路55主放大器56控制装置(控制器)60传感器线圈60A、60B传感器线圈61线轴61B中空的线轴62励磁线圈63检测线圈64虚设线圈65筒状部件76可变电阻77电阻桥接电路82带通滤波器83高频放大器84移相电路85cos同步检波电路86sin同步检波电路87,88低通滤波器89向量运算电路100研磨台100a台轴101研磨垫101a研磨面102研磨液供给喷嘴110顶环顶端111顶环轴112旋转筒113同步带轮114顶环用马达115同步带116同步带轮117顶环顶端轴124上下运动构件125旋转接头126轴承128架桥129支承台130支柱132滚珠螺杆138AC伺服马达132a螺纹轴132b螺母142弹性垫144夹具板150旋转接头151m垫片(薄板)152~155流体管路W半导体晶片mf金属膜(或导电性膜)P1~P4压力室具体实施方式以下对于本发明涉及的研磨装置的实施形态,参照图1至图31进行详细说明。另外,图1至图31中,相同或相当的构成要素赋予相同的符号,省略重复说明。图1是表示本发明涉及的研磨装置的整体构成的概略图。如图1所示,研磨装置具备有研磨台100和支承研磨对象物的半导体晶片等基板、按压研磨台上的研磨面的顶环1。研磨台100,通过台轴100a与配置在其下方的马达(未图示)连接,可绕着该台轴100a旋转。研磨台100的上面粘贴有研磨垫101,研磨垫101的表面101a构成研磨半导体晶片W的研磨面。研磨台100的上方设置有研磨液供给喷嘴102,通过该研磨液供给喷嘴102向研磨台100上的研磨垫101上提供研磨液Q。如图1所示,研磨台100的内部埋设有涡电流传感器50。顶环1基本由:将半导体晶片W向研磨面101a按压的顶环本体2和支承半导体晶片W的外边缘、防止半导体晶片W从顶环飞出的护环3构成。顶环1与顶环轴111连接,该顶环轴111,通过上下运动构件124而相对于顶环顶端110上下运动。通过该顶环轴111的上下运动,决定相对于顶环顶端110的顶环1整体的升降位置。另外,顶环轴111的上端安装有旋转接头125。令顶环轴111及顶环1上下运动的上下运动构件124,具备有:通过轴承126可旋转地支承顶环轴111架桥128;安装在架桥128上的滚珠螺杆132;由支柱130支承的支承台129;设置在支承台129上的AC伺服马达138。支承伺服马达138的支承台129,通过支柱130被固定在顶环顶端110。滚珠螺杆132具备有与伺服马达138连接的螺纹轴132a和螺合该螺纹轴132a的螺母132b。顶环轴111与架桥128成一体而上下运动。因此,驱动伺服马达138的话,通过滚珠螺杆132,架桥128会上下运动,由此,顶环轴111及顶环1会上下运动。此外,顶环轴111通过连接键(未图示)与旋转筒112连接。该旋转筒112的外周部具备有同步带轮113。顶环顶端110上固定有顶环用马达114,上述同步带轮113通过同步带115而与设置于顶环用马达114的同步带轮116连接。因此,通过旋转驱动顶环用马达114,通过同步带轮116、同步带115及同步带轮113,旋转筒112及顶环轴111一体旋转,顶环1旋转。另外,顶环顶端110通过顶环顶端轴117支承,该顶环顶端轴117被可旋转地支承在框架(未图示)上。如图1所示构成的研磨装置中,顶环1的下表面可支承半导体晶片W等的基板。顶环顶端110可以顶环轴117为中心旋转,下面支承有半导体晶片W的顶环1通过顶环顶端110的旋转而从半导体晶片W的获取位置移动至研磨台100的上方。然后,令顶环1下降,将半导体晶片W向研磨垫101的表面(研磨面)101a按压。此时,令顶环1及研磨台100各自旋转,从设置在研磨台100上方的研磨液供给喷嘴102向研磨垫101上提供研磨液。如此,令半导体晶片W与研磨垫101的研磨面101a滑动接触,研磨半导体晶片W的表面。图2是表示研磨台100、涡电流传感器50与半导体晶片W的关系的平面图。如图2所示,涡电流传感器50设置于通过被支承在顶环1上的研磨中的半导体晶片W的中心Cw的位置。符号CT为研磨台100的旋转中心。例如,涡电流传感器50在通过半导体晶片W下方的期间,可在通过轨迹(扫描线)上连续检测半导体晶片W的Cu层等金属膜(导电性膜)。接着,对于本发明涉及的研磨装置所具备的涡电流传感器50,使用图3至图19进行更详细说明。图3是显示涡电流传感器50的基本构成的图,图3(a)是显示涡电流传感器50的基本构成的框图,图3(b)是涡电流传感器50的等效电路图。如图3(a)所示,涡电流传感器50,在检测对象金属膜(或导电性膜)mf附近配置传感器线圈60,该线圈与交流信号源52连接。在这里,检测对象金属膜(或导电性膜)mf,是例如形成于半导体晶片W上的Cu、Al、Au、W等的薄膜。传感器线圈60为检测用线圈,对于检测对象的金属膜(或导电性膜),配置在例如1.0~4.0mm左右的附近。涡电流传感器中,存在有由于金属膜(或导电性膜)mf上产生涡电流,振荡频率变化、通过该频率变化检测金属膜(或导电性膜)的频率方式,以及电阻变化、通过该电阻变化检测金属膜(或导电性膜)的电阻方式。即,频率方式中,图3(b)所示的等效电路中,通过涡电流I2变化,电阻Z会变化,信号源(可变频率振荡器)52的振荡频率变化的话,可通过检波电路54检测该振荡频率的变化、检测金属膜(或导电性膜)的变化。电阻方式中,图3(b)所示的等效电路中,通过涡电流I2变化,电阻Z会变化,从信号源(固定频率振荡器)52观察到的电阻Z变化的话,可通过检波电路54检测该电阻Z的变化、检测金属膜(或导电性膜)的变化。电阻方式的涡电流传感器中,信号输出X、Y、相位、合成电阻Z如后述般被取出。通过频率F或电阻X、Y等,可以得到金属膜(或导电性膜)Cu、Al、Au、W的测定信息。涡电流传感器50,如图1所示,可内藏于研磨台100内部的表面附近的位置,对于研磨对象的半导体晶片,介着研磨垫相对,根据半导体晶片上的金属膜(或导电性膜)中流动的涡电流,可检测金属膜(或导电性膜)的变化。涡电流传感器的频率可使用单一电波、混合电波、AM调制电波、FM调制电波、函数发生器的扫频输出或多个振荡频率源,优选与金属膜的膜种类相适应,选择灵敏度好的振荡频率和调制方式。以下对于电阻方式的涡电流传感器进行具体说明。交流信号源52为2~8MHz左右的固定频率的振荡器,例如可使用水晶振荡器。然后,通过交流信号源52所提供的交流电压,传感器线圈60中有电流I1流通。通过配置在金属膜(或导电性膜)mf附近的传感器线圈60中有电流流通,其磁通量与金属膜(或导电性膜)mf互连,期间形成互感M,金属膜(或导电性膜)mf中有涡电流I2流通。在这里,R1是包含传感器线圈的初级侧等效电阻,L1同样是包含传感器线圈的初级侧自感。在金属膜(或导电性膜)mf一侧,R2为相当于涡电流损失的等效电阻,L2为其自感。从交流信号源52的端子a、b观察传感器线圈一侧的电阻Z,根据金属膜(或导电性膜)mf中形成的涡电流损失的大小而变化。图4(a)、(b)、(c)是显示以往的涡电流传感器的传感器线圈与本发明的涡电流传感器的传感器线圈的对比图。图4(a)是显示以往的涡电流传感器中使用的传感器线圈的构成例子的概略图,图4(b)是显示本发明的涡电流传感器50的传感器线圈的构成例子的概略图,图4(c)是显示本发明的涡电流传感器50的检测线圈的模式平面图。如图4(a)所示,以往的涡电流传感器50的传感器线圈51,用于在金属膜(或导电性膜)形成涡电流的线圈与用于检测金属膜(或导电性膜)的涡电流的线圈是分离的,由卷绕在线轴71的3个线圈72、73、74构成。为了得到传感器的灵敏度,必须增加线圈的卷绕数。因此,传感器线圈51中的3个线圈72、73、74,将“列”定义为对于半导体晶片(基板)W的垂直方向、“层”定义为对于半导体晶片(基板)W的平行方向时,由线轴71外周的线材ln各5列2层(10个转)卷成螺线状的线圈构成。在这里,中央的线圈72是与交流信号源52连接的励磁线圈(振荡线圈)。该励磁线圈72,通过交流信号源52所提供的电压形成的磁场,在配置于附近的半导体晶片(基板)W上的金属膜(或导电性膜)mf上形成涡电流。