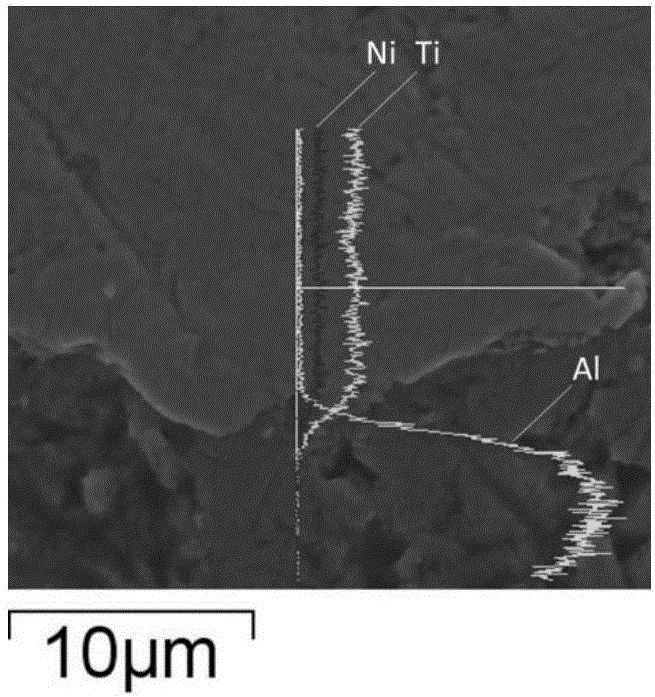
本发明涉涂层制备
技术领域:
,特别涉及一种等离子喷射熔覆制备冶金结合涂层的方法。
背景技术:
:柴油发动机以其燃料经济性好、机动性能好、使用范围广等优点成为了船舶、重型装备的核心和动力来源。近年来,我国的柴油机虽然己经取得了很大发展,但其耐用程度和国际一流水平还有很大差距,而评价内燃机一个重要指标就是看其缸体的耐用度。缸体是内燃机中工作环境最为恶劣的零部件之一,其内壁直接与高温高压燃气接触,承受着很高的燃气爆发压力、瞬变高温及活塞环的往复摩擦作用。随着柴油机强化指标(平均有效压力、活塞平均速度等)的提高,缸体磨损、腐蚀等也随之加快,致使缸体可靠性下降。因此,如何防止缸体失效已经成为一个函待解决的问题。不同机型的船舶柴油机和重型地面装备柴油机对其缸体内表面的基本要求都是相同的,即:抗磨损性、保油性、低摩擦系数、抗燃气腐蚀以及足够的机械强度。目前,为了满足缸体内表面的要求,镀铬、激光淬火、等离子淬火、等离子多元共渗、离子氮化及热喷涂等各种表面技术已经成功应用于缸体内表面的强化。但要对己磨损的缸体实现再制造,往往要求所采用的表面技术必须具备表面强化和尺寸恢复的双重作用。目前能够采用的表面技术主要有镀铬、激光熔覆和热喷涂等。然而这三种表面技术都存在明显的不足,限制了其在我军大、重型装备发动机中的应用。镀铬的不足主要是:①镀层中存在一定量的气孔与砂眼,容易造成腐蚀脱落;②在磨损中镀层容易突然剥落从而造成灾难性失效的倾向;③电镀液有毒性,对环境有污染。激光熔覆的不足主要是:①设备复杂、一次性投入大、使用和维护成本高;②仅适合对不小于内径350mm的孔内壁熔覆;③为防止涂层开裂,涂层材料种类受限,涂层硬度偏低;④在Al合金、Mg合金缸体上制备涂层困难较大。热喷涂的不足主要是:需采用内孔喷枪在缸体内表面制备涂层,涂层质量难以达到理想的程度。这其中一个非常重要的原因就是内孔喷涂环境与外圆喷涂有很大差别,特别是内孔较小、较深时尤为明显。一般缸体的孔径大于等于150mm时,再辅以特殊的喷涂工艺装置,涂层的性能指标才能够满足使用要求。内孔喷涂空间狭小,高温焰流的热量不容易散出,造成环境温度高,基体和喷枪都容易过热;烟尘、粉尘排出困难且在排出过程中也会严重污染涂层,造成内孔涂层质量得不到保证。另外制备的涂层与基体的结合为机械结合,结合强度偏低,发动机工作中涂层容易突然剥落。针对重型柴油发动机缸体实际工况,以及目前各种表面技术无法满足高可靠性缸体内表面强化和恢复尺寸修复的需求现状,需要提供一种新的表面修复与再制造技术。技术实现要素:本发明的目的是克服现有喷涂技术污染性强、涂层结合强度低、涂层制备困难的缺陷,提供了一种等离子喷射熔覆制备冶金结合涂层的方法,形成的涂层含有较多的陶瓷相,涂层硬度较高,耐磨性较高。本发明的另一个目的是克服现有喷涂技术中喷涂速度掌控困难,致使涂层结合强度差的缺陷,提供一种喷涂速度的计算方法,以提高涂层结合强度。本发明提供的技术方案为:一种等离子喷射熔覆制备冶金结合涂层的方法,包括如下步骤:步骤一、对待喷涂工件表面进行清洁;步骤二、预热工件至500~700℃;步骤三、使用等离子喷射枪在工件表面制备涂层,喷射材料为具有自放热反应性能的粉末,在涂层制备过程中保持基体的温度在500~700℃;步骤四、在喷涂环境中自然冷却工件至室温。优选的是,喷涂速度v满足v=15.58π2R3(h-867R)T·cosα]]>其中,R为粉末平均粒径,h为喷涂距离,α为喷涂角度,T为环境温度。优选的是,等离子喷射枪的电弧形式为非转移电弧、转移弧、联合弧中的一种。