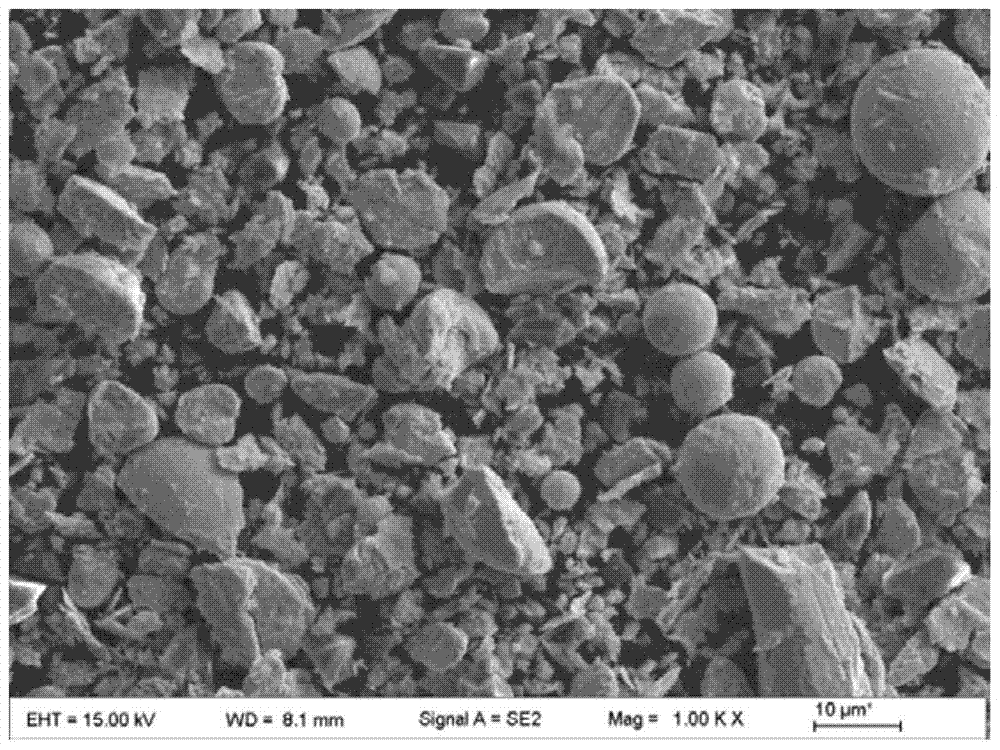
本发明涉及材料表面改性领域,具体涉及一种高硬度金属基/金刚石复合涂层及其高效制备方法。
背景技术:金属陶瓷兼有金属和陶瓷的优点,它密度小、硬度高、耐磨、导热性好,不会因为骤冷或骤热而脆裂。金属陶瓷既具有金属的韧性、高导热性和良好的热稳定性,又具有陶瓷的耐高温、耐腐蚀和耐磨损等特性。主要有烧结铝(铝-氧化铝)、烧结铍(铍-氧化铍)、TD镍(镍-氧化钍)等。由一种或几种陶瓷相与金属相或合金所组成的复合材料,广义的金属陶瓷还包括难熔化合物合金、硬质合金、金属粘结的金刚石工具材料。制备金属陶瓷复合涂层常用的方法有热喷涂法、复合镀法、激光原位合成法、自蔓延燃烧合成法、喷焊法及等离子堆焊法等,如利用超音速火焰喷涂已成功制备出WC系及Cr3C2系金属陶瓷复合涂层,并在诸多工业领域得到了应用。金刚石作为自然界中硬度最高的物质,其作为金属陶瓷复合涂层的强化相已成为国内外的研究热点,各国学者在金属基/金刚石复合涂层的制备方面开展了大量的探索研究。采用热喷涂、喷焊、等离子堆焊、激光熔覆及自蔓延燃烧合成等方法制备金属基/金刚石复合涂层时,固相金刚石颗粒会与高温熔融液态金属粘结相作用,产生热分解与溶解,使金刚石颗粒难以保留在涂层中。因此,无法有效地制备金属基/金刚石复合涂层。复合电镀法和化学镀法虽然避免了上述方法中出现的高温化学反应,能够将金刚石颗粒保留在涂层中,且涂层中金刚石的体积含量可达45%,但是当涂层中金刚石体积含量超过25%时,金刚石与粘结相的界面结合显著恶化,涂层的耐磨性难以提高,同时利用这些方法很难制备厚度超过200μm的金属基/金刚石复合涂层,而且制备效率低、工艺复杂、污染环境,很难实现工业化。近几十年发展起来的冷喷涂法,是一种依靠低温固态颗粒高速碰撞基体后发生强烈塑性变形而沉积形成涂层的一种新型喷涂技术,避免了热喷涂高温沉积过程中可能发生的成分、组织结构的变化,因此适用于温度敏感材料(如纳米材料、非晶材料等)、易氧化材料(如铝、铜、钛等)和易相变材料(如碳基复合材料等)的涂层制备。虽然利用冷喷涂法可以制备金属基/金刚石复合涂层,但复合涂层主要是通过在硬度较软的金属基体(如Al)中添加金刚石的方法来制备,难以制备高硬度的金属基/金刚石复合涂层,且涂层中金刚石颗粒与金属基结合较弱,容易脱落。此外,冷喷涂涂层与基体的结合机制主要是机械咬合,涂层/基体结合力较差,涂层容易剥落。综上所述,目前金属基/金刚石复合涂层的各种制备方法均存在以下一种或几种问题:(1)涂层厚度薄;(2)涂层中金刚石含量低;(3)涂层中金刚石与金属相结合差,容易脱落;(4)涂层中金刚石颗粒容易受热分解;(5)涂层与基体结合力差;(6)难以制备高硬度金属基/金刚石复合涂层。