线轴71的金属膜(或导电性膜)一侧,配置有检测线圈73,检测金属膜(或导电性膜)上形成的涡电流所产生的磁场。在夹着励磁线圈72的检测线圈73的相反一侧,配置有虚设线圈(平衡线圈)74。与此相对,本发明的涡电流传感器50,如图4(b)所示,具备有2个传感器线圈60A、60B。2个传感器线圈60A、60B互相分离配置为外侧的传感器线圈60B包围内侧的传感器线圈60A。内侧的传感器线圈60A由3个线圈62A、63、64A构成,未采用在线轴61上卷绕的方式。传感器线圈60A的3个线圈62A、63A、64A,将“列”定义为对于半导体晶片(基板)的垂直方向、“层”定义为对于半导体晶片(基板)W的平行方向时,是将线材或导电体ln各自卷绕1列N层而卷为螺旋状的线圈。更详细的,3个线圈62A、63A、64A,将“列”定义为对于半导体晶片(基板)W的金属膜(或导电性膜)形成面为垂直方向、“层”定义为对于半导体晶片(基板)W的金属膜(或导电性膜)形成面为平行方向时,是将线材或导电体ln各自卷绕1列N层而卷为螺旋状的线圈。N为2以上的整数。例如,与以往同等以上的卷绕数的话,N在11以上。所述3个线圈62A、63A、64A中,中央的线圈62A是与交流信号源52连接的励磁线圈(振荡线圈)。该励磁线圈62A,通过交流信号源52所提供的电压形成的磁场,在配置于附近的半导体晶片W上的金属膜(或导电性膜)mf上形成涡电流。励磁线圈62A的金属膜(或导电性膜)一侧,配置有检测线圈63A,检测金属膜(或导电性膜)上形成的涡电流所产生的磁场。夹着励磁线圈62A的检测线圈63A的相反一侧配置有虚设线圈(平衡线圈)64A。励磁线圈62A与检测线圈63A之间,配置有用于使励磁线圈62A和检测线圈63A之间的间隔保持一定的垫片S1,励磁线圈62A与虚设线圈64A之间,配置有用于使励磁线圈62A和虚设线圈64A之间的间隔保持一定的垫片S2。然后,与虚设线圈64A邻接,配置有线轴61。另外,励磁线圈62A与检测线圈63A之间以及励磁线圈62A与虚设线圈64A之间,有距离即可,也可不特别设置垫片而仅有空间。此外,外侧的传感器线圈60B由3个线圈62B、63B、64B构成,未采用在线轴61上卷绕的方式。传感器线圈60B的3个线圈62B、63B、64B,将“列”定义为对于半导体晶片(基板)W为垂直方向、“层”定义为对于半导体晶片(基板)W为平行方向时,是将线材或导电体ln各自卷绕1列N层而卷为螺旋状的线圈。更详细的,3个线圈62B、63B、64B,将“列”定义为对于半导体晶片(基板)W的金属膜(或导电性膜)形成面为垂直方向、“层”定义为对于半导体晶片(基板)W的金属膜(或导电性膜)形成面为平行方向时,是将线材或导电体ln各自卷绕1列N层而卷为螺旋状的线圈。N为2以上的整数,例如与以往同等以上的卷绕数的话,N在11以上。所述3个线圈62B、63B、64B中,中央的线圈62B,是与图3(a)所示的交流信号源52同样构成的另行设置的交流信号源(未图示)连接的励磁线圈(振荡线圈)。该励磁线圈62B,通过交流信号源提供的电压所形成的磁场,在配置于附近的半导体晶片W上的金属膜(或导电性膜)mf上形成涡电流。励磁线圈62B的金属膜(或导电性膜)一侧,配置有检测线圈63B,检测金属膜(或导电性膜)上形成的涡电流所产生的磁场。夹着励磁线圈62B的检测线圈63B的相反一侧配置有虚设线圈(平衡线圈)64B。励磁线圈62B与检测线圈63B之间,配置有用于使励磁线圈62B与检测线圈63B之间的间隔保持一定的垫片S1,励磁线圈62B与虚设线圈64B之间,配置有用于使励磁线圈62B与虚设线圈64B之间的间隔保持一定的垫片S2。然后,与虚设线圈64B邻接,配置有线轴61。另外,励磁线圈62B与检测线圈63B之间以及励磁线圈62B与虚设线圈64B之间,间隔距离即可,也可不特别设置垫片而仅有空间。图4(c)是表示2个传感器线圈60A、60B中的检测线圈63A、63B的模式平面图。如图4(c)所示,2个检测线圈63A、63B互相分离配置为外侧的检测线圈63B包围内侧的检测线圈63A。2个检测线圈63A、63B,是以对于半导体晶片(基板)W的金属膜(或导电性膜)形成面的垂直方向的共通轴线Ax(参照图4(b))为中心,卷绕了线材或导电体的线圈。此外,2个检测线圈63A、63B,在与所述轴线Ax垂直方向即半径方向上互相分离配置。如上所述,内侧的检测线圈63A由线材或导电体ln卷绕1列N层而卷为半径方向螺旋状的线圈构成。检测线圈63A,既可以通过与半导体晶片(基板)的金属膜(或导电性膜)mf形成面平行地将线材或导电体ln以N层卷绕为螺旋状,从而使得列方向(图4(c)中与纸面垂直的方向)的厚度仅为线材或导电体ln的直径厚度而形成为扁平,也可以通过将线材ln以N层卷绕为螺旋状时令其弯曲着逐渐接近(或远离)半导体晶片(基板)W,从而使得列方向具有线材或导电体ln的直径长度所规定的厚度。此外,外侧的检测线圈63B也由线材或导电体ln卷绕1列N层而卷为半径方向螺旋状的线圈构成。检测线圈63B,既可以通过与半导体晶片(基板)的金属膜(或导电性膜)mf的形成面平行地将线材或导电体ln以N层卷为螺旋状,从而使得列方向(图4(c)中与纸面垂直的方向)的厚度仅为线材ln的直径厚度而变为扁平,也可以通过将线材或导电体ln以N层卷绕为螺旋状时令其弯曲着逐渐接近(或远离)半导体晶片(基板)W,从而使得列方向具有线材或导电体ln的直径长度所规定的厚度。图4(c)中,图示了2个检测线圈63A、63B,但2个励磁线圈62A、62B也与图4(c)所示的检测线圈63A、63B为相同的形状。2个励磁线圈62A、62B,是以所述轴线Ax(参照图4(b))为中心、卷绕了线材或导电体的线圈,并且互相分离配置在与轴线Ax垂直方向的半径方向上。2个虚设线圈64A、64B也与图4(c)所示的检测线圈63A、63B为相同的形状。2个虚设线圈64A、64B,是以所述轴线Ax(参照图4(b))为中心、卷绕了线材或导电体的线圈,并且互相分离配置在与轴线Ax垂直的半径方向上。此外,传感器线圈60A中的各线圈62A、63A、64A及传感器线圈60B中的各线圈62B、63B、64B,也可由线材或导电体ln卷绕1列N层为螺旋状的图4(c)所示的线圈m个串联连接而构成。在这里,m为2以上的整数。1列N层的线圈m个串联连接时,各线圈相互接触的话,由于容量增加,优选1列N层的线圈在列方向(对于基板的垂直方向)排列m个,邻接的线圈间设置空隙。另外,优选在该空隙中设置介电常数低的材料或空间。图5(a)、(b)是表示1列N层的线圈m个串联连接的形态的示意图。图5(a)所示的形态中,1列N层的线圈A、线圈B串联连接。图5(a)的形态中,可以得到2列线圈的电感L1A+L1B和邻接的线圈间的互感M。邻接的线圈间的互感M如下式。【数1】在这里,k为耦合系数、L1A,L1B为自电感[H]。因此,图5(a)所示的例子中,合成电感为L0=L1A+L1B+2M。图5(b)所示的形态中,1列N层的线圈A、线圈B、线圈C串联连接。图5(b)的形态中,可以得到3列线圈的电感L1A+L1B+L1C和邻接的线圈间的互感M1AB、M1BC、M1AC。互感M1AB,M1BC,M1AC如下式。【数2】在这里,k0、k1、k2为耦合系数,L1A、L1B、L1C为自感。因此,图5(b)所示的例子中,合成电感为L0=L1A+L1B+L1C+2M1AB+2M1BC+2M1AC。图5(a)、(b)中,显示的是1列N层的线圈2个或3个串联连接的情况,1列N层的线圈m个串联连接时,由于线圈的合成电感L0为m列的电感与m列间的互感之和,因此,伴随着线圈的合成电感的上升,线圈整体的传感器输出值增加,可良好地进行检测。此外,图5(a)、(b)所示的例子中,通过在1列N层的线圈间设置切换开关,可适当选定串联连接的线圈数。因此,根据检测对象的金属膜和膜厚,可切换检测线圈63A(或63B)、励磁线圈62A(或62B)、虚设线圈64A(或64B)的线圈数(列数),可进行最佳检测。