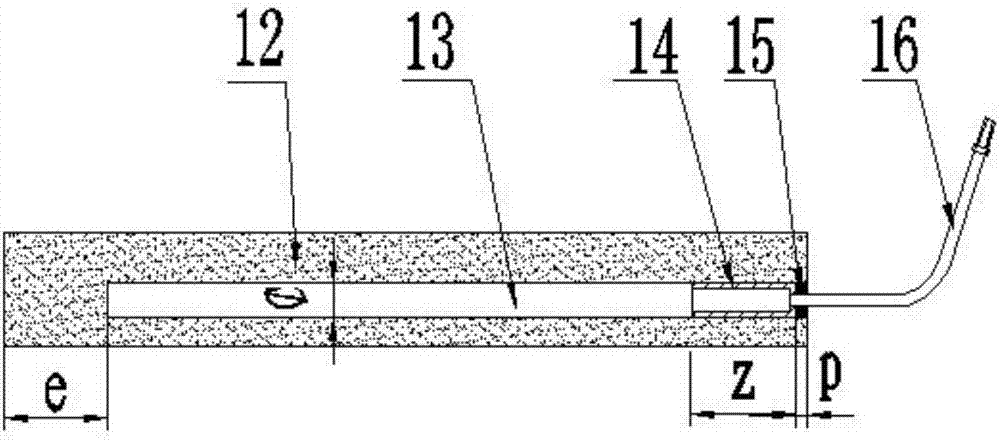
本实用新型涉及一种用于连铸中间包吹氩精炼装置,属钢铁冶金连铸中间包工艺
技术领域:
。
背景技术:
:在连铸机中间包内设置由湍流控制器、挡墙、斜孔挡坝组合使用的控流装置,可以改变中间包内钢水的运行路线,延长钢水在中间包内的停留时间,促进夹杂物上浮和去除,减少铸坯内部夹杂、改变夹杂物形态的冶金功能。近年来,为满足开发生产高纯洁净钢对夹杂物的控制要求,研究应用连铸中间包气幕挡墙技术,即将条形透气砖置于中间包包底,吹入氩气,氩气透过气幕挡墙上浮、形成一道微气泡气幕屏障,这些微气泡将夹杂物扑捉、上浮,从而被渣层所吸附,达到去除夹杂物净化钢液的目的。CN103990787A(申请号201410209515.2)公开了一种用于去除连铸中间包内钢液夹杂物的装置,包括湍流控制器、条形透气砖、挡墙和挡坝,条形透气砖(2)位于湍流控制器(1)与挡墙(3)之间,固定于中间包包底永久衬上,所述湍流控制器(1)的纵向中心线与条形透气砖(2)水平距离a为400~600mm,条形透气砖(2)与挡墙(3)的水平距离b为200~700mm,挡墙(3)与挡坝(4)的水平距离c为200~700mm,应用本发明,使得连铸坯中等效直径大于50μm的夹杂物基本去除,连铸坯中等效直径小于50μm的微小夹杂物数量比中间包内设置由湍流控制器、挡墙、挡坝组合使用条件下同比减少60%以上,比中间包内设置由湍流控制器、条形透气砖的使用条件下同比减少30%以上。该专利技术的不足:一是挡坝上设有直孔,不利于形成中间包内的钢液表面层流,死区比例较大,二是条形透气砖吹氩流量靠人工调节控制,没有根据中间包液面(中间包内钢水净重)的变化及时调整氩气流量大小,造成在钢包开浇、换包、停浇等中间包低液面条件下、因吹氩流量调整不及时、吹破渣面引发钢水卷渣的技术难题。技术实现要素:针对现有技术的不足,本实用新型提供一种用于连铸中间包吹氩精炼装置,在连铸中间包内设置一种吹氩精炼装置,在氩气流量控制上设计一套氩气管路系统和电气控制系统,根据中间包内钢水净重的变化,自动调整氩气流量,实现精准控制,解决了钢包换包等中间包低液面条件下、因吹氩流量调整不及时、吹破渣面引发的钢水卷渣等问题,提高了整个浇注过程中氩气泡捕获并去除夹杂物的效果,本实用新型用于板坯连铸中间包生产钢种为Q550D的连铸坯中的夹杂物,比应用
背景技术:
CN103990787A(申请号201410209515.2)同比减少15%以上。本实用新型的技术方案如下:一种用于连铸中间包的吹氩精炼装置,包括湍流控制器(1)、条形透气砖(2)、挡墙(3)和斜孔挡坝(4),其特征在于,湍流控制器安装在中间包注流冲击区包壁工作衬的内侧,其纵向中心线与大包长水口(9)的中心线重合,条形透气砖(2)与斜孔挡坝(4)的底端都固定于中间包包底永久衬(6)上,并部分埋入中间包包底工作衬(5)内,挡墙(3)的两侧端固定于中间包包壁永久衬上。优选的,斜孔挡坝(4)位于中间包包底永久衬拐角的顶点(A),斜孔挡坝(4)上的斜孔倾角β为30°~35°,斜孔下沿到中间包包底工作衬(5)工作面的垂直距离x为25~30mm,挡墙(3)位于湍流控制器(1)与斜孔挡坝(4)之间,挡墙(3)与斜孔挡坝(4)的水平距离a为250~300mm,条形透气砖(2)位于挡墙(3)和湍流抑制器(1)之间的中心处,即条形透气砖(2)中心线到挡墙(3)的距离b与条形透气砖(2)到湍流抑制器(1)的距离c相等。A为中间包包底永久衬(5)拐角的顶点,斜孔倾角β为斜孔挡坝(4)的斜孔与中间包水平面形成的夹角。本实用新型优选的,所述的条形透气砖(2)的上部高出中间包包底工作衬(5)的高度y为10~22mm,在条形透气砖(2)高出中间包包底工作衬(5)的侧部,采用涂抹料(11)涂抹成流线形。