技术实现要素:本发明针对现有的金属基/金刚石复合涂层制备技术存在的上述不足,提供一种采用硬度>50HRC的金属粉末作为金刚石粘结相的复合涂层及其高效制备方法,解决现有技术制备高硬度金属基/金刚石复合涂层厚度薄、涂层中金刚石颗粒容易脱落、复合涂层中金刚石容易分解、涂层中金刚石体积含量难以超过45%、涂层与基体结合力差等问题。为了达到上述的目的,本发明采用了以下的技术方案:一种金属基/金刚石激光复合涂层的制备方法,包括如下步骤:1)利用球磨法将高硬度金属粉末和金刚石粉末混合均匀形成复合粉末;所述高硬度金属粉末的硬度>50HRC,高硬度金属粉末形状为球形或类球形,粉末粒度为10~20μm;金刚石粉末为不规则形状,粉末粒度为30~50μm;2)将球磨好的复合粉末在还原炉中还原;3)对基体进行预处理;4)利用脉冲激光毛化技术对基体表面进行处理以提高表面粗糙度;采用连续激光辅助冷喷涂的方法在经过脉冲激光毛化处理的基体上同步沉积高硬度金属基/金刚石复合涂层。本发明利用激光毛化技术、激光热处理技术、冷喷涂技术高效制备这种高硬度金属基/金刚石复合涂层,该复合涂层的特征在于高硬度金属基的硬度>50HRC,复合涂层厚度超过1mm,涂层中的金刚石体积含量大于45%。本发明既实现了以高硬度金属粉末作为金刚石粘结相的复合涂层的制备,又通过脉冲激光毛化处理提高了复合涂层与基体的结合强度,最终制备出稳定、优质的高硬度金属基/金刚石复合高耐磨涂层,并实现了基材表面处理与涂层沉积制备的集成化、自动化和高效化。作为优选,所述高硬度金属粉末为镍基粉末、钴基粉末中的一种或多种。进一步优选,所述高硬度金属粉末为Ni55、Ni50、Ni60或stellite20。作为优选,所述步骤1)中,球磨法采用行星式球磨混合,球料比为30~100:1,球磨转速为200~600r/min,球磨时间为2~24h,球磨气氛为氮气或氩气。或者优选,所述步骤1)中,球磨法采用振动式球磨混合,球料比为30~100:1,振动频率为1200r/min,球磨时间为20~60min,球磨气氛为氮气或氩气。作为优选,所述步骤2)中,复合粉末的还原在马弗炉中进行,还原气氛为氢气,还原时间为30min,还原温度为200~400℃。所述基体为任意形状的铁基材料,基体预处理方法为超声波表面清洗或喷砂粗化。作为优选,所述步骤4)中,脉冲激光光斑在前,喷涂粉斑在后,两者间隔小于15mm,连续激光光斑与喷涂粉斑重合,连续激光光束与冷喷涂喷嘴之间的夹角为20~30°,脉冲激光光斑、连续激光光斑、喷涂粉斑三者保持同步移动,移动速度为30~50mm/s。进一步优选,脉冲激光的能量密度为为104~108W/cm2,脉宽为0.5~2ms,波长为1460~1610nm,半导体连续激光的能量密度为3~5×105W/cm2,波长为960~1064nm,半导体连续激光的输出功率通过闭环反馈控温模式实时调整,沉积温度依据高硬度金属粉末的熔点来选择,低于金属粉末的熔点,使其软化但不熔化。进一步优选,冷喷涂工艺参数为载气压力2~3MPa,载气预热温度300~600℃,喷涂距离15~40mm,送粉量40~80g/min,载气为压缩空气或氮气中的一种。