例如,金属膜的膜厚薄或金属的电阻值低时,可增加线圈数(列数)。另外,图5(a)、(b)中,在线圈A、线圈B、线圈C等的线圈间,虽然也可无需有空间(空隙),但最好设置。该空间(空隙)中可配置介电常数低的材料。图6是表示本发明的涡电流传感器的传感器线圈60A、60B与半导体晶片(基板)W的位置关系的模式立面图。本发明的传感器线圈60A、60B,可以为非卷绕在线轴的方式,因此,通过将各线圈63A、62A、64A;63B、62B、64B卷绕1列N层而卷为螺旋状,在各线圈厚度较薄的状态下可增加卷绕数。因此,可使得传感器线圈60中的各线圈63A、62A、64A;63B、62B、64B与半导体晶片W的间的距离(L1、L2、L3)接近,因此传感器灵敏度变好。然后,随着卷绕数增加,L成分也会上升,灵敏度提升。此外,实施了本发明的螺旋卷绕时,由于为1列N层卷绕,因此线路容量为串联连接而可以减小。然后,可增加卷绕数,将L成分保持为较高的同时,可令共振频率上升、令振荡频率上升。图4(b)、(c)中,例示了卷成螺旋形的线圈,但也可不仅是螺旋卷绕,其他的卷绕方法,只要是卷绕1列N层,则可以得到同样的效果。图7至图9是表示卷绕1列N层的线圈的其他卷绕方式的概略图。图7所示的例子中,将线材ln卷绕1列N层而卷为多边形,由此形成检测线圈63A。如图7所示,多边形可以是随着从半径方向内侧靠近半径方向外侧而多边形的边数增加的,也可以是仅由三角形和四边形构成、多边形的边数相同的。图8所示的例子中,将线材ln卷绕1列N层而卷为椭圆状,由此形成检测线圈63A。图9所示的例子中,通过在规定的基板BP上卷绕1列N层而螺旋状地实施印刷配线(printedwiring)PW,导电体1n形成为卷绕了1列N层的图案线圈所构成的检测线圈63A。另外,导电体1n卷绕1列N层的图案线圈,除了印刷配线以外,还可通过将金属部件(Cu膜、Cu箔、Cu材料等)以蚀刻或线切割等的加工而制作。另外,金属部件,除了Cu以外,也可以是AL等的其他材质。图7至图9所示的例子中,显示的是线材或导电体ln的各种卷绕方法适用于内侧的检测线圈63A的情况,但外侧的检测线圈63B也可适用同样的卷绕方法。此外,对于励磁线圈62A、62B及虚设线圈64A、64B,当然也可适用图7至图9所示的线圈的卷绕方法。图10(a)、(b)是表示卷绕1列N层的线圈中令电感(线圈的L)变化的例子的概略图。图10(a)所示的例子中,将线材或导电体1n卷绕1列N层而卷为螺旋状,由此形成检测线圈63A。如图10(a)所示,卷成螺旋形的线圈上,外周侧端部与内周侧端部各自与端子T1、T2连接,中间部与端子T3、T4连接。然后,端子T1与端子T2间可构成线圈长度最长的线圈1,端子T1与端子T3间可构成线圈长度最短的线圈2,端子T1与端子T4间可构成线圈长度居中的线圈3。如此,通过令线圈长度变化,可以令电感L变化。图10(b)所示的例子中,将线材或导电体1n卷绕1列N层而卷为螺旋状,由此形成检测线圈63A。如图10(b)所示,卷成螺旋形的线圈上,内周侧端部与外周侧端部各自与端子T1、T2连接,中间部与端子T3、T4连接。然后,端子T1与端子T2间可构成线圈长度最长的线圈1,端子T1与子T3间可构成线圈长度最短的线圈2,端子T1与端子T4间可构成线圈长度居中的线圈3。如此,通过令线圈长度,可以令电感L变化。图10(a)、(b)所示的例子中,显示的是令电感变化的方法适用于检测线圈63A的情况,但外侧的检测线圈63B也可适用同样的卷绕方法。此外,对于励磁线圈62A、62B及虚设线圈64A、64B,当然也可适用图10所示的令电感变化的方法。图11(a)是表示本发明的涡电流传感器中使用的传感器线圈的其他构成例子的概略图,图11(b)是表示图11(a)所示的传感器线圈的励磁线圈的模式平面图。另外,图11(a)中,线圈未图示线材或导电体,为示意性表示。如图11(a)所示,涡电流传感器50具备有2个传感器线圈60A、60B,2个传感器线圈60A、60B使用共通的励磁线圈62。即,内侧的传感器线圈60A由检测线圈63A、励磁线圈62、虚设线圈64A构成,外侧的传感器线圈60B由检测线圈63B、励磁线圈62、虚设线圈64B构成。2个检测线圈63A、63B互相分离配置为外侧的检测线圈63B包围内侧的检测线圈63A。此外,2个虚设线圈64A、64B互相分离配置为外侧的虚设线圈64B包围内侧的虚设线圈64A。图11(b)是表示励磁线圈62的图。如图11(b)所示,励磁线圈62由线材或导电体1n卷绕1列N层而卷为半径方向螺旋状的单一线圈构成。检测线圈63A、63B及虚设线圈64A、64B与图4(b)、(c)所示的线圈为同样的构成。图12(a)、(b)是显示本发明的涡电流传感器中使用的传感器线圈的其他构成例子的图,图12(a)是显示内侧的传感器线圈60A由卷成螺线状的线圈构成、外侧的传感器线圈60B由卷成螺旋形的线圈构成的例子的概略图。另外,图12(a)中,外侧的传感器线圈60B未图示线材或导电体,为示意性表示。如图12(a)所示,内侧的传感器线圈60A的3个线圈62A、63A、64A,将“列”定义为对于半导体晶片(基板)W的金属膜(或导电性膜)形成面为垂直方向、“层”定义为对于半导体晶片(基板)W的金属膜(或导电性膜)形成面为平行方向时,为线轴61的外周线材或导电体ln各自卷绕N列M层而卷为螺线状的线圈。N、M为2以上的整数,图12(a)所示的例子中为5列2层的线圈。在这里,中央的线圈62A为励磁线圈,励磁线圈62A的金属膜(或导电性膜)侧的线圈63A为检测线圈,夹着励磁线圈62A的检测线圈63A的相反一侧的线圈64A为虚设线圈。此外,外侧的传感器线圈60B由3个线圈62B、63B、64B构成,未采用在线轴61上卷绕的方式。将“列”定义为对于半导体晶片(基板)W的金属膜(或导电性膜)形成面为垂直方向、“层”定义为对于半导体晶片(基板)W的金属膜(或导电性膜)形成面为平行方向时,传感器线圈60B的3个线圈62B、63B、64B是将线材或导电体ln各自卷绕1列N层而卷为螺旋状的线圈。N为2以上的整数,例如与以往同等以上的卷绕数的话,N在11以上。在这里,中央的线圈62B为励磁线圈,励磁线圈62B的金属膜(或导电性膜)侧的线圈63B为检测线圈,夹着励磁线圈62B的检测线圈63B的相反一侧的线圈64B为虚设线圈。图12(a)中显示的是,励磁线圈62B与检测线圈63B之间及励磁线圈62B与虚设线圈64B之间未设置垫片、仅有空间的例子。图12(b)显示的是内侧的传感器线圈60A由卷成螺旋形的线圈构成、外侧的传感器线圈60B由卷成螺线状的线圈构成的例子的概略图。图12(b)所示的传感器线圈与图12(a)所示的传感器线圈的内侧和外侧相反。即,如图12(b)所示,内侧的传感器线圈60A中的3个62A、63A、64A,是将线材或导电体各自卷绕1列N层而卷为螺旋状的线圈。此外,外侧的传感器线圈60B中的3个线圈62B、63B、64B,是将线材或导电体各自卷绕N列M层而卷为螺线状的线圈。图13是显示本发明的涡电流传感器中使用的传感器线圈的其他构成例子的图,是显示内侧的传感器线圈60A及外侧的传感器线圈60B中的各线圈由卷成螺线状的线圈构成的例子的概略图。如图13所示,将“列”定义为对于半导体晶片(基板)W的金属膜(或导电性膜)形成面为垂直方向、“层”定义为对于半导体晶片(基板)W的金属膜(或导电性膜)形成面为平行方向时,内侧的传感器线圈60A的3个线圈62A、63A、64A是在线轴61A外周将线材或导电体ln各自卷绕N列M层而卷为螺线状的线圈。N、M为2以上的整数,图13所示的例子中为5列2层的线圈。在这里,中央的线圈62A为励磁线圈,励磁线圈62A的金属膜(或导电性膜)侧的线圈63A为检测线圈,夹着励磁线圈62A的检测线圈63A的相反一侧的线圈64A为虚设线圈。此外,将“列”定义为对于半导体晶片(基板)W的金属膜(或导电性膜)形成面为垂直方向、“层”定义为对于半导体晶片(基板)W的金属膜(或导电性膜)形成面为平行方向时,外侧的传感器线圈60B的3个线圈62B、63B、64B是在中空的线轴61B外周将线材或导电体ln各自卷绕N列M层而卷为螺线状的线圈。