本实用新型优选的,所述的条形透气砖(2),包括条形透气砖基体(12)、气室(13)、进气管(16),透气砖基体(12)内设置有气室(13),气室的进气端与进气管(16)连接并密封,进气管(16)的一端与气室连通,另一端伸出透气砖基体,连接气源。优选的,所述条形透气砖(2)还包括嵌入套管(14),嵌入套管(14)设置在气室的进气端,用于安装、固定进气管(16)。更优选的,嵌入套管(14)周围用胶泥(15)密封。本实用新型进一步优选的,所述的条形透气砖(2),其高度n为95~115mm,宽度m为120~130mm,气室(13)为圆柱形内腔,圆的直径¢为30~40mm,气室(13)中心线的高度w为40~50mm,气室(13)与条形透气砖基体(12)的盲端距离e为90~100mm,嵌入套管(14)的长度z为90~100mm,胶泥(15)的厚度p为10~15mm。本实用新型优选的,所述湍流抑制器(1)的内腔呈圆柱形,内腔圆的直径d为400~450mm,内腔圆的高度h为350~400mm。本实用新型的斜孔挡坝(4)位于中间包包底永久衬拐角的顶点(A),斜孔挡坝(4)的斜孔倾角β为30°~35°,斜孔下沿到中间包包底工作衬(5)工作面的垂直距离x为25~30mm,挡墙(3)位于湍流控制器(1)与斜孔挡坝(4)之间,挡墙(3)与斜孔挡坝(4)的水平距离a为250~300mm,条形透气砖(2)位于挡墙(3)和湍流抑制器(1)之间的中心处等设计,是本领域的技术人员经过大量的水模实验与数模研究和生产实践摸索得到的,水模实验与数模研究结果表明,本实用新型用于连铸中间包吹氩精炼装置利于形成中间包内的钢液表面层流,增加钢液的停留时间,减小死区比例,提高了氩气泡捕获并去除夹杂物的效果,将本实用新型的精炼装置与
背景技术:
CN103990787A(申请号201410209515.2)按照1:2建模进行水模实验,吹气量为6L/min条件下,测定的平均停留时间同比
背景技术:
CN103990787A(申请号201410209515.2)增加10%以上,死区比率同比
背景技术:
CN103990787A(申请号201410209515.2)降低35%以上,应用本实用新型浇注生产Q550D的连铸坯试样电解夹杂物重量同比应用
背景技术:
CN103990787A(申请号201410209515.2)生产的连铸坯中的电解夹杂物重量同比减少15%以上,取得了有益效果。所述的透气砖基体(12),采用机压成型技术生产的弥散型镁质条形透气砖,通过适当的颗粒级配以及外加剂的作用,通过高温烧成后形成较多的开口气孔,从而形成弥散型的透气方式,其主要理化指标:MgO(%)≥90,Al2O3(%)≤3,体积密度(g/cm3)≤2.85,显气孔率(%)≥20,常温耐压强度(MPa)≥15,常温抗折强度(MPa)≥5。所述的湍流抑制器(1)、挡墙(3)、斜孔挡坝(4)均采用现有镁质浇注料浇注成型,且在400~450℃中温烧制而成,其中斜孔挡坝(4)的高度k为330~420mm,厚度u为150~180mm,斜孔的半径R为39~45mm,挡墙(3)的高度H为850~900mmmm,厚度L为100~150mm。本实用新型还提供用于连铸中间包吹氩精炼装置的氩气控制系统及其控制方法,氩气控制系统包括氩气管路系统和电气控制系统。所述氩气管路系统,分为主吹支路和手动旁路,其中主吹支路包括第一球阀20a、气体过滤器21、第一压力表22a、第二球阀20b、压力变送器23、电磁阀24、冶金专用质量流量控制器25、减压阀26、第二压力表22b、第三球阀20c,手动旁路包括第四球阀20d、手动调节阀27,手动旁路安装于第一压力表22与a第二压力表22b之间,与主吹支路的第二球阀20b、压力变送器23、电磁阀24、冶金专用质量流量控制器25、减压阀26并联;用于主吹支路出现故障后、手动操作应用,管路元件连接关系如图8所示,氩气管路系统定位于控制柜内,其特征在于,氩气管路系统中的压力变送器23、减压阀26,具有机械式和电子式双重压力自动补偿功能,入口压力任意波动,出口压力自适应,不受背压扰动影响。