一种金属基/金刚石激光复合涂层,采用高硬度金属粉末作为金刚石复合涂层粘结相;复合涂层厚度超过1mm,涂层中金刚石体积比超过45%。本发明与现有技术相比,具有的有益技术效果如下:(1)本发明涉及的高硬度金属基/金刚石涂层是采用基于冷喷涂的技术制备的,保留了冷喷涂低温沉积的特性,避免了高温沉积技术导致的金刚石容易分解和溶解的问题,显著提高了涂层中金刚石的含量;(2)本发明涉及的高硬度金属基/金刚石涂层的制备方法是在冷喷涂的过程中同步引入激光辐照,激光的加热作用使高硬度金属粉末和基体材料得到软化,实现了高硬度金属基/金刚石复合涂层的有效沉积,而且由于高硬度金属粉末塑性变形较充分,其作为粘结相与金刚石颗粒结合良好,涂层中的金刚石颗粒不易脱落;(3)本发明在冷喷涂的过程中引入激光,激光对高硬度金属粉末的软化作用,大大降低了其临界沉积速度,提高了涂层沉积效率。此外,由于冷喷涂技术的低温沉积特性,涂层中热应力较小,且涂层中的残余应力主要为压应力,涂层不易开裂。因此,综合激光的软化作用和冷喷涂的固有特性,实现了高硬度金属基/金刚石的高效制备,涂层厚度显著增加;(4)本发明采用脉冲激光毛化技术代替传统的喷砂技术对基材表面进行粗化处理,避免了喷砂处理时基材表面容易被杂质污染的问题,从而提高了高硬度金属基/金刚石复合涂层与基体的结合强度,涂层不易剥落。此外,实现基材表面粗糙度处理和涂层沉积的一体化加工,提升了技术和设备的自动化、集成化和高效化。(5)本发明涉及的技术可以快速在金属基体上获得毫米级的高硬度金属基/金刚石复合涂层,基体热影响小,适合于薄壁类、精度要求高的零件的修复和强化。附图说明图1为涂层制备方法示意图;图2为Ni60粉末和金刚石粉末球磨混合后的SEM图片;图3为添加20wt%金刚石Ni60基复合涂层宏观形貌;图4为添加20wt%金刚石Ni60基复合涂层显微组织;图5为Ni60基/金刚石复合涂层中金刚石与Ni60的结合图片;图6为添加40wt%金刚石Ni60基复合涂层宏观形貌;图7为添加20wt%金刚石Ni60基激光熔覆涂层宏观形貌;图8为添加20wt%金刚石Ni60基激光熔覆涂层截面显微组织。具体实施方式下面结合附图对本发明的具体实施方式做一个详细的说明。实例1:选用Ni60粉末作为粘结相与金刚石颗粒混合,Ni60粉末平均粒度为18μm,金刚石选用-400目;Ni60粉末和金刚石粉末以4:1质量比在行星式球磨机中混合,球料比为30:1,球磨速度500r/min,混合时间2h,球磨后复合粉末的微观形貌如图2所示;基材选用100×50×10mm的45#钢板;利用激光毛化与激光辅助冷喷涂技术同步制备高硬度金属基/金刚石复合涂层;激光毛化采用光纤激光器,激光脉冲能量密度为106W/cm2,脉宽为1ms,波长为1510nm;喷涂载气为3MPa压缩氮气,载气预热温度为500℃;采用闭环反馈控温模式调整半导体激光功率,控制温度为800℃;毛化处理激光光斑与喷涂区域间隔5mm,喷涂距离为40mm,复合喷涂移动速度30mm/s。