N、M为2以上的整数,图13所示的例子中为5列2层的线圈。在这里,中央的线圈62B为励磁线圈,励磁线圈62B的金属膜(或导电性膜)侧的线圈63B为检测线圈,夹着励磁线圈62B的检测线圈63B的相反一侧的线圈64B为虚设线圈。如图4至图13所示,本发明的涡电流传感器50,线圈外径不同的多个传感器线圈60A、60B互相分离配置为外侧的传感器线圈60B包围内侧的传感器线圈60A。根据本发明的涡电流传感器50,内侧的传感器线圈60A中的检测线圈63A、励磁线圈62A、虚设线圈64A的外径小于外侧的传感器线圈60B中的检测线圈63B、励磁线圈62B、虚设线圈64B的外径。例如,比较图4(b)、(c)所示的涡电流传感器50中的内侧的检测线圈63A和外侧的检测线圈63B,内侧的检测线圈63A的外径为D1,外侧的检测线圈63B的外径为D2,设定为D2>>D1。通过使内侧的检测线圈63A的外径D1较小,内侧的检测线圈63A可检测目标金属膜(或导电性膜)的微细区域(第1区域)的涡电流。然后,外径大的外侧的检测线圈63B可检测包含内侧的检测线圈63A的测量区域(第1区域)的较宽区域(第2区域)的涡电流。此外,如图2所示,涡电流传感器50,研磨台100每旋转1周扫描半导体晶片(基板)W的表面(被研磨面),此时,内侧的检测线圈63A与外侧的检测线圈63B描绘相同的通过轨迹而扫描半导体晶片W的被研磨面上。因此,内侧的检测线圈63A与外侧的检测线圈63B,可在相同的通过轨迹上、在相同的时点连续测量半导体晶片W的金属膜(或导电性膜)。即,可在同一通过轨迹上,内侧的检测线圈63A检测目标金属膜(或导电性膜)的微细区域(第1区域)的涡电流,测量金属膜(或导电性膜),外侧的检测线圈63B检测包含所述微细区域(第1区域)的较宽区域(第2区域)的涡电流,测量金属膜(或导电性膜)。如图4(b)所示,与所述内侧及外侧的检测线圈63A、63B对应,以内侧的励磁线圈62A的外径为D1,以外侧的励磁线圈62B的外径为D2,设定为D2>>D1。如此,通过设定内侧的励磁线圈62A和外侧的励磁线圈62B的外径,内侧及外侧的励磁线圈62A、62B各自可在目标金属膜(或导电性膜)的微细区域(第1区域)和包含该微细区域(第1区域)的较宽区域(第2区域)分别形成涡电流。另外,虽然说明的是励磁线圈62A、62B的外径各自与检测线圈63A、63B的外径相同,当然,励磁线圈62A、62B的外径和检测线圈63A、63B的外径也可分别不相同。如此,本发明的涡电流传感器50由,具备有励磁线圈62A、检测线圈63A、虚设线圈64A的内侧的传感器线圈60A,和配置为包围内侧的传感器线圈60A、且具备有励磁线圈62B、检测线圈63B、虚设线圈64B的外侧的传感器线圈60B构成。因此,内侧的传感器线圈60A作为高灵敏度的传感器发挥作用,在目标金属膜变薄和金属膜的面积变小时也可检测金属膜,可进行半导体晶片(基板)W的被研磨面上的详细的残膜分布检测及半导体晶片W的边缘部分的薄膜检测。另一方面,外侧的传感器线圈60B作为低灵敏度的传感器发挥作用,可正确检测半导体晶片的被研磨面整体的残膜,可稳定进行研磨终点的检测。此外,内侧的传感器线圈60A与外侧的传感器线圈60B,由于在相同的通过轨迹上、在同一时点与金属膜(或导电性膜)反应而分别输出,因此通过比较两个输出,可以进行高精度的金属膜(或导电性膜)检测。接着,说明本发明的涡电流传感器50的变形例。图4至图13所示的实施形态中,说明的是线圈外径不同的多个传感器线圈60A、60B互相分离配置为外侧的传感器线圈60B包围内侧的传感器线圈60A的构成的涡电流传感器50,但也可以是传感器线圈60A、60B中的同一种类线圈的相互线圈位置重叠配置而构成的涡电流传感器50。图14是表示传感器线圈60A、60B中的同一种类线圈的相互线圈位置重叠配置的构成例子的概略图。如图14所示,本实施形态的涡电流传感器50具备有2个传感器线圈60A、60B。传感器线圈60A由3个线圈62A、63A、64A构成,未采用在线轴61上卷绕的方式。传感器线圈60A的3个线圈62A、63A、64A,将“列”定义为对于半导体晶片(基板)W为垂直方向、“层”定义为对于半导体晶片(基板)W为平行方向时,是将线材或导电体ln各自卷绕1列N层而卷为螺旋状的线圈。此外,外侧的传感器线圈60B由3个线圈62B、63B、64B构成,未采用在线轴61上卷绕的方式。将“列”定义为对于半导体晶片(基板)W为垂直方向、“层”定义为对于半导体晶片(基板)W为平行方向时,传感器线圈60B的3个线圈62B、63B、64B是将线材或导电体ln各自卷绕1列N层而卷为螺旋状的线圈。如图14所示,检测线圈63A的外径D1大于检测线圈63B的内径DIN,2个检测线圈63A、63B的线圈位置在列方向重叠。励磁线圈62A的外径也同样地大于励磁线圈62B的内径,2个励磁线圈62A、62B的线圈位置在列方向重叠。此外,虚设线圈64A的外径也大于虚设线圈64B的内径,2个虚设线圈的线圈位置在列方向重叠。如图14所示构成的涡电流传感器50中,传感器线圈60A中的检测线圈63A、励磁线圈62A、虚设线圈64A的外径也小于传感器线圈60B中的检测线圈63B、励磁线圈62B、虚设线圈64B的外径。例如,比较图14所示的涡电流传感器50中的检测线圈63A与检测线圈63B的话,检测线圈63A的外径为D1、检测线圈63B的外径为D2,设定为D2>>D1。即,通过使检测线圈63A的外径D1较小,检测线圈63A可检测目标金属膜(或导电性膜)的微细区域(第1区域)的涡电流。然后,外径大的检测线圈63B可检测包含检测线圈63A的测量区域(第1区域)的较宽区域(第2区域)的涡电流。与所述检测线圈63A、63B对应,以励磁线圈62A的外径为D1、以励磁线圈62B的外径为D2,设定为D2>>D1。如此,通过设定励磁线圈62A与励磁线圈62B的外径,励磁线圈62A、62B各自可在目标金属膜(或导电性膜)的微细区域(第1区域)与包含该微细区域(第1区域)的较宽区域(第2区域)分别形成涡电流。另外,说明的是励磁线圈62A、62B的外径各自与检测线圈63A、63B的外径相同,当然,励磁线圈62A、62B的外径与检测线圈63A、63B的外径也可各自不相同。检测线圈63B与励磁线圈62A之间设置有用于使检测线圈63B与励磁线圈62A之间的间隔保持一定的垫片S1,励磁线圈62B与虚设线圈64A之间设置有用于使励磁线圈62B与虚设线圈64A之间的间隔保持一定的垫片S2。然后,与虚设线圈64B邻接配置有线轴61。另外,检测线圈63B与励磁线圈62A之间以及励磁线圈62B与虚设线圈64A之间,设置距离即可,不特别设置垫片、仅设置空间也可。接着,由图4至图14所示的外径大的传感器线圈与外径小的传感器线圈构成的本发明中,对于1列N层的线圈m个串联连接的具体形态,参照图15(a)、(b)、(c)进行说明。图15(a)是表示外径大的线圈包围外径小的线圈时2个的线圈串联连接形态的概略图。如图15(a)所示,内侧的传感器线圈60A中的检测线圈63A、励磁线圈62A、虚设线圈64A各自为线材或导电体1n卷绕1列N层而卷成螺旋状的线圈2个串联连接构成。此外,外侧的传感器线圈60B中的检测线圈63B、励磁线圈62B、虚设线圈64B各自为线材或导电体1n卷绕1列N层而卷成螺旋状的线圈2个串联连接构成。2个的线圈串联连接时,可在线圈的内径侧连接,也可在外径侧连接。1列N层的线圈2个串联连接时,各线圈相互接触的话,容量会增加,因此将1列N层的线圈在列方向(对于基板的垂直方向)2个排列,在邻接的线圈间设置空隙,该空隙中设置介电常数低的材料E1、E2、E3。此外,检测线圈、励磁线圈、虚设线圈中的邻接的2个线圈间,与图4(b)所示的例子相同地设置有垫片S1、S2。图15(b)是表示外径大的线圈配置为对着半导体晶片(基板)W的金属膜形成面的垂直方向夹着外径小的线圈时,2个线圈串联连接形态的概略图。