所述电气控制系统,包括吹氩控制系统PLC、触摸屏、上位机操作系统、网路交换机、连铸基础自动化系统,各系统通过以太网通讯与网路交换机连接,中间包内钢水称重系统收集、发送中间包内钢水重量到连铸基础自动化系统,如图9所示。本领域技术人员可以根据实际需要进行选择,或者选用现有技术的控制系统。所述吹氩控制系统PLC通过以太网通讯收集、上传第一压力表(22a)压力值、冶金专用质量流量控制器(25)流量值、第二压力表(22b)压力值到连铸基础自动化系统数据库,并执行吹氩控制系统PLC的氩气流量自动控制指令,根据中间包内钢水净重的变化,自动调整氩气流量,实现对吹氩流量的精准控制。所述氩气管路系统元件,均为市场采购,其中所述球阀(包括第一球阀20a、第二球阀20b、第三球阀20c、第四球阀20d)的型号规格为304SS-1/2,气体过滤器(21)的型号规格为BK110-3,压力表(包括第一压力表22a、第一压力表22b)的型号规格为YT40,压力变送器(23)的型号规格为8323-25-G1/2,电磁阀(24)的型号规格为5281-1/2-NBR,冶金专用质量流量控制器(25)的型号规格为Flox(on)s,量程为0-200NL/min,减压阀(26)的型号规格为BK100-2,手动调节阀(27)的型号规格为28-1/2-MS。所述电气控制系统元件,均为市场采购,其中所述PLC控制系统的型号规格为西门子S7系列,PLC模拟量模块的型号规格为4AI/2AO,触摸屏的型号规格为西门子7寸触摸屏,上位机操作系统的型号规格为D610,上位机软件WINCC6.0以上。本实用新型的有益效果:1)本实用新型将斜孔挡坝(4)位于中间包包底永久衬拐角的顶点(A),斜孔挡坝(4)的斜孔倾角β为30°~35°,斜孔下沿到中间包包底工作衬(5)工作面的垂直距离x为25~30mm,挡墙(3)位于湍流控制器(1)与斜孔挡坝(4)之间,挡墙(3)与斜孔挡坝(4)的水平距离a为250~300mm,条形透气砖(2)位于挡墙(3)和湍流抑制器(1)之间的中心处等设计,利于形成中间包内的钢液表面层流,增加钢液的停留时间,减小死区比例,提高了氩气泡捕获并去除夹杂物的效果,将本实用新型的精炼装置与
背景技术:
CN103990787A(申请号201410209515.2)按照1:2建模进行水模实验,吹气量为6L/min条件下,测定的平均停留时间同比
背景技术:
CN103990787A(申请号201410209515.2)增加10%以上,死区比率同比
背景技术:
CN103990787A(申请号201410209515.2)降低35%以上,应用本实用新型浇注生产Q550D的连铸坯试样电解夹杂物重量同比应用
背景技术:
CN103990787A(申请号201410209515.2)生产的连铸坯中的电解夹杂物重量同比减少15%以上;2)本实用新型用于连铸中间包吹氩精炼装置的氩气控制系统,在中间包浇注过程中,根据中间包内钢水净重的变化,自动调整氩气流量,实现精准控制,解决了钢包换包等中间包低液面条件下、因吹氩流量调整不及时、吹破渣面引发的钢水卷渣等问题,提高了整个浇注过程中连铸中间包去除夹杂物效果的稳定性与可靠性,解决了该技术推广应用的又一技术难题。附图说明图1是本实用新型用于去除连铸中间包内钢液夹杂物装置的工艺布置示意图。图2是本实用新型实施例中条形透气砖结构主视图图3是本实用新型实施例中条形透气砖结构的侧视图。