20wt%金刚石含量的Ni60基/金刚石复合涂层宏观形貌如图3所示,复合涂层厚度超过1mm,涂层与基体结合很好。涂层中金刚石体积比超过45%,金刚石颗粒分布均匀,复合涂层致密无明显的孔隙,如图4所示;由于扫描速度快,激光加热温度低,涂层中金刚石没有热分解,最大限度地保持金刚石的硬度及形貌,金刚石颗粒与Ni60基体相结合良好,如图5所示。实例2:选用Ni60粉末为粘结相与金刚石颗粒混合,Ni60粉末平均粒度为18μm,金刚石选用-400目;Ni60粉末和金刚石粉末以3:2质量比在振动式球磨机中进行混合,球料比为30:1,球磨时间为60min,振动频率为800r/min;基材选用100×50×10mm的不锈钢板,利用激光毛化与激光辅助冷喷涂技术同步制备高硬度金属基/金刚石复合涂层;激光毛化采用光纤激光器,激光脉冲能量密度为106W/cm2,脉宽为1ms,波长为1510nm;喷涂载气为3MPa压缩氮气,载气预热温度为550℃;采用闭环反馈控温模式调整半导体激光功率,控制温度为800℃;毛化处理激光光斑与喷涂区域间隔5mm,喷涂距离40mm,复合喷涂移动速度30mm/s。40wt%金刚石含量的Ni60基/金刚石复合涂层宏观形貌如图6所示,涂层厚度超过1mm,涂层与基体结合很好。涂层中金刚石体积比超过45%,且分布均匀;复合涂层相比冷喷涂致密,没有明显的孔隙;由于扫描速度快,激光热量积累少,涂层中金刚石没有出现热分解,最大限度地保持金刚石的硬度及形貌,涂层耐磨性好。实例3:选用stellite20粉末为粘结相与金刚石颗粒混合,stellite20粉末平均粒度为20μm,金刚石选用-400目;stellite20粉末和金刚石粉末以4:1质量比在振动式球磨机中进行混合,球料比为60:1,球磨时间为60min,振动频率为1200r/min;基材选用45#钢棒;利用激光毛化与激光辅助冷喷涂技术同步制备高硬度金属基/金刚石复合涂层;激光毛化采用光纤激光器,激光脉冲能量密度为106W/cm2,脉宽为1.5ms,波长为1640nm;喷涂载气为3MPa压缩氮气,载气预热温度为600℃;采用闭环反馈控温模式调整半导体激光功率,控制温度为900℃;毛化处理激光光斑与喷涂区域间隔5mm,喷涂距离30mm,复合喷涂移动速30mm/s。20wt%金刚石含量的stellite20基/金刚石复合涂层厚度超过1mm,涂层与基体结合很好,涂层中金刚石体积比超过45%,且分布均匀;复合涂层相比冷喷涂层致密,没有明显的孔隙和裂纹;由于扫描速度快,激光热量累积较少,涂层中金刚石没有出现热分解,最大限度地保持了金刚石的硬度及形貌。实例4:选用stellite20粉末为粘结相与金刚石颗粒混合,stellite20粉末平均粒度为20μm,金刚石选用-400目;stellite20粉末和金刚石粉末以3:2质量比在行星式球磨机中混合,球料比为40:1,球磨速度600r/min,混合时间1h;基材选用100×50×10mm的17-4PH钢板;利用激光毛化与激光辅助冷喷涂技术同步制备高硬度金属基/金刚石复合涂层;激光毛化采用光纤激光器,激光脉冲能量密度为106W/cm2,脉宽为1.5ms,波长为1640nm;喷涂载气为3MPa压缩氮气,载气预热温度为600℃;采用闭环反馈控温模式调整半导体激光功率,控制温度为900℃;毛化处理激光光斑与喷涂区域间隔8mm,喷涂距离30mm,复合喷涂移动速度30mm/s。