如图15(b)所示,内侧的传感器线圈60A中的检测线圈63A、励磁线圈62A、虚设线圈64A各自为线材或导电体1n卷绕1列N层而卷成螺旋状的线圈2个串联连接构成。此外,外侧的传感器线圈60B中的检测线圈63B、励磁线圈62B、虚设线圈64B各自为线材或导电体1n卷绕1列N层而卷成螺旋状的线圈2个串联连接构成。2个线圈串联连接时,可在线圈的内径侧连接,也可在外径侧连接。检测线圈、励磁线圈、虚设线圈中邻接的2个线圈间设置有垫片S1、S2,这与图15(a)的情况相同。此外,虽未图示,但在邻接的小线圈间设置空隙、在该空隙设置介电常数低的材料,这也与图15(a)的情况相同。图15(c)是表示外径小的线圈配置为相对半导体晶片(基板)W的金属膜形成面为垂直方向夹着外径大的线圈时,2个线圈串联连接形态的概略图。如图15(c)所示,内侧的传感器线圈60A中的检测线圈63A、励磁线圈62A、虚设线圈64A各自为线材或导电体1n卷绕1列N层而卷成螺旋状的线圈2个串联连接构成。此外,外侧的传感器线圈60B中的检测线圈63B、励磁线圈62B、虚设线圈64B各自为线材或导电体1n卷绕1列N层而卷成螺旋状的线圈2个串联连接构成。2个线圈串联连接时,可在线圈的内径侧连接,也可在外径侧连接。检测线圈、励磁线圈、虚设线圈中邻接的2个线圈间设置有垫片S1、S2,这与图15(a)的情况相同。此外,虽未图示,但在邻接的大线圈间设置空隙、在该空隙设置介电常数低的材料,这也与图15(a)的情况相同。图4至图15中显示了外径大的线圈与外径小的线圈的组合,但本发明也包含线圈的中心直径有大小的传感器线圈的组合。图16(a)、(b)是表示线圈的中心直径有大小时2个线圈串联连接形态的概略图。图16(a)、(b)中,线圈的内径与外径的算术平均定义为线圈中心直径的话,以线圈中心直径大的作为外侧的线圈、以线圈中心直径小的作为内侧的线圈进行说明。图16(a)、(b)所示的形态中,外侧的传感器线圈60B中的检测线圈63B、励磁线圈62B、虚设线圈64B的线圈中心直径,设定为大于内侧的传感器线圈60A中的检测线圈63A、励磁线圈62A、虚设线圈64A的线圈中心直径。检测线圈63A(63B)、励磁线圈62A(62B)、虚设线圈64A(64B)各自为线材或导电体1n卷绕1列N层而卷成螺旋状的线圈2个串联连接构成。比较图16(a)、(b)所示的涡电流传感器50中的检测线圈63A与检测线圈63B的话,检测线圈63A的线圈中心直径为Dc1、检测线圈63B的线圈中心直径为Dc2,设定为Dc2>Dc1。即,通过使检测线圈63A的线圈中心直径Dc1较小,检测线圈63A可检测目标金属膜(或导电性膜)的微细区域(第1区域)的涡电流。然后,线圈中心直径大的检测线圈63B可检测包含检测线圈63A的测量区域(第1区域)的较宽区域(第2区域)的涡电流。与所述检测线圈63A、63B对应,以励磁线圈62A的线圈中心直径为Dc1、以励磁线圈62B的线圈中心直径为Dc2,设定为Dc2>Dc1。如此,通过设定励磁线圈62A与励磁线圈62B的线圈中心直径,励磁线圈62A、62B各自可在目标金属膜(或导电性膜)的微细区域(第1区域)和含有该微细区域(第1区域)的较宽区域(第2区域)分别形成涡电流。另外,虽然说明的是励磁线圈62A、62B的线圈中心直径各自与检测线圈63A、63B的线圈中心直径相同,当然,励磁线圈62A、62B的线圈中心直径与检测线圈63A、63B的线圈中心直径也可各自不相同。另外,虚设线圈64A、64B的线圈中心直径各自设定为与检测线圈63A、63B的线圈中心直径相同。检测线圈、励磁线圈、虚设线圈中的邻接的2个线圈间,如图4(b)所示的例子相同地设置有垫片S1、S2。此外,虽未图示,但邻接的线圈间可设置空隙、该空隙间可设置介电常数低的材料,这与图15(a)的情况相同。图17是显示传感器线圈60A、60B的各线圈62A、62B;63A、63B;64A、64B中励磁线圈62A、62B的形状形成为凹球面状的例子的概略图。如图17所示,励磁线圈62A、62B,是半径方向内侧向虚设线圈一侧凹下、随着靠近半径方向外侧而弯曲为凹球面状接近检测线圈一侧、卷绕了线材或导电体的线圈。螺旋形卷绕的传感器线圈,通过令振荡磁场变化,可令灵敏度变化。因此,如图17所示,通过令励磁线圈62A、62B弯曲形成为凹球面状,可令振荡磁场收敛至中央部,可提升传感器灵敏度。图18是显示图4(b)所示的传感器线圈的周围配置了高磁导率材料构成的筒状部件的概略图。如图18所示,传感器线圈60A、60B的线轴61及3个外侧线圈62B、63B、64B的周围被高磁导率材料构成的筒状部件65包围。筒状部件65通过使用例如相对磁导率μ=50的高磁导率材料(例如铁素体、非晶质、坡莫合金、超坡莫合金、导磁合金(μ-metal))制作,可以令传感器线圈的周围环境为空气的情况下的50倍的磁通量通过。换言之,较之于设置在陶瓷材料等的电气绝缘材料的周围环境内的情况,在1/50的厚度内可通过同等的磁通量。如图18所示,通过传感器线圈的周围配置有高磁导率材料构成的筒状部件65,即使研磨台100由不锈钢(SUS)材料等导电性材料制作而成,向配置在筒状部件65内的传感器线圈60A、60B的励磁线圈62A、62B提供电流所形成的磁通量,不会令研磨台内发生涡电流、使得测定所需要的大小的磁通量路径(磁路)变小,可使得半导体晶片W的金属膜获得可有效产生涡电流的路径。即,筒状部件65,不会使传感器线圈60A、60B的励磁线圈62A、62B产生的磁通量通入研磨台100的导电性母材内,作为半导体晶片W侧的检测空间内的扩展路径发挥作用,该磁通量可令测定对象金属膜(或导电性膜)mf内产生大的涡电流。因此,即使研磨台100由不锈钢(SUS)等导电性材料制作而成,也可确保与SiC等陶瓷材料(绝缘材料)制作时同样的灵敏度。图4至图9所示的螺旋形卷绕、多角形卷绕、椭圆卷绕等的卷绕1列N层的多个检测线圈互相分离配置为外侧的检测线圈包围内侧的检测线圈,该构成也可利用于检测线圈与电容器并联连接、构成科尔皮兹电路而励磁、具有检测功能的根据励磁频率的频率变化检测研磨终点的传感器。图4至图18所示的实施形态中,显示的是检测线圈、励磁线圈及虚设线圈各自在半径方向内侧与半径方向外侧配置的构成例子,当然,检测线圈、励磁线圈及虚设线圈各自也可以是从半径方向内侧向着外侧成同心圆状(或近同心圆状)配置3个以上。图19是显示螺旋形卷绕的3个检测线圈63A、63B、63C成同心圆状配置的例子。3个检测线圈63A、63B、63C均为线材或导电体ln各自卷绕1列N层而卷成螺旋状的线圈,可通过印刷配线(printedwiring)一体形成。如图19所示,根据3个检测线圈63A、63B、63C成同心圆状配置的涡电流传感器50,配置在最内周的检测线圈63A的外径D1、配置在中间部的检测线圈63B的外径D2、配置在最外周的检测线圈63C的外径D3的关系为D1<D2<D3。如此,通过使最内周侧的检测线圈63A的外径D1减小,最内周侧的检测线圈63A可检测目标金属膜(或导电性膜)的微细区域(第1区域)的涡电流。然后,中间部的检测线圈63B可检测包含最内周侧的检测线圈63A的测量区域(第1区域)的较宽区域(第2区域)的涡电流,最外周侧的检测线圈63C可检测包含中间部的检测线圈63B的测量区域的更宽区域(第3区域)的涡电流。另外,3个励磁线圈及3个虚设线圈也与图19同样构成。图20是表示传感器线圈60A中的各线圈的电路构成的概略图。图20中,仅显示线圈62A、63A、64A构成的传感器线圈60A的电路构成,由于线圈62B、63B、64B构成的传感器线圈60B的电路构成也相同,因此省略图示及说明。如图20(a)所示,线圈62A、63A、64A由1列N层的卷成螺旋形的线圈形成,检测线圈63A与虚设线圈64A互相逆相连接。检测线圈63A与虚设线圈64A如上所述,构成逆相的串联电路,其两端与包含可变电阻76的电阻桥接电路77连接。励磁线圈62A与交流信号源52连接,通过生成交变磁通,使配置在附近的金属膜(或导电性膜)mf上形成涡电流。