图4是本实用新型实施例中斜孔挡坝的结构主视图,图5是本实用新型实施例中斜孔挡坝斜孔挡坝的结构侧视图。图6是本实用新型实施例中挡墙的结构主视图,图7是本实用新型实施例中挡墙的结构侧视图。图8是本实用新型实施例中氩气管路系统示意图。图9是本实用新型实施例中电气连接示意图。图中,1.湍流控制器;2.条形透气砖;3.挡墙;4.斜孔挡坝;5.中间包工作衬;6.中间包永久衬;7.中间包内钢水正常浇注液面;8.中间包内钢水浇注低液面;9.大包长水口;10.上水口;11.涂抹料;12.条形透气砖基体;13.气室;14.嵌入套管;15.密封胶泥;16.进气管;17.斜孔挡坝本体;18.斜孔;19.吊钩;20.球阀(包括第一球阀20a、第二球阀20b、第三球阀20c、第四球阀20d);21.气体过滤器;22.压力表(包括第一压力表22a、第一压力表22b);23.压力变送器;24.电磁阀;25.冶金专用质量流量控制器;26.减压阀;27.手动调节阀,A为中间包包底永久衬拐角的顶点,斜孔倾角β为斜孔与中间包水平面形成的夹角。具体实施方式下面结合具体实施例对本实用新型作进一步说明,但不限于此。实施例1一种用于连铸中间包吹氩精炼装置,结构如图1-图7所示,包括湍流控制器1、条形透气砖2、挡墙3和斜孔挡坝4,湍流控制器安装在中间包注流冲击区包壁工作衬的内侧,其纵向中心线与大包长水口9的中心线重合,条形透气砖2与斜孔挡坝4的底端都固定于中间包包底永久衬6上,并部分埋入中间包包底工作衬5内,挡墙3的两侧端固定于中间包包壁永久衬上,其特征在于,斜孔挡坝4位于中间包包底永久衬拐角的顶点A,斜孔挡坝4上的斜孔倾角β为30°,斜孔下沿到中间包包底工作衬5工作面的垂直距离x为25mm,挡墙3位于湍流控制器1与斜孔挡坝4之间,挡墙3与斜孔挡坝4的水平距离a为300mm,条形透气砖2位于挡墙3和湍流抑制器1之间的中心处,即条形透气砖2中心线到挡墙3的距离b与条形透气砖2到湍流抑制器1的距离c相等。所述的条形透气砖2的底部安置于中间包包底永久衬6上,埋入中间包包底工作衬5,且条形透气砖2的上部高出中间包包底工作衬5的高度y为10mm,在条形透气砖2高出中间包包底工作衬5的侧部,采用涂抹料11涂抹成流线形。所述的条形透气砖2,包括条形透气砖基体12、气室13、进气管16,透气砖基体12内设置有气室13,气室的进气端与进气管16连接并密封,进气管16的一端与气室连通,另一端伸出透气砖基体,连接气源。所述条形透气砖2还包括嵌入套管14,嵌入套管14设置在气室的进气端,用于安装、固定进气管16。嵌入套管14周围用胶泥15密封。所述的条形透气砖2,其高度n为95mm,宽度m为120mm,气室13为圆柱形内腔,圆的直径¢为30mm,气室13中心线的高度w为40mm,气室13与条形透气砖基体12的盲端距离e为90mm,嵌入套管14的长度z为100mm,胶泥15的厚度p为10mm。所述湍流抑制器1的内腔呈圆柱形,内腔圆的直径d为400mm,内腔圆的高度h为350mm。所述的透气砖基体12,采用机压成型技术生产的弥散型镁质条形透气砖,通过适当的颗粒级配以及外加剂的作用,通过高温烧成后形成较多的开口气孔,从而形成弥散型的透气方式,其主要理化指标:MgO(%)≥90,Al2O3(%)≤3,体积密度(g/cm3)≤2.85,显气孔率(%)≥20,常温耐压强度(MPa)≥15,常温抗折强度(MPa)≥5。所述的湍流抑制器(1)、挡墙(3)、斜孔挡坝(4)均采用现有镁质浇注料浇注成型,且在400~450℃中温烧制而成,其中斜孔挡坝4的高度k为330mm,厚度u为150mm,斜孔的半径R为39mm,挡墙3的高度H为870mm,厚度L为150mm。