40wt%金刚石含量的stellite20基/金刚石复合涂层厚度超过1mm,涂层与基体结合很好,涂层中金刚石体积比超过45%,且分布均匀;复合涂层相比冷喷涂层致密,没有明显的孔隙和裂纹;由于扫描速度快,激光热量累积较少,涂层中金刚石没有明显的热分解,最大限度保持金刚石的硬度及形貌。实例5:选用Ni50粉末为粘结相与金刚石颗粒混合,Ni50粉末平均粒度为20μm,金刚石选用-400目;Ni60粉末和金刚石粉末以7:3质量比在行星式球磨机中混合,球料比为30:1,球磨时间为2h,转速为400r/min,获得混合均匀的复合粉末;基材选用100×50×10mm的2Cr13钢板;利用激光毛化与激光辅助冷喷涂技术同步制备高硬度金属基/金刚石复合涂层;激光毛化采用光纤激光器,激光脉冲能量密度为106W/cm2,脉宽为1.5ms,波长为1640nm;载气为3MPa压缩氮气,载气预热温度为500℃;采用闭环反馈控温模式调整半导体激光功率,控制温度为800℃;毛化处理激光光斑与喷涂区域间隔8mm,喷涂距离30mm,复合喷涂移动速度40mm/s。30wt%金刚石含量的Ni50基/金刚石复合涂层厚度超过1mm,涂层与基体结合很好,涂层中金刚石体积比超过45%,且分布均匀;复合涂层相比冷喷涂层致密,没有明显的孔隙和裂纹;由于扫描速度快,激光热量累积较少,涂层中金刚石没有明显的热分解,最大限度地保持金刚石的硬度及形貌。实例6(对比例):选用Ni60粉末作为粘结相与金刚石颗粒混合,Ni60粉末平均粒度为18μm,金刚石选用-400目;Ni60粉末和金刚石粉末以4:1质量比在行星式球磨机中混合,球料比为30:1,球磨速率100r/min,混合时间0.5h;基材选用100×50×10mm的45#钢板,表面利用喷砂技术除油除锈处理,喷砂使用24目白刚玉,喷砂压力0.8MPa;利用激光熔覆技术制备金属基/金刚石复合涂层;工艺参数为:激光功率1.2kW,熔覆速度10mm/s,送粉率15g/min,熔覆过程使用氩气保护同轴送粉熔覆。20.wt%金刚石含量的Ni60基/金刚石复合熔覆涂层显微组织如图7所示,熔覆涂层表面形貌如图8所示。显然在熔覆过程中金刚石烧蚀和碳化严重,涂层表面有明显的孔洞且疏松;相比激光毛化与激光辅助冷喷涂技术同步复合制备的20.wt%金刚石含量的涂层,熔覆涂层中金刚石含量明显下降,金刚石在熔覆熔池中烧蚀成为球形,且涂层中金刚石碳化严重。需要强调的是:以上仅是本发明的较佳实施例而已,并非对本发明作任何形式上的限制,凡是依据本发明的技术实质对以上实施例所作的任何简单修改、等同变化与修饰,均仍属于本发明技术方案的范围内。