优选的是,所述喷射材料为Ni包石墨与Ti机械混合的复合粉末,所述Ni包石墨与Ti的质量比为1:1。优选的是,所述喷射材料为Al、Cr2O3、Ti、C的混合造粒烧结复合粉末,Al、Cr2O3、Ti、C的质量比为7:3:2:5。优选的是,所述喷射材料为Al、Cr2O3、Si、C的混合造粒烧结复合粉末,Al、Cr2O3、Si、C的质量比为10:3:2:9。优选的是,所述喷射材料粉末粒径为15~45μm。优选的是,喷涂时的喷射速度为100~350m/s。优选的是,喷射距离为20~60mm。优选的是,步骤一中,采用使用酒精和超声波清洗对工件表面进行清洁处理。本发明的有益效果体现在以下方面:(1)采用的喷射熔覆材料是新研制的具有自放热反应的一种全新材料。自放热反应形成的涂层含有较多的陶瓷相,涂层硬度较高,耐磨性较高。(2)喷射的粒子温度和速度高,粒子速度大于350m/s。(3)设备系统的功能和调整范围宽。(4)与等离子熔覆技术相比较,在基体的喷射斑点处没有明显的熔池,基体的热应力小。(5)可以采用自粘结工艺方法直接满足需要的喷射熔覆层厚度。也可以在冶金自粘结涂层的表面,继续利用非转移弧高速喷射Co-WC、NiCr-Cr3C2等高硬度、高耐磨性材料或其它功能材料,可实现冶金结合底层至高性能面层的梯度涂层制备。附图说明图1为本发明所述的等离子喷射熔覆制备冶金结合涂层的方法的流程图。图2为本发明所述的Al合金表面Ni-Ti-C复合材料喷射熔覆层截面及EDS能谱分析示意图。具体实施方式下面结合附图对本发明做进一步的详细说明,以令本领域技术人员参照说明书文字能够据以实施。本发明提供了一种等离子喷射熔覆制备冶金结合涂层的方法,等离子喷射熔覆成形修复技术是利用等离子弧的能量加热、引燃具有自放热反应能力的材料粒子,并使粒子高速撞击具有一定预热温度的基体后堆垛沉积,形成冶金自粘结涂层的一种工艺方法。这种工艺方法是从Ni-Al热喷涂复合材料的自放热反应可使涂层界面达到微冶金结合的原理出发,借鉴自蔓延材料的成分组成及化学反应的放热原理,通过增大自放热反应能,适当提高基体整体预热温度和利用等离子射流实时对喷射粒子撞击基体形成的喷射放热反应池进行再次加热,增强喷射粒子撞击基体表面时的自放热反应效果,在结合部位获得具有较大成分过渡区的冶金结合涂层。涂层形成冶金结合的机理分析:(1)采用的Ni基和Fe基复合材料具有强烈的自放热反应特点,通过高温等离子弧能够被引燃。(2)颗粒间的自放热反应虽然是在瞬间完成,但仍存在由颗粒表面至芯部蔓延,颗粒逐步完全反应、熔融的一个过程,即自放热反应复合材料从被加热点燃到强烈放热需要一个短暂的时间(tr),也可称为自放热反应时间。(3)喷射粒子从被送入等离子射流至飞行撞击基体需经历一段时间(tf),也可称为粒子飞行时间。(4)通过采用工艺措施可使自放热反应时间tr和粒子飞行时间tf相匹配,粒子撞击基体时恰好反应最剧烈。(5)基体整体具有一定的预热温度,有利于界面处涂层与基体的熔合。(6)利用等离子射流实时对喷射粒子撞击基体形成的喷射放热反应池进行再次加热,有利于界面处涂层与基体的熔合。(7)复合材料粒子高速撞击具有一定适宜温度的基体时产生的变形促进了不同成分物质的充分接触,使自放热反应更加剧烈,同时也使得喷射粒子与基体充分接触,在结合处形成一定的接触压力,保证了自放热反应热能的传递,促进了结合部位的熔合。(8)等离子弧对基体的预热和基体上喷射部位的加热促进了界面冶金结合的形成。(9)在以上(1)、(4)~(8)等六方面的综合作用下,高温粒子在基体表面自放热反应释放的热能和电弧的热能能够使涂层与基体之间熔合,在界面形成冶金结合,即喷射粒子具有自粘结特点。