通过调整可变电阻76的电阻值,线圈63A、64A构成的串联电路的输出电压,当不存在金属膜(或导电性膜)时可调整为零。各个线圈63A、64A通过并列进入的可变电阻76(VR1、VR2)将与L1、L3的信号调整为同相位。即,图20(b)的等效电路中,为使VR1-1×(VR2-2+jωL3)=VR1-2×(VR2-1+jωL1)(1)调整可变电阻VR1(=VR1-1+VR1-2)及VR2(=VR2-1+VR2-2)。由此,如图20(c)所示,调整前的L1、L3的信号(图中虚线所示)为同相位、同振幅的信号(图中实线所示)。然后,金属膜(或导电性膜)存在于检测线圈63A附近时,因金属膜(或导电性膜)中形成的涡电流而产生的磁通量与检测线圈63A和虚设线圈64A互连,由于检测线圈63A配置在接近金属膜(或导电性膜)的位置,因此两线圈63A、64A产生的感应电压的平衡消失,由此可以检测因金属膜(或导电性膜)的涡电流而形成的互连磁通量。即,从与交流信号源相连接的励磁线圈62A分离出检测线圈63A和虚设线圈64A的串联电路,通过电阻桥接电路进行平衡调整,可调整零点。因此,金属膜(或导电性膜)中流通的涡电流可从零状态检测,因而金属膜(或导电性膜)中的涡电流的检测灵敏度提升。由此,可在较宽的动态范围内检测金属膜(或导电性膜)上形成的涡电流的大小。图21是表示涡电流传感器的同步检波电路的框图。图21显示的是从交流信号源52一侧观察传感器线圈60A一侧的电阻Z的测量电路例子。图21中,仅显示了传感器线圈60A的测量电路,但由于传感器线圈60B的测量电路也相同,因此省略图示及说明。图21所示的电阻Z的测量电路中,可取出伴随膜厚变化的电阻成分(R)、电抗成分(X)、振幅输出(Z)及相位输出(tan-1R/X)。如上所述,向配置在检测对象金属膜(或导电性膜)mf成膜的半导体晶片W附近的传感器线圈60A提供交流信号的信号源52,是由水晶振荡器构成的固定频率的振荡器,例如,提供2~32MHz的固定频率的电压。信号源52形成的交流电压,通过带通滤波器82提供给传感器线圈60A。传感器线圈60A的端子所检测到信号,经过高频放大器83及移相电路84,通过由cos同步检波电路85及sin同步检波电路86构成的同步检波部,取出检测信号的cos成分与sin成分。在这里,信号源52形成的振荡信号,通过移相电路84形成信号源52的同相成分(0゜)和正交成分(90゜)2个信号,各自被导入cos同步检波电路85与sin同步检波电路86,进行上述的同步检波。被同步检波的信号,通过低通滤波器87、88,除去信号成分以上的不要的高频成分,各自取出cos同步检波输出的电阻成分(R)输出和sin同步检波输出的电抗成分(X)输出。此外,通过向量运算电路89,从电阻成分(R)输出与电抗成分(X)输出可得到振幅输出(R2+X2)1/2。此外,通过向量运算电路90,同样从电阻成分输出与电抗成分输出可得到相位输出(tan-1R/X)。在这里,测定装置本体上,设置的各种滤波器用于除去传感器信号的噪声成分。各种滤波器设定为各自对应的截止频率,例如,通过将低通滤波器的截止频率设定在0.1~10Hz的范围,可除去研磨中的传感器信号中混杂的噪声成分,可高精度测定对象金属膜(或导电性膜)。图22是表示具备有涡电流传感器50的研磨装置的主要构成的图,图22(a)是表示包含涡电流传感器50的控制部的整体构成图,图22(b)是涡电流传感器部分的放大截面图。如图22(a)所示,研磨装置的研磨台100如箭头所示,可绕其轴心旋转。该研磨台100内,埋设有包含交流信号源及同步检波电路的前置放大器一体型的传感器线圈60A、60B。传感器线圈60A、60B的各连接电缆通过研磨台100的台轴100a内,经过设置在台轴100a轴端的旋转接头150,通过电缆介着主放大器55与控制装置(控制器)56连接。另外,传感器线圈60A、60B有时与主放大器55成一体。在这里,控制装置56中,设置有用于除去传感器信号的噪声成分的各种滤波器。各种滤波器设定为各自对应的截止频率,例如,通过将低通滤波器的截止频率设定在0.1~10Hz的范围,可除去研磨中的传感器信号中混杂的噪声成分,可高精度测定对象金属膜(或导电性膜)。如图22(b)所示,通过埋设在研磨台100中的涡电流传感器50的研磨垫一侧的端面具有四氟化乙烯树脂等氟系树脂的涂层C,取下研磨垫时,研磨垫与涡电流传感器不会被共同取下。此外,涡电流传感器的研磨垫一侧的端面,被设置在从研磨垫101附近的SiC等材料构成的研磨台100的面(研磨垫一侧的面)凹下0~0.05mm的位置,可防止研磨时与晶片接触。该研磨台面与涡电流传感器面的位置差尽可能小的话比较好,但实际装置中大多设定在0.02mm左右。此外,该位置的调整可采取垫片(薄板)151m调整和螺丝调整的方法。在这里,连接传感器线圈60A、60B与控制装置56的旋转接头150,在旋转部也可传送信号,但传送的信号线数有限制。因此,连接的信号线限制为8根,仅限于DC电压源、输出信号线及各种控制信号的传送线。另外,该传感器线圈60,振荡频率可在2~32MHz切换,前置放大器的增益也可根据研磨对象的膜质切换。接着说明具备有图1至图22所示构成的涡电流传感器的研磨装置中,检测研磨中的半导体晶片上的金属膜(或导电性膜)、进行监视的方法。如图20及图21中所说明的,2个传感器线圈60A、60B分别与传感器电路连接,因此,传感器线圈60A与传感器线圈60A用的传感器电路成一体,构成1个传感器,传感器线圈60B与传感器线圈60B用的传感器电路成一体,构成1个传感器。以下,将传感器线圈60A与传感器电路构成的传感器称为传感器径小的传感器,将传感器线圈60B与传感器电路构成的传感器称为传感器径大的传感器,两者区别说明。所述传感器径小的传感器指的是,如图4(b)、(c)及图14所示的小线圈外径(D1)的传感器及图16所示的小线圈中心直径(Dc1)的传感器,所述传感器径大的传感器指的是,如图4(b)、(c)及图14所示的大线圈外径(D2)的传感器及图16所示的大线圈中心直径(Dc2)的传感器。对于传感器径小的传感器及传感器径大的传感器的具体大小(尺寸),由于与研磨头(顶环)的压力室的尺寸相关并定义,因此在说明了压力室的构造后再说明。接着,说明传感器径大的传感器与传感器径小的传感器中的大小励磁线圈的输出频率相同和不同的情况。大小励磁线圈的输出频率相同时,大小检测线圈,尽管检测区域有大小,但检测同一频率的涡电流。大小励磁线圈的输出频率不同时,大小检测线圈,在检测线圈一侧各自设置规定的滤波器,可各自检测不同频率的涡电流。图23(a)显示的是涡电流传感器50扫描(scan)半导体晶片W的表面(被研磨面)时的轨迹与涡电流传感器50的输出的关系。如图23(a)所示,涡电流传感器50中的传感器径小的传感器与传感器径大的传感器,在伴随研磨台100的旋转而通过半导体晶片W下方的期间,与半导体晶片W的金属膜(或导电性膜)mf反应,各自输出规定的电压值(V)。传感器径小的传感器与传感器径大的传感器,在同一通过轨迹上与金属膜反应并输出,因此可以进行传感器输出的比较。图23(b)显示的是半导体晶片W的研磨开始时的涡电流传感器50的输出的图。图23(b)中,横轴为研磨时间(t),纵轴为涡电流传感器50的输出值(电压值)(V)或与膜厚相当的输出值,传感器径小的传感器的输出以细实线显示,传感器径大的传感器的输出以粗实线显示。如图23(b)所示,涡电流传感器50中的传感器径小的传感器与传感器径大的传感器,均可得到与半导体晶片上的金属膜(或导电性膜)mf反应的大致方形脉冲状的输出(电压值)。然后,电位从Low级别转变为High级别的上升沿时的输出、以及从High级别转变为Low级别的下降沿时的输出,传感器径小的传感器较传感器径大的传感器更陡。即,表示检测半导体晶片W的边缘部的残膜时,传感器径小的传感器较传感器径大的传感器的晶片,直径方向的分解能和灵敏度高。图23(c)是表示从半导体晶片W的研磨开始至规定时间后的涡电流传感器50的输出的图。