本实用新型还提供用于连铸中间包吹氩精炼装置的氩气控制系统及其控制方法,氩气控制系统包括氩气管路系统和电气控制系统。所述氩气管路系统,分为主吹支路和手动旁路,其中主吹支路包括第一球阀20a、气体过滤器21、第一压力表22a、第二球阀20b、压力变送器23、电磁阀24、冶金专用质量流量控制器25、减压阀26、第二压力表22b、第三球阀20c,手动旁路包括第四球阀20d、手动调节阀27,用于主吹支路出现故障后、手动操作应用,管路元件连接关系如图8所示,氩气管路系统定位于控制柜内,其特征在于,氩气管路系统中的压力变送器23、减压阀26,具有机械式和电子式双重压力自动补偿功能,入口压力任意波动,出口压力自适应,不受背压扰动影响。所述电气控制系统,包括吹氩控制系统PLC、触摸屏、上位机操作系统、网路交换机、连铸基础自动化系统,各系统通过以太网通讯与网路交换机连接,中间包内钢水称重系统收集、发送中间包内钢水重量到连铸基础自动化系统,如图9所示。所述吹氩控制系统PLC通过以太网通讯收集、上传第一压力表22a压力值、冶金专用质量流量控制器25流量值、第二压力表22b压力值到连铸基础自动化系统数据库,并执行吹氩控制系统PLC的氩气流量自动控制指令,根据中间包内钢水净重的变化,自动调整氩气流量,实现对吹氩流量的精准控制。所述吹氩控制系统PLC的氩气流量自动控制指令如下:1)从大包开浇至中间包内钢水净重为30吨的正常浇注液面7之前,即0<中间包内钢水净重<30吨,在大包开浇的同时,开启氩气,条形透气砖2的氩气流量控制在10NL/min;2)中间包内钢水达到钢水净重为30吨的正常浇注液面7以后,即中间包内钢水净重≥30吨,条形透气砖2的氩气流量增大到26NL/min;3)大包更换,从中间包内钢水净重为30吨的正常浇注液面7降低到中间包内钢水净重为22吨的低液面8之间,即22吨≤中间包内钢水净重<30吨,条形透气砖2的氩气流量减小到19NL/min;4)钢包换包完成后,中间包内钢水升高到钢水净重为30吨的正常浇注液面7以后,即中间包内钢水净重≥30吨,条形透气砖2的氩气流量增大到26NL/min;5)大包停浇后,从中间包内钢水净重为30吨的正常浇注液面7降低到中间包内钢水净重为22吨的低液面8之间,即22吨≤中间包内钢水净重<30吨,条形透气砖2的氩气流量减小到19NL/min;6)中间包内钢水降低到降低到中间包内钢水净重为22吨的低液面8以后,即中间包内钢水净重<22吨,停止条形透气砖2吹氩。所述氩气管路系统元件,均为市场采购,其中所述球阀20(包括第一球阀20a、第二球阀20b、第三球阀20c、第四球阀20d)的型号规格为304SS-1/2,气体过滤器21的型号规格为BK110-3,压力表22(包括第一压力表22a、第一压力表22b)的型号规格为YT40,压力变送器23的型号规格为8323-25-G1/2,电磁阀24的型号规格为5281-1/2-NBR,冶金专用质量流量控制器25的型号规格为Flox(on)s,量程为0-200NL/min,减压阀26的型号规格为BK100-2,手动调节阀27的型号规格为28-1/2-MS。所述电气控制系统元件,均为市场采购,其中所述PLC控制系统的型号规格为西门子S7系列,PLC模拟量模块的型号规格为4AI/2AO,触摸屏的型号规格为西门子7寸触摸屏,上位机操作系统的型号规格为D610,上位机软件WINCC6.0以上。实施例2、如实施例1所述的一种用于连铸中间包吹氩精炼装置,不同之处在于:所述斜孔挡坝4上的斜孔倾角β为35°,斜孔下沿到中间包包底工作衬5工作面的垂直距离x为30mm,挡墙3与斜孔挡坝4的水平距离a为250mm,条形透气砖2的上部高出中间包包底工作衬5的高度y为20m。