如图1所示,本发明提供的等离子喷射熔覆制备冶金结合涂层的方法包括如下步骤:(1)清理、清洗工件表面,去除油污、杂质。(2)预热工件至500~700℃。(3)进行等离子喷射熔覆,在基体表面制备涂层,在涂层制备过程中保持基体的温度在500~700℃之间。(4)在喷涂环境中自然冷却工件至室温。在喷涂过程中,喷涂速度v满足v=16π2R2(h-867R)·sinαT]]>其中,R为粉末平均粒径,h为喷涂距离,α为喷涂角度,T为环境温度。通过上述喷涂速度v的设置,能够使涂层达到更好的结合强度。一般而言涉及的参数取值如表1所示。表1实施例1:采用Ni包石墨(C:60%)与Ti机械混合的复合粉末(Ni包石墨:50%,Ti:50%),粉末粒径:15~45μm。基体为45钢。(1)对基体进行清理、清洗,去除基体表面的油污、杂质。(2)采用氧-乙炔火焰加热45钢基体至600℃。(3)采用等离子喷射熔覆设备按表2参数,在基体表面制备涂层。表2等离子喷射熔覆参数Ar压力1.2MPaAr流量60L/minH2压力1.1MPaH2流量5L/min工作电压140V工作电流340A送粉气压力0.6MPa送粉气流量6L/min送粉量40/min喷射距离38mm喷枪平移线速度1.5m/min基体温度600℃(4)涂层制备结束后,在喷涂环境中自然冷却工件至室温。实施例2:采用质量份数比Al:Cr2O3:Ti:C=7:3:2:5的造粒烧结复合粉末,粉末粒径:15~45μm。基体为45钢。(1)对基体进行清理、清洗,去除基体表面的油污、杂质。(2)采用氧-乙炔火焰加热45钢基体至600℃。(3)采用等离子喷射熔覆设备按表3参数,在基体表面制备涂层。表3等离子喷射熔覆参数(4)涂层制备结束后,在喷涂环境中自然冷却工件至室温。实施例3:采用质量份数比Al:Cr2O3:Si:C=10:3:2:9的造粒烧结复合粉末,粉末粒径:15~45μm。基体为45钢。(1)对基体进行清理、清洗,去除基体表面的油污、杂质。(2)采用氧-乙炔火焰加热45钢基体至600℃。(3)采用等离子喷射熔覆设备按表4参数,在基体表面制备涂层。表4等离子喷射熔覆参数Ar压力1.2MPaAr流量80L/minH2压力1.1MPaH2流量6L/min工作电压150V工作电流320A送粉气压力0.6MPa送粉气流量6L/min送粉量40/min喷射距离45mm喷枪平移线速度1.2m/min基体温度600℃(4)涂层制备结束后,在喷涂环境中自然冷却工件至室温。如图2所示,在Al合金基体制备的Ni-Ti-C复合涂层截面SEM形貌及EDS线扫描能谱分析照片,可以看到复合涂层与Al合金基体结合部形成了成分过渡区,产生了一定的冶金结合,说明了本发明提出的新技术具有可行性。本发明的的主要特点是:(1)采用的喷射熔覆材料是新研制的具有自放热反应的一种全新材料。自放热反应形成的涂层含有较多的陶瓷相,涂层硬度较高,耐磨性较高。(2)喷射的粒子温度和速度高,粒子速度大于350m/s。(3)设备系统的功能和调整范围宽。(4)与等离子熔覆技术相比较,在基体的喷射斑点处没有明显的熔池,基体的热应力小。(5)可以采用自粘结工艺方法直接满足需要的喷射熔覆层厚度。也可以在冶金自粘结涂层的表面,继续利用非转移弧高速喷射Co-WC、NiCr-Cr3C2等高硬度、高耐磨性材料或其它功能材料,可实现冶金结合底层至高性能面层的梯度涂层制备。尽管本发明的实施方案已公开如上,但其并不仅仅限于说明书和实施方式中所列运用,它完全可以被适用于各种适合本发明的领域,对于熟悉本领域的人员而言,可容易地实现另外的修改,因此在不背离权利要求及等同范围所限定的一般概念下,本发明并不限于特定的细节和这里示出与描述的图例。当前第1页1 2 3