图23(c)中,横轴为研磨时间(t),纵轴为涡电流传感器50的输出值(电压值)(V)或与膜厚相当的输出值,传感器径小的传感器的输出以细实线显示,传感器径大的传感器的输出以粗实线显示。如图23(c)的下图所示,半导体晶片上的金属膜(或导电性膜)上有同心圆状的较厚的部分和较薄的部分,但传感器径小的传感器较传感器径大的传感器,对半导体晶片上的金属膜(或导电性膜)的厚度敏感反应。因此,传感器径小的传感器适宜进行半导体晶片(基板)W的被研磨面上的详细的残膜分布检测及半导体晶片W的边缘部分的薄膜检测。研磨中对剖面的差异(例如,目标剖面与研磨中的剖面的差异)通过传感器径小的传感器同时监视,剖面持续发生异常时,输出警示。与此相对,传感器径大的传感器可正确检测半导体晶片的被研磨面整体的残膜,适宜稳定进行研磨终点的检测。图24是表示半导体晶片W的研磨开始至半导体晶片W上的中心部的金属膜(或导电性膜)mf消除(变无)为止的研磨工序与涡电流传感器50的输出的关系的图。如图24所示,半导体晶片W的研磨开始时,由于金属膜(或导电性膜)mf较厚,涡电流传感器50中的传感器径小的传感器(小口径传感器)与传感器径大的传感器(大口径传感器)的输出均变高,但随着研磨的进行,由于金属膜mf变薄,涡电流传感器50中的传感器径小的传感器与传感器径大的传感器的输出均下降。此时,研磨中产生的半导体晶片W上的小凹凸中,传感器径大的传感器如虚线dl所示不进行响应,因此终点检测时不会受到不要的凹凸的影响。与此相对,传感器径小的传感器,对于半导体晶片W上的小凹凸会进行响应,出现小的V形的输出值。然后,变为晶片中心部的金属膜消失、晶片端部有金属残膜的状态后,传感器径大的传感器的输出值变无,检测研磨终点。此时,传感器径小的传感器上,仅晶片端部一侧有输出值。另外,通过令频率切换和励磁线圈流通的电流变化,进行终点检测时可选择最佳状态。图25是表示半导体晶片W上的金属膜(或导电性膜)的研磨工序及监视工序顺序的流程图。如图25所示,研磨装置从晶片盒取出半导体晶片W,交接至顶环1,通过顶环1将半导体晶片W向研磨台100上的研磨面101a按压,开始研磨。开始研磨后,控制装置56监视涡电流传感器50中的传感器径小的传感器与传感器径大的传感器的输出值,在检测到研磨终点前持续进行研磨,持续涡电流传感器50中的传感器径小的传感器与传感器径大的传感器的输出值的监视工序。研磨终点的检测,通过检测传感器径大的传感器的输出值达到金属膜消失的程度而进行。检测到研磨终点后,不令半导体晶片W离开研磨面(研磨垫),过渡至残膜监视。残膜监视,通过监视传感器径小的传感器是否有输出值而进行。虽然图24显示的是晶片端部有残膜的情况,但在被研磨面上局部(例如,晶片中心部、晶片中间部等)有残膜的话,传感器径小的传感器对此进行检测后输出。接着,将残膜监视所得到的信息传达至控制CMP工艺整体的控制装置(过程控制器(未图示))。另外,控制CMP工艺整体的控制装置(过程控制器),可以是包含所述控制装置56的单一的控制装置,也可以是控制装置56外的别的控制装置。控制装置(过程控制器),根据残膜监视的信息判定是否需要实施追加研磨。然后,判定为需要实施追加研磨时,实施追加研磨,进行残膜监视,确认到没有残膜后,过渡至洗净工序。另一方面,判定为CMP的工序有异常时,并不实施追加研磨,而是在通知研磨剖面异常后,过渡至洗净工序。洗净工序,是将完成研磨的半导体晶片从顶环1取下后,通过研磨装置内的洗净机进行擦洗洗净、纯水洗净、干燥等。然后,洗净工序结束后,将完成研磨的半导体晶片W回收至晶片盒。接着,对于图25所示流程图中的残膜监视及追加研磨进一步进行说明。残膜监视是在晶片的主研磨处理后的水抛光中或过抛光中实施。在这里,水抛光指的是,向研磨面提供纯水(水)的同时减小施加在晶片上的面压,进行抛光。此外,过抛光指的是,在检测到特征点后向研磨面提供浆料的同时进行规定时间抛光的方法。残膜监视中检测到残膜时的追加研磨如下进行。作为追加研磨的实施方法,是在过抛光中检测到残膜时,改变过抛光的研磨时间。此外,通过残膜监视检测到晶片的特定位置点有残膜时,通过令检测到的特定位置点的顶环的压力变化而进行追加研磨,或者以专用的研磨条件进行追加研磨。追加研磨条件反馈为研磨之后的半导体晶片时的研磨条件。残膜监视中检测到残膜时,通常,实施追加研磨而除去金属薄膜。但是,通过追加研磨保持了晶片平坦性的情况下,由于CMP的工序有时有异常,因此可将研磨剖面的异常通知给研磨装置的控制装置。接着,对于上述的研磨终点及残膜监视方法,与以往的方法进行对比说明。从研磨开始至目标金属膜消失为止,仅使用具有规定灵敏度的传感器(传感器A)的情况下,目标金属膜变薄和金属膜面积变小时,金属膜的检测变得困难。另一方面,仅使用薄膜用传感器(传感器B)检测研磨终点的情况下,初期金属膜较厚时,输出会超出额定范围(测定范围外),因此无法监视研磨工序。因此,以往会使用灵敏度不同的2个传感器A、B,从研磨开始至传感器A的灵敏度变无为止监视输出,实施研磨终点的检测后,切换为传感器B,通过传感器B进行残膜监视,确认晶片上无金属残膜。与此相对,使用具备有传感器径小的传感器与传感器径大的传感器的一体单元的本发明的涡电流传感器50的情况下,如图24所示,半导体晶片W的研磨开始时,由于金属膜(或导电性膜)mf较厚,传感器径大的传感器的输出变高,但随着研磨的进行,由于金属膜mf变薄,传感器径大的传感器的输出下降。然后,变为“晶片中心部金属膜消失/晶片端部有金属残膜”的状态的话,传感器径大的传感器变为传感器灵敏度零的状态。因此,传感器径大的传感器实施研磨终点的检测。此时,传感器径小的传感器,由于较传感器径大的传感器的晶片直径方向的分解能和灵敏度高,因此晶片端部一侧的输出值变大为山形,可检测“晶片中心部金属膜消失/晶片端部有金属残膜”的状态。因此,通过传感器径小的传感器的输出值监视,可检测局部的面积小的残膜的发生。图26是表示通过监视涡电流传感器50中的传感器径小的传感器得到的输出值而检测局部残膜发生时,晶片下层的金属配线等的影响的图。图26(a)显示的是不受晶片下层影响的情况,图26(b)显示的是受到晶片下层的金属配线等的影响的情况。如上所述,通过监视传感器径小的传感器的各测定点的输出值,可检测局部面积的小残膜的发生。但是,由于传感器径小的传感器的传感器灵敏度高,因此可能受到金属膜下层的金属配线等的影响。因此,如图26(b)所示,输出上升的点较多时,判断为不是残膜,还是晶片下层的影响。接着,对涡电流传感器50扫描半导体晶片的表面时的轨迹(扫描线)进行说明。本发明中,为了使规定时间内(例如,移动平均时间内)涡电流传感器50在半导体晶片W上描绘的轨迹在半导体晶片W的表面整周大致均匀分布,而调整顶环1与研磨台100的转速比。图27是显示涡电流传感器50扫描半导体晶片W上的轨迹的示意图。如图27所示,涡电流传感器50,在研磨台100每旋转1周时扫描半导体晶片W的表面(被研磨面),研磨台100旋转的话,涡电流传感器50大致描绘出通过半导体晶片W的中心Cw(顶环轴111的中心)的轨迹,在半导体晶片W的被研磨面上进行扫描。通过令顶环1的转速与研磨台100的转速不同,半导体晶片W的表面中的涡电流传感器50的轨迹,如图27所示,伴随研磨台100的旋转,变化为扫描线SL1、SL2、SL3、…。此时也如上所述,由于涡电流传感器50配置于通过半导体晶片W的中心Cw的位置,因此涡电流传感器50描绘的轨迹毎次都会通过半导体晶片W的中心Cw。图28是表示研磨台100的转速为70min-1、顶环1的转速为77min-1、移动平均时间(该例子中为5秒)内涡电流传感器50描绘的半导体晶片上的轨迹的图。如图28所示,该条件下,研磨台100每旋转1周,涡电流传感器50的轨迹为旋转36度,因此每进行5次扫描,传感器轨迹仅在半导体晶片W上旋转半周。也考虑传感器轨迹的弯曲的话,通过移动平均时间内涡电流传感器50对半导体晶片W进行6次扫描,涡电流传感器50在半导体晶片W上进行大致均等的全面扫描。