所述的条形透气砖2,其高度n为115mm,宽度m为130mm,气室13为圆柱形内腔,圆的直径¢为40mm,气室13中心线的高度w为50mm,气室13与条形透气砖基体12的盲端距离e为100mm,嵌入套管14的长度z为90mm,胶泥15的厚度p为15mm。所述湍流抑制器1的内腔呈圆柱形,内腔圆的直径d为450mm,内腔圆的高度h为400mm。实施例3、如实施例1所述的一种用于连铸中间包吹氩精炼装置,不同之处在于:所述斜孔挡坝4上的斜孔倾角β为32°,斜孔下沿到中间包包底工作衬5工作面的垂直距离x为28mm,条形透气砖2的上部高出中间包包底工作衬5的高度y为15m。所述的条形透气砖2,其高度n为100mm,宽度m为125mm,气室13为圆柱形内腔,圆的直径¢为35mm,气室13中心线的高度w为45mm,气室13与条形透气砖基体12的盲端距离e为95mm,嵌入套管14的长度z为95mm,胶泥15的厚度p为12mm。所述的斜孔挡坝4的高度k为420mm,厚度u为180mm,斜孔的半径R为45mm,挡墙3的高度H为900mmmm,厚度L为100mm。所述湍流抑制器1的内腔呈圆柱形,内腔圆的直径d为420mm,内腔圆的高度h为380mm。所述吹氩控制系统PLC的氩气流量自动控制指令如下:1)从大包开浇至中间包内钢水净重为30吨的正常浇注液面7之前,即0<中间包内钢水净重(吨)<30,在大包开浇的同时,开启氩气,条形透气砖2的氩气流量控制在15NL/min;2)中间包内钢水达到钢水净重为30吨的正常浇注液面7以后,即中间包内钢水净重≥30吨,条形透气砖2的氩气流量增大到32NL/min;3)大包更换,从中间包内钢水净重为30吨的正常浇注液面7降低到中间包内钢水净重为22吨的低液面8之间,即22吨≤中间包内钢水净重<30吨,条形透气砖2的氩气流量减小到25NL/min;4)钢包换包完成后,中间包内钢水升高到钢水净重为30吨的正常浇注液面7以后,即中间包内钢水净重≥30吨,条形透气砖2的氩气流量增大到32NL/min;5)大包停浇后,从中间包内钢水净重为30吨的正常浇注液面7降低到中间包内钢水净重为22吨的低液面8之间,即22≤中间包内钢水净重<30吨,条形透气砖2的氩气流量减小到25NL/min;6)中间包内钢水降低到降低到中间包内钢水净重为22吨的低液面8以后,即中间包内钢水净重<22吨,停止条形透气砖2吹氩。对比例中国专利文献CN103990787A(申请号201410209515.2)公开了一种用于去除连铸中间包内钢液夹杂物的装置。实验例将本实用新型实施例1-3的吹氩精炼装置与对比例的精炼装置按照1:2建模进行水模实验,吹气量为6L/min条件下,测定的平均停留时间和死区比率对比分析如表1所示:表1方案平均停留时间/min死区比率/%实施例16.2283.772实施例26.2253.797实施例36.2233.767对比例5.5766.281将实施例1~3的吹氩精炼装置及氩气控制方法及对比例的去除连铸中间包内钢液夹杂物的装置,在莱芜钢铁集团银山型钢有限公司炼钢厂单流宽板坯连铸中间包上应用对比分析,钢种Q550D,在铸坯1/4处分别取大样电解试样,加工成直径为60mm、高度为100mm的圆棒,进行大样电解夹杂物检测,检测数据如表2所示:表2通过表1的数据对比,本实用新型实施例1-3的水模实验中,测定的平均停留时间同比对比例CN103990787A(申请号201410209515.2)增加10%以上,死区比率同比对比例CN103862014A(申请号:201410114064.4)降低35%以上。通过表2的数据对比,应用本实用新型的装置,本实用新型实施例1-3生产出的连铸坯试样电解夹杂物重量同比应用对比例CN103990787A(申请号201410209515.2)生产的连铸坯中的电解夹杂物重量同比减少15%以上。当前第1页1 2 3