上述的例子中,显示的是顶环1的转速快于研磨台100的转速的情况,当顶环1的转速慢于研磨台100的转速时(例如,研磨台100的转速为70min-1、顶环1的转速为63min-1),传感器轨迹仅是向反方向旋转,在规定时间内令涡电流传感器50描绘半导体晶片W表面的轨迹分布在半导体晶片W的表面整周这一点与上述的例子相同。此外,上述的例子中,虽然说明了顶环1与研磨台100的转速比接近1的情况,但转速比接近0.5和1.5、2等(0.5的倍数)时也相同。即,顶环1与研磨台100的转速比为0.5时,研磨台100每旋转1周,传感器轨迹旋转180度,从半导体晶片W观察的话,涡电流传感器50每旋转1周,从反方向在同一轨迹上移动。于是,使顶环1与研磨台100的转速比稍稍偏离0.5(例如,使顶环1的转速为36min-1、研磨台100的转速为70min-1),使研磨台100每旋转1周传感器轨迹旋转(180+α)度的话,可使得传感器轨迹外观上为偏离α度。因此,设定α为只要在移动平均时间内使传感器轨迹仅在半导体晶片W的表面上旋转约0.5次或约N次或约0.5+N次(换言之,0.5的倍数、即0.5×N次(N为自然数))(即,设定顶环1与研磨台100的转速比)即可。通过在移动平均时间内使涡电流传感器50在半导体晶片W的表面描绘的轨迹在整周大致均匀分布,使得也考虑移动平均时间的调整的话,可在较宽范围内选择转速比。因此,也可应对根据研磨液(浆料)的特性等而必须将顶环1与研磨台100的转速比进行较大变更的研磨工序。但是,一般,除了顶环1的转速恰好为研磨台100的转速的一半的情况,涡电流传感器50在半导体晶片W上描绘的轨迹如图25所示般弯曲。因此,即使在规定时间内(例如移动平均时间内)涡电流传感器50在半导体晶片W上描绘的轨迹分布在半导体晶片W的整周,但传感器轨迹并不一定在严格意义上在周向均匀分布。为了使传感器轨迹在半导体晶片W的周向严格均匀分布,必须每个规定时间使传感器轨迹在半导体晶片W的周围恰好仅旋转N次(N为自然数)。该期间内,涡电流传感器50在半导体晶片W的表面全周在周向以均匀的方向、朝向扫描。为了实现它,可例如在研磨台100仅旋转规定次数(自然数)的期间,使顶环1恰好仅旋转与研磨台100的旋转次数不同的次数(自然数),以此确定研磨台100与顶环1的转速。此时,由于如上所述传感器轨迹弯曲,因此传感器轨迹不能说在周向等间隔分布,但以2根传感器轨迹成对考虑的话,可认为传感器轨迹在任意半径位置上在周向均匀分布。图29是其表示例,是表示与图28相同的条件下研磨台100旋转10周期间的半导体晶片W上的传感器轨迹的图。如上,涡电流传感器50,较之于上述的例子,可获取更平均反映了半导体晶片W整面的数据。图30是表示适宜用于本发明的研磨装置中的具备有多个压力室的顶环的模式截面图。顶环1具有与半导体晶片W相接的圆形的弹性垫142和用于支承弹性垫142的夹具板144。弹性垫142的上周端部被夹具板144支承,弹性垫142与夹具板144之间设置有4个压力室(气囊)P1、P2、P3、P4。压力室P1、P2、P3、P4中,各自通过流体管路152、153、154、155被提供加压空气等的加压流体,或者被抽真空。中央的压力室P4为圆形,其他的压力室P3、P2、P1为圆环状。这些压力室P1、P2、P3、P4排列在同心上。压力室P1、P2、P3、P4的内部压力,可通过未图示的压力调整部而令其相互独立变化,由此可以独立调整对半导体晶片W的4个区域、即边缘部、外侧中间部、内侧中间部及中间部的按压力。该例子中,按压结构为压力室P1、P2、P3、P4相互独立地对半导体晶片W进行按压。研磨中的半导体晶片W的金属膜(或导电性膜)mf的膜厚,通过设置于研磨台100的涡电流传感器50(参照图1)进行测定,半导体晶片W的直径方向的膜厚分布通过控制装置56(参照图22)取得。控制装置56根据膜厚分布而控制压力室P1、P2、P3、P4的内部压力,例如,半导体晶片W上的金属膜(或导电性膜)mf的边缘部膜厚厚于中央部的膜厚时,使压力室P1的压力高于压力室P4的压力,使金属膜(或导电性膜)mf的边缘部的研磨压力高于中央部的研磨压力而进行研磨,从而实现期望的研磨剖面。以下说明通过包括具有如图30所示的压力室P1~P4的顶环1和埋设有本发明的涡电流传感器50的研磨台100的研磨装置,使用涡电流传感器50监视半导体晶片W上的金属膜(或导电性膜)时的涡电流传感器50的构成及数据处理方法。本发明中,根据膜厚分布控制压力室P1、P2、P3、P4的内部压力,控制各压力室正下方的膜厚。成同心状设置的压力室P1、P2、P3、P4中的半径方向的宽度,将压力室P1设定为宽度W1、压力室P2为宽度W2、压力室P3为宽度W3、压力室P4为宽度W4,其关系为W1<W2<W3<W4。然后,传感器径小的传感器,传感器径设定为可以检测小于压力室P1半径方向的宽度W1的范围。此外,传感器径大的传感器,传感器径大于传感器径小的传感器,传感器径最大设定为可以检测小于最大的压力室P4的宽度W4的范围。如此,本发明中,传感器的尺寸(传感器径)根据压力室P1~P4的半径方向的宽度W1~W4设定,通过压力室P1~P4,可对应每个半导体晶片W的区域独立控制研磨压力。即,研磨中,对于半导体晶片W的边缘部的膜厚,通过传感器径小于压力室P1半径方向的宽度W1的传感器进行检测,对于半导体晶片W的中央部的膜厚,通过传感器径小于压力室P4半径方向的宽度W4、大于所述传感器径小的传感器的传感器进行检测。如此,本发明中,传感器径小的传感器与传感器径大的传感器,与半导体晶片(基板)W按区域独立按压的多个压力室对应设置,可检测与所述多个压力室对应的每个半导体晶片(基板)W的区域的涡电流。因此,即使是以往难以检测的半导体晶片的边缘部的狭窄区域,也可检测涡电流。以往,即使想要将半导体晶片研磨平坦,但仅边缘部未被研磨、被研磨面呈凹状,相反,仅对边缘部加速研磨而被研磨面变为凸状的情况也很多,此外,由于边缘部宽度窄、难以取测定点,研磨状态的测定也很困难,因而边缘部的研磨控制很困难。与此相对,根据本发明,随着半导体晶片的边缘部的狭窄区域的研磨状态检测精度提升,可提升研磨精度。此外,作为传感器径的决定方法,可以涡电流传感器50中的采样周期和研磨台100的转速为指标。例如,涡电流传感器50的采样周期为1msec时,研磨台100的转速为150rpm的话,每1msec的涡电流传感器50的移动距离为3mm,因此,小的传感器的传感器径设定为3mm,大的传感器的传感器径为大于3mm。对于数据处理方法,以往的涡电流传感器50中的采样周期,是对半导体晶片W的边缘部和中央部以相同的采样周期进行数据处理。但是,由于半导体晶片W的边缘部的监视范围扩大,本发明中,采样频率为以往的10~100倍(或100倍以上),由此在实现提升检测精度的同时实现高效地收集数据。例如,研磨台100的转速为60rpm时,每1msec的涡电流传感器50的移动距离为1.2mm左右。研磨台100的转速上升的话,每1msec的涡电流传感器50的移动距离变大,涡电流传感器50无法充分取得半导体晶片W的边缘部的数据。因此,本发明中,通过令涡电流传感器50的半导体晶片W中的边缘部的数据采样周期与中央部的数据采样周期不同,以此提升分辨率。图31是表示可根据压力室P1~P4的半径方向的宽度设定采样周期的形态的图。图31的左图显示的是涡电流传感器50扫描(scan)半导体晶片W的表面(被研磨面)时的轨迹与涡电流传感器50的输出的关系,图31的右侧图表显示的是涡电流传感器50的输出与压力室P1~P4中的采样周期。如图31所示,可根据压力室P1~P4的半径方向的宽度设定采样周期。如压力室P1、P2,当压力室的半径方向的宽度较小时,使采样周期详细,如压力室P3、P4,随着压力室的半径方向的宽度变大,扩大采样周期。图31所示的例子中,压力室P1、P2中设定为10μsec的采样周期,压力室P3中设定为100μsec的采样周期,压力室P4中设定为1msec的采样周期。如此,本发明中,使采样频率为以往的10~100倍(或100倍以上),在提升检测精度的同时可有效地收集数据。以上对本发明的实施形态进行了说明,但本发明不限定于上述的实施形态,当然可在其技术思想范围内实施各种不同形态。